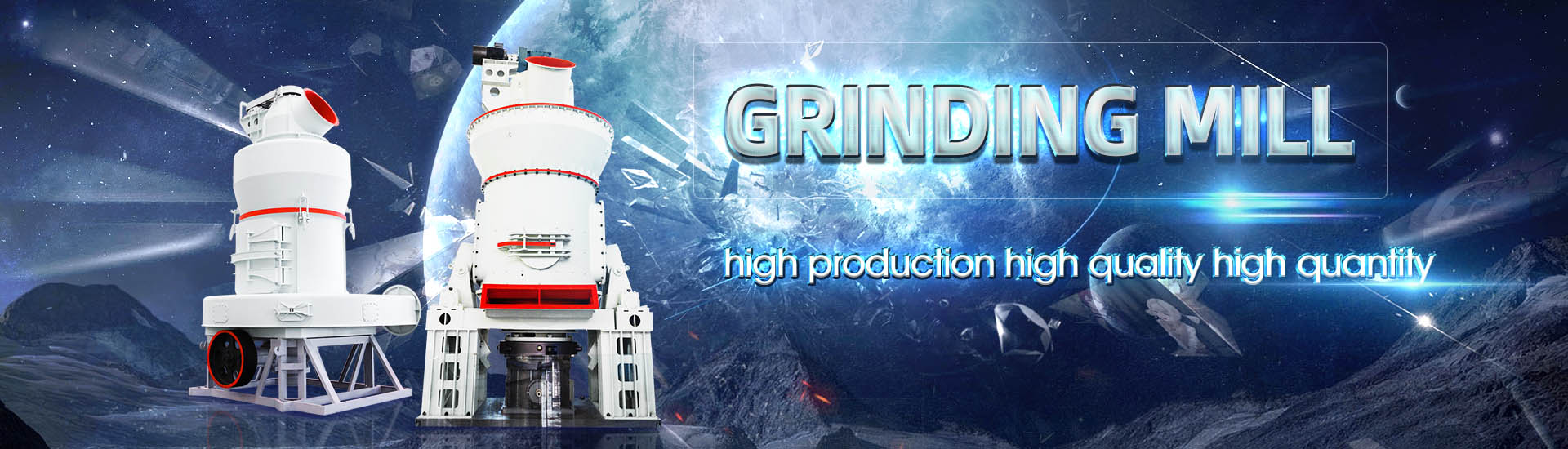
Pulverized coal production road
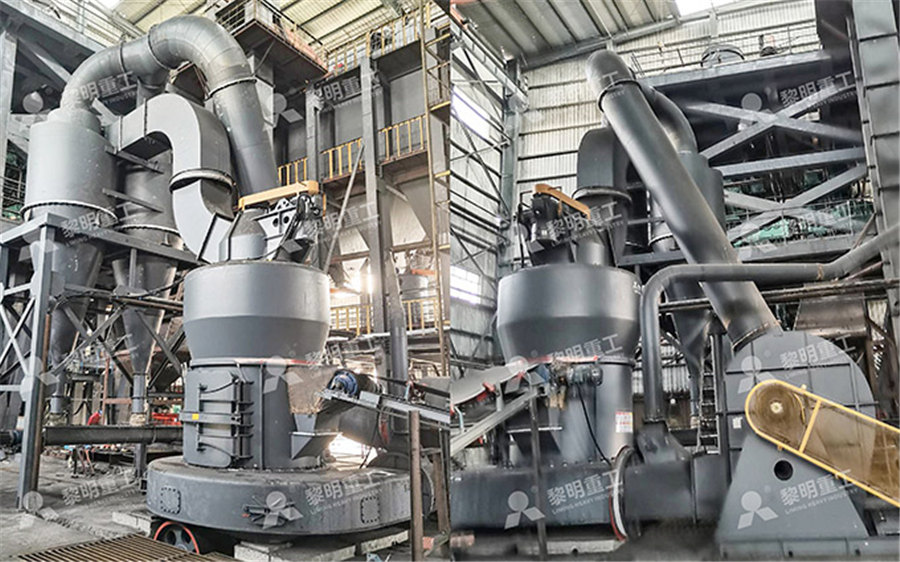
Fundamentals of pulverised coal combustion ICSC
It addresses the processes and their underlying mechanisms involved in pulverised coal combustion namely: drying and heating, devolatilisation, volatile oxidation and char oxidation Pollutant formation during combustion is also reviewed How these processes may be affected Pulverised coal firing has been the dominant technology for generating power in utility boilers for almost a century During this period, boiler designs have evolved through an accumulating Understanding pulverised coal, biomass and waste combustion2023年1月13日 The pulverized coal combustion process in power boilers is still being improved by the preliminary cleaning of coal and the use of various catalytic additives(PDF) Pulverized CoalFired Boilers: Future Directions of For a higher efficiency of the technology supercritical and ultrasupercritical coalfired technologies have been developed These technologies can combust pulverised coal and Pulverised Coal Combustion with higher efficiency
.jpg)
Nitrogen migration and gasification characteristics of pulverized
2024年11月10日 In this technology, a multinozzle impinging entrainedflow gasifier is used for the first time to preheat pulverized coal (PC), and the gasified fuel enters a downfired 2021年11月26日 Characterization of coal finds an important place in researches concerning coal spontaneous combustion and coal dust explosion This study investigated the physico Physicochemical characteristics of pulverized coals and their 2019年2月14日 The aim of present paper is to review various aspects of pulverized coal combustion such as oxyfuel combustion, cocombustion of coal and biomass, emissions from pulverized coal furnaces, ash formation and A complete review based on various aspects of Oxyfuel combustion makes it possible to implement the scenario of Carbon Capture and Storage (CCS) to significantly reduce CO2 emissions without using sorption processes after New Technologies of Pulverized Coal Combustion OxyFuel

A Review of the Numerical Modeling of Pulverized Coal
