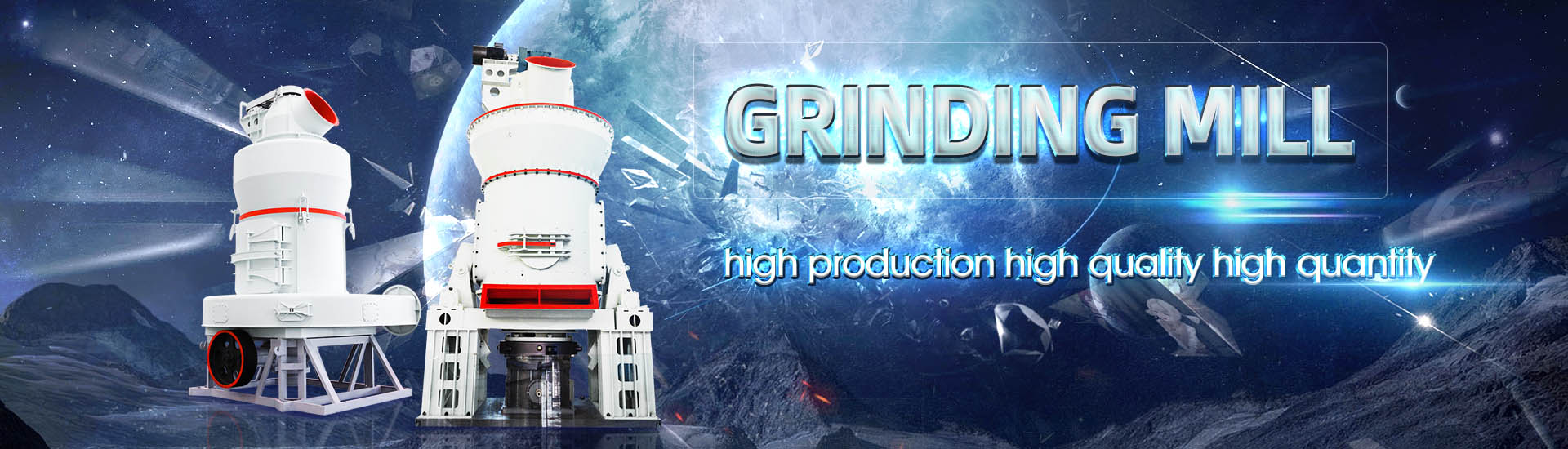
Performance of suspended industrial roller mill
.jpg)
Optimization of working parameters of highpressure roller mill
2024年11月15日 In this paper, based on the simulation of orthogonal test data, the entropy weight method is used to construct a comprehensive evaluation system for the performance of 2022年5月31日 The vertical roller mill (VRM) is commonly used for secondary and tertiary crushing processes in numerous industries In this study, the discrete element method (DEM) Analysis of vertical roller mill performance with changes in material 2017年4月1日 ABSTRACT This study shows the performance of a currently running vertical roller coal mill (VRM) in an existing coalfired power plant In a power plant, the coal mill is the Operational parameters affecting the vertical roller mill 2021年3月1日 Issues concerning the modification of mill designs, especially in terms of improving performance characteristics, are among the important ones due to the very low Selected Aspects of Modelling and Design Calculations of Roller
.jpg)
Roller Mill Based on Experimental Method Semantic Scholar
Abstract: This work concentrates on the energy consumption and grinding energy efficiency of a laboratory vertical roller mill (VRM) under various operating parametersThe roller mill’s ability to reduce materials to a uniform particle size provides more control of product characteristics and minimizes waste, as shown in Figure 1 The mill’s controlled Roller mills: Precisely reducing particle size with greater efficiency2017年4月1日 In this study, pilot scale tests were performed with a mobile verticalrollermill grinding plant to investigate the relationships between operational parameters The Operational parameters affecting the vertical roller mill 2023年8月15日 To describe the behavior of the rolling mill while accounting for many parameters and their interactions, finite element analysis techniques are used The Enhancing hot rolling mill performance through experimental
.jpg)
Nonlinear optimal control for the hotsteel rolling mill
2019年9月26日 Control of hotsteel rolling mills aims at raising the levels of quality of the related industrial production and at minimising the cost of the electric energy consumed by such industrial units This paper proposes a non 2017年1月1日 Thus, the performance of an industrial ball mill can be adequately described using the orespecific breakage distribution function together with the systematic variation of the material transport (PDF) Performance optimization of an industrial ball Horizontal roller mills are often compared with vertical roller