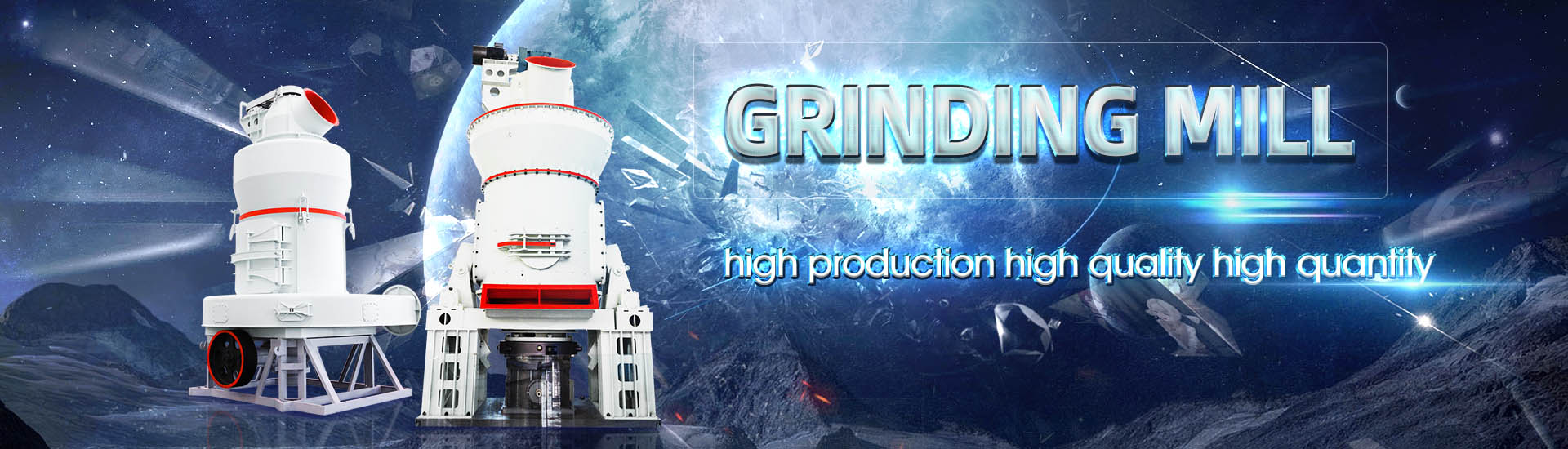
60 spiral pressurized ore grinding mill
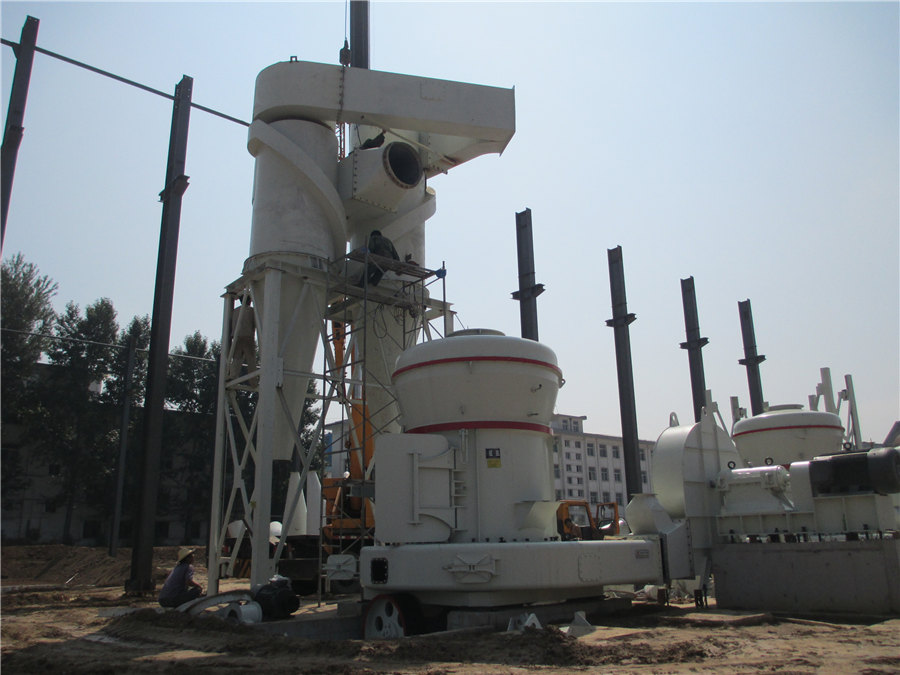
Grinding mills for mining and minerals processing Metso
Browse Metso's wide offering of reliable grinding mills: AG mills, SAG mills, ball and pebble mills, and stirred mills to fit your needs Our pioneering innovations in horizontal grinding mills For over 60 years, CITIC HIC has focused on providing global customers with reliable, energysaving and highefficiency mineral grinding mills, such as AG mills, SAG mills and overflow Grinding Mills Mineral Processing Equipment CITIC HICCustomized grinding mill parts including heads, shells, trunnions and liners, main bearings, gears and pinions, and more! Metallic, PolyMet™, Megaliner™, Rubber and Orebed™ mill liners for Grinding MetsoRotor mills are used for highspeed size reduction of soft to mediumhard as well as temperaturesensitive or fibrous materials The powerful Ultra Centrifugal Mill ZM 300 provides maximum Mill, Grinding mill All industrial manufacturers
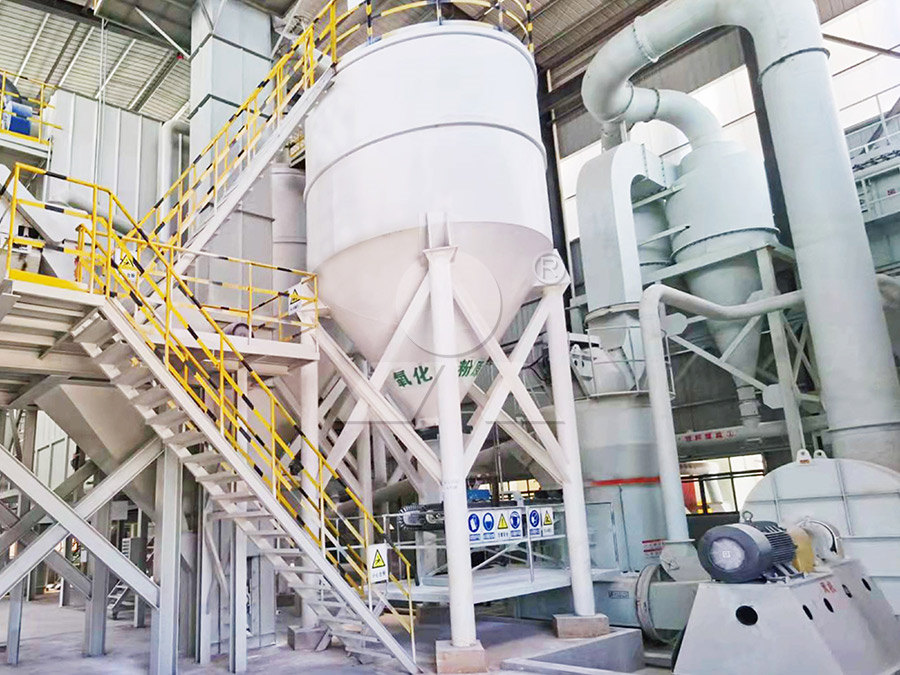
HIGmill high intensity grinding mill Metso
The Metso HIGmill™ is an advanced, energyefficient fine and ultrafine grinding solution that utilizes proven technology With the tall, narrow, vertical body arrangement, grinding media is VIBRADRUM® Grinding Mills excel over conventional ball, stirred media, or vertical roller mills in both grinding and energy efficiency The features listed below highlight why our mills are so VIBRADRUM® Grinding Mill Solutions General KinematicsSpiral classifier is widely used in beneficiation plant to match with ball mill to form a closed circuit circulation path to distribute ore sand Filter the material powder milled in the mill, and then Spiral Classifier JXSC MachinerySavona Equipment is your source for mill components and accessories for large primary ore process concentrating through secondary and tertiary fine material as well as complete ore processing facilities All our reconditioned mill components will be supplied ready for service We can supply SAG mill parts and Ball mill wearparts including ball mill liners and shell liners Our Grinding Mill Parts for Sale Ball Mill Parts SAG Mill Parts
