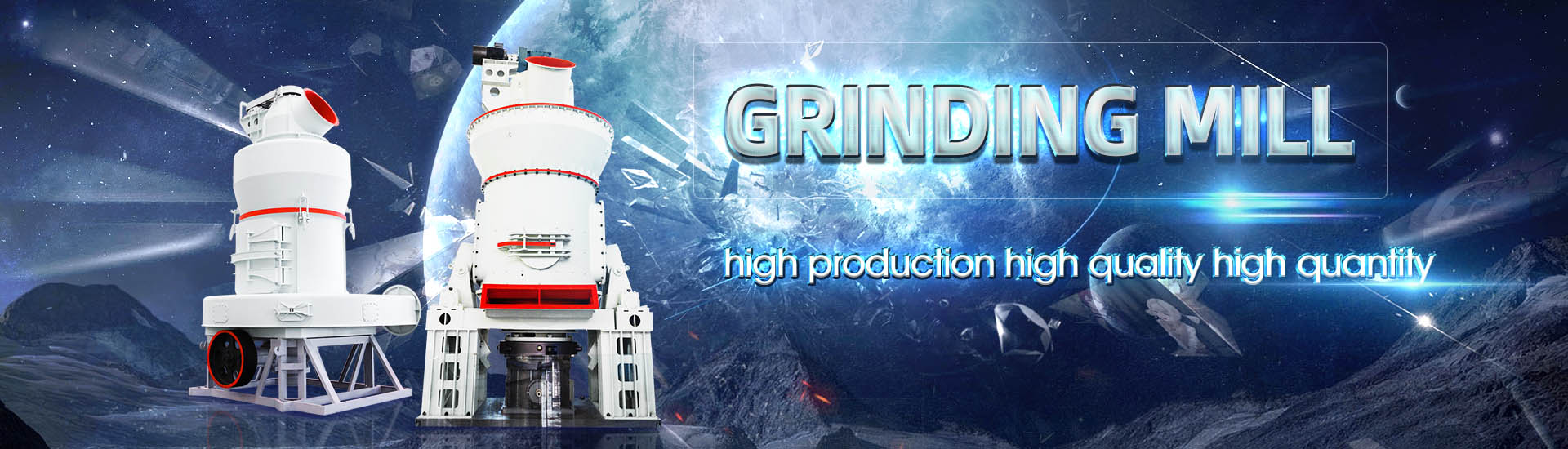
How to discharge slag from submerged arc furnace
.jpg)
Basic parameters in the operation and design of
2018年5月31日 Slag reduction and viscosity are closely related in the practical operation of a submerged arc furnace for ferromanganese (FeMn) productionAfter a short summary of the historical milestones of the submerged arc furnace, the paper will highlight different applications and their specific smelting furnace requirements in the non Rectangular furnace design and revolutionary DCslag cleaning A case from practical furnace operation is presented, showing how the furnace dimensioning and design affect the furnace efficiency and hence the specific energy consumption Possibilities for further improvement of furnace efficiency Basic parameters in the operation and design of 2021年9月3日 A computational fluid dynamics (CFD) method is proposed to analyze the operation of a submerged electric arc furnace (SAF) used in ferronickel productionThreedimensional computational fluid dynamics analysis of an
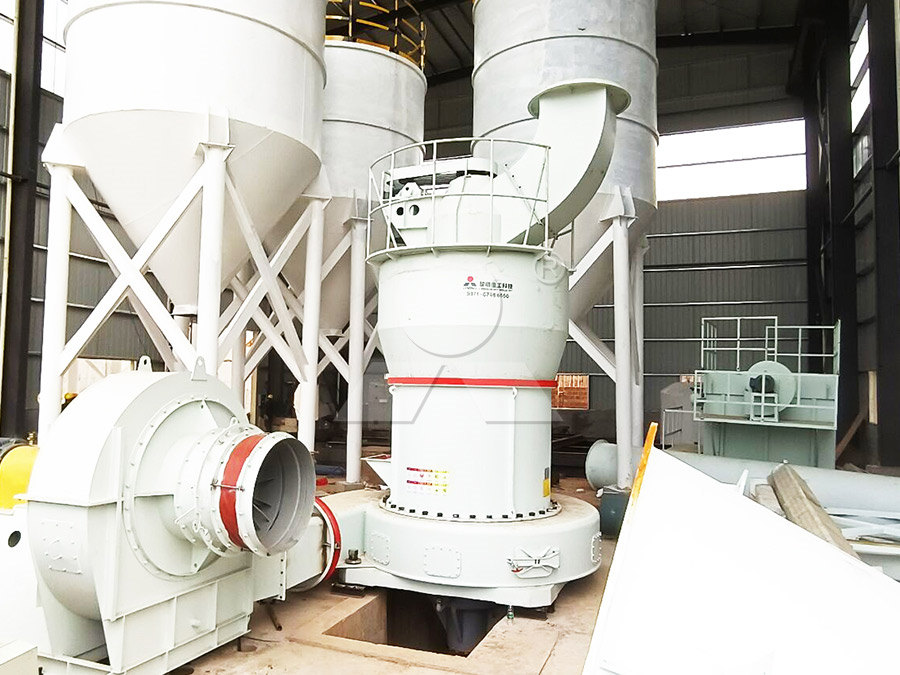
The submerged arc furnace (SAF) State of the art in metal recovery
enhanced slag cleaning process via electromagnetic slag stirring Proof of Principle at IME • Slag charged liquid from TBRC • Reactor volume 250L • 6 kW magnetic fieldIn this present work we present a model for the tapping of the submerged arc furnaces Using the model the ef fects of furnace crater pressure, metal height and permeability of the different Modelling the Tapping Process in Submerged Arc Furnaces Used 2022年2月3日 Effective water sidewall cooling, together with the efficiency of the heat dissipating conductive refractories, lowers the temperature of the lining below that of the molten materials This causes a layer of slag and process An Overview of Submerged Arc Furnaces Tapping The main function of the furnace is the reduction of the matte and metal level in the slag Depending on the upstream process, the slag is either liquidcharged via launders into the THE SUBMERGED ARC FURNACE ( SAF ) STATE OF ART IN METAL
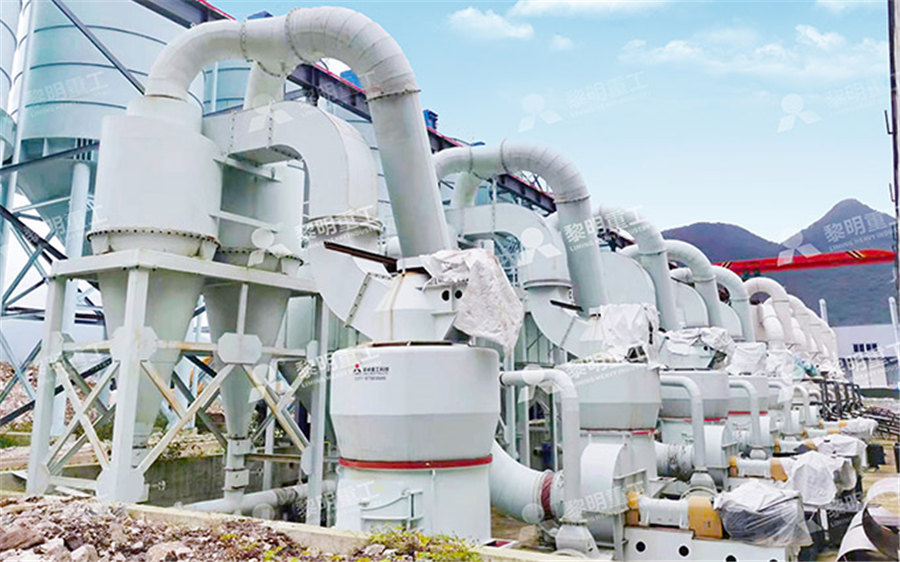
An Indepth Analysis on Submerged Arc Furnace for Metallurgy
