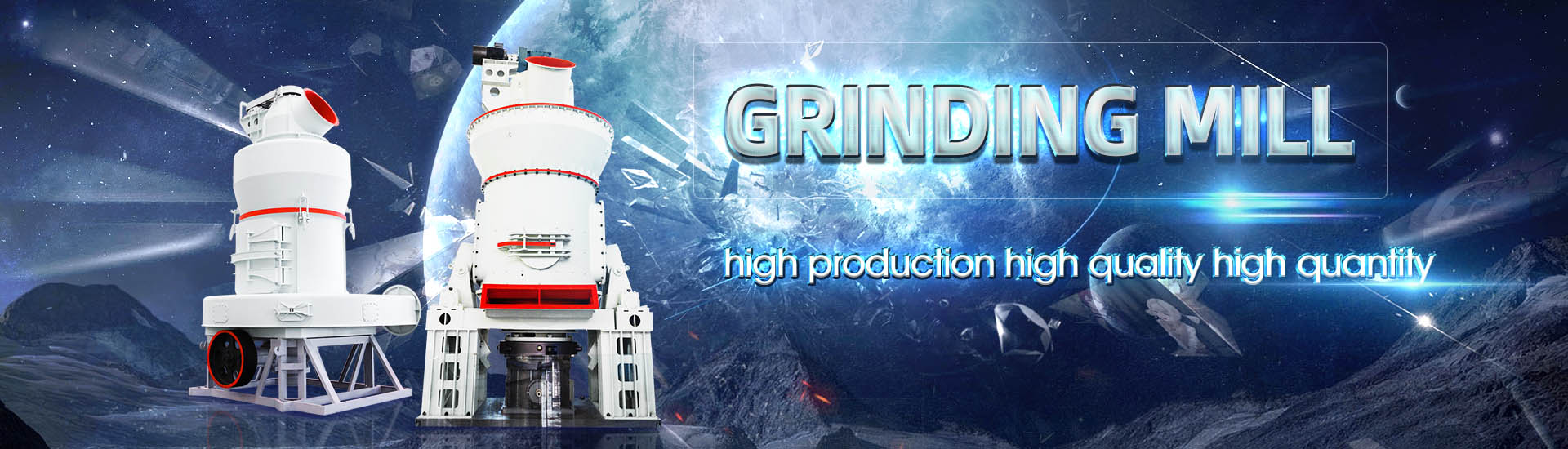
Parameters of ore mill MPφ800×600
.jpg)
高压辊磨机在金属矿选矿与球团预处理领域的工艺和
2019年4月12日 Based on the current research results and industrial data, this paper compares the process flow of highpressure roller mill in metal mine and pellet pretreatment industry, as 2013年4月1日 Milling parameters of the PGM ore are measured and others backcalculated Simulated and measured product size distributions were satisfactorily compared Milling Determination of the milling parameters of a platinum group 2017年4月1日 Pilot plant test results with various ores showed that low energy consumption feature of vertical roller mills is applicable to the ore industry Grinding test results for zinc ore Operational parameters affecting the vertical roller mill 2017年10月1日 In this article, we present laboratory scale batch grinding and leaching profiles of a monosized gold ore sample (1700 + 850 μm) The sample was obtained from a runofmine (PDF) Determining optimum wet milling and leaching parameters
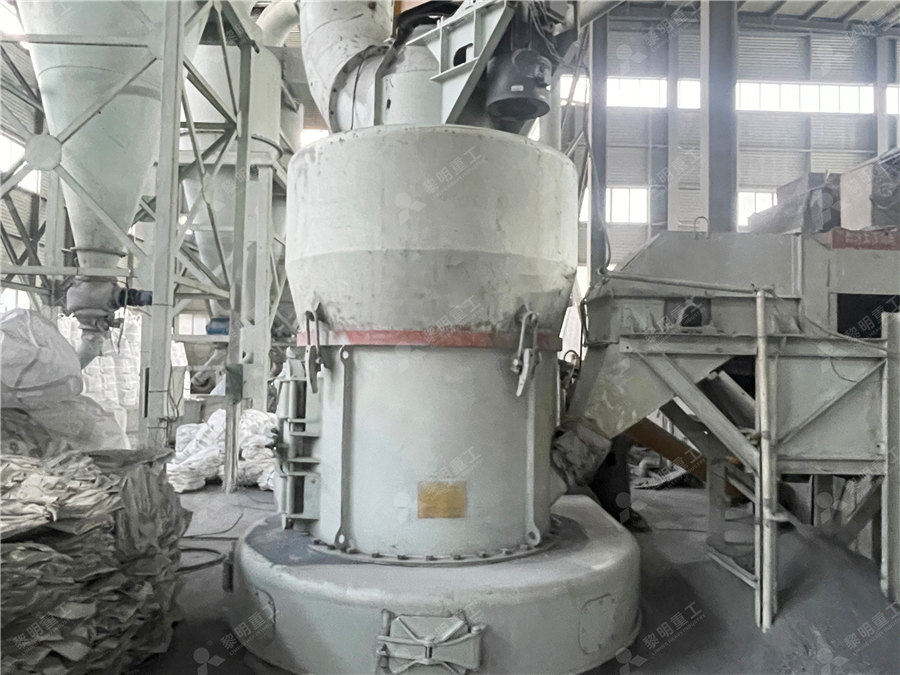
Comparison of Ore Hardness Measurements for Grinding Mill
2021年1月14日 Six samples were tested by Hazen Research, Inc (HRI) to obtain the JK parameters using the JK Drop Weight Test, standard Bond crushing, and rod mill work indices, 2019年2月11日 A detailed test work was carried out with an industrial semiautogenous (SAG) mill in a copper plant in close and open circuits to specify the effects of ore characteristics and Relationship among operational parameters, ore characteristics, 2023年7月20日 There are several impact factors of the grinding operation (1) Structure parameters of grinding mill, including its specifications, model, aspect ratio, ore discharging Ore Grinding SpringerLinkIn this study, the simulation of grinding of quartz is investigated in order to identify the optimal mill operating parameters With the use of population balance modeling the specific rate of (PDF) Identification of Optimal Mill Operating Parameters during
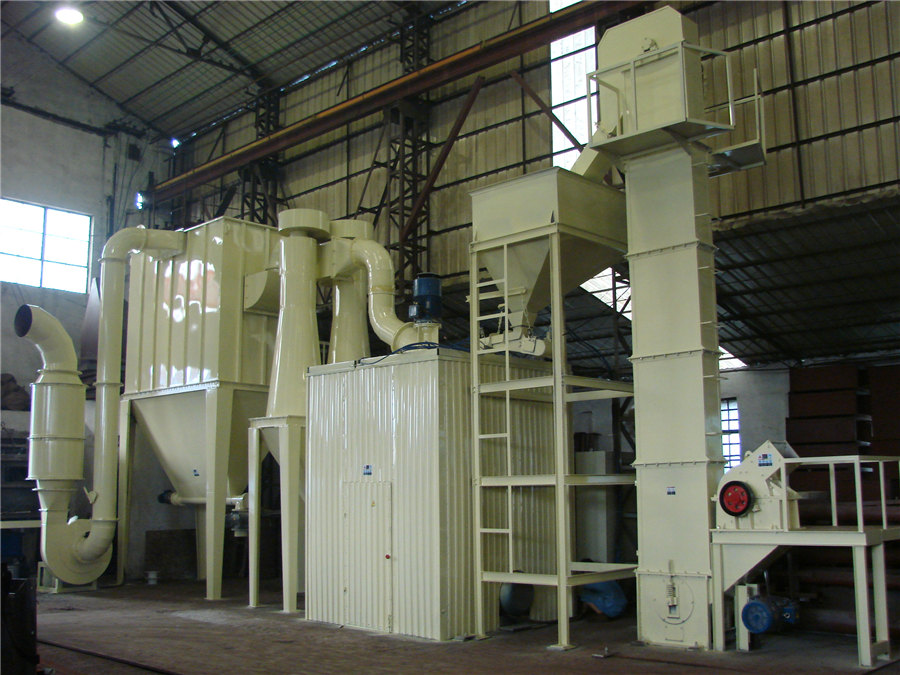
Measurement and Control for Ore Grinding and Classification