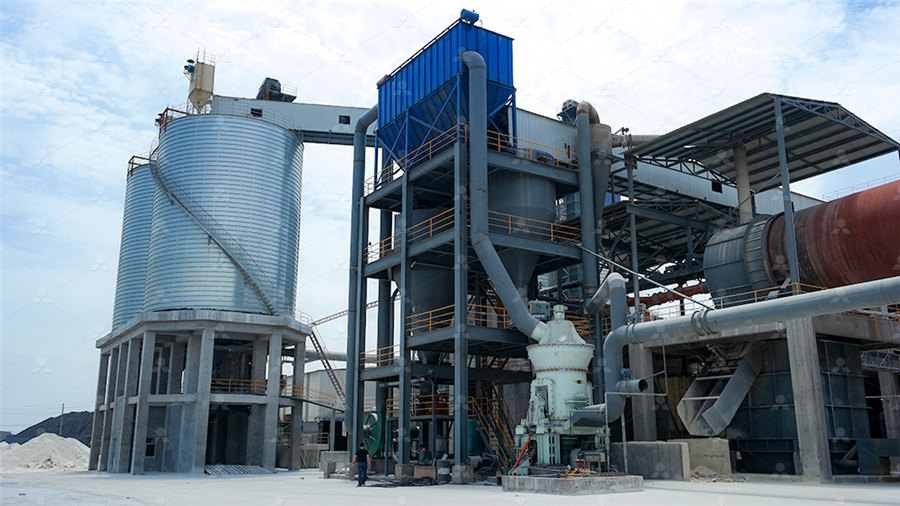
Analysis of grinding in a spiral jet mill Part 1: Batch grinding
2020年11月1日 Download Citation Analysis of grinding in a spiral jet mill Part 1: Batch grinding Jet milling is widely used in several industrial applications to produce fine particles with a narrow size 2020年8月12日 As one of the three major forces of coal mills, the grinding force exerts a significant impact on the working process of coal mills and parameters like mill current and outlet temperatureAn investigation of performance characteristics and Grinding Mills: Ball Mill Rod Mill Design PartsCommon types of grinding mills include Ball Mills and Rod Mills This includes all rotating mills with heavy grinding media loads This article focuses on ball and rod mills excluding SAG and AG mills Although their concepts are very similar, they are not discussed herePhotographs of a glass ended laboratory ball mill show Grinding Mills 911MetallurgistThis mill accepts grinding set weights of up to 30 kg, the largest grinding jar has a volume of 2,000 ml chemical industry, etc, it has two ore grinding Compare this product Remove from comparison tool ball grinding mill horizontal for ore ball grinding mill Final grain size: 74 µm Ore mill, Ore grinding mill All industrial manufacturers
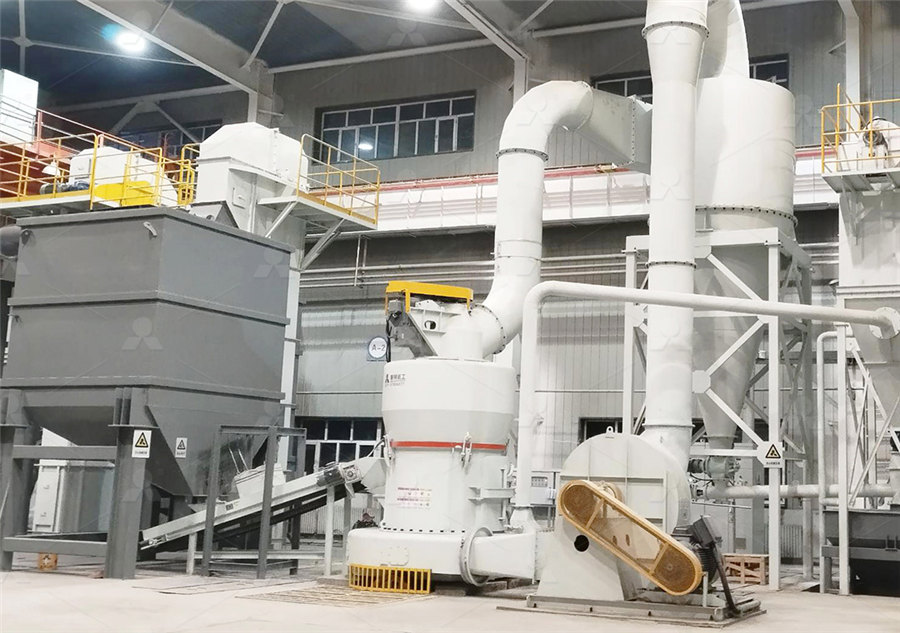
Ball Mill Is Indispensable For Lithium Ore Processing
2024年11月21日 The grinding and grading stage of lithium ore is to ensure that lithium minerals are fully dissociated from gangue mineral monomers Therefore, lithium ore extraction is inseparable from ore grinding, and the common equipment for lithium ore grinding is ball mill Onestage closedcircuit grinding and grading process can be adopted, and the onestage Each grinding mill is unique, so why treat the mill linings differently? We work with you to engineer a mill