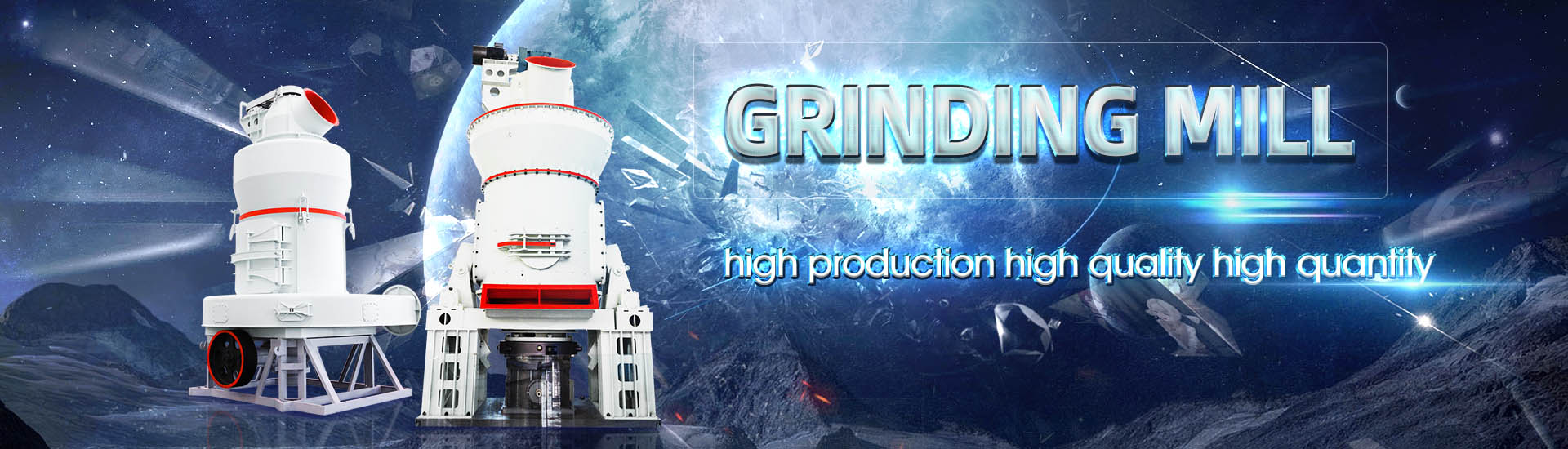
The role of 80 square rod mills in 1 hour Raymond mill
.jpg)
Rod Mill Design Calculations 911Metallurgist
2018年4月5日 Explore essential rod mill design calculations with 911 Metallurgist Our comprehensive guide provides formulas and techniques for optimizing rod mill performance and ensuring effective mineral processing2016年1月1日 Tubular tumbling mills loaded with rods as the grinding media are used for primary grinding of rocks and minerals Rods are placed parallel to the length of the mill, their Tubular Rod Mills ScienceDirectThe rod mill feeds a wet ball mill at a feed size of 10 mm (1000 μm) and produces a product with 80% passing a 150 μm screen The rod mill is in an open grinding circuit Determine: 1 the Rod Mill an overview ScienceDirect Topics2021年2月9日 This book throws new light on the internal mechanics of mills It covers among others the following aspects: Ball, tube, rod, pebble, batch, gratedischarge, trunnion BALL TUBE AND ROD MILLS, Rose And Sullivan 2 Archive
.jpg)
Ball Mills vs Rod Mills 911Metallurgist
2017年7月3日 Is it better to use a grinding mill with large balls or will small rods? How do you decide between using a ball mill or a rod mill? Many investigators have attributed the selective 2024年1月1日 Therefore, rod mill has the function of selective grinding, and its products are uniform in particle size and overgrinding is slight The rod mill is mainly used for gravity or Rod Mill SpringerLinkTUMBLING MILL MECHANICS A tumbling mill is a collective name for the generally known ball mills, rod mills, tube mills, pebble mills and autogeneous mills For all these kinds of mills the TUMBLING MILL MECHANICS2012年1月25日 It is intended in this research to investigate in details the effect of the presence of rods as stirring media in the rotating drum (mill) on the material flow characteristics in the Flow of materials in rod mills as compared to ball mills in dry
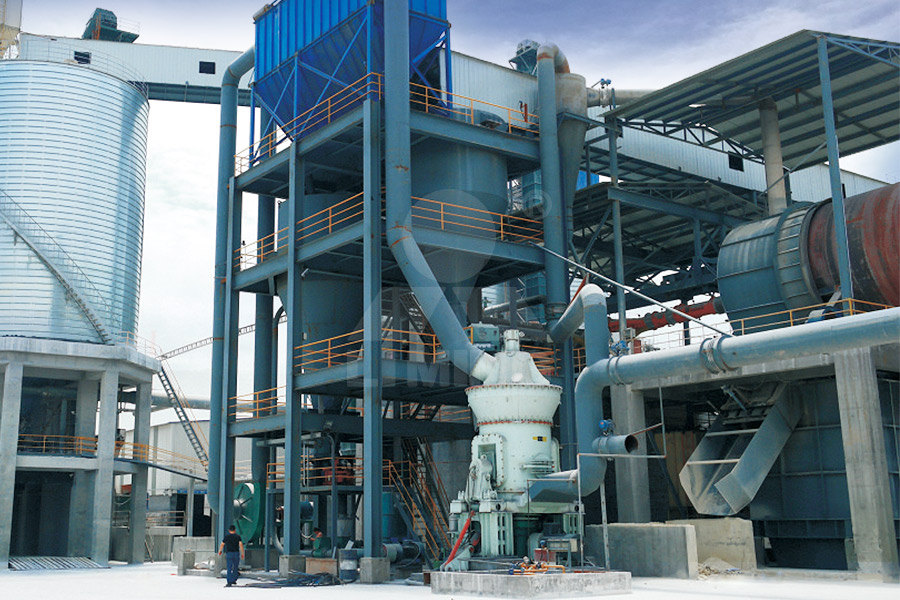
Raymond Roller Mill airswept vertical ringroll
