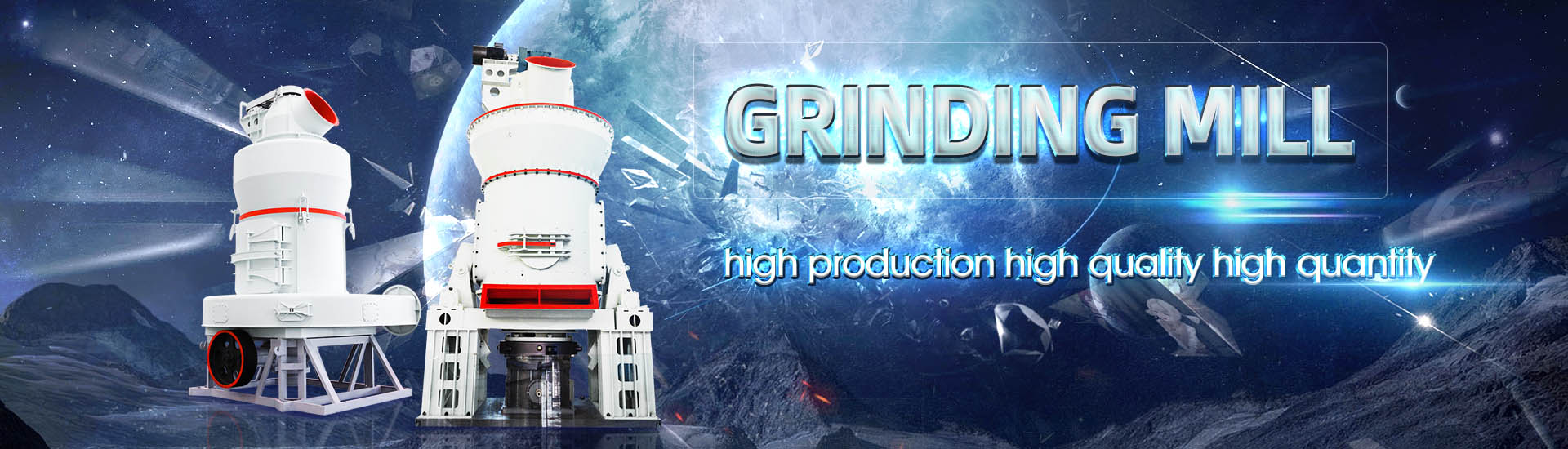
Roller x crusher work analysis
.jpg)
Design, Fabrication and Testing of a Double Roll Crusher
Design and production of an indigenous roll crusher from locally available materials for low hardness rocks was carried out in this work The throughput capacity of the machine was 2018年11月7日 By means of orthogonal experiment, simulation analysis considers the influence factors of the roller spacing, the rotational speed and the pitch angle The best test scheme and the order of(PDF) The Influence of the Structure of Double Toothed 2016年5月25日 Reduction of solid particles is achieved by crushing, grinding, cutting and vibrating [1] Particle reduction is a paramount aspect of a lot of industries; it is used for Design, Fabrication and Testing of a Double Roll Crusher2016年1月1日 Roll crushers consist of two or more adjacent rolls placed parallel to each other and rotated in opposite directions Single roll crushers are also available which rotate a single Roll Crushers ScienceDirect

Comparison of Crushing Effect of Differently Shaped
2023年6月21日 The mechanical analysis of the crushing process reveals that the disc crushing roller (DCR) has the characteristics of large unitlength kneading area; the spiralnotched serrated crushing roller (SNSCR) has transverse 2022年3月29日 Analysis of the designs of roll crushers and mills for the disintegration of lumpy and granular materials shows that they exist in numerous standard sizes, but conventional(PDF) Roll crushers and mills (Design review)In this paper, by analyzing the crusher mechanism of double toothed roller crusher, on the basis of previous research, the author analyzes the influencing factors and the order of crushing The Influence of the Structure of Double Toothed Roller Crusher 2021年12月11日 Roller crusher is widely used in solid and block material pulverizing Roll gap between the rollers is usually adjusted to satisfy the particle size of output material In order to 3,'ZLWKGHFLVLRQIDFWRUVHOI FRUUHFWLRQ IOPscience
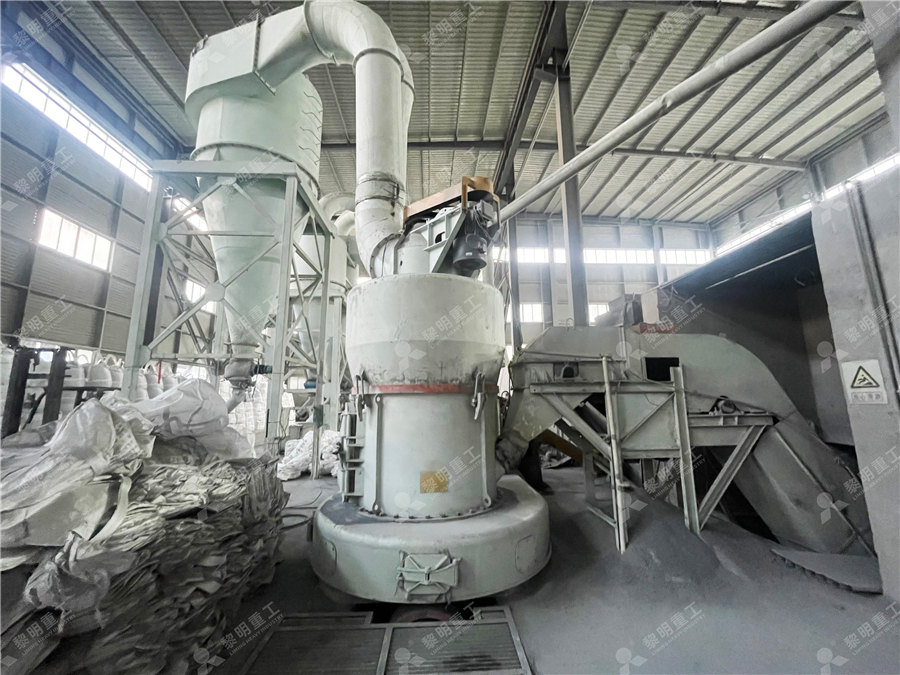
Justification of Rational EnergyPower Parameters of the Drive of