2021年4月8日 This Review comprehensively summarizes the current research on numerical modeling to offer a better understanding of the technical aspects and provides future research requirements of HELE coalfired boilers, 2023年1月13日 The paper provides an outlook on future directions of research and the possible applications for pulverized coalfired boilers One potential direction for future research is to focus on the ways (PDF) Pulverized CoalFired Boilers: Future Directions made by coke production Increased productivity CP Pulverized Coal Injection Technik (GB) 04/2016 / Issue 1 Due to a policy of continued improvement, 788 Cheung Sha Wan Road, Lai Chi Kok, Kowloon, Hong Kong T: +852 2544 1848 E: Pulverized Coal Injection Ammermann2015年1月5日 Worldwide, the major thrust for coal research and development is focussed on developing and commercialising high efficiency low polluting plant In particular, coalfired plant capable of carbon capture and storage is a high priority Work on fundamental coal science therefore tends to be organised to support these aimsUnderstanding pulverised coal, biomass and waste combustion
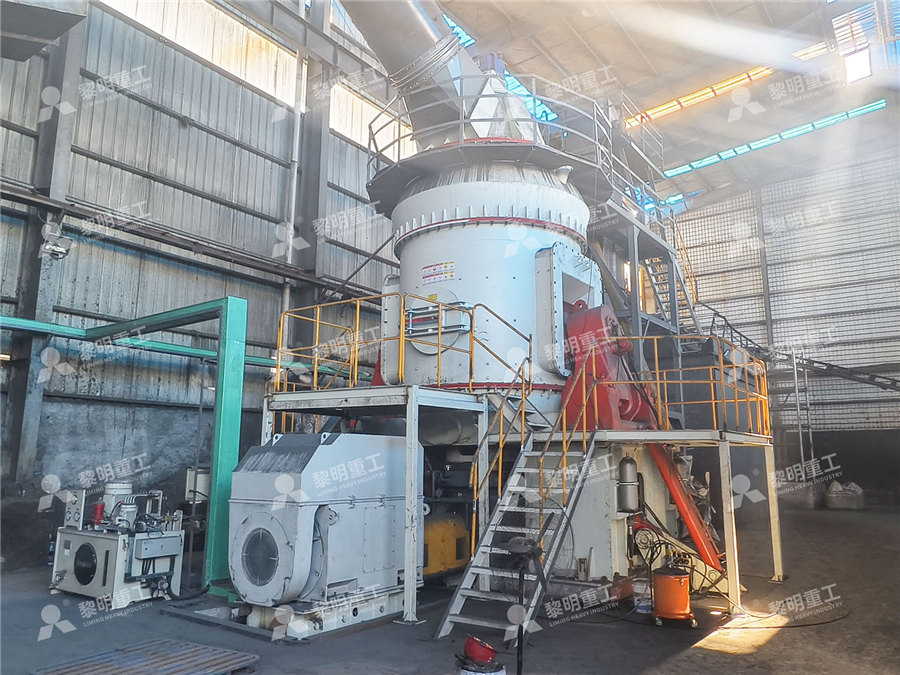
A complete review based on various aspects of pulverized coal
2019年2月14日 Coal is the most abundant energy source, and around 40% of the world's electricity is produced by coal combustion The emission generated through it put a constraint on power production by coal combustion There is a need to reduce the emissions generated through it to utilize the enormous energy of coal for power production1996年4月10日 Exhaust gas temperature in coalfired power plants can reach approximately 120 °C to 140 °C, with the thermal energy accounting for approximately 3% to 8% of the total input energyDevelopments in Pulverized CoalFired Boiler Technology2019年1月1日 Review of the investigations of pulverized coal combustion processes in large power plants in laboratory for thermal engineering and energy: Part B January 2019 Thermal Science 23(Suppl 5):16111626(PDF) Review of the investigations of pulverized coal combustion Pulverised coal power plants account for about 97% of the world's coalfired capacity The conventional types of this technology have an efficiency of around 35% For a higher efficiency of the technology supercritical and ultrasupercritical coalfired technologies have been developed These technologies can combust pulverised coal and produce steam at higher temperatures Pulverised Coal Combustion with higher efficiency
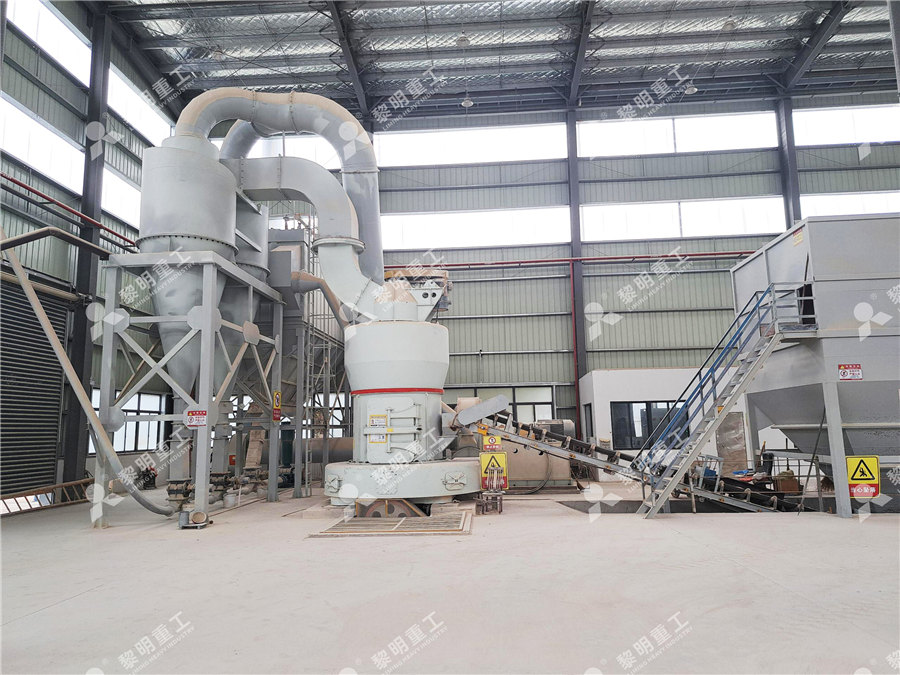
