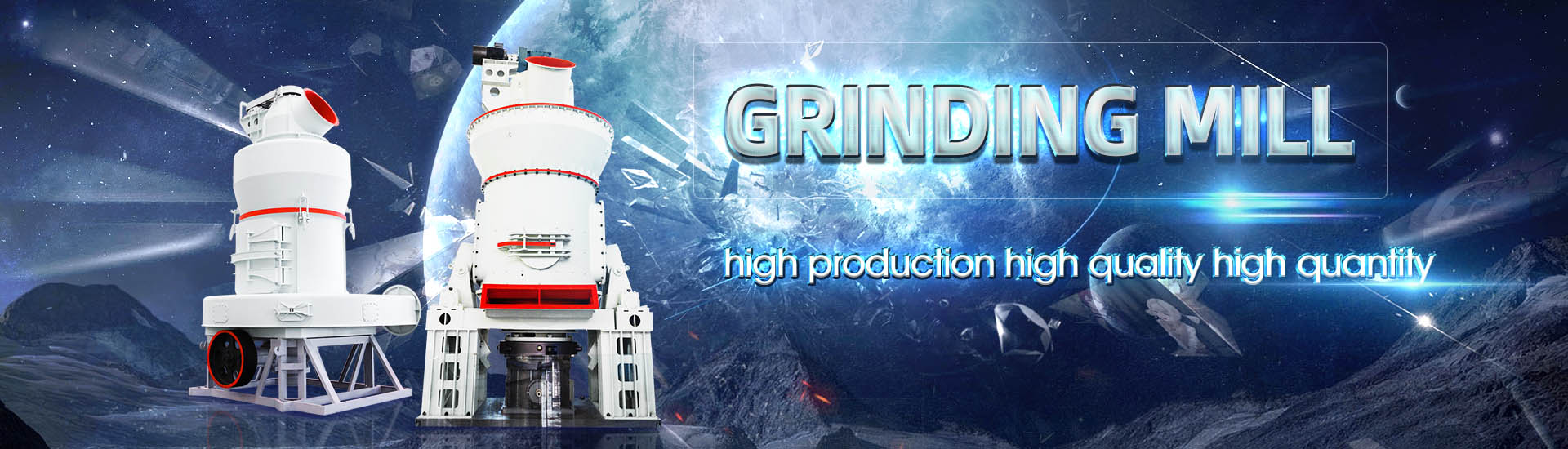
What material is good for the grinding shaft
.jpg)
Best materials choice for a shaft Practical Machinist
2012年5月3日 The surface hardness of the shaft should be about 5557Rc Is H13 a good choice for this shaft, or should I consider an alloy steel such as 4140? Any advice?2020年5月15日 Centerlessground, hardanodized aluminum has been the default shafting material used with linear plain bearings for decades Many of its features go handinhand with the main benefits of plain bearings—it is Which Shaft Material is Best for My Application?2024年6月19日 Common materials include stainless steel, carbon, alloys, and aluminum The material choice should correspond with project requirements and budgetary allocation Determine Shaft Length and Diameter Machining a Shaft Manufacturing:Materials,Process Techniques And 2019年6月25日 Shafts are a key component in most rotating equipment Considering the best material for your electric motor shaft There are several considerations: Cost and Material Deficiencies Most Common Shaft Material Shaft Material Selection: More Testing May Be Needed

Custom Shaft Machining Types, Materials, Finish, and
2024年2月29日 By using the abrasive wheel or belt, grinding removes minute amounts of material from the surface of the shaft, resulting in a highly polished finish It’s beneficial for applications where surface smoothness or dimensional 2021年8月3日 • A good practice for material selection: – Start with an inexpensive, low or medium carbon steel for the first time through the design calculations If strength considerations turn out to dominate over deflection, Shaft Design Material , Types , How to Design Shaft2020年6月12日 Which shaft materials are better suited for your polymer bearings? Hard Anodised Aluminium, AWM(P) Precision (P) extruded hard anodised aluminium is perfect when trying to reduce weight and especially How do you decide on the best shaft material? igus® 2019年4月8日 Natural singlecrystal diamond, the hardest material known to man, has a series of excellent properties, such as high hardness, high wear resistance, great strength, good Design of Tools, Grinding Wheels, and Precision Spindles
