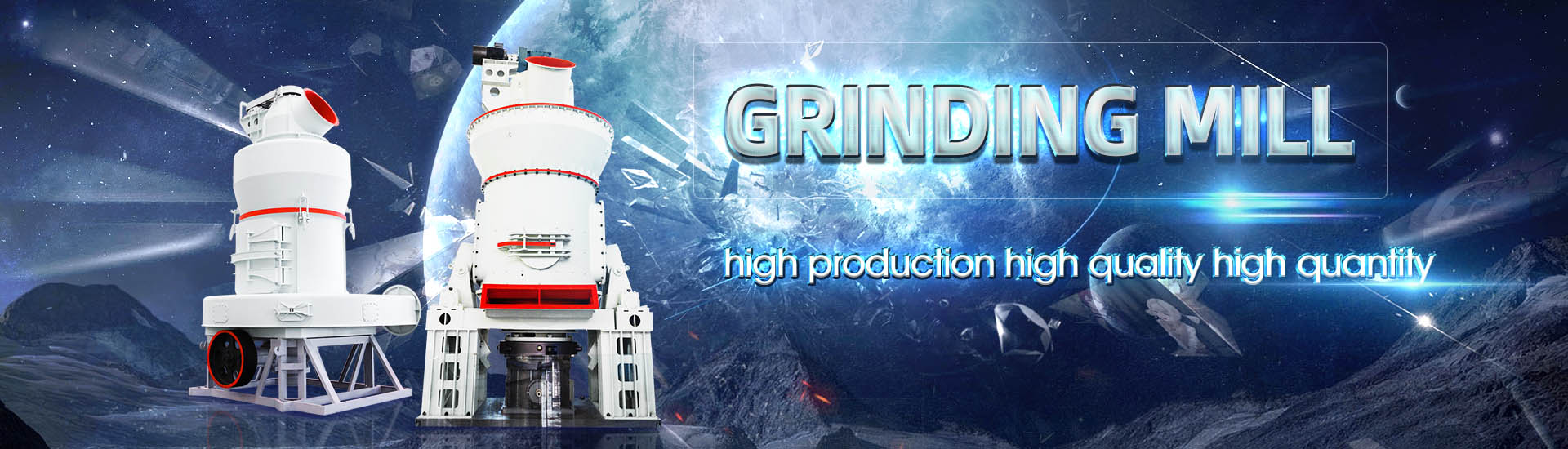
1Ore grinding mill production safety protocol

Ensuring Safety in Coal Mills – Best Practices and Precautions
Coal mills, essential components in power generation and various industrial processes, pose significant safety risks if not properly managed These mills, used to grind coal into a fine By following the recommended procedures and safety guidelines, operators can ensure safe and efficient operation, minimize equipment wear and tear, and prolong the lifespan of the ball mill Ball mill operation procedures and safety precautionsCoal mills, also known as pulverizers, play a critical role in power plants by grinding coal into fine powder, which is then used in various pyroprocesses These mills pose significant safety risks Coal Mill Safety: A Critical Aspect of Power Plant Operations Coal The safety of coal grinding operations is paramount to protecting workers, equipment, and facilities By understanding the hazards associated with coal dust and grinding machinery, and Safety Aspects of Coal Grinding Coal Mill Safety, Explosion and

Mill Operators Manual Safety Haas Automation Inc
When you use CNC machines and their components, you must always follow basic safety precautions to reduce the risk of personal injury and mechanical damage The work area must Safe coal handling practices are designed to ensure that the fuel remains intact throughout its journey from the mine until the point at which it is ignited in the boiler It takes as little as 14 kg STRENGTHENING PLANT SAFETY IN COAL GRINDING MILLS AND 2022年4月11日 This blog discusses grinding mill inching drive safety in the operation of mines, and how minor and even fatal accidents can be avoided An inching drive, what is it and why is it needed? Grinding mills are typically Inching drives – one way to improve mill safety MetsoSAFETY GUIDELINES FOR IRON STEEL SECTOR MINISTRY OF STEEL, GOVT OF INDIA ReRolling Mills Doc No: SG/34 Rev no : 00 Effective Date: 1 OBJECTIVE: Rolling and SAFETY GUIDELINES FOR IRON STEEL SECTOR MINISTRY OF
.jpg)
Grinding Safety Precautions and Control Measures
2023年10月11日 In this article, we will explain what grinding safety precautions are and how they can be identified and implemented using a grinding risk assessment and provide you with grinding safety tips to keep your workers Learn essential safety measures for protecting personnel and equipment during industrial mixing and milling processes with HockmeyerSafety in Industrial Mixing Milling HockmeyerThe European Commission (EC) maintains the consideration of tungsten as a critical raw material for the European industry, being the comminution stage of tungstenbearing minerals an essential step in the tungsten concentration Grinding Kinetics Study of Tungsten Ore MDPI2022年4月11日 Grinding the mill out (cutting the feed to the mill), thus reducing the charge load prior to mill maintenance is a good practice This lowers the weight of the charge, thus the roll back torque Also, after inching the mill to Inching drives – one way to improve mill safety Metso
