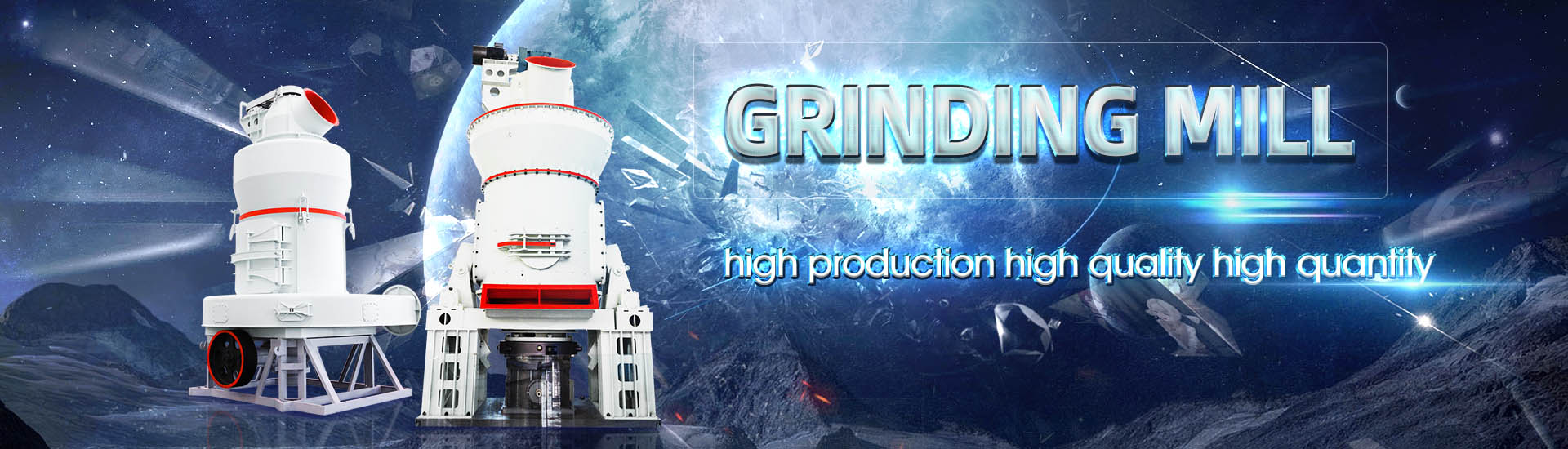
The grinding process of quicklime ore
.jpg)
Realtime monitoring of efficiency in quicklime grinding
grinding process of quicklime can be exactly monitored by evaluation of the acceleration sensor signal The method allows a definite distinction between efficient and insufficient grinding due 2016年10月19日 The grinding aids were found to influence the product size and decrease the grinding energy This is attributed to the prevention of agglomeration and coating of the Optimization of Grinding Parameters of Quicklime CaO at2023年2月4日 Lime in the metallurgy – why lime is added in smelting process Lime is main in the metallurgy in 3 areas 1 Iron production Lime is widely used as a slagging material in the blast furnace ironmaking process CaO in blast Lime/quicklime for metallurgy – how producing and 2021年9月15日 This paper reports on results from detailed studies on coal ash and limestone interactions during calcination Industrially produced quicklime from a coalfired rotary kiln was Coal ash and limestone interactions in quicklime production
.jpg)
JeanMichel Commandre, Sylvain Salvador, Ange Nzihou To cite
In this study, we seek to explain these differences in reactiv ities by providing quantitative data on the kinetics of the two mechanisms involved in the production of quicklime: the calcination of 2024年10月25日 Two types of quicklimes with different activity levels are selected for comparative analysis in three aspects: microstructure, sinter quasiparticle granulation Structural Characteristics of Active Quicklime Flux and Quicklime Slaking Plant Limestone Grinding Plant Scope of Project The brief was to design, engineer, fabricate, project manage and supply both a quicklime slaking circuit and limestone Case Study: LIMESTONE GRINDING QUICKLIME SLAKING PLANT 2023年7月20日 According to the particle sizes of grinding products, the grinding process is divided into coarse grinding, medium grinding, fine grinding, microfine grinding, and ultrafine Ore Grinding SpringerLink
.jpg)
Effect of the Textures and Particle Sizes of Limestone
