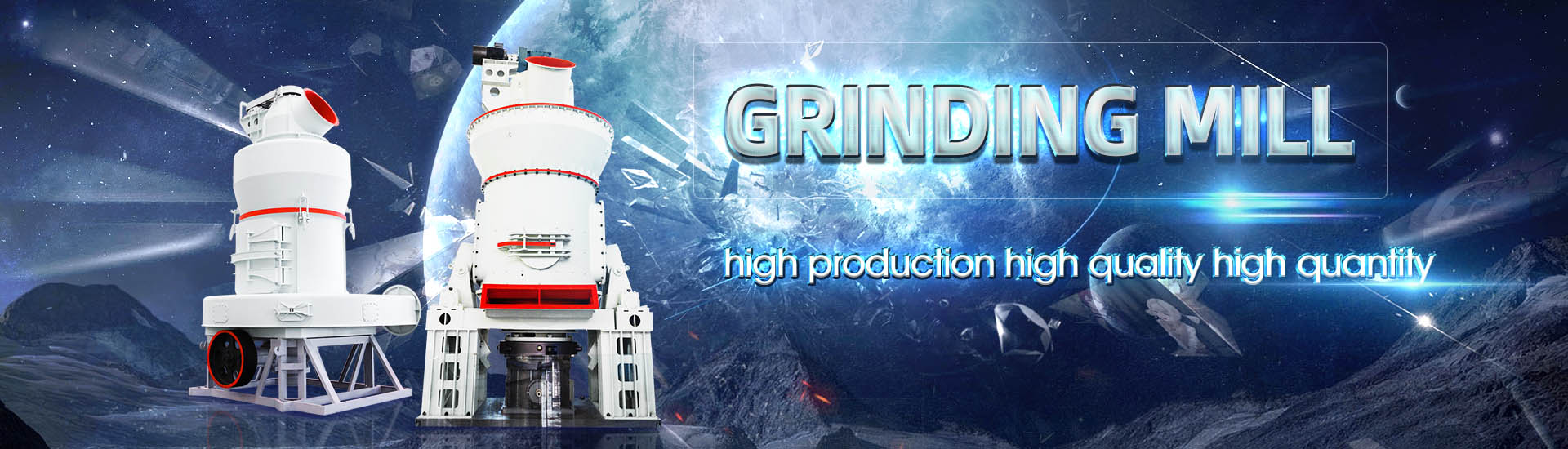
What is the main secondary crushing of large ore rocks
.jpg)
The Complete Guide to Primary Crushing, Secondary Crushing,
Primary crushing is the first stage in the comminution process and involves breaking down large rocks into smaller pieces of a size that can be handled by the downstream machinery 展开The stone that is too large to pass through the top deck of the scalping screen is processed in the secondary crusher Cone crushers are commonly used for secondary crushing (although 11192 Crushed Stone Processing and Pulverized Mineral Processing2023年2月28日 Primary crushers typically have a larger crushing ratio, meaning that they can reduce large rocks or ores to a more manageable size in a single pass Secondary crushers, however, have a smaller crushing ratio, meaning Primary vs Secondary Crushers: Understanding the 2023年7月22日 Ore crushing is the process of breaking, splitting, extrusion, impacting, and grinding of large solid ore with external force to reduce the particle size of large ore materials Ore Crushing SpringerLink
.jpg)
Crushing Plant an overview ScienceDirect Topics
In threestage circuits, ore is reclaimed from ore storage with secondary crushing product typically ranging from 37–50 cm, and tertiary crushing further reducing the ore to ca 05–2 cm in 2023年2月28日 Crushers play a crucial role in the mining and construction industry, as they are used to break down large rocks and stones into smaller particles, making them easier to transport and use The two primary types of Primary Crusher vs Secondary Crusher: Understanding 2015年7月25日 Almost all secondary and tertiary crushing circuits use the same type of crusher, the cone crusher Within a secondary and tertiary crushing circuit there are three main types of machinery, CONVEYORS, CRUSHERS, and Secondary Tertiary Crushing Circuits 911MetallurgistPrimary crushing and secondary crushing are stages in the mining and quarrying process where large pieces of ore or rock are broken down into smaller, more manageable sizes Primary What is primary crushing and secondary crushing?

