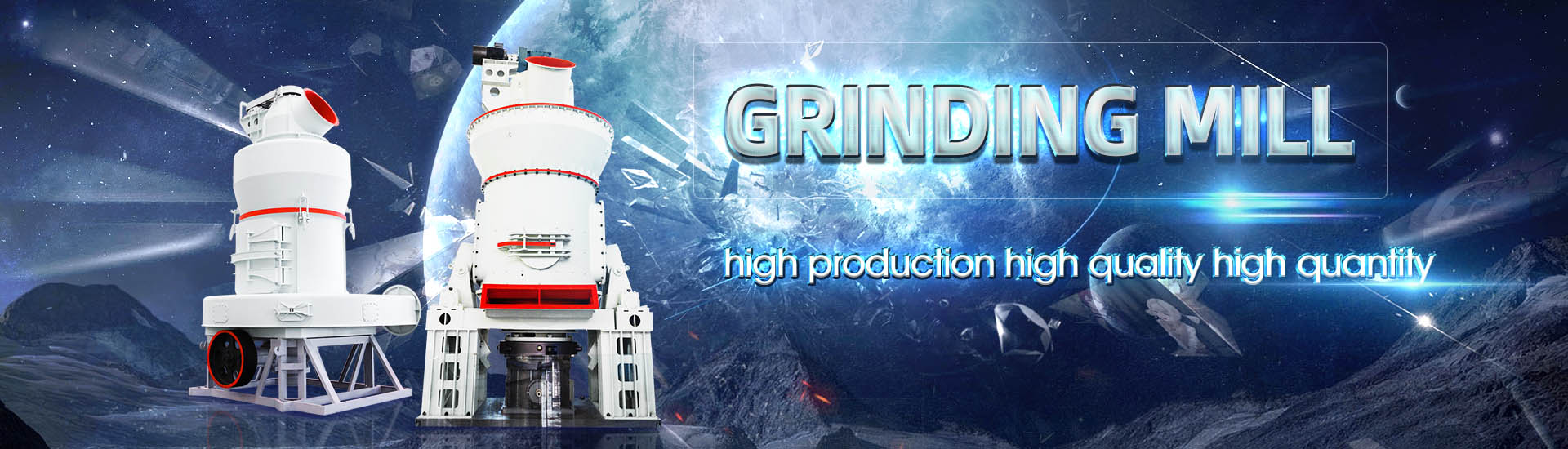
Therefore, its grinding efficiency is high
.jpg)
Effect of different parameters on grinding efficiency
2016年11月22日 The grinding efficiency is analysed by considering the rubbing, ploughing and cutting of a singlegrit grinding By analysing the features of acoustic emission in singlegrit grinding tests, an evidencebased scientific 2018年1月1日 However, highperformance dry machining processes (especially of lowstrength materials) offer about 104 times higher energy efficiency than grinding processes with small Energy efficiency of stateoftheart grinding processes2024年1月20日 The results showed that an increase in the theoretical grinding depth results in a higher material removal efficiency and grinding temperature as well as a superior ground Comprehensive analysis of the effects of different parameters on 2024年3月11日 When further increasing the grinding speed, there is highperformance grinding (also called highefficiency deep grinding, HEDG) with high material removal rate and grinding Towards Sustainable Grinding of DifficulttoCut Alloys—A Holistic
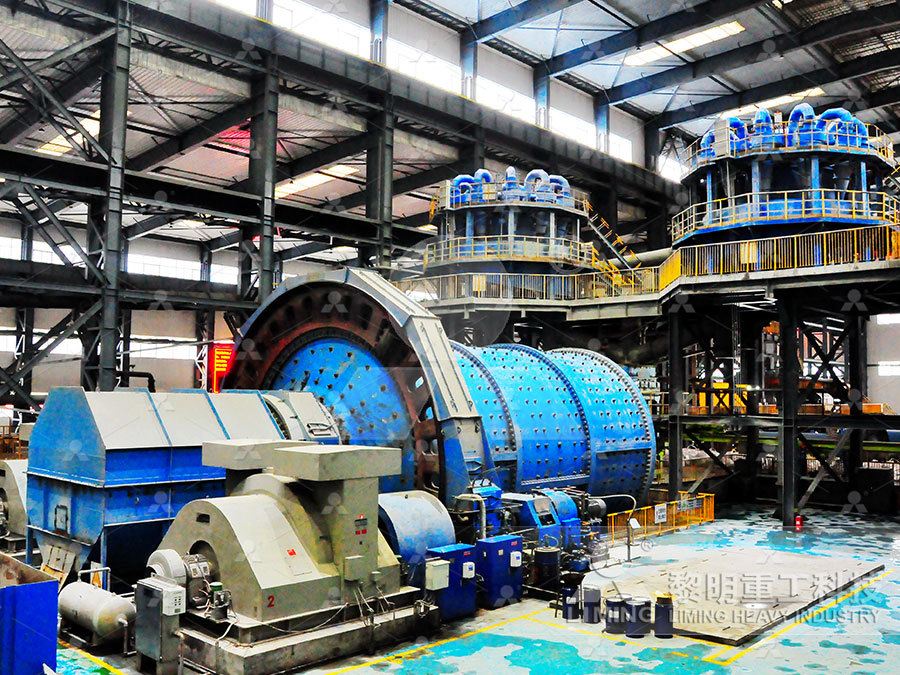
Efficiency and effectivity of high precision grinding manufacturing
2019年1月1日 Cluster analytics is utilised to identify grinding parameter sets and grinding results with similar characteristics within a group Data Envelopment Analysis (DEA) is applied to 2016年12月31日 High Performance Grinding processes offer a huge potential to overcome these challenges and increase productivity They are characterized by a significant increase in (PDF) High Performance Grinding ResearchGate4 天之前 Grinding tests were performed in a UPZ315Li highspeed precision grinder (Okamoto, Japan) with a spindle power of 22 kW and a maximum wheel speed of 20,000 rpm Three Enhanced prediction accuracy in highspeed grinding of brittle 2012年6月1日 High efficiency deep grinding (HEDG) achieves very high removal rates with moderate temperature rise It is shown that key factors are high wheel speeds, large depths of cut and moderatelyHigh efficiency deep grinding with very high removal
.jpg)
Thermal performance analysis of phase change heat storage grinding
2024年9月5日 A large amount of grinding heat is generated during the highefficiency grinding process, which causes workpiece burnout Although the utilization of a significant quantity of coolant can lower grinding temperature, it inevitably leads to environmental pollution and damages the health of operators To reduce coolant usage, it is worth considering reducing 2023年7月25日 Gamma titaniumaluminum intermetallic compounds (γTiAl) have an important application significance in the field of aeroengines owing to their excellent mechanical properties (eg, hightemperature resistance and high