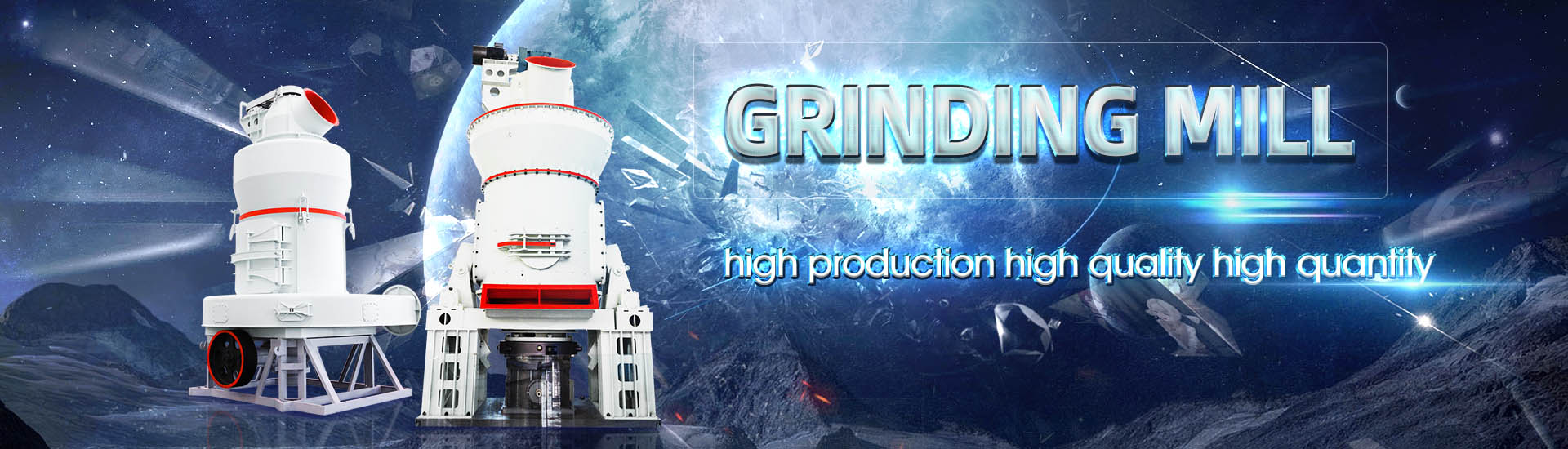
HOME→Closedcircuit raw material mill process flow Closedcircuit raw material mill process flow Closedcircuit raw material mill process flow
Closedcircuit raw material mill process flow Closedcircuit raw material mill process flow Closedcircuit raw material mill process flow
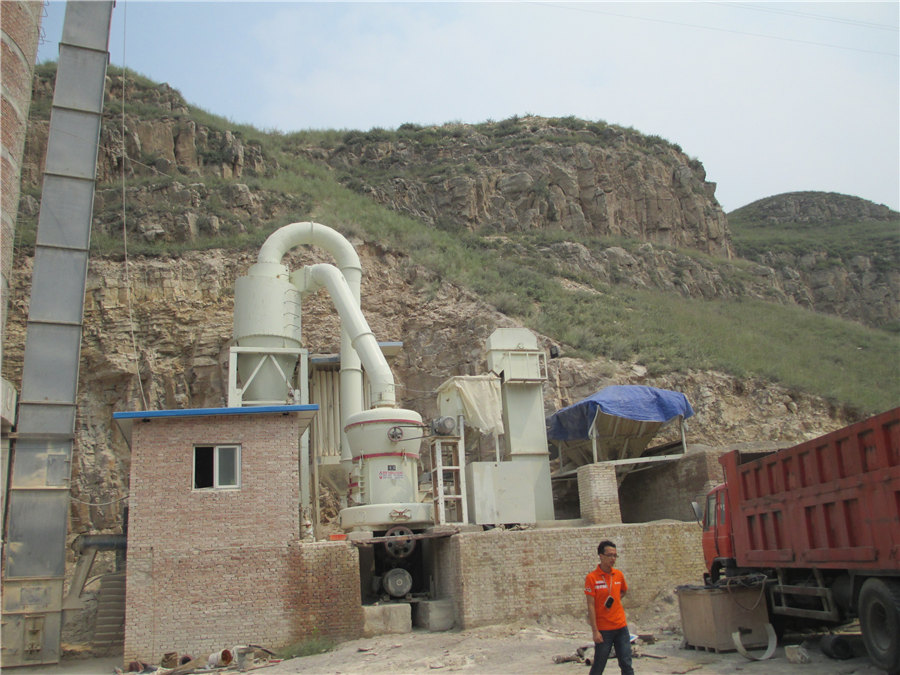
5 MATERIAL FLOW MODELS OF CLOSEDCIRCUIT GRINDING
The macrostructural models describing the material flows in closed circuit ball mill grinding include the rules of mass flow for steadystate, the nonlinear character of the mill, and the dead time 2013年4月1日 Two past approaches, experimental and modelling, for quantifying the effects of classification efficiency and circulating load on the capacity of closed ball mill circuits, are Closed circuit ball mill – Basics revisited ScienceDirectThis paper discusses the designing and implementation of different linear and nonlinear models and its simulation for a closed loop ball mill grinding circuit and advantages of using the non MODELING AND SIMULATION OF A CLOSED LOOP BALL MILL In the demonstrated closed circuit process, the raw materials’ feeding is performed via three weight feeders, feeding first a crusher The crusher outlet goes to the recycle elevator and Modeling of Raw Material Mixing Process in Raw Meal Grinding
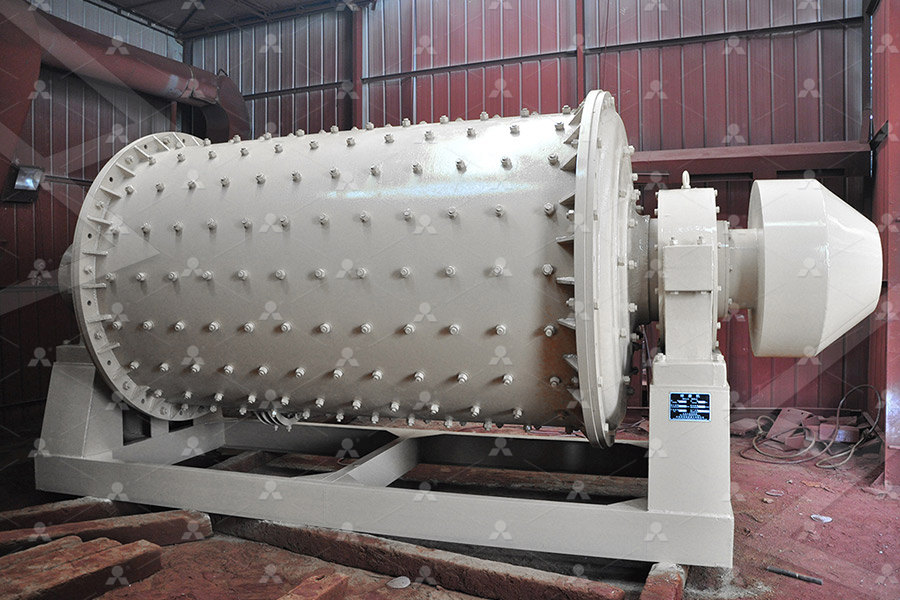
Material Flow Models of ClosedCircuit Grinding SpringerLink
The macrostructural models describing the material flows in closed circuit ball mill grinding include the rules of mass flow for steadystate, the nonlinear character of the mill, and the dead time Some simplified correlations are presented in a few figures which may be useful for designing new system or for improving old system, if data on mill and classifier performances are available In connection to it, a simple method for (PDF) Design of ClosedCircuit Grinding System with Requirements to energy efficiency of the grinding process in a closed circuit ball mill cause the