.jpg)
The effects of iron ore concentrate grinding methods (HPGR and
2020年10月18日 An iron ore concentrate sample was ground separately in a pilotscale HPGR mill in multiple passes and a dry opencircuit ball mill to increase the specific surface area of particles2024年9月26日 Energy savings and consumption reduction of ball mills are crucial for industrial production The grinding medium is an important component of a ball mill In theory, using higherdensity grinding media can yield better grinding results However, for materials with varying grindability, employing grinding media of different densities can reduce energy consumption Optimization and Experimental Study of Iron Ore Grinding 2020年6月3日 The design of such grinding mills is extremely critical, requiring sophisticated software tools, proprietary calculation worksheets, and experienced technical engineers and drafters This blog will review how the mill design process has changed over the last 30 years While most of the changes have been positive, new issues and problems have risen in the How grinding mill design changed over the last 30 yearswhere K is the grinding rate constant and t is the grinding time Despite the fact that the firstorder hypothesis is the most widely used approach to describe the grinding process in a ball mill and many studies have pointed out its advantages [31, 32], deviation from the linear kinetics has been experimentally observed in several cases whenModeling of Bauxite Ore Wet Milling for the Improvement of
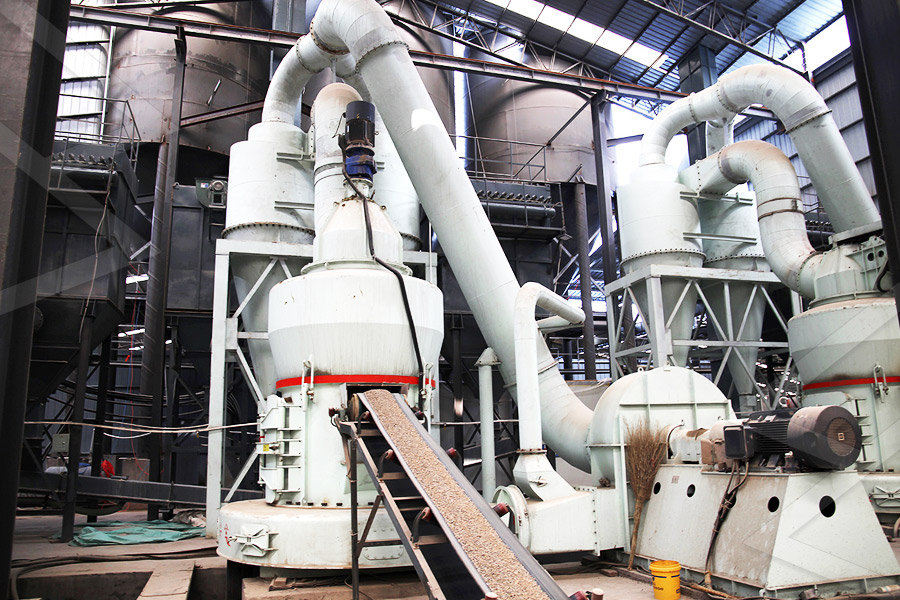
Monitoring ore loss and dilution for minetomill integration in
2016年2月1日 The conditions of declining gold grade in the ore, increasing depth of excavation, and decreasing unallocated stock of deposits make it necessary to develop efficient solutions for the mineto 2024年2月26日 Oxidised pellets have become an indispensable highquality charge for blast furnaces Nevertheless, highquality pellet feeds are becoming scarcer and scarcer To broaden the range of sources of pellet feeds and reduce the production cost of pellets, more steel mills are predicted to use coarse iron ore fines with a relatively low iron grade and low impurities for the Grinding of Australian and Brazilian Iron Ore Fines for Low from grinding is nearly always produced from cyclones, even when grinding is done in a single stage SAG mill Cyclones work best when the cyclone feed size is limited to 5 mm top size, as noted above when referring to screen selection The product size is also a function of