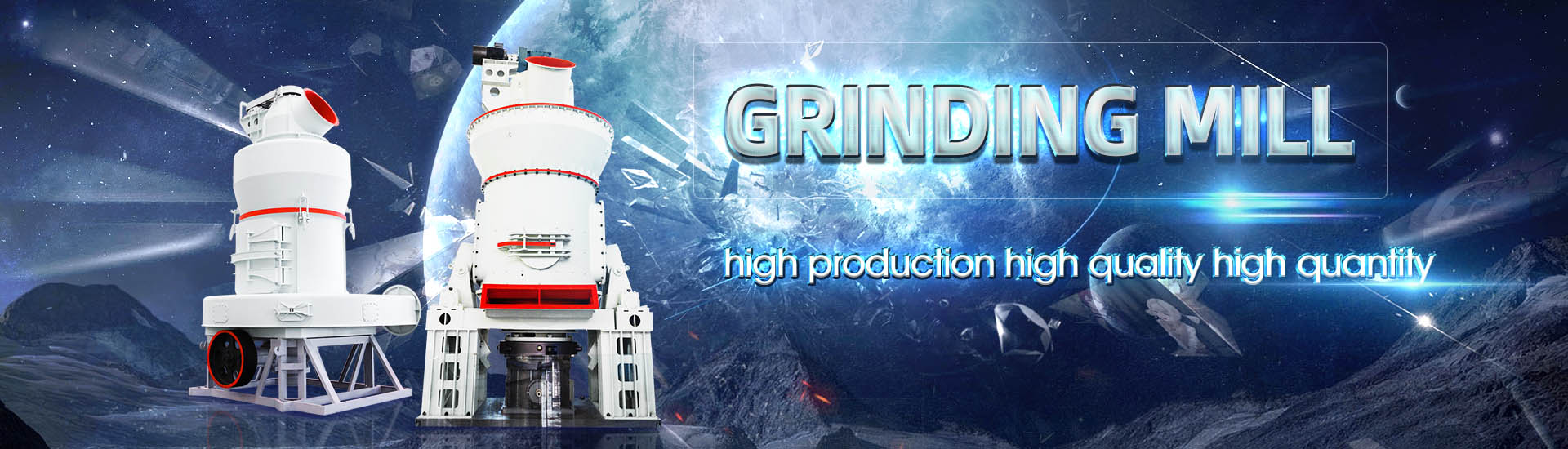
Speech on Pulverized Coal Preparation in Cement Plant
制粉-10.25公众号.jpg)
Modeling of Pulverized Coal Combustion in Cement Rotary Kiln
Combining the models of gassolid flow, heat and mass transfer, and pulverized coal combustion, a set of mathematical models for a fullscale cement rotary kiln were established2023年1月1日 The utilization of coal in the cement and concrete industries takes three basic forms: (1) as a fuel in the production of cement clinker; (2) ash produced by burning coal in Coal utilization in the cement and concrete industriesTo achieve calcination temperature between 860 °C and 950 °C, according to (1), additional heat must be provided which is mostly (up to 70%) achieved by burning a primary fuel (such as Identification and Control of Precalciner in the Cement PlantThe cement industry is one of the largest pollutant emitters One way to cope with high pollutant emissions is to cocombust biomass with pulverized coal A mathematical model was developed, which is detailed enough to consider the Improving Pulverized Coal and Biomass
.jpg)
Pulverised Coal an overview ScienceDirect Topics
Pulverized coal (PC) combustion is presently the system of choice for coalfired powergenerating plants In PC combustion, the coal is dried and is ground to a specified fineness, with a Pulverized coal combustion (PCC) is the most widely used technology for coal power generation In this process, coal is milled, pulverized, and injected in the boiler with air to allow Pulverised Coal Combustion an overview ScienceDirect TopicsCombining the models of gas−solid flow, heat and mass transfer, and pulverized coal combustion, a set of mathematical models for a fullscale cement rotary kiln were established In terms of Modeling of Pulverized Coal Combustion in Cement Rotary KilnCombustion of coal in pulverised form has been developed over several decades, with continuous improvements in design and performance It is most commonly used in either large scale utility Fundamentals of pulverised coal combustion ICSC
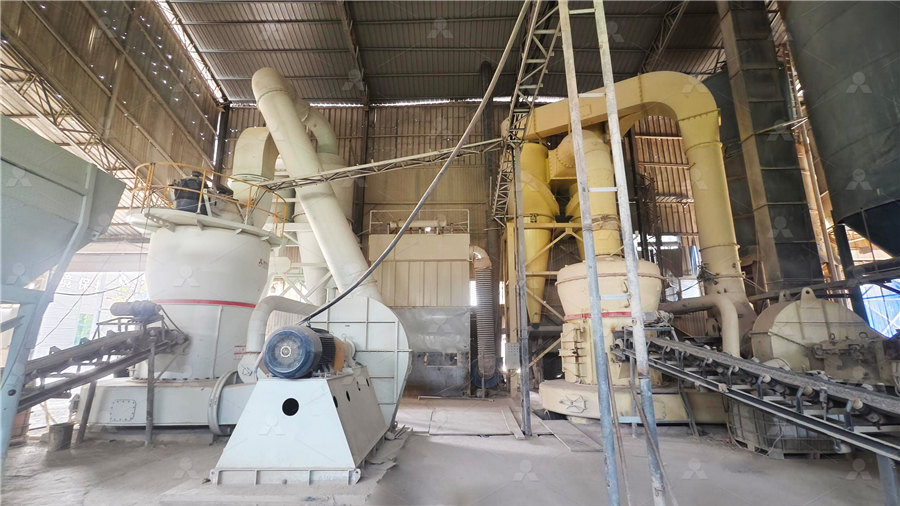
Coal utilisation in the cement and concrete industries
