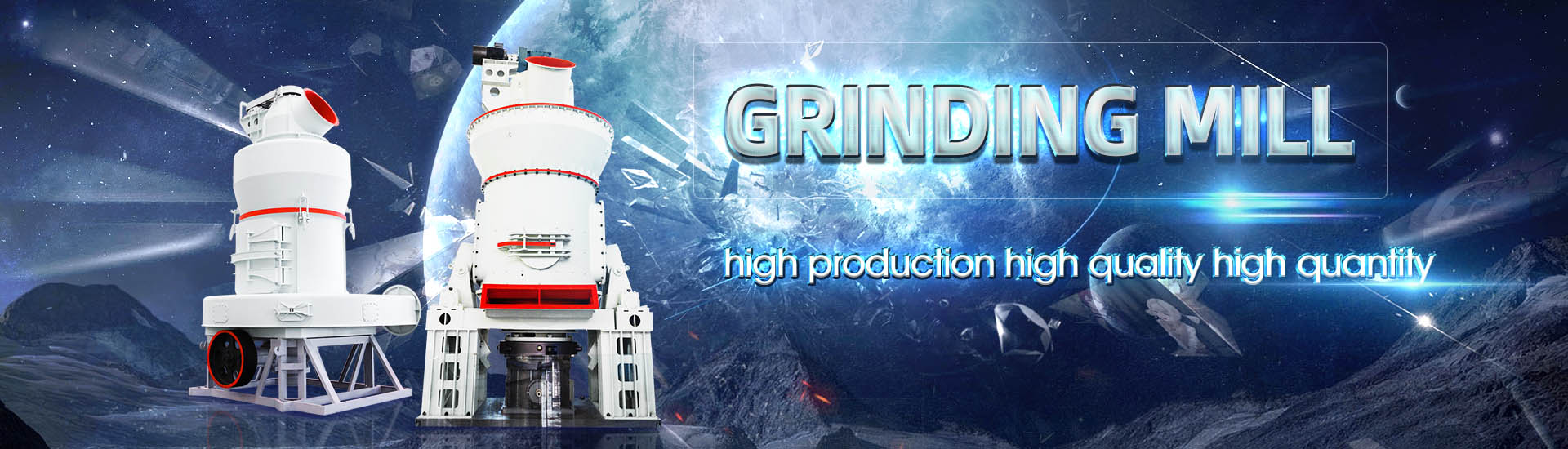
Introduction to rotary kiln cement energysaving powder grinding production line
.jpg)
Rotary kiln process: An overview of physical mechanisms, models
2023年2月25日 Beginning with the research conducted on directly heated rotary kilns for cement applications, this review extends the scope of application to other fields, including waste, Beginning with the research conducted on directly heated rotary kilns for cement Rotary Kiln Process2023年2月25日 Beginning with the research conducted on directly heated rotary kilns for cement applications, this review extends the scope of application to other fields, including waste, Rotary kiln process: An overview of physical mechanisms, models 2014年5月1日 In this study, thermal performance of the rotary kiln presented in a cement plant is investigated using energy analysis based the first and second laws of thermodynamics The Analysis of the parameters affecting energy consumption of a
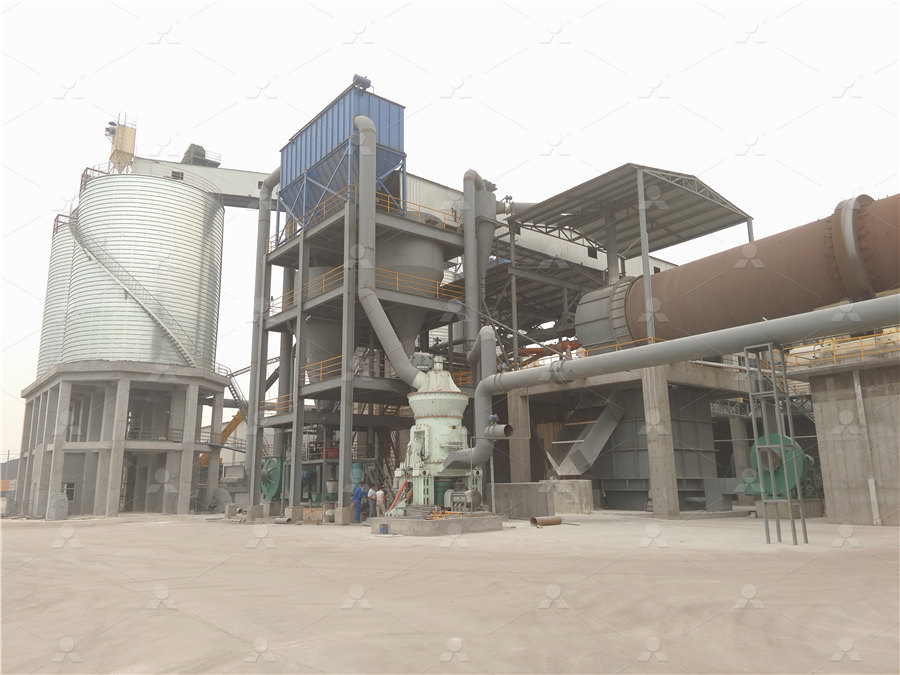
Rotary kiln process: An overview of physical mechanisms, models
The rotary kiln is used in many solid processes, including drying, incineration, heating, cooling, humidification, calcination and reduction This widespread application can be attributed to This report provides information on the energy savings, costs, and carbon dioxide emissions reductions associated with implementation of a number of technologies and measures Energy Efficiency Improvement Opportunities for the Cement 2014年5月1日 In this study, the effects of refractory bricks and formation of anzast layer on the specific energy consumption of a rotary kiln are investigated Thermodynamic analysis of the Analysis of the parameters affecting energy consumption of a 2016年2月1日 An electrical system for efficient kiln drive operation was designed, developed, simulated and installed to improve the mechanical operation of the incorporated machinery, Energy savings and operation improvement of rotating cement
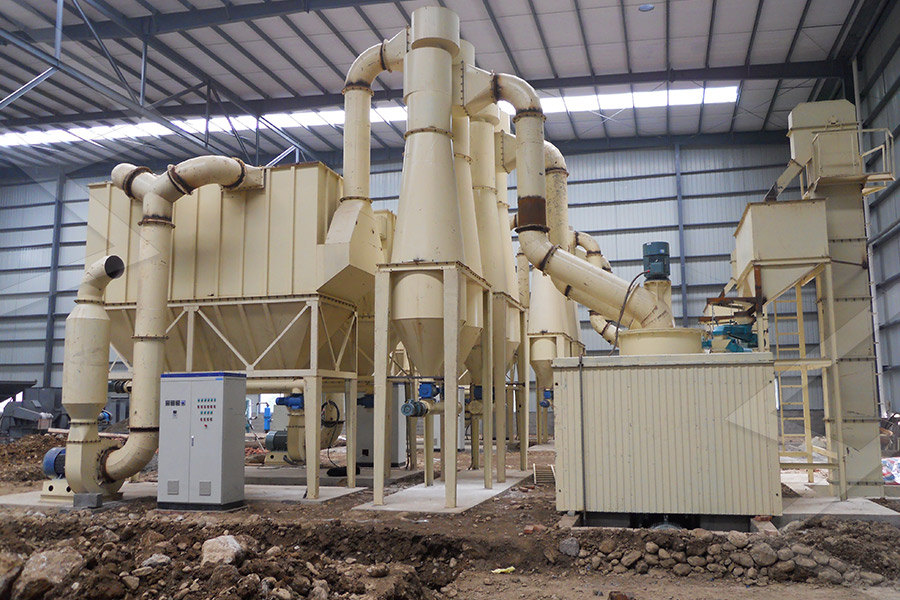
Energy Conservation Measures In Kiln For Clinker Production