Coal Fly Ash Utilization in India SpringerLink
2023年2月10日 11 Characterization of Fly Ash Physical properties The physical properties of fly ash powders are varied Naik et al reported that the bulk density (g/c) of fly ash powders ranges from 09 to 13, the specific gravity is between 16 and 26, the plasticity is either lower or nonplastic, the shrinkage limit (volume stability) is higher, the clay content is negligible (%), 2017年5月1日 The introduction of pulverizedcoal injection at Yenakiieve Iron and Steel Works in 2016 is described The state of the lining of the blastfurnace shaft and hearth is analyzedIntroduction of pulverizedcoal injection at Yenakiieve Iron Download Citation On Aug 1, 2023, Binxuan Zhou and others published Twostage gasification process simulation and optimization of pulverized coal for hydrogenrich production using Aspen plus Twostage gasification process simulation and optimization of 2020年9月11日 The pulverized coal injection (PCI) is pursued to reduce the hot metal production cost by replacingthe expensive metallurgical coke with the noncoking coalTechnological advancements in evaluating the
.jpg)
Pulverised Coal an overview ScienceDirect Topics
Pulverized coal (PC) combustion is presently the system of choice for coalfired powergenerating plants In PC combustion, the coal is dried and is ground to a specified fineness, with a maximum particle size of 250–300 μm, depending on the reactivity of the coal2024年3月22日 On average, the production cost of biochar is estimated at $200 to $400 per ton, with energy consumption ranging from 1000 to 1500 kWh per ton In contrast, the production processes of pulverized coal and coke are usually more complex, requiring significantenergy and equipment inputs The production cost of pulverized coal and coke can rangeToward Carbon Emission Reduction in Steel Production by 2019年5月30日 It is therefore important to understand the pulverizedcoal combustion mechanisms and develop clean coal technology for pulverized coal fired power plants However, the combustion of pulverized coal is a complex phenomenon compared to that of gaseous or liquid fuels, since dispersion of coal particles, devolatilazation and oxidation reactions take CFD Study of a Pulverized Coal Boiler SpringerLinkCoalbased fly ash Shania Zehra Naqvi, Kamal K Kar, in Handbook of Fly Ash, 2022 161 Pulverized coal combustion In pulverized coal combustion (PCC), dust burners are used to feed coal into the combustion chamber, where flame core zones of the combustion chamber having a temperature range between 1450°C and 1600°C are presentPulverised Coal Combustion an overview ScienceDirect Topics