The Raymond Roller Mill is an airswept vertical ringroll mill with an integral classification system that simultaneously dries, pulverizes and classifies limestone, Raymond Roller Mills are available with grinding ring diameters 2016年6月1日 ROD MILL CAPACITIES The above tables list some of the most common Open End Rod Mill sizes Capacities are based on medium hard ore with mill operating in closed circuit under wet grinding conditions at speeds Rod Mills: Efficient Grinding Solutions for Mining2019年10月1日 The fourroll rolling process (4RP) enables the further evolution of sizing processes in rolling mills for round sections The wellknown advantages of the threeroll process over the tworoll Roll Pass Design Methods for Three and FourRoll Metso Rod Mills are built in sizes from 3’ to 14’ shell diameter with shell lengths 1 1/2 to 2 1/2 times the diameter, Because of this, the rod mill can effectively reduce 1”feed size to 10 mesh or finer in open circuit The “voids” (or interstitial space) within a rod load are approximately half those in a ball mill grinding2060 Rod Mill Rsvd 911 Metallurgist
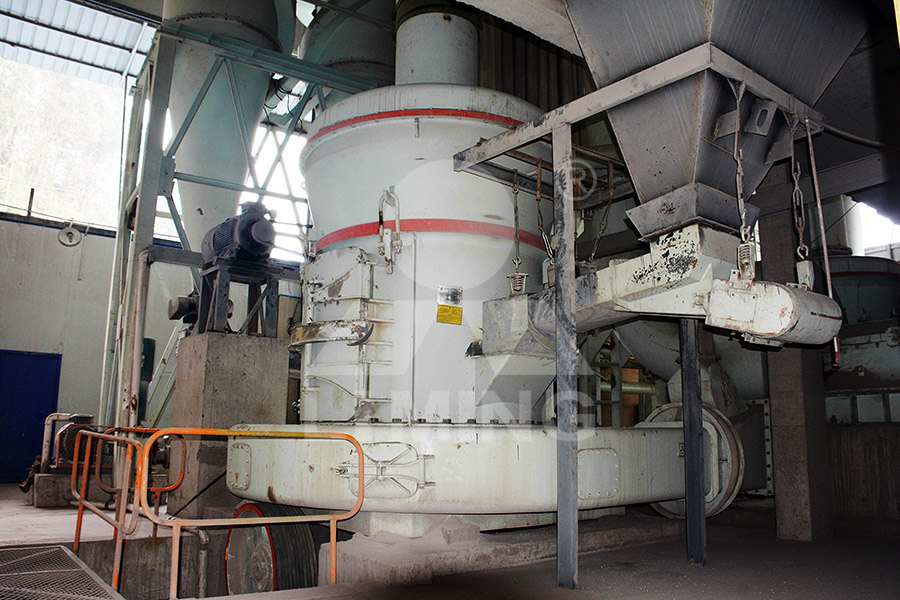
Main Features of a Modern Wire Rod Mill – IspatGuru
2014年1月3日 Modern wire rod mills are expected to meet the several requirements consisting of (i) high mill availability coupled with high productivity and high yields, (ii) meeting the need of low maintenance, (iii) meeting the need of lower energy consumption, (iv) close dimensional tolerances of wire rods in the range of +/ 010 mm and ovality in the range of around 02 mm, 2020年7月2日 The mill was simulated at 60, 65, 70, 75 and 80% of critical speed One of the most used tumbling mills is the ball mill the balls to powder weight ratio also plays an important role in (PDF) Effects of Ball Size Distribution and Mill Speed and Their 2023年10月27日 The ball mill is a rotating cylindrical vessel with grinding media inside, which is responsible for breaking the ore particles Grinding media play an important role in the comminution of mineral ores in these mills This work reviews the application of balls in mineral processing as a function of the materials used to manufacture them and the mass loss, as A Review of the Grinding Media in Ball Mills for Mineral Robert Mills (born 21 June 1982 [citation needed]) is an Australian actor, television host and singersongwriterHe was one of the finalists from the first season of Australian Idol in 2003 He cohosted the latenight quiz show The Mint with his childhood idol, JDawg, the two would go on to star in the hit show Young Talent Time, and was a regular singer on the game show The Rob Mills Wikipedia