2024年10月14日 Submerged arc furnace (SAF) play a fundamental role in the metallurgical industry Whether you are smelting, or purifying metal alloys, SAF guarantees efficiency and reliability In this guide, you will find all information you need about these furnace – from parts, working principle to practical applications Let’s dive right in: []2024年1月1日 Since then, opentype submerged arc furnace and semiclosed submerged arc furnace with lowsmoking hood have been adopted one after another, and the capacity of electric furnace has been expanded After the Second World War, Elekm closed furnace and Demag closed furnace were invented by Norway and Federal Germany successivelySubmerged Arc Furnace SpringerLinkThe submerged arc furnace (SAF) State of the art in metal recovery from nonferrous slag Bernd Friedrich 1 , Michael Kalisch 2 , David Friedmann 1 , Rolf Degel 2The submerged arc furnace (SAF) State of the art in metal 2024年6月15日 Steel, often hailed as the backbone of modern civilization, is the essential material that shapes our world Its multifaceted applications in construction, infrastructure, machinery, and transportation are foundational to global progress [1, 2]Electric arc furnace (EAF) steelmaking is the manufacture of steel from direct reduced iron (DRI) or scrap melted by A review of simulation and numerical modeling of electric arc furnace
.jpg)
The Working Principle Process of The Submerged Arc Furnace
2024年8月3日 Customized metallurgical machinery and equipment range: Electric Arc Furnace, Submerged Arc Furnace, LF Refining Furnace, Vacuum Furnace, Induction Furnace, Dust Remove System, Water Treatment Equipment, etc Providing the most advanced equipment integration services, metallurgical equipment can be customized according to different needs 2021年9月3日 A computational fluid dynamics (CFD) method is proposed to analyze the operation of a submerged electric arc furnace (SAF) used in ferronickel production A threedimensional mathematical model Threedimensional computational fluid dynamics analysis of For a threephase furnace, the furnace reactance X in m is defined as follows: [8] where Q is the reactive furnace power in kVAr, measured on the primary side of the furnace transformers, excluding the load of capacitor banks, and I is the electrode current in kA Whereas the furnace load is depending on the operatingBasic parameters in the operation and design of submerged arc The Metso Outotec Submerged Arc Furnace (SAF) is a closedtype, environmentally friendly, and energyefficient solution for ferrochrome, ferromanganese, silicomanganese, ferronickel, ilmenite (titanium dioxide slag), and titanomagnetite applications It offers low raw material consumption, high metal recovery, and low CO2 and dust emissionsMetso Outotec SAF Smelting
