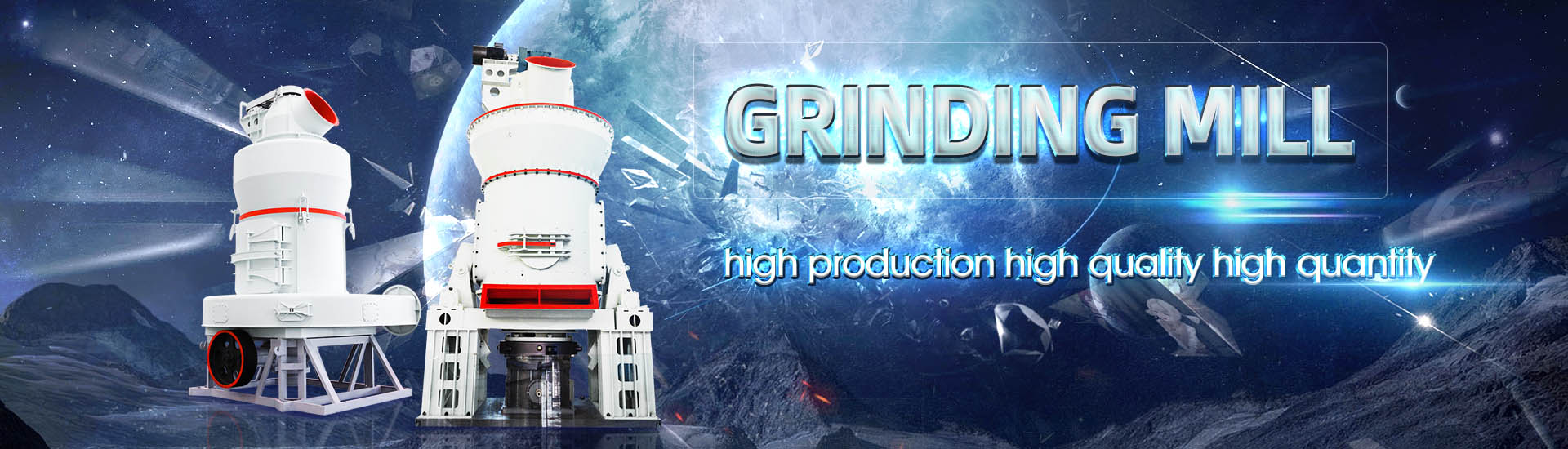
Does the speed of the ore mill affect the crushing ratio
.jpg)
Crushing characteristics and performance evaluation of iron ore in
2023年12月1日 The effects of the eccentric speed on the residence time of particles in the crushing chamber can be indicated by its influence on the number of circulations, while the The current crushing setup is operating at 15 tonnes per hour which is low compared to their production rate such that ore from the ground is piling up This paper addresses the critical Design of a crushing system that improves the crushing efficiency Since the crushing plants operate under harsh conditions and involve very abrasive material, multiple factors can influence their performance This paper assesses a number of factors affecting the performance of the crushing plant (PDF) Field monitoring and performance evaluation of In most mills the crushing plant does not run for 24 h a day, as hoisting and transport of ore is usually carried out on two shifts only, the other shift being used for drilling and blasting The Crushing Plant an overview ScienceDirect Topics
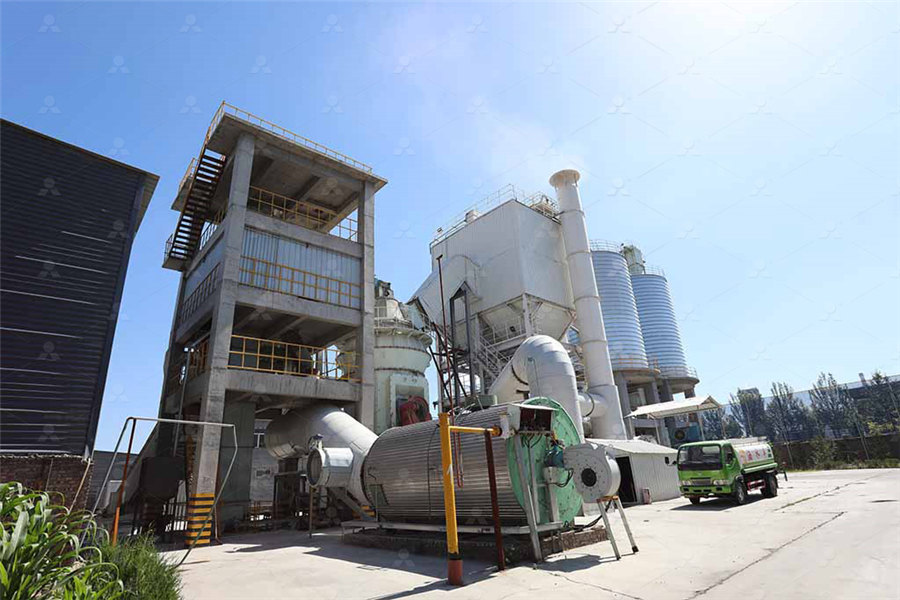
THE EFFECTS OF PROCESS VARIABLES ON THE GRINDING OF
2020年10月13日 The results of the analyses clearly show that using a sieve of +180µm and its bottom180µm, the best time for grinding 05kg of Itakpe iron ore with 3kg of grinding media 2023年6月3日 (4) The operation variable makes the crusher in the best working conditions by adjusting, including ore feeding speed and ore discharge port size Ore feeding speed is MeasurementControl for Crushing and Screening Process2023年6月30日 This includes improving the crushing chamber, working bodies, and drive designs, increasing the conditions for removing the crushed ore from the outlet, ensuring a continuous supply of raw materials, increasing the filling Modeling and Improving the Efficiency of Crushing 2023年7月22日 The ore crushing process includes four types: ore coarse crushing, ore medium crushing, ore fine crushing, and ore superfine crushing Ore coarse crushing is a process of Ore Crushing SpringerLink
.jpg)
The Importance of Primary Crushing in Mill Feed Size Optimization
copper with an ore:waste ratio of 1 With currently outlined ore reserves, the mine is expected to operate until the first quarter of 2009 The concentrator treats approximately 135,000 tpd through five parallel grinding lines These five grinding lines consist of two fully autogenous2015年7月29日 As you add ore to the mill you are also adding WATER and changing density which affects the slurry rheology and workings of the grinding action inside that 911 Metallurgist is a trusted resource for practical insights, solutions, and support in mineral processing engineering, helping industry professionals succeed with proven expertise Effect of Water Density on Effect of Water Density on Grinding Mill 911Metallurgist2023年8月5日 Under the same roll surface pressure, when the roll surface speed is increased to a certain amount, the uniformity coefficient of the intermediate material increases, the particle size distribution is more concentrated, the crushing ratio increases, and the product particle size becomes finer, but it affects the uniformity coefficient of the Factors affecting the particle size of the highpressure roller mill2017年10月26日 The following are factors that have been investigated and applied in conventional ball milling in order to maximize grinding efficiency: a) Mill Geometry and Speed – Bond (1954) observed grinding efficiency to be a function of ball mill diameter, and established empirical relationships for recommended media size and mill speed that take this factor into Factors Affecting Ball Mill Grinding Efficiency
