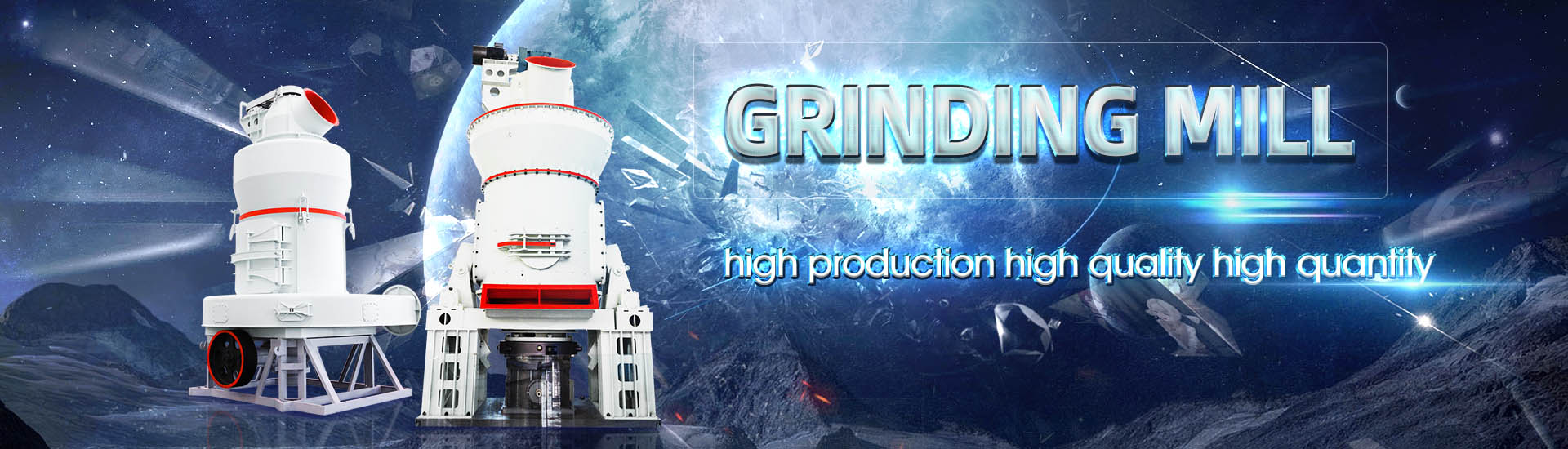
Selection of large gear module for roller mill
.jpg)
DRIVE SELECTION FOR LARGE LOESCHE VERTICAL ROLLER MILLS
The drive of a vertical roller mill – essentially the mill gearbox – has to fulfill two tasks: The first is to reduce the speed of the electric motor to the selected mill speed and to transmit the torque 2017年1月1日 Keyßner, M and Fahrland, T: Drive selection for large Loesche vertical roller mills Cement International, 2/2016, pp 4148 Operational experience from India's first MVR vertical(PDF) Drives for large vertical roller mills ResearchGateprocedures of universal joints for mill gear spindles are discussed in this article, including a review of operating characteristics, bearing life, length compensating features, roll end support design Design and Selection of Universal Joints for Rolling MillsGear technology developed in synchrony with mill power Starting with the first generation drives featuring bevel parallel shaft gears, the torque passing 1 Mio Nm required torque splitDevelopment of the 4th Generation Vertical Roller Mill Drives
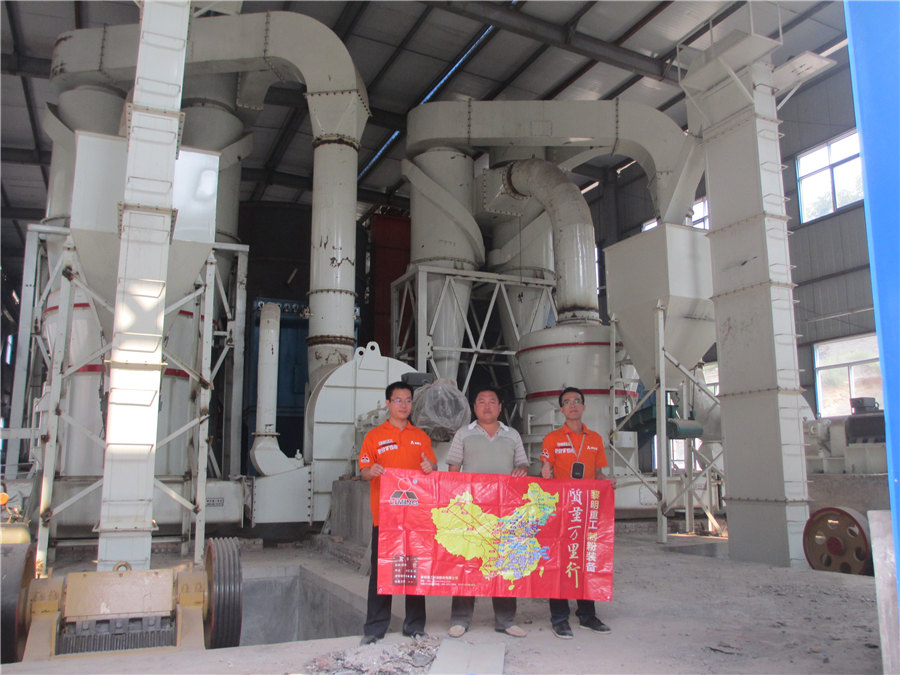
Roll Drive Design Considerations for Steel Mill Rolling Operations
According to the American Gear Manufactures Association (AGMA) selection criteria, reducers can be selected by Service Factor or Load Classification Both are a means of classifying gear ratio of the bevel stage and a torque split in the planetary stage The largest 3stage WPV gearbox by FLSmidth Maag Gear is now available up to 9000 kW, with a tested version forDrives for large vertical roller mills ResearchGateThe first gearbox generation for vertical roller mills consisted of two helical gear stages combined with a bevel stage as shown in Fig 3 This concept was used from 50 kW up to 3900 kW A New Gearbox Generation for Vertical Roller Mills Artec MachineDrives for rolling mills Rolling mill applications demand high precision and high overloadability They are characterized by quickly changing loads, rapid alternation between driving and ABB drives in metals
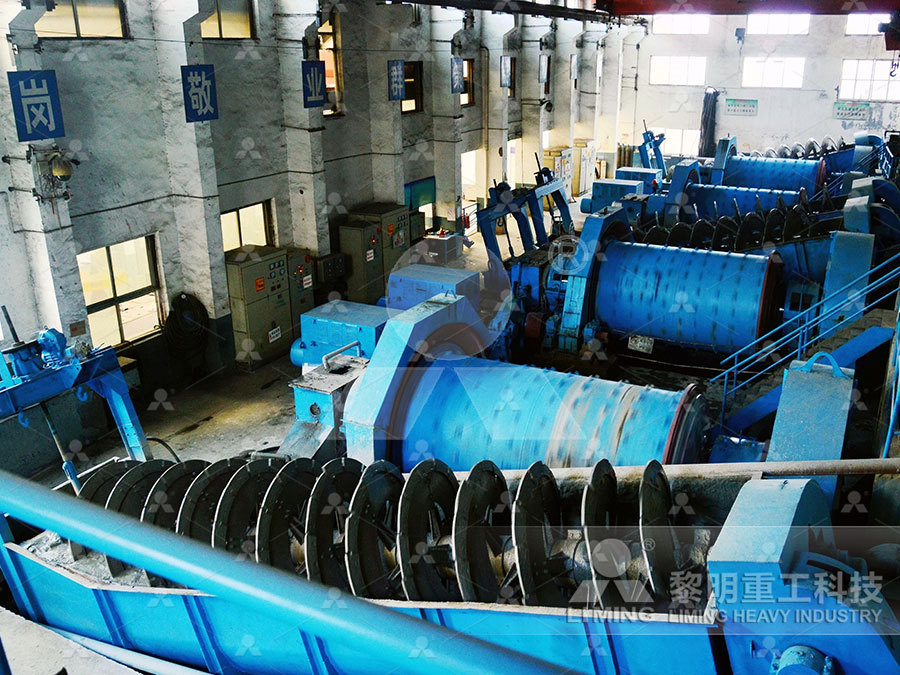
Large AC Adjustable Speed Motors for Metals Rolling Mills