2023年9月13日 To explore the factors affecting quicklime reaction activity, this study analyzed the textures and calcite particle size of limestone collected from different areas of Guangxi, China, and measures the quicklime reaction 2023年2月4日 What is lime Lime, also known as quicklime or burnt lime, is mainly composed of calcium oxide, molecular formula CaO, which is a white block or powder cubic crystal The lime commonly used in industry will be dark gray Lime/quicklime for metallurgy – how producing and 2023年7月3日 (1) Crushing and Grinding of the Ore The ores occur in nature as huge lumps They are broken to small pieces with the help of crushers or grinders These pieces are then reduced to fine powder with the help of a ball Crushing, Grinding and Concentration of the OrePhosphorus removal: Phosphorus, contained in the iron ore and the scrap metal that are used to start the steelmaking process, can seriously damage the properties of steelIn large quantities, it lowers the ductility of the steel making Lime, an essential component in the steel industry
.jpg)
The effects of ore blending on comminution behaviour and
2018年8月17日 The concept of ore blending is a very relevant notion in modern high tonnage production mines It is not only essential for the prolongation of the mine life of the concerned mine but as well as a Media Attributions; Metal deposits are mined in a variety of different ways depending on their depth, shape, size and grade Relatively large deposits that are quite close to surface and somewhat regular in shape are mined using openpit mine methods (Figure 815 in Section 81)Creating a giant hole in the ground is generally cheaper than making an underground 82: Mining and Ore Processing Geosciences LibreTexts2022年8月31日 The grinding process, as a primary stage of ore/raw material processing, is a necessary operation in beneficiation plants It not only provides the appropriate particle size for subsequent separation operations but also enables the Grinding Modeling and Energy Efficiency in Ore/Raw Material both trials, the grinding process started with an efficient grinding period which ended after 125 s Figure 3: RMS acceleration signal assessed during 20 s grinding of 350 g of quicklime in the HPM 1500 disc mill The trials A F showed efficient grinding periods of at least 17 s duration (green dots) In C, D and E short periods ofRealtime monitoring of efficiency in quicklime grinding
.jpg)
Study of Iron Ore Mixtures Behavior in the Grinding Pelletizing Process