.jpg)
Crushing Wheel Create Wiki Fandom
Crushing Wheels are the more advanced version of the Millstone It applies Crushing recipes to any items inserted from the direction they are spinning away from 1) First, arrange the crafter as follows Note that direction of the arrows (black lines) It is critical that these are in the right direction or it may not work Use the wrench to rotate them as needed The central column 2023年2月21日 Discover everything you need to know about jaw crushing machines, from the various types such as single and double toggle, hydraulic and portable models, to their working principles, advantages, and disadvantages This comprehensive guide also provides expert tips on maintenance and selecting the right machine for your specific applicationThe Ultimate Guide to Jaw Crushing Machines: Types More Tips 2023年10月30日 The selection and design of crushing equipment in the mineral processing industry are influenced by several key factors, all of which are critical for achieving efficient and effective ore processing Chief among these factors is the material's inherent characteristics The hardness, abrasiveness, moisture content, and size distribution of the ore significantly impact The selection and design of Crushing equipment Performance 2016年6月6日 When buildup of these materials does occur, pebble crushing can improve mill throughput even more dramatically than when the critically sized fraction results purely from a breakage rate deficit alone For these ore types, a pebblecrushing circuit is tin imperative for efficient circuit operationSAG Mill Grinding Circuit Design 911Metallurgist
.jpg)
Physical Bauxite Processing: Crushing and Grinding of Bauxite
2022年1月23日 Additionally, when the downstream process involved grinding mills, the fines created from highspeed crushing circuit were a and not based solely on the fact that this is a bauxite mine versus a mine for some other type of ore A crusher does not know what Regular entry into the mill will therefore affect the 2022年1月1日 The size of grinding media is the primary factor that affects the overall milling efficiency of a ball mill (eg power consumption and particle size breakage)Effect of grinding media on the milling efficiency of a ball mill2024年7月17日 The airflow dynamics within hammer mills’ crushing chambers significantly affect material crushing and screening Understanding the crushing mechanism necessitates studying the airflow distribution Using a selfbuilt crushing test platform and computational fluid dynamics (CFD) simulations, we investigated the impact of screen aperture size, rotor speed, hammer Numerical Simulation and Analysis of the Airflow Field in the Crushing 2023年7月20日 (2) Various working parameters of grinding mill, including fraction of critical speed for grinding mill, filling rate for grinding mill, grinding concentration, grinding cycle load, etc (3) And grinding material properties, including ore grindability, feeding particle size, etc Huge energy and steel consumption in ore grinding process greatly affect the subsequent separation Ore Grinding SpringerLink
