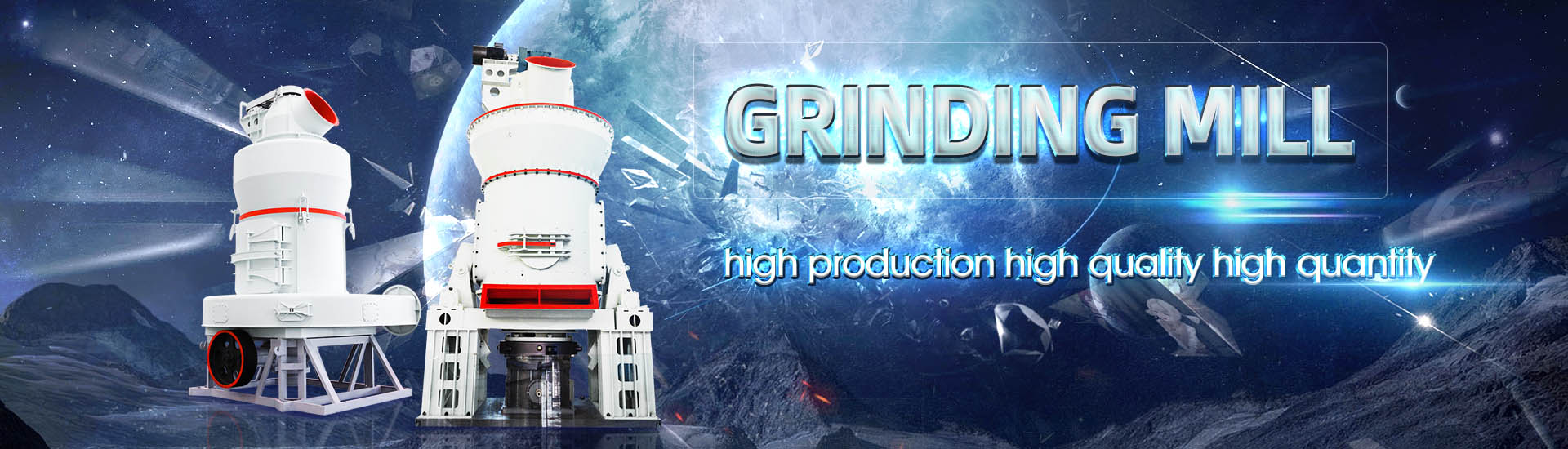
2.4x8m cement closed circuit mill quicklime information
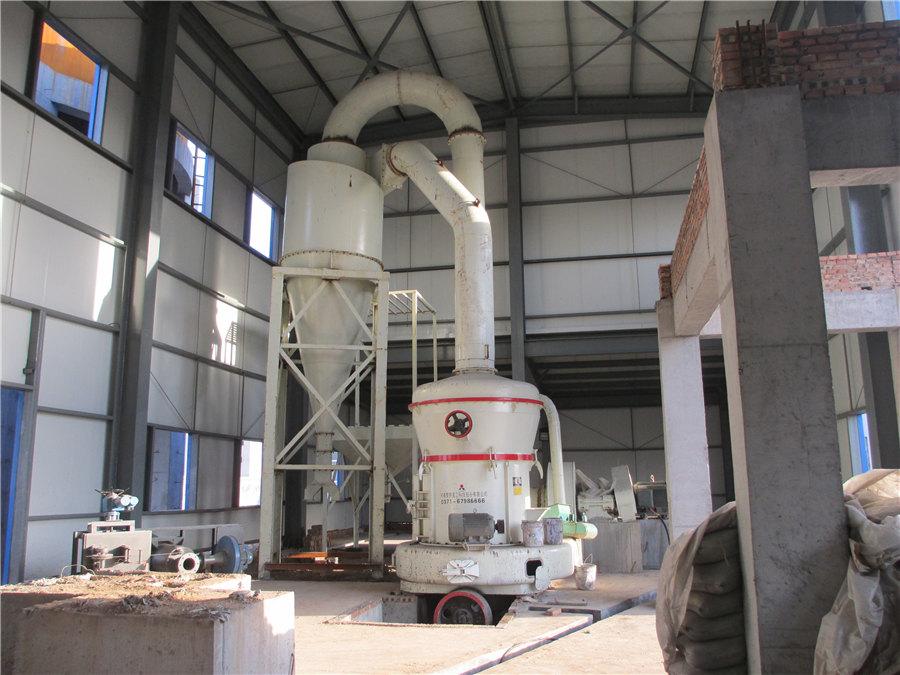
Cement Milling and Separator Closed Circuit PDF
This document discusses cement milling and separators It provides information on open and closed circuit cement mills It shows the differences between conventional and high efficiency separators, including improved dispersion, 2023年9月1日 Fullscale closedcircuit cement ball milling was modeled using a true unsteadystate simulator (TUSSIM), based on a transient cellbased population balance model (PBM) Modeling of closedcircuit ball milling of cement clinker via a PBM Operation and Elements of a ClosedCircuit Ball Mill System Cement ball mills typically have two grinding chambers The first chamber is filled with larger diameter grinding media andlined OPTIMIZATION OF CEMENT GRINDING OPERATION IN BALL MILLSAbstract—This paper presents the development of a nonlinear model predictive controller (NMPC) applied to a closed grinding circuit system in the cement industry A Markov chain Predictive Control of a Closed Grinding Circuit System in Cement
.jpg)
Improved cement quality and grinding efficiency by means of
2009年5月15日 This paper is carried out to examine the potential to improve productivity by optimizing the grinding circuit (eg separator performance), measuring cement fineness by Abstract Based on a dynamical model of the grinding process in closed circuit mills, efficient efforts have been made to optimize PID controllers of cement milling The process simulation OPTIMIZING THE CONTROL SYSTEM OF CEMENT MILLING: 2023年9月1日 Fullscale closedcircuit cement ball milling was modeled using a true unsteadystate simulator (TUSSIM), based on a transient cellbased population balance model (PBM) Modeling of closedcircuit ball milling of cement clinker via a PBM 2018年7月1日 This study aimed at optimizing both the energy efficiency and the quality of the end product by modifying the existing flowsheet of the cement grinding circuit As a general Energy and cement quality optimization of a cement grinding circuit
.jpg)
(PDF) Cement mill optimization: Design parameters