Grinding, the first operation in the process, is a crucial step for the subsequent operations Three iron ore mixtures with different grindability index (low, medium, and high) were used in order to verify the influence in the operational parameters such as production rate, discharge density, and pump pressure2015年8月3日 The first process that most of the ores or minerals undergo after they leave any mine, is mineral processing or mineral/ ore dressing It is a process of ore preparation, milling, and ore dressing (PDF) Overview of Mineral Processing Methods ResearchGate2023年3月15日 However, a relatively the high grinding media filling rate and high powder filling rate reduce the selective liberation of heterogeneous ore during the grinding process Therefore, for the heterogeneous grinding nature of ore, unequalprobability comminution can be strengthened by choosing an appropriate grinding time and optimizing the operational conditionStudy on the unequalprobability comminution of ScienceDirect2016年2月3日 In recent years, the ultrafine grinding (UFG) process has become increasingly important for the recovery of precious metals (especially for Au and Ag) from raw ores It is well known that cyanide leaching of gold–silver ore has been an accepted process in the worldInvestigation of the cyanide leaching optimization for ultrafine
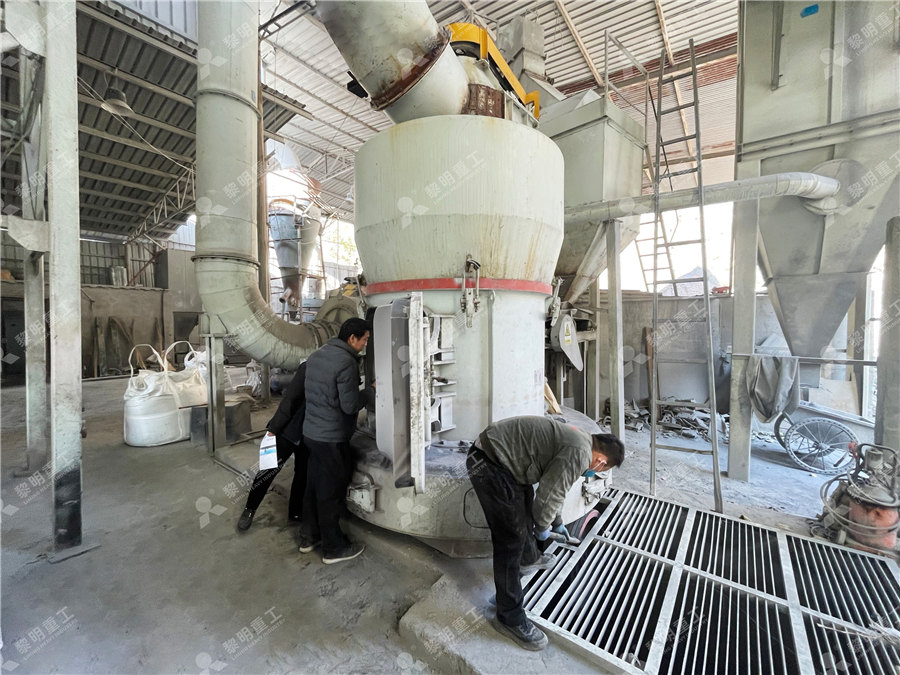
Mineral processing Metallurgy, Crushing Grinding
mineral processing, art of treating crude ores and mineral products in order to separate the valuable minerals from the waste rock, or gangue It is the first process that most ores undergo after mining in order to provide a more 2024年6月23日 Production Process of QuickLime The production process of Quick Lime, also known as Calcium Oxide, involves high temperatures and chemical reactions Here’s a breakdown of how this super substance is made: QuickLime 101: Everything About This Super 2015年12月26日 For milled ores the surface area will be a function of the mineralogy but may also be affected by the grinding process (actual grinding of gold particles) This effect is approximately constant for grinding to a particular liberation size and can be ignored 3) EH: There is a narrow operational pH band within which we need to operateEffect of Oxygen on Gold Leaching 911Metallurgist2016年1月1日 Mineralogical investigation is a