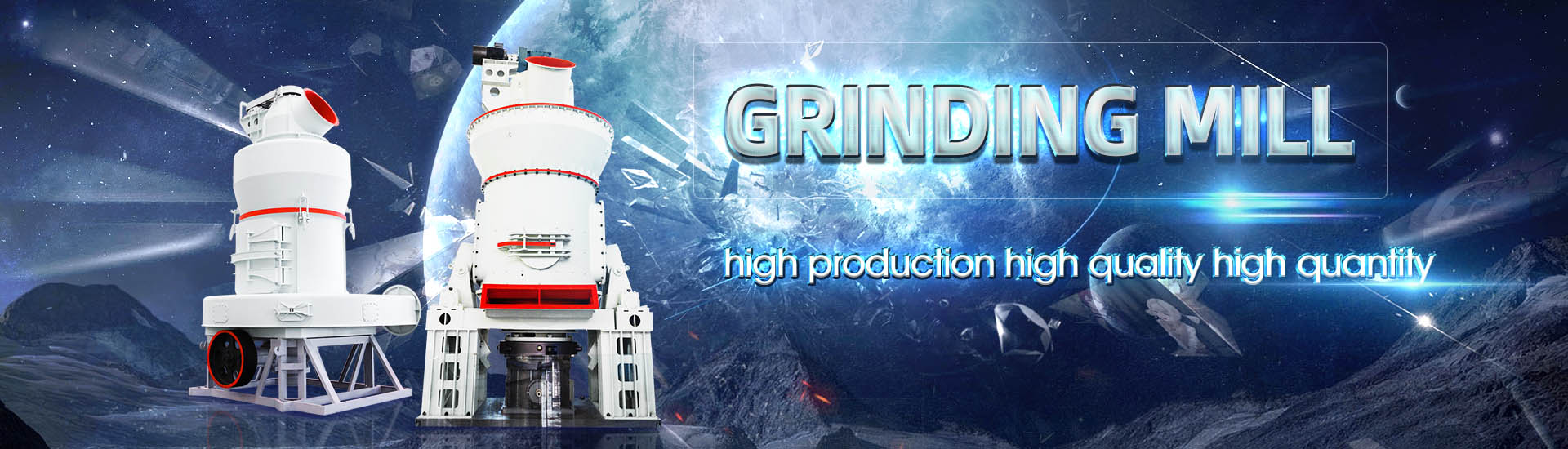
Ultrasonic highfine vertical mill transducer
.jpg)
Ultrahigh Frequency (100 MHz–300 MHz) Ultrasonic Transducers
2016年6月22日 In this paper, we report the design, fabrication and characterization of pressfocused LiNbO 3 transducers at frequencies of 100–300 MHz The high resolution imaging 2016年6月22日 We present an alloptical focused ultrasound transducer with a submillimeter aperture and demonstrate its capability for highresolution Ultrahigh Frequency (100 MHz–300 MHz) Ultrasonic 2020年4月1日 This paper presents the current state of ultrasonic transducers of magnetostrictiv type and piezoelectric type as well as applications of power ultrasound in various industrial Power ultrasound and its applications: A stateoftheart review2023年12月1日 Piezoelectric ultrasonicassisted precision machining (PUAPM) technology is considered to be an efficient and environmentally friendly machining strategy by virtue of A critical review of piezoelectric ultrasonic transducers for
制粉项目-2023.11.17.jpg)
Development of a highprecision piezoelectric ultrasonic milling
2022年5月15日 A novel piezoelectric ultrasonic milling tool based on a longitudinalbending hybrid piezoelectric transducer (LBHT) is proposed The major novelty of the proposed tool is 2024年8月1日 Piezoelectric micromachined ultrasonic transducers (PMUTs) capable of generating and receiving ultrasonic signals at the micrometer level have become a prominent technology in the field of ultrasound It is important Design and Fabrication of HighPerformance 2023年3月6日 Considering the need to investigate the 2D resonant vibration motion at the workpiece, this research aims to develop the twomode vibrational motion piezoelectric Design of a novel 2D ultrasonic transducer for 2D highfrequency 2023年9月15日 Here, we propose a method exploiting flexible piezoelectric ultrasonic transducers (FPUT) with 13 PZT8/PDMS composites to achieve a highfrequency and Active acoustic field modulation of ultrasonic transducers with
.jpg)
Fabrication, modelling and use of porous ceramics for
2007年3月29日 Porous ceramics are of interest for ultrasonic transducer applications Porosity allows to decrease acoustical impedance, thus improving transfer of acoustical energy to water or biological tissues For underwater 2008年6月1日 However, there is not enough documented information on design and technology of manufacturing a high power ultrasonic transducer this table pertain to fine and welltreated American bolts,An approach to design a high power piezoelectric 2016年6月22日 Transducer Morphology In this work, three kinds of transducers with center frequencies of 100 