Abstract: The utilisation of coal in the cement and concrete industries takes three basic forms: 1 As a fuel in the production of cement clinker, 2 Ash produced by burning coal in power 2023年12月14日 The author first reviews some of the uses of pulverized coal in the industries — such as the cement, steel and copper industries, after which he gives a technical definition of Pulverized Coal as a Fuel J Fluids Eng ASME Digital Collection2014年5月1日 Request PDF Improving the Sustainability of Cement Production by Using Numerical Simulation of Limestone Thermal Degradation and Pulverized Coal Combustion in a Cement Calciner The cement Improving the Sustainability of Cement Production by Using 2023年1月1日 In the 1990s Gulf Cement Co, at their Khor Khuwair plant in the United Arab Emirates, developed a process in which coal and/or Petcoke could be microground and an oil–coal mixture fired by a kiln originally intended for oil firing (Gulf Cement Co, 2011)Coal utilization in the cement and concrete industries
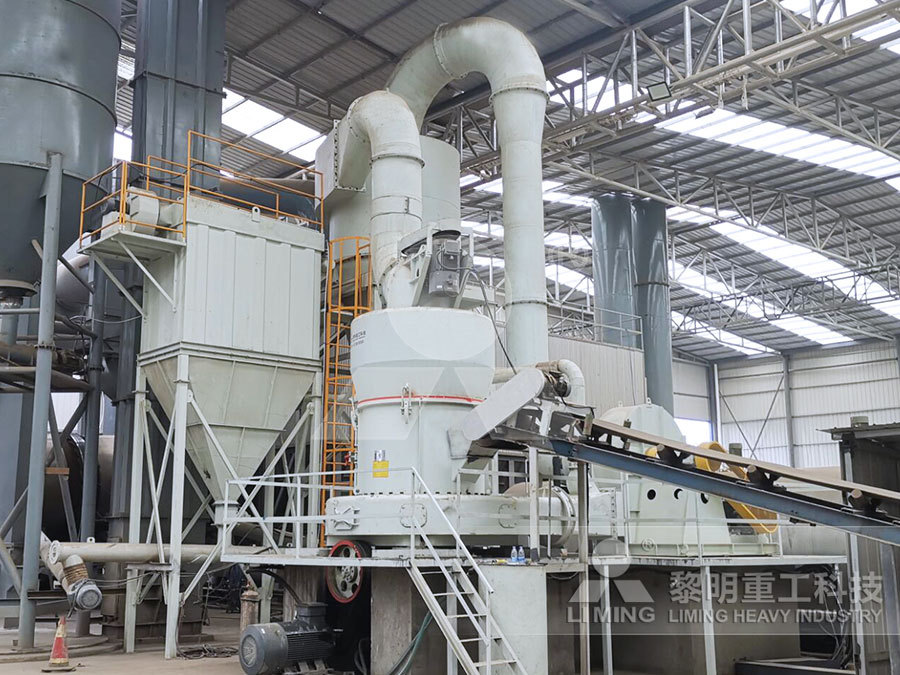
Discussion on Safety Production of Coal Milling System in Cement Plant
2022年1月25日 Pulverized coal needs to be prepared in advance and has a certain amount of storage to eliminate the impact of coal supply supplementation on cement productionIn the 1890″s pulverized coal firing was achieving its first real commercial success in the cement industry of the United States The cost of a coal preparation department of a cement plant amounts to about 1520 % of the cost of the total plant machineryFuels in the cement industry INFINITY FOR CEMENT EQUIPMENTThe most common type of coalfired power plant is pulverized coal combustion (PCC), shown in Figure 21 A mixture of pulverized coal and air (Juniper, 2000) because of its ability to handle a wide variety of lowquality fuels (including coal preparation wastes) and its capacity to produce minimal SO 2 emissions from combustion of coals Pulverised Coal Combustion an overview ScienceDirect TopicsHigh Efficiency Pulverized Coalfired Power Generation Technology 4D2 Lowrank Coal Upgrading Technology Cavein prediction Coal preparation plant Coal exploration EAGLE SCOPE21 DME 3 Coal mine Coal carrier Coal train Carbonization Power plant Cement plant Iron works Chemical plant Electrostatic precipitator Enhanced Oil Recovery Technology Innovation in the Coal Industry 一般財団法人