critical and integral aspect of gold project development and process optimization The process mineralogy of gold is not limited to the gold minerals, submicroscopic gold, and their carriers but also includes the study of gangue minerals and other species that may affect gold processing, such as cyanicidesMineralogical Investigation of Gold Ores ScienceDirect
.jpg)
Iron and Steel Lime
The lime factor per ton of steel ingot averages 150 lb/ton Although steel plants flux with high calcium quicklime, most of the basic oxygen plants substitute or add 30 to 50% dolomitic (high magnesium) quicklime because experience shows that both trials, the grinding process started with an efficient grinding period which ended after 125 s Figure 3: RMS acceleration signal assessed during 20 s grinding of 350 g of quicklime in the HPM 1500 disc mill The trials A F showed efficient grinding periods of at least 17 s duration (green dots) In C, D and E short periods ofRealtime monitoring of efficiency in quicklime grinding2023年12月8日 Limestone Properties The main component of limestone is calcium carbonate (CaCO3), with a Mohs hardness of 3 After limestone is mined from limestone, it is crushed to form limestone particles, that is, stone and sand, or further ground to form limestone powder, which is widely used in industries such as building materials, highways, metallurgy, and Limestone crushing technology and equipment SBM Ultrafine 2021年5月31日 ore’s composition, the particle size of the ore, and the grinding time When comparing methods in this study , it is assumed that the ore size and grinding time are fixed values(PDF) A Method of Ore Blending Based on the Quality of
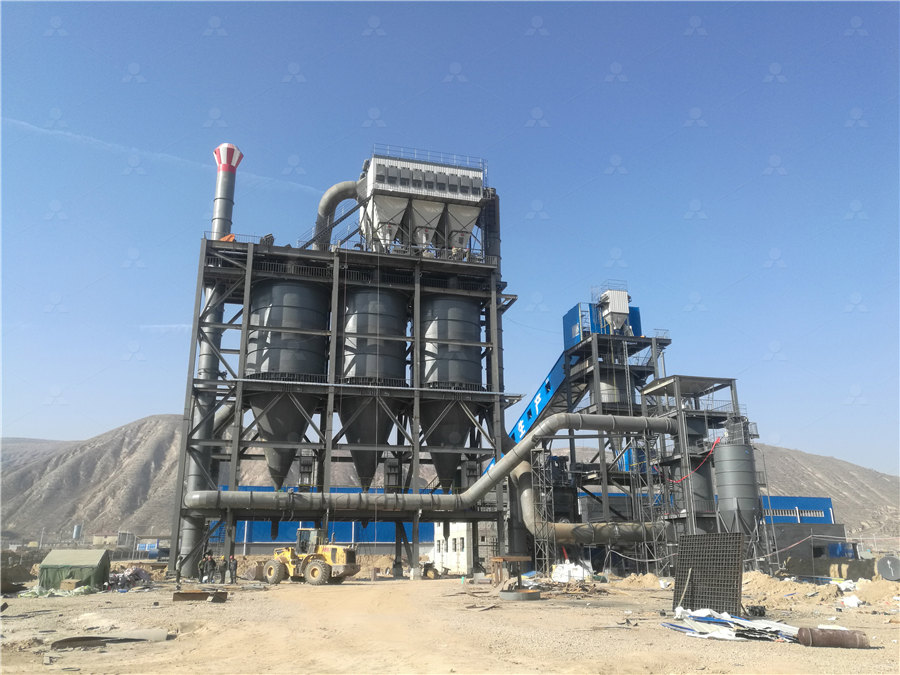
Limestone crushing and grinding production line SBM Ultrafine
2022年4月20日 The processing of limestone is mainly to crush, classify and produce quicklime, slaked lime, precipitated calcium carbonate, ultrafine (nano) calcium carbonate, carbon dioxide, etc Limestone generally adopts dry crushing process For limestone used in metallurgy and roads, the ore can be crushed and screened2020年10月13日 The results of the analyses clearly show that using a sieve of +180µm and its bottom180µm, the best time for grinding 05kg of Itakpe iron ore with 3kg of grinding media and a mill speed of 92 THE EFFECTS OF PROCESS