.jpg)
Effect of ball and feed particle size distribution on
2018年2月1日 In another study to investigate ball size distribution on ball mill efficiency by Hlabangana et al [50] using the attainable region technique on a silica ore by dry milling, a threeball mix of 2019年8月14日 • Central discharge ball mill: the inlet of medium unloading ball mill is at both ends, and the outlet is in the middle of the ball mill 4 According to the ore discharge of ball mill: • Overflow ball mill: Discharge the ore through hollow shaft • Grid ball mill: Discharge the ore through the plaid plateThe Ultimate Guide to Ball Mills Miningpedia2020年2月18日 Speed rate refers to the ratio of the speed of the mill to the critical speed, where the critical speed is n c = 30 / R In practice, the speed rate of the SAG mill is generally 65% to 80% Therefore, in the experiment, the speed was set to vary in 50% and 90% of the critical speed (128–164 rad/s) for the crossover test as shown in Table 2 Optimal Speed Control for a SemiAutogenous Mill Based on2020年11月13日 The speed of ball mill directly affects the motion state of steel balls and ores in the ball mill When the speed is too slow, the steel balls and ore will slide down without rising high, and the crushing effect will be small; when the speed is too fast, the grinding medium will attach to the inner wall of the ball mill and rotateFactors that Affect Grinding Efficiency of Your Ball Mill
.jpg)
23: Milling of Wheat Chemistry LibreTexts
Bran and germ are sifted out, and the coarse particles are rolled, sifted, and purified again This separation of germ and bran from the endosperm is an important goal of the miller It is done to improve doughmaking characteristics and colour As well, the germ contains oil and can affect keeping qualities of the flour2023年4月23日 ciency include mill design, liner design, mill speed, charge ratio, and grinding media properties The authors also indi cated that circuit efficiency is determined by how well the power applied (PDF) Grinding Media in Ball MillsA Review ResearchGate1 Grindability: The grindability of the ore affects the efficiency of the grinding mill Harder ores require more energy and longer grinding times, which can impact the mill's performance and operational costs 2 Media andliner Wear: The condition of the grinding media and liners affects the mill's efficiencyUnderstanding the operation of grinding mills in the mining and 2016年2月26日 The hammer mill is the best known and by far the most widely used crushing device employing the impact principle of breaking and grinding stone Thus far we 911 Metallurgist is a trusted resource for practical insights, solutions, and support in mineral processing engineering, helping industry professionals succeed with proven expertise Hammer Mill Crusher Grinder 911Metallurgist
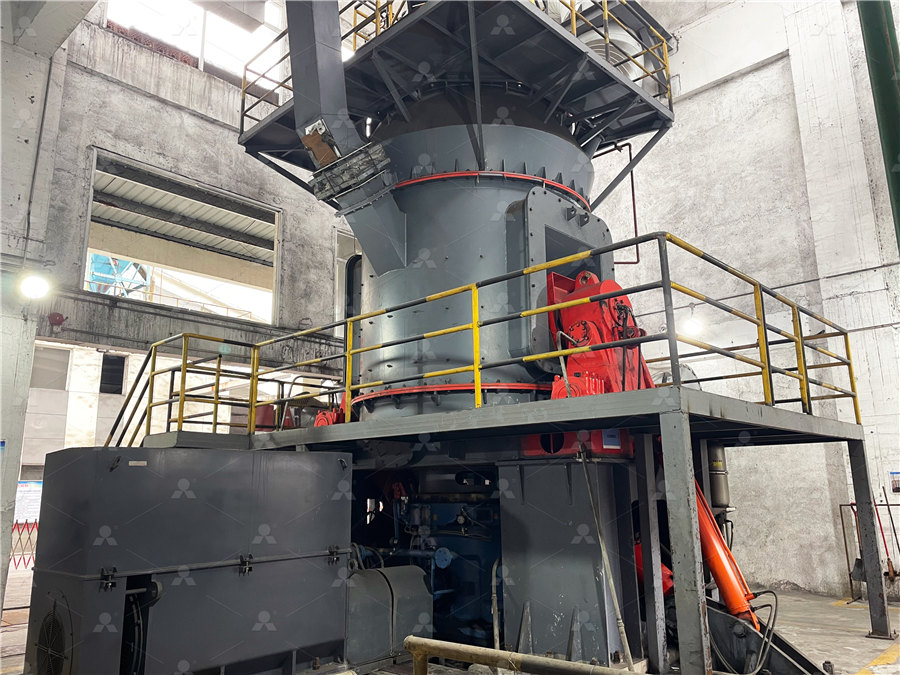
Modeling and Improving the Efficiency of Crushing