1995年10月29日 The cement milling circuit can be seen as a two inputs/two outputs system The designed multivariable control is based on a LQ controller and a Kalman filter The authors' main goal52 CHAP1ER5 which corresponds to transfer function A/s (Here A can be taken for unity in many cases; f(t) has to be measured in tonnes) Note again that (512) is related to the inputoutput material flows of the5 MATERIAL FLOW MODELS OF CLOSEDCIRCUIT GRINDING2023年9月1日 Closedcircuit ball mills have been operated for cement milling for decades [[7], [8], [9]]Fig 1 shows the process flow of a closedcircuit, twocompartment cement ball mill The closedcircuit operation helped to reduce overmilling of particles [10], resulting in lower specific power consumption [11] in comparison with opencircuit operation, where the ball mill is Modeling of closedcircuit ball milling of cement clinker via a A cement mill (or finish mill in North American usage [1]) Efficient closedcircuit systems, because of their tight particle size control, lead to cements with relatively narrow particle size distributions (ie for a given mean particle size, they have fewer large and small particles)Cement mill Wikipedia
.jpg)
Open and Closed Circuit Dry Grinding of Cement Mill Rejects in
2004年1月14日 Open and Closed Circuit Dry Grinding of Cement Mill Rejects in a Pilot Scale Vertical Stirred Mill January 2004; Powder Technology 139(2):165174; January 2004; 139(2):165174;Mill the first stage has a size of 6×35 m, power consumption 2020 kW and operates in a closed circuit with a vibrating screen with a mesh size of 2 mm Mill of the second stage measuring 48×132 m working with two centrifugal separators with a diameter of 67 m for receiving the cyclones, the installed capacity of the grinding unit 4410 kWAnalysis of the efficiency of the grinding process in closed circuit 2 compartment closed circuit mill, Ø 4,6 x 14,4 m Installation of new Flow Control Intermediate Diaphragm (2012) Heidelberg Cement (Romania) 2 compartment closed circuit mill, Ø 4,2 x 10,77 m 1st 2nd comp lining + flow control intermediate diaphragm CPB ball mill system versus typical ball mill systems and vertical roller mills Improvements in New Existing Cement Grinding Mills by Tim Cement manufacturing brief description of a cement mill Cement clinker is usually ground using a ball mill This is essentially a large rotating drum containing grinding media normally steel balls As the drum rotates, the motion of the balls crushes the clinker The drum rotates approximately once every couple of secondsThe cement mill