Secondary Crushing SpringerLink
In primary crushing the largest lumps of ore mined must be dealt with In secondary crushing the maximum sized piece is unlikely to exceed 6″ in average diameter and some of the unwanted Roll crushers are generally not used as primary crushers for hard ores Even for softer ores, like chalcocite and chalcopyrite they have been used as secondary crushers Choke feeding is not Crusher an overview ScienceDirect Topics2024年7月17日 Crushing is a multistage process that includes primary crushing, secondary crushing, and tertiary crushing Different types of crushing equipment are used at each stage to meet various crushing requirements Types of Crushers: Choosing the Right One for Each 2023年2月28日 There are many examples of successful primary and secondary crusher applications in various industries In the mining industry, for example, primary crushers are often used to reduce the size of large rocks or ores for Primary vs Secondary Crushers: Understanding the
.jpg)
Factors affecting the performance of crushing plant
2014年1月1日 To achieve optimal performance of a crushing plant, not only the design of the individual machines but also the cost of running them should be taken into accountIn this paper a novel method for Primary crushing: The first crushing phase usually uses jaw crushers, which work by compressing large rocks between two steel jaws until they break into smaller pieces This stage focuses mostly on turning larger rocks into smaller, more manageable pieces for easier crushing later onRock Crushing 101: A Beginner's Guide Senya Crushers2023年4月11日 Crushing and Grinding: Copper ore is typically mined as large rocks or ores, which need to be crushed and ground into smaller particles for further processing Crushing and grinding are carried out to break down the ore into smaller pieces, which increases the surface area and exposes the copper minerals for subsequent processingCopper (Cu) Ore Minerals, Occurrence » Geology Science2016年1月17日 In mineral processing, the reduction of minerals by crushing and grinding may be regarded as having one or other of two main objectives: the attainment of a size appropriate for the direct industrial application of the mineral, eg barytes, sand, aggregate; or the release of metallic or ore inclusions from an unwanted matrix with a view to maximum separationCrushing Mineral Processing 911Metallurgist
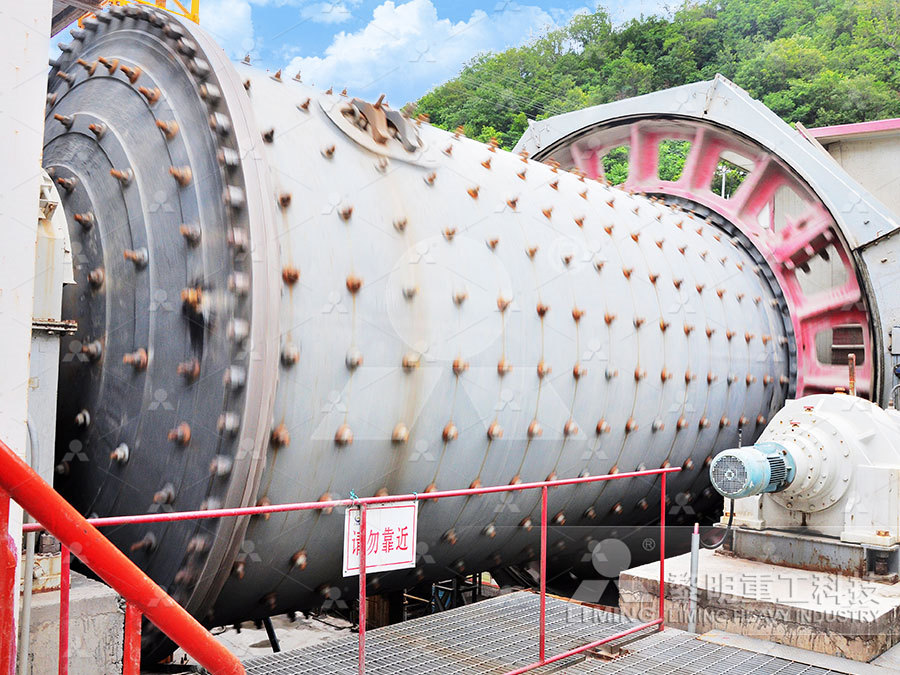
What Is A Jaw Crusher MEKA