2024年1月1日 The main parameters of grinding and classification process include measurement of millfeeding quantity, mill load measurement, measurement of ore slurry density, Online 2013年4月1日 Highlights Milling parameters of the PGM ore are measured and others backcalculated Simulated and measured product size distributions were satisfactorily compared Milling kinetics of the desired size class for flotation were simulated using the parameters Results show good match between experimental and predicted Validity of the determined parameters Determination of the milling parameters of a platinum group the experimental laboratory ball mill used is shown in Fig 3 22 Sample preparation The coppercobalt ore used in the actual test work was obtained from the feed to the primary mill (run of mine) at the Etoile mine of Rwashi mining, a subsidiary of the Metorex group The ball mill feed content mass was calculated using following Determination and scaleup of the milling parameters of a high 2022年2月17日 In openpit mines, the blast operation should be effectively optimized, leading to minimization of production costs through the application of specific technical specificationsAn Evaluation on the Impact of Ore Fragmented by
.jpg)
(PDF) Operational parameters affecting the vertical roller mill
Within the scope of the study, ore grinding performance of the VRM was investigated via a mobile grinding plant and relationships between operational parameters were identified In this context, gold ore was ground under different process conditions The samples collected after the test works and size distributions were determined2013年4月16日 Investigation of some parameters affecting the Ultrafine grinding of refractory silver ore tailings by stirred mill 0 200 400 600 800 1 000 Ener gy C ons four important parameters of (PDF) Investigation of some parameters affecting the Ultrafine 2013年4月1日 To this end, three monosize classes feeds 850–600 μm, 600–425 μm and 425–300 μm of a platinum ore were ground using three different ball sizes (10, 20 and 30 mm) in a laboratory mill for the grinding times 05, 1, 2, 4, 8, 15 