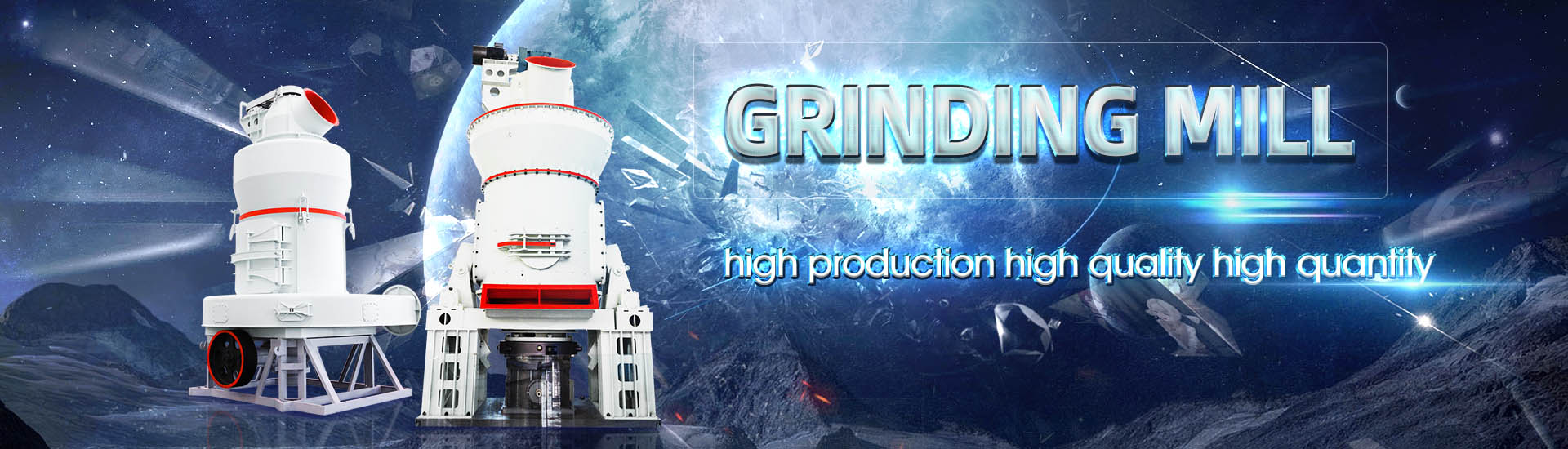
Electrolytic aluminum waste slag grinding mill hydraulic rock grinding mill HB30G
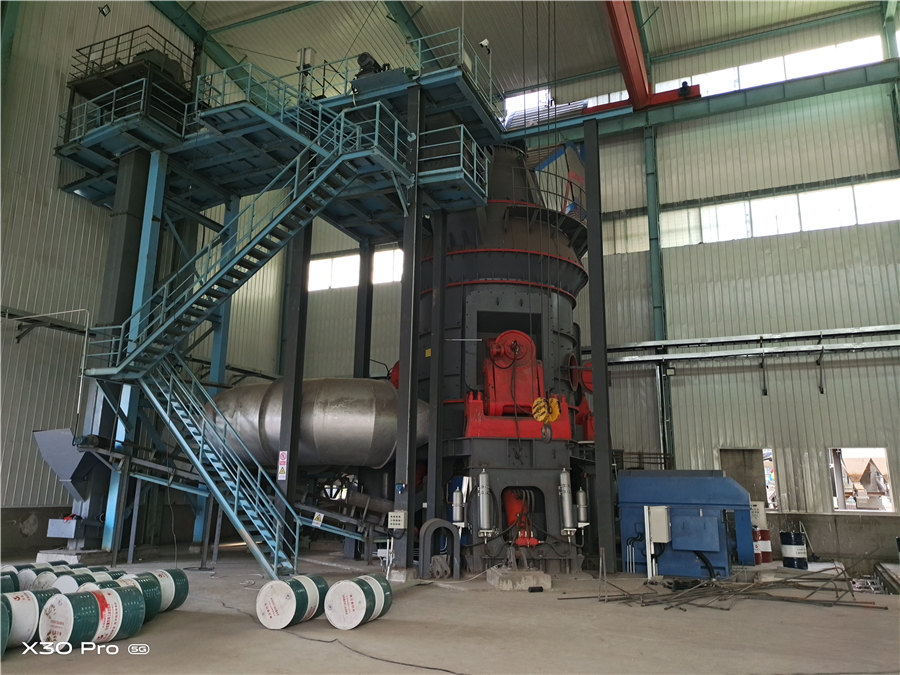
Research Progress of Electrolytic Aluminum Overhaul Slag Disposal
2023年4月25日 This article analyzes and summarizes the composition and hazards of the overhaul slag and the current development status of domestic and international electrolytic Coal gangue is a byproduct of the production of coalassociated minerals, Review of Research on the Pr2024年2月1日 The electrolytic aluminum industry generates a large amount lithium (Li)containing electrolytic aluminum slag (EAS) annually, and this can result in severe Efficient lithium recovery from electrolytic aluminum slag via an 2023年3月12日 The aluminum electrolysis industry continually and unavoidably produces hazardous solid waste in the form of carbon anode slag Carbon anode slag poses a serious (PDF) Recovery of Carbon and Cryolite from Spent Carbon Anode
.jpg)
Regeneration of raw materials for aluminum electrolysis from
2023年5月20日 A closedloop recycling process was proposed to recover valuable components from SCA and regenerate raw materials for aluminum electrolysis in this paper A new two 2023年3月12日 For carbon anode slag of electrolytic aluminum, Ni et al investigated the selective comminution and grinding mechanisms of rod and ball mills and proposed that a Recovery of Carbon and Cryolite from Spent Carbon Anode Slag2022年1月10日 In this study, grinding characteristics of spent carbon anode from aluminum electrolysis in both ball mill and rod mill were analyzed, and compared based on the utilization Selective comminution and grinding mechanisms of spent carbon 2022年10月10日 In this work, electrolytic aluminum carbon anode slag was separated by flotation Using the selectivity index ( SI ) as an indicator, the influencing factors of the carbon Recovery of carbon and cryolite from spent carbon anode slag of
.jpg)
The recycling of carbonrich solid wastes from aluminum