For better energy efficiency in kiln, requires the implementation of energy conservation measures in kiln in order for optimum performance and energy saving of kiln The cement process, have 2006年3月1日 Rotary cement kilns are used for converting calcineous raw meal into cement clinkers In this paper, we discuss and evaluate possible ways of reducing energy Modeling of Rotary Cement Kilns: Applications to Reduction in 2020年9月5日 In this study, the operational data from a cement factory are gathered and the relationships between variables analyzed via using ANN via MATLAB toolbox ANN proposed Improvement of a cement rotary kiln performance using artificial Description of Horizontal Grate Cooler: Our HCFC horizontal grate cooler is a kind of new energysaving machinery for clinker, and the internationally advanced flow control technology has been employed in this machine Based on the advancedHorizontal Grate CoolerCement Production Line,Cement Machine,Rotary
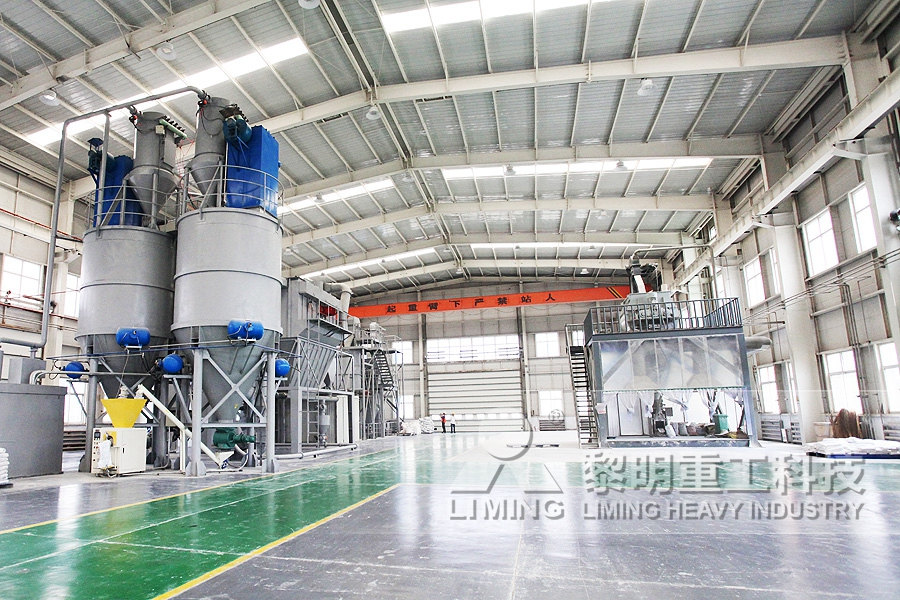
China Cement Machine Leading Manufacturer, Rotary
Leading manufacturer of Chinese cement machinery; large mining mill production and export company; China rotary kiln production champion enterprisePengfei Group,global export base of kiln and energysaving grinding mill equipment, is The main products: Rotary kiln system mainly includes rotary kiln, preheater, dryer, cooler and rotary kiln control system;The grinding equipment system mainly includes tube mill (including ball mill and coal mill), roller press, vertical mill, separator and grinding equipment control system;Cement production line: Including 1 000 t/d, 2 500 t/d, 3 000 t/d, 5 000 t/d cement About UsCement Production Line,Cement Machine,Rotary Kiln What Is Cement Rotary Kiln Cement rotary kiln, also called cement kiln, is a pyroprocessing device used for calcining cement clinker in cement production linesIt is the main engine in the cement manufacturing process, commonly known as the “heart” of the cement plantIn the production process, an equipped kiln burner produces heat by burning fuel, and the heat is Cement Rotary Kiln Rotary Kiln Rotary Kiln ManufacturersAnalysis of the parameters affecting energy consumption of a rotary kiln in cement industry Adem Atmaca *, Recep Yumrutas¸ University of Gaziantep, Department of Mechanical Engineering, 27310 Applied Thermal Engineering ResearchGate
.jpg)
Cement Production Line, Cement machinery, Rotary kiln, Cement