MHz, 200 MHz and 300 MHz were fabricated and labelled as “LN100”, “LN200” and “LN300”Ultrahigh Frequency (100 MHz–300 MHz) Ultrasonic 2008年1月17日 Application of ultrasonic waves has been considerably progressed during the last decade and piezoelectric ceramics have had a common use as the driving source of such waves However, there is not enough documented information on design and technology of manufacturing a high power ultrasonic transducer In this paper, an attempt has been made to An approach to design a high power piezoelectric ultrasonic transducer
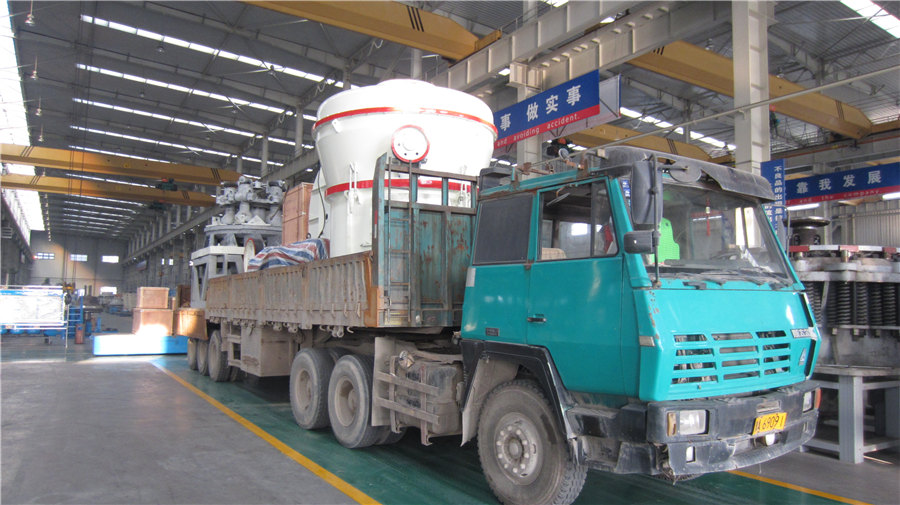
Maximize Efficiency with Ultrasonic Vibrating Screens Unitfine
Ultrasonic Transducer: The heart of the ultrasonic vibrating screen is the ultrasonic transducer This transducer generates highfrequency mechanical vibrations, typically in the range of 36,000 to 40,000 Hz (cycles per second) Vibrating Screen Mesh: The screen mesh is a sievelike surface that separates particles based on their size2019年12月6日 The viability for dry coupling of piezoelectric ultrasonic transducer components was investigated, using a thin foil of annealed silver as a filler material/coupling agent at each component interface(PDF) Dry Coupling of Ultrasonic Transducer Components for High 2010年12月6日 The major advantages of LiNbO3 and LiTaO3 over PZT are: (i) extremely chemically inert and leadfree materials; (ii) very high Curie temperatures (> 1150 °C and 600700 °C, respectively) thus (PDF) High temperature ultrasonic transducer up to 1000 °C 2020年4月1日 The objective of this paper is to present the latest developments of the ultrasonic transducer and power ultrasonic applications The review contents include the following two aspects: (1) Highlighting the current research trends in magnetostrictive transducer and piezoelectric transducer of different types; (2) Applications of power ultrasound in various Power ultrasound and its applications: A stateoftheart review
.jpg)
High Frequency and High Fill Factor Piezoelectric Micromachined
2014年5月30日 This paper presents high frequency (10 55 MHz), fine pitch (45 70 µm) PMUT arrays, which are fabricated with a simple Capacitive micromachined ultrasonic transducer 2020年11月1日 The Panametrics Videoscan ultrasonic transducer of 225 MHz and 13 mm diameter (V106SM) was used and it was configured to operate in pulseecho mode The transducer support was designed to be mounted between 2 ″ flanges and was machined in a thermoplastic material to improve the acoustic coupling with liquidsFlow pattern classification in waterair vertical flows using a single 2011年2月1日 To date, there are a number of groups