.jpg)
Schematic of a submerged arc furnace for production of
Ferroalloys are mostly produced in submerged arc furnaces (SAF) during carbothermic reduction of oxide raw materials at high temperatures, where the main smelting products are molten metal and slagadvanced submerged arc furnaces make use of software controllers The DC application for submerged arc furnace technology shows worldwide an increasing market share in niche areas especially in some ferroalloys, slag cleaning and TiO2 production units Nevertheless, the majority of submerged arc furnaces are and will remain ACtechnologybasedNew Trends in Submerged Arc Furnace TechnologyHow does a submerged arc furnace work: An electric current is passed through a conductive material reached inside the furnace produce a specific alloy or metal Skip to content The tapping process requires careful control of the flow of molten metal and slag out of the furnace The metal is collected in ladles or molds, How Does A Submerged Arc Furnace Work Hani Metallurgy2022年2月3日 A submerged arc furnace (SAF) is generally used in the production of ferroalloys (referred to as metal in this study) Viable production of ferroalloys requires a consistent tappingTapping process where metal and slag are extracted from the furnace The tapping flowMetal and Slag Extraction from Different Zones of a Submerged Arc
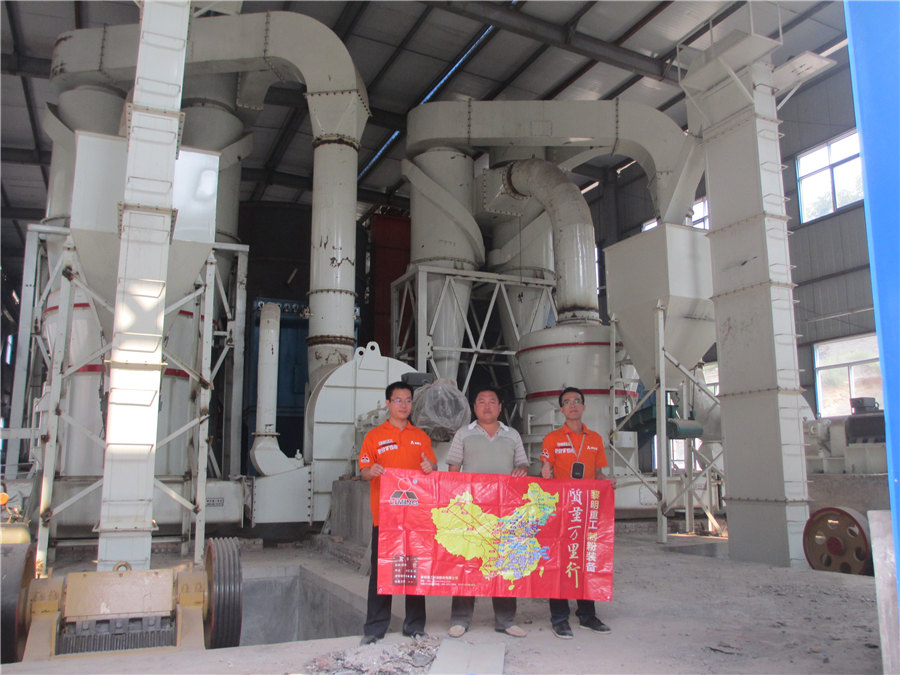
Electric Arc Furnace 101: A Complete Guide for
2024年9月30日 4 Submerged Electric Arc Furnace (SAF) In a submerged arc furnace, the electrodes are immersed directly into the material that needs to be smelted You apply this furnace in a way that it is mainly used in the reduction Discover the ultimate SAF Submerged Electric ARC Furnace manufacturer short net, water cooling system, smoke exhaust system, dust removal system, electrode shell, electrode pressure discharge and lifting system, feeding and unloading system silicomanganese, ferroniobium, and titanium iron ore (TiO2 slag) Additionally, SAFs offer SAF Submerged