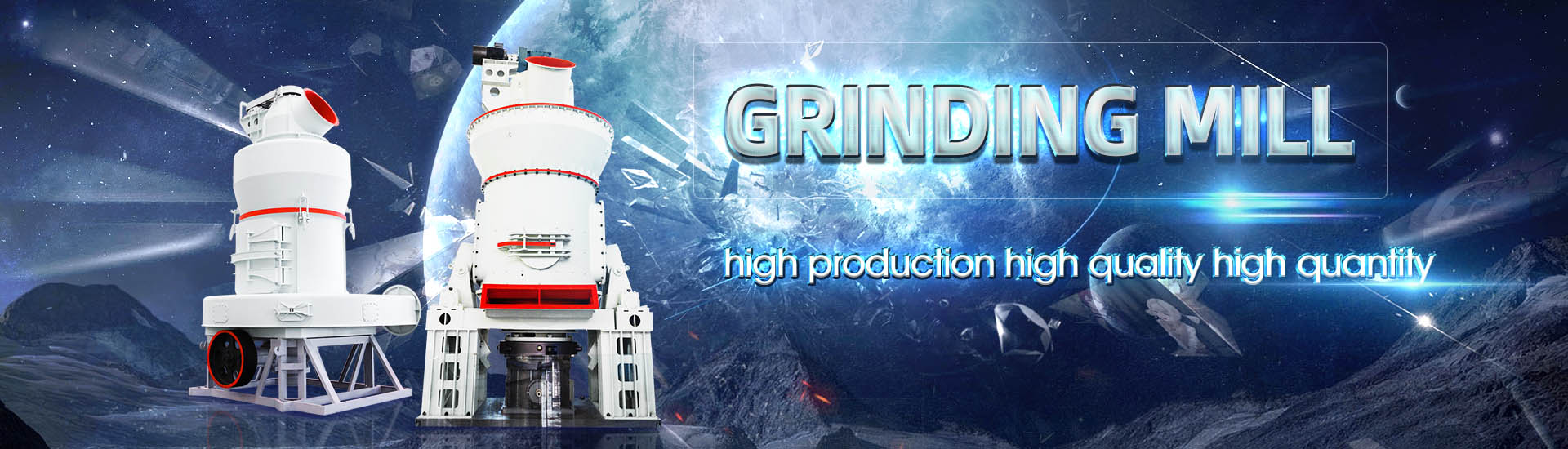
The process of making bricks from smelting waste slag with limestone crusher
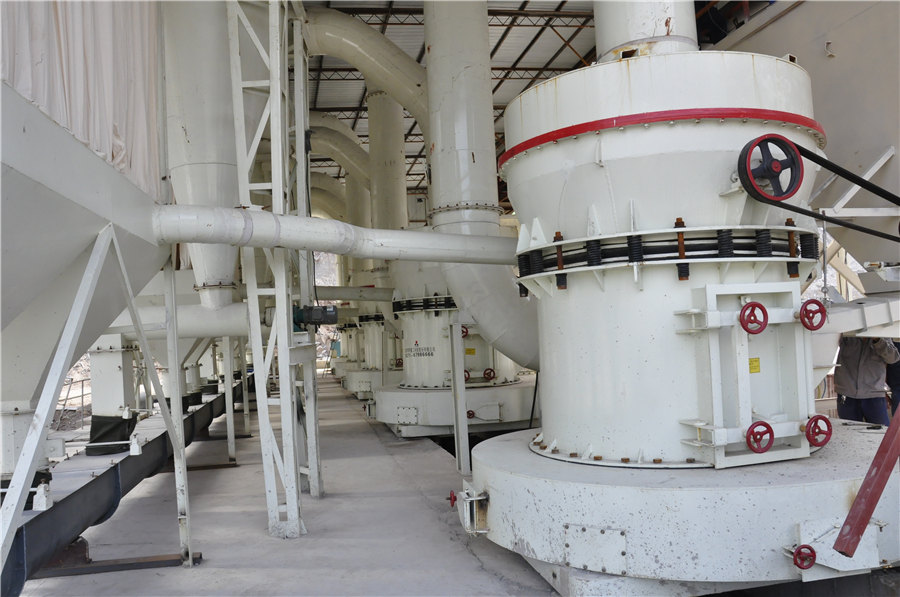
Characteristics of bricks made from waste steel slag
2004年1月1日 The characteristics of a construction material made from waste steel slag were investigated in this research Bricks with a steel slag addition of less than 10% and a firing 2020年1月30日 The present study firstly proposed a reasonable way to deal with the large amount of iron ore tailings and coal gangue powder by making them as the sintered bricks with Preparation, characteristics and mechanisms of the composite Conventional bricks are produced from clay with high temperature kiln firing or from ordinary Portland cement (OPC) concrete, and thus contain high embodied energy and have large Production of bricks from waste materials A review2013年1月1日 The procedure for producing the bricks simply includes mixing the tailings with an alkaline solution, forming the brick by compressing the mixture within a mold under a specified Development of Bricks from waste material: A review paper
.jpg)
Utilization of Waste Materials in Construction Brick ResearchGate
2023年10月14日 Numerous attempts and efforts have been made to include wastes such as wood sawdust, rubber, processed waste tea, limestone dust, polystyrene, sludge, and fly ash 2018年9月7日 Addition of waste bricks in composition results in a reduction of thermal conductivity of samples When a waste brick is used up to 25% for 800 °C sintering samples, Manufacturing of green building brick: recycling of waste for 2013年9月1日 This paper aims to compile this state of the art work of manufacturing bricks in the past and the current trend in the bricks industry with respect to the raw materials, ways of (PDF) Manufacturing of Bricks in the Past, in the Present and in the 2018年2月5日 Piles of steel slag, a solid waste generated from the iron and steel industry, could be seen due to no utility found for the past century Steel slag has now gained much attention Review on the innovative uses of steel slag for waste minimization
.jpg)
Review Production of bricks from waste materials – A review
2013年10月1日 Methods for producing bricks from waste materials can be divided into 3 categories: firing, cementing and geopolymerization Commercial production of bricks from 2014年4月30日 Novel lightweight bricks have been produced by sintering mixes of zinc smelting slag and clay A twostage sintered process has been proposed to recovery of Zn and Pb and reutilization of the zinc smelting slag In the first stage of the process, called reduction and volatilization procedure, zinc a The recovery of Zn and Pb and the manufacture of lightweight bricks 2017年2月1日 Pyrometallurgical process, hydrometallurgical process and their combination