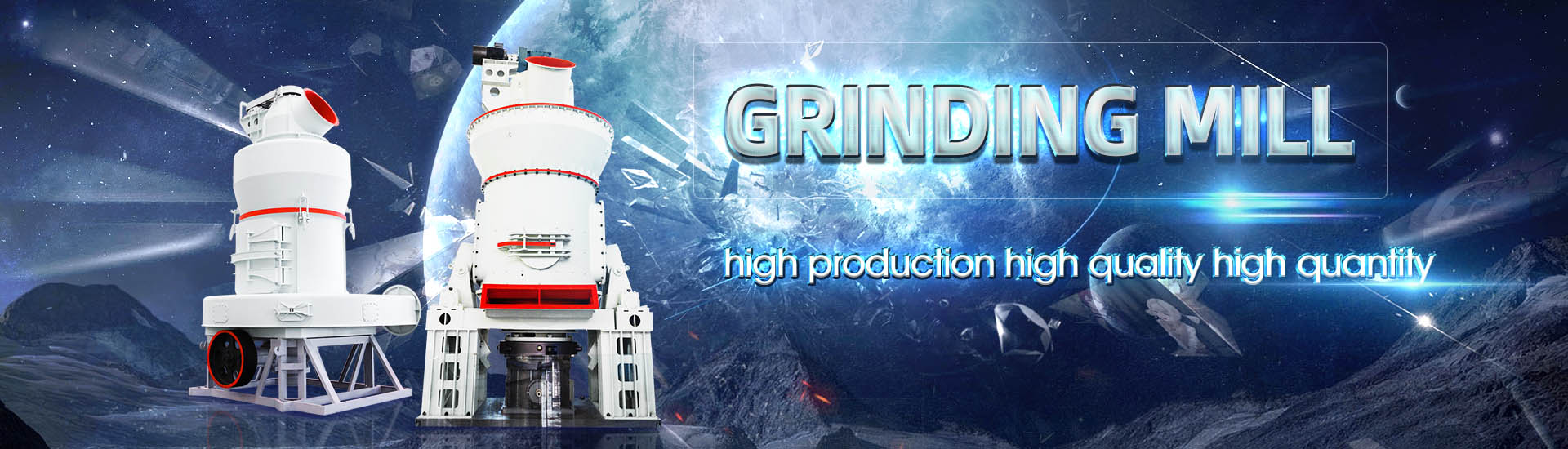
Energyefficient ore mill
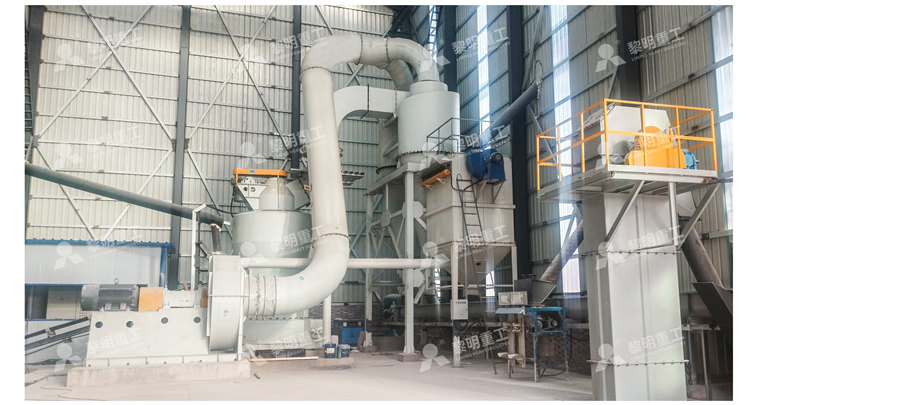
Energy Efficiency Analysis of Copper Ore Ball Mill Drive
2021年2月26日 One method for increasing the energy efficiency of ball mills is to optimize their drive systems This article looks at two variants of drive 2009年6月1日 The data show that the stirred mill has an advantage over the ball mill The energy saving of 25%, 37% and 27%, respectively, treating the three ore samples by using the Comparison of energy efficiency between ball mills and stirred energy requirements across the mill and smelter The new methodology discussed here will integrate downstream processing energy with mineral processing energy, to find the overall Improving Energy Efficiency Across Mineral Processing and 2017年11月2日 In openpit mines, improvements in mill performance have been achieved by increasing the energy intensity of blast patterns, thereby reducing the size of feed to the mill A EnergyEfficient Comminution: Best Practices and Future Springer
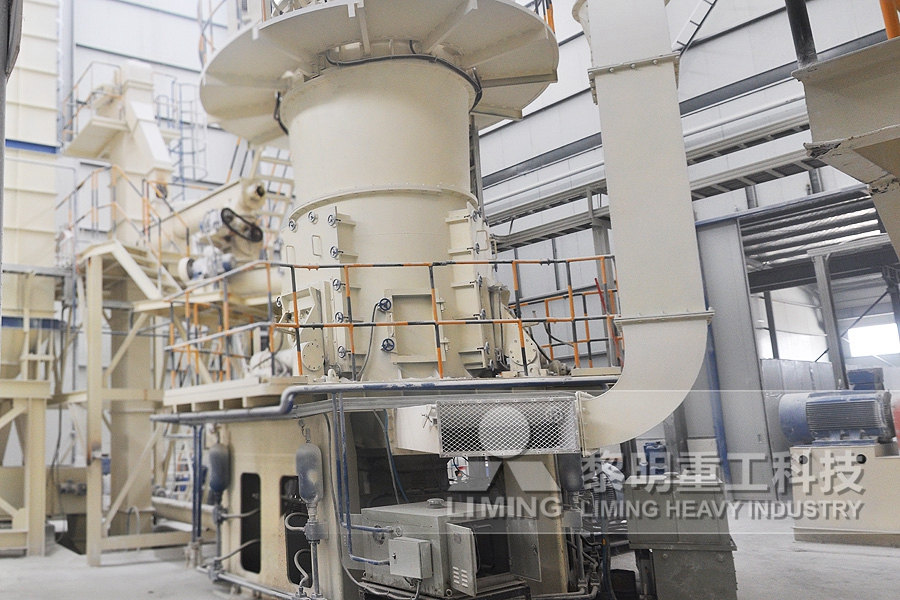
Energy Efficiency Analysis of Copper Ore Ball Mill Drive Systems
2021年3月23日 One method for increasing the energy efficiency of ball mills is to optimize their drive systems This article looks at two variants of drive systems with efficiencies higher than One method for increasing the energy efficiency of ball mills is to optimize their drive systems This article looks at two variants of drive systems with efficiencies higher than the already Energy Efficiency Analysis of Copper Ore Ball Mill Drive Systems2014年11月28日 Although energy consumption in mills is most efficient at design capacity, they are not always operated in this manner Topdown/bottomup energy assessment reduces The link between operational practices and specific energy Researchers from the University of Utah are developing a pilotscale SAG mill facility that will imitate a fullscale operation It will have sensors for online mill load, power, flow and other ITP Mining: Improving Energy Efficiency in SAG Mills
.jpg)
Performance Comparison of the Vertical and