Proven AC drive solution for each type of rolling mill application, ranging from large torque, slowspeed roughing mills to the highspeed, wide tension range aluminum foil mills Synchronous NGC’s MLXSeries for Vertical Roller Mills (VRM) feature a unique combination of strength, reliability and durability not available in standard mill drives Designed to accommodate all Gearboxes for Vertical Roller MillsPDF On May 1, 2017, Caroline Woywadt published Grinding process optimization — Featuring case studies and operating results of the modular vertical roller mill Find, read and cite all the (PDF) Grinding process optimization — Featuring case As the acknowledged leader in fluid bed roller mill design, Williams Roller Mills provide years of reliable, consistent, and efficient operation However, what truly sets our equipment apart is their ease of use and maintenance Learn more Industrial Roller Mills Williams Crusher
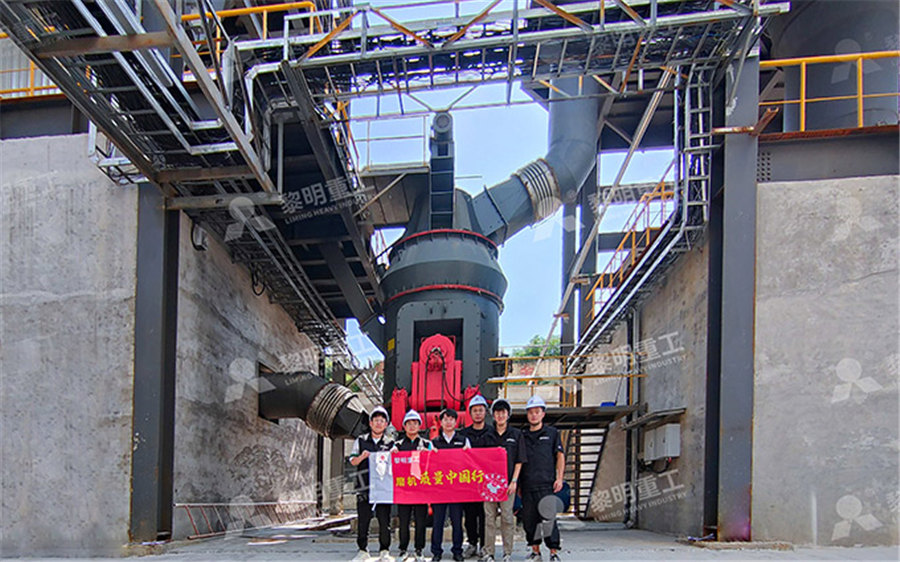
Redundancy and interchangeability – large vertical roller mills
Equipping the mill with six rollers instead of increasing the size of the rollers of a Loesche mill with four or three rollers made it possible to use the existing roller modules from mills that have already been operating successfully for many years The roller module ( of a roller mill Stages in the assembly of a roller mill in Australia View into the interior of the mill during assembly Grinding table gear unit Coarse feed valve elevator to the grinding table or is conveyed to the highefficiency separator The discharge ring is of modular design and made of highly wearresistant elePolysius Roller Mills For grindingWith the large‐scale development of the ball mill, the direct‐drive gearless ball mill has emerged, eliminating the limitation of the transmission torque of large gear However, it is difficultto process, transport, install and maintain the gearless ball mill because of its vast volume, and the coils cannot be decoupled freelyElectromagnetic design and thermal analysis of module combined Fig 1 Flowsheet of modular vertical roller mill 5000 R4 The required throughput rates were achieved in short time All fineness figures met the target values as well without anyGrinding Process Optimization Featuring Case Studies and
.jpg)
big Module Girth Gears and spur gear for Ball Mill and rotary kiln