mills, and they boast several advantages: Better particle size distribution: The horizontal arrangement can lead to a more consistent grind Lower initial investments: Sometimes they are more economical when it comes to capital expenditure Flexible operation: Skilled operators can adjust horizontal mills to Exploring the Different Types of Roller Mills2022年1月23日 This work concentrates on the energy consumption and grinding energy efficiency of a laboratory vertical roller mill (VRM) under various operating parameters For design of experiments (DOE), the response surface method Analysis and Optimization of Grinding Performance of
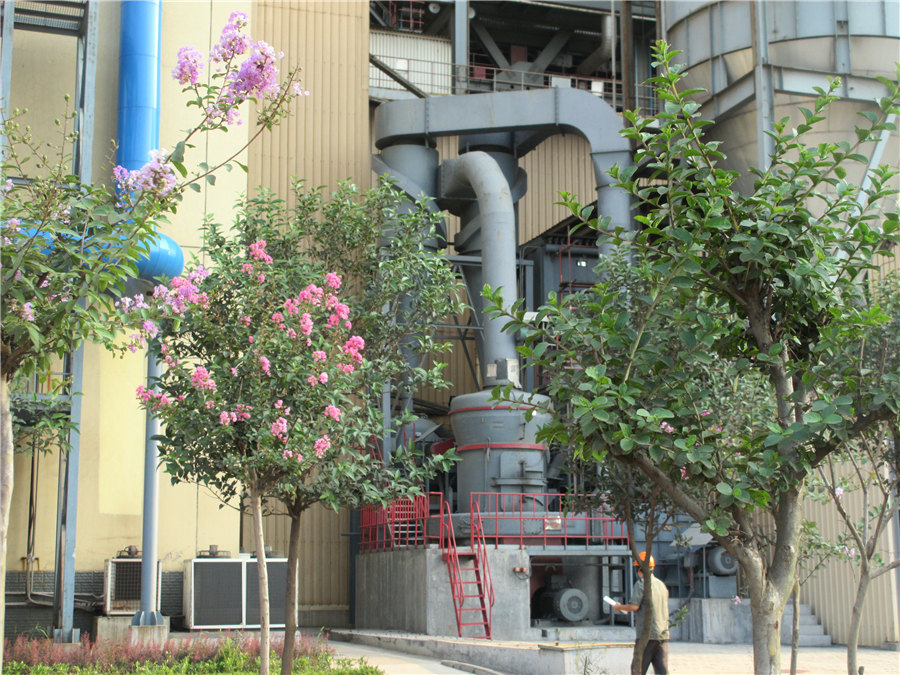
Analysis and Optimization of Grinding Performance of Vertical Roller
2022年1月23日 This work concentrates on the energy consumption and grinding energy efficiency of a laboratory vertical roller mill (VRM) under various operating parameters2021年9月16日 The performance of hammer mill was evaluated taking into consideration hammer mill capacity, efficiency, particle size distribution (fineness degree), power, energy requirement and operational costDesign, Fabrication, and Performance Evaluation of a Hammer Mill 2017年4月1日 In this study, pilot scale tests were performed with a mobile verticalrollermill grinding plant to investigate the relationships between operational parameters The identification and quantification of the grinding parameter relationships was carried out to implement these relationships into a computational verticalrollermill performance modelOperational parameters affecting the vertical roller mill performance 2024年1月15日 Sun et al [9] carried out study of a roller mill (HRM 4800 by Hefei Zhong Ya, China) and analysed air flow patterns in the mill to improve the energy efficiency of the mill Shah et al [ 10 ] used modelling to optimise the performance of a coal pulveriser by studying the influence of variation in inlet vane angles on the collection efficiency of the powder and desired Optimisation of the performance of a new vertical roller mill by
.jpg)
Industrial Roller Mills Williams Crusher
Williams industrial roller mills are used for a wide range of applications and materials, which means that the proper feeder selection is essential for highcapacity, troublefree operation, and more efficient production You can customize your roller mill system depending on what material you need reducedDigital Solutions for Industrial Processes (SODA) from ABB aims to do just that Key concepts from SODA have now been integrated into the ABB Ability™ Data Analytics for cold rolling mills solution, which forms