2023年1月31日 In this study, HIGMill and IsaMill, which were vertically and horizontally chamber oriented, respectively, were compared for a regrinding process of copper ores with similar characterization and almost the same Energy Efficiency Analysis of Copper Ore Ball Mill Drive Systems Piotr Bortnowski, Lech Gładysiewicz, Robert Król and Maksymilian Ozdoba * Citation: Bortnowski, P; [20] Specific energy demand by a mill depends on its efficiency, which is directly related to the speed of the mill Optimal mill speed is typically 65 75% of its critical Energy Efficiency Analysis of Copper Ore Ball Mill Drive Systems2017年11月2日 System designs that conserve energy and apply energyefficient technologies can result in significant reductions in Little WM, Mainza AN, Becker M, Gerold C, Langel J, Naik S (2015) Assessing the performance of the Vertical Roller Mill for grinding Platreef ore In: Sixth international conference on semiautogenous high press EnergyEfficient Comminution: Best Practices and Future2023年1月1日 Therefore, PGE bearing lowgrade chromite ore needs an energyefficient grinding mill for the downstream beneficiation process 34 Comparison of HPGRBall mill and HPGRStirred mill circuit The optimal conditions for the stirred mill for grinding of PGE bearing chromite ore were discussed elsewhere [43]Size reduction performance evaluation of HPGR/ball mill and
.jpg)
Comparison of energy efficiency between ball mills and stirred
2009年6月1日 It can be concluded that the HPGRStirred mill combination was a more energyefficient grinding circuit than the HPGRBall mill combination for PGE bearing chromite ore View Show abstractEnergies 2021, 14, 1786 2 of 14 size [11] The cost of the energy used in comminution represents 50 ÷ 60% of the entire ore processing costs [12]Energy Efficiency Analysis of Copper Ore Ball Mill Drive SystemsOUTOTEC HIGMILL – ENERGYEFFICIENT HIGHINTENSITY GRINDING With global ore grades declining and the demand for commodities continuing to increase, mining BENEFITS companies require new ways to costeffectively • High energy efficiency with patented liberate minerals and maximize recovery levelsOutotec Higmill – EnergyEfficient HighIntensity GrindingIn addition, the combined use of energyefficient crushing and fine grinding equipment helps reduce energy use through the following: Reducing primary and secondary recirculating loads, for lower power requirements, less ore to handle and a switch to a smaller millMining energygovau