toughness) Grinding as an important method was used to realize the high efficiency and precise machining for difficulttocut materials However, Grindability of γTiAl intermetallic compounds during ultrasonic 2022年1月1日 A pilotscale grinding technology of ceramic medium stirred mill was proposed in this study Based on the specific productivity and grinding efficiency, the appropriate grinding parameters were ascertained as follows: material ball ratio of 07, ceramic ball medium size ratio (10 mm: 15 mm: 20 mm = 3:2:5), stirring speed of 110 rpm, grinding concentration of 50%, Highefficiency and energyconservation grinding technology using 2008年9月1日 Specific energy (total energy required to remove per unit volume of workpiece material) in grinding process is substantially high in comparison with other machining processes, which makes it a Modelling of specific energy requirement during highefficiency deep
.jpg)
Coolant condition and spindle power in highefficiencydeepgrinding
2021年11月18日 To avoid sudden burnout of the workpiece in high efficiency grinding, the OHPs in the grinding wheel are supposed to dissipate a high heat flux in a very short time, therefore, such OHPs should 1993年1月1日 High Efficiency Deep Grinding has been developed from a combination of high speed and creep feed grinding technique It can be characterised by its ability to achieve high stock removal rates and (PDF) High Efficiency Deep Grinding ResearchGatepart of the endosperm Therefore, based on the determination of the degree of extraction into flour during grinding of these substances, it is possible to assess the completeness of the use of grain, ie varietal grinding efficiency Recently, other criteria have been proposed based on taking into account the initialOperational control of grain grinding efficiency e3s 2022年8月31日 Therefore, any research effort that has the potential to reduce energy consumption while maximizing grinding efficiency is of great importance This Special Issue welcomes papers that highlight innovations and future trends in modeling grinding and technological ways to improve the grinding efficiency in ore/raw material beneficiationMinerals Special Issue : Grinding Modeling and Energy Efficiency
.jpg)
Grinding SpringerLink
2022年2月28日 Generally, grinding process efficiency can mainly be improved by either improving the grinding behavior of the material being ground or enhancing the grinding machines Recently, the use of additives socalled grinding aids, which is applied in a small amount of 001–025 wt% related to the mass of product, has reduced these problems and been 2016年12月31日 Exemplarily, highefficiency deep grinding (HEDG) uses high cutting speeds of v c > 80 m/s in combination with high depths of cut of a e > 03 mm in order