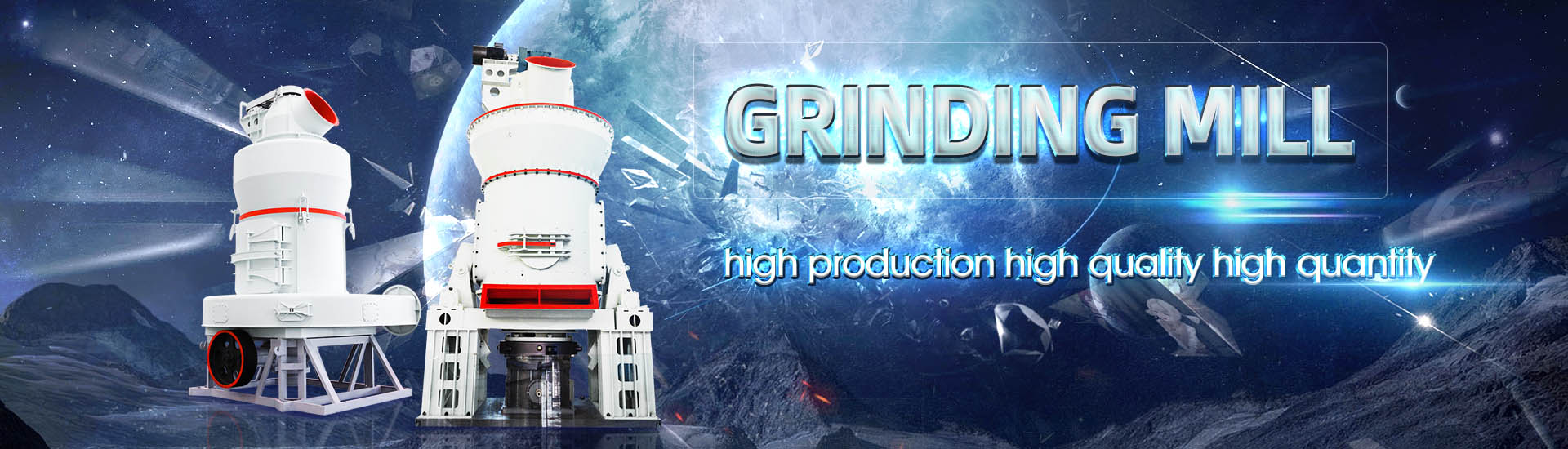
Working in a cement plant to learn the process flow
.jpg)
The Cement Plant Operations Handbook International Cement
The Cement Plant Operations Handbook is a concise, practical guide to cement manufacturing and is the standard reference used by plant operations personnel worldwide Providing a comprehensive guide to the entire cement production process from raw materialThis article will guide readers through each step in the manufacturing of cement, detailing critical processes such as blending, hydration, and the role of calcium carbonate, silica, alumina, and iron oxide in cement productionStepbyStep Guide to the Manufacturing of Cement2024年10月7日 The course’s first objective is to give an overview of the process chain within the cement industry All the main processes involved during cement production will be discussed, AN INTRODUCTION TO THE CEMENT MANUFACTURINGCement manufacturing: components of a cement plant This page and the linked pages below summarize the cement manufacturing process from the perspective of the individual components of a cement plant the kiln, the cement mill etc Cement manufacturing: components of a cement plant
.jpg)
Cement Manufacturing Process The Engineering
2018年8月28日 cement manufacturing process flow chart Cement is the basic ingredient of construction and the most widely used construction material It is a very critical ingredient, because only cement has the ability of enhancing Cement Manufacturing and Process Control 41 Cement Manufacturing: Basic Process and Operation To design the Refractory for the lining of different equipments in a cement plant, it is Chapter 4 Cement Manufacturing and Process ControlCement Plant: The Manufacturing Process worldcementassociation 1 Limestone (CaCO3) is taken from a quarry 2 4 3 The limestone is fed into a crusher and then stored until needed The Cement Plant: The Manufacturing Process 4 5 World Cement There are 4 stages of cement production that help maintain consistent raw material quality with minimal chemistry deviation, from quarry to silo to customer The Quarry: The cement A practical guide to improving cement manufacturing processes
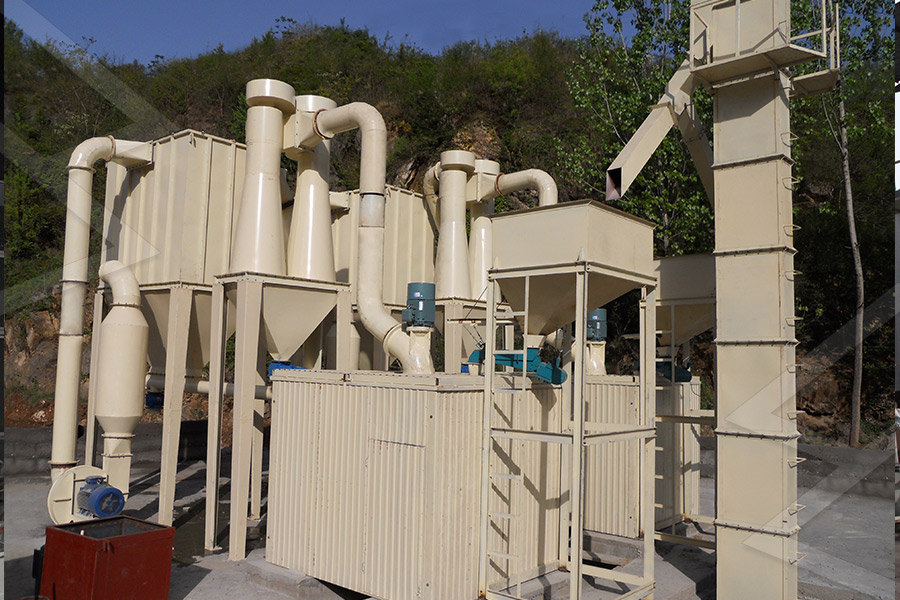
Typical cement manufacturing process flow
Download scientific diagram Typical cement manufacturing process flow diagram [4] from publication: Model Development for CO2 Capture in the Cement Industry Climate change has become a Cement Manufacturing Process by TIZITA MOGES , SELAMU ABULE DEREJE ENDALAMAW IF YOU NEED THIS GUIDE AND ALL OTHER USEFUL EXCEL SHEETS WHICH WILL MAKE YOU MASTER THE Cement Manufacturing Process INFINITY FOR 2024年10月7日 A 2week modular course is designed for engineers or technical degreed persons and newly hired in the cement industry It is also intended for engineers or technical degreed persons already working in the cement industry, whose work experience has not required indepth knowledge of the cement process, or those who want a comprehensive AN INTRODUCTION TO THE CEMENT MANUFACTURING15 Cement plant construction and valuation 244 1 New plant construction – 2 Project management – 3 Cement plant investment costs – 4 Project phases – 5 Plant valuation Section B – Process calculations and miscellaneous data B1 Power 262 1 Specific power consumption 2 Power conservation – 3 Threephase power – 4The Cement Plant Operations Handbook International Cement