lining that meets your operational requirements and goals Choose from three material options: Rubber Ideal for combating wear and tear against abrasion Rubber mill linings are a less costly and readily available solutionSuperior wear protection – FLS mill liners2017年2月20日 All Grinding Mill Ball Mill Manufacturers understand the object of the grinding process is a mechanical reduction in size When choosing primary autogenous grinding, run of mine ore up to 200300 mm in size is fed to the In this case the thickness used was 60 mm for small mill sizes up to and including 2940 and 80 mm for Grinding Mill Design Ball Mill Manufacturer 911Metallurgist2016年6月1日 The Ball Mill Discharge Spiral Screen is designed to make a sized product, particularly for “SubA” Unit Flotation Cells and concentrating tables It is also 911 Metallurgist is a trusted resource for practical insights, solutions, and support in mineral processing engineering, helping industry professionals succeed with proven expertise Ball Mill Discharge Spiral and Ball Mill Discharge Spiral and Trommel Screen 911Metallurgist
.jpg)
The six main steps of iron ore processing Multotec
The primary grinding mill grinds the material before it undergoes spiral gravity separation Efficient grinding means that there will be minimal recirculation material from a cyclone cluster or screening after milling, When the material exits the mill, the iron ore is classified using cyclones or vibrating screens that separate fine and fragmentation in the mill [4] Grinding conditions in the spiral jet mill have been extensively studied, with the consensus agreeing that particle feed rate and grinding pressure are the two most influential parameters [1,5–9] In general, increasing the grinding pressure results in Analysis of holdup and grinding pressure in a spiral jet mill The Autogenous Mill, also known as AG Mill, is a type of grinding mill used in the mining industry This machine uses ore and rock itself as grinding media to perform its job Unlike other types of mills that use steel