the basis for the newreleased ABB Ability™ Performance Optimization Service for cold rolling millsImproving cold rolling mill performance with data analytics2022年5月31日 Analysis of vertical roller mill performance with changes in material properties and operating conditions using DEM Author links open overlay panel Chang Liu a, Zuobing Chen a, Weili Zhang b, Ya Mao a, Pengyun Xu c, Qiang Xie a Due to the limitation of industrial experiments, Analysis of vertical roller mill performance with changes in 2020年11月4日 1 Introduction The vertical roller mill, integrating various processes including crushing, grinding, drying, conveying, and powder selection [1, 2], is broadly employed in many fields like cement, electric power, metallurgy, chemical, and nonmetallic ore industriesHowever the vertical roller mill, as a common choice due to its multiple functions, always consumes Effects of Blade Parameters on the Flow Field and Classification
.jpg)
A comparison of wear rates of ball mill grinding
2016年1月1日 The performance of grinding media in a ball mill is also measured in terms of its wear rate These tests are inexpensive and less timeconsuming than the tests in industrial millsVertical Roller Mill Summary Free download as PDF File (pdf), Text File (txt) or view presentation slides online Ball mill vs vertical mill Operations Structure of a vertical mill Working Process Components Dam Ring Armour Ring Louver Ring Grinding Table Rollers Separators Maintenance Performance ImprovementVertical Roller Mill Summary PDF Mill (Grinding) Industrial 2021年1月1日 With the grinding capacity of a vertical roller mill and the ability to dry, grind and sort in a single unit, the vertical roller mill offers a definite advantage over the ball mill system [10] A twocompartment ball mill with a highly efficient separator is still procured for new cement grinding units installation, although the vertical roller mill has now become a trueReview on vertical roller mill in cement industry its performance 2020年11月4日 Effects of Blade Parameters on the Flow Field and Classification Performance of the Vertical Roller Mill via Numerical Investigations November 2020 Mathematical Problems in Engineering 2020(4):115Effects of Blade Parameters on the Flow Field and Classification
.jpg)
Optimization of milling performance of a sugar mill ResearchGate