Rotating gear ring for ball mill offered find extensive application in different industry sectors including in sponge iron plants, steel cement industry, mining industry, wind mills as well as in other industry sectorsThese are made available in module range of 10 Module to 70 Module and in minimum diameters of 100 mm to 15000 mm Further, these comprise maximum weight of 2023年7月4日 Roller mill is a type of grinding equipment for crushing materials by which is subjected to pressure and shear force It has the advantages of a large processing capacity, easy (a fixed roller and a movable roller), the driving system (main motor, reducer, belt pulley, and gear shaft), the hydraulic system, the Roller Mill SpringerLinkThe 'module' system is widely used all over the world to conveniently designate sizes of gear teeth Here, we will explain the definition of the module TEL : +81 48 254 1744Gear Module KHK Gear Manufacturer2010年5月20日 The failed module can then be repaired on a bench, or sent back to the manufacturer for repair Most manufacturers have a fixed exchange price, where they send out a complete module, while the customer sends the damaged module back The manufacturer then repairs and tests the module and keeps it for use by the next customerDrive selection for rolling mills Russula
.jpg)
Gear Cutting Tools and Gear Hobs LMT Tools
gear finishing LMT Fette is the technology leader in gear hobbing We offer the most innovative tool program for gear milling Explore the highlights of our product portfolios: from small modulated automotive milling cutters all the way to large Galbiati Group has recently manufactured a large gear wheel with relative carburized pinion, intended to be positioned inside a twin drive gearbox, for R1F1 rolling mill control Initially, on the gear wheel, welding operations (WPS) were Large gear wheel and pinion for rolling mill plantQianHong Wang et al / Physics Procedia 33 ( 2012 ) 437 – 443 439 temperature, pressure, and flow rate, things as a simulation signal and equipment as state of switchDesign and Realization Of Roller Mill Control SystemLarge Girth Gear for Ball Mill and Rotary Kiln Production, Module Range: 10 Module to 70 Module Diameter : Min 800mm to16000 mm Weight : Max 120 MT single piece High Quality Max Diameter 2m Forged Roller Shaft US$1,0000020,00000 / Piece Small Spare Parts Large Girth Gear for Ball Mill and Rotary Kiln Production