Raw meal system includes limestone crushing section, prehomogenization storage shed, raw meal grinding mill raw meal silo, etc Burning system includes kiln inlet section, kiln section and kiln outlet section; coal powder production section if coal is used as fuel Cement production system: clinker silos, cement grinding mill section, etc Finished product transporation 2014年5月1日 The formation of anzast layer and the use of high quality magnesia spinel and high alumina refractory bricks provide 727% reduction in energy consumption corresponding to a saving of 27178 MJ Analysis of the parameters affecting energy consumption of a rotary 2019年3月8日 Figure 2: Rotary Cement Kiln fine gray powder called cement Many cement plants include the Thermal energy savings from process control systems may IMPROVING THERMAL AND ELECTRIC ENERGY EFFICIENCY AT CEMENT 2022年10月20日 Cement production plants are one of the extremest CO2 emissions, and the rotary kiln is a cement plant’s most energyconsuming and energywasting unit Thus, enhancing its operation assessments (PDF) Modeling operational cement rotary kiln variables with
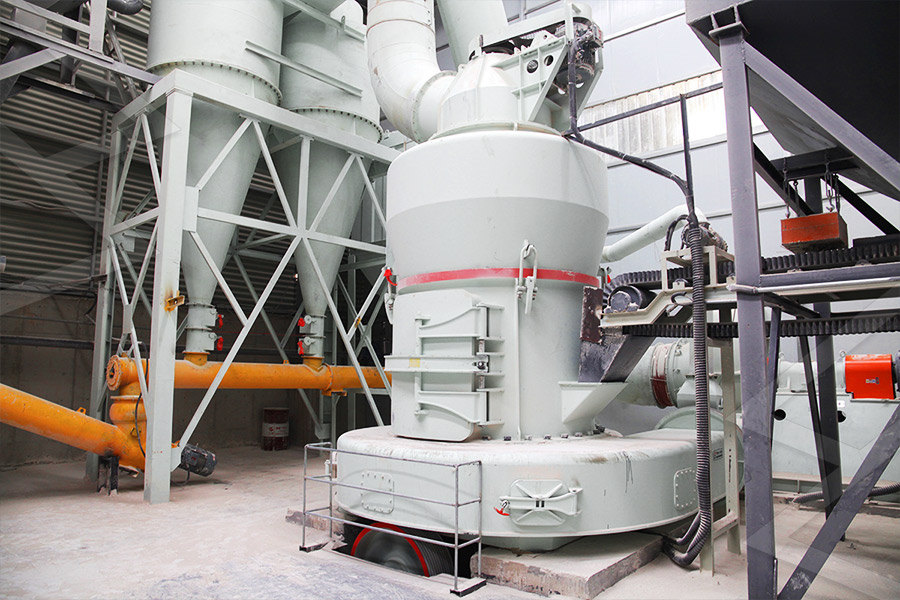
Cement Production Line Rotary kiln Cement Tube mill Ball mill Cement
Jiangsu Pengfei Group Co, Ltd is one of the leading manufacturers of rotary kiln and grinding equipment in China and the global marketThe business scope includes the design, manufacture and service of equipment in the fields of building materials, metallurgy, chemical industry, environmental protection, etc, and as an EPC service provider, providing customized onestop Energy Saving Measures of Cement Grinding Plant Select energysaving cement mill At present, some cement production enterprises are still using traditional cement mills It greatly reduces the production efficiency, increases the Making Your Cement Grinding Plant Energy SavingLimestone in the preheater will be preheated by the hot air, then it will be discharged to rotary kiln through chute that connecting preheater and kiln, it will stay in the kiln for 152 hours for calcination, during the process, it will be Active Lime Production LineEnergy Efficiency: Green cement often requires less energy in production due to lower kiln temperatures needed for processing alternative materials Durability and Performance : Some forms of green cement offer enhanced durability and Cement Making Guide: Steps, Impact Green
.jpg)
An overview of energy savings measures for cement industries