necessity of searching the optimal schemes of grinding As shown by the charts grinding in the Analysis of the efficiency of the grinding process in closed circuit Abstract—This paper presents the development of a nonlinear model predictive controller (NMPC) applied to a closed grinding circuit system in the cement industry A Markov chain Predictive Control of a Closed Grinding Circuit System in Cement
.jpg)
Closed circuit ball mill – Basics revisited Request PDF
2013年4月1日 The ball mill in closed circuit with hydrocyclones is an industry standard, and well known methodologies exist for equipment sizing, selection and design5 MATERIAL FLOW MODELS OF CLOSEDCIRCUIT GRINDING The macrostructural models describing the material flows in closed circuit ball mill grinding include the rules of mass flow for steadystate, the nonlinear character of the mill, and the dead time relating to 5 MATERIAL FLOW MODELS OF CLOSEDCIRCUIT GRINDINGPerformance of a conventional Polysius twocompartment ball mill and a OSepa® high efficiency dynamic air classifier (FLSmidth) closed circuit process was investigated at the steady state Process flow diagram of the primary ROM ball Download scientific diagram Flow chart of raw meal production from publication: Effective Optimization of the Control System for the Cement Raw Meal Mixing Process: IIFlow chart of raw meal production Download
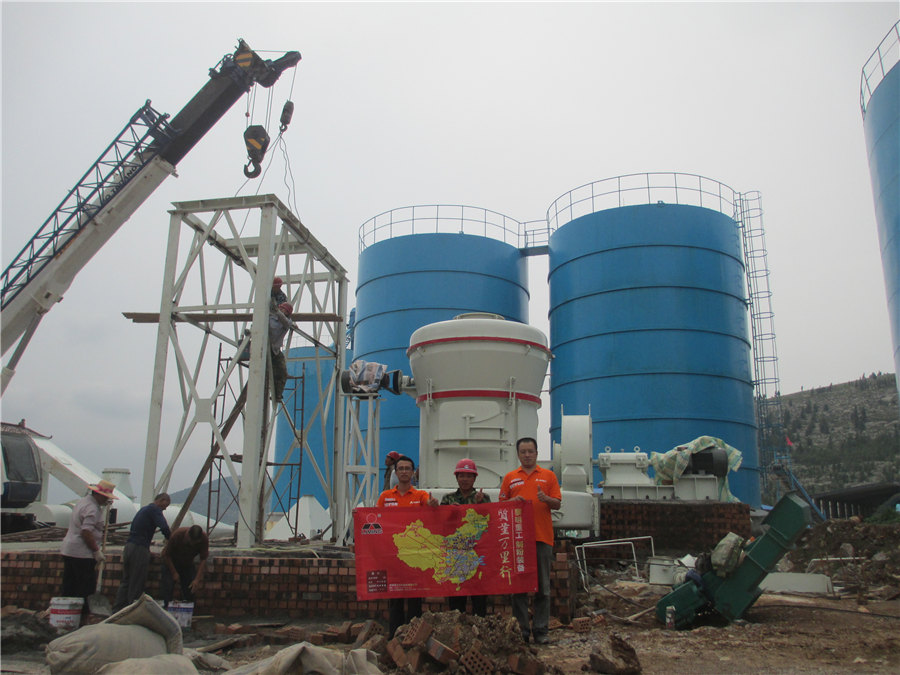
Optimization of A Fully AirSwept Dry Grinding Cement Raw Meal
Optimization of a Fully Airswept Dry Grinding Cement Raw Meal Ball Mill Closed Circuit Capacity With the Aid Free download as PDF File (pdf), Text File (txt) or read online for free This document discusses optimizing the production capacity of a fully airswept industrial scale twocompartment cement ball mill through simulation The mill has two compartments, with the first Part Three: Raw Mill Process of Raw Mill The proportioned raw material is feed first to a grinding mill In the mill, particles ground in to very fine sizes In the grinding