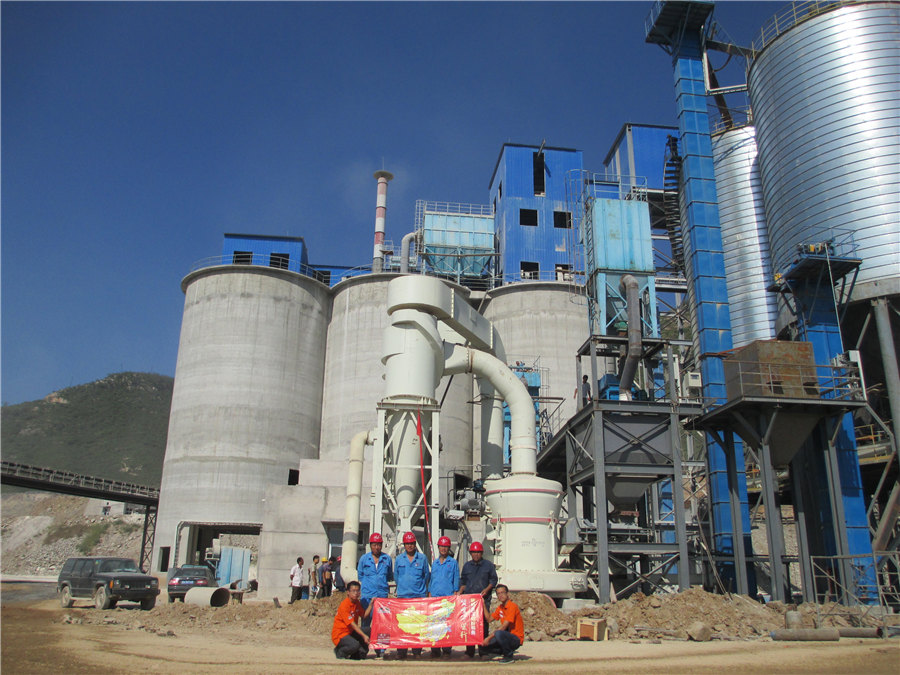
Towards waterless operations from mine to mill ScienceDirect
2022年9月1日 The objective is to provide an overview and some selected examples of potential methods for energyefficient production of valuable materials from complex ores, consider ways of mitigating waste from the mill feed, and examine the main methods for waterless processing of minerals and management of tailingsUnderstanding the SAG Mill in Copper Ore Mining Process Are you curious about the machinery behind copper ore mining? SAG mills use their own weight and the force of material being fed into them to grind ores This makes them more energyefficient than other types of machinesUnderstanding the SAG Mill in Copper Ore Mining Process2018年11月28日 In this study, energyrelated operational parameters for modern and traditional (conventional) sugar mills are analyzed, with the goals of identifying improvements in energy efficiency and potential for surplus electricity export Results show that the powertoheat ratio of modern and traditional mills is clearly distinct, lying in the ranges of 03–05 and 004–007, Energy performance comparisons and enhancements in the sugar 2023年9月29日 PDF Link for citation: Zakamaldin AA, Perevoshchikov FV, Shilin AA Efficient use of electric energy when operating a ball mill with a constant Find, read and cite all the research you EFFICIENT USE OF ELECTRIC ENERGY WHEN OPERATING A BALL MILL

EnergyEfficient Technologies in Cement Grinding
2015年10月23日 In this chapter an introduction of widely applied energyefficient grinding technologies in cement grinding and description of the operating principles of the related equipments and comparisons over each other in 2023年7月10日 The present literature review explores the energyefficient ultrafine grinding of particles using stirred mills The review provides an overview of the different techniques for size reduction and (PDF) EnergyEfficient Advanced Ultrafine Grinding of 2024年2月12日 Automating a feed mill could be the key to unlocking energy efficiency and substantial cost savings, this is done by controlling the speed of the machine that feeds the product into the mill Here, Gary Kernaghan, automation manager at systems integrator Technidrive, explores how