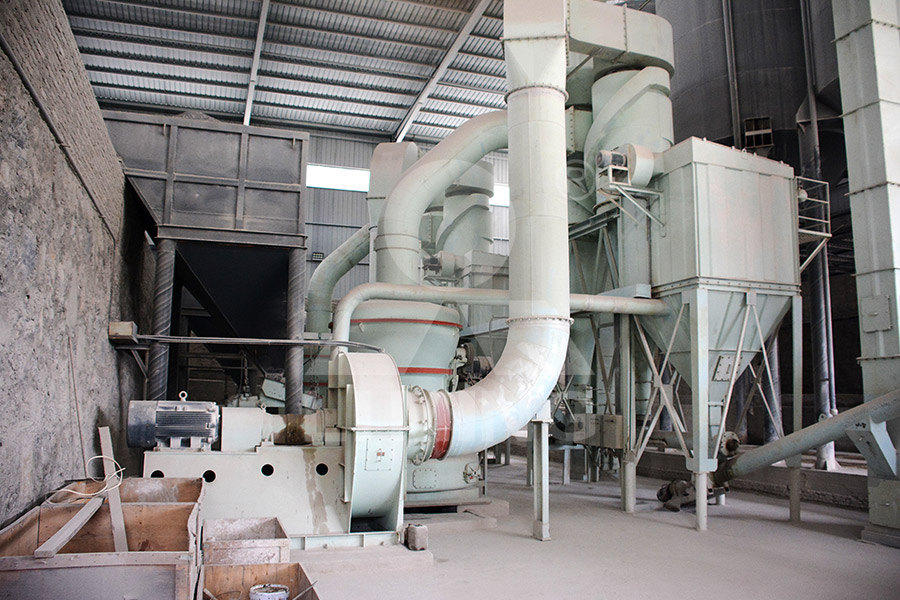
Why Pulverized Coal is Used in a Power Plant Bright Hub
Before going into the details, let us look at the quantity of coal processed in a power plant A 2000 MW power station could be handling coal in the range of 1600 tons/hr or around 12 million tons of coal annually2014年6月24日 The use of waste wood biomass as fuel is increasingly gaining significance in the cement industry The combustion of biomass and particularly cofiring of biomass and coal in existing pulverized Numerical study of cofiring pulverized coal and biomass inside a ★ Pulverized Coal Preparation System 1 The raw coal from storage and conveying system come into air swept coal mill for grinding The coal powder mass and heat transfer with 200℃~350℃ hot air The moisture enter into flue gas from coal Coal powder is dried by hot air Then coal powder come to powder separator with airflow for Pulverized Coal Preparation Pulverized Coal Grinding Plant Coal Cement Manufacturing Process by TIZITA MOGES , SELAMU ABULE DEREJE ENDALAMAW IF YOU NEED THIS GUIDE AND ALL OTHER USEFUL EXCEL SHEETS WHICH WILL MAKE YOU MASTER THE Cement Manufacturing Process INFINITY FOR
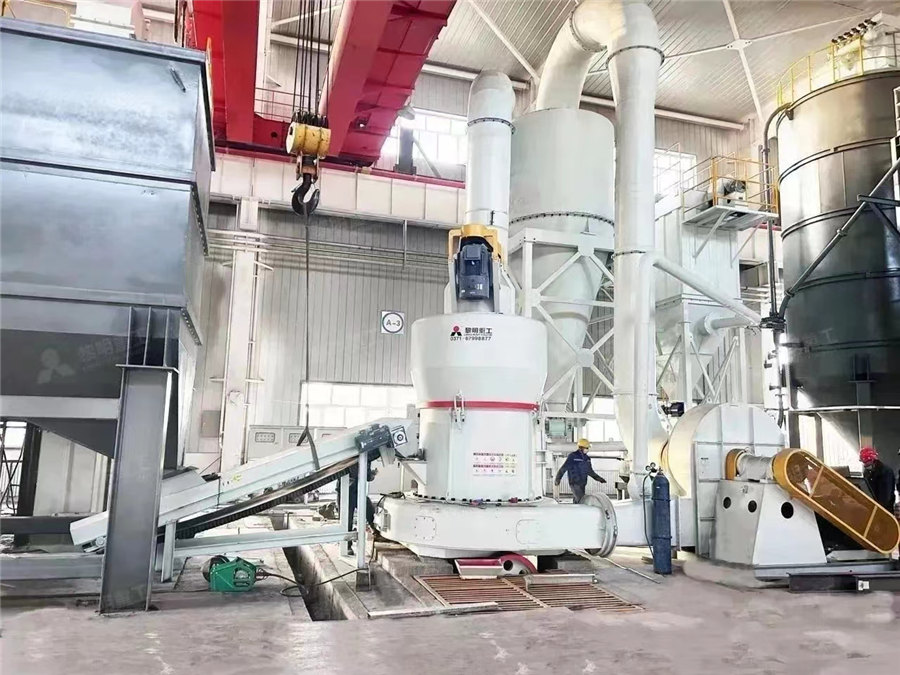
Coal mill pulverizer in thermal power plants PPT
2012年11月17日 2 1Introduction Coal continues to play a predominant role in the production of electricity in the world, A very large percentage of the total coal is burned in pulverized form Pulverized coal achieved its first commercial 2020年10月31日 The potential utilization of boiler slag generated in large amounts from pulverizedcoalcombustion (PCC) power plants has recently drawn much attention due to the serious problems caused to (PDF) Utilization of Boiler Slag from PulverizedCoal2018年10月21日 Fig 1 Pulverized coal combustion and gas composition in raceway The extent of combustion (combustion efficiency), and hence the amount of unburnt material transported out of the raceway, depends on several parameters which include (i) properties of the coal, such as the VM