.jpg)
Grain Roller Mills Automatic Equipment
We want you to get more gain from your grain with our wide selection of electric and PTO roller mill equipment CSU Mills Low Profile Electric Mills Choose our economical and easytooperate CSU mills and lowprofile mills Automatic Manufacturing’s largecapacity roller mills are the perfect fit for the jobtion of the mill Unfortunately, to get what is required, this information needs translation into something that the gear designer can input into the rating calculations The calculation of actual contact stress s c does not have an input for tons/ hour of mineral produced A theoretical relation of mill diameter to power is ~ mill diameter25TECHNICAL How to Spec a Mill Gear Power Transmission%PDF16 %âãÏÓ 1 0 obj >stream ð+¹ = ?¼rž8Žé(¦ éÜ2ƒ÷ˆÌ?Š[+w÷ þ ÍAëGÁeµÈÚãl 0uÞ¾–go’ZD ïf( q ^×ד !F"ⵎð L xw\/ 3ê˜öz Õ>5 ™ Q5™ k'Drpôn™ËÛFç\ƒÑGŠ9FÛ?Y8>= Ïí} Ãä’®Ô(¨Wyã6 J ²éÇ Ã벑wÍn e†N®bš! ÛõÂX±²Éµl õΚâ^ÇâŽ?(mgC‡¾ ß\ÛıH› n ûÚøÊ O;YG+‘nQ K³(ææR‘Þ Rò ÿëZ(Þ(ä 5 Guidelines for Gear Unit Selectionkiln support roller; kiln shell; tip plate and sealing parts; and strong impact resistance For the large girth gear of a typical ball mill, materials like ZG270500, ZG310570 made from materials like ZG45, ZG40CrMO, which require tempering treatment to control their hardness above that of the large girth gear Selection of Small Girth Knowledge about Ball Mill Girth Gear You Need to Know
.jpg)
Drives for large vertical roller mills ResearchGate
Drives for large vertical roller mills TEXT Dr Joachim Harder, OneStone Consulting SL, Barcelona/Spain The continuing development in the size of vertical roller mills and2017年7月17日 The last setting to consider is the speed and gear ratio of the rollers Either a 1to2 or 1to3 gear ratio is recommended for best results Again, this depends on your application and material The lower gear ratios will have a lower top speed, which can work well for highly viscous materials Overall, finding the most suitable machine is a Threeroll mill selection tips Processing Magazine2010年11月1日 The new MVR vertical roller mill for grinding cement raw material, cement and granulated blast furnace slag has a modular