to achieve high removal rates [4, 5](PDF) High Performance Grinding ResearchGate2016年4月1日 Request PDF Study on the model of high efficiency and low carbon for grinding parameters optimization and its application Reducing the carbon emissions and enhancing the carbon efficiency in Study on the model of high efficiency and low carbon for grinding 2024年3月11日 Grinding, a critical precision machining process for difficulttocut alloys, has undergone continual technological advancements to improve machining efficiency However, the sustainability of this process is gaining heightened attention due to significant challenges associated with the substantial specific grinding energy and the extensive heat generated Towards Sustainable Grinding of DifficulttoCut Alloys—A
.jpg)
Crushing and Grinding Process JXSC Machine
2019年10月8日 Grinding is a highefficiency and lowefficiency operation The power consumption of crushing operations only accounts for 8% to 12% of grinding operations Improving the grinding process is an effective way to Ball mills come in many different sizes, shapes, and speeds; however, all share one basic feature: they are designed to achieve high grinding efficiency There are two main factors that affect ball mill grinding efficiency: particle size distribution and speed of rotationGrinding efficiency of ball mill calculating equation2019年11月8日 Grinding of brittle materials is always a removal process of coexisting ductile and brittle removal modes Ductilityoriented grinding has been regarded as a precision machining pursuit for grinding quality and efficiency This paper is devoted to investigating ductilityoriented grinding mechanism and process design for quality promotion with a higher efficiency in high Ductilityoriented highspeed grinding of silicon carbide and 2023年4月27日 Under certain grinding conditions, the higher the grinding speed, the higher the grinding efficiency However, excessively high grinding speed can cause the grinding wheel to overheat, burn the grinding surface, and affect the grinding quality Therefore, when selecting the grinding speed, appropriate adjustments should be made according to the How to select grinding parameters? Comprehensive analysis of grinding
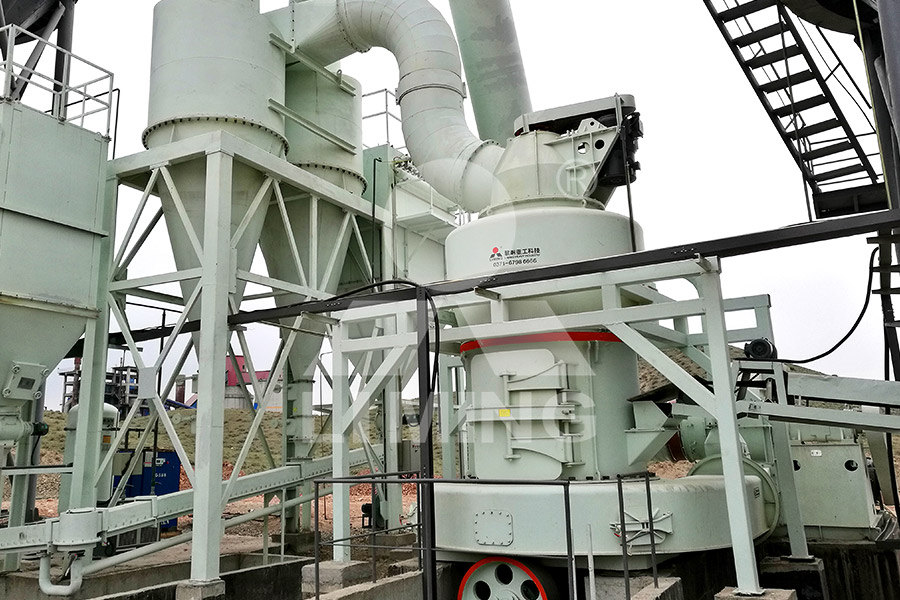
The Influence of the Grinding Media Diameter on Grinding Efficiency
2024年6月14日 The grinding process plays a crucial role in industry, allowing for the reduction of particle sizes of raw materials and substances to the required fineness—either as a finished product or for further technological processes The high demand for micro and nanopowders or suspensions is associated with the high energy consumption of the milling process Therefore, 2023年10月8日 Grinding is widely used as a finishing or