2023年9月4日 Based on the results of the study of the crushing process of metallurgical coke, rational energypower parameters of roller crushers used for fractional preparation of solid Robby Rizki Rukmana, Melody Lingua Franca, Safaruddin, Deddy Abstrak Penelitian ini untuk mengetahui beberapa faktor yang mempengaruhi produktivitasEvaluasi Produktivitas Double Roller Crusher Untuk Mencapai Roller diameter (mm) Roller length (mm) Max Feeding Size (mm) Process capacity (t/h) Roller rotation (r/min) Motor power (kw) Model 2PG400×25 2 2200×834×830 C3800 C8 The crusher should work steadily and there should be no vigorous vibration Each fastening part should be reliable The lubrication parts should be fullyOnestop Turnkey ROLL CRUSHER FTM Machinery2022年3月29日 Analysis of the designs of roll crushers and mills for the disintegration of lumpy and granular materials provided the original work is properly cited УДК 621926302728(04883 (PDF) Roll crushers and mills (Design review)
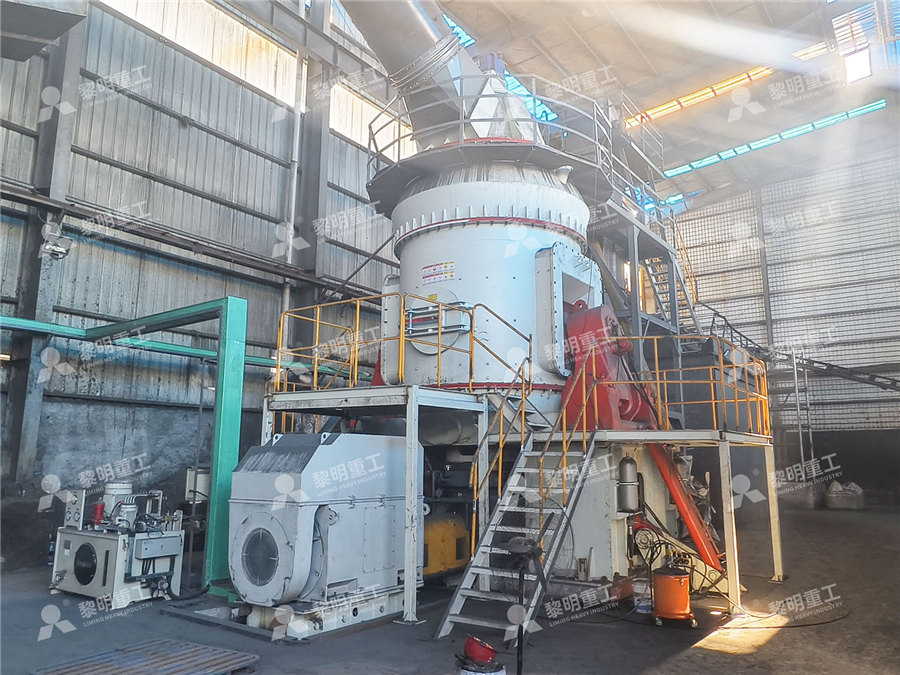
Roll Crusher with Stable Performance Fote Machinery
After the noncrushed materials are discharged, the spring can help recover the gap between the rollers to the original condition and the roll crusher continues to work 3 factors affecting roll crusher price The price of roll crushers is influenced by the following factors: Quality assurance of FTM Machinery roll crushers Quality2019年1月2日 Failure of crusher components has considerable influence on the productivity of a crushing plant In order to improve performance and operational reliability, its critical components are needed to be identified to make replacement in time before any catastrophic failure happens Though traditional maintenance practices exist in crushing plants, a methodical analysis of Failure rate analysis of Jaw Crusher: a case study Sādhanā2021年4月1日 This work shows, for the first time, a systematic wear and damage analysis on a novelty roller crusher component used in the iron ore mining industry Crusher suffers from complex abrasiveimpact load during the comminuting the mineral ore in processing plants, which induce severe damage and defects that can result in a decreased performance or in a crusher Roller crushers in iron mining, how does the degradation of Minimum value of deformation is 0 mm which is at bearing position Maximum value of total deformation is 024424 mm at pinion end of discharge roller B Static Analysis of Discharge Roller: C Static Analysis of Feed Roller: CAD model, meshing, material, boundary conditions are same as that of top rollerIJERTStatic Structural Analysis of Crushing Rollers of Three Roller