are usually applied for treating SWS (Ke et al, 2016, Li et al, 2015, Min et al, 2016)Among them, pyrometallurgy technology was proven an effective way of zinc and lead recovery from SWS, in which zinc and lead oxides are reduced to volatilize by reductant or volatilized by volatile agentClean strengthening reduction of lead and zinc from smelting waste slag 2019年9月3日 Industrially, the pyrometallurgical treatment of laterites is mostly accomplished with a wellestablished method, namely, the rotary kiln–electric arc furnace (RKEF) process, which includes (PDF) Nickel Laterite Smelting Processes and Some
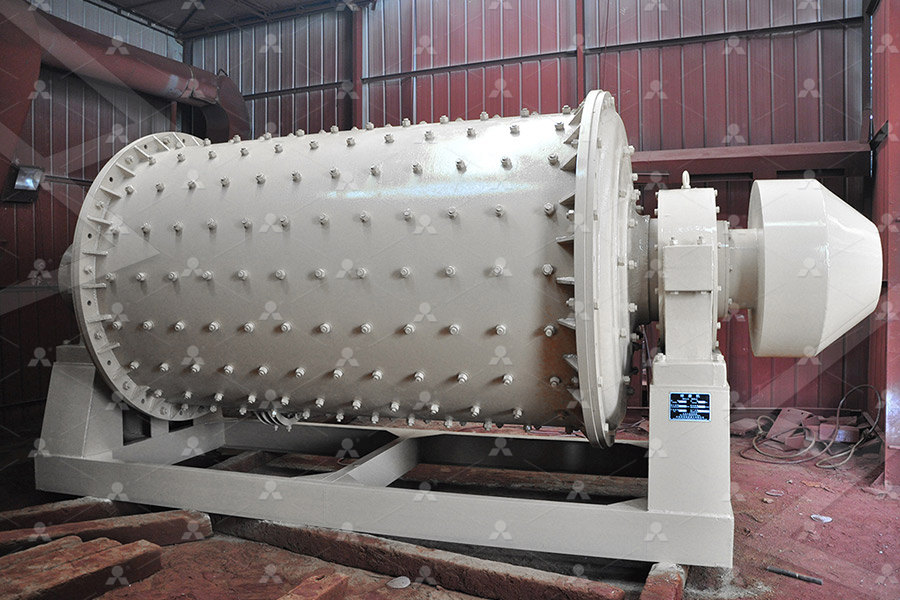
Sustainable and Comprehensive Utilization of Copper Slag: A
2023年4月21日 Metal Losses to the Slag in Smelting and Converting 80% of the copper produced from ores worldwide originates from sulfide ores The copper concentrate which results from flotation of the ore is typically smelted and converted to blister copper []During smelting S and Fe are oxidized, where SiO 2 is added to form a liquid ferric or ferrous silicate slag2024年5月3日 The utilization of solid waste resources is an essential strategy in the pursuit of sustainable development Among the various techniques used for solid waste treatment, brickmaking technology Review of Solid Waste Resource Utilization for Brickmaking2023年5月15日 Steel slag is the main solid waste generated in the steelmaking process, accounting for 15 to 20% of crude steel output [1]China's crude steel output in 2021 was 1035 billion tons [2], more than half of the global crude steel output (19505 billion tons) [3], and the steel slag output exceeded 120 million tonsIn contrast, the comprehensive utilization rate of Comprehensive utilization of steel slag: A review ScienceDirect2023年2月15日 Slag bricks Slag brick production process Slag brick is made by mixing, watering, grinding and pressing slag and limestone In the production process of slag brick, the particle size of the slag is generally smaller than 8 mm, and the steam temperature injected into the kiln is about 80 ℃ to 100 ℃, the maintaining time is about 12 hoursHow to Process Slags (with detailed process)? Fote Machinery
.jpg)
Treatments and Recycling of Metallurgical Slags IntechOpen
2018年11月7日 Steelmaking plants continuously strive to reduce the environmental load in the steelmaking process, resulting in the recycling of energy, water, and other byproducts In this chapter, techniques for the treatment and recycling of metallurgical slags are described Metallurgical slags are considered secondary raw materials and are used or added during the Fig5 Subdivision of raw materials for solid waste brickmaking 31 Solid Waste Brick Making with Sludge and Red Mud Sludge and red mud from sewage and other sources have long been recognized and