that have successfully fabricated PZT thick films for transducer applications Tsuzuki et al [16] prepared PLZT thick films by multiple electrophoretic deposition and sintering process Barrow et al [17] and Lukacs et al [18] have reported thick PZT ceramic coatings using sol–gel derived porous 0–3 composites for high Piezoelectric films for high frequency ultrasonic transducers in 2015年7月1日 A shearverticalwave pointfocusing electromagnetic acoustic transducer is developed for the purpose of detecting stress corrosion cracking in stainless steelDevelopment of shearverticalwave pointfocusing
R)8OC`6F[ZIB.jpg)
Highperformance ultrasonic transducer based on PZT
2023年7月1日 Ultrasonic transducers are applied widely in nondestructive evaluation (NDE) in the industry [1], [2], [3], [4]Driven by enormous practical demands, NDE is expected to be employed in hightemperature environments [5]For instance, to achieve an online measurement of viscosity and density during the manufacturing process of molten plastic and glasslike During the testing process, it is necessary to adjust the vertical and angular positions of the ultrasonic transducer to maximize the echo signal The pulse transmitter/receiver used in this experiment (OLYMPUS, 5073 PR) is configured with a repetition frequency of 200 Hz, a damping of 50 Ω, energy of 124 μJ, and applied gain of 0 dBPiezoelectric metasurface for highfrequency ultrasonic transducer 2022年2月1日 Highfrequency ultrasound imaging technology can achieve longitudinal spatial resolutions higher than 40 μm, and is therefore ideal for both medical ultrasound imaging, as well as ultrasonic nondestructive testing applications [1]Accordingly, this technology is highly suitable for the observation of fine structures in human tissues and small defects in semiconductor Fabrication of 1–3 piezoelectric composites via ScienceDirect2020年11月1日 The signals were obtained from a single ultrasonic transducer mounted on the outer surface of the pipe using a water box The water box was used to acoustically couple the transducer with the pipe Using a spatiotemporal distribution of echo intensities, Ref [14] showed a qualitative difference between the signals of the different flow patternsFlow pattern classification in waterair vertical flows using a single
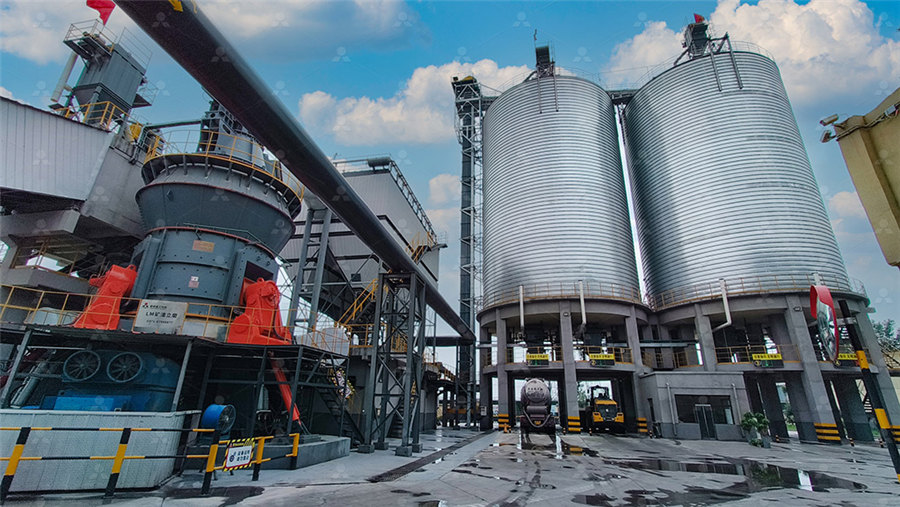
Ultrasonic HighResolution Imaging and Acoustic Tweezers Using