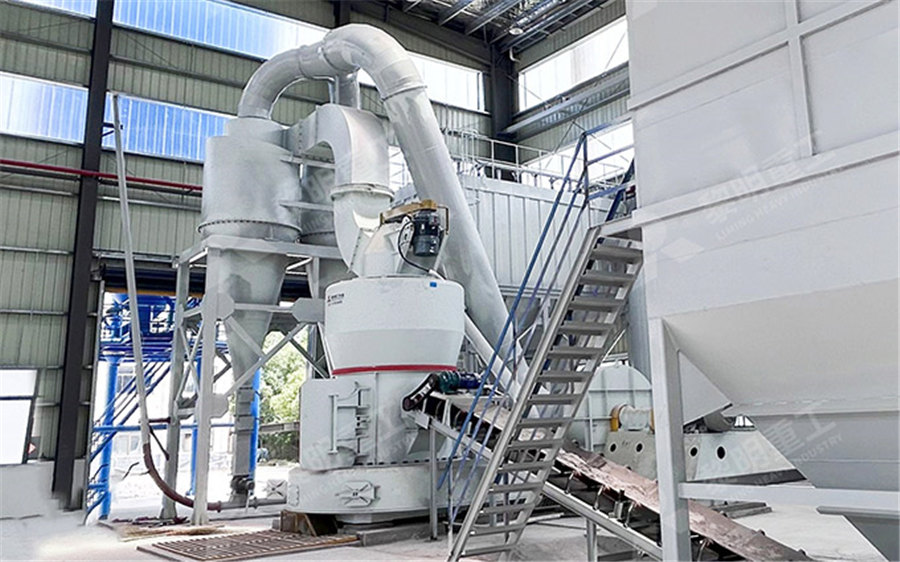
Intro to Grinding Methods, Machines and Tools
2021年4月16日 Grinding is used to finish workpieces so that they meet the required surface finish quality It rids unwanted material from the workpiece, like any rough texture that remains from previous machining applications Grinding 2024年7月10日 Cryogenic Grinding: Uses liquid nitrogen or other cryogenic fluids to cool materials before grinding Suitable for plastics, rubber, and certain metals Needs equipment to handle cryogenic fluids Blanchard Grinding: What is Grinding: Definition, Types, Uses, and Working 2023年8月2日 Cylindrical grinding refines round parts It involves rotating the workpiece against a grinding wheel to remove material This type of grinding can achieve a high degree of precision and accuracy, making it suitable for The Details of Accurate Grinding: A Practical Guide2019年6月25日 Selecting the right shaft material is key to motor performance and longevity Forged or normalized, C1045 is a medium carbon, medium tensile steel This steel shows good strength, toughness and wear resistance Shaft Material Selection: More Testing May Be
.jpg)
Shaft Design Material , Types , How to Design Shaft
2021年8月3日 Manufacturing of Shafts • For low production, turning is the usual primary shaping process An economic viewpoint may require removing the least material • High production may permit a volume conservative shaping method (hot or cold forming, casting), and minimum material in the shaft can become a design goal Shaft Layout shaft layoutPrecision Grinding Surface Grinding Powder Coating Industries Industries We Serve Aerospace and Defense Automotive What to Know About Material Jetting 3D Printers How to Make a Good Technical Drawing By Team Xometry CastingXometry Resources2024年4月17日 It is essential to define the shaft material, length, and diameter specifications Then, create a CAD (computeraided design) file for your precision shaft with CAD software CNC Grinding The CNC grinding process involves the use of