Pulverized Coal Injection of Blast Furnace Ironmaking
2024年1月1日 The characteristics of pulverized coal injection of blast furnace ironmaking include basic performance (ash, sulfur, and fixed carbon) and process performance (ignition point, explosibility, grindability, ash fusion temperature, combustibility, and reactivity), which is an important basis for the selection of coal types for pulverized coal injection of blast furnace Road Repairing Machine Pulverized coal production line is widely used in power plants, steel works, industrial boilers, textiles, heating centers, steam power centers, etc Capacity: 6110tons/hr Moisture of Raw Coal: ≤15% Finish Pulverized Coal Production Line2021年8月18日 The combustion of pulverized coal has been extensively studied by CFD models in the tuyere and raceway of TBF, and the reliability of this method has been fully proven20,28,29 As shown in supplementary Table S4, although the simulation conditions such as blast parameters and pulverized coal characteristics are not completely consistent with those in Ref Influence of Reducing Gas Injection Methods on Pulverized Coal Steel Production: In the steel industry, pulverized coal injection (PCI) is used in blast furnaces to reduce coke consumption and enhance furnace efficiency Cement Production: Pulverized coal is used as a fuel in rotary kilns for cement production, contributing to the clinker formation process Benefits of Pulverized Coal The use of Understanding Pulverized Coal: Benefits, Risks, and Safety

Analysis of pulverized coal migration during CBM production
2015年4月20日 Coal fines can block fractures in coal reservoirs, leading to the nonrecoverable decrease of coal permeability Therefore, coal fines can directly affect the gas production of CBM wells ( Cao et Various characterization methods are used to investigate the physical and chemical properties of steel plant flying dust and waste oil sludge, and the combustion characteristics of the mixtures with pulverized coal are studied via thermogravimetric analysis; the catalytic combustion mechanism is also explored The