Sensors 2023, 23, 1916 3 of 13 details on the transducer design and fabrication procedure can be found in Lim et al [49,56] The fnumber was designed at 13 for both transducersUltrasonic transducers for extreme conditions: (a) with a thin protective layer; (b) with a delay line; (c) with a wedge; (d) with a waveguideHigh temperature ultrasonic transducers possess piezoelectric elements and passive parts (housing, protective/matching layers, electrodes, backing materials, adhesives, and connecting wires), which should be resistant to a high High Temperature Ultrasonic Transducers: A Review PMC2023年3月28日 The selected material has the following parameters, which are used to match the materials for each layer to build a hightemperature ultrasonic transducer: its coefficients of thermal expansion (CTE) are α 11 = 1486 × 10 − 6 / ∘ C and α 33 = 654 × 10 − 6 / ∘ C, its speed of sound v = 7340 m/s, its density is ρ = 465 g/cm 3 and so its acoustic impedance Z = 34 Ultrasonic Transducers for InService Inspection and Continuous Thus, high temperature measurements should always be done in Mode 2 or Mode 3 with either a delay line transducer (with an appropriate high temperature delay line) or an immersion transducer Sound velocity in all materials changes with temperature, normally increasing as the material gets colder and decreasing as it gets hotter, with abrupt changes near the freezing or Theory and Application of Precision Ultrasonic Thickness Gaging
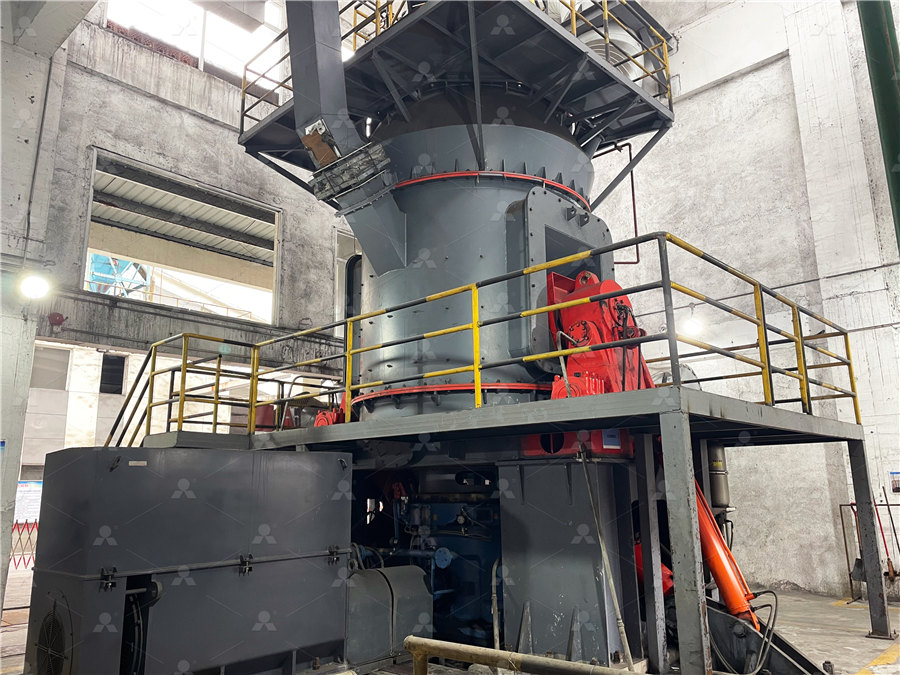
Ultrasonic Vibrating ScreenDAHAN Vibration
Solve the network blockage: convert 220V, 50Hz electric energy into 38KHz high frequency electric energy, input the ultrasonic transducer, and turn it into 38KHz mechanical vibration, so as to achieve the purpose of screening and cleaning 2009年6月1日 A highfrequency ultrasonic transducer for copper or gold wire bonding has been designed, analyzed, prototyped and tested Modeling techniques were used in the design phase and a practical design (PDF) Design of a Smart Ultrasonic Transducer for 2006年5月18日 Studies on ultrasonic microfeeding of fine powders View the table of contents for this issue, or go to the journal homepage for more 2006 J Phys D: Appl Phys 39 2444Studies on ultrasonic microfeeding of fine powders ResearchGate2023年3月6日 Ultrasonic vibration–assisted machining (VAM) is a process in which a tool or workpiece is vibrated using ultrasonic frequency smallamplitude vibrations to improve cutting performance, and an ultrasonic transducer usually generates these vibrations This study investigates how twodimensional vibrations are generated using axially polled piezoceramics Design of a novel 2D ultrasonic transducer for 2D high
.jpg)
Enhancement of the Transmission Performance of Piezoelectric