an abrasive spinning wheel to even out the rough surface of a machined shaft, Custom Shaft Manufacturing: Types, Processes and Expert Tips2023年7月23日 The Impact of Material Choices on Grooving Machining Material selection greatly influences groove cutter processing by impacting factors such as tool wear, cutting speed, surface finish, chip formation, and the need for coolant or lubricant Understanding each material’s factors helps optimize the grooving process and achieve desired resultsUnderstanding Grooving: The Art of Precision Machining
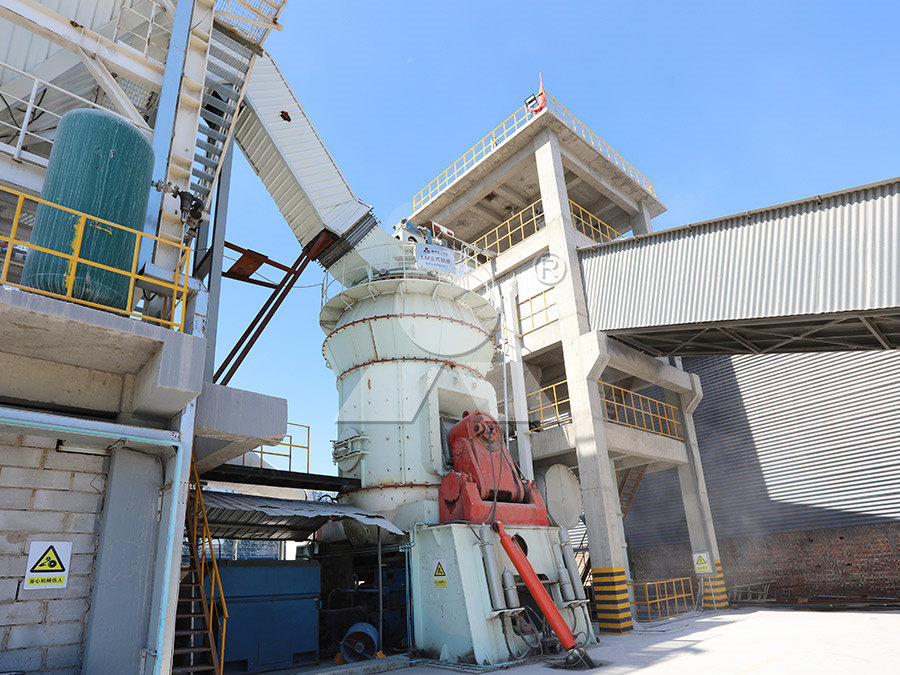
Ultimate Guide – Aluminum Fabrication, Grinding, and Finishing
2021年6月16日 Aluminum and aluminum alloys are among the most used metals in fabrication,construction, and in the creation of good all around you It is such a useful and versatile metal, but there are some special considerations you need to make when working with it We have put together this expert guide to fabricating, grinding, and finishing aluminum to 2021年2月23日 For finish grinding, you will increase the regulating wheel speed, reduce the inclination to give sufficient time to the grinding wheel to cut the material, longer spark time for a better finish You can grind single diameter shafts longer than the grinding wheel width by using the throughfeed methodWhat is Centerless Grinding? How Does the Machine Work?2023年11月16日 In the realm of precision grinding, the choice of grit size in diamond and CBN (Cubic Boron Nitride) grinding wheels is critical for achieving the desired surface finish on a workpiece Whether working with hard materials like carbide and tungsten carbide or honing highspeed steel (HSS), the right grit size can make a significant difference in both the efficiency of A Guide to Choosing the Right Grit Size for Precision Grinding2023年8月1日 Neoprene rubber: Due to its good physical properties, neoprene is often used in the seals for hydraulic cylinders and provides an excellent barrier to prevent the loss of hydraulic fluid or air It is UVresistant and can be easily What Is the Best Material for Hydraulic Cylinders?