results show that two types of metallurgical byproducts with Combustion Characteristics of Coal for Pulverized Coal 2024年5月10日 In this study, simulations were carried out to study the combustion characteristics within a 600 MW Wshaped pulverized coal boiler under O2/N2 and O2/CO2 atmospheres The objective of this work is to Simulation of Soot Formation in Pulverized Coal D max are shown in Fig 9a The overall performance is that when v is the same, the larger D max is, the lower K is The production performance of Well W1 under different D max values is Schematic diagram of pulverized coal production
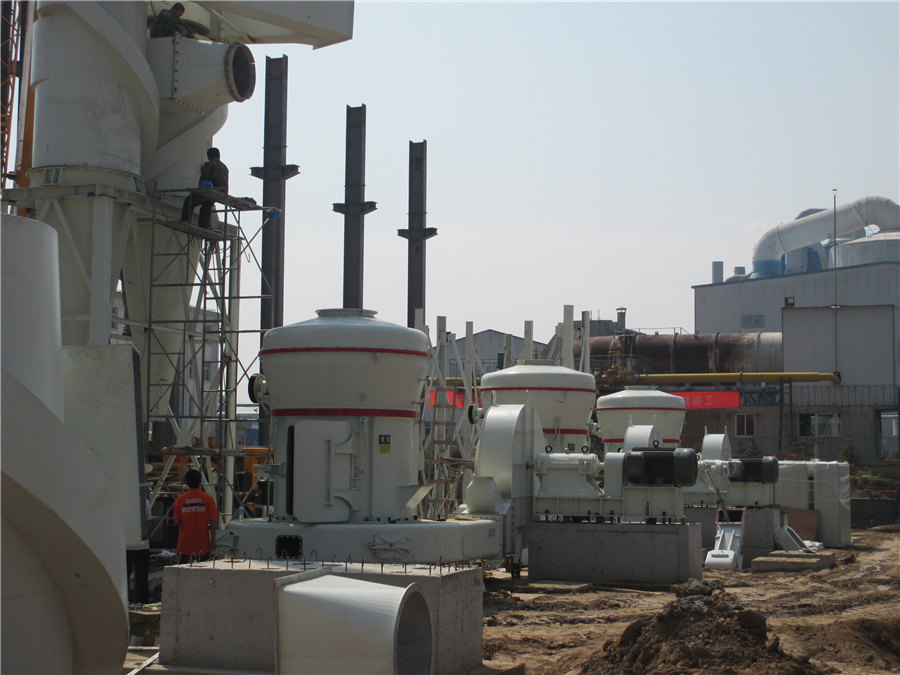
Pulverized coal versus circulating fluidizedbed boilers Perspectives
Keywords: circulating fluidized bed, pulverized coal, emissions Abstract—Power generation in South Africa has historically and continues to depend on the use of pulverized coal combustion The pulverized coal boilers are used by the majority of power stations around South Africa Although other types of technologies, such as2022年8月1日 Existing pulverized coal (PC)fired power plants are increasingly being operated in loadfollowing mode [1]Most of PC power plants in the United States are the drumtype subcritical units, which were built over 30 years ago, and designed for base load operationPredictive modeling of a subcritical pulverizedcoal power plant bituminous coal with a heating value (HHV) of 11,380 Btu/lb The coal's ultimate analysis is shown in Figure 1 The original fuel system consisted of three springloaded, MB type, vertical spindle mills, each gravimetric belt feeder, seal air fan, 1800 rpm primary air fan, and four mill outlets supplying pulverized coal to one of the threeWorldProven Coal Pulverizer Technology Debuts in the USand pulverized coal along with mixing uniformity under scanning electron microscopy (SEM), the graphite powder whose properties are similar to pulverized coal (the average particle size is close to pulverized coal) is adopted as the base mixing substance, and the additives and adding method are the same as bustion Characteristics of Coal for Pulverized Coal Injection
.jpg)
Physicochemical characteristics of pulverized coals and their