2022年4月10日 In this paper, a threedimensional model of a highfrequency piezoelectric micromachined ultrasonic transducer (PMUT) is established based on the finite element method (FEM)2014年10月1日 The images show a significantly fine blood speckle and allow for visual differentiation of vessel O 3 –PbTiO 3 system grown by the vertical Bridgeman method and its characterization Jpn J Appl Phys, 1 (37) (1998), pp 33823385 Broadband and hightemperature ultrasonic transducer fabricated using a Pb(In 1/2 Nb 1/2 Piezoelectric single crystal ultrasonic transducers for biomedical The models for the piezoelectric transducer and ultrasonic transmission media are of major importance in the design and simulation of electronics for ultrasonic systems Transducer impedance and material parameters used have a large influence on received echo amplitudes For simulation purposes a modified Leach model for the transducer [5] was High temperature phased array ultrasonic system with integrated 2021年4月1日 Request PDF Vertical cavity capacitive transducer The capacitive micromachined ultrasonic transducer (CMUT) has inherent advantages, such as larger bandwidth and monolithic integration Vertical cavity capacitive transducer Request PDF ResearchGate
.jpg)
High Performance RelaxorBased Ferroelectric Single Crystals
2014年7月29日 Abstract: Relaxorbased ferroelectric single crystals Pb(Mg 1/3 Nb 2/3)O 3PbTiO 3 (PMNPT) have drawn much attention in the ferroelectric field because of their excellent piezoelectric properties and high electromechanical coupling coefficients (d 33 ∼2000 pC/N, k t∼60%) near the morphotropic phase boundary (MPB) Ternary Pb(In 1/2 Nb 1/2)O 3Pb(Mg 2017年4月27日 Acoustic Parameters of Ultrasonic Transducers A hydrophone (HGL0085, ONDA Co, Sunnyvale, CA, USA) was used to measure acoustic fields of both excitation transducer and detection transducers, and Multifunctional Ultrasonic Microelastography Imaging System 2022年3月26日 Ultrasonic machining is a process of manufacturing that removes material from the presence of fine abrasive particles In this paper, we will study the Definition, Construction or Parts, Working The highfrequency Ultrasonic Machining: Definition, Parts, Working 2023年6月1日 This study used a PbNb 2 O 6 piezoelectric crystal with a high Curie point suitable for working in hightemperature environments to make a hightemperature piezoelectric ultrasonic transducerDevelopment of A Hightemperature Piezoelectric Ultrasonic Transducer
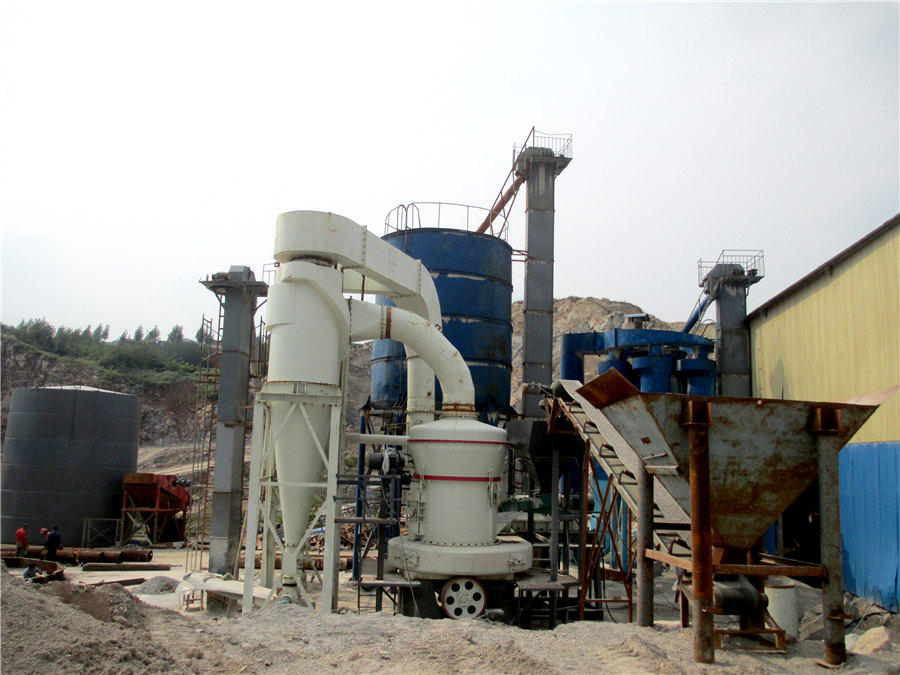
(PDF) Design and Fabrication of HighFrequency