unit, drying, grinding and mixing takes place simultaneously Hot gas from clinker burning unit is passed into the grinding unit to assist the drying and grinding processCement Manufacturing Process INFINITY FOR CEMENT EQUIPMENT2016年10月12日 The simplest grinding circuit consists of a ball or rod mill in closed circuit with a classifier; the flow sheet is shown in Fig 25 and the actual layout in 911 Metallurgist is a trusted resource for practical insights, solutions, and support in mineral processing engineering, helping industry professionals succeed with proven expertise Closed Circuit Grinding VS Open Closed Circuit Grinding VS Open Circuit Grinding2010年10月1日 Modeling of Raw Material Mixing Process in The results indicate high parameters uncertainty due to the large number of disturbances during the raw mill In the de monst rated closed circuit (PDF) Modeling of Raw Material Mixing Process in Raw Meal
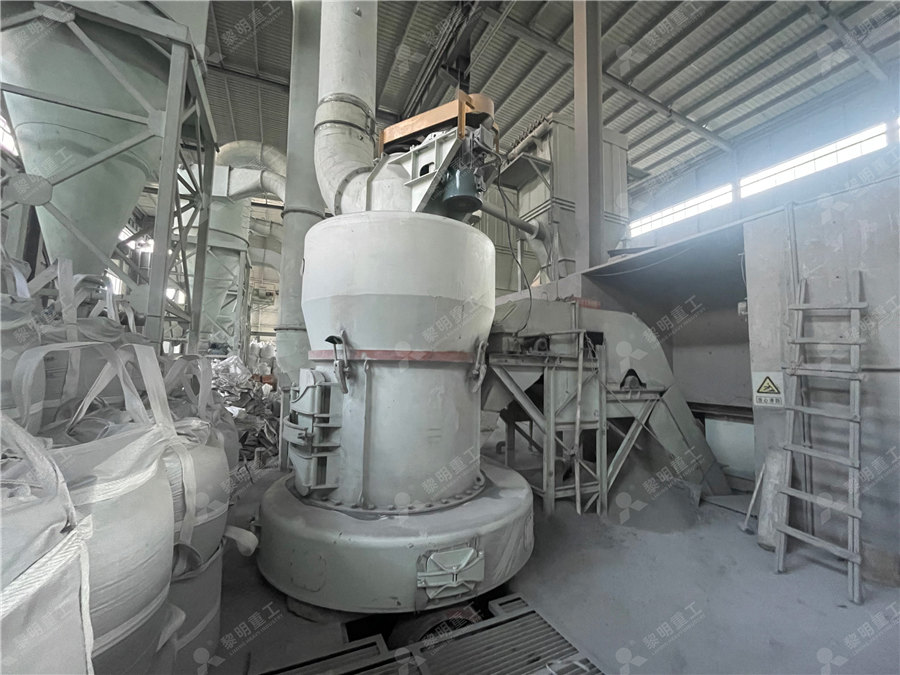
Analysis of the efficiency of the grinding process in closed circuit
2016年1月1日 The purpose of the study is to assess the grinding and classification performance of a conventional Polysius® twocompartment ball mill and a Sepol® dynamic air classifier closed circuit process crushed ore is fed into a SAG/Ball mill circuit with a median size of approximately 12,000 microns Most SAG Mills are operated in closed circuit with a screen The screen fi lters undersized ore, normally minus ½ inch, to a ball mill discharge sump The combined mill discharges are pumped to undergo classifi cation, normally via hydrocyclonesMill Circuit Pump Manual 911 Metallurgist2015年4月1日 Optimization of a fully airswept dry grinding cement raw meal ball mill closed circuit capacity with the aid of simulation The simplified process flowsheet of the sampled circuit with the sampling points is given in Fig 1 probable increase in amount of fine material due to the low air flow rate, Optimization of a fully airswept dry grinding cement raw meal 2013年7月15日 The ball mill in closed circuit with hydrocyclones is an industry standard, recovery should be expected as the leaching process benefits from very fine material sand flow and slumping(PDF) Energy Efficient Ball Mill Circuit – Equipment