R)8OC`6F[ZIB.jpg)
Roll Crushers ScienceDirect
2016年1月1日 In conventional work, Bond’s work index is usually accepted as the measure of the net specific energy required for comminution Klymowsky and Liu [13] found that Bond’s work index was not quite applicable in the case of the HPGR as it was determined using a tumbling mill where repeated impact and grinding forces were responsible for size reduction2023年3月11日 Single roller crushers find application in various industries, including mining, construction, and chemical processingThey are used to crush materials such as coal, limestone, gypsum, and claysAdditionally, they can be used for secondary crushing in combination with other types of crushers One example of a successful implementation of single roller crushers Single Roller Crusher Simple And Efficient Crushing EquipmentRoller Crusher is Applications: Aggregates Shaping, Mechanism sand, Bituminous Concrete, Metal Mine, Chemical, Order data analysis and preparation of raw materials 4 machine Machine for quantitative powder adopts an airflow feeding control structure to automatically complete the work process of bag clamping, Roller crusher SHANGHAI LATITUDE HEAVY INDUSTRY deposit The EDS analysis of the weld deposit as compiled in Table 3 indicates that a stainless steel (SS) electrode was used for TIG welding of the roller pin with the cage ring Discussion Failure of the cylindrical roller bearing occurred from the ends of the roller pins where they were welded with the cage ringFailure Analysis of a Cylindrical Roller Bearing from a Rolling Mill
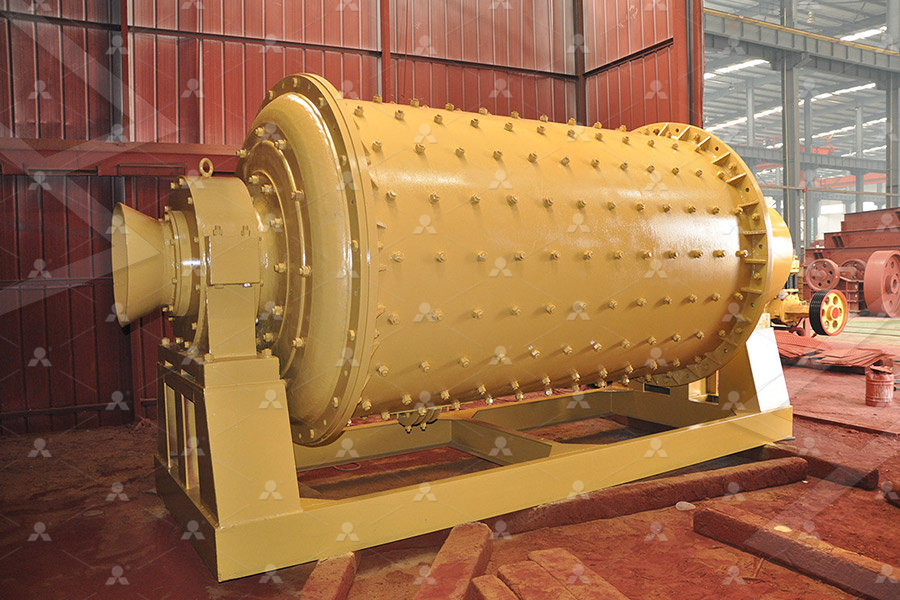
Design and Analysis of Belt Conveyor Roller Shaft
shaft for 170 to 180 create model Analysis using hyperwork By using design failure modes and effects Analysis (DFMEA) for systematic, proactive method for identifying where and how it might fail pulleys Keywords — Existing Roller Shaft, Analysed Roller shaft with DFMEA I INTRODUCTION As a kind of continuous transportation2014年9月16日 A twinroll crusher is selected, like those given in the Roll Crusher capacity Table above, to serve as the reduction