This is the second stage of crushing Feed size, which is around 150 to 300 mm, of the rock or ore from the primary crushing process is reduced to between 50 and 80 mm Tertiary Crushing This is the third stage of crushing The size, which is around 50–80 mm, of the ore or rock from the secondary crushing process is reduced to between 5 and In the mining and minerals industry, crushing is a crucial process for breaking down large ore chunks into smaller, manageable sizes The primary and secondary crushing stages are essential for efficient processing and extraction Here’s an overview of the solutions used for both:Crushing Explained Gold Rock ProjectsThis pressure breaks up the rocks until they are small enough to pass through the jaw box The distance between the jaw plates can be made smaller or larger depending on the size of the material you want to process When used as a primary crusher, the main aim is to get the rocks to a size that the secondary crusher can crush with easeWhat is a Primary Crusher? Machinery Partner2020年12月17日 Mechanized crushing has existed for 150 years Despite the fine differences between the equipment, at the end, they all have the same objective: to reduce the size of rocks and, of course, to supply the market with products as varied as gravel for construction or iron ore for the steel sectorCrushing 101 – Different types of crushers for distinctive needs
.jpg)
Crusher Rock: Exploring the Types of Rock Crushers
2024年6月28日 They are responsible for breaking down large rocks into smaller, more manageable pieces for different applications There are two main groups of rock crushers: compressive crushers, which include primary crushers used in 2023年1月16日 Crushing helps to reduce the size of mined material, making it easier to process and transport Rock crushers come in three main types: primary, secondary, and tertiary crushers Primary Rock Crushing; Primary Types Of Rock Crushers And When To Use ThemA moving inner member and fixed outer crusher piece make crushing operations possible You can find rollerbearing and shafttype cone crushers with similar functions Generally, the main difference between the two types is a rotating Choosing the Right Crusher: Types, Features2024年2月5日 Primary Crushing: To reduce large and bulky materials to a manageable size Jaw Crusher: 500 mm to 800 mm: Reduced to about 125 mm to 150 mm Large chunks of material are fed into the jaw crusher where strong compressive forces break them down Secondary Crushing: To refine the size of the materials from the primary crushing stage Cone How Does a Jaw Crusher Work? A Simple Guide JXSC

Gyratory Crusher vs Cone Crusher: What's the Difference?