.jpg)
EnergyEfficient Technologies in Cement Grinding
2016年10月5日 A raw material moisture of up to 8 % can be dried when utilizing the preheater exit gases only If hot air from an air heater is also supplied, then a raw material moisture of up to 18 % can be handled The power requirement 4 CLOSED CIRCUIT SYETEM WITH A GRINDING MILL CLASSIFIER An example of a toner manufacturing process is shown in Figure 3 A closed circuit system of a classifier and a mechanical mill is employed in this process An effective classification is possible with this system because dispersed particles can be fed to the classifier by the THE IMPROVEMENT OF GRINDING AND USING CLOSED CIRCUIT chute for the BM+RP mill circuit with feed chute truck assembly The designed chute's flow characteristics will be analyzed by using DEM software For designing and analyzing the Roller press circuit Ball mill chute, UMS 46m diameter, RP+BM (Roller press + Ball Mill) Circuit Cement Ball mill feed materials and its properties are takenDESIGN AND ANALYSIS OF BALL MILL INLET CHUTE FORWhenever the kiln is in normal operation and raw mill is stopped, the exhaust gases induced by ID fan are cooled by Gas conditioning tower(GCT) to around 150160oC If both kiln and raw mill are in operation, hot gases are supplied to the raw mill Manufacturing process flow 1 Quarrying and Crushing Messebo
.jpg)
Open and closed circuit dry grinding of cement mill rejects in a
2004年1月14日 Open and closed circuit dry grinding of cement mill rejects in a pilot There are many studies about grinding process including those on the effect of farine size distribution of raw material on pyroprocessing, melting about 26% of the total electrical power is used in grinding the raw materials During grinding process, Portland clinker is the main constituent of most