content, particle size and density, and (ii) operating conditions, for example, blast gas Understanding Pulverized Coal Injection in Blast Furnacebituminous coal with a heating value (HHV) of 11,380 Btu/lb The coal's ultimate analysis is shown in Figure 1 The original fuel system consisted of three springloaded, MB type, vertical spindle mills, each gravimetric belt feeder, seal air fan, 1800 rpm primary air fan, and four mill outlets supplying pulverized coal to one of the threeWorldProven Coal Pulverizer Technology Debuts in the US
.jpg)
(PDF) Assessing the impact of specific weight of differentsized
2023年1月1日 In case of firing pulverized coal in power steam boiler certain fuel preparation process has to be taken in order to ensure stable and optimal combustion in boiler furnace5 Table 1 Parameters of cement rotary kiln The size of the rotary kiln used in this paper is ∅4×46 m Due to the thickness of the refractoryNUMERICAL SIMULATION OF PULVERIZED COAL COMBUSTION 2015年2月1日 The cement industry sector is one of the largest carbon emitting industrial sectors, and due to the effect of global warming sustainable cement production is increasingly gaining on importance Controlling the combustion of coal and the thermal degradation of limestone, the two main thermochemical processes that occur inside a cement calciner, is of Improving the sustainability of cement production by using 2024年2月3日 Fine slag (FS) is an unavoidable byproduct of coal gasification FS, which is a simple heap of solid waste left in the open air, easily causes environmental pollution and has a low resource utilization rate, thereby restricting the development of energysaving coal gasification technologies The multiscale analysis of FS performed in this study indicates typical grain size Multiscale analysis of fine slag from pulverized coal gasification in
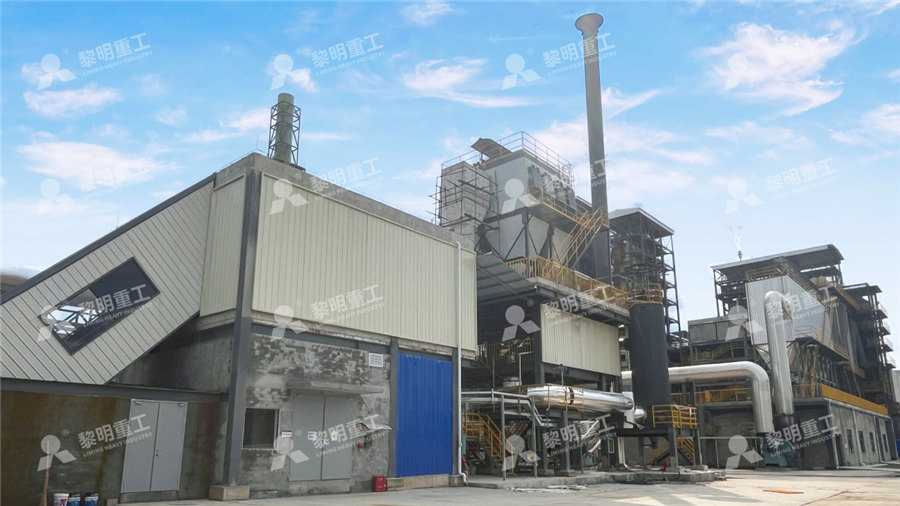
Developments in Pulverized CoalFired Boiler Technology
