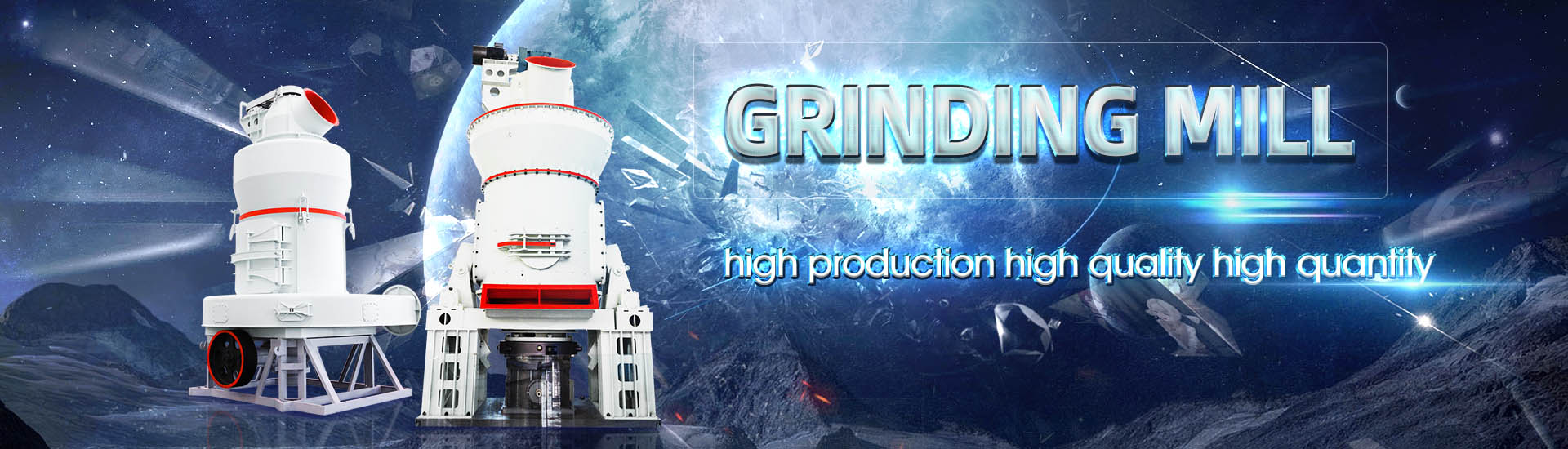
iron oxide grinding process
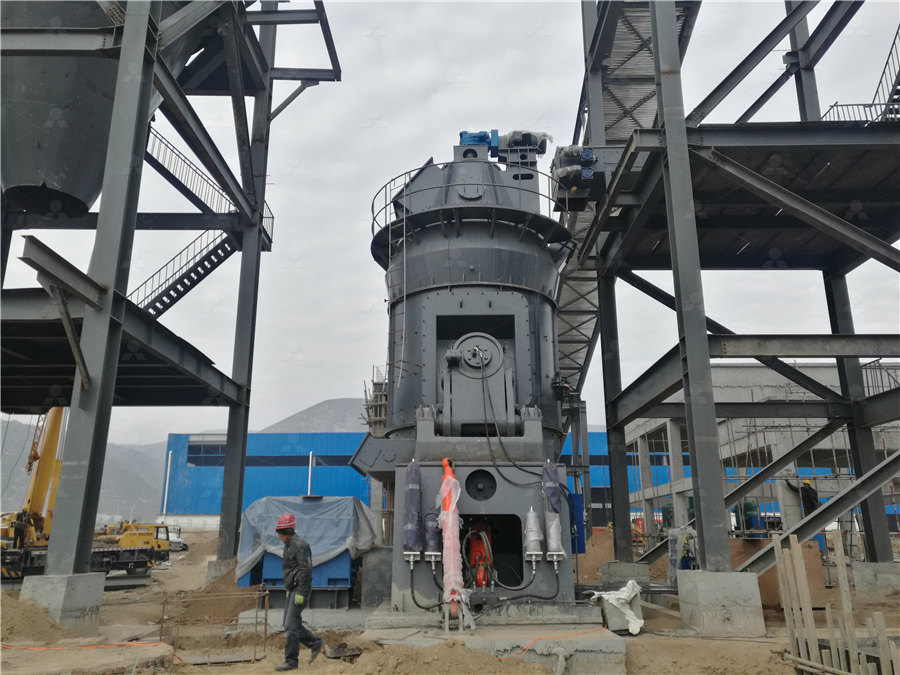
Iron Ore Processing: From Extraction to Manufacturing
2024年4月26日 Iron ore processing is a complex and vital process that transforms raw iron ore into usable steel From exploration and extraction to grinding, beneficiation, and ironmaking, each stage plays a crucial role in 2011年1月1日 Grinding mills typically used in the process include the attrition jet, planetary, oscillating and vibration mills, all of which are classified as highenergy mills Among these Preparation of iron oxide nanoparticles by mechanical milling2020年2月1日 Optimization studies were carried out in the production of γFe2O3 nanoparticles by using coprecipitation method Iron (II) chloride and iron (III) chloride were used as Production of Iron Oxide Nanoparticles by CoPrecipitation 2020年10月1日 This study aims to characterize and then determine the method which allows for a high efficiency and quality for grinding the αFe 2 O 3 red powder into red iron oxide pigment An investigation on optimum grinding system and conditions for
.jpg)
Manufacturing and Properties of Spherical Iron
2023年4月3日 Further processing of these iron oxide powders could enable the production of iron powder for various applications in powder metallurgy For this purpose, a new process route with an ecofriendly hydrogen reduction Iron ore processing refers to the techniques used to extract iron from oolitic iron ores, involving processes such as beneficiation, roasting, and magnetic separation to remove impurities like Iron Ore Processing an overview ScienceDirect Topics2022年1月12日 Comminution tests with a laboratoryscale rod and ball mill of 13 predefined ore types from the Per Geijer iron oxideapatite deposits were conducted The grinding setup refers to the socalled Malmberget method Process Mineralogical Assessment of the Grinding 2018年8月17日 Blends with different iron ore oxides morphologies were subjected to grinding, filtering and pot grate tests on industrial scale trials Results of grinding tests showed the Toward the influence of iron oxide morphology on the grinding
.jpg)
New insights into the dissolution mechanisms of iron oxides and