2020年1月1日 This study was conducted to find the optimization of milling performance of a sugar mill based on extraction (EXT The m aximum throughput could be limited due to insufficient roller 2024年8月6日 While the process of developing roller milling came into existence in the 19th century, it took an industrial revolution to make roller flour mills the most common flour mills today The arrival of automatic machinery, forced by steam and like electricity, put the wheel of grain processing on the move, achieving higher yields and cleaner flour qualityRevolutionizing Flour Production: The Development and 2022年8月11日 The comparative technique was found suitable in the evaluation of the performance of the mills ment of handquern with roller wheel mill a round 1000 BC [6] Though the A Comparative Technique for Performance Evaluation of Hammer Mill Raymond Roller Mills: More than 2,000 roller mills have been supplied since the first mills were designed in the late 1800’s These early machines were the forerunner of the heavyduty, rugged ringroll mill manufactured today The roller mill provides the needed flexibility to economically and efficiently process a wide variety of materialsRAYMOND® ROLLER MILLS PDF4PRO
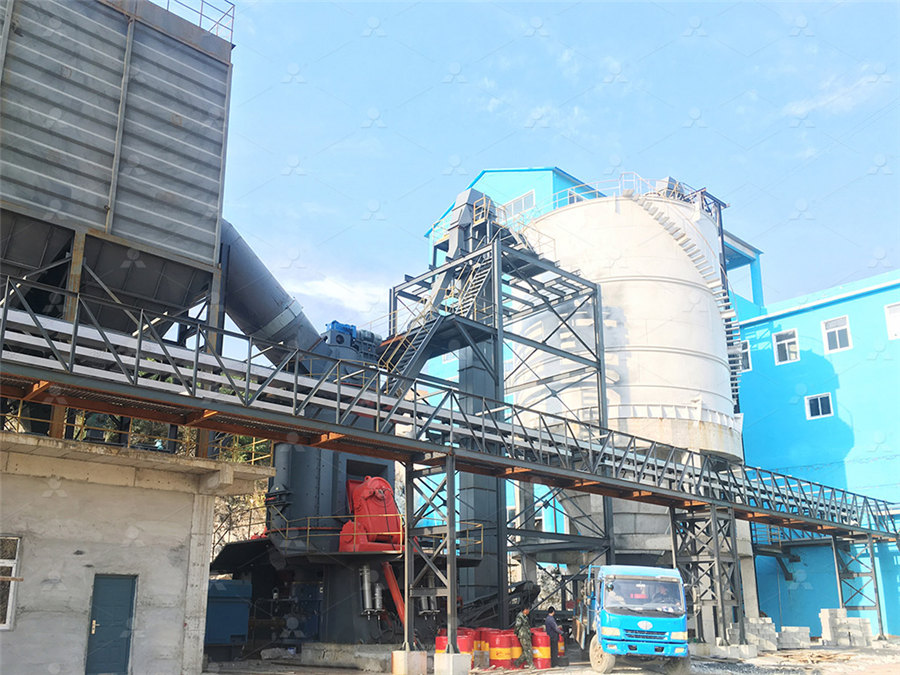
Grinding and classification performance evaluation and
Grinding and classification performance of an industrial scale Horomill grinding and classification closed circuit was evaluated Perfect mixing modelling approach was implemented to model Horomill process Classification performance of the high efficiency dynamic TSV air separator was evaluated by using efficiency curve approach [2]Manufacturer of Flour Mill Machinery Automatic Roller Mill, Roller Mill, Roller Flour Mill Machinery and Roller Flour Mill Plant offered by Indopol Food Processing Machinery Private Limited, Faridabad, HaryanaAutomatic Roller Mill Manufacturer from Faridabad IndiaMARTRolling mills offer numerous advantages in metal shaping and production processes, but they also present certain limitations and challenges that must be addressed Understanding the pros and cons of rolling mills is essential for optimizing their usage and performance in various industrial applications Advantages:Metal Shaping: The Impact of Rolling Mills and Rolling Machines for energy saving and size reduction One of the roller press mills available is Poittemill produced by POITTEMILL INGENIERIE Group, France This mill combined with air classifiers has been commercially applied into powder processing plants (Wang and Forssberg, 2004) To date the modelling of the performance of high pressure roll mill has beenModelling of an Industrial Scale High Pressure Roller Mill DiVA
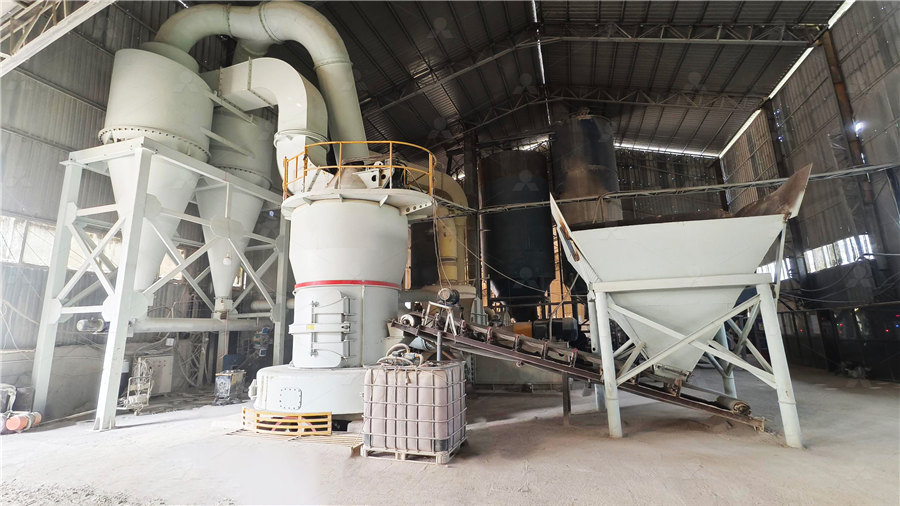
An investigation of performance characteristics and energetic