discussed as important components of solid waste In recent years, extensive research has been conducted on these materials, with a foReview of Solid Waste Resource Utilization for Brickmaking2023年1月1日 Steel slag is a byproduct waste material that is generated in steelmaking furnaces during the process of separating molten steel from impurities The chemical reactions that take place when mineral aggregates and asphaltic materials meet one another impact the mechanical qualities of the mixture as well as its viability for use in various engineering Utilization of steel slag waste as construction material: A review2014年4月30日 Loss on ignition and water absorption increased with increasing zinc smelting slag addition as shown in Fig 4, Fig 5, while bulk density and sintering shrinkage decreased with zinc smelting slag content, due to the large loss on ignition of the zinc smelting slag For sintered bricks added zinc smelting slag, the bulk densities are much lower The recovery of Zn and Pb and the manufacture of lightweight bricks
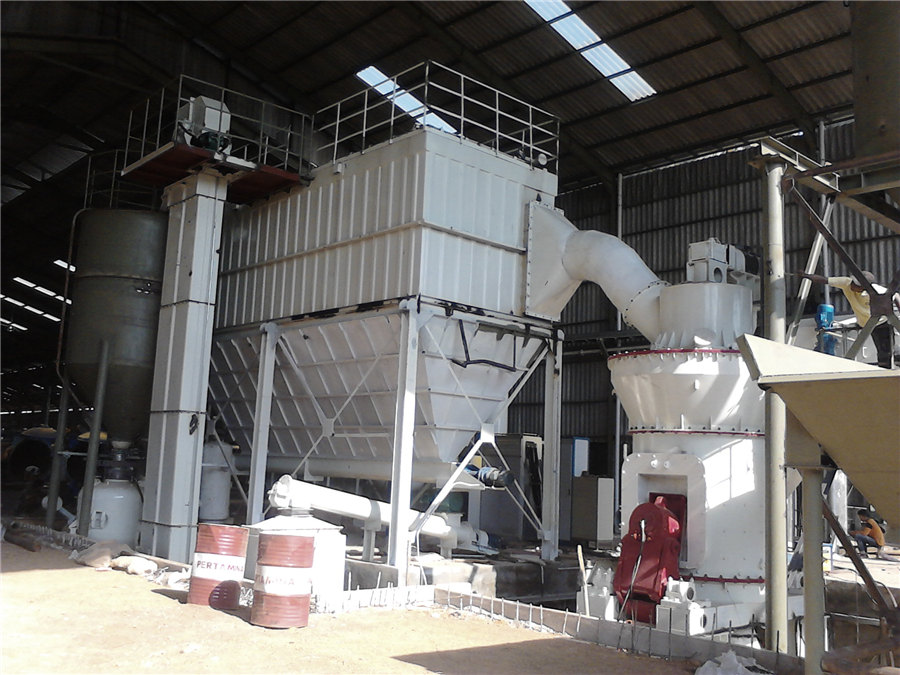
A comprehensive review on the recovery of copper values from copper slag
2023年8月1日 As copper slag has been identified as a hazardous waste, it requires the adoption of adequate precautionary measures for safe disposal [94] Therefore, recovering copper and other metal values from the slag would be a prudent approach to promote environmental protection and a circular economy [ 2 ]2021年11月11日 Slag is also called molten slag The melt that floats on the surface of liquid substances such as metals during the pyrometallurgical process is composed mainly of oxides (silicon dioxide, aluminum oxide, calcium oxide, Recycle Metal From Slag: The Recycling ProcessPDF On Jan 1, 2013, AA Shakir and others published Development of Bricks from waste material: A review paper Find, read and cite all the research you need on ResearchGateDevelopment of Bricks from waste material: A review paper2024年2月7日 Reduction The reduction process for copper slag is typically followed by magnetic separation []Depending on the temperature and intensity of reduction, it can be classified as direct reduction, deep reduction, and smelting reduction []Commonly used reducing agents include coke, biomass carbon, and natural gas [31, 32]The reduction process converts Resource Utilization of Copper Slag with a Focus on Springer
.jpg)
The Phase Transition and Element Distribution of Copper Smelting Slag