.jpg)
THE PROCHECK GUIDE FOR CEMENT PACKING PLANTS Haver
2023年3月20日 The German machinery and plant manufacturer highlights more than 100 different optimization needs experienced by customers worldwide and shows the causes and solutions for each of them To do so, THE PROCHECK GUIDE draws on detailed plant analyses from the global market and decades of experience of HAVER BOECKER engineers and 2023年12月20日 The Cement Manufacturing Process flow chart sums up where in the process each type of technology is making a difference Cement operators also use these analysis systems to analyze and adjust the coal mix instream, which enables the plant to reduce energy consumption by using exactly the amount of coal fuel required to meet the specific heating The Cement Manufacturing Process Thermo Fisher Scientific2023年9月5日 Process control experts in the cement industry need to be wellversed with the process flow, the chemical reactions, and the physical transformations that occur in a cement plant They need to understand the interdependencies between the various process parameters and how they affect the quality of the cement and the efficiency of the production processMastering Process Control Instrumentation in Cement Plants: A APC such as ABB Ability™ Expert Optimizer is best conceptualized as the autopilot that drives a plant to its optimum state Using model predictive control (MPC), APC is able to reduce process variation and move the process closer to the constraints It is able to achieve this by first understanding process interactions and delays through data driven empirical models, such as Cement plant on autopilot: a practical guide to success
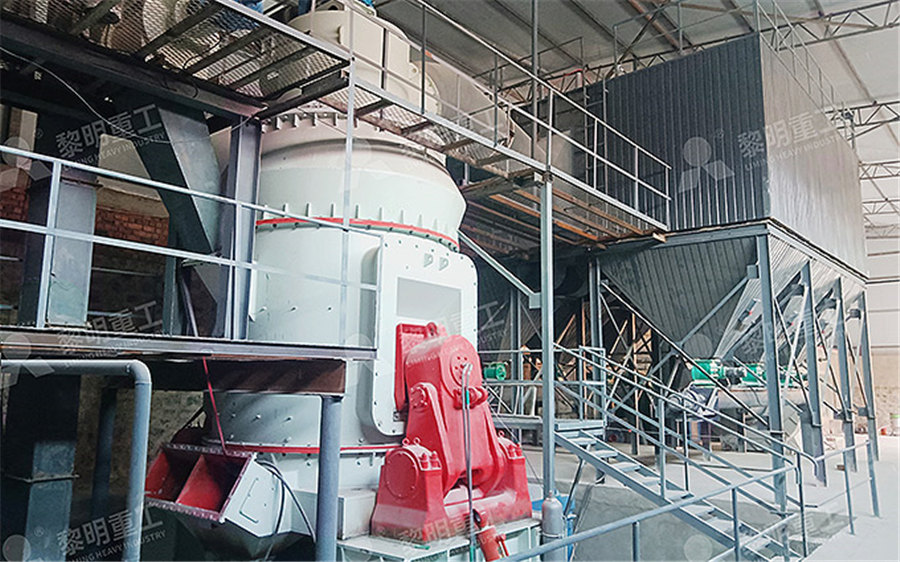
Cement Production Demystified: StepbyStep Process and
The use of fossil fuels such as coal, natural gas, and oil is common in cement production, both as a fuel for the kiln and as a source of heat for other parts of the process which leads to CO2 emitted by combustionHowever chemical reactions happening in the kiln (calcination) are also responsible for up to 60% of the total of emissions of the cement production process [PCA]2015年8月1日 This cement plant operates on a dry process line with a fi vestage suspension preheater and an inline precalciner The kiln is 4 m in diameter and 60 m in lengthAnalysis of material flow and consumption in cement production processThe whole process of cement manufacturing in Messebo Cement plant which consists of two separate Cement Production lines can be summarized into the following processes ;as can be seen in the process and Quality flow diagram below; 1 Quarrying and Crushing 2 Raw material Storage and Transportation 3 ProportioningCEMENT PRODUCTION AND QUALITY CONTROL A Cement manufacturing Process2024年9月5日 The Manufacturing Process of Cement Now, let’s explore the steps involved in the cement production process in more detail: 1 Mining and Crushing The process of making cement begins with mining, where raw A Comprehensive Guide to the Cement Manufacturing
.jpg)
ID Fans in the Cement Industry: All you need to know