liberation and downstream requirementsDesign SAG mill production when you need it most: In day 1 and The discovery of excess mill pooling in the SAG mill prompted a review of the “pumping” capacity of the SAG mill The excess slurry pool inhibited grinding and caused unnecessary power draw on the mill with the internally recirculating slurry Crash stop inspections (Figure 2) of the mill interiorIMPROVING ENERGY EFFICIENCY IN BARRICK GRINDING CIRCUITS
.jpg)
Intelligent optimal control system for ball mill grinding process
2 Grinding process description The ball mill grinding process is mainly composed of a ball mill, a hydrocyclone cluster, a sump, a slurry pump and an ore bin The schematic diagram of this process is shown in Fig 1 Fig 1 Schematic diagram of ball mill grinding process The variables of this process shown in Fig 1 are explained as follows: W2018年8月8日 The paper presents a study on the effectiveness of the grinding process in an electromagnetic mill devoted to ultrafine grinding, and the influence of processing parameters on the mill’s performance The research was Grinding Kinetics Adjustment of Copper Ore Grinding Safe operation of coal grinding systems: Raw coal silo protection against fire and explosions Safe operation of coal grinding systems: Raw coal yard management The purchasing process for coal grinding systems needs changes Talk at a Coal Mill Safety In Cement Production IndustriesRequest PDF On Mar 15, 2015, Mathis Reichert and others published Research of iron ore grinding in a verticalrollermill Find, read and cite all the research you need on ResearchGateResearch of iron ore grinding in a verticalrollermill
.jpg)
Estimation of Grinding Time for Desired Particle Size Distribution
standard grinding reference time to the laboratory ball mill for optimizing the grinding time of each ore The desired P 80 (150 μm) with an acceptable range of hematite liberation (>75%) was obtained in the laboratory ball mill after reducing 6 min Table 1: Power Intensity of Different Grinding Devices Ball Mill is a 56m D x 64m L @ 26MW Tower Mill is a 25m D x 25m L @ 520KW Table 2: Mill Comparison of Media Size, Power Intensity, number of grinding media The ability to use smaller media is probably the dominant impact on grinding efficiency ItFine Grinding as Enabling Technology – The IsaMill2022年3月19日 An iron ore concentrate sample was ground separately in a pilotscale HPGR mill in multiple passes and a dry opencircuit ball mill to increase the specific surface area of particlesGrinding iron ore concentrate by using HPGR and ball mills and Coal grinding is a critical process in the production of energy and industrial products like cement It comes with inherent risks Ensuring the safety of workers and equipment in coal grinding operations is paramount This article outlines key safety measures and best practices to mitigate the hazards associated with coal grindingEnsuring Safety in Coal Grinding Operations Coal Mill Safety
