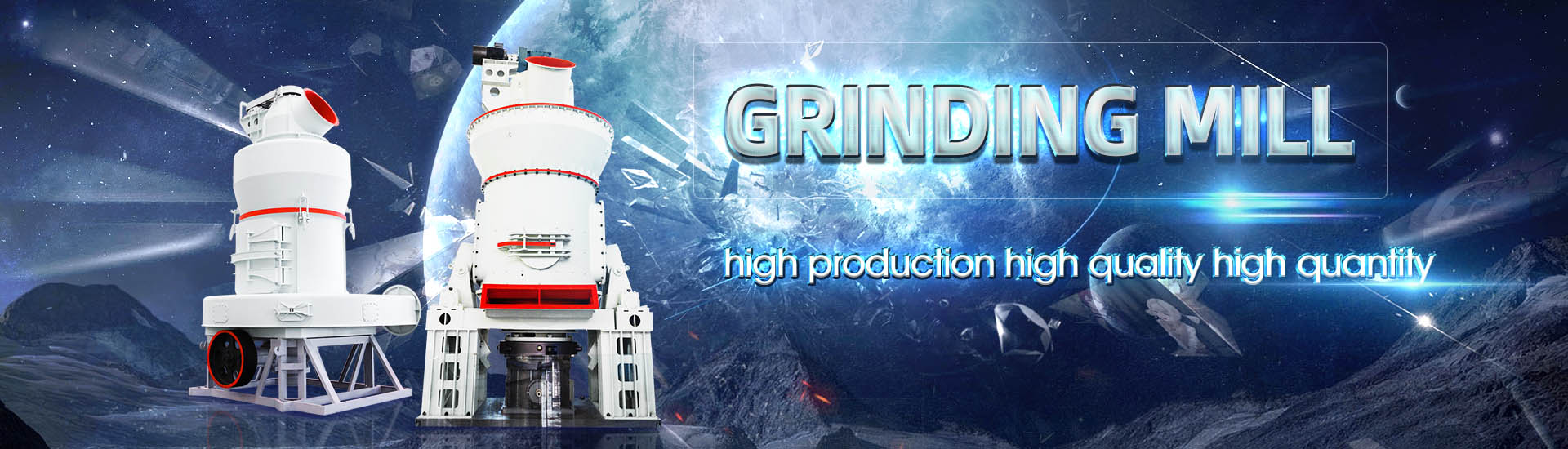
Equipment production cost table
.jpg)
GENERAL PROCESS PLANT COST ESTIMATING,
2014年6月1日 Many engineering design projects are developed to provide sizing information from which estimates of capital and operating costs can be made Chemical plants are built to make a profit, and an2024年6月25日 Production costs refer to all of the direct and indirect costs businesses face from manufacturing a product or providing a service Production costs can include a variety ofProduction Costs: What They Are and How to Calculate The cost of equipment for civil engineering construction projects can range from 25 to 40% of the total project cost Figure 31 illustrates the ability to influence the construction cost of a project Chapter 3: Equipment Productivity FreeTable 41 summarizes the probability of different delivery times for an item In this table, the first column lists the possible shipping times (ranging from 10 to 16 days), the 411 Choice of Project Management for Construction: Labor, Material and
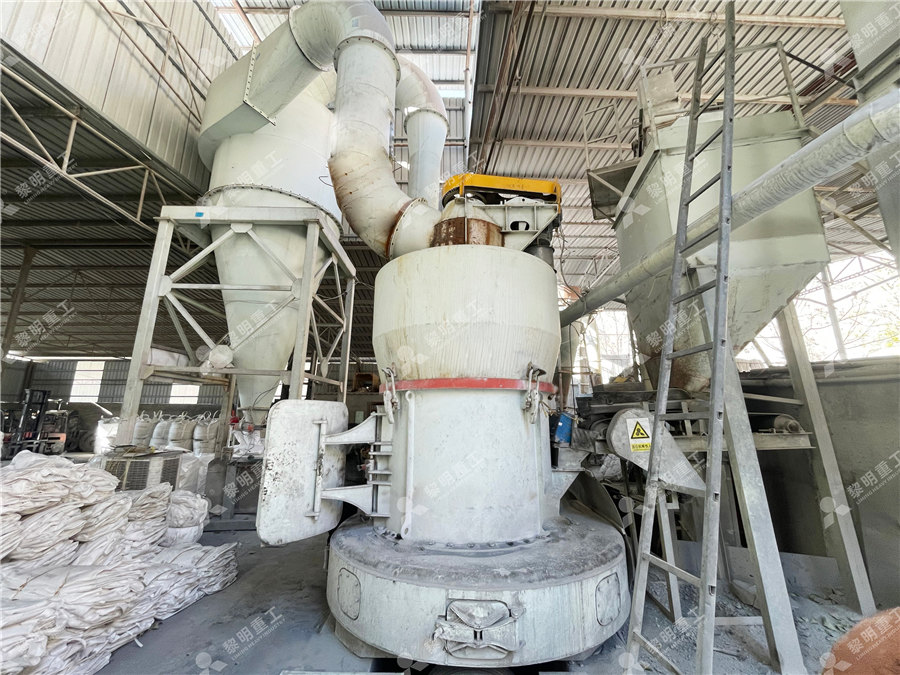
LECTURE 06 Equipment Sizing and Capital Cost Estimation
Extensive data are used to estimate the costs of materials, labor, and construction equipment – based upon detailed design calculations for foundations, platforms, piping, instrumentation, The equipment configurations, costs, and produc tion rates are given in Table 1 The conversion involves replacing tool b with tool b', which costs $18 million; a brandnew line ofEquipment Costs and Production Rates Download TableWe will learn in this chapter that short run costs are different from long run costs We can distinguish between two types of cost: explicit and implicit Explicit costs are outofpocket costs, that is, actual payments Wages that a firm pays its Costs and Production – Introduction to Activitybased costing (ABC) is the process that assigns overhead to products based on the various activities that drive overhead costs All products consist of material, labor, and overhead, and the major cost components have 63: Calculate ActivityBased Product Costs Business
.jpg)
Process Equipment Cost Estimating By Ratio And Proportion