2024年11月19日 Understanding the microscopic phenomena during iron oxide dissolution is crucial for optimizing industrial processes such as corrosion product removal 1–3 and iron ore For grinding ferrous metals with aluminum oxide wheels, the important chemical reactions usually involve the oxidation of iron and the reaction of the oxide with the abrasive to form the spinel Grinding Processes SpringerLink2022年1月12日 DOI: 101080/2021 Corpus ID: ; Process Mineralogical Assessment of the Grinding Products of the Per Geijer Iron OxideApatite Deposits @article{Krolop2022ProcessMA, title={Process Mineralogical Assessment of the Grinding Products of the Per Geijer Iron OxideApatite Deposits}, author={Patrick Krolop and Kari Process Mineralogical Assessment of the Grinding Products of 2018年4月15日 Preparation and formation mechanism of monodisperse micaceous iron oxide from iron chromium grinding waste Author links open overlay panel Bo Liu a, Shengen Zhang a (NH 4) 2 SO 4 solution can be used to prepare ammonia by ammonia recycling process The obtained iron‑chromium hydroxide precursors were mixed into NaOH solution Preparation and formation mechanism of monodisperse micaceous iron
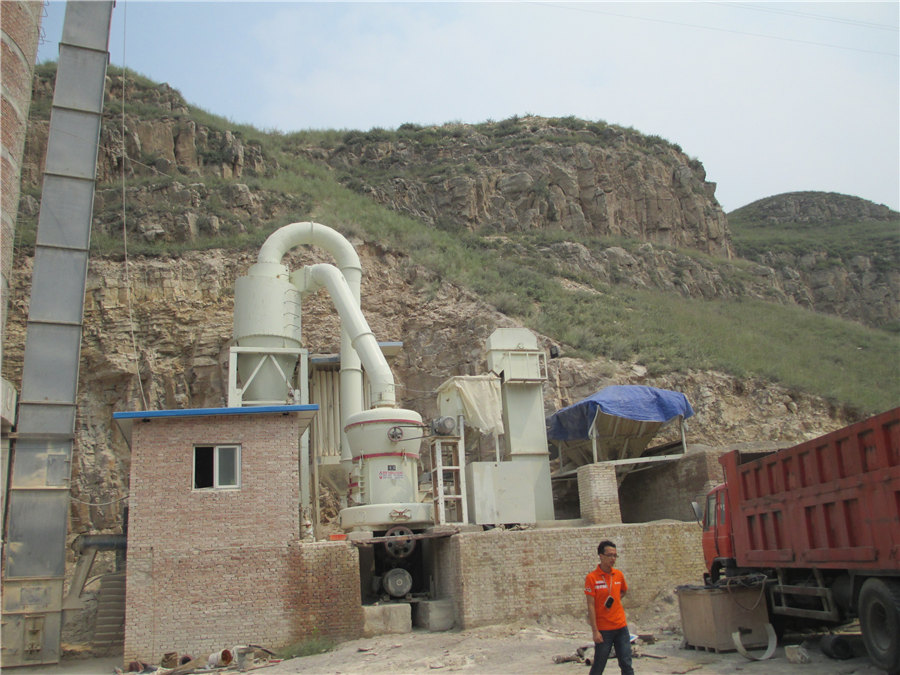
Grinding and Polishing Guide Buehler
2021年11月15日 Grinding should commence with the finest grit size that will establish an initially flat surface and remove During the lapping process, (SiO2) icollidal suspension For certain materials, cerium oxide, chromium 2024年3月20日 Electrochemical production of iron metal can support a decarbonized process for steelmaking Here, we report a lowtemperature, electrochemical cell that consumes lowcost and abundant iron oxide, salt, and water, while producing both iron and the alkaline electrolyte needed for efficient operation of the cell Coproduction of iron, lye, and chlorine leads to a process Electrochemical chloriron process for iron production from iron oxide 2019年11月19日 Overview of the Groveland Mine iron ore beneficiation process, the collector from attaching to the iron oxides, allowing for stage grinding, gravity separation, magnetic separation, and(PDF) Flotation of Iron Ores: A Review ResearchGate2013年2月23日 Recrystallization of iron oxides is essentially a physical process in which smaller particles consolidate into larger ones with the loss of surface energy During the recrystallization of iron oxides, continued growth of iron oxide crystals imparts sufficient strength During the process, the grain growth for hematite starts at around 1100 deg CIntroduction to Iron ore Pellets and Pelletizing processes
.jpg)
Grinding Processes SpringerLink