1996年4月10日 Exhaust gas temperature in coalfired power plants can reach approximately 120 °C to 140 °C, with the thermal energy accounting for approximately 3% to 8% of the total input energy2008年6月1日 Lowsulphur Yanzhou coal and highsulphur Changguang coal were selected as experimental coals, and quaternary phase (Qphase) cement clinker cogeneration experiments were conducted on a twostage Experimental study on Qphase cement clinker cogeneration in pulverized We supply pulverized coal burners for rotary kilns; feel free to contact us! Skip to content +86 s about blog contact EN AGICO CEMENT supplies EPC projects for both cement plant and single Pulverized Coal Burner Pulverized Coal Burner For Using highsulfur Changguang coal for experimental purposes,tests concerning the influence of calcination temperature,the material's retention time and its way of preparation,as well as the atmosphere existing in the furnace etcon the coproduction of Qphase cement clinker,by pulverized coal fired boilers,were studied with the help of a doublestage polyphase reaction Experimental Study on Factors Influencing Semantic Scholar
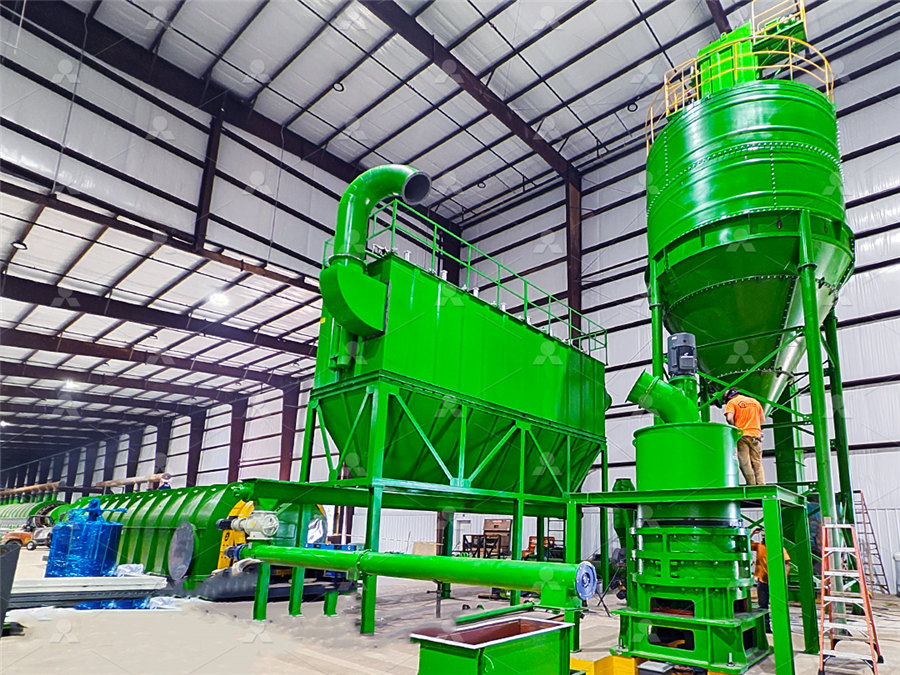
ENERGY CONSUMPTION PREDICTION OF CEMENT CALCINATION
storage The fuel coal, dried and grounded by the coal mill, is stored in the form of pulverized coal in the pulverized coal silo and then supplied to the decomposition furnace and rotary kiln Coal consumption is mainly concentrated during the calcination process of the calciner and kiln, while electricity consumption is mainly concentrated in 2019年2月14日 The aim of present paper is to review various aspects of pulverized coal combustion such as oxyfuel combustion, cocombustion of coal and biomass, emissions from pulverized coal furnaces, ash formation and deposition, and carbon capture and sequestration (CCS) technologies to outline the progress made in these aspectsA complete review based on various aspects of pulverized coal energies Article Utilization of Boiler Slag from PulverizedCoalCombustion Power Plants in China for Manufacturing Acoustic Materials Jing Li 1,* , Xinguo Zhuang 1, Carlos Leiva 2, Celia Arenas 2, Ana Cornejo 2, Xavier Querol 3, Natalia Moreno 3, Oriol Font 3 and Constantino Fernández Pereira 2 1 Key Laboratory of Tectonics and Petroleum Resources, China University of Utilization of Boiler Slag from PulverizedCoalCombustion Power 2020年10月20日 Use of coal with high volatile contents requires precautions against spontaneous combustion due to lowtemperature oxidation Laboratory tests were carried out to investigate the differences of Experimental investigations on spontaneous combustion of pulverized