balls or rods for Understanding the SAG Mill in Copper Ore Mining 2015年4月9日 Grinding Mills and Their Types satyendra; April 9, 2015; 12 Comments ; autogenous grinding, ball mill, grinding mills, hammer mill, rod mill, roller mill, SAG,; Grinding Mills and Their Types In various fields of the Grinding Mills and Their Types – IspatGuru
.jpg)
Fine Grinding as Enabling Technology – The IsaMill
Table 1: Power Intensity of Different Grinding Devices Ball Mill is a 56m D x 64m L @ 26MW Tower Mill is a 25m D x 25m L @ 520KW Table 2: Mill Comparison of Media Size, Power Intensity, number of grinding media The ability to use smaller media is probably the dominant impact on grinding efficiency It2024年1月1日 The vertical stirred mill is vertically installed, and gravity works in the grinding process With the advantages of high grinding efficiency and less area occupation, it is widely used in the regrinding, fine grinding, and ultrafine grinding process of such metal mines as iron ore, copper ore, leadzinc, and such nonmetallic mineral industries as calcium carbonate, Stirred Mill SpringerLink2023年10月17日 3 Ultrafine Powder Grinding Mill Ultrafine powder mill (threering / fourring mediumspeed micropowder mill) feed particle size ≤25 mm, production capacity 0545 t/h, production fineness 1503500 mesh,it is a highefficiency and lowconsumption ultrafine powder processing equipment that successfully replaces the traditional jet mill and complex process How to choose a suitable ore powder grinding mill?2024年8月15日 Grinding equipment: Applicable materials: Advantages: Energy Consumption: Ball mill: Various ores, from hard to soft Widely used for fine grinding; can operate in dry or wet modes based on process requirements High Rod mill: Largersized ores Ideal for coarse ore grinding, preventing overgrinding Low Autogenous millMineral Processing Plants: What You Need to Know
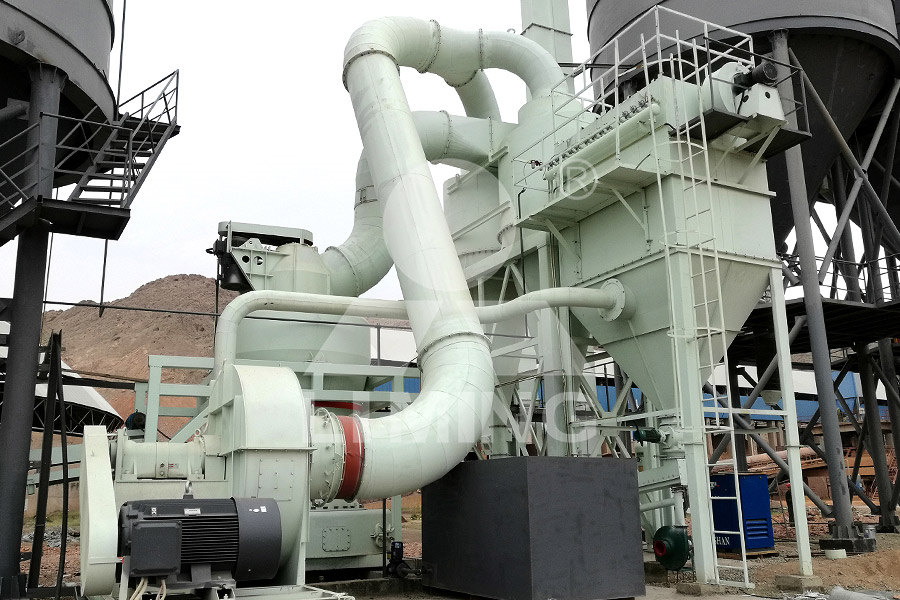
SAG Mill Grinding Circuit Design 911Metallurgist