Electric ARC Furnace Manufacturer/Supplier2013年5月15日 DC Electric Arc Furnace satyendra; May 15, 2013; 3 Comments ; Ac arc furnace, anode, cathode, Conductive bottom, DC arc furnace, electrode, refractories, DC Electric Arc Furnace DC (direct current) electric arc furnace (EAF) is a furnace for primary steelmaking which represents a different concept in the designs of arc furnacesDC Electric Arc Furnace IspatGuru2004年1月1日 Ferrosilicon production is based on the carbothermal reduction of silica and iron oxide in submerged electric arc furnaces The reducing process of iron oxide and silicon oxide is carried out by (PDF) THE BEHAVIOUR OF COKE IN SUBMERGED ARC FURNACE
.jpg)
Dynamic Current and Power Distributions in a Submerged Arc Furnace
2019年2月10日 The current distribution in the submerged arc furnace is critical to good operation in the silicon metal production process Phase current or resistance are among the most important control parameters, but for modern silicon metal or ferrosilicon furnaces, there is no mechanism to measure the actual current distribution 2020年7月1日 Removal of zinc from submerged arc furnace flue gas wash water using steel slag with polyacrylamide The aim of this research was to investigate zinc removal from submerged arc furnace flue gas wash water with steel slag and polymer treatment The amounts of impurities such as zinc in the discharge water is regulatedRemoval of zinc from submerged arc furnace flue gas wash 2018年6月9日 The amount of slag per ton of SiMn is mainly determined by the ore/slag ratio Increasing share of FeMn slag at the expense of Mn ore leads to larger slag/metal ratio in the production process of SiMn High volume of slag leads to an increased consumption of energy and probably to higher losses of Mn inclusions in the final slagProduction of SilicoManganese in a Submerged Arc FurnaceThe Submergedarc furnace for phosphorus production is a particular subtype of electric arc furnace used to produce phosphorus and other products usually once per day Slag, however, is continuously tapped through two alternating, water Submergedarc furnace for phosphorus production Wikipedia
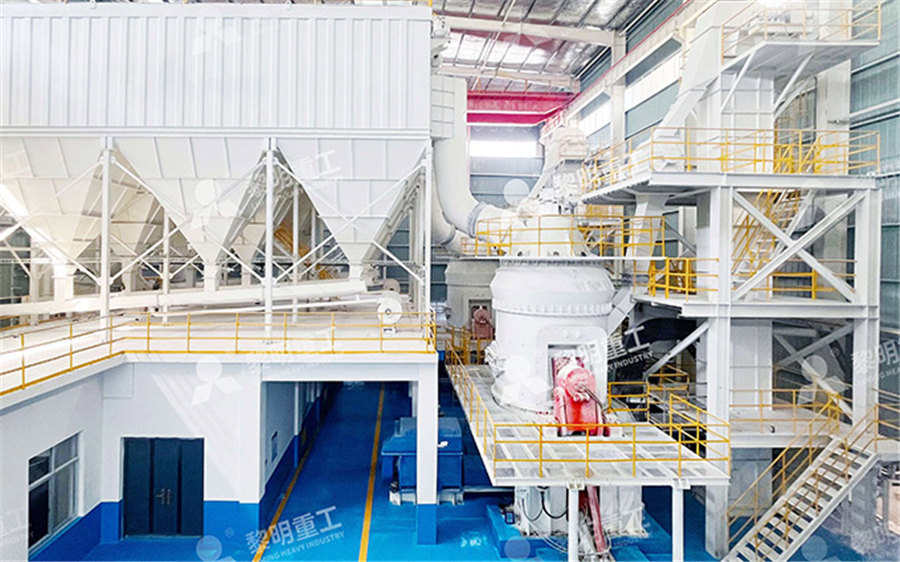
Modelling the Tapping Process in Submerged Arc Furnaces Used