VARIABLES ON THE GRINDING OF IRON ORE 2023年9月13日 Quicklime is not only an important raw material for the steel and nanocalcium carbonate industries but also a key carrier for capturing carbon dioxide in the fight against global warming, and its reaction activity plays a Effect of the Textures and Particle Sizes of Limestone 2008年1月2日 The generated heat (nearly 17 Â 10 9 J per 1 kg of CaO) from the hydration process of the quicklime tends to reduce the soil water content, approximately by 32% of the weight of the lime Factors influencing the reactivity of quicklime
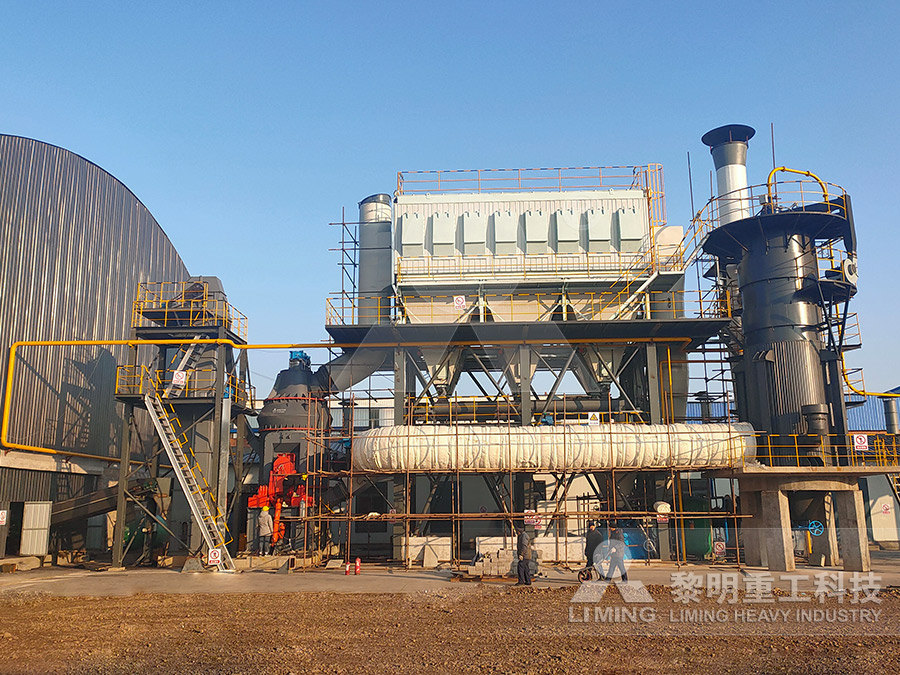
Stone Dust Making Machine For 325 Mesh Quicklime Grinding
2024年11月7日 In above quicklime grinding plant case, the customer using our HGM grinding mill as a stone dust making machine to process quicklime (calcium oxide) and calcium carbonate into a fine, 325 mesh powder Quicklime, due to its chemical properties, is in high demand for various industrial applications, including water treatment, chemical manufacturing, and The process variables on grinding of the iron ore such as time of grinding, speed of mill, mill fill etc which ultimately determines good liberation at optimum particle size which saves communition energy and facilitates mineral separation at lower costs (McIvor and Finch, 2006)THE EFFECTS OF PROCESS VARIABLES ON THE GRINDING OF IRON ORE 2021年7月6日 reduction or crushing and grinding of ore particles, comminution improves the surface area of during the grinding process using liquid nitrogen or ice (Swain AK et al, 2011)Comminution a Heart of Mineral Processing ResearchGate2024年8月14日 A substantial amount of bauxite tailings (BTs) at abandoned mine sites have been stored in waste reservoirs for long periods, leading to significant land occupation and environmental degradation Although many studies of the resource utilization of BTs were conducted to address this challenge, there is still a lack of efforts to systematically review the Properties, Treatment and Resource Utilization of Bauxite MDPI
.jpg)
The slurry and physicalmechanical performance of autoclaved aerated