2016年6月6日 Mill operating conditions including mill speed (for circuits with variablespeed drives), density, and total mill load; The effect of feed hardness is the most significant driver for AG/SAG performance: with variations in ore hardness come variations in circuit throughput2017年1月6日 Grinding coarse ore in a ballmill is done by steel balls of three sizes (5, 4, and 3 inches); fine ore is ground in a tubemill by 2 and 1½inch balls or by flint pebbles or by hard, rounded mine rock such as quartzite Spiral Classifiers The Akins, Hardinge, Basic Ball Mill Grinding Circuit 911Metallurgist2024年4月26日 The choice of grinding mill depends on factors such as the desired product size, capacity requirements, and energy consumption b Autogenous and SemiAutogenous Mills: In some cases, autogenous (AG) and semiautogenous (SAG) mills are used for grinding These mills utilize the ore itself as the grinding media, reducing the need for additional Iron Ore Processing: From Extraction to ManufacturingIn the operation period of the vertical spiral stirring mill of the embodiment, ore grinding media are required to be filled into the cylinder, the media are generally steel balls or ceramic balls, the diameter of the media is 1025 mm, and the filling amount of the media is about 3050% of the effective volume in the cylinder; a highpressure air pulsation device is uniformly arranged on CNU Verticaltype spiral stirring mill Google Patents
.jpg)
Energy conservation and consumption reduction in grinding
2023年11月1日 Grinding operation is the last preparation stage before beneficiation In this stage, the material undergoes the combined action of impact and grinding, so that the ore particle size is diminished and the qualified materials is provided for succeeding beneficiation operations [1, 2]Generally, the quality of the grinding product is also an important factor to determine the 2023年5月18日 The vertical stirred mill is vertically installed, and gravity works in the grinding process With the advantages of high grinding efficiency and less area occupation, it is widely used in the regrinding, fine grinding, and