and 30 minDetermination of the milling parameters of a platinum group 2021 JKSimMet (JKMRC) and USIM PAC (CASPEO) had sold 600 and 300 licenses, respectively Simulation modeling software JKSimMet characterizes the physical and mechanical properties of ore using the parameters A, b and t a obtained from the drop weight testing by JK DWT and SMC Parameter SAG mill 10500×4600 (No 1) SAG m ill 10500×4600 (No ORE HARDNESS PROPERTIES EVALUATION BASED ON
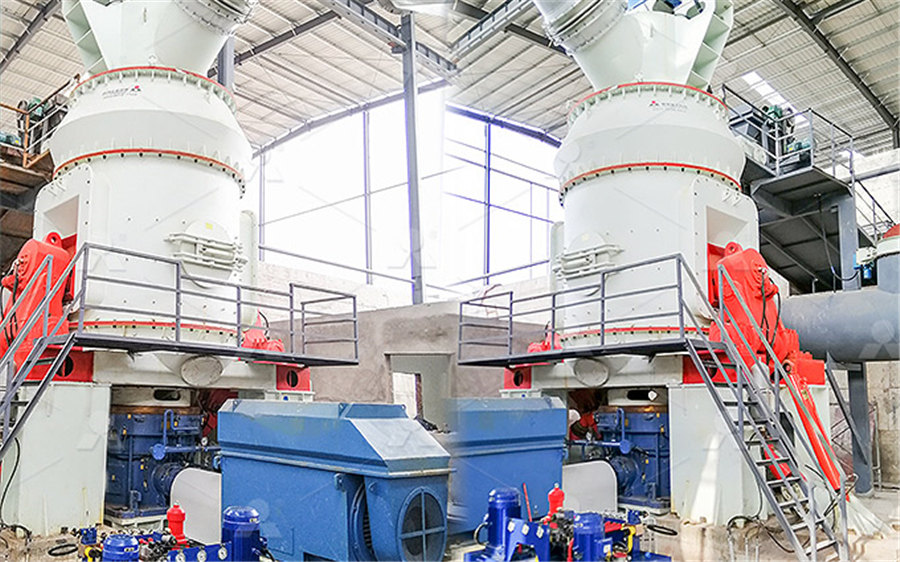
Inferential measurement of SAG mill parameters II: State estimation
2002年12月1日 This paper discusses the combined state and parameter estimation of SAG mill inventories and model parameters Recognised simulation models are utilised for the rock and water charge state equationsTo address this issue, the CVs in Table 2 that relate to the integrating nature of the SAG mill, namely, the mill weight, powerdraw, rock charge and ball charge, were modelled as integrators In the Connoisseur environment, integrators are modelled by way of rateofchange (ROC) modelsThe ROC coefficients are calculated using as follows:INFERENTIAL MEASUREMENT OF SAG MILL PARAMETERS V: MPC SIMULATION2010年9月27日 Load of the ball mill affects the productivity, quality and energy consumption of the grinding process But sensors are not available for the direct measurement of the key parameters for mill load Modeling of operating parameters for wet ball mill by 2022年1月23日 This work concentrates on the energy consumption and grinding energy efficiency of a laboratory vertical roller mill (VRM) under various operating parameters For an ore market × 10 − 6 Analysis and Optimization of Grinding Performance of
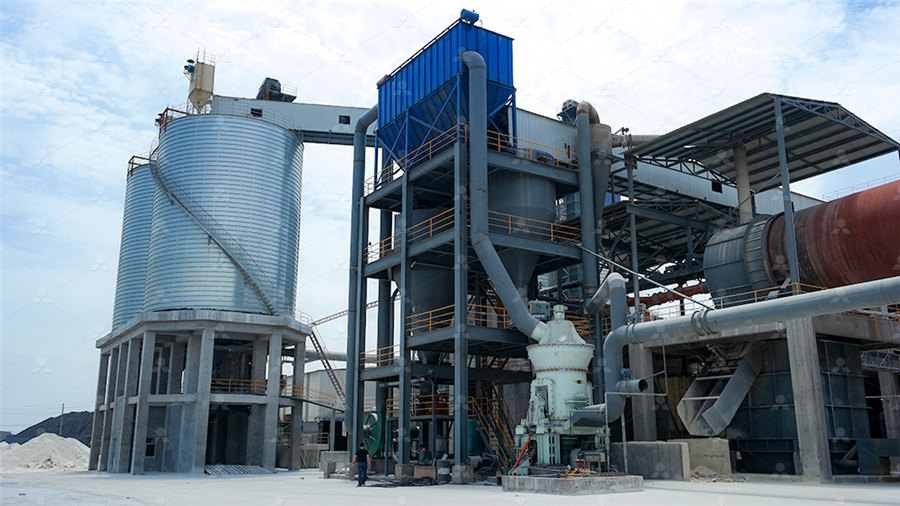
Optimization of stirred mill parameters for fine
2020年7月23日 Optimization of stirred mill parameters for fine grinding of PGE bearing chromite ore, Particulate Science and Technology, DOI: 101080/2020 To link to this article: https://doi The chosen parameters J L*D Db f U n t Dmax Fractional ball filling (%) Mill sizes (height*diameter) Bead sizes (mm) The formal bed porosity of beads (%) The Particlebead ratio Stirrer speeds (rpm) Grinding periods (s) Maximum particle size of feed (Starting sample) Real density of bead (gr/cm3) dgm The calculated parameters Vd Effective mill volume (cm3) Vbb Studying the effect of different operation parameters on the 2017年10月1日 This book is intended as a compact introduction to the mathematical treatment of the unit operation of size reduction by mechanical means, that is, the sizing, behavior, and performance of (PDF) Determining optimum wet milling and leaching parameters for 2012年5月1日 The effect of ore characteristics on the particle shape were studied using two detailed industrial surveys to monitor breakage events taking place inside industrial SemiAutogenous (SAG) mills as Effects of ore characteristics on product shape ResearchGate
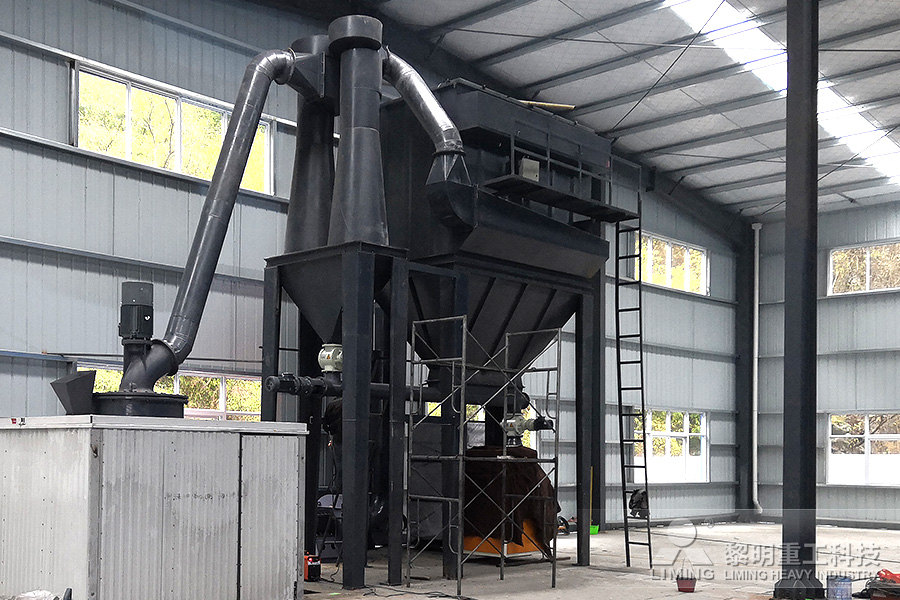
Optimization of cyanidation parameters to increase the capacity
to the plant restrictions), these parameters were fixed in experiments Table 3 The values of leaching parameters on Pooyazarkan mineral processing mill Parameter Value Sodium cyanide 1450 ppm (Free cyanide concentration is 500 ppm) Dissolved Oxygen 46 mg/l pH 10105 Solid Percent 38 d80 75 micron Residence TimeVertical stirred mill is a fine grinding equipment that covers advantages of low rotation grinding efficiency of minerals by constantly searching for ways to improve and develop energysaving highefficiency ore grinding equipment 600: 35: 37×39: 127: 101: 5768: CSM750 750: 39: 39×41: 13: 108: 7286: CSM850 850: 46: 42×4 Vertical Stirred Mill Mineral Processing Equipment CITIC HIC2009年9月23日 equipment manufacturer recommended ball mixture was used to validate the model(PDF) Effect of ball size distribution on milling parametersFind your ore mill easily amongst the 42 products from the leading brands (Fritsch GmbH, Retsch, Eriez, ball grinding mill Ф2200×7500 horizontal for limestone stone ball grinding mill Ф2200×7500 Final grain size: 74 µm 600 kg/h 1,200 kg/h Devours Ore mill, Ore grinding mill All industrial manufacturers
.jpg)
A developed approach based on grinding time to determine ore