The ring and roller mill of the MPS series is an applied force mill with 3 stationary grinding rollers that roll on a rotating grinding table The material to be ground fedRequest PDF On Sep 1, 2016, Deniz Altun and others published Operational parameters affecting the vertical roller mill performance Find, read and cite all the research you need on ResearchGateOperational parameters affecting the vertical roller mill performance Vertical roller mills and ball mills represent two clearly distinct technologies However, with proper adjustments to the operational parameters of the vertical roller mill almost identical cement properties can be achieved by the two mills that satisfy the cement user’s demandsNevertheless, the two types of mills have their distinctive meritsCement grinding Vertical roller mills VS ball mills2003年1月31日 All rolls were manufactured to industrial configurations for wheat flour milling, having diameters of 250 mm, but only 100 mm in length (compared with 1000 mm typically for industrial roller millsOn Predicting Roller Milling Performance IV: Effect of Roll
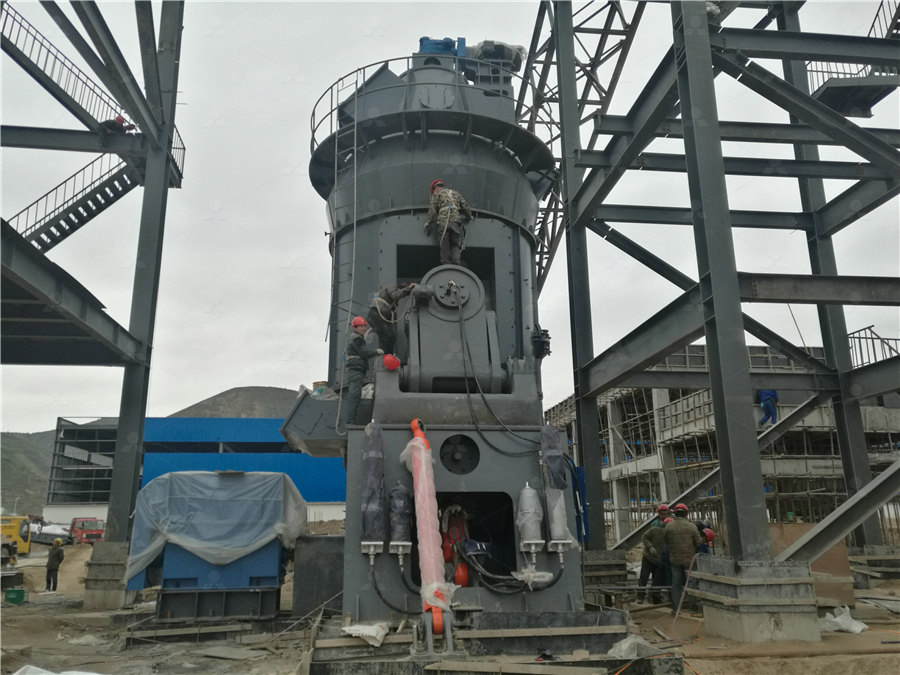
Grinding and classification performance evaluation and
Request PDF On Jan 1, 2016, Ö Genç published Grinding and classification performance evaluation and modelling of an industrialscale horizontal roller mill process Find, read and cite all 2023年1月1日 A twostage HPGR–horizontal stirred mill circuit has been proposed and its specific energy requirement was determined by a series of stirred mill tests adopting a pilotscale HPGR and JKSimMet® model, it was shown that this circuit consumed 13 %–31 % less energy than SAB/AGBC/SABC circuits for Cu porphyry ore (Wang, 2013) and consumed 92 % and Evaluating the performance of an industrialscale high pressure efficient The majority of the available corn mill designs in the Philippine market are for the village and industrial level operations that are high in price and capacity The aim of this study was to develop a financially feasible hammer mill for smallscale corn milling operation TheDesign, Fabrication, and Performance Evaluation of a Hammer Mill 2020年11月22日 Various treatment processes for pulp and paper industrial effluents, including aerobic, anaerobic, photocatalysis, electrochemical, ozonation, coagulation–flocculation and adsorption treatment (PDF) Characteristics and Treatment of Pulp and Paper Mill
.jpg)
VersaMill RMS RollerGrinder