automation can improve energy consumption management in feed Energyefficient milling Reduce energy costs and improve Advantages of Wind Power Wind power creates goodpaying jobs There are nearly 150,000 people working in the US wind industry across all 50 states, and that number continues to grow According to the US Bureau of Labor Statistics, wind turbine service technicians are the fastest growing US job of the decadeOffering career opportunities ranging from blade fabricator to Advantages and Challenges of Wind Energy
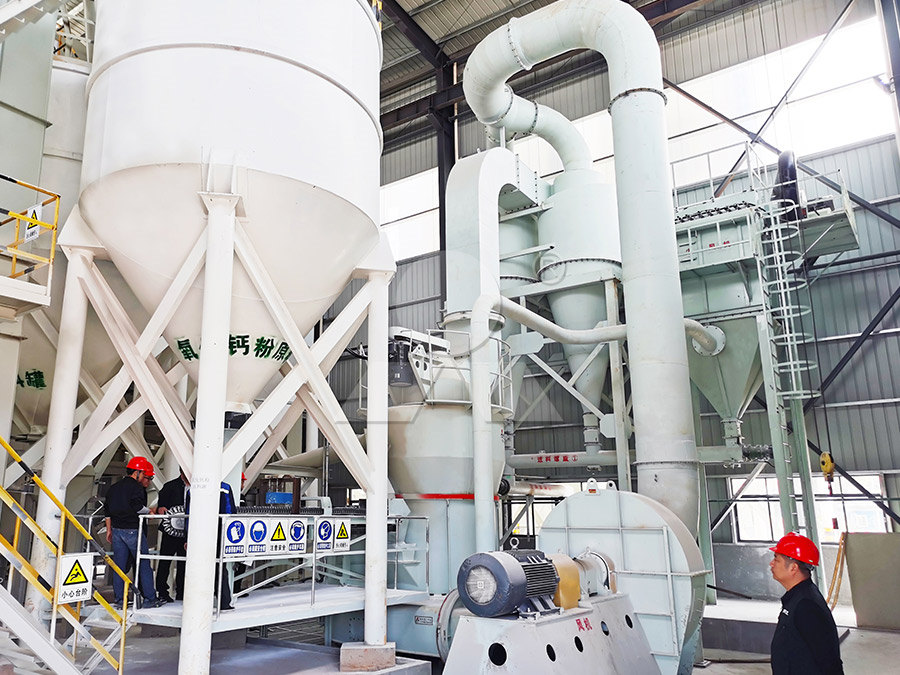
MicroGrinding Systems, Inc EnergyEfficient Vibratory Mills
The VibroKinetic Energy (VKE) Mill is designed to fill the need for a fine to ultrafine grinding mill which is both low cost and economical to operateOptional features include air classification while dry grinding, which greatly improves the efficiency of the mill Wet grinding with hydrocyclone recycle for accurate sizing, and use of vibratory table for concentration of ore values is also 2023年9月28日 A reduction in energy consumption, however minor it may seem, can significantly enhance a mill’s profit margin or mitigate operating costs This article delves into the multifaceted realm of energysaving strategies for millers, exploring everything from efficient machinery and renewable energy sources to innovative technologies and meticulous Tips in energy saving for flour millers Miller MagazineAlthough 60% of total energy is estimated to be consumed in mining equipment, this category covers a very wide variety of different equipment Comminution, consuming close to 40% of total energy contains a single piece of equipment—the grinding mill—that is typically the largest single consumer in a mining operationMINING ENERGY CONSUMPTION 2021 CEEC (Coalition for Eco Efficient energy management systems ensure efficient use and recovery of energy throughout the steelmaking process for use within the steelworks boundary or exported from the site Improvements in energy efficiency have led to reductions of about 60% in energy required to produce a tonne of crude steel since 1960, as demonstrated in Figure 11Fact sheet Energy use in the steel industry
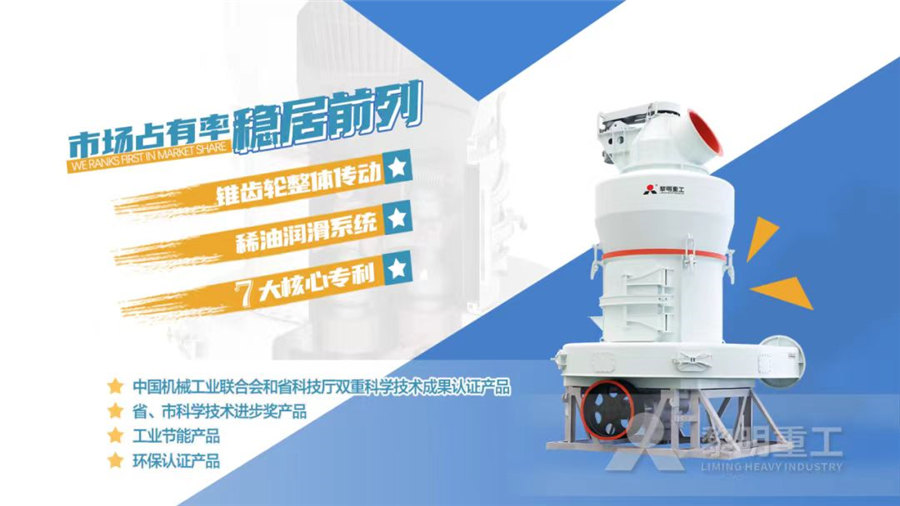
Benchmarking comminution energy consumption for the