cements In Portland cement, a little calcium sulfate (typically 310%) is added in order to retard the hydration of tricalcium aluminateThe calcium sulfate may consist of natural gypsum, anhydrite, or synthetic wastes such as fluegas desulfurization gypsum In addition, up to 5% calcium carbonate and up to 1% of other Cement mill WikipediaFigure 2335 Schematic diagram, showing the preparation and flow of samples in the raw meal control process It may be mentioned that Xray fluorescence (XRF) spectrometers are the preferred analytical tools in plant laboratories Normally the simultaneous spectrometer is used for its simplicity, speed, and reliabilityEverything you need to know about cement Materials Preparation and Raw 2013年4月1日 The reference point is a conventional ball mill circuit in closed circuit with cyclones operating at 250% circulating load and having 38% of fine material reporting to cyclone underflow, resulting in a classification efficiency of 50% ThisClosed circuit ball mill – Basics revisited ScienceDirect
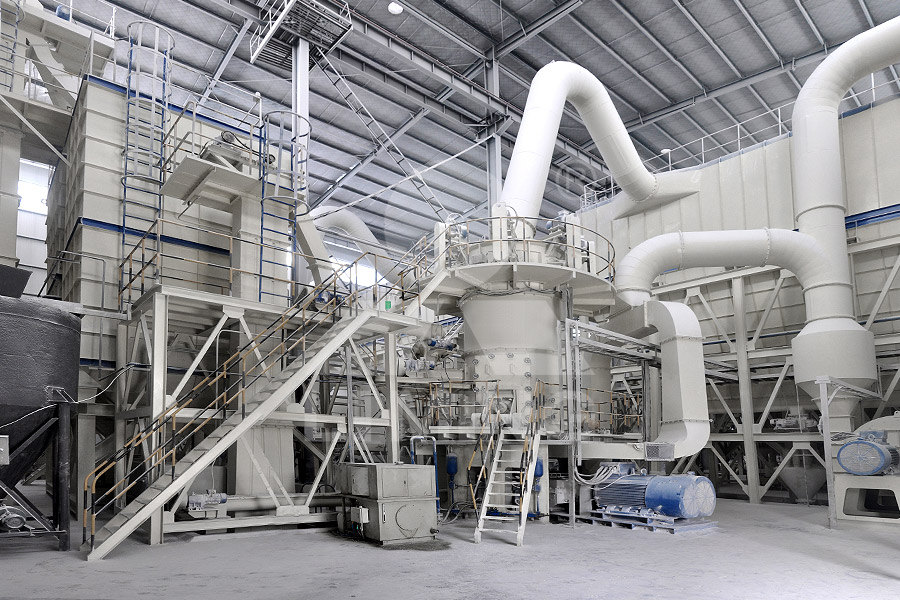
Circulating load calculation in mineral processing closed circuit
2013年1月1日 A problem for solving mass balances in mineral processing plants is the calculation of circulating load in closed circuits A family of possible methods to the resolution of this calculation is the iterative methods, consisting of a finite loop where each iteration the initial solution is refined in order to move closer to the exact solution2021年3月15日 Although there are already some scientific publications on this type of mill, the dry stirred media mill is not yet sufficiently understood For example, Altun et al investigated the influence of process parameters (Altun et al, 2013) and mill geometry (Altun et al, 2014) on the comminution of cement clinker in a horizontal, dry stirred media parison of open and closed circuit mode using a dry 2016年3月21日 To estimate the circulating loads in and the efficiency of each of the two classifiers operating in closed