ultrafine grinding process of such metal mines as iron ore, copper ore, leadzinc, and such nonmetallic mineral industries as calcium carbonate, Stirred Mill SpringerLinkOre grinding machines can be divided into many types according to different classification methods, each with significant characteristics The following is a general introduction to the types of oregrinding machines and their characteristics According to the different media of the mill, the grinding machines are divided into: If the medium is steel balls, it is called a ball mill;Ore Grinding Machines: Ball Mill, Rod Mil Grinding MediaRequest PDF On Apr 1, 2013, Alex Jankovic and others published Closed circuit ball mill – Basics revisited Find, read and cite all the research you need on ResearchGateClosed circuit ball mill – Basics revisited Request PDF
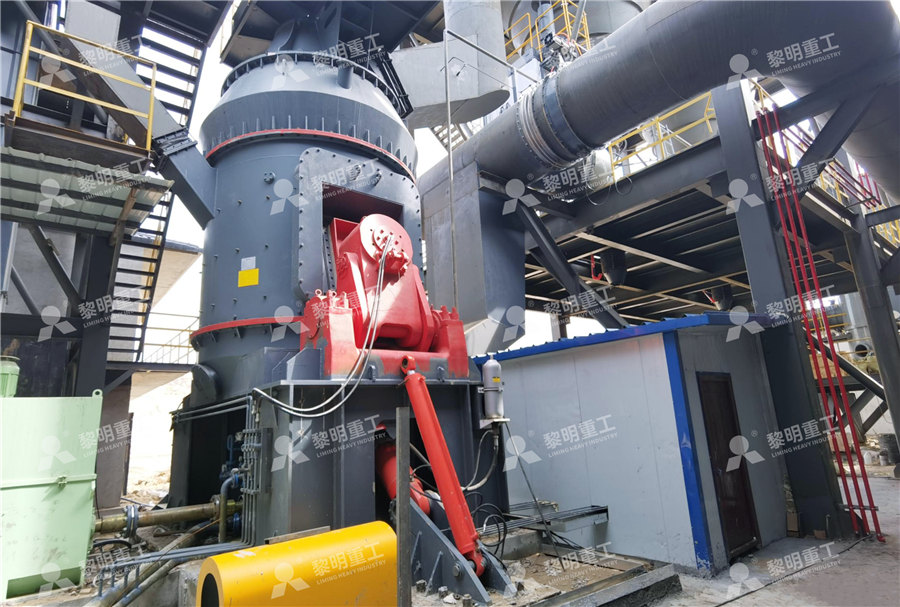
Grinding in Ball Mills: Modeling and Process Control
2012年6月1日 As the cylinder starts to rotate, the grinding balls inside the cylinder crush and grind the feed material, generating mechanical energy that aids in breaking bonds, activating the catalyst, and 2023年7月10日 The present literature review explores the energyefficient ultrafine grinding of particles using stirred mills The review provides an overview of the different techniques for size reduction and (PDF) EnergyEfficient Advanced Ultrafine Grinding of Particles At Bellian Mining Machinery, we specialize in crafting advanced solutions for ore crushing, sand making, and grinding processes Whether it's efficiently crushing ores, creating highquality sand for construction, or precision grinding for various applications, Choose Bellian Mining Machinery for all your mining and processing needs, where technology and excellence converge Ore Crushing, Sand Making, Grinding Machinery Bellian Mining 200 mm Diameter X 240 mm Long Grinding Mill which can be used as Ball Mill or Rod Mill; Mill Motor Power of 103kW; Feed Ore is precrushed to 15 mm; This ultra small scale grinding mill can function as a primary ball mill or rod mill for or mini flotation plant or as a regrind mill if your pilot plant is built using our larger primary mill SMALL GRINDING / REGRINDING MILL 3 TO 10 KILO/HR