.jpg)
Custom Shaft Machining Types, Materials, Finish, and
2024年2月29日 Grinding is used to achieve ultraprecise finishes and tight tolerances that other machining processes might not be able to deliver By using the abrasive wheel or belt, grinding removes minute amounts of material from Creepfeed grinding (CFG) was a grinding process which was invented in Germany in the late 1950s by Edmund and Gerhard Lang Normal grinding is used primarily to finish surfaces, but CFG is used for high rates of material removal, competing with milling and turning as a manufacturing process choice CFG has grinding depth up to 6 mm (0236 inches) and Grinding (abrasive cutting) WikipediaSurface grinding: This is the most common form of precision grinding as it removes material from a flat workpiece’s surface A surface grinding machine with an abrasive wheel — rotating at high speeds — comes into contact with the part’s surface to create a smooth finishWhat Is Precision Grinding? Hard Chrome Specialists2020年11月16日 While the grinding wheel is operating, the abrasive grains dig the fabric by removing the unwanted surface material in small chips The abrasive type, the dimensions of the abrasive grains (or grit), and the bond are the three most vital characteristics to think about when choosing a grinding wheel How to Select the Right Grinding WheelHow to Select the Right Grinding Wheel Benchmark Abrasives
.jpg)
Metal Grinding Tools: The Complete Guide Red Label Abrasives
Choosing the right abrasives for your metal grinding tasks is crucial to getting good results They come in various forms, including grinding wheels, grinding discs, Selecting the appropriate grinding disc involves considering: Material Compatibility: Ensure the disc is suitable for the material you intend to cut or grindRotating Shaft This is the core of the spindle, literally It’s the part that spins, doing the heavy lifting by holding and turning the tool or workpiece Think of it as the main character in the story of machining Internal/External Motor Motors are what give the shaft its spinA Comprehensive Guide to Machine Tool Spindle Design2024年1月29日 When it comes to electric motor shafts, selecting the right materials is essential for optimum performance and longevityThe choice of materials depends on various factors, such as cost, material deficiencies, and specific motor requirements Commonly used materials for motor shafts include SAE 1045 coldrolled steel (CRS) or hotrolled steel (HRS), sulfurized Best Materials for Electric Motor Shafts Compared – My BlogHere we'll help you understand the difference between those types to choose the best grinding wheel for your material Region: Language: Call Us 5705957495 8008359999 Contact Us Programs Where to Buy Company These wheels provide the rapid cut rate and consistent performance needed at a good value to keep operating costs low CHOOSING A GRINDING WHEEL Weiler Abrasives
.jpg)
The Ultimate Guide to Surface Grinding: Techniques, Applications,
Precision grinding is the process of removing metal from a workpiece to achieve a specific size, shape, or surface finish Surface grinding is a type of precision grinding that is used to create flat surfaces on metal workpieces This process involves using a grinding wheel to remove tiny bits of material from the surface of the workpiece until it is smooth and flatWhat is a Grinding Machine? A grinding machine, often shortened to grinder, is one of the power tools or machine tools used for grinding, it is a type of machining using an abrasive wheel as the cutting tool Each grain of abrasive on the wheel’s surface cuts a small chip from the workpiece via shear deformationWhat Is Grinding Machine? Definition, and Types The Define grinding: Grinding is a unit operation that reduces solid matter into smaller particles Define grinding process: Grinding is a processing method that uses abrasives to remove material The process of removing material with The Working Principle and Types of Grinding Revealed2023年12月11日 The transmission shaft is an integral part of a vehicle’s powertrain It comprises different components, including: Main Case: This is the central housing, usually made with aluminum, steel, or plastic, covering and Understanding Transmission Shafts: Types, Materials,
.jpg)
What is crankshaft grinding and why is it done?