Process Equipment Cost Estimating By Ratio And Proportion 2020 Instructor: Randall W Whitesides, PE PDH Online PDH Center 5272 Meadow Estates Drive Fairfax, VA 220306658 Table 1 below can be used It lists the value of a size exponent for various types of process equipment The Table 1 values have been condensed from aProduction Costs Adding administrative expenses to Factory costs equal Production costs These administrative expenses include office rent, asset depreciation, audit fees, bank charges, and other miscellaneous office Download Cost Sheet With COGS Excel TemplateIt incurs $30,000 in manufacturing overheads and $50,000 in direct material costs Help the business to determine the overall cost of production Use the given data for the calculation of production cost Calculation of Production Production Cost Formula What Is It, How to 2024年5月30日 Method 3 – Apply User Defined Function to Calculate Production Cost Using VBA To calculate the production cost using a userdefined function made with VBA code, we’ll use the following simplified dataset, containing the costs for direct labor, direct material, and manufacturing cost STEPS: Go to the Developer tab on the ribbonHow to Calculate Production Cost in Excel (3 Effective Ways)
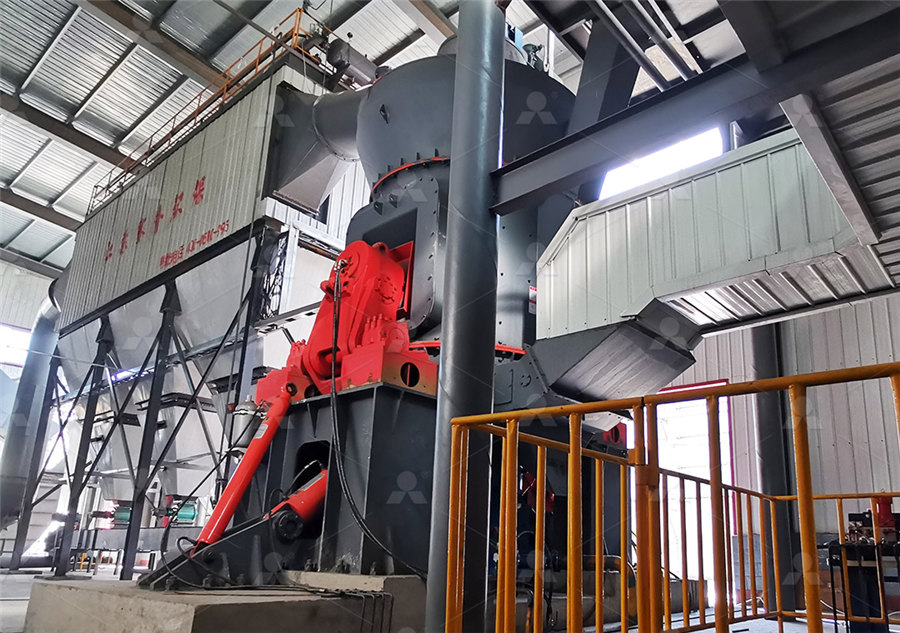
Introduction to Production, Costs, and Industry Structure
Example A shows the firm’s cost calculation when wages are $40 and machines costs are $80 In this case, technology 1 is the lowcost production technology In example B, wages rise to $55, while the cost of machines does not change, in which case technology 2 is the lowcost production technologyEquipment Productivity • Bulldozer Productivity • Excavator Productivity • Scraper Production 33 Municipal/Utility Construction Projects The Mechanized Excavation System • The Guidance Control System • The Propulsion System • The Spoil Removal System • The Control System • The Pipe Lubrication System • Equipment CostChapter 3: Equipment Productivity FreeThe target population for the MEPI consists of all industries in Canada that purchase machinery and equipment The product universe for the MEPI consists of all machinery and equipment purchased by industries in Canada and corresponding to the classification by commodity incorporated in the SupplyUse tables (SUT), that is the SupplyUse Machinery and Equipment Price Index (MEPI) Statistics Canada2015年11月13日 SAP PP Tables for Production Orders A production order defines which material is to be processed, at which location, at what time and how much work is required It also defines which resources are to be used and how the order costs are to be settledSAP PP Tables – Important Production Planning Tables in SAP PP