2014年10月1日 As the mining industry continues to seek greater energy efficiency, it needs more effective characterization of ore material as it progresses from mine to mill The energy cost of ore mineral 2023年1月31日 Varied types/geometries of stirred mills have been produced by different manufacturers, and the comparison task has been accomplished for some of the technologies, ie, Tower mill vs IsaMill However, the main Performance Comparison of the Vertical and 2024年7月9日 The Coalition for Energy Efficient Comminution (CEEC) 26, 2019 ABSTRACT A comprehensive energy study was carried out for the Red Chris mill, which processes coppergold ore at a rate of 30,000 tonnes per day (t/d) and is located in Northern British Columbi Energy Efficiency CEEC (Coalition for Eco Efficient Comminution)sized materials, once the domain of tower and ball mills The need for energy efficient grinding circuits will only result in more IsaMill™ circuits being applied in the future IsaMill™ OPERATION Grinding Mechanism The IsaMill™ is a horizontally stirred mill consisting of a series of 8 discs rotating around a shaftIsaMillTM Technology Used in Efficient Grinding Circuits
.jpg)
Improving energy efficiency in comminution
2018年10月1日 How are IPCCs more energyefficient than traditional truck and shovel The trial demonstrated a 148 percent increase in mill throughput for the specific ore selected for the study, 2021年5月1日 Efficient electrical energy usage has been recognised as one of the significant factors to reduce the cost of electrical energy consumption In this world, hospitals are public buildings that use Improving Energy Efficiency at Palm Oil Mill IndustriesReducing Grinding Energy and Cost Magnetite Iron Ore Design Case Study A Jankovic and W Valery Metso Process Technology Innovation, PO Box 1028, Eagle Farm Qld, 4009, AustraliaReducing Grinding Energy and Cost Magnetite Iron Ore2016年10月18日 The paper industry is heavily using energy during all the phases of the manufacturing process This is especially the case in Nordic mills where pressure ground wood is the source of fiber The purpose of this case study is to show how energy consumption behaves on a monthly basis in a Finnish paper mill that has several paper machine lines The research Energy efficiency at the paper mill—dilemma of improvement