crusher The smallest, 24 x 16 roll crusher shown in the Roll Crusher capacity Table above has Crusher Efficiency Calculations 911Metallurgistconsequences This report highlights the work done by various researchers for bearing fault detection describes the suitability of different cause of failure Time domain analysis, frequency domain analysis, and wavelet transform analysis has DIAGNOSTICS AND ANALYSIS OF DIFFERENT TYPES OF ROLLER 2019年7月31日 The necessary press force is created by a hydraulic—pneumatic system which works like a spring The movable roller is actuated towards the static roller with the help of a hydraulic cylinder to grind the clinkers fed from the vertical chute/hopper over the rollers The roller comprises of a steel shaft and a mounted tire made of “bainite”Fault Diagnosis and Root Cause Failure Analysis of Press Roller
.jpg)
3D design and analysis of the crushing roller of a highpressure
2002年10月1日 The crushing roller is one of the main parts of a highpressure grinding roller, which is a type of highly efficient ore crushing equipment In the work reported in this paper, a kind of assembled 2024年4月19日 A shorthead cone crusher has a short crushing chamber and it is designed for the production of finer output sizes, generally between 6 mm and 25 mm A fine cone crusher, also known as a tertiary cone crusher, is used for the production of They are manufactured to produce very fine output sizes, mostly below 6 mmTypes of Crushers Explained: Everything You Need to Know JXSCThis work intends to illustrate vibration behavior of roller bearings as a function of lubricant viscosity Experimental tests were conducted in roller bearings, lubricated with mineral oil of three different viscosity grades (ISO 10, 32 and 68) under different loads and shaft speedsA Review Paper On Failure Analysis of Cylindrical Roller BearingIn brick making field, roller crusher is a common machine But how does a roller crusher work ? This video presents what is inside the roller crusher and howHow a roller crusher works YouTube
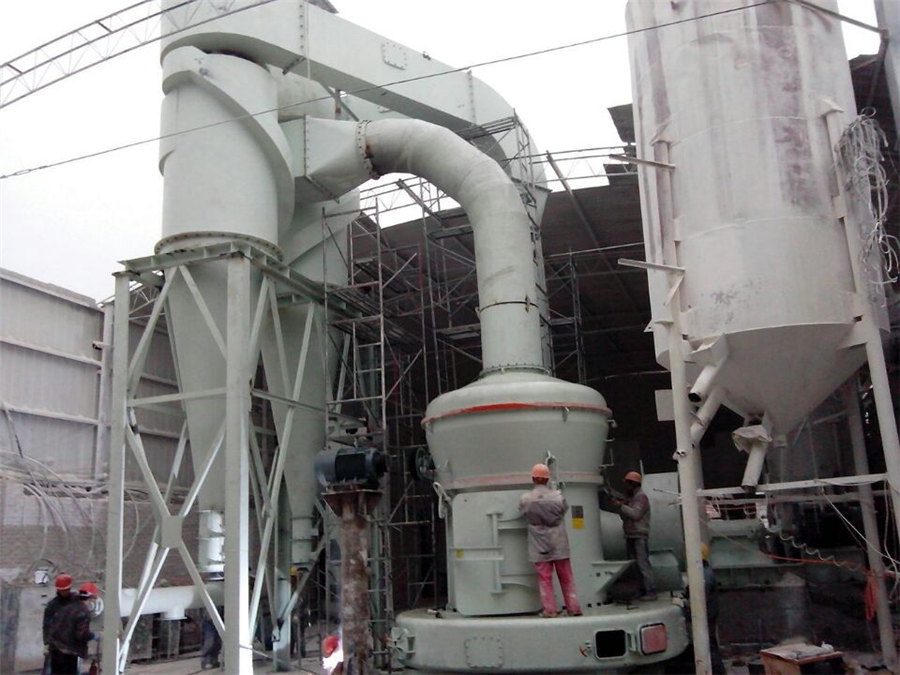
(PDF) Static Structural Analysis of Crushing Rollers of Three Roller