2023年2月22日 Copper smelting slag is the largest solid waste produced in coppermaking process, and slow cooling beneficiation technology is the most widely used method in recovering remaining treasures from the slag The phase transition law and element distribution behaviors of the copper smelting slag in the cooling process have significant importance, and they have As such, analysis has been carried out and studied by using slag as the main composition of brick casting in this study 12 Materials 121 Slag: It is the byproduct of metal smelting, and hundreds of tons of it are produced every year all over world in the process of refining metals and making alloys Slag being lighter, than the heavy and Appropriate use of waste materials in Infrastructure projects Slag BricksDevelopment of construction sand from waste steel slagJSW: Development of construction sand from waste steel slag2014年5月3日 The utilization of solid waste is the challenge for the civil and environmental engineers to utilize the waste from different industry to excel the sustainable development, and in the same time, it is matching with the cost concern of the present materials Copper slag is a byproduct obtained during smelting and refining of copper The waste copper slag can be used Use of waste copper slag, a sustainable material
CFB石灰石脱硫剂制备——磨机公众号12.8 推送案例(8)53.jpg)
Making Bricks From Recycled Plastic: A StepbyStep Guide To A
2022年12月24日 As part of their efforts to develop innovative machinery, an industry is developing CUBICLE, a new plastic brick making machine Plastic waste from savesay savesay savesay savesay’s recycling furnace is transformed into paving bricks The waste plastic – aggregate brick is stronger and more durable than the existing interlocking bricksbetter effects But, because of the difference in the composition of the slag, each process may have different effects Therefore, a flotation approach was studied, aiming at the recovery of copper from smelting slag Experimental Materials The smelting slag used in this study was obtained from a copper plant in ChinaThe Recovery of Copper from Smelting Slag by Flotation Process2020年3月31日 The current development of coalbased smelting reduction iron making process is introduced with main features of 10 smelting reduction processes Up to now, only COREX is of best performance and Development of Smelting Reduction Ironmaking 2021年12月1日 Matte with copper grade of 68% was produced from concentrate dried with steam dryer, granulated converter slag, silica and limestone with submerged lances smelting with using oxygen enriched process air with 300 kPa(g) Offgas from the Sfurnace was led via HRB and ESP to the ID parison of environmental performance of modern copper smelting
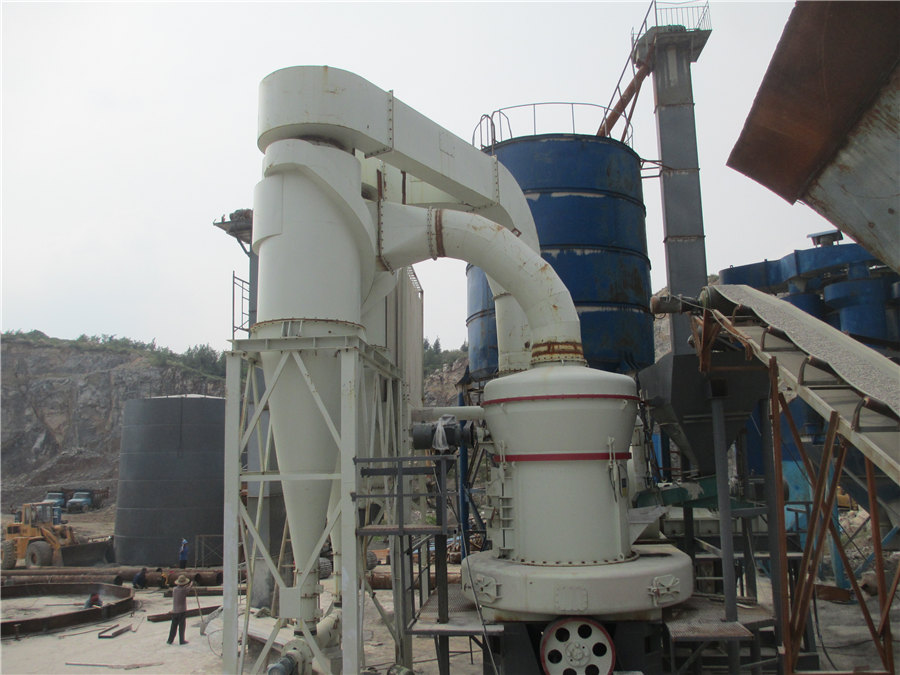
The aluminium industry: A review on stateoftheart technologies