2024年5月23日 Here, we review carbonrich solid wastes with focus on sources and hazards, detoxification, separation, recovery, recycling and disposal Treatment techniques include 2024年7月24日 The lithium was selectively recovered and enriched from spent aluminum electrolyte slag by using calcium salt roasting transformation followed by HBL121solvent Cleaner Process for the Selective Extraction of Lithium from Spent 2007年2月1日 But nowhere in the world have so many roller mills for granulated blast furnace slag grinding been sold as in China during the last 6 years First Polysius slag roller mill in China The first Polysius roller mill for slag grinding in China is in operation since 2002 in Anshan in the province of LiaoningSlag grinding with the Polysius Roller Mill in China2022年10月9日 1 Department of Mining Engineering, Shanxi Institute of Technology, Yangquan, China; 2 Department of Mining Engineering, Balochistan University of Information Technology, Engineering and Management Sciences Recovery of carbon and cryolite from spent carbon
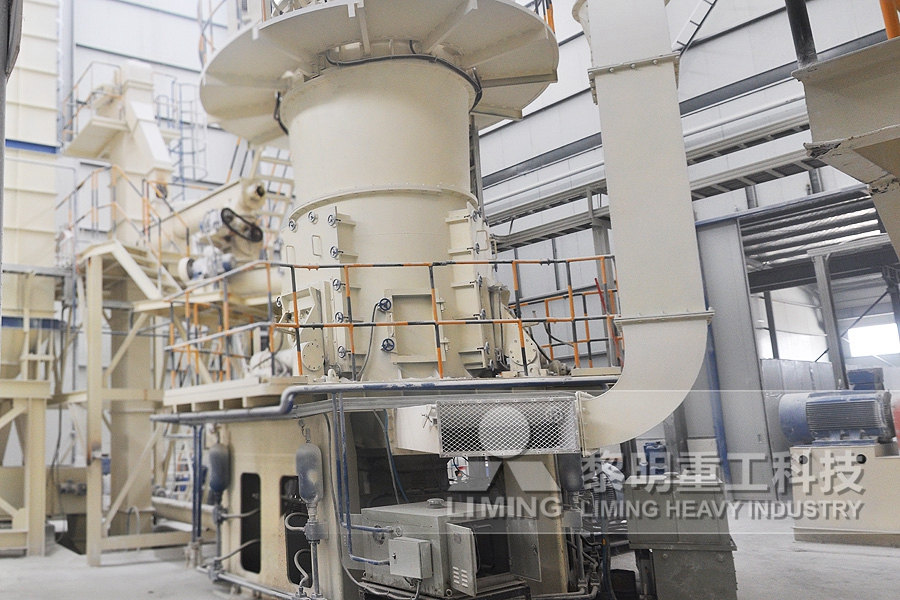
The recycling of carbonrich solid wastes from aluminum electrolytic
2024年5月23日 16 Million metric tons of spent carbon electrodes modify carbonrich solid wastes from aluminum electrolysis are produced annually, threatening ecosystems by cyanide and fluoride pollution Here, we review carbonrich solid wastes with focus on sources and hazards, detoxification, separation, recovery, recycling and disposal Treatment techniques 2017年2月20日 All Grinding Mill Ball Mill Manufacturers understand the object of the grinding process is a mechanical reduction in size of crushable material 911 Metallurgist is a trusted resource for practical insights, solutions, and support in mineral processing engineering, helping industry professionals succeed with proven expertise Grinding Mill Design Ball Mill Grinding Mill Design Ball Mill Manufacturer 911MetallurgistFor grinding slag, we proposal you the Vertical Grinding Mill, which is designed and manufactured based on our advanced design idea, in combination with the European technology and the market demand Spare PartsSlag Grinding Mill PlantKefid MachineryProduct Name: GGBS Production Line / Slag Mill Capacity: 3,6000 – 1,000,000 T/Y Grinding Systems: VRM system, Ball mill open circuit system, Ball mill closed circuit system, Roller press final grinding systemGGBS Production Line Slag Mill for Slag Powder Grinding AGICO
.jpg)
Stone Crushers, Mill and Grinding