For grinding ferrous metals with aluminum oxide wheels, the important chemical reactions usually involve the oxidation of iron and the reaction of the oxide with the abrasive to form the spinel FeAl 2 O 4, which is an intermediate compound between the oxidized workpiece metal and aluminum oxide linked to stronger bonding between iron and aluminum oxide2023年11月15日 PDF Iron Ore, Iron Ore Pellets, Direct Reduced Iron )DRI( Pellets, Iron Ore Pellets Market, Pelletizing Process, Sintering, Binder, Induration Find, read and cite all the research you need (PDF) IRON ORE PELLETIZING PROCESS ResearchGateKeywords: micaceous iron oxide (MIO), magnetic separation, belt type high gradient magnetic separator, high gradient magnetic separator, pulsating high gradient magnetic separator 1 Introduction Natural iron oxides occur widely, and are exploited from a variety of deposit types World iron oxide pigment mine production in 2014 is given in Table 1Micaceous iron oxide production by application of magnetic 2023年6月20日 Ultrasonicassisted electrolytic inprocess dressing (ELID) grinding can be used in the highefficiency and highprecision machining of difficulttoprocess materials This paper establishes a prediction model of oxide film thickness growth We conducted ultrasonicvibrationassisted experiments on an electrolytic castironbonded grinding wheel and carried out high Oxide film thickness and composite mechanical properties of an
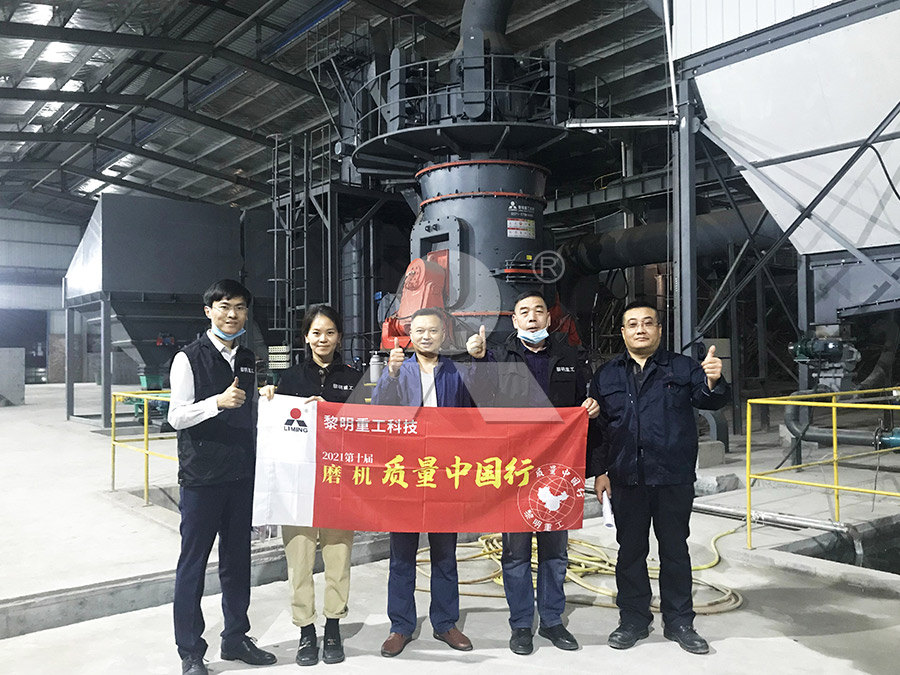
Process for preparing transparent iron oxide pigment dispersions
This invention relates to a process for preparing transparent iron oxide pigment dispersions The dispersions are prepared by milling a mixture of iron oxide pigment and a liquid vehicle in a bead mill containing glass beads as the grinding media The pigment dispersions can be used in the preparation of paints and coatings which exhibit transparent quality and absorb ultraviolet 2018年7月15日 The most important aspect is that iron oxides experience repeated reduction and oxidation whereas inert oxides remain as initial For the different phases of iron oxides, the melting temperature of Fe 3 O 4 is higher than that of Fe 2 O 3 According to the XRD results in Fig 3, the main phase was Fe 3 O 4 after reduction with 10 minRedox reaction induced morphology and microstructure evolution of iron Iron oxides are abundant minerals and are chemical compounds composed of iron and oxygen The best known natural iron oxide is rust Engineered iron oxide constitutes a main component of products in the paint industry, pharmaceutical industry, plastic