Permeability of the Packed Beds in the Furnace Excavations of the submerged arc furnaces3–5) show that inside the furnaces there are different zones with different physical properties Due to different chemical reactions, uneven heat distribution, softening and melting of charge parWhenever the ores contain only small amounts of metal (eg in nickel production) or prereduced material with a high degree of metallization (DRI) is used or minerals are to be (re)melted or slags are to be treated, the SAF is designed as a “slag furnace”: with a slag bath height of about 1,000 mm to 1,500 mm, with electrodes immersed in the slag and the use of the slag (and not the The SAF Homepage der Bluemetals GmbH, SAF expertsSuch a furnace is known as a submerged arc furnace, because the electrode tips are buried in the slag/charge, and arcing occurs through the slag, between the matte and the electrode The casing and casing fins of the electrode melt the Electric arc furnace Wikipedia2021年9月10日 The submerged arc furnace has been widely used in the ferroalloy industry and has great energy saving potential [] In the ferrochrome production, ore is smelted by a threephase submerged arc furnace [] Friedrich et al [] indicated that the inner part of the submerged arc furnace consists of the selfbaked Soderberg electrodes, arc, furnace charge, slag, alloy, Modeling on Reduction Reaction of Metal Oxides for Submerged Arc
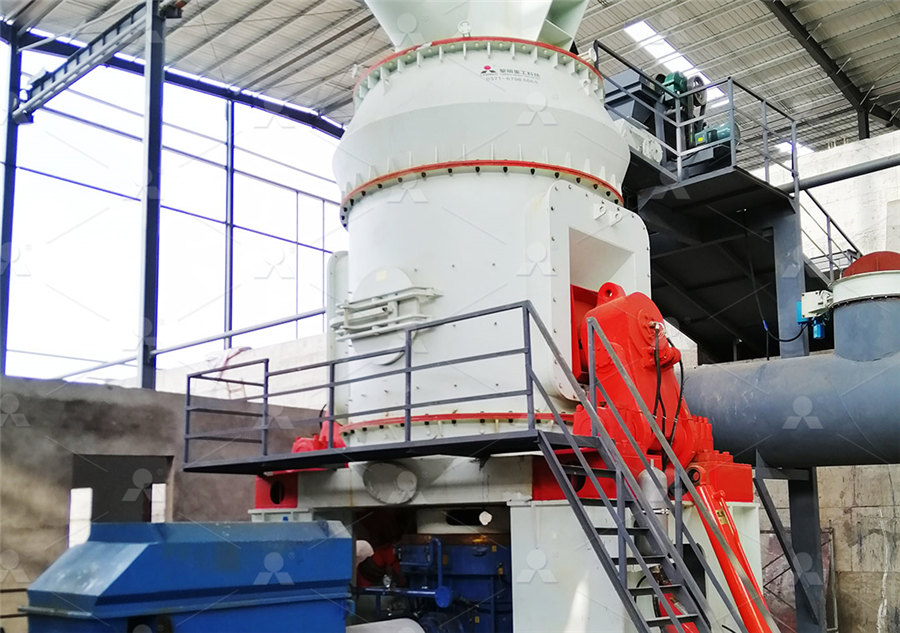
The Use of Submerged Arc Furnace (SAF) as a Robust
2020年5月14日 Firstly, a submerged arc furnace (SAF) and an electric resistance furnace (ERF) were used to melt MSWI bottom ash obtained from a Dutch MSWI plant at 1500 and 1400 °C, respectivelyFerrochrome slag (FCS) is a byproduct of ferrochrome industries and is produced during the extraction of ferrochrome from chromite ore The chemical composition of FCS comprises of 27–33% SiO2 Schematic diagram of the reaction zones in submerged arc furnace 2017年9月6日 1 Introduction Nickel is of particular economic consequence in the production of stainless steels, superalloys and fuel cells [1,2]The principal nickel production route comprises the reductive smelting of calcine in electric submerged arc furnaces (EAFs); calcine is the yield of reductive roasting of nickelferrous lateritic ores in rotary kiln furnaces [3–5]Pragmatic analysis of the electric submerged arc furnace 2010年7月30日 This article presents