As of 2019, Shibang Industry and its affiliated companies have 5 advanced mining machine production bases and a production base in Xiuwu, Jiaozuo, Henan, which is under construction, with a total production area of 1,200,000 square meters, and will be able to better meet the needs of global customers in the future Grinding Mills: Ball Mill Rod Mill Design PartsCommon types of grinding mills include Ball Mills and Rod Mills This includes all rotating mills with heavy grinding media loads This article focuses on ball and rod mills excluding SAG and AG mills Although their concepts are very similar, they are not discussed herePhotographs of a glass ended laboratory ball mill show Grinding Mills 911MetallurgistHCM’s HC1700 vertical pendulum Raymond mill, HLM series manganese carbonate vertical mill and other equipment have a high reputation in manganese ore enterprises all over the world market share, the following two types of electrolytic manganese powder grinding mill equipment will be introduced to youNews How to choose the electrolytic manganese powder grinding mill 2 GRINDING ICNTERNATIONAL CEMENT REVIEW SEPTEMBER 2022 energy requirements:1 • ball mill: 38kWh/t • HPGR plus ball mill: 3034kWh/t • VRM: 2832kWh/t Grinding is a very energy intensive process that accounts for a significant amount of production costs7 This is why advances in classifier technology have been vital in increasing productionGRINDING Grinding options for slag and pozzolan PEC
.jpg)
Raymond Grinding Mill JXSC Machine
【Raymond Mill Plant】 The Raymond mill plant usually contains a cyclone collector, pipe fittings, dust collector, storage hopper, elevator, crusher, electric control cabinet, feeder, main plant, blower, separator, etc, Structural 2016年6月6日 Sufficient capacity (primarily a concern of large circuits where multiple pebble crushers are required to serve one grinding line); Design for bypassing crushers during maintenance, and; Evaluation of the where to SAG Mill Grinding Circuit Design 911Metallurgist2022年1月10日 Selective comminution and grinding mechanisms of spent carbon anode from aluminum electrolysis using ball and rod mills January 2022 Physicochemical Problems of Mineral Processing 58(3):Selective comminution and grinding mechanisms of 2020年6月3日 The design of such grinding mills is extremely critical, requiring sophisticated software tools, proprietary calculation worksheets, and experienced technical engineers and drafters This blog will review how the mill design process has changed over the last 30 years While most of the changes have been positive, new issues and problems have risen in the How grinding mill design changed over the last 30 years