2015年6月1日 Walmiki SRathod, Chetan T Rathod (2012), Design and Analysis of Two Roller Sugar mill using FEA Technique, International Journal of Scientific Engineering and Technology, volume No 1, Issue No 2021年4月1日 This work shows, for the first time, a systematic wear and damage analysis on a novelty roller crusher component used in the iron ore mining industry Crusher suffers from complex abrasiveimpact load during the comminuting the mineral ore in processing plants, which induce severe damage and defects that can result in a decreased performance or in a crusher Roller crushers in iron mining, how does the degradation of 2022年8月14日 Figure 210 shows the structure and working principle of the roller crusher The roller 1 is mounted on a fixed bearing 4 on the frame 3, and the roller 2 is supported by a movable bearing 4' The two rollers are respectively driven by two motors and are rotated in How does the roller crusher work?2022年8月21日 The design has been developed for a singleroll crusher with the forced supply of destroyed material into the crushing zone []The capture of a crushed piece occurs due to the stop located on the roll (see Fig 1); in this case, the condition for formation of a complex stress state in the crushed piece is observed, and the energy consumption is reduced by 39–40% []Capacity Calculations of the Crasher with Stops on a Roll
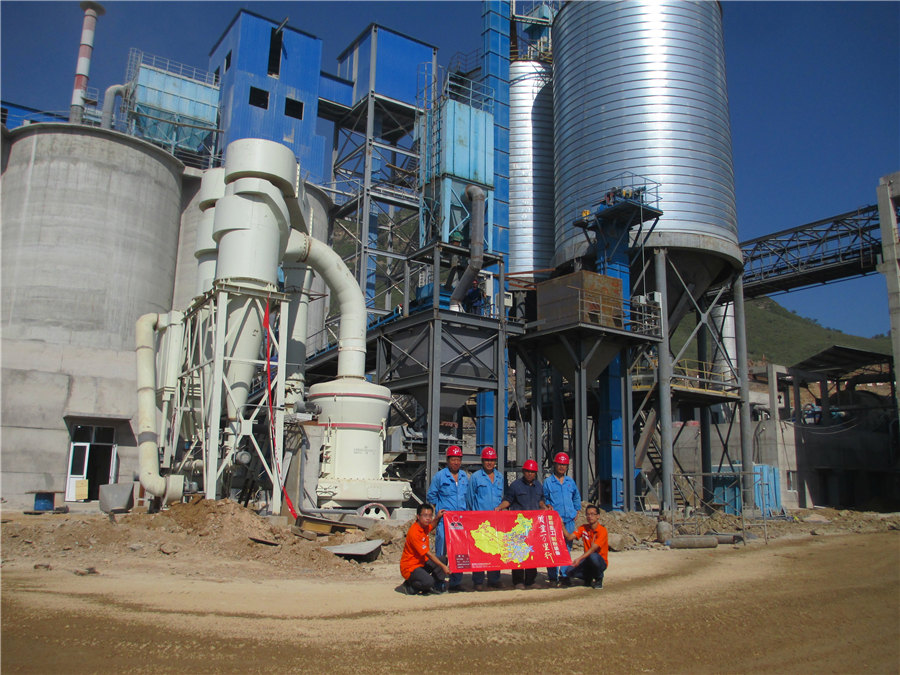
Mechanical structure of roller crusher ResearchGate
Download scientific diagram Mechanical structure of roller crusher from publication: A CNNbased interactive contrast enhancement algorithm, called IceNet, is proposed in this work, Single Roll Crushers Single Roll Crushers are typically used as primary crushers that provide a crushing ratio of up to 6:1 They crush materials such as ROM coal, mine refuse, shale, slate, gypsum, bauxite, salt, soft shale, etc, while producing minimal finesDesigned with intermeshing roll teeth and a curved crushing plate, they are extremely effective in reducing slabby feedsRoll Crushers McLanahanMinimum value of deformation is 0 mm which is at bearing position Maximum value of total deformation is 024424 mm at pinion end of discharge roller B Static Analysis of Discharge Roller: C Static Analysis of Feed Roller: CAD model, meshing, material, boundary conditions are same as that of top roller(PDF) Static Structural Analysis of Crushing Rollers of Three Roller 2021年7月18日 To find out the obstacles that make the crusher unit work not achieved, it is necessary to analyze the tool itself analysis is needed to determine the efficiency and productivity of the unit in Evaluasi Produktivitas Double Roller Crusher Untuk Mencapai