The size and capacity of the ID fan will depend on the size and type of the cement plant, as well as the specific requirements of the process ID fans are essential for the proper functioning of a cement plant, as they play a critical role in the AGICO supplies cyclone preheaters for the new dry process of cement manufacturing Project Cases; Solutions Menu Toggle Factory Scales Menu Toggle Mini Cement Plant Hot Sale; Cement Plant 700 ~ 2000tpd; Cement Plant 2500 By using the computer numerical simulation technology to simulate the gassolid twophase flow field of the cement Cement Plant Cyclone Preheater2024年5月23日 The belt conveyor in cement plant operations is an essential component that significantly contributes to the efficiency, safety, and environmental sustainability of the cement manufacturing process By providing a seamless, reliable, and costeffective method for transporting materials, belt conveyors play a vital role in ensuring the smooth operation of Optimizing Material Flow with Belt Conveyor in Cement Plant2024年11月23日 Cement Extraction, Processing, Manufacturing: Raw materials employed in the manufacture of cement are extracted by quarrying in the case of hard rocks such as limestones, slates, and some shales, with the aid of blasting when necessary Some deposits are mined by underground methods Softer rocks such as chalk and clay can be dug directly by Cement Extraction, Processing, Manufacturing Britannica
.jpg)
Cement Manufacturing
Cement making process – Raw materials, clinker, cement • Cement Chemist’ Language2023年7月10日 Cement manufacturing is a significant industrial activity that plays a vital role in the construction sector However, the process of cement production is associated with various environmental Cement Manufacturing Process and Its Environmental ImpactThe comparison data between the wet process cement production line and the new dry process cement production line shows that with the same rotary kiln size (diameter), the production capacity of the cement kiln which adopts the predecomposition production process increases more than 200%, the output rises from 2777kg /m3 to 20082kg /m3, and the unit heat Cement Making Process Cement Production Process Cement PlantIn a recent trend, the majority of cement factories are using the dry process of cement manufacturing Read More: What Is Cement And History Of Cement In Construction Advantages The following are the major advantages of the Wet Process of Cement Manufacturing, Raw material can be mixed easily, so a better homogeneous material can be obtainedWet Process Of Cement Manufacturing With Flow Chart
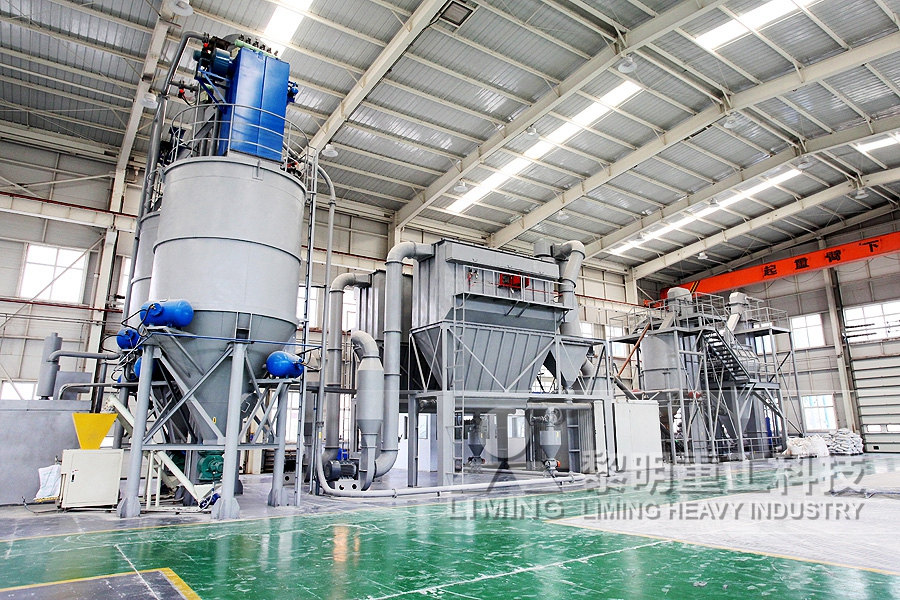
Cement Processing Equipment Rotary Feeders
The resulting raw mix is fed into a cement kiln which heats them to extremely high temperatures of about 1400 C to 1500 C Bulk material handling equipment, such as a rotary feeder in a cement plant, is used to transfer these raw materials 2024年8月5日 Concrete batching plant is an indispensable and important equipment in modern construction projects It transforms various raw materials into highquality concrete through a series of sophisticated processes In this article, we will provide you with a detailed process flow diagram of a concrete