2023年2月23日 When it comes to crushing equipment in the mining industry, two popular options are gyratory crushers and cone crushers While both types of crushers are designed to crush rock and other materials, there are significant differences between them In this article, we'll explore the key differences between gyratory crushers and cone crushers, as well as their Primary crushing operations could be declared as the main size reduction process of relatively huge rock blocks Following that, industrial rock aggregates are manufacturedCOMPARISON OF SECONDARY CRUSHING OPERATIONS 2021年7月6日 Ore deposit is the gathering of ore where ore is defined as a rock or sediment which contains sufficiently high levels of minerals that can be profitably minution a Heart of Mineral Processing ResearchGate2021年3月25日 Primary crushers reduce large runofmine material, such as rocks and ore lumps, into smaller sizes for further processing downstream, whether that be transport to additional crushers or to a wet processing plantWhat Type of Crusher Is Best for Primary Crushing? McLanahan
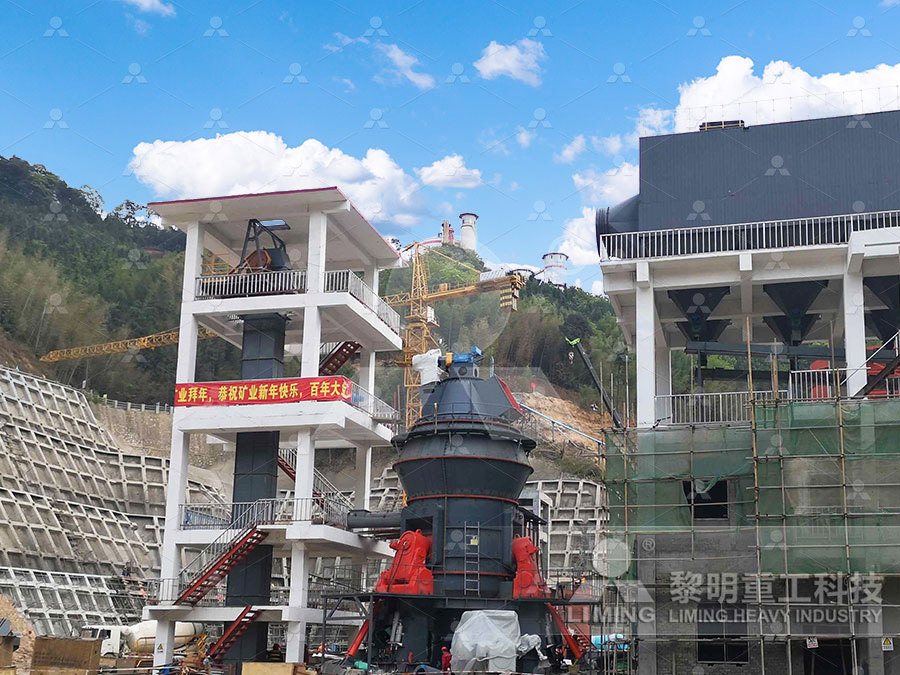
Crushing in Mineral Processing Eastman Rock Crusher
2020年4月20日 Industrial crushers are primarily used to take very large pieces of material and make them smaller Having smaller pieces of the material allows for easier transportation, further processing, and/or better ability to differentiate the different compositions of the material Why crushing? There are many practical purposes for industrial crushingMining: Crushing ores and other hard materials Construction: Producing aggregate for building roads, bridges, and other infrastructure Demolition Recycling: Breaking down construction and demolition waste for recycling Quarrying: Reducing the size of large rocks extracted from quarries 514 Types of Jaw CrushersWhat Are The Main Types Of Crushers? Mega Crushing Plants2024年5月30日 Primary Crushing Primary crushing is the first stage It involves breaking down the raw material into manageable pieces Jaw crushers are commonly used in this stage They can handle large rocks and reduce them to The Ultimate Guide to Rock Crushers Mellott2024年6月28日 Wide application: Suitable for both dry and wet crushing, for materials with up to 15% moisture Onetime forming: Eliminates the need for primary and secondary crushing, reducing costs by approximately 40% Large feed opening: Handles feed sizes up to 1000 mm, making it ideal for coarse crushing Nonclogging: Designed to ensure smooth flow of high What Crusher Should You Choose for Primary Crushing?
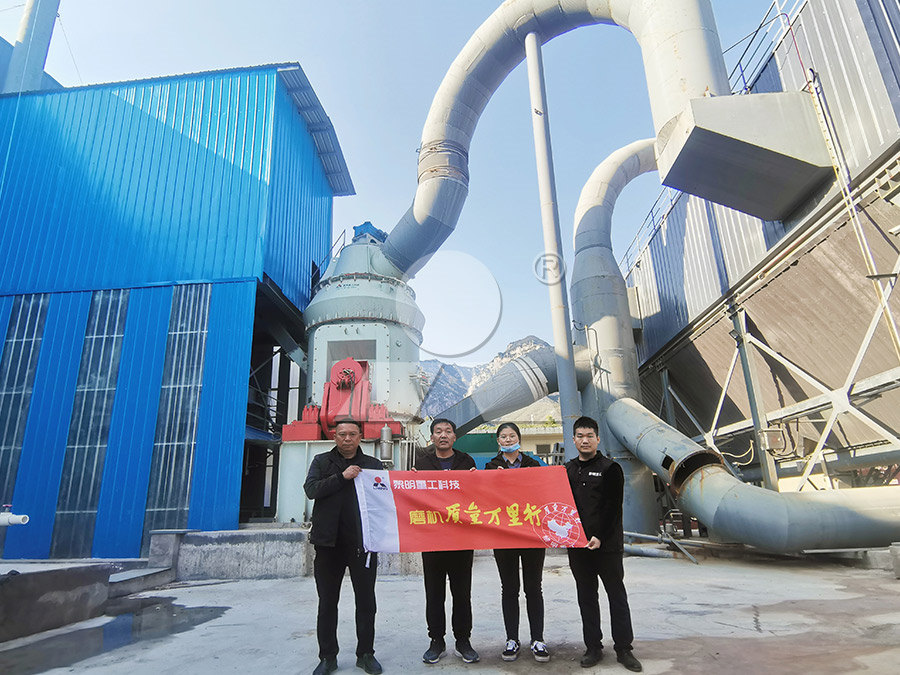
What Are The Different Types Of Crushers?