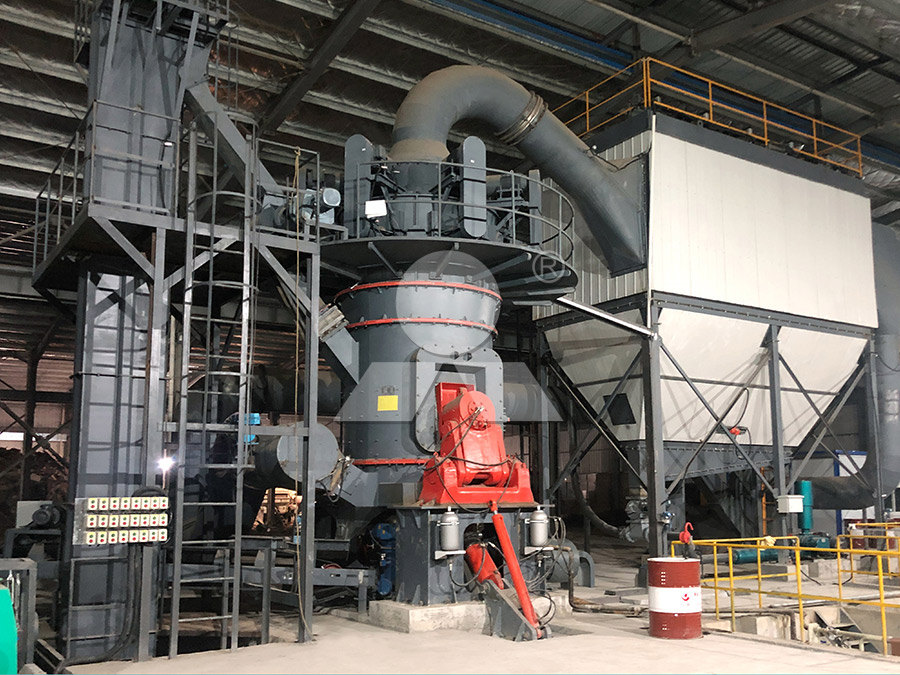
Mill lining solutions for horizontal Mill
influence on grinding efficiency It transforms the mill rotation into charge motion, and both profile and spacing must be selected to suit each specific mill When designing a shell lining, the type of ore, mill size and speed, maintenance schedules, safety, impact levels and efficient use of materials should all be considered Discharge systems2019年2月5日 High Pressure Grinding Roll ("HPGR") technology is applied is a broadening range of applications In the last few years, increasing numbers of HPGR units have been or are being installed in High Pressure Grinding Rolls for Bauxite Size The capacity, or throughput, of a ball mill is directly linked to particle size of the ball mill discharge For example, it takes approximately 3 times as long to achieve 200 mesh grind as it does to achieve 65 mesh grind Establishing a Ball Mills Mt Baker Mining and Metals2013年4月16日 ABSTRACT In this study, ultrafine grinding of a refractory silver ore tailings was studied A laboratory scale pintype vertical stirred mill and ceramic beads were employed for the grinding testsInvestigation of some parameters affecting the Ultrafine grinding
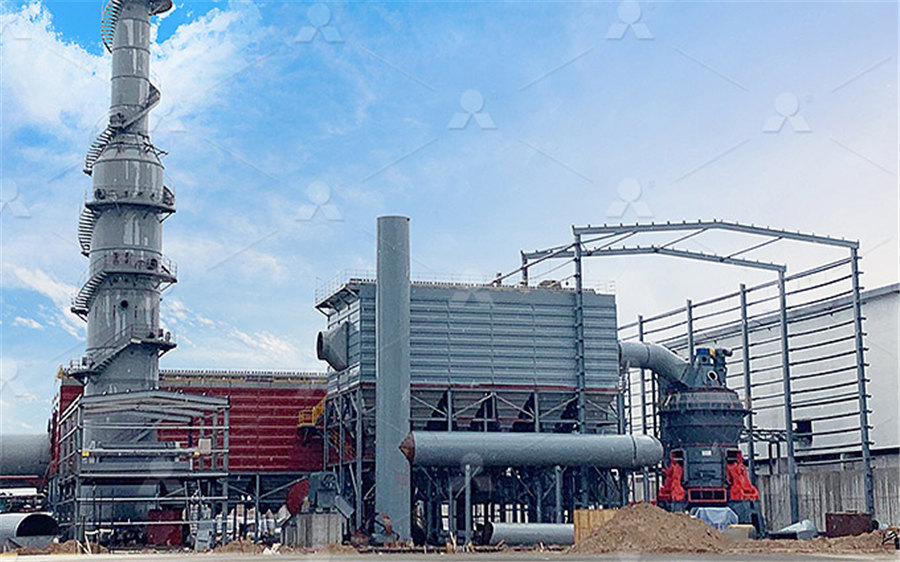
Crushing and Grinding Wet Sticky Ore 911Metallurgist
2016年5月10日 In the handling of wet, sticky ores such as encountered in tropical areas having distinct dry and rainy seasons, the crushing plant is a section of the mill which must be planned very carefully Unless this is done, crushing becomes a constant source of trouble resulting in lost production and high milling cost In some areas rainfall is high for prolonged periodsSBM micro powder grinding mill is a highly efficient industrial grinding mill, its finished products: 3253000 mesh; quantitative belt scale→elevator→spiral conveyor→deironing