2013年12月31日 The grinding process for all the three iron ores is carried out individually in Bond’s ball mill and the total retention time taken by each iron ore sample is calculatedOptimization of stirred mill parameters for fine grinding of PGE bearing chromite ore, Particulate Science and Technology, DOI: 101080/2020 To link to this article: https://doi Optimization of stirred mill parameters for fine grinding of PGE 2022年1月29日 Heterogeneous Selective Ensemble Learning Model for Mill Load Parameters Forecasting by Using MultiScale Mechanical Frequency Spectrum January 2022 DOI: 1021203/rs3rs/v1Heterogeneous Selective Ensemble Learning Model for 2021年8月20日 In terms of prediction of milling cutter wear: Zhang et al 7 introduce a tool wear prediction model with cutting parameters and cutting time Chen et al 8 propose and evaluate an artificial neural networks based in Optimization of milling process parameters and
.jpg)
Dual particle filters for state and parameter estimation with
2012年4月1日 Request PDF Dual particle filters for state and parameter estimation with application to a runofmine ore mill Measurements are not readily available for grinding mills owing to the nature of Çukurova Üniversitesi Mühendislik Mimarlık Fakültesi Dergisi, 33(3), ss 225236, Eylül 2018 Çukurova University Journal of the Faculty of Engineering and Architecture, 33(3), pp 225236, September 2018 ÇÜ Müh Mim Fak Dergisi, 33(3), Eylül 2018 225 Optimization of Wet Grinding Parameters of Calcite Ore in StirredOptimization of Wet Grinding Parameters of Calcite Ore in Stirred Ball Mill2024年9月26日 The present article focuses on incorporating mill scale, a steel plant solid waste, into the iron ore pelletization process The characterization results indicated that the mill scale contained about 71% of Fe and predominantly consists of magnetite and wustite mineral phases A detailed pelletization study is conducted using the mill scale at different proportions (0%, Evaluation of Quality Parameters and Mineralogy of Iron Ore speed and diameter of the ball have a great inuence on the MA leaching process with an optimum speed of 600 rpm and diameter of 10 mm (r 0 = 220 ˜m) yielding values r 600rpm retained = 076˜m and r600rpm reacted = 2124˜m when compared with nonMA traditional method with values r retained = 210˜m and rEffect of Ball Mill Parameters’ Variation on the Particles of a