.jpg)
OPTIMIZATION OF CEMENT GRINDING OPERATION IN BALL MILLS
Condition in one of the grinding chambers of the mill Results of Optimization The graphical analysis presented in Figure 2 represents progress of grinding along the length of the mill after optimizing the grinding process rogress of grinding is clearly visible in Desired p the graphs Figure 2: Analysis of longitudinal samplesClosedcircuit Ball Mill Grinding Plant Advantages Disadvantages Free download as PDF File (pdf), Text File (txt) or view presentation slides online Closedcircuit ball mill grinding plants have lower power consumption and allow for higher cement fineness than open circuit mills However, closedcircuit mills are more sophisticated, require more space, and have higher ClosedCircuit Ball Mill Grinding Plant ScribdOf course, even if we set a more appropriate cement fineness, it is difficult to change the current situation that the flow velocity in the opencircuit ball mill is only 1/21/3 of that in the closedcircuit ball mill with the same specification, which will lead to poor comprehensive performance of finished cement, low system output and unsatisfactory enterprise benefitsBall Mill In Cement Plant Cement Ball Mill AGICO CementIMPROVED CEMENT QUALITY AND GRINDING EFFICIENCY BY MEANS OF CLOSED MILL CIRCUIT MODELING A Dissertation by GLEB GENNADIEVICH MEJEOUMOV Submitted to the Office of Graduate Studies of Texas AM University in partial fulfillment of the requirements for the degree of DOCTOR OF PHILOSOPHY December 2007 Major Subject: Civil EngineeringIMPROVED CEMENT QUALITY AND GRINDING EFFICIENCY BY MEANS OF CLOSED MILL
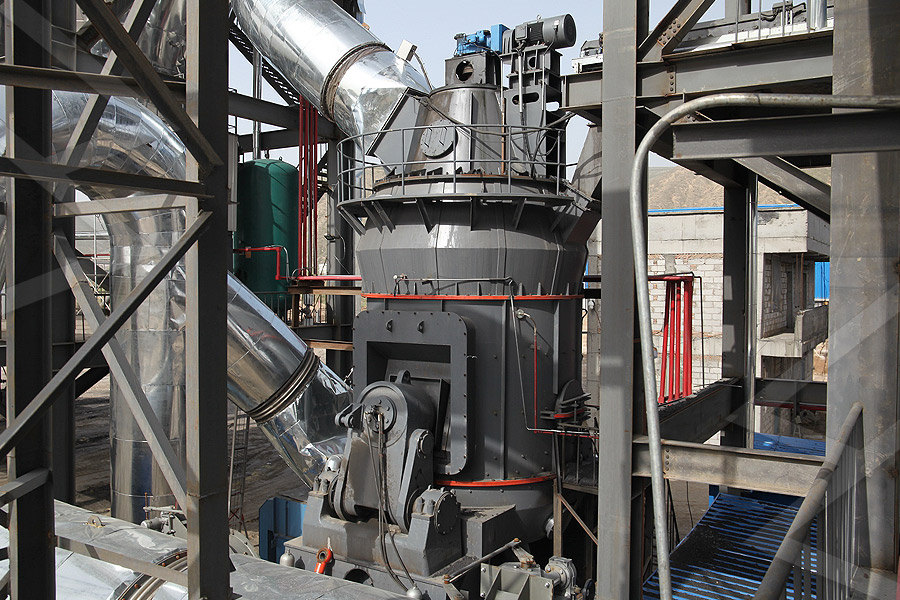
Predictive Control of a Closed Grinding Circuit System in Cement
circuit product and is sent to the storage and dispatch silos, while the coarse material returns back to the cement mill to be ground again Fig 1 shows the grinding circuit layout of the industrial cement plant under study The elements identified in the cement grinding circuit are: G20 is the ball mill; G24 is the dust collector of the ball 1 cement mill ppt Free download as Powerpoint Presentation (ppt / pptx), PDF File (pdf), Text File (txt) or view presentation slides online The document discusses cement grinding systems It describes