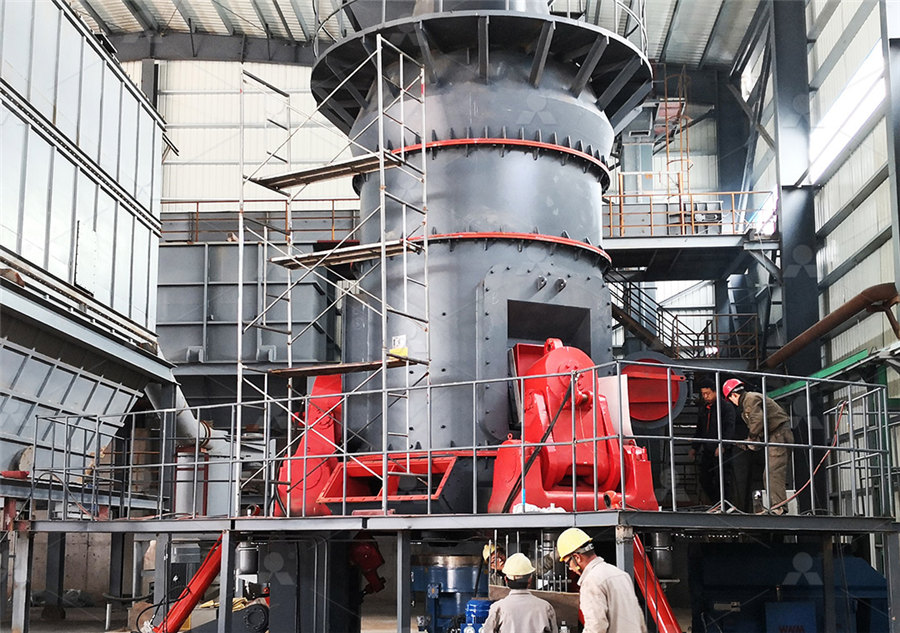
Analysis and Optimization of Grinding Performance of Vertical Roller
2022年1月23日 340 mm, roller width 105 mm, roller inclination 13 °, millstone radius 300 mm, millstone revolution rate 0–72 rpm, motor revolution rate 0–1000 rpm, maximum motor power 15 kW, loading Abstract : Sugarcane roller process is the key piece of sugar industry The primary goal of processing is to isolate the sucrosecontaining juice from the stick The extraction of juice in a factory is accomplished by pressing arranged stick between two rolls In this technique the strong model of the segment is subdivided into littler components, imperatives and burdens are [PDF] Design and Analysis of Rolling mill crusher shaft for weight The aim of this work is to synthesize a cam mechanism with translating roller follower based on optimization approaches and reliability analysis The study consists of two parts At first, this study performs preliminary deterministic optimization to find the optimum size of a cam system and to ensure its high operating performanceOptimization and a reliability analysis of a camroller JSTAGEEssa RC3000 Rolls Crusher If you’re looking for a larger feed size, try the Essa RC3000 This rolls crusher is a dependable and sturdy midrange secondary crusher that has a maximum feed size of 40 mm It’s also packed with considerably more power Floor or bench mountMidrange rolls crushers – tough on any material
.jpg)
(PDF) Design and Analysis of Rolling mill crusher shaft for weight
References [1]Shinde VV etal Weight Reduction and Analysis of Sugar Mill Roller Using FEA Techniques Vol 5 Issue 1 January 2015 [2]E Vijaya Kumar etal Design and Analysis of Rotor Shaft Assembly of Hammer Mill Crusher Volume3, Issue2, April 2013 [3] Santosh Y Salunkhe etal Static Structural Analysis of Conventional Sugar Mill Roller Shaft for Ø40”x 80” Milling 2023年6月22日 Figure 3 shows a sieve analysis for a grind from a hammermill and a roll crusher Each grind produced a distribution with a mean particle diameter of