2020年2月1日 For these reasons, exploring waste heat recovery (WHR) for reuse in the process has been heavily targeted by companies of all industries as an avenue in which to invest In this regard, the study of the aluminium industry is of great importance, particularly due to intensifying concern regarding global warming, GHG emissions, and the rising trend in fuel prices2020年9月24日 With the rapid development of China’s steel industry, rising rates of steel production have led to the increase of steel slag emissions Steel slag is a kind of industrial solid waste produced in the process of iron and steel smelting, and its emission is about 15 wt%–20 wt% of crude steel output []According to the data released by the World Iron and Steel Sustainable Utilization of Steel Slag from Traditional Industry and 2021年8月25日 Steel slag from an electric arc furnace (EAF) may contain significant amounts of oxides of valuable metals The recovery of iron and other metals from the EAF slag using smeltreduction process Metallurgical resource recovery from waste steelmaking slag from 2016年2月29日 When the smelting process is complete, the charge is poured into a mold Once the slag is cool, this can be separate from lead and precious metals by using a hammer or any device than can break the slag The metallic product is named button and have to be processed in the other smelting process called cupellationGold Smelting Refining Process 911Metallurgist
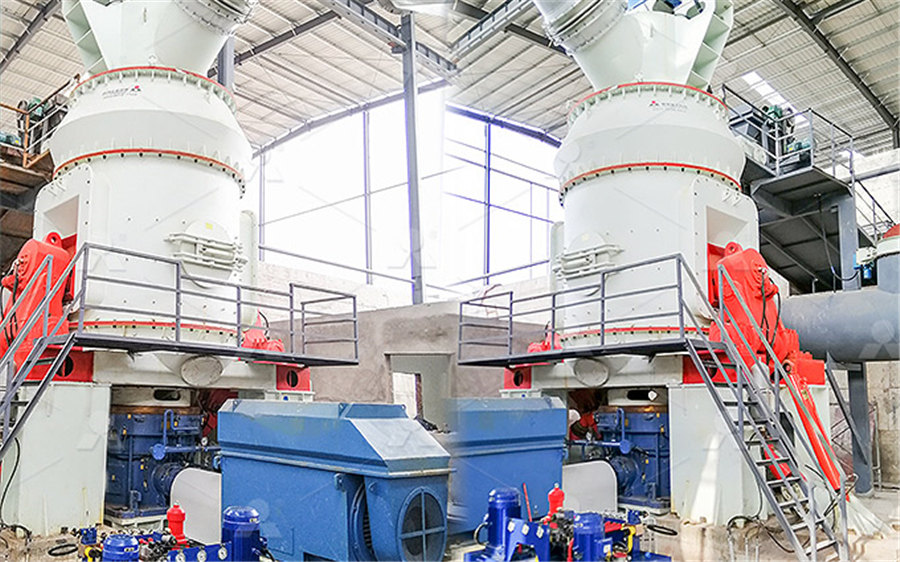
By the hand of the smelter: tracing the impact of decisionmaking
2022年4月4日 Slag analyses from archaeological iron smelting sites are common Rigorous analyses of iron and slag from successful experimental smelting, however, are still rare Furthermore, thorough analyses from a series of smelts, and of the slag produced in different phases of the smelt, are exceedingly rare The present study investigates the effect of an iron 2019年5月23日 Steel slag is the waste generated in the steelmaking process and includes ferric oxide and the impurities of some infusible matters It is the byproduct when slagforming constituents (such as fluorite, lime, and deoxidant) are added for deoxidization, desulfurization, and dephosphorization in prehensive Utilization Technology of Steel Slag2022年12月1日 This paper presents ecofriendly unburnt bricks made up of fly ash, waste plastic powder, waste glass powder, lime, gypsum and crusher sand as alternatives to conventional burnt clay bricks for (PDF) Employment of cisco metal slag in fly ash bricks for a 2021年4月30日 At present, there are two main magnesium smelting methods: electrolytic smelting and reduction smelting Compared to electrolytic smelting, reduction smelting has the advantages of having a simple and mature process, requiring a small investment, short construction period, can use various heat sources, produces good quality magnesium, Magnesium Smelting via the Pidgeon Process SpringerLink
.jpg)
Comprehensive recycling of zinc and iron from smelting waste