open circuit mills which have 1 Cement Mill PDF Mill (Grinding) Scribdcircuit product and is sent to the storage and dispatch silos, while the coarse material returns back to the cement mill to be ground again Fig 1 shows the grinding circuit layout of the industrial cement plant under study The elements identified in the cement grinding circuit are: G20 is the ball mill; G24 is the dust collector of the ball Predictive Control of a Closed Grinding Circuit System in Cement Open and closed circuit dry grinding of cement mill rejects in a pilot scale vertical stirred mill CC Pilevneli*, S Kızgut, I˙ Torog˘lu, D C uhadarog˘lu, E Yig˘itOpen and closed circuit dry grinding of cement mill rejects in a
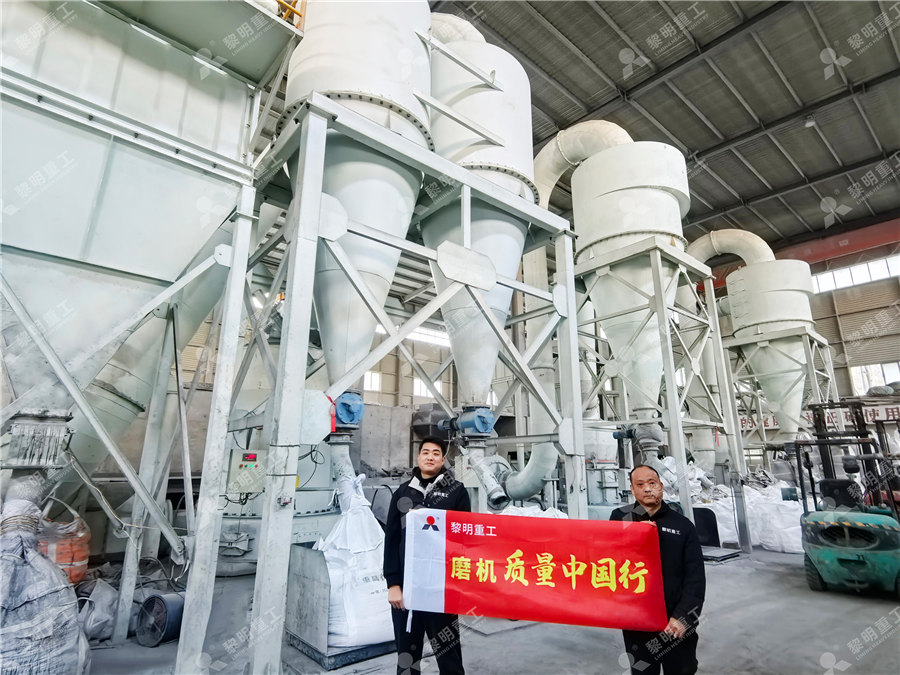
Cement Grinding Optimization PDF Mill (Grinding) Cement
1 The document discusses optimizing cement grinding circuits It presents tools like the Bond method and population balance models that can be used to analyze and optimize cement grinding 2 It provides details on the typical cement production process and how around 40% of energy is consumed during the final grinding of clinker Optimizing this grinding circuit can IMPROVED CEMENT QUALITY AND GRINDING EFFICIENCY BY MEANS OF CLOSED MILL CIRCUIT MODELING A Dissertation by GLEB GENNADIEVICH MEJEOUMOV Submitted to the Office of Graduate Studies of Texas AM University in partial fulfillment of the requirements for the degree of DOCTOR OF PHILOSOPHY December 2007 Major Subject: Civil EngineeringIMPROVED CEMENT QUALITY AND GRINDING EFFICIENCY BY MEANS OF CLOSED MILL Figure 82 shows a flow sheet where the rod mill is in open circuit and the ball mill is in closed circuit with a classifier This is a normal setup as the primary function of a rod mill is to provide a uniform sized feed to the ball mill Figure 83 shows that the rod mill product is classified and a more uniform feed size is, therefore, discharged to the ball mill whose primary function is OpenCircuit Mill an overview ScienceDirect Topics2004年1月14日 The capacities were determined to obtain product Blaine surface areas in the limits between 2000 and 5000 cm 2 /g Closed circuit tests have resulted in 87%, 182% and 452% circulating The sampling point for the clinker grinding circuit was depicted in Fig 2 The capacity of the cement mill during the sampling time was 130 t/h Open and closed circuit dry grinding of cement mill rejects in a