.jpg)
Effects of CoFiring Biomass and Pulverized Coal on NO
2024年1月23日 With increased awareness of the largescale CO2 emissions from the cement industry, there has been growing focus on greenhouse gas reduction strategies Among all these strategies, fuel substitution using biomass fuel is extensively used to achieve CO2 zeroemission in cement production Due to the avoidable hightemperaturegenerated thermal nitrogen 2022年3月1日 Fu et al 25 used coal gasification slag to replace Portland cement and proved that a low dosage of coal gasification slag (10%) could play a role in nucleation and pozzolanic effect in Portland Investigation on the utilization of coal gasification slag in Portland A pulverized coalfired boiler is an industrial or utility boiler that generates thermal energy by burning pulverized coal (also known as powdered coal or coal dust since it is as fine as face powder in cosmetic makeup) that is blown into the firebox The basic idea of a firing system using pulverised fuel is to use the whole volume of the furnace for the combustion of solid fuelsPulverized coalfired boiler WikipediaPDF On Aug 1, 2017, Wiehan A Pelser and others published Analysis of energy consumption and cost distribution on a South African cement plant Find, read and cite all the research you need on (PDF) Analysis of energy consumption and cost
.jpg)
Ball Mill Coal Pulverizer for power plant – ZJH minerals
It is the main equipment of pulverized coal preparation system It is used for pulverizing all kind of coal in different harness It is also used for the coal grinding in the industries of cement, metallurgy, chemical, etc In Power Plant, the ball The document discusses coal preparation for use in cement production It describes different types of solid fuels used including coal, lignite, coke, peat and wood It discusses the consumption of fuels in dry and wet cement production processes It also discusses the history of using pulverized coal and the replacement