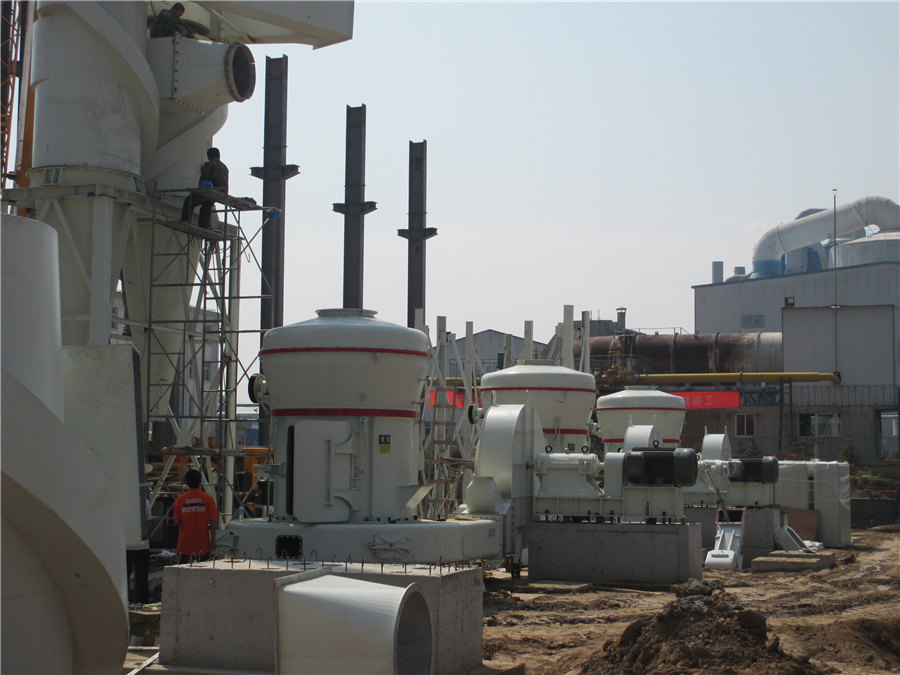
Operation Analysis of a SAG Mill under Different Conditions Based on
2020年10月9日 This method simulates the particles size, mill power, and qualified particles quality of crushed particle, which reveal the grinding strength and energy consumption of the SAG mill In this paper As a byproduct of production, aluminum plant waste residue is also increasing The total loss of aluminum content in the waste residue of aluminum plant in the production process is 112% HCMilling (Gulin Hong Cheng) can provide you with the best quality aluminum plant slag grinding mill machine and serviceWhat’s The Use Of Aluminum Plant Waste? The Price Of Aluminum Waste 2016年7月8日 The Work Index values listed in Table I and II apply directly to a wet grinding overflow type rod mill 75 feet in diameter in open circuit; and to a wet grinding overflow type ball mill 75 feet in diameter in closed circuit with a rake classifier at 250% circulating load, and with 80% or more of the feed passing 4 meshEquipment Sizing: Crusher or Grinding Mill 911Metallurgist2023年1月10日 Its grinding efficiency and grinding quality directly affect the cost and quality of slag grinding production As the core equipment in the production process of slag grinding, the LM slag vertical roller mill of SBM integrates fine crushing, grinding, drying, powder selection and transportation, ensuring the continuity and stability of slag Slag Vertical Roller Mill
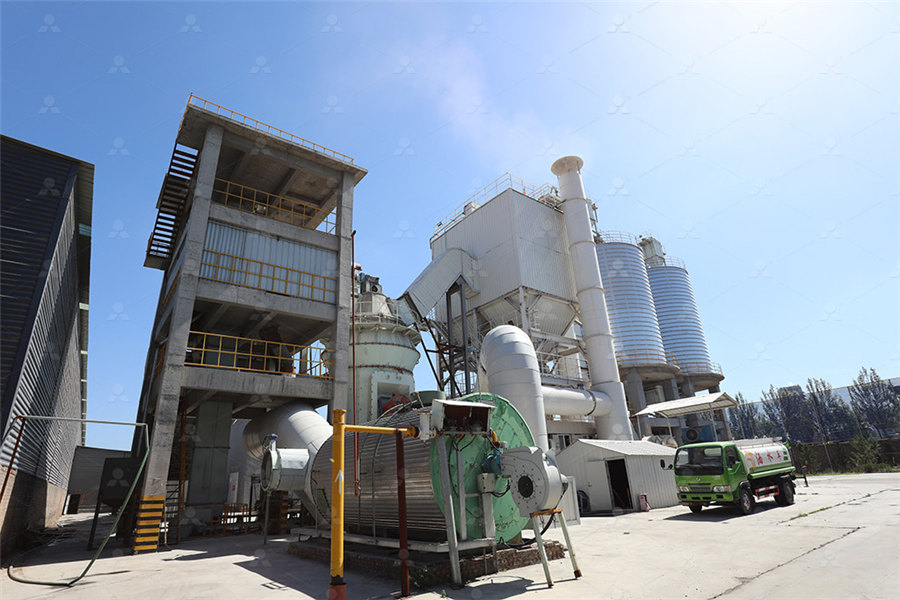
HIGmill high intensity grinding mill Metso
The grinding chamber is filled up to 70% with inert ceramic grinding media beads Rotors stir the charge and grinding takes place between beads by attrition The number of rotors (grinding stages) depends on the application and can be as high as A crushing plant delivered ore to a wet grinding mill for further size reduction The size of crushed ore (F 80) was 40 mm and the SG 28 t/m 3 The work index of the ore was determined as 122 kWh/t A wet ball mill 1 m × 1 m was chosen to grind the ore down to 200 micronsGrinding