circuit with a ball mill: Original feed may be applied at the ball mill or the primary classifier T—Tons of original feed Common Basic Formulas for Mineral Processing 2015年6月19日 The basic parameters used in ball mill design (power calculations), rod mill or any tumbling mill sizing are; material to be ground, characteristics, Bond Work Index, bulk density, specific density, desired mill Ball Mill Design/Power Calculation 911Metallurgist
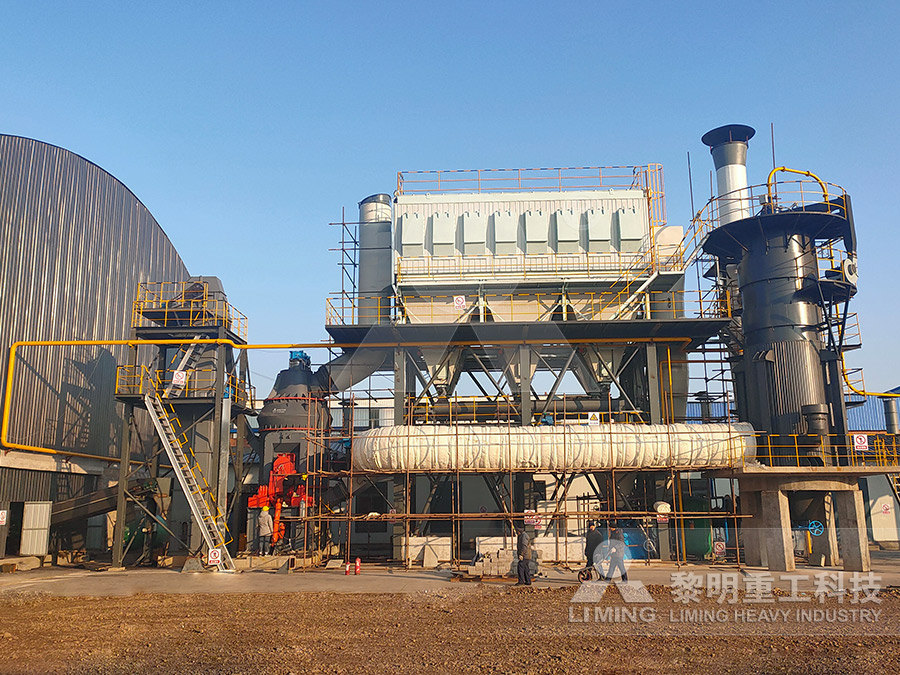
(PDF) Supplementary Relationship between Circulating Load and
2023年8月15日 Particle size characteristics of each product in the closed circuit ball mill system of the size requirements into the next process, flow of the coarse material in the mi ll discharge 2005年2月1日 A raw material grinding circuit was modeled using plant data Samples were collected from around the circuit and, following a crash stop, from inside the millModeling and simulation of a fully air swept ball mill in a raw This paper presents results regarding the grinding behaviour of two batches of material (clinker) in a ball mill with its own twostep grinding process: the first one with a ball load, the second Closed circuit milling flowsheet Download Scientific DiagramSince the plug flow assumption is reasonable for industrial tube mills, Equation 9 is usable for opencircuit grinding; The equations derived from the comminution kinetics and material balances for a closedcircuit grinding system with a lionideal classifier are developed, and a method for designing practical systems is proposed(PDF) Design of ClosedCircuit Grinding System with Tube Mill
.jpg)
AMIT 135: Lesson 6 Grinding Circuit – Mining Mill Operator
SAG Mill Circuit Example — Gold Processing SAG mill circuit example for gold processing [image: (13563)] AG/SAG Mill AG/SAG mills are normally used to grind runoffmine ore or primary crusher product Wet grinding in an AG/SAG mill is accomplished in a slurry of 50 to 80 percent solids 2D and 3D simulations of particles in a SAG Mill2018年4月23日 