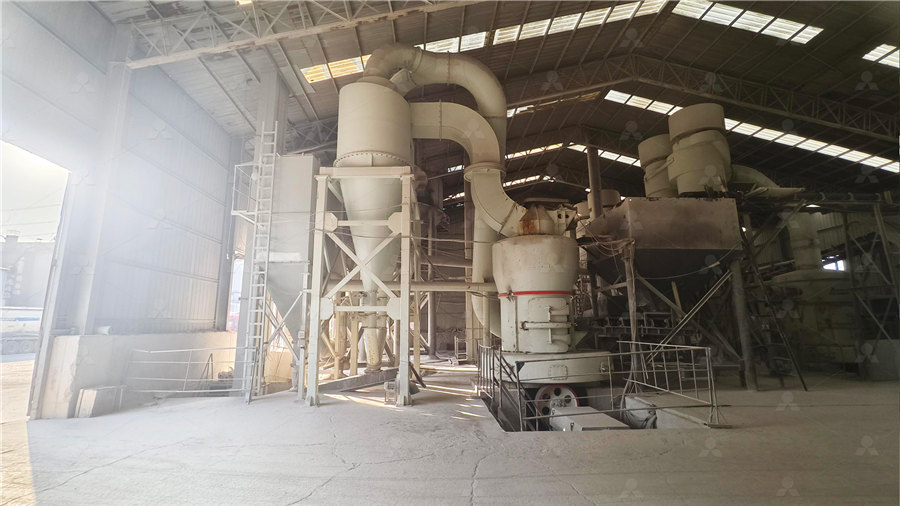
The #1 Product Cost Analysis Template Excel PMITOOLS
2024年8月16日 Understanding Product Cost Analysis: Product cost analysis involves examining all expenses associated with producing a product It includes direct costs like materials and labor and indirect costs such as overhead and administrative expenses The primary goal is to determine the total cost of production and identify areas for cost reduction or 2024年9月20日 Equipment inventories typically include the description of the equipment, its current value, operating and maintenance costs, and depreciation information 9 Excel templates, this one is the most important for creating a budget by compiling accurate estimates of the cost and timeframe for completing production tasks18 Free Manufacturing Excel Templates ProjectManager2024年6月15日 Cost of production refers to the total expenses incurred in manufacturing a product or providing a service It plays a crucial role in determining the profitability and competitiveness of a business Understanding the cost of production is essential for effective financial management and decisionmaking Insights from different perspectives shed light on Cost of Production: How to Calculate and Minimize the Costs of Costs of production: Overview Examples Importance Formula Reduce Types labour, equipment, rent, and marketing costs In simple terms, it is the sum of all expenses necessary to produce and sell a product or service Table 1 Total costs calculation Costs Of Production: Meaning, Examples Importance
.jpg)
The Ultimate Guide to Cost Management Smartsheet
2017年4月25日 Direct Costing: Direct costing, also called contribution costing or variable costing, is a technique that only assigns variable manufacturing costs to the cost of a product You do not add fixed manufacturing costs to the cost of In the realm of manufacturing and production, factory overhead costs play a critical role in determining the overall expenses incurred beyond direct materials and direct labor This article