Iron Oxide Micronization : Jet PulverizerGrinding Process, Table 1 Methodological overview of typical grinding methods in accordance with DIN 8589 Full size table For peripheral plungegrinding methods, after calculating the material removal rate Q w and subsequent division by the width of the active grinding wheel profile b s eff follows the specific material removal rate Q Grinding Process SpringerLink
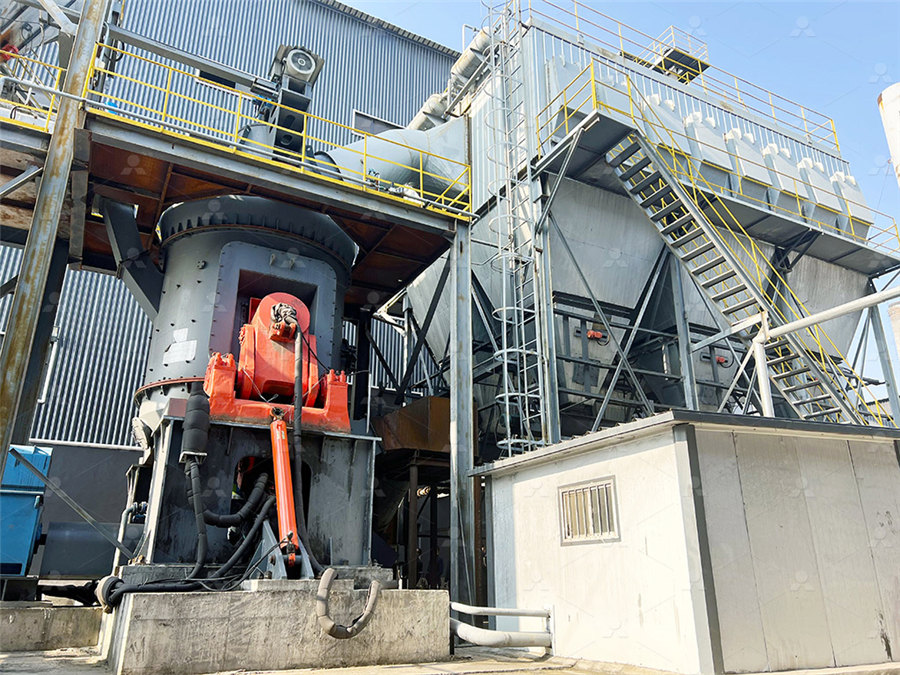
Manufacturing Process for Float Glass
Lowiron Glass Lowiron float glass refers to glass with significantly lower iron content that results in a more neutral appearance and slightly higher light transmittance than standard clear float glass The manufacturing process used to create lowiron glass reduces iron oxide content from raw material, resulting in lessThe iron ore pelletizing process consists of three main steps: 1 Pelletizing feed preparation and mixing: the raw material (iron ore concentrate, additives anthracite, dolomite and binders are prepared in terms of particle size and chemical specifications, dosed, and mixed together to feed the pelletizing process; 2Iron Ore Pelletizing Process: An Overview IntechOpen2022年1月13日 For finegrained iron oxide minerals, the iron oxide minerals distribution of 80–100% composition class differed by 22% at −75 + 53 μm size fraction with the two grinding methods, and its Process Mineralogical Assessment of the Grinding Products of 2023年10月27日 Cast iron can be grey or white, but white cast irons are commonly used in abrasive wear applications in the comminution process Cast iron grinding media are one of the ancient media, whereby a protective oxide layer is formed on the grinding media surface after the rapid initial corrosion of the grinding media surface A Review of the Grinding Media in Ball Mills for Mineral
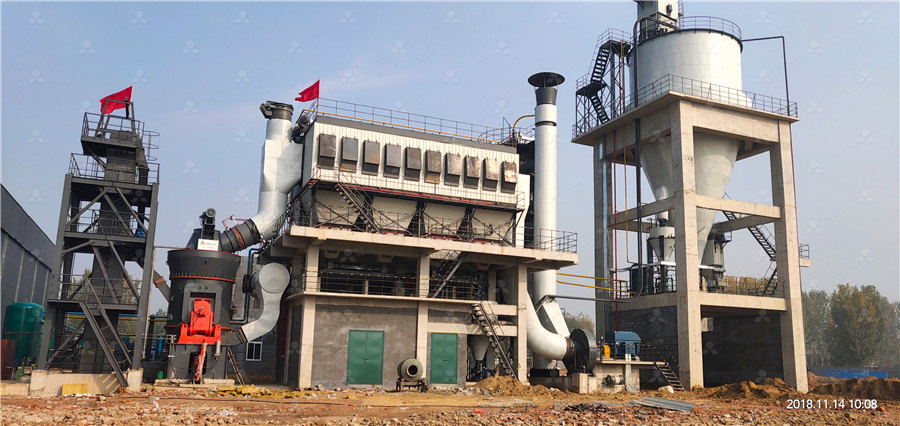
Study of Aluminum–Iron Oxide Composites Obtained by Die
2023年7月18日 The iron oxide particles and aluminum matrix produced a thermite reaction, forming different kinds of interfaces as a function of the quantity of during the grinding process, the aluminum was subjected to cold work, and so an increase in the dislocation density is anticipated 24 Table I Crystallographic information of sintered 2018年7月11日 The iron ore production has significantly expanded in recent years, owing to increasing steel demands in developing countries However, the content of iron in ore deposits has deteriorated and lowgrade iron ore