An industrial ball mill operating in closed–circuit with hydrocyclones was studied by five sampling surveys The aim of the present study was to optimise operating parameters (ie charge volume A Survey on Troubleshooting of ClosedCircuit Grinding System2004年1月14日 Based on the statistics of the electricity consumption of the raw material mill system of 1005 production lines in China between 2014 and 2019, it is found that the average electricity consumption Open and Closed Circuit Dry Grinding of Cement Mill Rejects in a Raw material grinding has the objective of producing a homogeneous raw meal with a fineness requirement (less than 10 to 15% residue on the 90μm sieve) from a raw material containing moisture (3 to 8%) with a feed particle size of 100–200 mm Usually, silos after the grinding mill are used for a final homogenisation of the raw mealGrinding Circuit an overview ScienceDirect Topics
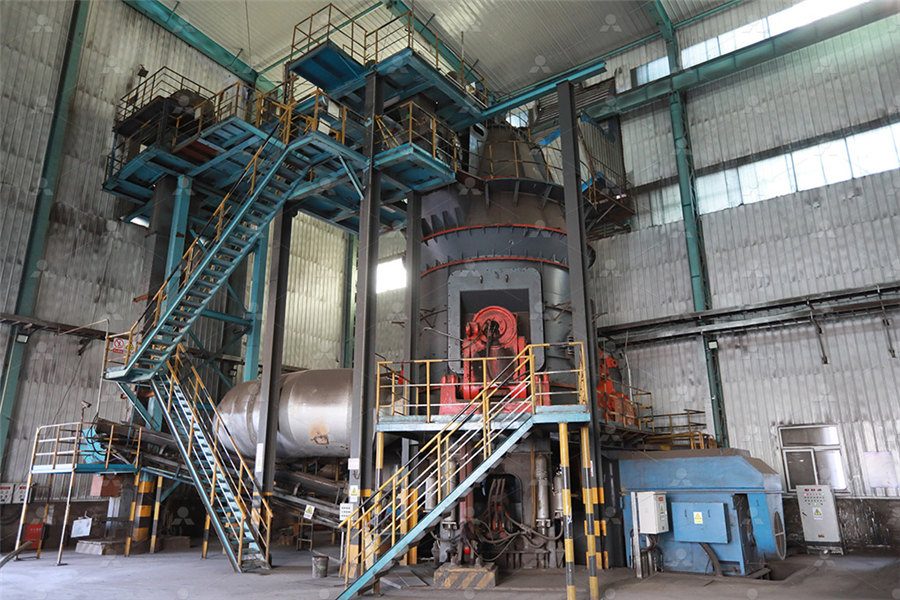
Flow chart of the grinding and blending process
The flow chart of the investigated closed circuit process is shown inFigure 1 of [8], including three raw materials feeders The mill exit stream is fed to a homogenizing silo connected in series 2014年11月1日 Request PDF Modelling and simulation of raw material blending process in cement raw mix milling installations A series of multivariable models composed from linear differential equations Modelling and simulation of raw material blending process in cement raw 2015年7月28日 Simple “Open Circuit” 1 Ball Mill Grinding Circuit/Flowsheet Our second flow sheet, Simple 1 “Closed Circuit” Ball Mill with Cyclone Grinding Circuit/Flowsheet The material that has not been ground enough will be sent back to the mill for regrinding The material that is ready for the next phase of processing will Simple Grinding Circuits Flowsheets 911MetallurgistFigure 82 shows a flow sheet where the rod mill is in open circuit and the ball mill is in closed circuit with a classifier This is a normal setup as the primary function of a rod mill is to provide a uniform sized feed to the ball mill Figure 83 shows that the rod mill product is classified and a more uniform feed size is, therefore, discharged to the ball mill whose primary function is OpenCircuit Mill an overview ScienceDirect Topics