batching plant to help you better understand this complex and efficient Batching Plant Process Flow Chart ZOOMJOAPC such as ABB Ability™ Expert Optimizer is best conceptualized as the autopilot that drives a plant to its optimum state Using model predictive control (MPC), APC is able to reduce process variation and move the process closer to the constraints It is able to achieve this by first understanding process interactions and delays through data driven empirical models, such as Cement plant on autopilot: a practical guide to success2020年8月25日 Before you send inquiry Please provide us with project information as much as possible: For a complete project: the material availability, the required output capacity, the process technology, your budgetary and financing status, the estimated starting time, etc For singular machinery: the model, the capacity, your budgetary information, other requirements, etcCement Production Process Cement Manufacturing Process AGICO CEMENT

PERFORMING A CEMENT PLANT OPERATIONS AUDIT
The cement plants and process engineer (due to training and job title) is frequently asked to examine the “big picture” in a production/operations environment This can be a formal request for a diagnostic review or a vague request from top management to see what’s wrong or what kind of improvements can be done with production/operationsDownload scientific diagram Aspen Plus process simulator flow sheet for a typical cement manufacturing from publication: Energetic assessment of a precalcining rotary kiln in a cement plant Aspen Plus process simulator flow sheet for a typical cement Manufacture Process of Cement The manufacture procedures of Portland cement is described below Mixing of raw material; Burning; Grinding; The powdered limestone and water washed clay are sent to flow in the channels and transfer to grinding mills where they are completely mixed and the paste is formed, ie, known as slurryManufacture of Cement Materials and Manufacturing Process of 2024年11月4日 CEMENT TRAINING TECHNICAL SERVICES An emphasis on the understanding of the pyroprocess technology system: – Raw Mix Design, Burnability, and Clinker Quality – Optimization of Heat Consumption – Operation and Process Diagnostic Studies and Productivity Enhancement of the Clinker Production – Energy Conservation and Energy Audit PYROPROCESS TECHNOLOGY COURSE The Cement Institute
.jpg)
Cyclone Preheater Cement Plant
The cyclone preheater, also called cement preheater, suspension preheater, is a kind of preheater in cement plantAs the core equipment of dry method cement production line, cyclone preheater use suspension preheating to preheat and partly decompose the cement raw mix, shorten the length of the rotary kiln, fully mix raw mix and hot air in the kiln, increase heat exchange rate, In addition, the required precalciner volume of tertiary air flow precalciners is less than the volume required for total flow and hybrid precalciners Examples of the currently used total flow and tertiary air flow precalciners are, respectively, the F L Smidth Co’s InLine Calciner (Figure 326), and SeparateLine Calciner (Figure 327)Everything you need to know about Preheaters and Precalciners2020年1月3日 Before starting to build a cement