separator→micro powder grinding mill→pulse dust collector→fan→air door Micro Powder Grinding Mill Use in Ore FieldMicro Powder Grinding Mill1 Introduction 11 Presentation The reduction of energy consumption in a grinding circuit is not restricted just to the changes made in mill, like the optimization of the ball load, for PARATIVE STUDY BETWEEN THE USE OF CYCLONE AND SPIRAL Wet Pan Mill also known as amalgamation grinding mill, gold grinder mill, which is a versatile ore grinding pan mill for wet materials It’s the best replacement for a mediumsmall capacity ball mill, owing to the excellent performance for wet crushing, small investment, and high output, widely used for separating gold, iron, molybdenum, lead, zinc, antimony, and so onWet Pan Mill JXSC Mineral
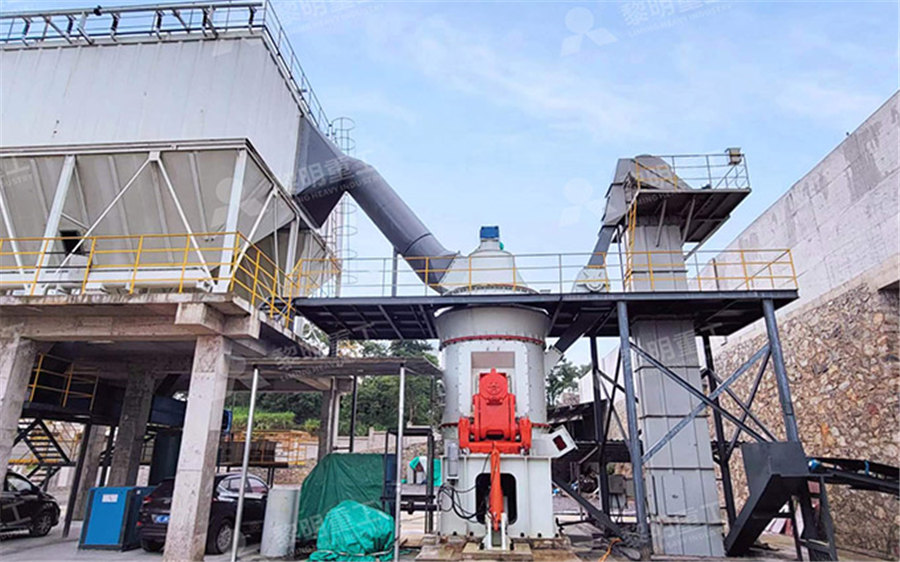
Ore Grinding SpringerLink
2023年7月20日 Therefore, the rod mill is mostly used for coarse grinding of the previous period of ball mill, or grinding of brittle materials and materials against overcrushing, such as tungsten and tin ore before gravity separation; and (3) autogenous mill – it refers to the materials which themselves are collided and ground mutually to be crushed when the grinding mill rotates, and It is well known in the industry that good classification system performance is vital to efficient ball mill circuit performance But what is meant by good classification system performance, and how is it achieved? Unfortunately, the perceived complexity of classification systems, and the daytoday time demands placed on the practicing metallurgist, all too often put the lowhanging fruit of A guide to maximising ball mill circuit classification systemPlant feed Oxidised ore Sulphide ore Complex ore Wi (kWh/ton) 101 627 1253 1384 Despite the major variations among the work indices of the different ore types, the plant feed prepared by blending the three ores gives a mean value Breakage functions of the ore were also measured to expose the breakage behaviour of the ores TheseMODELLING AND SIMULATION OF GRINDING CIRCUIT IN