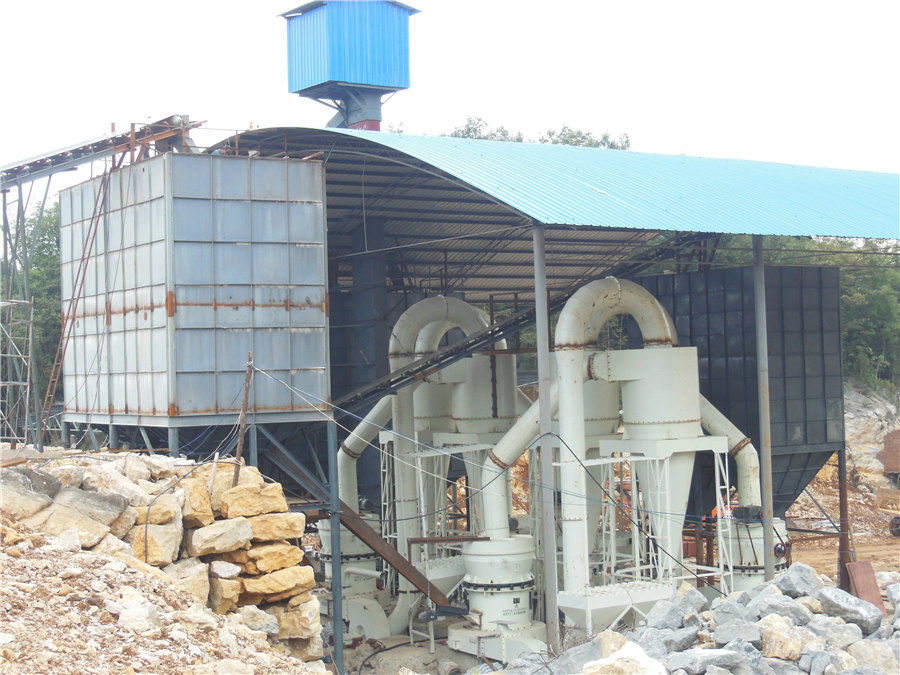
Breaking down energy consumption in industrial grinding mills
2017年1月17日 Other process activities, such as spraying the ore with water for dust control or the fact that runofmine ore moisture is approximately 2%5% are not generally considered (Bleiwas, 2012a)energy requirements across the mill and smelter The new methodology discussed here will integrate downstream processing energy with mineral processing energy, to find the overall most energy efficient circuit design and operating strategy The proposed methodology includes: • determining what grade and recovery positions can be achieved inImproving Energy Efficiency Across Mineral Processing and pilot mill The result will optimize the performance of SAG mills and increase its energy efficienc y The pilot mill will be operated with sample ore/ slurry from participating mine sites Considering the operating conditions, optimal shell lifter , grate and pulp lifter designs will be suggested for achieving maximum energy benefitITP Mining: Improving Energy Efficiency in SAG Mills2023年1月1日 Download Citation Ball mill energy efficiency optimization techniques: A review Ball mills are essential machinery in the mining industry, thermal powerproducing companies, and cement Ball mill energy efficiency optimization techniques: A review
.jpg)
SAG mill optimization insights by measuring inside the mill
Given the status of current energy models and the progress toward measuring inside mills, it is reasonable to think that successfully combining real time data from inside the mill with mill optimizing mathematical models might provide an industry stepchange to the efficacy of energy efficient mill optimizationThis paper shows results of measurements inside a mill and explores These variables were investigated in regard to the Itakpe iron ore A representative sample of 105kg of the iron ore was collected and milled, taking appropriate quantities to study the process variables; the effect of grinding (PDF) Reducing Grinding Energy and Cost A recent publication highlights how gearless grinding solutions can enhance efficiency and support decarbonization in the mining sector Research reveals that Gearless Mill Drives (GMDs) are up to 36% more energyefficient