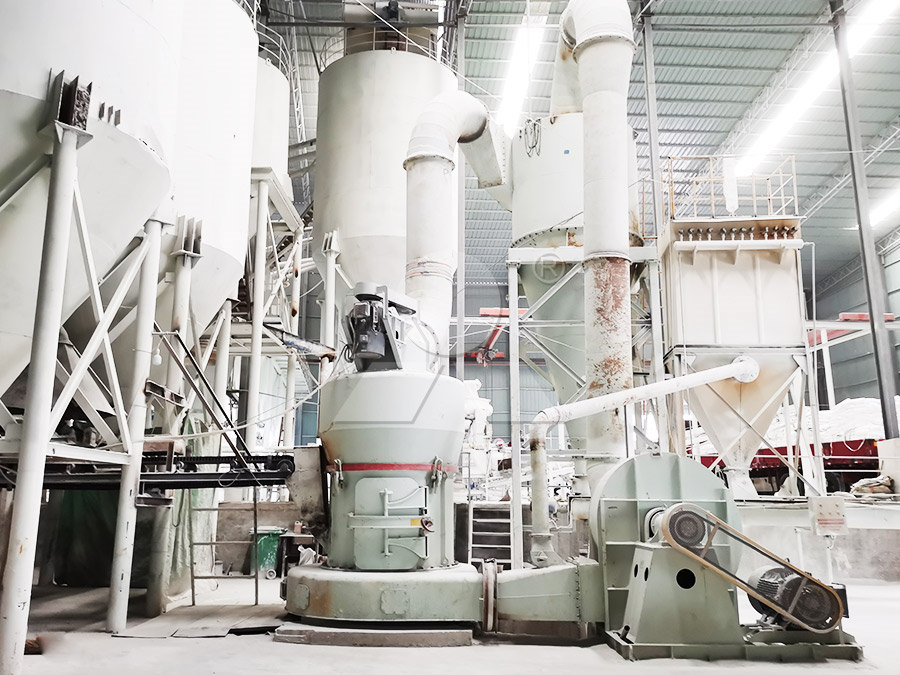
Safety Aspects of Coal Grinding Coal Mill Safety, Explosion and
Coal grinding is a critical process in various industries, particularly in power generation and cement production However, the process involves significant safety risks due to the combustible nature of coal dust and the mechanical hazards posed by grinding machinery Ensuring safety during coal grinding is essential to prevent accidents, explosion2020年3月31日 Crosssectional SEMBSE images of polished surfaces of (a) nonmagnetic product NMI and (b) magnetic product MIII obtained after magnetic separation of the −0300 mm fractionGrinding Behavior and Potential Beneficiation Options of Bauxite 2015年8月7日 Grinding Circuit Safety Grinding circuits are made up of large, moving pieces of machinery When carrying or moving objects in and around this equipment extreme care should be taken As an example, when operating the crane, never hoist anything directly over the millsGrinding Circuit and Mill Safety 911MetallurgistA crushing plant delivered ore to a wet grinding mill for further size reduction The size of crushed ore (F 80) was 40 mm and the SG 28 t/m 3 The work index of the ore was determined as 122 kWh/t A wet ball mill 1 m × 1 m was chosen to grind the ore down to 200 micronsGrinding Mill an overview ScienceDirect Topics
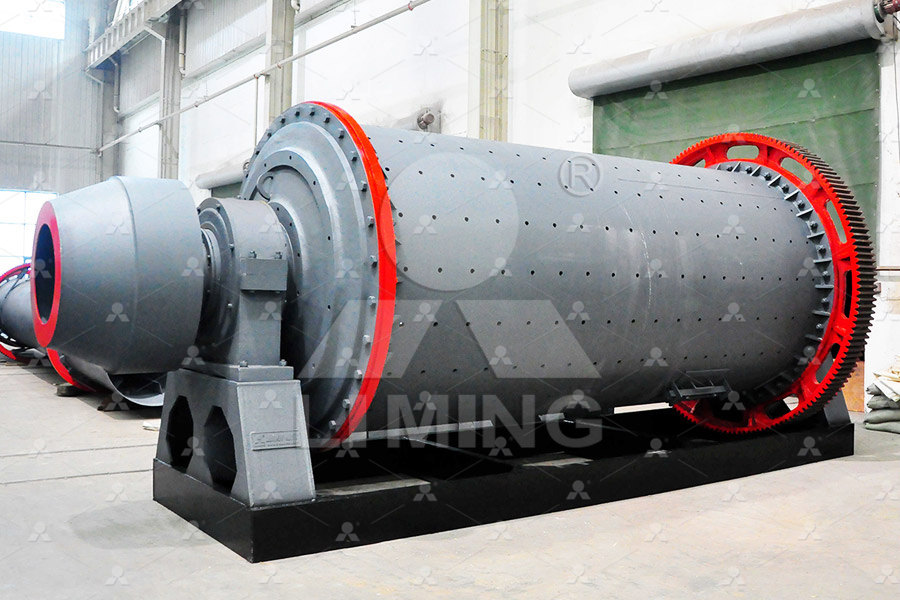
Research of iron ore grinding in a verticalrollermill
2015年3月15日 For the grinding tests, a Loesche mill LM45 (table diameter 045 m) is used (Fig 2a) This pilot scale mill is a special development for ore grinding, which is reflected by several features The mill has four rollers, which are able to stress the particle bed with grinding pressures of up to 5000 kN/m 22023年5月7日 10 Objective: To lay down a procedure for the operation of Colloidal Mill 20 Scope: This standard operating procedure is applicable to the operation of Colloidal Mill in the production area 30 Responsibility: Officer, Executive – To implement this procedure Head of Department – To overall compliance with this procedureSOP on Operation of Colloidal Mill PharmagudduCoal mills, essential components in power generation and various industrial processes, pose significant safety risks if not properly managed These mills, used to grind coal into a fine powder for combustion, present potential hazards such as fire, explosion, and mechanical failures This article outlines best practices and precautions to ensure thBest Practices and Precautions Coal Mill Safety, Explosion and 2022年2月28日 Comparing dry and wet grinding curves in a ball mill in the same condition (an equal amount of materials and grinding media has been used on each pair of wetdry experiments) (Fig 17) indicated two significant differences at higher power values of wet grinding, specifically when speed exceeded 06 critical speed and for higher ω Pmax in the Grinding SpringerLink