2013年3月1日 The current global consumption of cement industry is about 15 billion tons per annum and is rising at almost 1% per annum Cement production requires approximately 110 kW h/t of electrical energy, with 40% directed to clinker grinding [26]Using real auditing, Avami and Sattari [17] investigated technological methods that would reduce the energy consumption, method for cement production by applying Low Pour Fuel Oil (LPFO) and natural gas to firing the kiln to generate heat energy required in the kiln for production of clinker from the kiln feed In modern cement plant, natural gas and fuel oil are preferred for firing the kiln over coal The main reason being thatQuantitative Optimization of Cement Rotary Kiln for Heat 2 REVIEW FOR ENERGY SAVING IN CEMENT KILN 21 Modeling Balance of Cement Kiln The share of energy consumed in a cement clinker kiln plant attains 7078% of the overall energy consumed in the process of cement production as a whole The residual (2230%) is the share of electrical energy On the other hand,Different Possible Ways for Saving Energy in the Cement ProductionCement production line: Including 1 000 t/d, 2 500 t/d, 3 000 t/d, 5 000 t/d cement production lines and EP/EPC engineering general contracting services of various grinding production lines with annual output of 100,000 tons, 300,000 tons, 500,000 tons, 1 million tons and 2 million tonsJIANGSU PENGFEI GROUP CO,LTD Company Profile Cement Production Line
.jpg)
Cement Extraction, Processing, Manufacturing Britannica
2024年11月23日 Cement Extraction, Processing, Manufacturing: Raw materials employed in the manufacture of cement are extracted by quarrying in the case of hard rocks such as limestones, slates, and some shales, with the aid of blasting when necessary Some deposits are mined by underground methods Softer rocks such as chalk and clay can be dug directly by Step 4:Cement grindingClinker , gypsum,mix materials and so on aProcess introduction: Clinker , gypsum, mixed materials in a ball mill , cement grinding into a qualified drug cement The use of the powder selecting machine can conveniently adjust 300tpd Wet Processing Cement Product Machine Cement Production Line Uses of alternative fuels and raw materials in the cement industry as sustainable waste management options Alfonso Aranda UsónAna M LópezSabirónGermán FerreiraEva Llera Sastresa, in Renewable and Sustainable Energy Reviews, 2013 21 Worldwide production One of the wellknown characteristics of cement production is that cement plants are not uniformly Cement Production an overview ScienceDirect TopicsRequest PDF On Jun 1, 2014, Mert Gürtürk and others published Energy and exergy analysis of a rotary kiln used for plaster production Find, read and cite all the research you need on Energy and exergy analysis of a rotary kiln used for plaster production