than traditional RingGeared Mill Drives (RMDs) The energy savings linked to GMDs could lead to a reduction of up to 195,000 tons of CO₂ABB releases white paper on Gearless Mill Drive technology’s role Proc of Int Conf on Emerging Trends in Engineering Technology, IETET Use of Energy Efficient Electric Motors in Rice Mill Industry: A Case Study Ranjit Singh1 and Arvind Dhingra2 1 2 Assistant Professor, Guru Nanak Dev Engineering College, Ludhiana Assistant Professor, Guru Nanak Dev Engineering College, Ludhiana (PDF) Use of Energy Efficient Electric Motors in Rice Mill Industry:
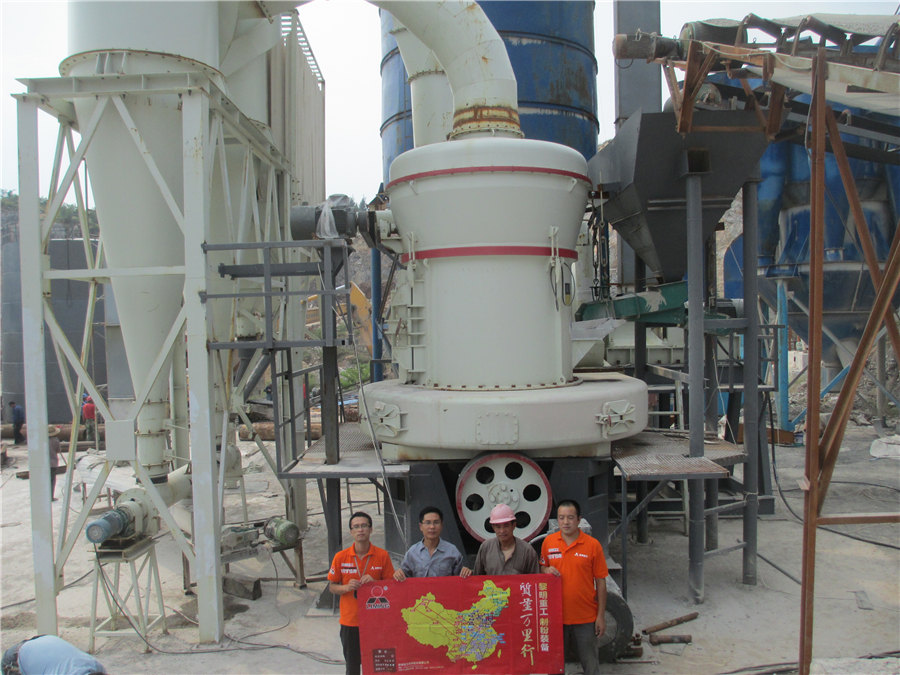
Ecoefficient and costeffective process design for magnetite iron ore
The most significant operating cost (OPEX) variables between options are those relating to power, media and liner consumption The two options including AG mill circuits have between 27 and 32 percent higher power consumption costs relative to Option 4, which utilizes the more energyefficient autogenous grinding technologiesBetween 1993 and 2003, a series of AG and SAG mill pilot plant trials were conducted using Hardinge Ical pilot plant scale SAG mills on numerous ore samples and ranging across a wide variety of AG/SAG mill throughput vs specific Energy ResearchGateThe total energy consumption for ore comminution will further increase within the next decades One contribution to minimise the increase is to use more efficient comminution equipment Verticalrollermills (VRM) are an energyefficient alternative to conventional grinding technology One reason is the dry inbed grinding principleResearch of iron ore grinding in a verticalrollermill2 天之前 Download Citation On Dec 1, 2024, Liana Noor Megashah and others published Energyefficient and improved productivity of cellulose nanofibril processing in wet disc mill by regulating the Energyefficient and improved productivity of cellulose nanofibril
.jpg)
Grinding Modeling and Energy Efficiency in Ore/Raw Material
2022年8月31日 The main concern in ore beneficiation and processing plants is producing the desired product size with the lowest possible energy consumption It has been estimated that grinding consumes up to 4% of global electrical energy and accounts for more than 50% of the total energy used in mining operations