has been processed The fines resulting from the concentration process must be agglomerated for use in iron and steelmaking This chapter Iron Ore Pelletizing Process: An Overview Semantic ScholarThe red iron oxide or ferric oxide glaze is one of those prevalent glazes that act as a much more common colorant for the glazing mixture With its easy availability, it offers a beautiful color to the glazing when fired inside the kiln Everything You Wanted to Know About Iron Oxide 2024年2月20日 A: Aluminum oxide grinding wheels are commonly used for grinding and shaping various metals, including steel, iron, and stainless steel They are also effective for sharpening tools, removing rust, and shaping Ultimate Guide to Aluminum Oxide Grinding Wheels
.jpg)
(PDF) Processing and Characterization of Iron Oxide
2023年3月21日 In this study iron oxide (Fe2O3) nanoparticle samples was prepared using mechanical grinding method The optical properties were studied using UVVis spectrophotometer within a range of 2001100nmIron Oxide is a black crystal or a reddishbrown powder It is used in polishing compounds, drums or other storage containers to process containers * Before entering a confined space where Ferrous Oxide (FeO) (grinding, mixing, blasting, dumping, etc), other physical and mechanical processes IRON OXIDE HAZARD SUMMARY Iron Oxide The Official Web 2021年5月18日 21 Iron (III) Oxides Iron (III) oxide is, of course, a compound that exhibits four different crystalline polymorphs: αFe 2 O 3, βFe 2 O 3, γFe 2 O 3, and εFe 2 O 3Hematite and maghemite usually appear in nature, while beta and epsilon structures are generally synthetic oxides [10, 11]In general, the iron (III) oxides anions arrange in closepacked structures, Synthesis, Properties, and Applications of Iron Oxides: Versatility 2020年2月1日 Optimization studies were carried out in the production of γFe2O3 nanoparticles by using coprecipitation method Iron (II) chloride and iron (III) chloride were used as precursors which are dissolved in distilled water followed by centrifugation, drying and grinding process in order to obtain dried dark brown precipitated γFe2O3 powderProduction of Iron Oxide Nanoparticles by CoPrecipitation
.jpg)
Choosing The Right Grinding Wheel Modern Machine Shop