2021年11月26日 Characteristics of pulverized coals have significant influence on the spontaneous combustion and explosion processes This paper presents an experimental and theoretical framework on physicochemical characteristics of coal and their interrelations from spontaneous combustion and explosion perspectives The chemical properties, morphology, 2023年8月1日 As the major primary energy source in China, coal has been proved to be capable to improve its physical and chemical characteristics by the pretreatment of the selfpreheating burner In this study, the effects of altering operating conditions including preheating temperature (Tp) and primary air equivalence ratio (λp) on preheating characteristics of three typical Experimental Study on Product Characteristics of Typical Pulverized 2022年3月16日 The production process of direct reduced iron from titanomagnetite by coal reduction in air in rotary kiln is a key step in the extraction of titanium and iron This process is conducive to alleviating the stocking problem of a large amount of Tibearing blast furnace slag The relationships between particle movement and pulverized coal injection combustion in Particle motion simulation and pulverized coal injection 2024年1月11日 With a vertical roller mill (VRM) VRMs consist of a rotating table or bowl and rollers 1 To grind the coal, feed raw or initially crushed coal into the mill which is then ground between the rotating components; 2 Finally, hot air How to Process Coal into Pulverized Coal in 5 Steps?
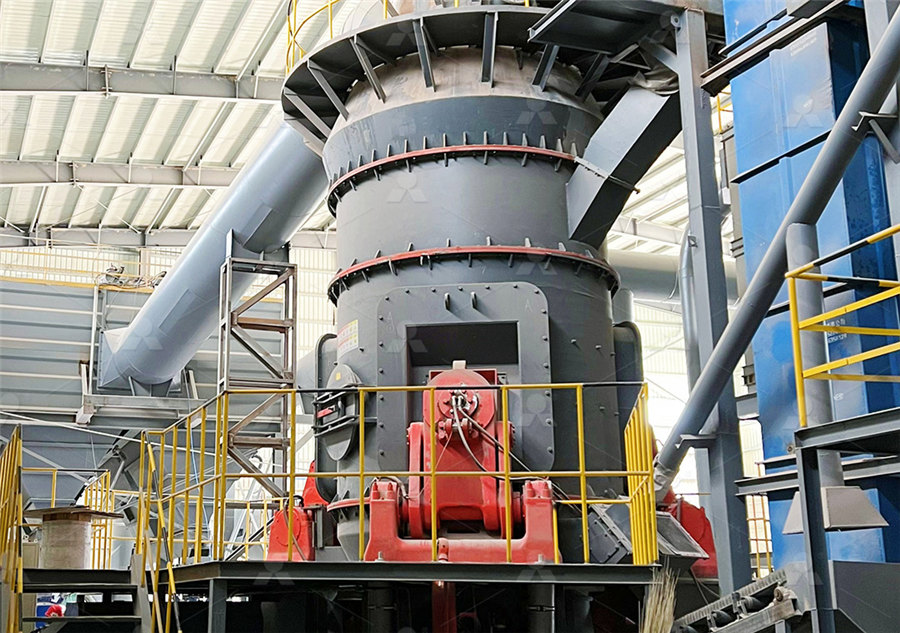
Strategy Paper on Coal Import Substitution
Coal Production and projection in FY 2030 PCI Pulverized Coal Injection PRC Peak Rated Capacity thm tonnes of hot metal UG MGR, Belt, Road etc) and suggest suitable long term and shortterm measures for enabling coal import substitution 2019年1月1日 For coal and gas dualfired boiler, pulverized coal mass flow and gas volume flow into furnace are important criteria for boiler operation adjustment, and they are important input parameters for Calculation Method of Pulverized Coal Mass Flow Spontaneous combustion of pulverized coal has become a safety topic and has been extensively researched This study using differential scanning calorimetry investigated the exothermic characteristics and spontaneous combustion risk of three metamorphic pulverized coal samples during oxidative combustion, for oxygen concentrations of 21, 19, 17, 15, 13, 11, 9, 7, and 5 Effect of Oxygen Concentration on the Oxidative Thermodynamics Also, the