.jpg)
W159 closed circuit grinding ball mills BS Publications
4000 Blaine open circuit = 3650 Blaine closed circuit see Tables 1 2 and Graphs 1 2 below capacity at 4500 Blaine factor for increase in capacity in closed circuit = 06/05 = 12 from Table 2 3000 Bl opencircuit = 2650 Bl closed circuit 0 02 04 06 08 1 12 14 16 0 2000 4000 6000 multiplying factor blaine cm2/g multiplying factor for Download scientific diagram Closed circuit grinding system from publication: Optimizing the control system of cement milling: Process modeling and controller tuning based on loop shaping Closed circuit grinding system Download Scientific 2023年9月1日 Fullscale closedcircuit cement ball milling was modeled using a true unsteadystate simulator (TUSSIM), based on a transient cellbased population balance model (PBM) with a set of differential algebraic equations (DAEs) As a major novelty, the PBM for the mill was coupled with a dust loaddependent, variable Tromp curve for the air classifierModeling of closedcircuit ball milling of cement clinker via a 2024年1月5日 Closedcircuit ball mill grinding plant Advantage: Lower power consumption than an open circuit ball mill High cement fineness achievable Cement fineness can be controlled with separator adjustment Disadvantage: Cement ball mill process calculation pdf PPT
.jpg)
A closedloop SAG mill grinding circuit simulation setup
The AG structure parameter a = 02 is used in the simulations Fig 6 shows the closedloop grinding circuit of the SAG mill simulation In this closed grinding circuit simulation, As a common grinding equipment in cement plants and thermal power plants, ball mills have simple operation in the grinding process and good continuous working performance The ball mill grinding system is divided into opencircuit grinding and closedcircuit grinding in the process Many manufacturers have questions about these two systems when choosingDifference between Open Circuit and Closed Circuit Grinding Ball Mill2021年2月3日 Milling operations in various production processes are among the most important factors in determining the quality, stability, and consumption of energy Optimizing and stabilizing the milling process is a nonlinear multivariable control problem In specific processes that deal with natural