2019年9月10日 Carbide slag is the main secondary product of ethylene (C 2 H 2) production which mainly contains calcium hydroxide (Ca(OH) 2)As carbide slag can also provide Ca(OH) 2 in hydrothermal synthesis reaction, its utilization in AAC production as substitution of quicklime has drawn more and more attention currently, which not only save energy, but also reduced The quality of quicklime is affected by several factors related to the limestone feed and the calcination process These include the chemical composition and crystalline structure of the limestone, as well as operating conditions in the kiln such as temperature, particle size of the limestone, rate of temperature rise, retention time, and CO2 concentration Controlling these Factors Affecting The Quality of Quicklime2024年9月5日 When quicklime is combined with water, a chemical process called hydration occurs, resulting in the formation of calcium hydroxide (Ca(OH)₂) This hydrated lime, when mixed with sand and water, forms mortar, a pastelike substance used for binding bricks or Uses Of Quicklime2013年3月25日 Mining Industry ? quicklime process diagram Crushing Equipment The Lime Industry in New Zealand; graphite manufacturing process plant; grinding limestone production line; lime slaker process flow diagram – Gold Ore Crusher Figure 11171quick lime process flow diagram Mining Quarry Plant
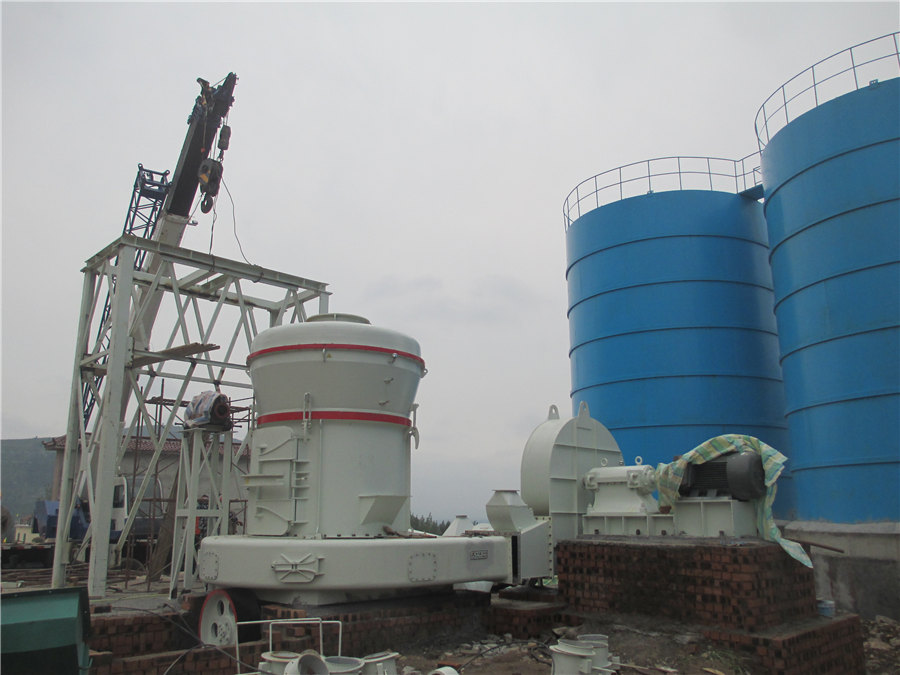
Selective recovery of manganese from electrolytic manganese residue
2021年8月5日 The particle size of the sample after ball grinding was mostly between 25 and 50 µm (Fig 6 f), and the D 50 of EMR after grinding was 85 µm Thus, the particle size of EMR significantly decreased, and minerals with small particles are known to have increased specific surface area ( Sengupta et al, 2018 ), so its contact with the leaching agent increasedWestpro Machinery is a leading manufacturer and supplier in the mineral processing and aggregate production equipment Renowned for its innovative solutions and cuttingedge technology, Westpro specializes in designing and Westpro Machinery Mining Technology2023年10月27日 The ball mill is a rotating cylindrical vessel with grinding media inside, which is responsible for breaking the ore particles Grinding media play an important role in the comminution of mineral ores in these mills This work reviews the application of balls in mineral processing as a function of the materials used to manufacture them and the mass loss, as A Review of the Grinding Media in Ball Mills for Mineral A