influences of pulverized coal injection on the coke consumption, the production rate of pigiron and the bosh gas temperature are examined in relation to some blast gas conditions such as the oxygen enrichment and the moisture addition KEY WORDS: ironmaking; pulverized coal injection; blast furnace; coal combustion; coke combustion;Maximum Rates of Pulverized Coal Injection in Ironmaking Blast Furnaces
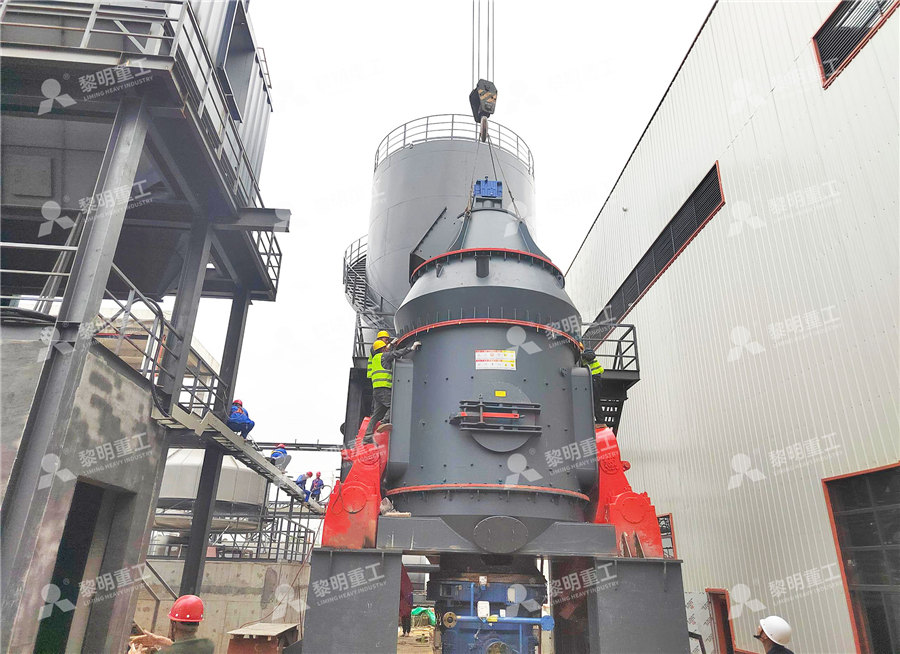
Novel coaltomethanol process with nearzero carbon emission
2022年3月10日 For coalbased methanol production, coal is intermingled with O 2 of AS and subsequently subjected to CG for producing crude syngas The cryogenic separation technology is primarily used in the AS for oxygen production, which is a high energy consumption process (Xiang et al, 2014)Because of the small hydrogentocarbon (H/C) ratio in coal, WGS process used in India for electricity production is bituminous coal Kumar and Nandi [14] studied the combustion characteristics of high ash Indian coal (Bhatgaon coal mine), wheat husk (WH), wheat straw (WS), and their blends for the temperature range of 30700oC at atmospheric oxygen content and pulverized coalIgnition and Emissions Characteristics of Pulverized Coal 2015年1月5日 During the last hundred years, pulverised coal combustion has been widely applied for electricity generation [1] More recent, deregulation of the European power sector [1], low coal prices and a Understanding pulverised coal, biomass and waste combustion – A pulverized coalfired boiler is an industrial or utility boiler that generates thermal energy by burning pulverized coal (also known as powdered coal or coal dust since it is as fine as face powder in cosmetic makeup) that is blown into the firebox The basic idea of a firing system using pulverised fuel is to use the whole volume of the furnace for the combustion of solid fuelsPulverized coalfired boiler Wikipedia
.jpg)
Pulverized Coal Boiler an overview ScienceDirect Topics
Fuel preparation for a pc boiler occurs in a mill, where coal is typically reduced to 70% through a 200mesh (74μm) screen Figure 2 shows a particlesize distribution from a bowlmill grinder typically used in power plants A typical utility specification for particle size distribution of the coal is that 70% of the mass should pass through a 200mesh screen, which is equivalent to 70%