a process model of a phosphorusproducing, submerged arc furnace The model successfully incorporates accurate, multifield thermodynamic, kinetic, and industrial data with computational flow dynamic calculations and thus further unifies the sciences of kinetics and equilibrium thermodynamics The model is structurally threedimensional and Process Modeling and Optimization of a Submerged Arc Furnace
.jpg)
Different zones of a FeMn submerged arc furnace [2]
In principle the computational fluid dynamics (CFD) model for submerged arc furnace can handle fluid flow, heat and mass transfer for furnace gases, molten slag and alloy, and the solid feedIn principle the computational fluid dynamics (CFD) model for submerged arc furnace can handle fluid flow, heat and mass transfer for furnace gases, molten slag and alloy, and the solid feedA schematic illustration of submerged arc furnace for chromite 2004年1月1日 Furnace wall cooling methods are related to the requirements resulting from specific furnace process conditions, including slag and metal compositions, as well as arc and bath powerFurnace technology for ferronickel production by the chemistry of the slag in the coke bed zone Therefore, the proper amount of slag flux is very important for SAF operation to produce FeMn In order to understand the chemical equilibration between the liquid slag and the liquid FeMn in the coke bed zone, accurate thermodynamic properties of the slag and the liquid FeMn phase are necessaryFerromanganese Production in a Submerged Arc Furnace
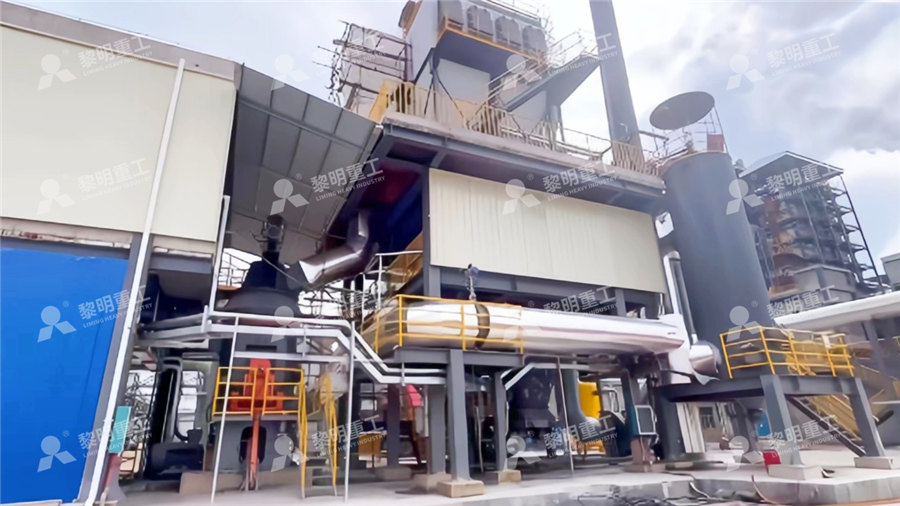
(PDF) Process Zones Observed in a 48 MVA Submerged Arc Furnace
Process Zones Observed in a 48 MVA Submerged Arc Furnace Producing Silicomanganese According to the OreBased Process Joalet Dalene Steenkamp, Johan Petrus Gous, Wiebke Grote, Robert Cromarty and Helgard Johan Gous Abstract Excavation of industrialscale furnaces allows for the systematic study of reaction sequences by identifying the different reaction Unlike the submerged arc furnace, the PLASMARC furnace is an open bath process Consequently, compared to the submerged arc furnace, the energy losses are far higher; typically higher by some 1000 kWhper ton ofchargechromiumThis higher energy consumption is compensated for by the use offines, higher chromium yield, the ability to remelt metal