aims to provide a comprehensive explanation of what factory overhead costs entail, their significance in accounting and finance, examples to illustrate their application, and their Understanding Factory Overhead Costs: Definition, Examples, and We will not consider calculating articles in detail We automate the process of calculating the planned production cost of production using Excel formulas Our task is to create a table using Excel tools so that when you substitute data, the production cost of goods, works, and services is automatically considered The production cost Calculation of production costs in ExcelFigure 63 How Output Affects Total Cost At zero production, the fixed costs of $160 are still present As production increases, we add variable costs to fixed costs, and the total cost is the sum of the two Figure 63 graphically shows the relationship between the quantity of output produced and the cost of producing that outputCosts and Production – Introduction to Microeconomics
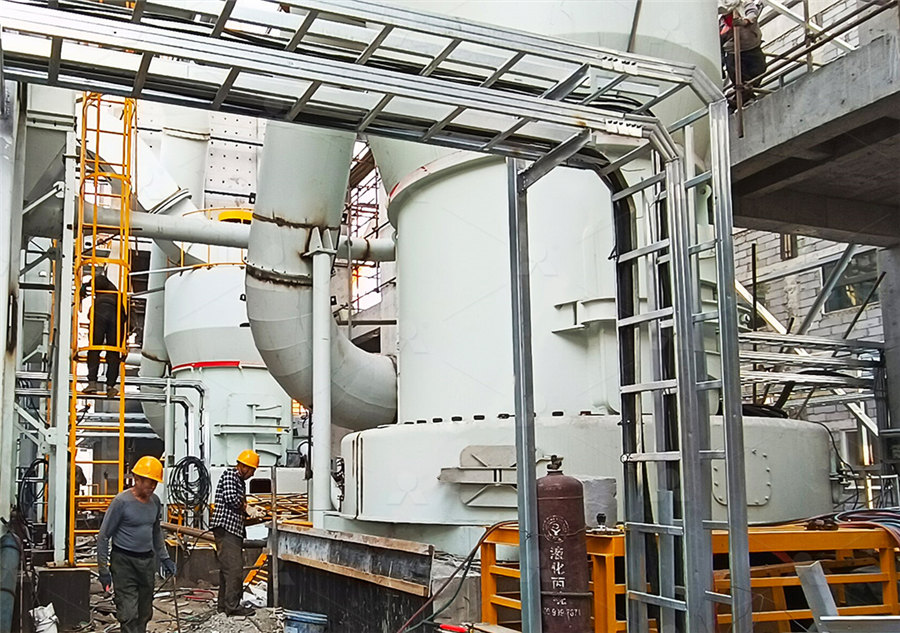
Matches' 275 Equipment Cost Estimates
Matches provides 275 process equipment conceptual capital costs estimates office (405) 3402673 fax (866) 5833035 tollfree (800) 5256277 Home; About; News; Products; Services; Calendar; Contact; Matches provides conceptual process, cost and optimization engineering services to the chemical and metallurgical industryDownload Table Equipment specification and cost from publication: Activated carbon from broiler litter: Process description and cost of production Animal manure continues to represent a Equipment specification and cost Download Table2024年11月21日 Conversion cost formula: (basechassiscost * (09 tech) + newmodulecost) * prodmodifiers + dismantlecosts Note that for the equipment designers, the base chassis cost is not shown in the research or production screens (those have modules priced in), but is seen in the tooltip for production cost in the designer itselfProduction Hearts of Iron 4 Wiki2024年1月12日 Today’s Techni Waterjet Manufacturing Manager, Jonathan Schlick, has over 20 years experience in the field of industrial machinery After a 12 year career in laser machinery, he moved to waterjets where he’s grown his skills and knowledge of the technology through leading Techni’s Regional ServiceMachines Used in Manufacturing: Full List of Manufacturing Equipment