nearfinishing process due to low cost, high machining efficiency, and good quality [1,2,3]During grinding process, numerous abrasives in a random distribution and with varied types, percentages, sizes, and shapes removal workpiece material in the form of tiny chips []In the past several decades, advanced grindingrelated Effects of bodyarmorlike grinding wheel parameters on surface 2023年2月15日 The grinding process of related structure of ferrous metals is to use such as resin abrasive grinding wheel and sintering saw blade, which can meet the processing requirements with the properties of low efficiency and bad security Therefore, the engineering application of high efficiency machining on ferrous metals is an urgent requirement Wear characteristics of brazing diamond abrasive wheel on high Grinding kinematics is one of the main mechanisms affecting the behaviour and efficiency of the creepfeed grinding process; it is thus essential in understanding the interplay of its parameters CreepFeed Grinding: An Overview of Kinematics ResearchGate
.jpg)
Thermal analysis of high efficiency deep grinding Request PDF
2001年1月31日 Request PDF Thermal analysis of high efficiency deep grinding The FEM model offers the most fidelity, but computational demands prevent its use in a digital twin Therefore, 2002年12月31日 High efficiency deep grinding (HEDG) of a low alloy steel (51CrV4) has been carried out on an Edgetek 5axis CNC grinding machine, using electroplated CBN wheelsHigh Efficiency Deep Grinding of a Low Alloy Steel with2020年9月14日 In order to realize automatic blisk polishing of aeroengines, Shi YY, Lin XJ et al, from Northwestern Polytechnical University independently developed “fiveaxis NC + flexible grinding head + elastic grindstone (sanding wheel)” polishing technological equipment; 1,16 this equipment has high trajectory accuracy, good adaptivity and other advantages, and elastic An optimization study of polishing efficiency of blisk and its 2023年8月22日 Grinding is usually used to increase the specific surface area of steel slag to improve its activity However, due to the large amount of hardtogrind minerals in steel slag, a large amount of energy is wasted in the grinding process Therefore, the current investigation aims to remove the hardtogrind minerals in steel slag as much as possible to explore the The Effect of Removing HardtoGrind Minerals from Steel Slag on
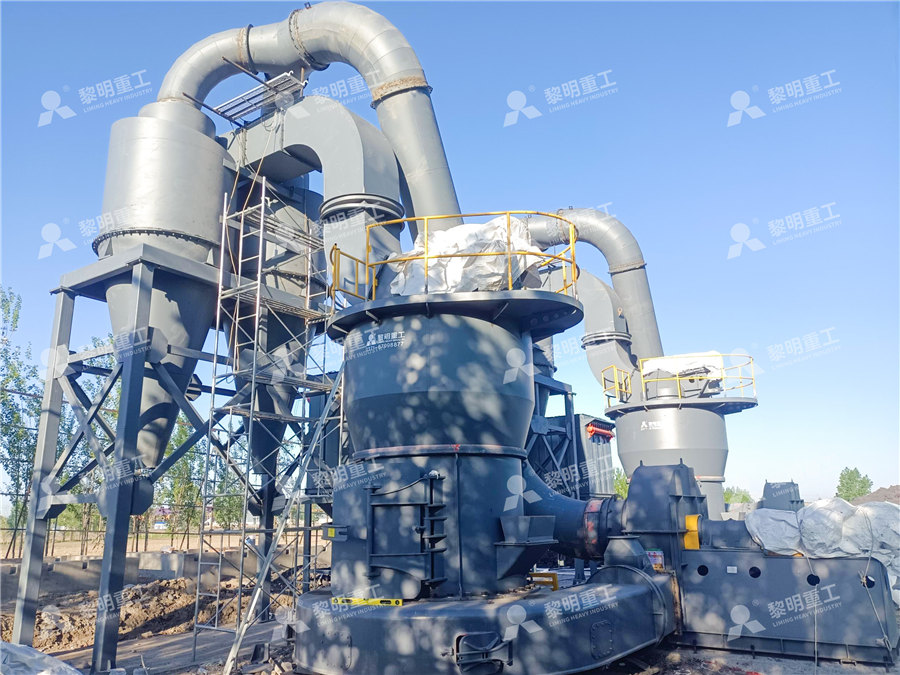
Simulation and experimental thermal analysis of ultrasonic