approximately 710 microns, but the distribution from the roll Hammermill and roll crusher maintenance and operationWahyu Adi Saputra, Safaruddin, Melody Lingua Franca adalah membuat Gudang penyimpanan tanah liat (clay storage), selanjutnya untuk mengatasi ukuran / bongkahan tanah liat yang tidak sesuai dengan Analisa Roller Crusher Untuk Mereduksi Ukuran Bahan Galian References [1]Shinde VV etal Weight Reduction and Analysis of Sugar Mill Roller Using FEA Techniques Vol 5 Issue 1 January 2015 [2]E Vijaya Kumar etal Design and Analysis of Rotor Shaft Assembly of Hammer Mill Crusher Volume3, Issue2, April 2013 [3] Santosh Y Salunkhe etal Static Structural Analysis of Conventional Sugar Mill Roller Shaft for Ø40”x 80” Milling (PDF) Design and Analysis of Rolling mill crusher shaft for weight
.jpg)
Safe Job Procedures For Crusher Operations
Roller Crusher Safe Work Procedure Mobile Crusher Crusher South Africa In Fixed Plant Operations operating jaw crusher, an operator injured his 26 Documented safe work procedures are provided for crusher maintenance Download SWMS for Concrete Crusher Operation Work Method Statement (x 1 /x 2) and wi = work index In this work Q = 356 t/hr and x 1 = 75mm A roll gap of 5mm had already been specified and x 2 is less than or equal to this value Maximum power is drawn for x 2 = 5mm Thus Maximum power requirement for limestone, with w i of 7 kWh/t [8] becomes, P = 356 x 15x 7 = 374kW Electric motors are rated in horsepowerDesign, Fabrication and Testing of a Double Roll Crusher2023年11月21日 In the present incident, one of the rollers of grinding mill in cement plant failed during operation, exhibiting longitudinal cracking over inner surface Deposition welding was carried out just before the incident to match the wornout profile of the roller Investigation revealed that the subsurface of the cracked region contained discontinuities like blow holes Operational Failure of Vertical Roller Attached to a Grinding Mill 2017年3月10日 I believe his crusher, with the improved eccentric, is the best thing on the market today” A jawcrusher constructed upon certain lines, having a jawopening 10 in by 20 in, and weighing not over 15,000 lb, will take a steady stream of 10in runofmine and reduce it without sliming to 1in sizeRoll Crushers 911 Metallurgist