Mill an overview ScienceDirect Topics2023年12月27日 Ball mill; Steel slag belongs to a type of industrial waste If not properly utilized, it will inevitably cause environmental pollution The most suitable equipment for processing this mine is the ball mill Steel slag through grinding Steel Slag Processing Plant Equipment SelectionVideo credit: shsbjq / CC BYSA 40 Specifications Important specifications when selecting grinding mills and pulverizers include, The size of the mill can range from pilot/lab to production, eg, 35 to 1600 cu ft; Feed size, material, and Grinding Mills and Pulverizers Information
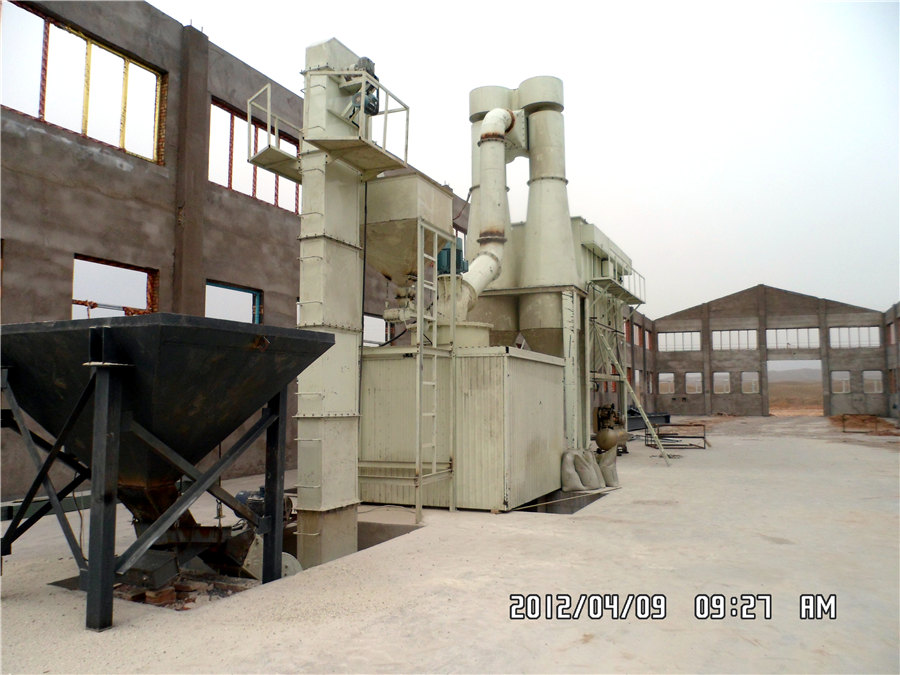
Ultimate Guide – Aluminum Fabrication, Grinding,
2021年6月16日 Aluminum and aluminum alloys are among the most used metals in fabrication,construction, and in the creation of good all around you It is such a useful and versatile metal, but there are some special 2022年10月10日 The comprehensive recovery and utilization of electrolytic aluminum spent carbon anode slag (Hereinafter simplified as “carbon anode slag”) are therefore necessary Flotation is a physical separation method used to separate particles by using the difference in surface property of particles ( Chen et al, 2022 ; Ni et al, 2022 )Recovery of carbon and cryolite from spent carbon anode slag of 2017年1月17日 Grinding mills are infamous for their extremely low energy efficiency It is generally accepted that the energy required to produce new mineral surfaces is less than 1% of the electricity consumed Breaking down energy consumption in industrial grinding millsCurrent systems for steel slag grinding that include ball mill systems, vertical mill systems and roller press systems on the market The ball mill system has high energy consumption, high noise and small singleunit capability, but the ball mill has low investment and it is widely used in small and mediumsized cement plants Before the steel slag grinding treatment in China, the ball How is the steel slag vertical mill grinding process?
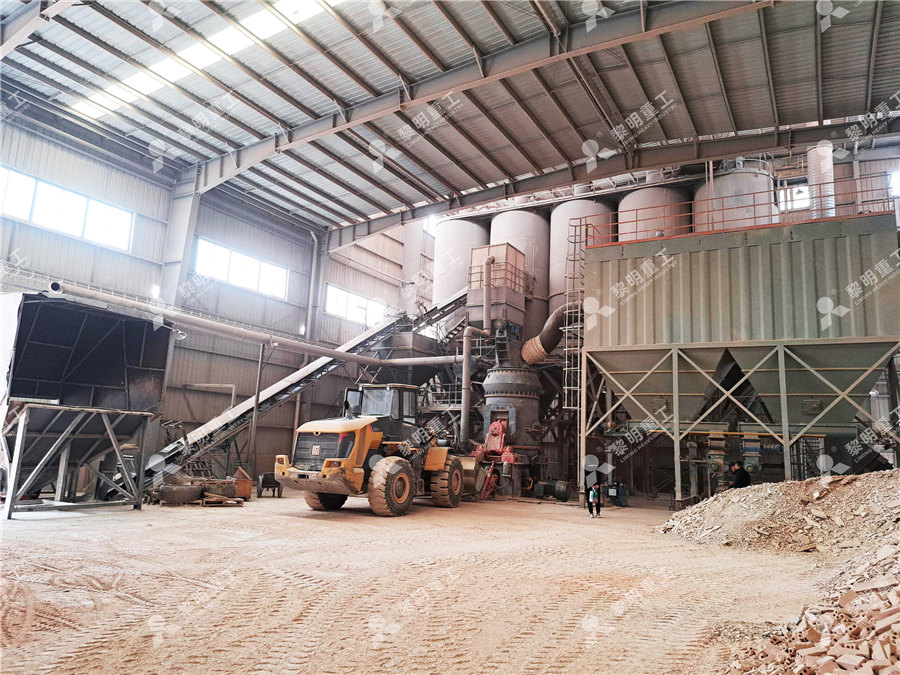
Options for Grinding Slag and Pozzolan for Use as Construction