2000年12月15日 Silicon carbide is an abrasive used for grinding gray iron, chilled iron, brass, soft bronze and aluminum, as well as stone, rubber and other nonferrous materials Ceramic aluminum oxide is another major development in abrasives This is a highpurity grain manufactured in a gel sintering process2023年8月25日 Iron is one of the most stubborn impurities in quartz minerals, and the iron content partly determines the various applications of quartz Iron can exist in quartz in the forms of iron minerals, fluid inclusions, and lattice impurities The removal of iron and the consequent purification of quartz minerals are the key processes to obtaining highquality quartz Iron A Review on Removal of Iron Impurities from Quartz Mineral MDPI2024年7月10日 The grinding process is influenced by a number of factors, Ceramic Aluminum Oxide Wheels: Used for precise grinding of highstrength steel and various alloys Silicon Carbide Wheels: Suitable for grinding cast iron, nonferrous metals, and nonmetallic materials Aluminum Oxide Wheels: Used for steel and metal alloys, What is Grinding: Definition, Types, Uses, and Working ProcessIdeal for grinding cast iron, nonferrous metals, and nonmetallic materials Hardness: Ranges from soft to hard (A to Z) Grit size: Coarse (16) to fine (600) ####Ceramic Aluminum Oxide Wheels: Used for precision grinding of highstrength steel and various alloys It's often the first step in a multistage grinding process and is followed Grinding in Engineering:Definition,Process,and Applications
.jpg)
Mechanochemical synthesis of metal oxide nanoparticles
2021年10月12日 The grinding process is involved in mechanochemical processing only to Bercoff, P G Fanovich, M A Magnetic iron oxides nanoparticles obtained by mechanochemical reactions from 2011年1月1日 The requirements for finer powders of iron oxide with specific microstructure characteristics have increased due to the development of new processes and 2007) Grinding mills typically used in the process include the attrition jet, planetary, oscillating and vibration mills, all of which are classified as highenergy mills Preparation of iron oxide nanoparticles by mechanical millingIn general, the reduction of Fe 2 O 3, called hematite, does not occur directly to metallic iron, FeIf the reduction temperature is lower than 570 °C, reduction to Fe occurs stepwise from Fe 2 O 3 to Fe 3 O 4, called magnetite, and continues to Reduction of Iron Oxides with Hydrogen—A Review2024年2月26日 Oxidised pellets have become an indispensable highquality charge for blast furnaces Nevertheless, highquality pellet feeds are becoming scarcer and scarcer To broaden the range of sources of pellet feeds and reduce the production cost of pellets, more steel mills are predicted to use coarse iron ore fines with a relatively low iron grade and low impurities for the Grinding of Australian and Brazilian Iron Ore Fines for Low