.jpg)
Rotary Kiln For Activated Carbon Production
Before you send inquiry Please provide us with project information as much as possible: For a complete project: the material availability, the required output capacity, the process technology, your budgetary and financing status, the Rotary kiln cement plant is the cement manufacturing plant with cement rotary kiln as the clinker calcining equipment and other cement equipment as The rotary kiln cement plant has a wide range of energy utilization, which can make full use of cheap Cement Production Line Stone Crushing Plant Cement Grinding Plant Fly Ash Rotary Kiln Cement Plant Cement Rotary Kiln AGICO Cement 2014年5月1日 The cement plant operates on a dry cement process line The rotary burner is a refractory lined tube type kiln with a diameter of 42 m and 59 m length It is inclined at an angle of 35°, and its rotational speed is 1–2 rpm The average clinker production capacity of the rotary kiln is Analysis of the parameters affecting energy consumption of a rotary New type cement production line: Capacity: 1000TPD: Main equipment: GRMR2221 raw material vertical mill, GRMC1621 coal vertical mill, GRMK3331 vertical cement mill, φ32x50m cement rotary kiln: Characteristics: Energy saving, environmental protectionCement Production Line CHAENG
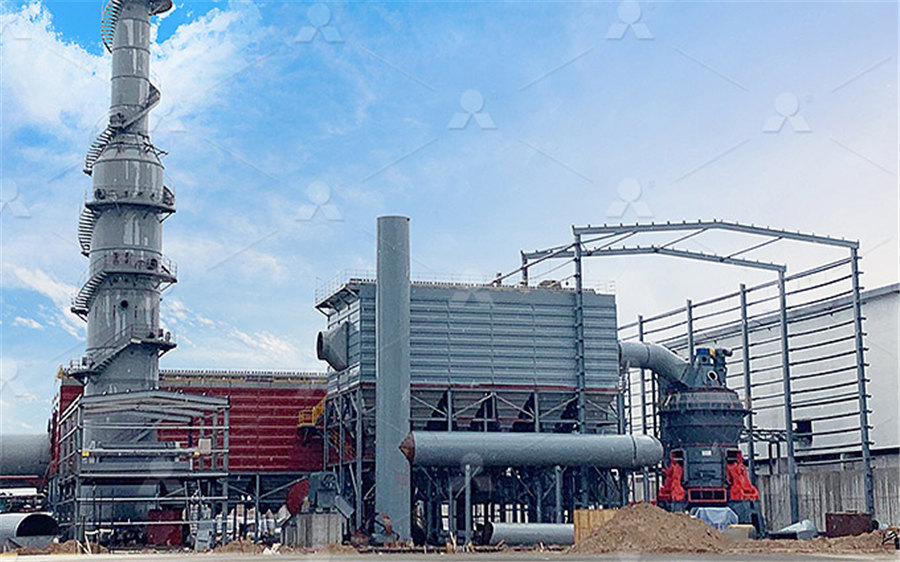
Why Choose Rotary Kiln In Cement Manufacturing Plant?
2019年11月6日 As a rotary kiln manufacturer, AGICO Cement offers rotary kiln and other related cement equipment, such as stacker and reclaimer, cement ball mill, vertical cement mill, cement crusher, suspension preheater, cement dryer, clinker cooler, cement roller press, etc we also provide turnkey EPC project for cement manufacturing, including mobile crusher, cement 2024年10月7日 Cement production in the world is approximately 36 billion tons per year Around 2% of the electricity produced worldwide is used during the grinding process of raw materials The total electrical energy consumption for cement production is about 110 kWh/t cement, about twothirds of this energy is used for particle size reductionEnergy consumption of a rotary kiln in cement industry(Worrell and Galitsky, 2004), evaluated the energysaving