.jpg)
Grinding Mills and Their Types – IspatGuru
2015年4月9日 Lining of the cylinder plays very important role It protects the mill from abrasions and at the same time it helps in lifting of the The drum diameter is limited to 06 or 07 times the length of the mill Rod mills are used for grinding Throughput or capacity is often given in tons per hour ( kg per hour for small mills)If a ball mill uses little or no water during grinding, it is a ‘dry’ mill If a ball mill uses water during grinding, it is a ‘wet’ mill A typical ball mill will have a drum length that is 1 or 15 times the drum diameter Ball mills with a drum length to diameter ratio greater than Ball Mill (Ball Mills Explained) saVRee saVRee2016年7月8日 Therefore, a 350hp motor is required and this in turn indicates that an 812 (8′ x 12′) Rod Mill is required In the same way Fig 3 indicates that an 800hp motor and a 101/214 or 105′ by 14′ Ball Mill is required Following is a Equipment Sizing: Crusher or Grinding Mill2014年5月8日 For design of precast elements the reader is referred to the PCI Design Handbook (2014) Smaller, or mini mill, frameworks are usually built using steel construction Some of the smallest mills are skidmounted and Design Considerations for the Construction and
.jpg)
Rolling of Steel in a Modern Long Product Rolling Mill
2017年6月19日 Since crosssectional area is reduced progressively at each set of rolls, the rolling stock moves at different speeds at each stage of the rolling mill A wire rod rolling mill, for example, gradually reduces the crosssectional area of a starting billet (eg, 150 mm square, 1012 meters long) down to a finished rod (as small as 50 mm in 2015年11月27日 Good figures for rod and bar mills are 90 % to 93 %, for structural mills, the good mill utilization figures are 75 % to 78 % If a mill rolls 80 % of the calendar year, that is 365 x 24 x 080 = 7008 hours If the mill rolls 800,000 tons per year, it runs at an average production rate of 11416 tons/hourUnderstanding Rolling Process in Long Product Rolling MillRod mills are widely used in various industries for their efficient grinding capabilities and ability to handle different types of materials [Introduction]: Rod mill is a grinding equipment with steel rod as medium [Capacity]: 062~250t/h [Improvement]: TAYMA rod mills include overflow rod mill, end peripheral discharge rod mill and center peripheral discharge rod mill, which could meet Rod Mill TAYMACHINERYDifferent types of rod mills are available, each with its unique features and advantages In this article, we will discuss the various types of rod mills and their applications Types of Rod Mills 1 Overflow Rod Mill This type of rod mill is used when a product with high fines content is desiredWhat are the Different Types of Rod Mill? ball mills supplier
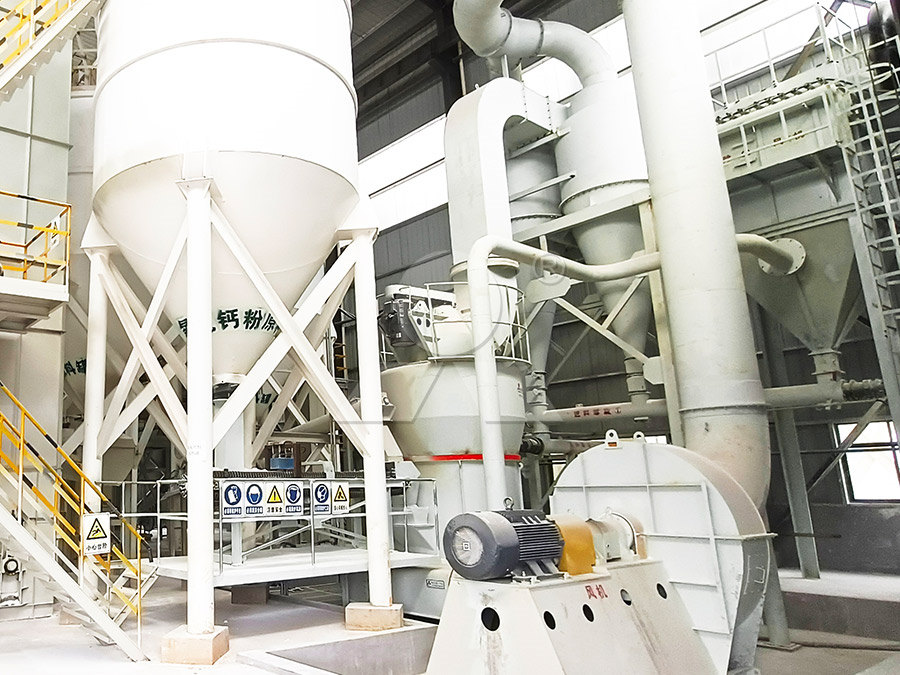
Tubular Rod Mills ScienceDirect
2016年1月1日 The crusher feeds a wet rod mill such that 80% of the crusher product passes a 16 mm screen The rod mill feeds a wet ball mill at a feed size of 10 mm (1000 μm) and produces a product with 80% passing a 150 μm screen The rod mill is in an open grinding circuit Determine: 1 the shaft power of the rod mill, 2 the size of the industrial millDownload scientific diagram Classical pass design for a wire rod mill from 80 mm square to 55 mm round, after [2] from publication: DataDriven Roll Pass Design of Wire Rod Mills The Classical pass design for a wire rod mill from 80 mm square to 2012年6月1日 As the cylinder starts to rotate, the grinding balls inside the cylinder crush and grind the feed material, generating mechanical energy that aids in breaking bonds, activating the catalyst, and Grinding in Ball Mills: Modeling and Process Control2015年12月3日 The difference in the two mill types is the coil box which, in compact hot mills, is installed between the roughing and the finishing mill It equalizes the transfer bar temperatures to the effect that with as few as six finishing stands final gauges of 12 mm can be achievedRolling of steel in Hot Strip Mill – IspatGuru
.jpg)
Rod Mill Design Power Draw 911Metallurgist
2015年10月19日 The rod mill motor power is in horsepower at the mill pinionshaft For different length rod mills power varies directly as rod length For difference between new and worn liners increase power draw by 6%, and adjust for bulk density per Table A Wet grinding rod mills are normally used in minerals processing plants2023年4月23日 between the ball mill a nd rod mill showed that particles in a ba ll mill h ave a shorter residence time than in a rod mill [5 8] This is because balls offer