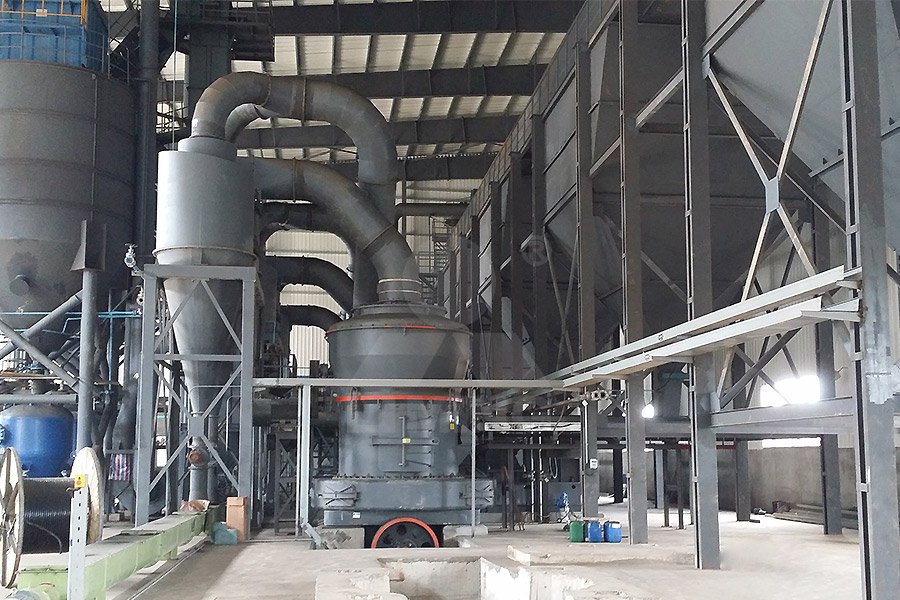
How Is Job Costing Used to Track Production Costs?
Let’s start by looking at actual product costs for the three costliest tables produced in May It would be helpful to break these costs out for direct materials Chan Company received a bill totaling $3,700 for machine parts used in maintaining factory equipment The bill will be paid next month Make the journal entry to record this Introduction There are persistent gaps in access to affordable medicines The WHO Model List of Essential Medicines (EML) includes medicines considered necessary for functional health systems Methods A generic price estimation Estimated costs of production and potential prices for 2008年7月10日 Hi all, I want to know the tables from where i can get 1) Planned cost of the production ordermaterials, activities, overheads 2) Actual cost of the production ordermaterials, activities, overheads Regards, MHPTables for the production order costs SAP Communityproduction pathways • Assess the potential to meet H 2 production cost targets (H2 Shot: $1/kg of H 2 by 2031) • Evaluate the uncertainty and show the potential for H 2 cost reduction for each pathway through single and multivariable sensitivity analysesHydrogen Production Cost and Performance Analysis Energygov
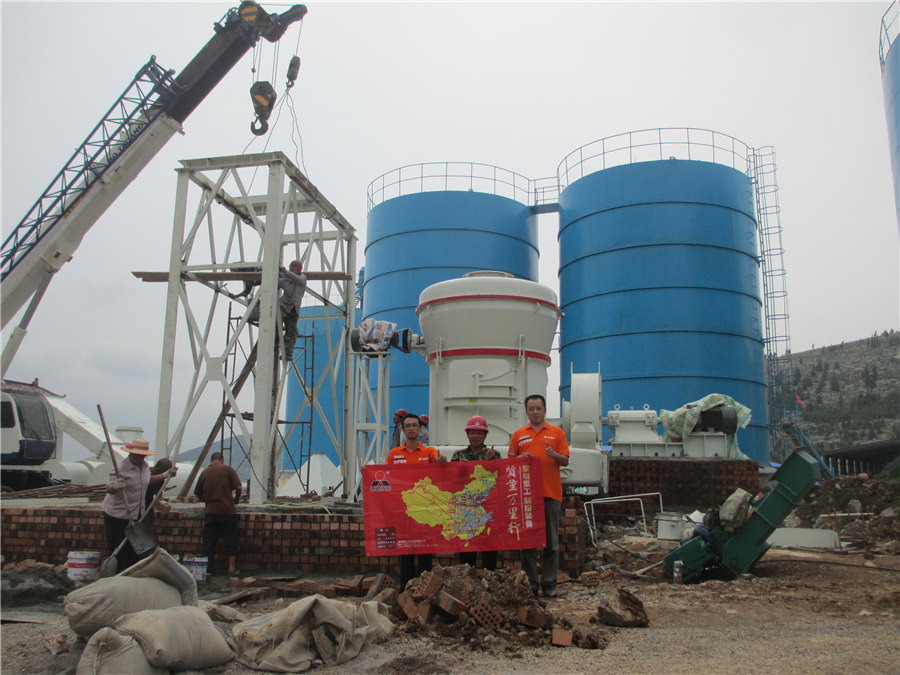
81: Production Choices and Costs: The Short Run
Our analysis of production and cost begins with a period economists call the short run The short run in this microeconomic context is a planning period over which the managers of a firm must consider one or more of their factors of production as fixed in quantity For example, a restaurant may regard its building as a fixed factor over a period of at least the next yearPDF On Jan 1, 2008, John Nowatzki and others published Strip Till for Field Crop Production : Equipment, Production, Economics Table 10 Estimated cost and use factors for striptill equipment(PDF) Strip Till for Field Crop Production : Equipment, Production 3 For capital cost estimation: FOB equipment cost increases with sizen where n is usually 06 to 07 When n = 1 there is no capital cost advantage to building larger; increase size or capacity by duplicating equipment 4 For capital cost