Highpressure grinding rolls (HPGR) technology was first utilized in the grinding of clinker and raw material in the mid1980s and quickly proved be an economical choice in the comminution process 10 The HPGR compresses the material into a “cake” that includes both fines and coarse material, which later needs to be deagglomerated by a hammer mill, ball mill or a Vseparator 2022年2月26日 Blast furnace slag can be processed into the following materials by various processes In China, blast furnace slag is usually processed into water slag, slag gravel, expanded slag and slag beadsWater slag is the process of putting the hotmelt blast furnace slag into water for rapid cooling, which mainly includes slag pool water quenching or furnace front What is Blast Furnace Slag and How to Process It?2015年2月14日 CO 2 sequestration by mineral carbonation can permanently store CO 2 and mitigate climate change However, the cost and reaction rate of mineral carbonation must be balanced to be viable for industrial applications In this study, it was attempted to reduce the carbonation costs by using mine waste rock as a feed stock and to enhance the reaction rate Ultrafine grinding and mechanical activation of mine waste rock 2015年3月25日 1 The working principle of the hydraulic system vertical roller mill The hydraulic system ofvertical mill is an important system, the main function ofthe hydraulic system is to break the grinding roller, which is when the internal grinding cavity wear parts wear, can stop open on both sidesofthe grinding roller mill, to replace the inside parts or repairThis type vertical roller Hydraulic system vertical roller mill operation PDF SlideShare
.jpg)
LM Vertical Grinding Mill SBM Mill Crusher
2023年3月15日 SBM has launched the LM Vertical Grinding Mill which integrates five functions of crushing, grinding, powder selection, Vertical Slag Mill Series Models and parameters: LM130N: LM150N: LM170N: LM190N: If you have the equipment purchase demand for Slag Grinding Mill Machine, please contact mkt@hcmilling or call at +86773, HCM will tailor for you the most suitable grinding mill program based on your needs, more details News Application Of Slag Grinding MillOur bestinclass OK™ Mill is a globally successful vertical roller mill solution for grinding raw material, cement and slag Its cuttingedge design features consistently deliver the highest quality products with the greatest efficiency It OK™ Raw and Cement Mill1927 First Loesche coal mill delivered for the Klingenberg power station in Berlin 1953 500th coal mill plant sold worldwide 1961 Introduction of hydraulic spring assembly system 1965 Construction of first pressure mill (LM 122 D) 1980 Delivery of first modular coal mill (LM 263 D) 1985 Delivery of first selfinerting coal grinding plant (LM 212 D) for the steel industry (PCI LOESCHEMILLS