less resistance to t he flow of (PDF) Grinding Media in Ball MillsA ReviewThis book throws new light on the internal mechanics of mills It covers among others the following aspects: Ball mills, tube mills, rod mills, pebble mills, batch, gratedischarge, trunnion overflow, hardinge and airswept mills; open and closedcircuit grinding; dry and wet milling; contamination of products; Single ball in mill; cascading; cataracting; equilibrium surface of charge, etc Ball, Tube and Rod Mills, Rose and Sullivan, Publication Year 1958 Upgrading rod and bar mills with stateoftheart an important role in the decision by the mill owner to select ABB’s newgeneration Rolling Mill Control A new 3stand roughing mill was installed in 1995, increasing the original rolling capacity from 120 mm to 165 mm square billets This addition also included the ABB RMC 200 system Upgrading rod and bar mills with stateoftheart control
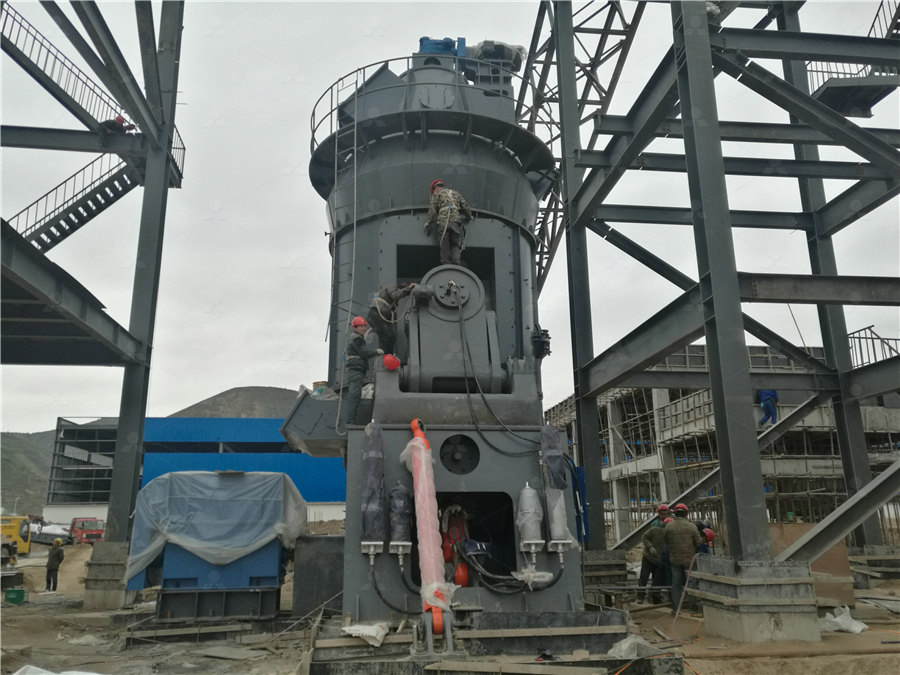
2020 Technology and Operation of a Hot Rolling Mill
2020年1月3日 This content was downloaded from IP address 21280200255 on 03/01 for mini mills, that is, combined casting ho In a lying head for wide rod rolling mill it is important to know the Mill Type Overview Three types of mill design are common The Overflow Discharge mill is best suited for fine grinding to 75 – 106 microns; The Diaphram or Grate Discharge mill keeps coarse particles within the mill for additional grinding and typically used for grinds to 150 – 250 microns; The CenterPeriphery Discharge mill has feed reporting from both ends and the product AMIT 135: Lesson 7 Ball Mills Circuits – Mining Mill Operator 2013年7月15日 mill tests are used to determine specific energy c onsumption (kWh/t) to grind from a given feed 80% passing size (F80) to 80% passing size product (P80 ) Variations in the original Bond methodology(PDF) Energy Efficient Ball Mill Circuit – Equipment Sizing 2020年6月8日 The internal working principle of Raymond Mill is as follows: the crushed materials are continuously and uniformly fed into the grinding chamber of the host machine for grinding The powder after grinding is carried away by the airflow of the fan and is classified by the analysis machine , The powder meeting the fineness enters into the large cyclone collector What is the working principle of Raymond Mill?