.jpg)
高压辊磨机在金属矿选矿与球团预处理领域的工艺和
2019年4月12日 高压辊磨机能量利用率高,目前已在水泥行业、金属矿山、冶金球团等领域广泛应用。结合当前研究成果及工业现场数据,本文对比了高压辊磨机在金属矿山和球团预处理行业中的工艺流程,以及辊面比压力、辊面线速度、辊缝几个工艺参数,为高压辊磨机在金属矿山和球团预处理应用中工艺参数的 2012年4月1日 We explain the concept of dual particle filtering for state and parameter estimation Dual particle filters are implemented on a runofmine ore mill The state and parameter estimates for the mill can be used in an advanced control strategy A sensitivity analysis is done and indicates the class of systems for which dual estimation produces Dual particle filters for state and parameter estimation with 2013年4月1日 The mill is used to grind platinum ore from which the samples used by Chimwani et al [13] to determine the selection and breakage function parameters were collectedDetermination of the milling parameters of a platinum group 2016年4月30日 The proposed procedure can be also applied for the identification of optimal mill operating parameters for –0850+0600 mm, –0425+0300 ate the oper ating ef ciency of any g iven Identification of Optimal Mill Operating Parameters during

Analysis of vertical roller mill performance with changes in
2022年5月31日 Mineral crushing is the main source of energy consumption in mineral processing According to statistics, this consumption accounts for about 35–50% of the total cost of the mine (Curry et al, 2014), or even higherIt may also account for 18% of the global electrical energy consumption (NapierMunn, 2015)More efficient crushing equipment needs to be 2021年5月31日 The nature of the ore blending problem is due to uncertainty and the uneven distribution of minerals in geology The benefits of ore blending are extending the ore reserve base by utilization of (PDF) A Method of Ore Blending Based on the Quality 2015年9月20日 Every comminution testwork program should include the appropriate