potential of about 30 energyefficiency technologies and practices that could be applied to both wet and dry process cement production For this analysis, we compare current energy use (both for electricity and for fuels) for cement production in California in 2002 (van Oss, 2003) to best practice values for these two types of TIPS TO SAVE ENERGY IN CEMENT MANUFACTURING PROCESS2500TPD new type dry process cement clinker production line The 2500t / d cement clinker production line adopts a new dry process, with an annual output of 775,000 tons of cement clinker and a total cement output of 105 million tons / year A cement production line and auxiliary facilities from limestone crushing to cement packaging are Cement Production Line,Cement Machine,Rotary Kiln,Cement
.jpg)
Rotary Kiln, Cement Rotary Kiln, Lime Rotary Kiln, Cement
Brief Introduction to Wet Rotary Kiln Process The kiln body of wet rotary kiln is usually relatively long (the aspect ratio is 3040) In order to increase the heat transfer area of the kiln, the chains are often hung at the kiln tail to accelerate water evaporation2020年9月9日 Italian cement industries are among the major cement producers in the European panorama In the last decades, because of the increasingly stringent specifications on environmental impact and energy saving, technology in the cement plant has been significantly improved []In this context, Advanced Process Control (APC) systems have become the Optimization of the Clinker Production Phase in a Cement Cement rotary kiln plays a variety of roles in the cement production line at the same time It is not only a combustion device, but also a heat exchange device, a chemical reactor, and a conveying device The rotary cement kiln we supply is Rotary Kiln for Cement Plant AGICOIn the diagram above of a precalciner kiln, raw meal passes down the preheater tower while hot gases rise up, heating the raw meal At 'A,' the raw meal largely decarbonates; at 'B,' the temperature is 1000 C 1200 C and intermediate Manufacturing the cement kiln Understanding
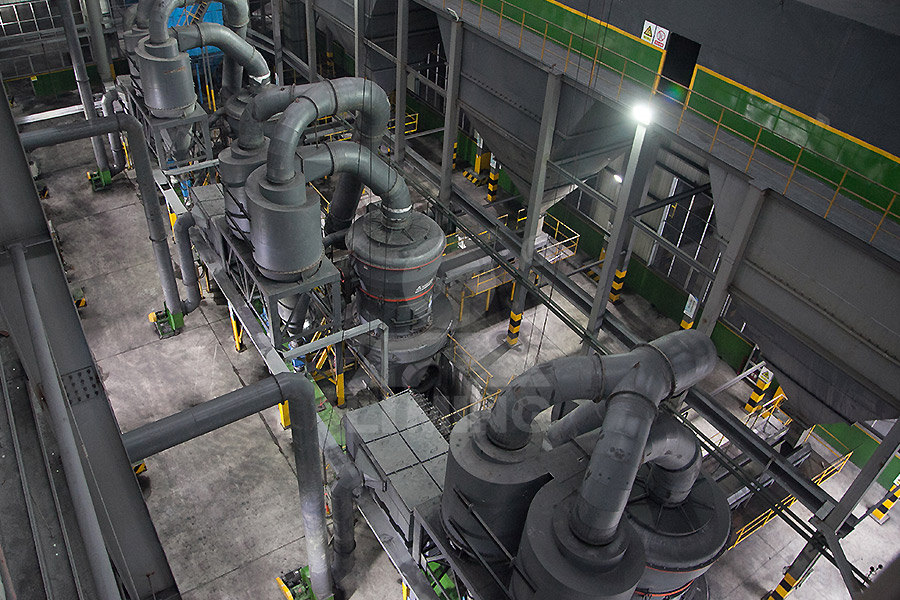
Review on energy conservation and emission reduction