design, which enables operation to be continued even if one roller module The new pfeiffer MVRR vertical roller mill for producing raw meal Vertical Roller Mill Drives Peter Boiger RENK AG 86199 Augsburg, Germany peterboiger@renk Abstract The Vertical Roller Mill (VRM) has proven a universal tool for grinding limestone, clinker and slag in the cement industry The maximum mill powers doubled from 2500 kW in the midseventies to 5000 kW in the nineties Today, another 20 yearsDevelopment of the 4th Generation Vertical Roller Mill Drives
.jpg)
Numerical Investigation of Vertical Roller Mill Operation Using
2023年12月4日 When higher rolling resistance is applied due to particle shape complexity at less mill speed, more vertical force is exerted on the roller, and the roller speed is insensitive to rolling resistance This study provides the basis for further experimental investigations on industrialscale VRM and supports the design optimization of the VRMsteel mill Nonuniform and heavy shock loads are considered normal operating conditions Many design engineers handle this requirement by increasing the service factor of the gearbox According to the American Gear Manufactures Association (AGMA) selection criteria, reducers can be selected by Service Factor or Load ClassificationRoll Drive Design Considerations for Steel Mill Rolling Operationsassure the best overall selection Roller Drive Chain Selection and Engineering Information Class of Driven Load Type of Input Power Internal Combustion Engine with Hydraulic Drive Electric Motor or Turbine Internal Combustion Engine with Mechanical Drive Uniform 1 1 12 Moderate 12 13 14 Heavy 14 15 17 sec293294TI 11/19/08 12:45 PM Roller Drive Chain Selection and Engineering Informationand methods in the construction of large gears Gear Material selection and Construction for Large Gears Frank C uherek 40module (125DP to 064 DP) Single stage reduction gears range from 8:1 to a 6,250kW ball mill gear at 1676rpm output speed has a required rim thickness value of 210mmGear Material Selection and Construction for Large Gears
.jpg)
Custom Large Girth Ring Gear for Ball Mill / Rotary Kiln