ore characterisation tests to describe the variability of ore breakage properties, but there are several ways to interpret the Geometallurgy Applied in Comminution to Minimize Design Risks2021年3月1日 Mill scale scrap and manganese ore were used as the iron and manganese resources, respectively, for the preparation of manganese ferrite The chemical compositions of manganese ore and mill scale scrap are listed in Table S1The manganese ore contains 4558 wt% total Mn (TMn) and 1192 wt% total Fe (TFe), while the mill scale comprises 7117 wt% Innovative methodology for cotreatment of mill scale scrap and
.jpg)
Experimental observations of lifter parameters and mill
2010年12月1日 There are several dimensional and opera62 tional parameters which have influences on the mill powerdraw 63 and can be considered for its prediction (feed rate, speed, size of 64 mill, F 80 , P 2024年3月1日 To validate the calibration method, iron ores were selected for laboratory experimentation Iron ores from Dagushan, Anshan, Liaoning Province (China) were processed into cylindrical specimens, as illustrated in Fig 13 (c) The results of the laboratory test revealed the UCS of ores of 5823 MPa and the MS of ores of 284 × 10 3 MPaA method to determine the bondedparticle model parameters 2014年1月1日 Conference: Proceedings of the 23rd International Mining Congress and Exhibition of Turkey IMCET 2013; At: Kemer, Antalya, Turkey, April 1619, 2013, pp 293301Factors affecting the performance of crushing plant operationsParameter specification of iron ore magnetic separator The most common iron ore magnetic separators in our company have 13 specificationsspecifications The cylinder diameter×cylinder length is between 600*1200 and 1500*3000, and the model CTB6012 to model CTB1530Introduction of Iron ore magnetic separator parameters
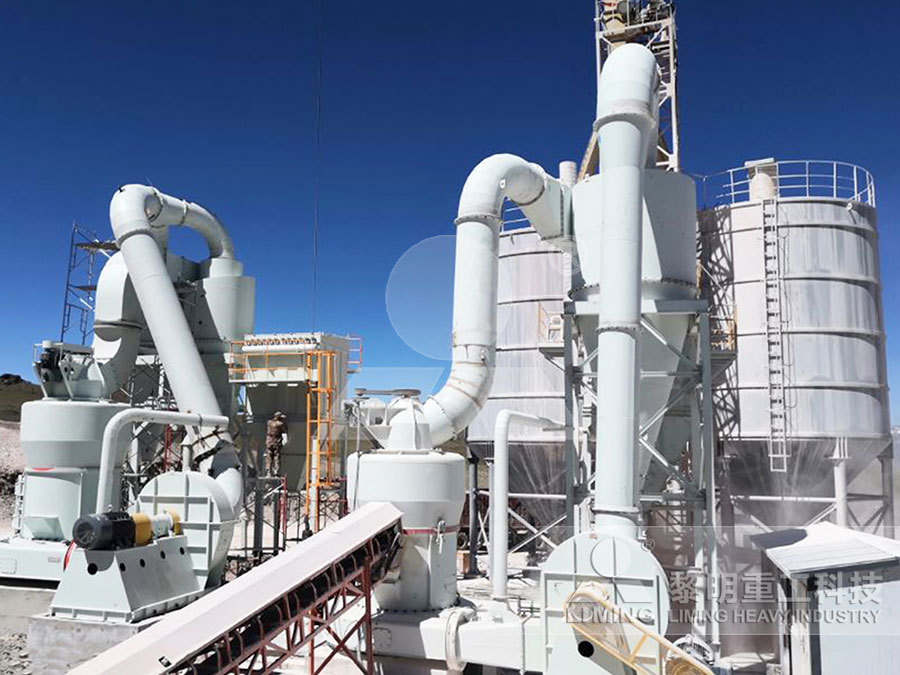
Monitoring ore loss and dilution for minetomill integration in
2016年2月1日 The purpose of this study is to understand how ore loss and dilution affect the mine call factor, with the aim of subsequently improving the quality of ore mined and fed to the mill