In recent years, the highefficiency deep grinding (HEDG) technique has become a crucial method for efficiently and precisely machining difficulttocut materials, thanks to its remarkable material removal rate [8], [9], [10]However, owing to the limited plasticity and exceptional strength of γTiAl materials, high grinding forces and excessive heat, even burns, can occur during the grinding Keywords Acousticemission Precisionandhighefficiency grinding Insitumonitoringsystems Brittlefracture Hard materials 1 Introduction Precision and highefficiency grinding is one of the most used techniques for very hard and brittle materials Previous research on fixed abrasive wear indicated that brittle fractureAnalysis of acoustic emission in precision and highefficiency grinding 2023年7月20日 According to the different grinding medium, the grinding mill is divided into three types: (1) ball mill – it is used widely, and almost all materials can be triturated by ball mill; (2) rod mill – its efficiency is relatively high with the feeding particle size less than 30 mm and the product particle size around 3 mm, and the produced Ore Grinding SpringerLink2024年1月6日 During the grinding process, the consumption of grinding media is large, and its cost accounts for half of the grinding cost Understanding the relationship between grinding media and grinding efficiency can provide highquality conditions for the grinding process and improve grinding efficiency, thereby Achieve direct or indirect reduction of grinding costsHow does Grinding Medium Affect Grinding Efficiency? Xinhai

Material removal mechanisms in ultrasonic vibrationassisted high
2024年11月1日 Grinding wheel wear is crucial for grinding processes directly affecting surface quality and processing efficiency To achieve efficient, highquality, and stable grinding, it is necessary to closely monitor the forms and mechanisms of grain wear 22, 23, 24 UVAG has advantages in reducing grinding wheel wear 25, 26 Yang et al 27 found that applying 2014年2月11日 Grinding kinematics is one of the main mechanisms affecting the behaviour and efficiency of the creepfeed grinding process; it is thus essential in understanding the interplay of its parameters (PDF) CreepFeed Grinding: An Overview of Kinematics2016年12月31日 High Efficiency, High Speed Grinding of a Composite Material Consisting of Polymer Concrete and Therefore, a high dynamic stiffness for the headstocks of machine tool structures is essential (PDF) High Efficiency, High Speed Grinding of a 2013年8月28日 Highefficiency deepgrinding (HEDG) The outlet velocity of the coolant jet and grinding speed have significant effects on the idle and grinding powers Therefore, Highperformance grinding—A review Request PDF
.jpg)
An experimental investigation on surface layer damage in high