2023年6月30日 affect the crushing process [5] Crusher modeling is hardly achievable without identifying the basic parameters of crushers; this is an essential basis for any model [ 6 ]mining Due to different crushing chamber designs these machines can either prepare materials for downstream processing with a high crushing ratio, or reduce overburden to a size suitable for belt conveying with a low crushing ratio (Smith, 2013) 252: Cone crusherDesign of a crushing system that improves the crushing efficiency 2018年6月1日 Impact crushing quick facts 1 The faster the speed, the finer the gradation 2 Setting has some effect on gradation and throughput, but speed is by far the most important factor 3 Rotor penetration is critical for best The basics of crushing Pit Quarry2021年6月29日 The aim of this work was to observe the impact of the milling technique employed by the DESI 11 disintegrator on the properties of fly ash This type of mill is a highspeed pin mill with two Effects of Mill Speed and Air Classifier Speed on Performance of
.jpg)
Crushing and Grinding Wet Sticky Ore 911Metallurgist
2016年5月10日 In the handling of wet, sticky ores such as encountered in tropical areas having distinct dry and rainy seasons, the crushing plant is a section of the mill which must be planned very carefully Unless this is done, crushing becomes a constant source of trouble resulting in lost production and high milling cost In some areas rainfall is high for prolonged periodsThe Millstone is a more basic equivalent of the Crushing Wheels, and is most likely the first of the two that the Player will construct It is capable of applying milling recipes to any valid items inserted from above There are 2 variables that effect the processing speed of the Millstone: RPM and recipe duration The recipe duration is a number assigned to each recipe to determine is Millstone Create Wiki FandomDistribution of types of ore crushed Blend type Crushed ore (%) Spec CO BYO BCO 29 42 10 19 Ore type distribution (%) BO YO CO LGO BYO BCO 14 6 1 5 60 1 5 0 13 73 2 12 10 8 6 9 3 1 83 6 0 11 3 68 The best crushing performance is respectively obtained (PDF) Field monitoring and performance evaluation of crushing plant 2020年4月30日 Batch loading and the interaction effect of batch loading with impeller speed are significant parameters that affect the quality attributes of the mill Predictive regression models were developed for throughput of the mill, milled product bulk density and milled product tapped density (with an R2 of 0987, 0953, 0995 respectively) to enable their use in downstream Understanding the Effect of Granulation and Milling Process
.jpg)
An Evaluation on the Impact of Ore Fragmented by Blasting on
2022年2月17日 In openpit mines, the blast operation should be effectively optimized, leading to minimization of production costs through the application of specific technical specifications However, there is inadequate information in the literature to link blasting to comminution stages To this end, the effective parameters for the performance of mining unit operations were 2024年5月20日 The ball mill lifts the grinding media by rotation of its horizontal cylindrical part which then falls back impacting the ore particles The grinding action is then achieved by attrition, abrasion, and impact between the ore and the grinding media 3 Spherical media has been commonly used in ball mills; however, different shapes of grinding media have different Effect of grinding media shape on the particle size distribution of 2021年9月15日 Two jaw crusher