2020年8月1日 The comprehensive recycling of zinc and iron from smelting waste containing zinc ferrite (SWCZF) remains a challenge A study is to be the first proposed that hazardous SWCZF is directionally converted with SO 2 for simultaneous recycling of zinc and iron In the first step, zinc and iron phases in SWCZF were transformed into zinc sulfate and ferric oxide via oriented Currently, there is a limited amount of research on the smelting slag in general Zhang S et al has successfully developed highporosity ceramics and glass ceramics using smelting slag from the waste automobile catalyst [31]In addition, the Chinese invention patent also mentioned a method for recovering rare metals lanthanum, cerium, and zirconium from smelting prehensive recycling of slag from the smelting of spent 2004年2月1日 Request PDF Characteristics of Bricks made from waste Steel Slag The characteristics of bricks made from steel slag were investigated in this research Slag addition was shown to reduce the Characteristics of Bricks made from waste Steel Slag2019年10月4日 Abstract The processing of electric arc furnace dust by the Waelz process forms the ironcontaining residue called Waelz slag In the paper, best practices for recycling of Waelz slag from electric arc furnace dust processing have been analyzed and physicochemical characteristics and microstructure of the Waelz slag obtained from JSC Chelyabinsk zinc plant State of the Art and Prospect for Recycling of Waelz Slag from
.jpg)
Characterization and Leaching Assessment of Ferronickel Slag
2012年1月1日 Slag, on the other hand, is a waste byproduct obtained from smelting ore in an electric furnace at a very high temperature while a reducing agent is present [7]2019年7月1日 The materials for the manufacturing process are hemp fibers, hydrated lime, sodium hydroxide (NaOH) (Adam et al, 2021), sodium silicate, binder, fine stone ground and water (Rautray et al, 2019 (PDF) BioBrick Development of Sustainable and Cost Effective 2020年6月3日 Smelting slag is a typical hazardous waste generated in the smelting and metallurgy industry 1,2Slag contains high concentrations of heavy metals, such as Cu, Zn, Cr and Ni, which are harmful if Highpurity recycling of hematite and Zn/Cu mixture from waste smelting 2007年1月1日 a Distribution of premodern smithing and smelting slag compositions in the system FeOSiO 2 Al 2 O 3 Data reduced by combining suitable oxides (eg FeO and MnO) and omitting minor compoundsDecisions set in slag: the human factor in African iron smelting
制粉-10.25公众号.jpg)
Basics of slag production Article on the slag industry from Global Slag
2011年10月27日 BOS Slag Process When molten iron (referred to as “hot metal”) from the blast furnace is to be converted into steel, the main tasks are the removal of carbon, silicon and phosphorus The LD (LinzDonawitz) process is by far the most widely used, and takes its name from the towns where it was developed