.jpg)
Blast Furnace Slag Ball Mill
According to the characteristics of blast furnace slag, the blast furnace slag grinding line is equipped with a magnetic separator for iron removal Blast furnace slag ball mill adopts a special liner, sieving device, motor, and discharging device In the production process, slag ball mill can not only grind the slag separately, but also mix This slag grinding mill integrates crushing, drying, grinding and conveying in one unit The mill has simple process, compact structure layout, it only takes 50% floor area is of ball mill and can be installed in outsideNews Carbide Slag Grinding Plant HLM Vertical MillThis study collected electrolytic aluminum waste cathodes, anodes, limestone and other materials After grinding the materials with an electric mill, 50 grams of electrolytic aluminum waste samples were sieved to 0075 mm The sample was then dried for 2 hours at a temperature of 110 °C in the dryer, then stored in aResearch on the Coprocessing of Mixed Electrolytic Aluminum Waste 2016年10月28日 The grinding efficiency of steel slag was obviously increased and the particle characteristics were improved after using grinding aids (GA), especially the particle proportions of 332 Mm were (PDF) Comparison of Grinding Characteristics of Converter Steel Slag
.jpg)
Steel Slag Ball Mill Quality Ball Bill Supplier Provide Best Price
The emergence of steel slag ball mill meets the needs of steel slag plant for processing steel slag grinding, and also enables the rational use of steel slag and avoids waste of resources AGICO GROUP pays attention to product quality, relies on scientific and technological innovation, and constantly optimizes the product structure2012年3月1日 Vertical roller mills are the mills traditionally used for processing granulated blastfurnace slag and for grinding composite cements From the energy aspect they are superior to grinding plant Operating experience with a vertical roller mill for grinding