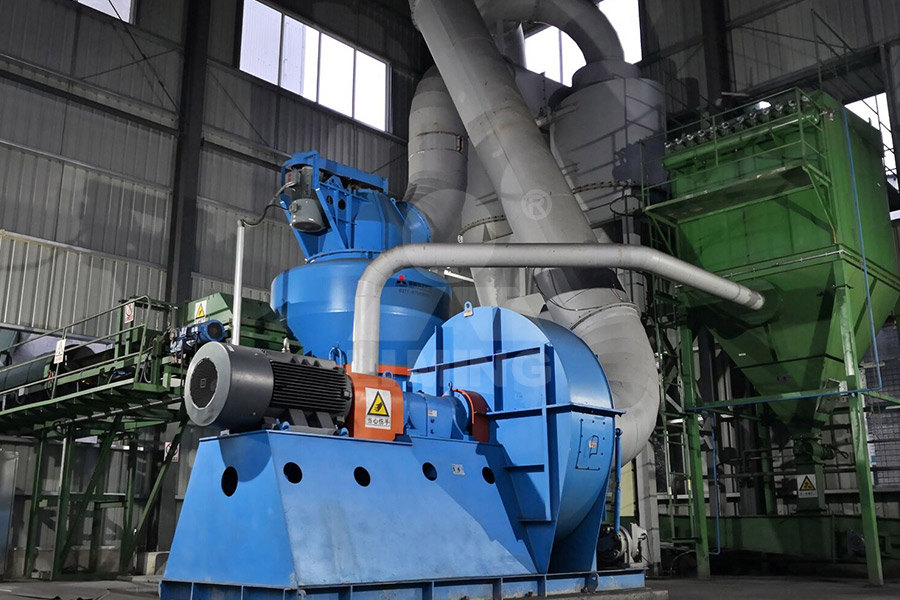
The important role of vertical roller mills in the cement industry
The important role of vertical roller mills in the cement industry Companies in the global cement industry are facing major challenges: If they are to improve productivity while simultaneously decreasing costs, they need highperformance products that are also energyefficient and offer maximum availability and flexibility These products also need to comply with environmental 2017年7月3日 Because of this, the rod mill can effectively reduce 1″ feed size to 10 mesh or finer in open circuit The voids (or interstitial space) within a rod load are approximately half those in a ball mill grinding loadBall Mills vs Rod Mills 911MetallurgistRod Mills Price Select 2024 high quality Rod Mills Price products in best price from certified Chinese Mineral Rod Mill manufacturers, Mineral Mill suppliers, wholesalers and factory on MadeinChinaRod Mills Price MadeinChina2017年7月3日 Effect of Rod Mills Ore Charges Speeds but that status need not vitiate the comparisons In the rod mill with the 152inch rods, the tons per horsepowerhour were nearly the same as in the ball mill The efficiency, that is, the surface tons per horsepowerhour, of the rod mill was a little below that of the ball millEffect of RPM Rod Mill Speeds 911Metallurgist
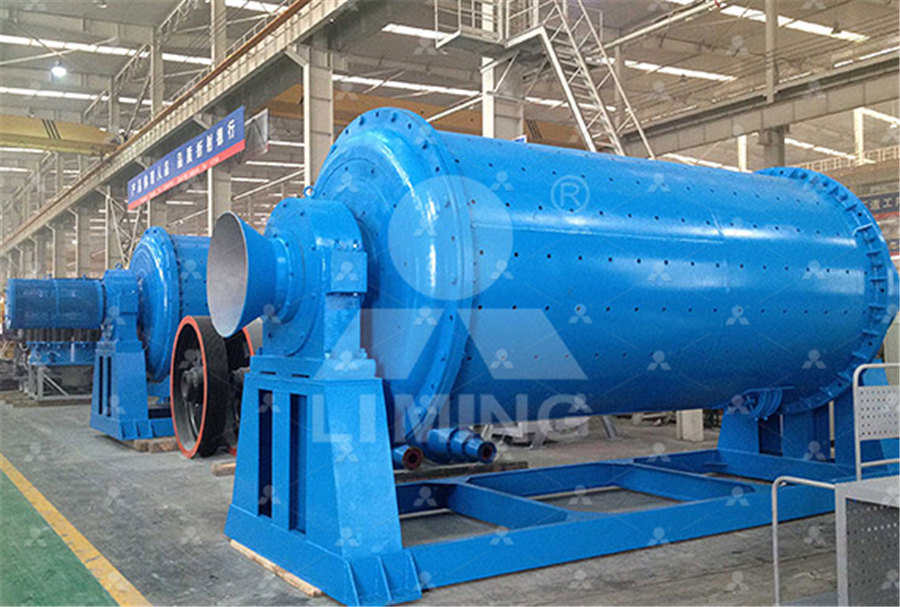
(PDF) Critical Speed in Rod and Ball Mills n y Academia
The angular velocity of this point inside the mill can be calculated as follows: T = [ 2 π ( R / 2 ) ] / v = 1570 / 39 = 4 sec f = 1 / T = 1 / 4 = 025 sec ω = 2 π * f = 2 π * 025 = 1570 rad / sec 4 nyıldız 3Critical Speed As the mill rotates, when the load created by the pulp and grinding medium inside the mill is very high, the mill, under the influence of centrifugal force, will 2019年5月26日 Fig 1 Components of a roll stand Housing – Housing creates a framework of the rolling mill stand and for absorbing the total metal pressure on rolls during the process of rolling Hence, the housing is to be solid and its structure is to enable easy and fast roll changing Also, there need to be easy access