estimates: (FOB q L+M* ) + installed instruments + buildings required within the battery limits = L+M costAppendix D: Capital Cost Guidelines Wiley Online Library2008年3月9日 Hi , All PP Guru, I would like to know , List of all Tables for "Production Order" I only know AFPO AFKO What are other than that SameerList of all Tables for "Production Order" SAP Community
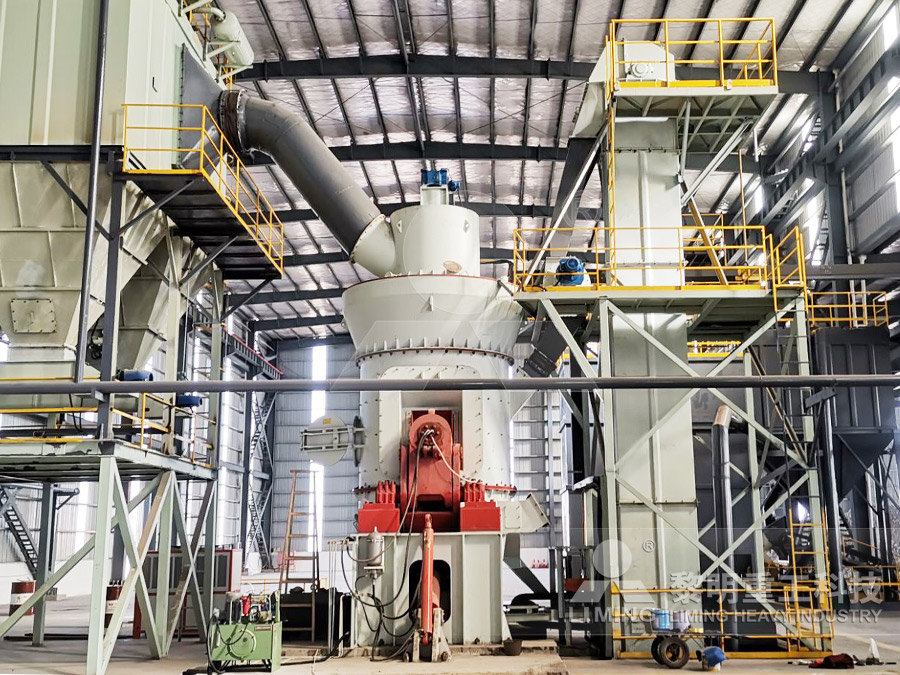
Brewing Equipment Cost Analysis Guide
2024年8月14日 New or Used Equipment: The production cost of brewing equipment also depends on whether you buy new or used brewing equipment for your startup Of course, new equipment will be more expensive than used equipment, but if your used commercial brewing equipment is in good condition, it won’t affect your brewing at all and can be considered an 2015年9月25日 production equipment In table 1 there Continuous increasing of production capacity along with simultaneously reducing of production costs and maintains quality of the product at least the IMPACT OF PRODUCTION EQUIPMENT SELECTION ON PRODUCTION COSTS Note: The total product cost in cell H4 on the Costing sheet is the same as the product cost of the manufactured stock item that is included in column H on the StockCode sheet The Costing sheet can therefore be used to view a detailed breakdown of all the cost components that are included in the product cost of any manufactured stock itemProduct Cost Template Excel SkillsDownload Table Coefficients and correlations for estimation of the purchased equipment costs from publication: Cost Engineering Techniques and Their Applicability for Cost Estimation of Organic Coefficients and correlations for estimation of the purchased equipment
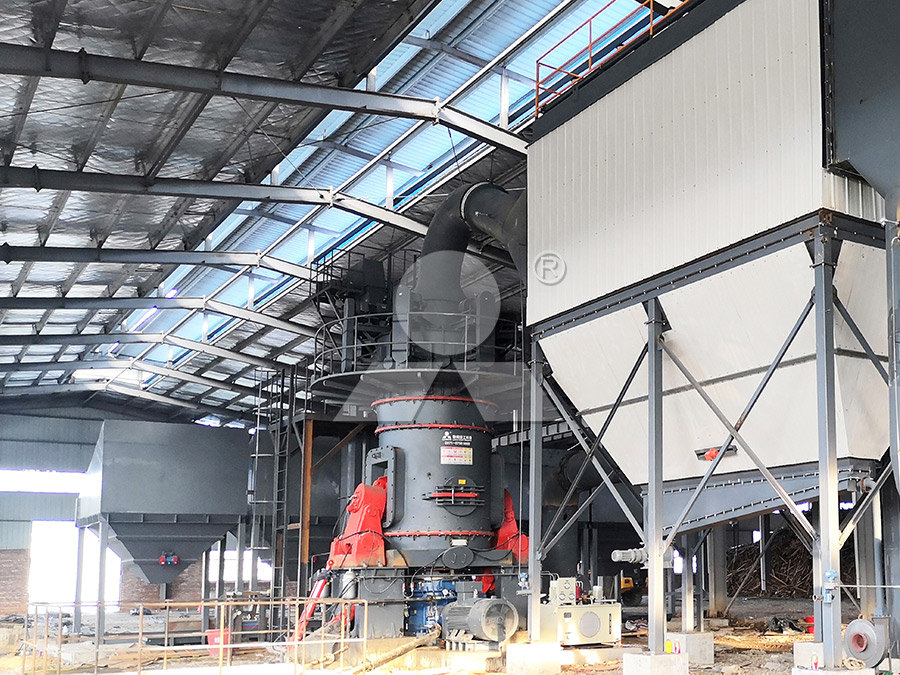
Cost of Production Report: Unraveling the Cost of Production
2024年6月24日 A Cost of Production Report and varnish used in making a table 2 Direct Labor: It accounts for the wages paid to workers who are directly involved in the manufacturing process For instance, A cosmetic company might allocate the cost of shared packaging equipment to various makeup products based on usage 72024年6月13日 3 Analyzing Materials, Labor, and Overhead Expenses One of the most important aspects of running a business is understanding the cost of production This is the total amount of money that