2019年11月8日 Rail grinding is an important part of rail maintenance However, the processing efficiency of rail grinding by corundum grinding wheel is low due to the limitation of grinding thermal damage In this work, a slotted singlelayer brazed CBN grinding wheel is used to repair the rail surface replacing corundum grinding wheel, because the CBN abrasive has better heat 2019年11月11日 Therefore millers do their best to obtain high efficiency Raw material, equipment and production flow are the key factors affecting the flour yield Grain characteristics such as moisture content, environmental characteristics such as temperature and humidity in the mill and the level of experience of the miller are other factors affecting the yieldEFFICIENCY IN GRINDING AND ENERGY MANAGEMENT IN 2023年4月23日 Comparative trials of ultrasonic vibrationassisted high efficiency deep grinding (UVHEDG) and high efficiency deep grinding (HEDG) were carried out to study the grinding performance, in terms of Grindability of γTiAl intermetallic compounds during ultrasonic 2007年8月3日 High Efficiency Deep Grinding (HEDG) is an emerging technology that allows grinding to be undertaken at high wheelspeeds (up to 250 m/s), relatively large depth of cut (1 to 25 mm or more) and Process monitoring in high efficiency deep grinding HEDG
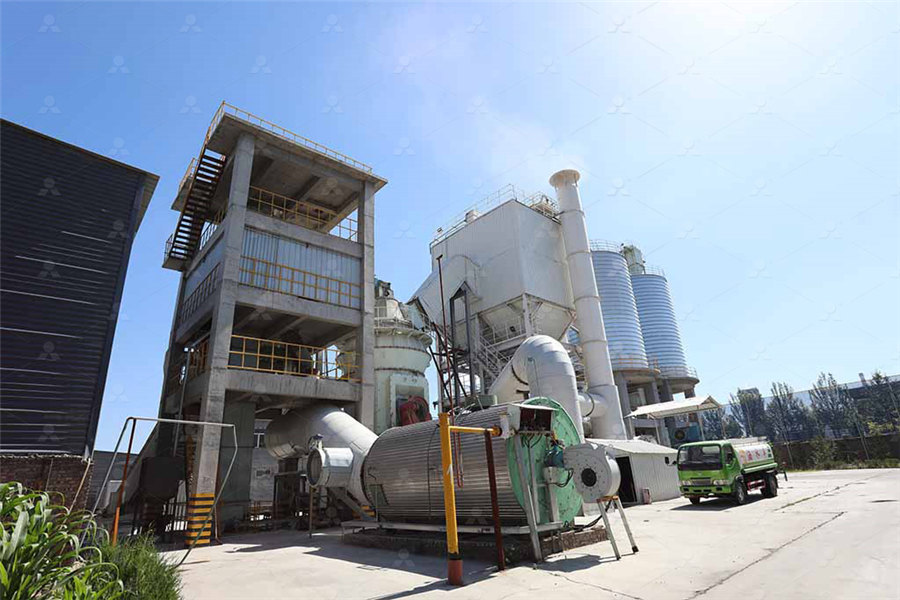
Highspeed grinding: from mechanism to machine tool
2024年10月5日 Highspeed grinding (HSG) is an advanced technology for precision machining of difficulttocut materials in aerospace and other fields, which could solve surface burns, defects and improve surface integrity by increasing the linear speed of the grinding wheel The advantages of HSG have been preliminarily confirmed and the equipment has been built for 2018年1月1日 It enables a combination of high speed grinding and creepfeed grinding, typically referred to as high performance grinding [17] Especially when employed on highperformance alloys using high cutting velocities, the high costs of CBN are compensated by increased productivity and tool life compared to other abrasives [18]Energy efficiency of stateoftheart grinding processes2021年6月14日 Super abrasive diamond grinding wheels are the most promising tools for the precision machining of advanced ceramics and carbide materials However, the efficiency of conventional conditioning of these tools is limited owing to high dressing tool wear, long process time, low form flexibility, and induced damage to the abrasive grains Wire electrical discharge Grinding efficiency and profile accuracy of diamond grinding 2023年8月8日 With the development of society, the world’s energy problems are becoming increasingly severe, and reducing energy consumption in manufacturing and improving energy efficiency in machining have become meaningful ways to reduce the energy burden In view of the problems of high energy consumption, low time efficiency, and high economic cost in the A multiobjective modeling and optimization method for high efficiency