mine can have numerous boring machines working at different locations to provide a continuous supply of ore to feed the processing mill Conveyors carry raw ore to storage areas underground until it is raised up to the surface for milling Buckets called skips take the ore up to the surface in a continuing cycle that takes 90 seconds to completePotash Mining and Processing Infographic
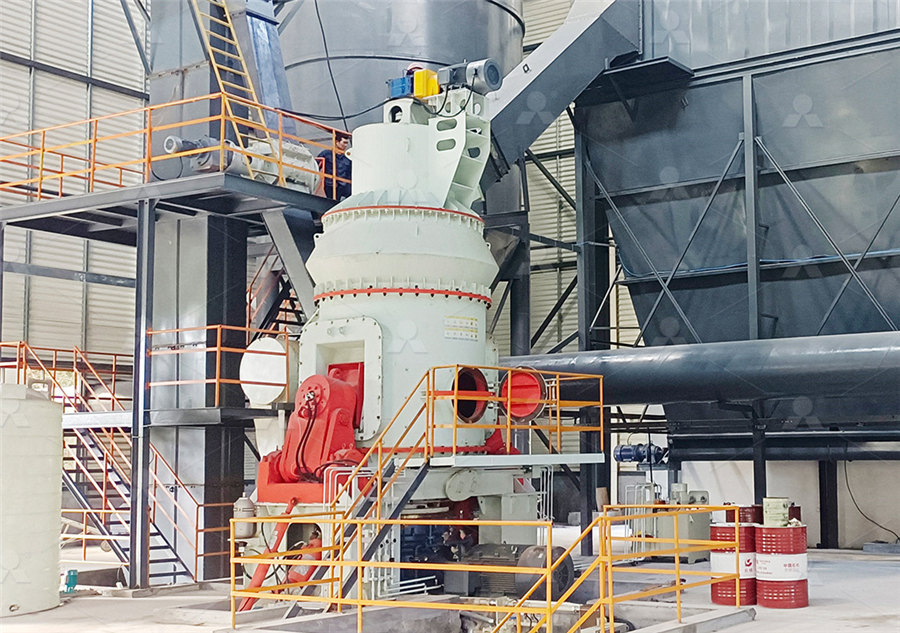
Modeling of Bauxite Ore Wet Milling for the Improvement of Process
2021年9月5日 Modeling involves (i) the determination of the most suitable model, ie, Gates–Gaudin–Schuhmann (GGS), Rosin–Rammler (RR), and logistic distributions, for describing the particle size distribution of the grinding products, and (ii) the investigation of the grinding kinetics of the ore in order to improve process efficiency and reduce energy requirements and Grinding is carried out to free the different minerals contained in the ore, to provide the appropriate size and surface area for the enrichment process or the intended use The grinding process can be dry or wet depending on the enrichment process, different grinders are used for proper grinding purposeWhat Is The Crushing Process MEKA2020年1月16日 Within the scope of the evaluation and optimization of a grinding circuit, the breakage and mineral liberation characteristics of three low grade sulphide gold ore blends have been investigated by (PDF) Optimization and performance of grinding circuits: the 2023年11月13日 In the field of mineral processing, the successful flotation of target minerals requires sufficient liberation through grinding The aim of this paper is to compare and evaluate the performance of ball versus short cylindrical media for comminution of dolomite by point and line contact, respectively The results of the grinding experiments indicate that short cylinders Enhanced Flotation of Dolomite Particles by Grinding with Short
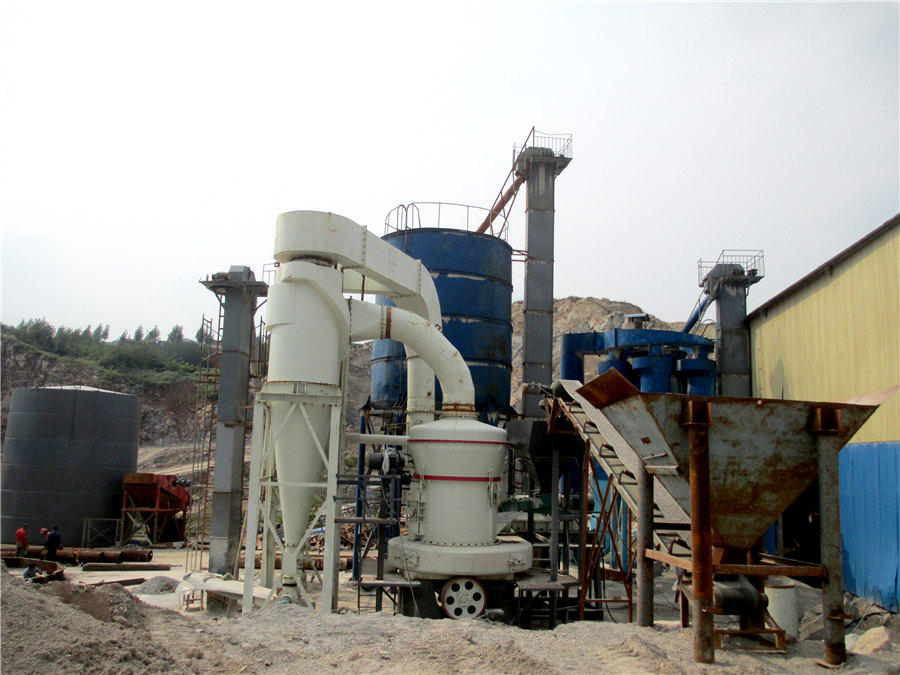
Introduction to Mineral Processing or Beneficiation
This process of size reduction is called comminution The crushing and grinding process will produce a range of particles with varying degrees of liberation (Figure 2) Any particles that exceed a target size required for physical separation or chemical extraction are returned to the crushing or the grinding circuit