From corn cracker machines to versatile roller mills, upgrade your ethanol production with RMSRoller Grinder RMS is your partner in ensuring the best possible equipment for your application Talk to An Expert2022年2月14日 Corn ground with either a hammer mill (HMC) or a roller mill (RMC) was used in a starter diet with 3142 kcal metabolizable energy (ME)/kg (fed 0 to 21 days) and in grower diets with 3032 and 3109 (PDF) Effect of Grain Moisture Content and Roller Mill Gap Size on Alvan Blanch manufacture Roller Mills with proven highperformance results on a variety of cereals and pulses Hammermills Alvan Blanch produces a wide range of Hammermills that can be used for industrial or farm applications: for grinding grain to fine flour or to coarse meal for animal feed productionRoller Mills • Alvan Blanch 2024storage roller hearth furnace No 1 (TF1), two large reduction roughing mills (RM), pendulum shear No 2 (PS2), double heat storage roller hearth furnace No 2 (TF2), six finishing mills (FM), highspeed flying shears (HSS), and two downcoilers (DC) Compared with the traditional hot rolling production line, this production lineImprovement in shape control performance of finishing mills in
.jpg)
Operational parameters affecting the vertical roller mill performance
Operational parameters affecting the vertical roller mill performance In a future case study, they will be given for a possible industrial scenario The main parameter related with the product rate and product particle size is the classifier rotor speed2023年12月4日 This study investigated the effect of table speed (mill speed), roller and table gap, dam ring height, and rolling resistance of material using the discrete element method in an industrialscale VRMNumerical Investigation of Vertical Roller Mill Operation Using 2023年12月4日 An industrialscale vertical roller mill has been developed and successfully simulated employing the discrete element method Pareek P, Sankhla VS (2021) Review on Vertical Roller Mill in Cement Industry and its performance parameters Mater Today: Proc 44:4621–4627 https: Numerical Investigation of Vertical Roller Mill Operation Using parameters on vertical roller mill grinding performance In this context, systematic test plans have been generated According to test plans; dam ring height, grinding pressure, classifier rotor speed, airflow rate, mill differential parameters were tested ii INVESTIGATION OF EFFECT OF OPERATIONAL PARAMETERS ON VERTICAL ROLLER
.jpg)
Vertical Roller Mills used for the comminution of mineral ores
energyefficient size reduction compared to tumbling mills Figure 1: Vertical roller mill operating principle (left: standard configuration, right: configuration with grit extraction) Pilot plant description and standard testing methods The grindability of a particular mill feed forms the basis for the design of an industrial grinding plant