to all parts of the housing and other details of the roll standRolling Mill and its Technological Equipments – IspatGuru1 9 5 4 3 2 10 8 7 7 2 1 8 10 6 6 6 7 7 The information (including, eg, figures and numbers) provided in this document contains merely general descriptions or characteristics of performance based on estimates and assumptions which have not LOOPERS FOR LONG ROLLING MILLS Primetals TechnologiesBar mill and wire rod mill optimization: profile rolling process goes digital Harness high level plant and process data and use it to trace and visualize the KPI’s important to your profile rolling mill, right down to individual billet precisionBar mill and wire rod mill optimization ABB Group
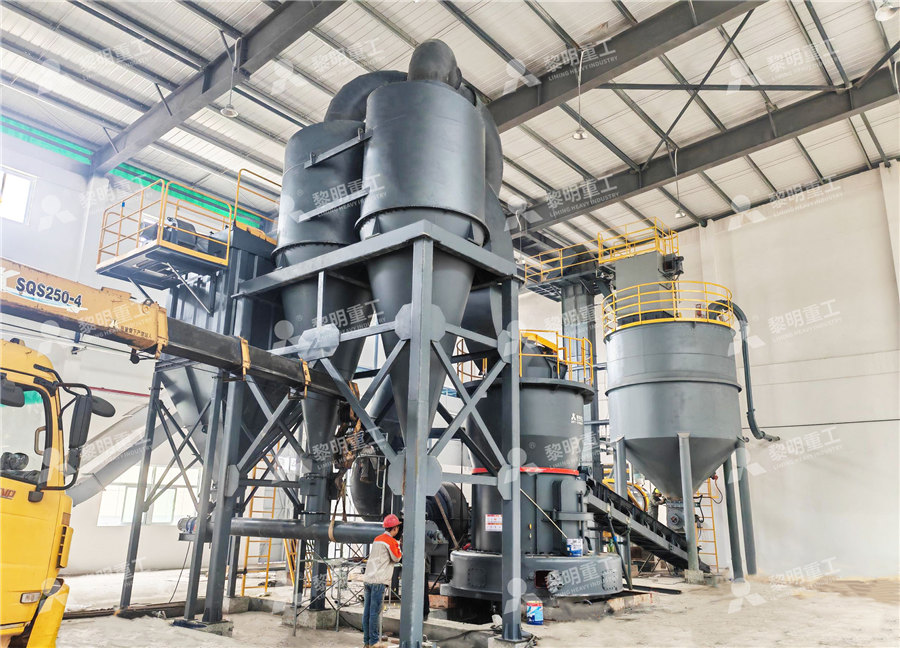
ECONOMICAL PRODUCTION ON WIRE ROD AND BAR MILLS
Sizing) mill in the finishing part of the mill, single family rolling is used from stand 1 up to the block exit The complete finished product size range from 5 to 25 mm is rolled 8stand Block FRS® Sizing Mill Roughing Intermediate Mill Patented Multiline Loop area Figure 1 High speed Wire Rod Mill for quality steel Figure 1a Covered runoutThe Raymond mill is an efficient, ecofriendly grinder for processing nonmetallic minerals (1–22 t/h), and the finished product fineness is 0173 mm–0044 mm (80–325 mesh) Model 4525 4119 Feeding Size(mm) ≤30 ≤25 Output Size(mm What are the advantages of FTM Machinery's Raymond mills? Automatic Highefficient Raymond Mill Fote MachineryOriginalarbeit Fig 4: Passsequencefor55mmwirerodrolling[7,13] grooves forabarmillcanrangefrom150–250groovesdependingonthesizesteps Amodernwirerodmillproduces rod sizes from 55 (50) mm to 24 mm in 05 mm stepsModels for Rod and Bar Rolling Mills with 2roll, 3roll, and 4roll The Sterling rod mill reduces a 130 mm (5 1/8”) square billet to 171 mm (067”) in 14 stands The stands in the roughing and intermediate mills are configured in a horizontal/vertical arrangement with roll diameters ranging from 565 mm (22”) to 380 mm (15”), with a shear located after the sixth and 14th stands Following stand 14,PREFINISHING MILL MODERNIZATION ON THE STERLING STEEL ROD MILL*