Custom Large Girth Ring Gear for Ball Mill / Rotary Kiln, wind mills as well as in other industry sectors These are made available in module range of 10 Module to 70 Module and in minimum diameters of 100 mm to 15000 mm Further, We supply mill heads,feed inlet,grinding roller,cement kiln riding ring, and methods in the construction of large gears Gear Material selection and Construction for Large Gears Frank C uherek Printed with permission of the copyright holder, the American Gear Manufacturers Association, 1001 N Fairfax Street, Fifth Gear Material Selection and Construction for Large Gears2021年10月6日 Abstract With the large‐scale development of the ball mill, the direct‐drive gearless ball mill has emerged, eliminating the limitation of the transmission torque of large gearElectromagnetic design and thermal analysis of module combined The large vertical planetary gear reducer was developed using stateoftheart technology With a construction of one bevel gear stage and two planetary gear stages, the gear unit features high transmission accuracy, uniform stress distribution and high load bearing capacityVertical Roller Mills Cement Processing Equipment CITIC HIC
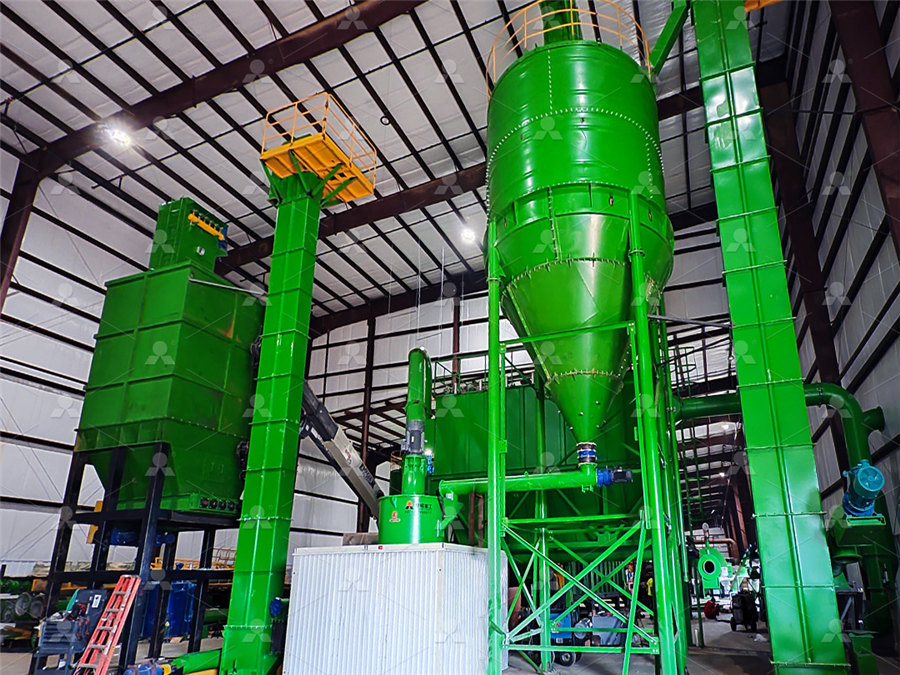
Cheap Large Diameter Ring Gear Manufacturers
In summary, the costeffectiveness of a large ring gear depends on various factors, including size, complexity, material selection, manufacturing process, and operational requirements By considering these aspects and weighing the 2023年6月16日 S, cigar and other special curved roll body: CVC rolling mill, UPC rolling mill (2) Section steel mill roll : There is a rolling groove (pass type) on the roll body (3) Special rolls : Generally used in special or special rolling mills Classification of rolling mill rolls and selection of 2021年11月5日 The lower rocker arm is an important part of the vertical roller mill and its lightweight design is of great significance for reducing the mass and production cost of the roller millOptimization Design of the Lower Rocker Arm of a 2024年1月1日 Roller mill is a type of grinding equipment for crushing materials by which is subjected to pressure and shear force It has the advantages of a large processing capacity, easy (a fixed roller and a movable roller), the driving system (main motor, reducer, belt pulley, and gear shaft), the hydraulic system, the Roller Mill SpringerLink
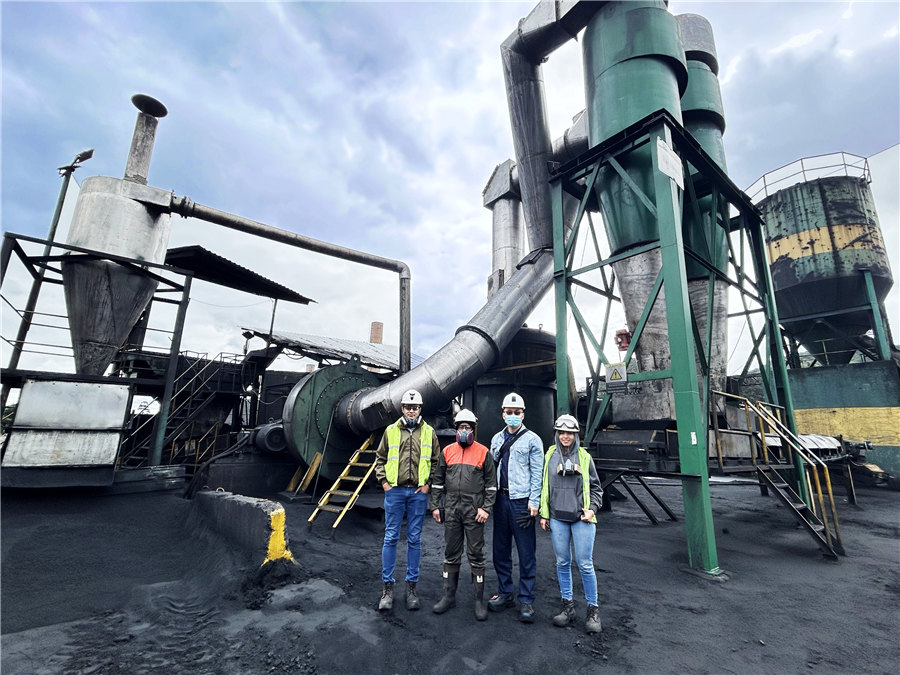