2022年12月1日 In the cement industry, the total energy consumption accounts for 50–60% of the overall manufacturing cost, while thermal energy accounts for 20–25% (Wang et al, 2009; Singhi and Bhargava, 2010)The modern cement industry requires 110–120 kWh of electrical power to produce one ton of cement (Mejeoumov, 2007)Thermal energy is used mainly during The rotary kiln system considered for the energy audit is schematically shown in Figure2 31 Mass Balance of Cement Kiln The mass balance for both preheater, rotary kiln and cooler is shown as the following: 311 Mass Balance of Preheater Calciner Inlet mass =outlet mass Inlet mass= mc+mra+m kg+m kd+mtair+mpair Outlet mass=m ex gases + m h c+ mpd 3 12 Mass Different Possible Ways for Saving Energy in the Cement Productionproduction Cement rotary kiln Energy efficiency 1 Introduction Italian cement industries are among the major cement producers in the European panorama In the last decades, because of the increasingly stringent specifications on environmental impact and energy saving, technology in the cement plant has been significantly improved [1]Optimization of the Clinker Production Phase in a Cement Plant2015年6月1日 In this paper, implementation of proper energy saving actions in an Iranian cement production plant was studied and several useful methods were suggested to improve energy consumption, since cement industry is considered to be one of the most energy intensive industries [7], [8]Establishment of proper saving actions is necessary to facilitate energy Energy consumption assessment in a cement production plant
.jpg)
Energetic assessment of a precalcining rotary kiln in a cement
2021年11月1日 ANN model is validated and demonstrated it is capable of predicting cement rotary kiln energy efficiency accurately with a correlation coefficient (R²) of 0991White cement production line adopt many new technologies with complete independent intellectual property right, such as the new out kiln decomposition calcining process, clinker of white cement bleaching, heat regeneration and etc, the white cement clinker heat consumption less than 1200kcal/kg below the international advanced level, use pulverized coal to replace White cement production line plan LCDRI CNSOLUTION2: Lime Production Line With Vertical Kiln The vertical lime kiln is suitable for smallcapacity active lime production lines, lowcost, safe and environmentally friendly The vertical lime kiln uses the principle that the material’s own weight descends and the hot gas rises for heat exchange to burn lime We supply twin shaft lime kiln, double beam lime kiln, annular lime kiln Lime Production Line Active Lime Production Line Cement