.jpg)
Reengineering of the ore preparation production process in the
Reengineering of the ore preparation production process in the context of “Almalyk MMC” JSC Margarita Naumova1, Ilnur Basyrov1,*, and Khakim Аliev1 1National University of Science and Technology “MISiS”, Leninskiy prospekt, 4, Moscow, , Russia Abstract The review of ore crushing and grinding processes at the2022年12月16日 Milling machines use rotating milling cutters and other cutting tools to remove material from metal, wood, and different workpieces These tools often run at high cutting speeds, causing chips and other flying debris to exit the workpiece at The Most Important Milling Machine Safety Precautions2009年1月1日 Also, equipment like ball mill is used at the final stages of grinding Among the comminution and grinding equipment, HPGR is increasingly utilized as tertiary crusher or primary mill because of Processing of Magnetite Iron Ores–Comparing Grinding OptionsFuel grinding systems in cement plants require adequate protection against the hazards originated by potential fires and dust explosions Coal Mill Safety takes ICR readers through the design of the part of the coal and petcoke grinding system to highlight the design required to operate a safe fuel grinding systemSafe Fuel Grinding Coal Mill Safety, Explosion and Fire
.jpg)
Metallurgists Mineral Processing Engineers 911Metallurgist
911 Metallurgist can enter the scene and see what you have become blind to We can fix issues in ways you never thought possible Our fresh eyes will open new opportunities for your plant Each mineral processing plant has varied ore types, mining equipment, (crusher, ball mill, flotation, tailings), and management (operating) philosophyThe evaluation and prioritization of variables 2020年12月10日 As a safety manager in the manufacturing industry, you’ll be aware of the huge range of hazards workers face And, often, it’s up to you to put measures in place to reduce the risk of workplace accidents Contents hide 1 The 7 Best Safety Practices in Manufacturing (Per OSHA)We are the global leader in aggregates production solutions for quarries and Fewer mill liner parts improve safety and cut downtime by 50% Customer The extensive product support and optimization services help in maximizing the efficiency of your grinding mill, grinding circuit or entire grinding process Grinding mills CategoryGrinding MetsoIn discussion: Coal Mill Safety At best, coal mill safety is not well understood and, at worst, it is ignored When it comes to coal mill systems, most cement plant operators just presume that the supplier of the equipment knows all of the standards and rules and is 100% capable of making a system that conforms to these and is therefore safeIn discussion: Coal Mill Safety Coal Mill Safety, Explosion and