Polysius Roller Mills For grinding
of a roller mill Stages in the assembly of a roller mill in Australia View into the interior of the mill during assembly Grinding table gear unit Coarse feed valve elevator to the grinding table or is conveyed to the highefficiency separator The discharge ring is of modular design and made of highly wearresistant eleA sugar mill gear is a crucial component of a sugar mill, which is responsible for grinding and processing sugarcane into sugar The gear is typically a large, heavyduty, and complex machine that is designed to handle the high loads and stresses involved in sugar processingThe sugar mill gear is responsible for transmitting power from the mill's main drive motor to the rollers, which Large Module Sugar Mill Gear Luoyang Yujie Industry Trade Vertical Roller Mills FLSMidth Free download as PDF File (pdf), Text File (txt) or read online for free This document discusses different drive solutions for vertical roller mills used in cement production It provides an overview of conventional drive systems, which use a horizontal motor and gearbox with a bevel gear stage to change the rotation axisVertical Roller Mills FLSMidth PDF Electric Motor Gear2021年10月6日 With the largescale development of the ball mill, the directdrive gearless ball mill has emerged, eliminating the limitation of the transmission torque of large gear However, it is difficult to prElectromagnetic design and thermal analysis of module
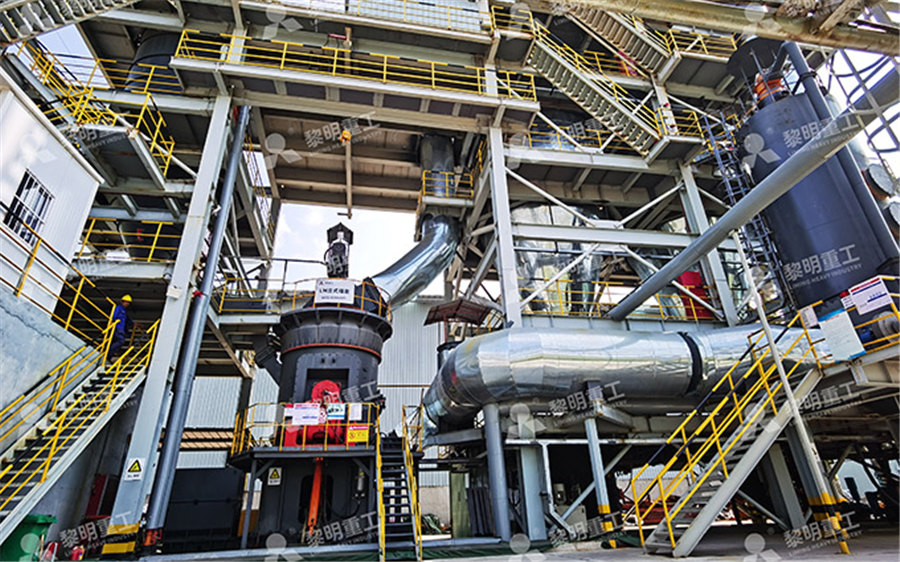
Industrial gear unit drive solution for ball mills SEWEURODRIVE
Power to mill and grind: Industrial gear units and gear wheel rims for ball mills Ball mill: Drive solutions for small and large torques Large girth gears are installed around the cylinder to rotate the horizontal ball mill cylinders A pinion connects these directly to the industrial gear unitRoller shell dimension of different roller, as shown in table 1 tjprc editor@tjprc 830 R R Karthi L Emmanual Table 1: Shell Dimensions Rollers Outer Diameter (mm) Groove Depth (mm) Pitch Circle Diameter (mm) Feed 878 778 8002 Top 915 48 867 Discharge 900 615 8385 Setting: Feed roller side =36mm, Discharge roller side =145mm, Trash plate side =70mm (PDF) DESIGN AND ANALYSIS OF ROLLER SHAFTS FOR SUGAR