plant, it is imperative to know what the cement making process involves The cement manufacturing process starts with mining of limestone followed by grinding it with other raw materials Key factors in setting up a cement plant Indian Underpinning the development of intelligent plants, these digital solutions support the cement industry achieve peak plant operating conditions Where once the industry may have relied on engineer’s experience and data from previous Building an intelligent cement plant Advanced
.jpg)
Simulation and Optimization of an Integrated Process
2021年3月9日 In this study the process flow diagram for the cement production was simulated using Aspen HYSYS 88 software to achieve high energy optimization and optimum cement flow rate by varying the flow rate of calcium In a rotary kiln system producing cement clinker, gas flows are countercurrent to material flows Gases enter the kiln as secondary air at about 600°C – 1100°C and rise abruptly to over 1750°C as heat from fuel combustion, and the exothermic heat of clinker formation are releasedEverything you need to know about Kiln System Operations in Cement It would be appropriate to devote a few paragraphs to the subject of laboratory automation/robotics, and the overall concept of that automation entity and its role in cement plant integration The quality aspects of analytics and how they provide data for cement plant management and control have been covered in another chapterEverything you need to know about Automation and Optimization 2019年6月27日 If you’re considering working in the process manufacturing industry, and you’d like to learn more about the basics of process control and how it’s used, you’re in the right place in this article, we’ll discuss everything that you need to know about process control – with a special emphasis on process control in manufacturing, and understanding different process Process Control – Everything You Need To Know Process
.jpg)
116 Portland Cement Manufacturing US EPA
1971年8月17日 116 Portland Cement Manufacturing 1161 Process Description17 Portland cement is a fine powder, gray or white in color, that consists of a mixture of hydraulic cement materials comprising primarily calcium silicates, aluminates and aluminoferrites More than 30 raw materials are known to be used in the manufacture of portland cement, and theseDownload scientific diagram Cement Manufacturing Process Flowsheet (Flow Chart) from publication: Cement Manufacturing – Process Modeling and TechnoEconomic Assessment (TEA) using SuperPro Cement Manufacturing Process Flowsheet (Flow Chart)The cement production process 1 The Quarry: The cement production process begins with the extraction of limestone and clay from the quarry 2 Crusher and PreBlending: The material is then crushed to reduce particle sizes and blended to reduce variability in composition 3 Raw Mill and Kiln: Raw materials and additives areA practical guide to improving cement manufacturing processes 2021年7月1日 In this paper, we analyze numerically the characteristics of turbulent gasparticle flow, heat transfer, and coal combustion process in a fluidizedbed calciner for a cement manufacturing process(PDF) DEVELOPMENT OF SUITABLE MACHINE LEARNING MODEL FOR A CEMENT PLANT