2022年8月14日 The two prominent MEMS ultrasonic transducers, the capacitive micromachined ultrasonic transducer (CMUT) and the piezoelectric micromachined ultrasonic transducer (PMUT), are known for their We also offer special hightemperature wedges for use with angle beam transducers: the ABWHT series for use up to 260 °C or 500 °F and the ABWVHT series for use up to 480 °C or 896 °F For more detailed information on available sizes, reach out to your local Evident sales representative Couplants for HighTemperature Ultrasonic TestingHighTemperature Ultrasonic Testing Olympus IMS2003年6月1日 1 IntroductionUltrafine pitch wire bonding and copper bonding require a higher stability and robustness of the ultrasonic vibrations generated by the transducer compared to current ultrasonic horns [1], [2]Furthermore bond grid arrays (BGA) applications and the prospect of being able to dramatically decrease the temperature of the wire bonding process demand New technology for the design of advanced ultrasonic 2018年1月5日 In this work we use high performance polyethylenimine (PEI) as a backing substrate with the product name Ultem 1This polymer substrate with thickness around 850 μm provides good thermal stability (for our processing temperatures ≤135 °C) and good impedance matching to the copolymer layerAlso, its low acoustic attenuation allows us to estimate High frequency copolymer ultrasonic transducer array of
.jpg)
High Frequency Flexural Ultrasonic Transducers The University
Our levitation system can be oriented in different ways, from vertical through to horizontal, maintaining the levitation of the particles, "The high frequency flexural ultrasonic transducer for transmitting and receiving ultrasound in air", IEEE Sensors 2022年5月15日 In terms of the WVAM, the workpiece is driven by the vibration of the worktable For example, Ko et al [61] developed a onedimensional WVAM worktable with a frequency of 40 kHz, which realized the highprecision milling of 6061 aluminum alloy with a surface roughness of Ra 0105 μm through ICE Shen et al [62] presented a onedimensional WVAM worktable that Development of a highprecision piezoelectric ultrasonic milling 2017年2月1日 Finally, we discuss the future prospects of highfrequency ultrasonic transducer techniques Discover the world's research 25+ million members; 160+ million publication pages;Progress and prospects of highfrequency ultrasonic transducer 2019年12月19日 The ultrasonic horn is a crucial component of RUMSs; it amplifies the amplitude of ultrasonic vibrations originating from the transducer, transmits the ultrasonic energy, and matches the system impedance 53 The design objectives for the ultrasonic horn are (1) to ensure that the resonant frequency is close to the theoretical value, (2) to minimize the energy Advances in rotary ultrasonic machining system for hard and