it takes to produce the goods or services that you sell to your customers The cost of production can be divided into two main categories: direct costs and indirect costsCost of Production: How to Calculate and Report the Cost of 2024年6月24日 The cost per unit includes all costs associated with production, delivery, marketing, sales, warehousing, management, etc per unit of the product You can add new rows in the Fixed Cost and Variable Cost table to insert new costs without changing the formula Rightclick on the 13th row on the leftmost buttonHow to Calculate Cost per Unit in Excel (With Easy Steps)2023年4月25日 To calculate product costs, you’ll use the following equation: Direct labor + direct material + overhead = Product costs To break this down into a perunit cost, then use this formula: Product costs (the answer from the previous equation) divided by the number of units produced = Perunit cost Let’s apply this formula using a practical What is product cost and how to calculate (with example)
.jpg)
Cost of production with the example of calculation in Excel
Several versions of the calculation of the cost of production in the tables, samples of which can be downloaded free of charge The costs of maintaining equipment – 5% from basic salary The general expenses – 9% from the average basic wage The overhead costs – 2024年6月2日 The variable cost of production is a constant When the manufacturing line turns on equipment and ramps up production, The table below shows how the variable costs change as the Variable Cost: What It Is and How to Calculate It InvestopediaFixed production overhead costs are expenses incurred by a business that do not vary with changes in production levels or output These costs are associated with the production process but remain constant within a certain range of activity, regardless of how much the business produces They are essential in accounting for determining the total cost []Understanding Fixed Production Overhead Costs: A AccountendAccurate and practical production rate estimates are crucial for an accurate forecast of contract completion time As costs of highway projects increase with time, the importance of estimating highway construction contract time has increased significantly,Effective Production Rate Estimation Using Construction Daily