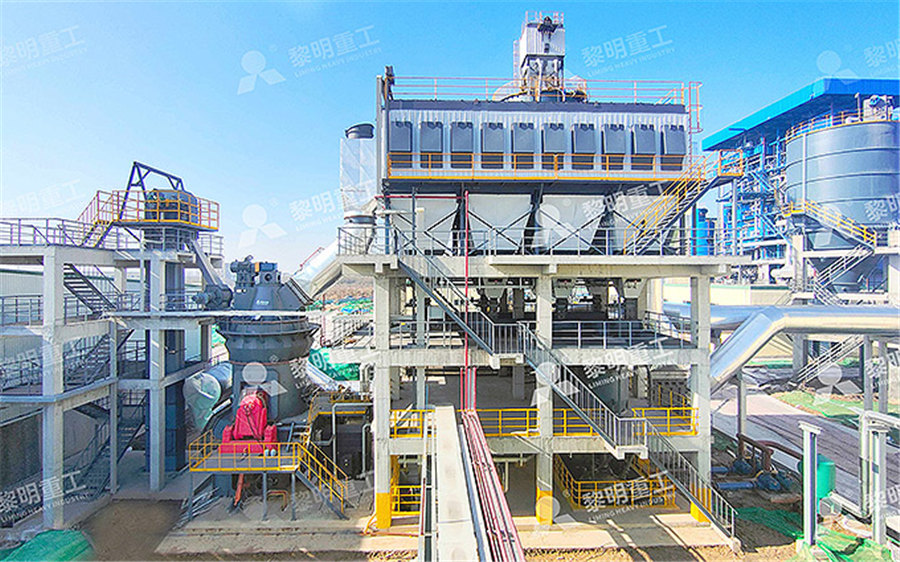
Chapter 16: Grinding Wheels and Operations American Machinist
2020年6月29日 The manufactured abrasives most commonly used in grinding wheels are aluminum oxide, silicon carbide, cubic boron nitride, and diamond Aluminum oxide Refining bauxite ore in an electric furnace makes aluminum oxide The bauxite ore is heated to eliminate moisture, then mixed with coke and iron to form a furnace chargeA thermite reaction using iron(III) oxide The sparks flying outwards are globules of molten iron trailing smoke in their wake In the following example, elemental aluminium reduces the oxide of another metal, in this common example iron oxide, because aluminium forms stronger and more stable bonds with oxygen than iron: Fe 2 O 3 + 2 Al → 2 Fe + Al 2 O 3Thermite WikipediaGRINDING PROCESS A Grinding wheel actually cuts away chips from the piece being ground Types of Abrasives : Aluminium oxide and Silicon carbide are the two major abrasives used in the manufacture of grinding wheels These synthetic or manufactured abrasives allow accurate control over the form and physical characteristics of the abrasive grainGrinding Wheels Master Abrasives2024年4月16日 Iron ore pelletization is a critical aspect of the steel manufacturing process, providing a method to utilize fine iron ore particles and beneficiate lower grade ores, which enhances the overall output and efficiency of steel production processes Pelletization involves converting iron ore fines into compact pellets, which are then used in blast furnaces or direct Iron Ore Pelletization: A Critical Review of Processes and
.jpg)
Preparation and formation mechanism of monodisperse micaceous iron
2018年4月15日 The aim of this study is to develop a new method for the preparation of highvalue, environmentally friendly products from iron chromium grinding waste (ICGW) Using iron‑chromium hydroxide precursors from the wet treatment of ICGW as raw material, monodisperse micaceous iron oxide (MIO) has been prepared via hydrothermal methodThe 2018年4月1日 Dry grinding can extended to the production of ultrafine particles There are many ways of manufacturing process in making iron oxideThis study is mainly aimed at solid reaction of Micaceous iron oxide production by application of magnetic separation