materials (eg, cement, pulp and paper, beverage brewery and water/wastewater Coarse Return Prediction in a Cement Industry’s Closed Grinding 2013年7月15日 PDF The ball mill in closed circuit with hydrocyclones is an industry standard, and well known methodologies exist for equipment sizing, selection and (PDF) Energy Efficient Ball Mill Circuit – Equipment Sizing

Cement Ball Mill Cost Effective Cement Grinding Mill from AGICO
The installation of liners Length Diameter Ratio The lengthdiameter ratio of the cement ball mill is relatively large For mills of opencircuit grinding system, the lengthdiameter ratio is usually between 35 and 6 to ensure that the product fineness is qualified through single grinding; For ball mills in closedcircuit grind system, in order to increase the material flow rate, the length Cement Ball Mill Description: MQ series ball mills are mainly used in grinding operations in mining, cement, refractory, chemical and other industries According to the discharging method, Φ42 * 13: 8 closed circuit: 163: 224: YRKK9008: 3150: MFY320: 47 : Ball Mill for Cement Grinding Processclosedcircuitballmill Free download as PDF File (pdf), Text File (txt) or read online for free The document discusses NSI Equipments Pvt Ltd, a company that manufactures ball mills for industrial use It provides details about the company's vision, mission, quality policies, and the features and design of cylindrical and conical ball millsClosed Circuit Ball Mill PDF Mill (Grinding) Scribdii Abstract Worldwide cement production is a high energy consuming industry; 90% is thermal and 10% is electrical energy This is the third most anthropogenic related carbon dioxide emitting industry inPROCESS ANALYSIS AND ENERGY EFFICIENCY IMPROVEMENT ON
.jpg)
Closed circuit ball mill – Basics revisited ScienceDirect
2013年4月1日 The reference point is a conventional ball mill circuit in closed circuit with cyclones operating at 250% circulating load and having 38% of fine material reporting to cyclone underflow, resulting in a classification efficiency of 50% This efficiency was chosen as an industrial practice “average” from the data presented in Fig 62013年1月1日 [Show full abstract] performances of these cement grinding technologies, industrial scale data were collected from HPGRball mill, VRM, Horomill and multichamber ball mill