factory pictures The crusher is a crushing machine used in the processing of metal ores and nonmetallic ores that can crush the mined raw ore into small particles by means of extrusion and 8 Factors That Affect Production Efficiency of 2023年6月30日 The basic method of primary preparation of raw materials is to crush the mined ore Crushing is the first and most accurate overview of the various parameters of the crushing process, eg, how different particle Modeling and Improving the Efficiency of Crushing
.jpg)
Study of the EnergyPower Parameters of the Crushing Process in
2023年3月6日 As experience shows, when one determines the energypower parameters of crushing and grinding processes by using the existing methods, the power of motors used in drives of existing crushers of various types often turns out to be excessive [10, 11]In this case, the drive will operate at a relatively low load (ratio of the power consumed by the working body 2021年8月15日 Several works from the literature have reported applications of process control strategies in the mineral processing industry For example, Wei and Craig (2009) published a survey with qualitative data from process control solutions, and Bouffard (2015) reported quantitative data supporting the benefits of such strategies A series of works (Bouchard et al, A review of modeling and control strategies for cone crushers 2016年6月20日 Speed of travel can be increased by inclining the screening surface If the surface is greatly inclined, the stroke must be short to prevent material sliding over the mesh too quickly Inclination of the surface can keep the mesh holes open more easily Speed of travel Speed of travel has an effect on screening efficiency and capacityOre, Rock Aggregate Screening (Complete Guide)2009年5月1日 In a previous paper [Morrell, S 2008a A method for predicting the specific energy requirement of comminution circuits and assessing their energy utilisation efficiencyPredicting the overall specific energy requirement of crushing,
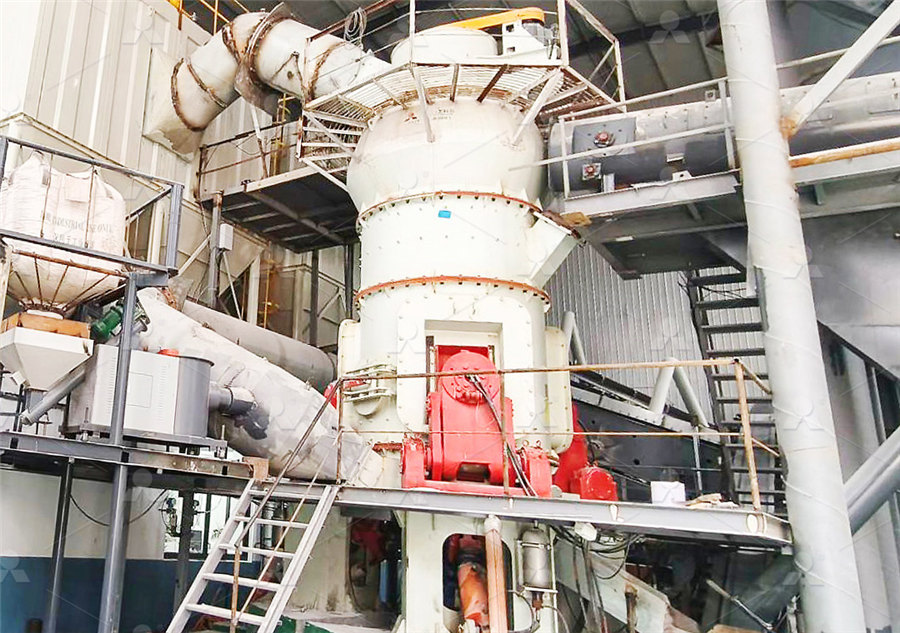
(PDF) Numerical calculation of sugarcane crushing process based
2023年7月1日 When the roller diameter, roller speed, and compression ratio of the milled mixture are 1060 mm, 5 rpm, and 3, the maximum stress and speed of the milled mixture are 1857 MPa and 4536 mm/s2024年4月19日 Compression Crushing: Compression crushing, also known as compressive force, applies a compressive force to the material between two surfaces until it breaksThis way is frequently applied in jaw crushers and cone crushers In jaw crushers, the material is squeezed between the fixed jaw and the moving jawTypes of Crushers Explained: Everything You Need to Know JXSC2020年1月11日 The crushing efficiency is higher than the grinding efficiency, so a crusher can be equipped before grinding Such crusher can be a jaw crusher with a large crushing ratio and an extensive application, or a roll crusher that can increase ore microcracks through lamination crushing Jaw crusher is used to work with ball mill to reduce the feed size5 Ways to Improve the Ball Mill Efficiency FTM2020年6月10日 For this reason, the effect of granulation variables such as liquidtosolid ratio, granulator impeller speed and the amount of binder in the formulation were analyzed(PDF) Understanding the Effect of Granulation and Milling Process