DC Arc Furnace Technology Applied to Smelting Applications2023年3月6日 This work presents a process model developed based on mass and energy conservation to assess high carbon ferrochrome production from cradle to gate through four supply routes: (1) a conventional submerged arc furnace (SAF), (2) a closed submerged arc furnace with preheating (CSAF+PH), (3) a closed submerged arc furnace with 60% Energy Consumption and Greenhouse Gas Emissions of High 2022年1月18日 Ferromanganese alloy is produced by the carbothermal reduction of MnO2 and Mn2O3 ores at high temperature using a submerged arc furnace (SAF) The production rate and chemical composition of liquid ferromanganese alloy in the SAF process are highly dependent on slag flux composition, coke amount, and temperature controlled by electric power In the Ferromanganese Production in a Submerged Arc Furnace
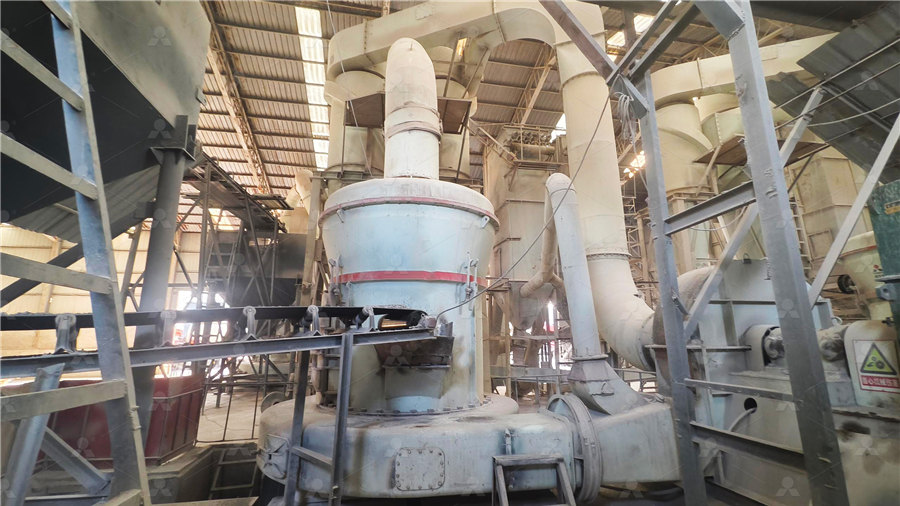
(PDF) The taphole key to furnace performance ResearchGate
2014年5月27日 The critical importance of taphole design and management for furnace performance and longevity is explored through examining some of the specific matte, metal, and slag tapping requirements of 2020年7月1日 The aim of this research was to investigate zinc removal from submerged arc furnace flue gas wash water with steel slag and polymer treatment The current treatment for the submerged arc furnace flue gas wash water is treatment with polymer only which aids in the settling of particulate zinc However, in this research enhanced removal of zinc by also Removal of zinc from submerged arc furnace flue gas wash 2018年5月1日 Electric arc furnace slag (EAF) has the potential to be reutilized as an alternative to stone material, The fabrication was achieved using the submerged direct current (DC) arcdischarge method employing two graphite electrodes, one of which was filled with a mixture of carbon powder, TiO2, submerged arc furnace: Topics by SciencegovFigure 1: Schematic of submerged arc furnace used for Silicon production In this paper a 3D CFD multiphase model for the tapping process of silicon melt from the submerged arc furnace is proposed Our goal is to investigate how different parameters such as high gas pressure in the crater zone and a low permeability situation on the furnaceMODELING THE TAPPING OF SILICON MELT FROM THE SUBMERGED ARC