of coal with fuel oil and natural gas for economic reasons Coal Preparation PDF Lignite CoalAccording to the annual census of coal preparation plants conducted by Coal Age [], the USA operates 286 coal preparation plants in 12 statesThis number is relatively small by comparison to the worldwide fleet which is estimated to be 2,283 plants []The capacity of the plants can range from less than 200 t/h for small operations to 6,000 t/h or more for large industrial plantsCoal Preparation SpringerLink2012年2月1日 Taking Changguang highsulfur coal and Yanzhou lowsulfur coal as experimental coal types, carrying out the experiment of Qphase cement clinker cogenerated from coal on twostage polyphase reaction setup and conducting XRD analysis on the mineral composition in cogeneration clicker sample, the result shows that the major mineral species in Study on Pulverized Combustion Boiler CoGeneration Belite Q
.jpg)
Study on Pulverized Combustion Boiler CoGeneration Belite Q
2012年2月1日 Taking Changguang highsulfur coal and Yanzhou lowsulfur coal as experimental coal types, carrying out the experiment of Qphase cement clinker cogenerated from coal on twostage polyphase 2010年10月1日 Cement industry is highly energy and emissions intensive Thermal energy is majorly used in the kiln and calciner systems, accounting for over 90% of total energy use in cement plant, and Study on a separation technology for more efficient utilization 2022年1月17日 To examine the effect of cofiring on pulverized coal injection (PCI) in BFs, two coals of different ranks were blended with the biomass in different proportions, and then their combustion Effects of Cofiring Coal and Biomass Fuel on the Pulverized Coal 2022年12月23日 This review provides an indepth analysis of the complex chemistry of cement, offering valuable insights for researchers(PDF) An Insight into the Chemistry of Cement—A Review
.jpg)
Simulation Study on Measuring Pulverized Coal Concentration in
2019年2月28日 In the actual power plant operation, the pulverized coal concentration is generally between 02 kg/kg and 10 kg/kg [10], the dielectric permittivity ε is the maximum of 17 When there is only air in the pipeline, the cutoff frequency