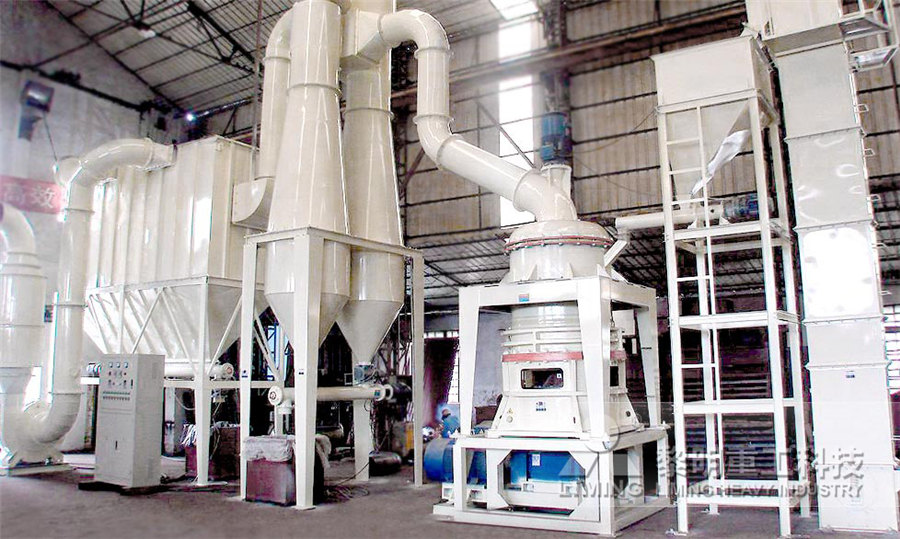
Crushing Plant Flowsheet DesignLayout 911Metallurgist
2016年3月11日 In the majority of cases, the last crushing stage is closed circuited using anywhere from 10MM (3/8″) square to 14MM (9/16″) slotted openings on the sizing deck In some copper concentrators, the mill feed is all passing 13MM(½”), using three stages of crushing and 14MM (9/16″) square openings on the closed circuit screens2016年6月6日 Adding pebble crushing as a unit operation is the most common variant to closedcircuit AG/SAG milling (instead of direct recycle of oversize material ) more competent material consumes mill volume and limits throughput including total mill volumetric flow rate; recirculating load Feed Chute Design Discharge Diaphram DesignSAG Mill Grinding Circuit Design 911Metallurgist;as can be seen in the process and Quality flow diagram below; 1 Quarrying and Crushing 2 Raw material Storage and Transportation 3 Proportioning 4 Raw material Grinding and Transportation 5 Raw meal storage, homogenization and Kiln feeding 6 Pyroprocessing (Raw meal preheating, calcination Clinkerization, clinker cooling,CEMENT PRODUCTION AND QUALITY CONTROL A Cement manufacturing Process2020年12月3日 Closedcircuit mill feed includes, it has been assumed that the ground material is brittle 1 Investigating the efficiency of closedcircuit ball mill from process mineralogy perspective A process mineralogy approach to study the efficiency of
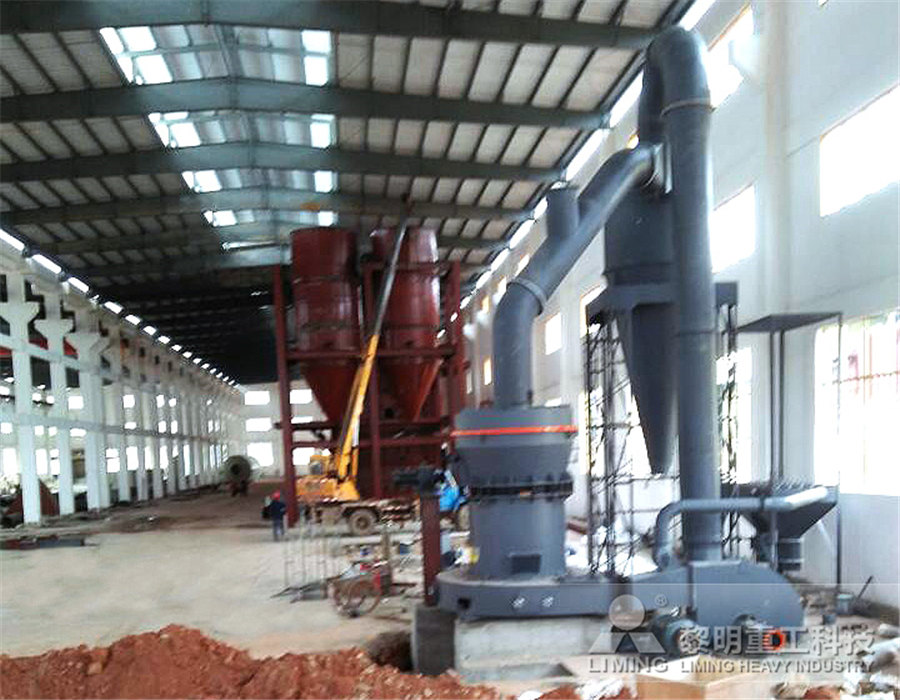
Optimization of a fully airswept dry grinding cement raw meal
2015年4月1日 The paper focusses on improving the energy utilization of a cement grinding circuit by changing the flow sheet of the process The circuit was comprised of ball mill, static classifier and dynamic