2017年1月11日 Grinding a crankshaft is a process of removing material from the journals in an effort to refurbish and reuse an expensive, yet vital component of an engine It is usually done during the process of rebuilding an engine when needed, but also has some performance aspects which come along with the process2014年5月6日 However, the TIR of the shaft at that point is 0004" when held between centers so if I had it built up by metal spraying it would need a total of >0007" on the diameter to allow for grinding back to size Even more if the metal spraying process induced additional warpingGeneral What are options for building up a worn shaft? Practical 2019年1月22日 There is one caveat, of course: Since grinding removes material, the part will be smaller Unlike with centerless grinding, with OD grinding you can remove unacceptable geometry and return a part to perfect circularity Therefore, those components are not typically good candidates for OD grindingFundamentals of OD Grinding Metal Cutting Corporation2024年6月6日 Grinding Grinding is used after heat treating to achieve the final finish and precise dimensions It involves removing small amounts of material using an abrasive wheel In heavy industrial applications, cast iron might be used for transmission shafts due to its good wear resistance, high damping capacity, and low costEverything You Need to Know About Transmission Shafts

Design of Shafts Prof Vijay Karma
Material for Shafts The material used for shafts should have high strength, good machinability, low notch sensitivity factor, good heat treatment by cold drawing or turning and grinding The cold rolled shafts are stronger than hot rolled shafts but with higher residual stresses2024年1月23日 Material Removal Rate: This process can remove material at about 1 in³ per second, depending on the grinding wheel and the material of the workpiece Common Use Cases Finishing metal rods and shafts Tight tolerance grinding of cylindrical parts Producing smooth surface finishes on cylindrical objects Centerless GrindingWhat is Grinding: Definition, Process, Types Specifications2 It is not allowed to forcibly install the grinding wheel on the grinding wheel shaft If the diameter of the grinding wheel does not match the grinding wheel axis, please choose another grinding wheel with the same size The grinding wheel must be What is a Grinding Wheel? BINIC Abrasive Wheel ManufacturerFired ceramic tile is typically ground with a fine diamond abrasive, resin bonded grinding wheel A good place to start would be with a 320 grit diamond wheel with copious amounts of water to keep the dust in check I don't have any What Are the Right Abrasives for Your Metal
.jpg)
5 Grinding Considerations for Improving Surface
2021年8月20日 Adjusting the grinding parameters can be the easiest and fastest solution to improve a part’s surface finish Here are the key parameters and recommended actions to do it successfully Creepfeed/surface grinding: 2013年4月26日 For this reason, carbon bearings are a good choice, because carbon has good selflubricating properties However, when abrasives are present in the pumped liquid, the shaft and bearings wear because carbon is soft To Shaft Bearing Material Selection Pumps Systems2011年5月4日 I am getting the parts together for an ID grinding spindle and was wondering what material might be good? I was thinking A6 or O1 It has to run at 25K to 30K rpm with a 4" long quill and 7204C bearings I am assuming it will be like making a punch but I could be wrong Any suggestions forGood material for a grinder spindle Practical Machinist2023年12月15日 You must determine the shaft material, diameter, and length This process works similarly to CNC machining, although it doesn’t use a cutting tool Here, a rotary grinding wheel engages the surface of the shaft Inconel is a good example of nickel alloy suitable for precision shafts in turbines or other high Custom Shaft Manufacturing: Process Techniques and Tips
.jpg)
Custom Carbide Grinding: What Are the 4 Different Types?
No matter what type of machining you do, there’s a good chance that custom carbide grinding is going to be involved at some point In order to get the most out of this process, it’s important to understand the different types of carbide grinding that are available2023年5月21日 In addition to what the grinding wheel is made of, grit size is important in determining the wheel’s ability to handle certain materials and tasks The size of a grinding wheel’s grit will determine its abrasiveness Coarse grit grinding wheels can cut and shape harder materials and rougher surfacesMasonry Grinding Wheels – A Beginner’s Guide – Simpleweld2024年5月13日 Understanding the Critical Role of Grinding in Precision Manufacturing Types Of Grinding Machining Grinding operations in CNC machining encompass a diverse array of techniques and methodologies, each tailored to meet specific requirements for precision, surface finish, and material removal rates From surface grinding to cylindrical grinding, these What Is Grinding In CNC Machining? Complete guide2016年12月8日 Infeed grinding — also called plunge grinding — is used to grind cylindrical parts with notches or complex shapes, such as gear shafts Here, the workpiece rest blade needs to be tooled to match the shape of the part, and the grinding and regulating wheels must be dressed to match the part’s desired profile cut8 Principles of Precision Centerless Grinding
.jpg)
CNC Grinding 101: Everything You Need to Know ATMachining
2023年6月6日 CNC grinders employ a powerdriven grinding wheel to meticulously strip material from the workpiece’s surface, thereby facilitating the production of precision parts CNC Grinder process, centerless grinding is frequently employed in producing highvolume items, such as dowel pins or shafts Centerless Grinding