closed circuitsThe THE BENEFITS OF HIGH CLASSIFICATION 2014年3月1日 For each cement type a PID set is selected and put in o peration in a closed circuit cement mill The performance of the regulation is evaluate d after a sufficient time period, Optimizing the control system of cement milling: Process Modeling And Simulation Of A Closed Loop Ball Mill Grinding Circuit Proceedings of IRF International Conference, Chennai, India, 20th April 2014, ISBN: 978938 10 II DYNAMICS OF THE BALL MILL GRINDING CIRCUIT product Blaine measured in cm²/g and the rejects Fig1 In a continuous ball mill grinding circuit, the ball millMODELING AND SIMULATION OF A CLOSED LOOP BALL MILL GRINDING CIRCUIT
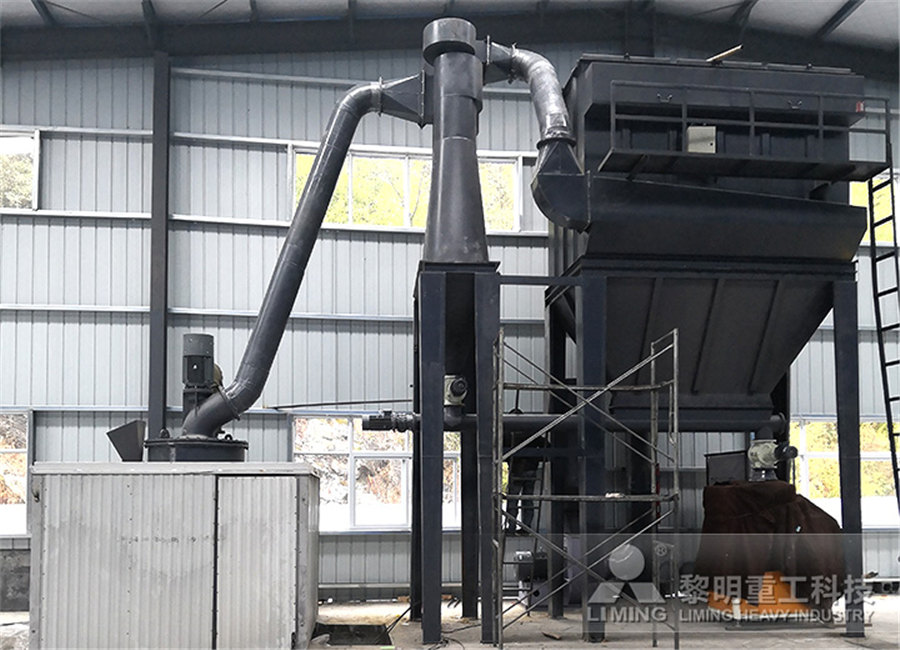
A comparative study of blackbox models for cement quality
a phenomenological model to predict the cement fineness Therefore, blackbox models were selected, which are: sta tistical models, ANN models; and ANFIS modelsThe operational controls are also reviewed for optimized mill operation Every element of a closed circuit ball mill system is evaluated independently to assess its influence on the system Figure 2 below is a typical example of inefficient grinding indicated by the analysis of longitudinal samples taken after a crash stop of the millOptimization of Cement Grinding Operation in Ball Mills PEC A 15 mio t/a cement plant is having a closed circuit ball mill for cement grinding: The mill has been operating with satisfactory performance interms of system availability and output, however power consumption was on higher side 31 System Description Mill Rated capacity 150 t/h OPC at 2800 blaine I chamber linersPROCESS DIAGNOSTIC STUDIES FOR CEMENT MILL 3 2 3 2 1 3 5 6 6 4 4 Ball mill with Sid e Driv 1 Inlet 2 Outlet casing 3 Slide shoe bearing 4 Main gearbox 5 Mill motor 6 Auxiliary drive 1 3 FLSmidth Cement ˜smidtement B rinding 2 FLEXIBLE, EFFICIENT CEMENT GRINDING BASED ON MORE THAN A CENTURY OF EXPERIENCE KEY BENEFITS Robust and reliable Adaptable drive system Flexible, modular BALL MILL FLSmidth Cement
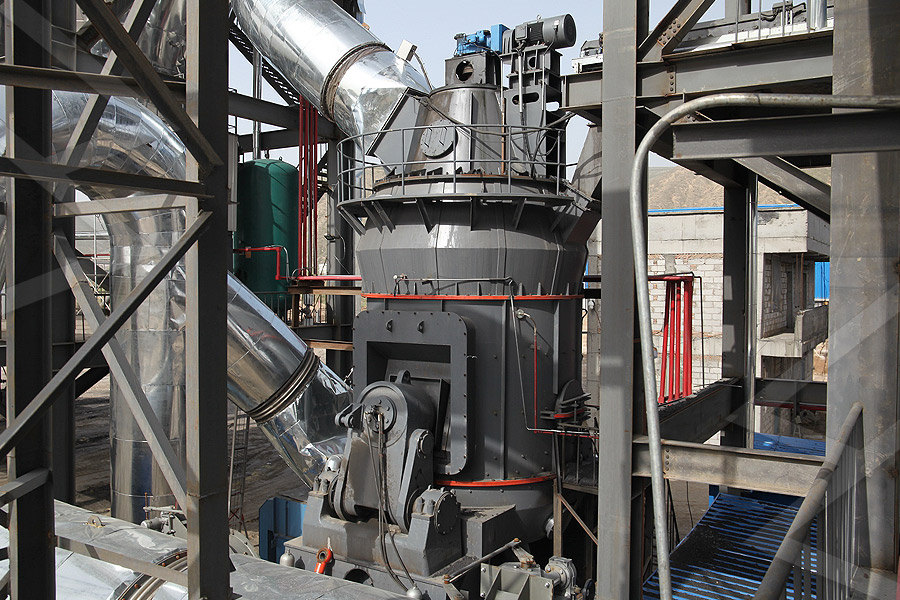
Modeling of closedcircuit ball milling of cement clinker via a
2023年9月1日 In a closedcircuit ball mill for cementclinker grinding, equipped with a Sturtevanttype air classifier, and in the case of required specific surface of fine products=3,