.jpg)
Machine Learning Algorithms for SemiAutogenous Grinding Mill
2023年10月25日 Energy consumption represents a significant operating expense in the mining and minerals industry Grinding accounts for more than half of the mining sector’s total energy usage, where the semiautogenous grinding (SAG) circuits are one of the main components The implementation of control and automation strategies that can achieve production objectives 2022年10月13日 Grinding plays an important role in mining, construction, metallurgy, chemical, coal and other basic industries In terms of beneficiation, grinding is the most energy consuming operation So, reasonable grinding conditions according to the properties of ores is the key to obtain good grinding results and reduce energy consumption and resource waste In this Research on Grinding Law and Grinding Parameters Optimization 2023年9月10日 Aiming to reveal the kinetic characteristics of ceramic ball grinding of fine magnetite comprehensively, two types of ceramic balls ground with the same filling rate and total weight as steel balls were researched The results show that the breakage rate of ceramic ball grinding is only half of that of steel ball grinding with the same media filling rate With the same Ceramic Grinding Kinetics of Fine Magnetite Ores in the Batch Ball MillBasic safety: This machine can cause severe bodily injury This machine is automatically controlled and may start at any time Consult your local safety codes and regulations before you operate the machine Contact your dealer if you have questions about safety issuesMill Operators Manual Safety Haas Automation Inc
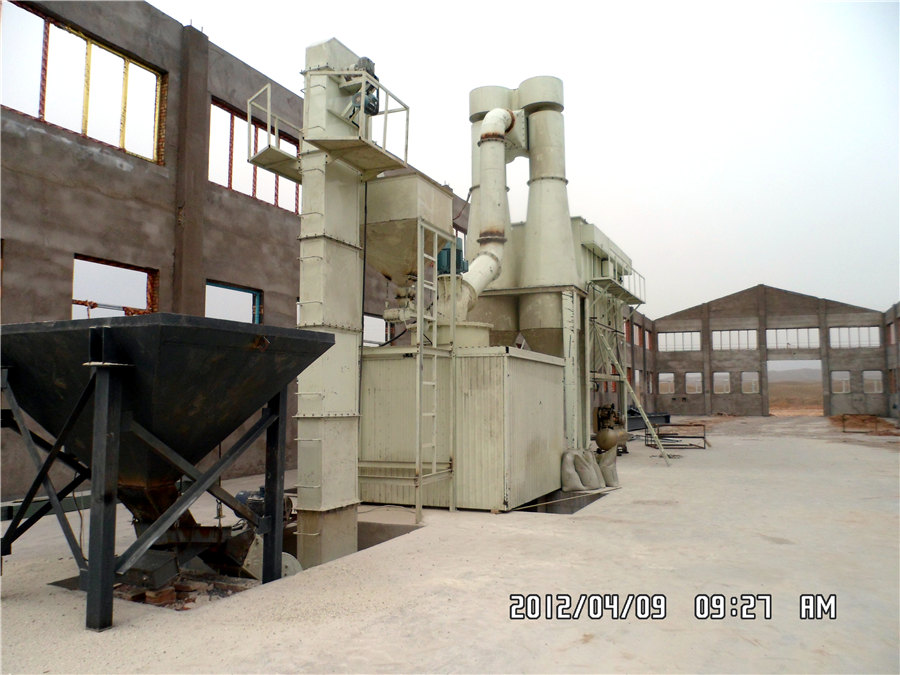
Grinding Machine Safety: Essential Tips for Operators
2024年7月21日 8) When grinding the end face of a workpiece, the feed amount and speed should be within the range that the grinding wheel strength can withstand to prevent the grinding wheel from breaking 9) When switching from external to internal grinding, the screw under the operating handle must be tightened after moving the grinding wheel carriage to the front endSafe operation of coal grinding systems: Raw coal silo protection against fire and explosions Safe operation of coal grinding systems: Raw coal yard management The purchasing process for coal grinding systems needs changes Talk at a virtual seminar, November 2023 Accept the probability that the fire and explosion safety of your coal grinding system is nothing more than a mirageFire and explosion protection of coal grinding systems Where are