2 Secondary Crushing Secondary crushing is the second stage of rock crushing or the second granularity process of comminution after primary crushing and is mainly to produce fine particle product Unlike primary crushing, secondary 2023年7月22日 The ore crushing process includes four types: ore coarse crushing, ore medium crushing, ore fine crushing, and ore superfine crushing Ore coarse crushing is a process of crushing ore blocks with a feeding particle size of 500–1500 mm to 125–400 mm The maximum crushing ratio of coarse crushing is about three The main force in the coarse Ore Crushing SpringerLink2023年2月22日 Primary Jaw Crusher: This type of jaw crusher is used for the first stage of crushing large and hard stones It is designed to handle high capacities and has a large feed opening Secondary Jaw Crusher: Secondary jaw crushers are used for the second stage of crushing They have a smaller size and are designed to handle mediumhard to hard stonesDifferent Types of Stone Crusher Machines AGICOLarge pieces of ore are broken once, and then fall to a lower position (because they are now smaller) where they are broken again This process continues until the pieces are small enough to fall through the narrow opening at the bottom of the crusher A cone crusher is suitable for crushing a variety of midhard and above midhard ores and rocksCrusher Wikipedia
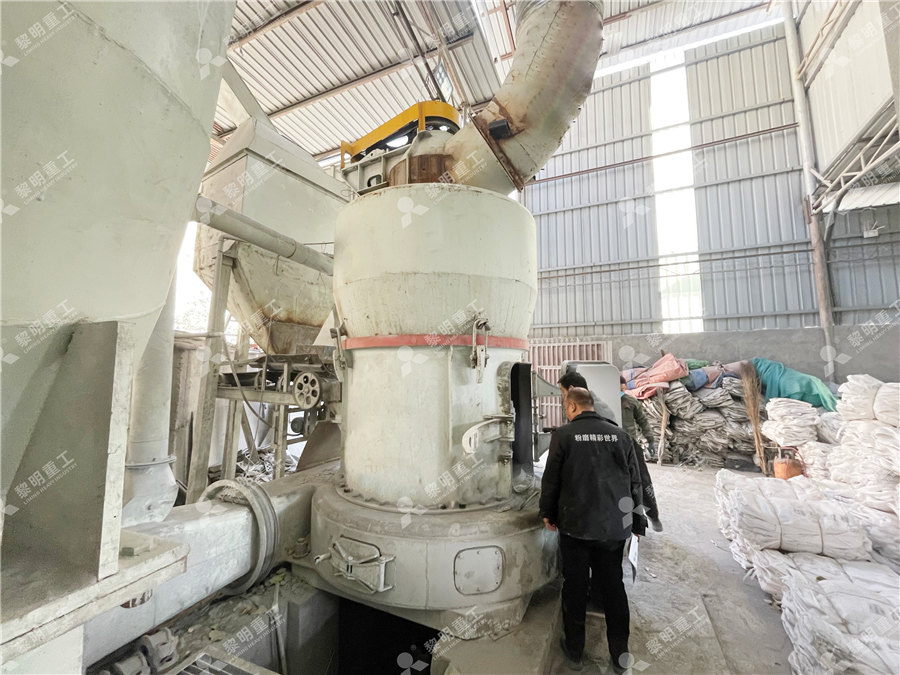
PQ University Lesson 7: Crushing Secondary Breaking
2019年9月2日 The vertical shaft impact crusher (or VSI) has a rotating shaft that runs vertically through the crushing chamber In a standard configuration, the VSI’s shaft is outfitted with wearresistant shoes that catch and throw the feed stone against anvils that line the outside of the crushing chamberWhen iron ore is extracted from a mine, it must undergo several processing stages Six steps to process iron ore 1 Screening We recommend that you begin by screening the iron ore to separate fine particles below the crusher’s CSS before the crushing stage A static screen is used to divert the fine particles for crushingThe six main steps of iron ore processing MultotecPrimary crushing brings runofmine ore down to a maximum size of the order 4″ to 6″ in average diameter; secondary crushing receives feed at −6″ and reduces it to below “Dry” crushing includes work on ore as mined, which may be somewhat moist when delivered It is succeeded by comminution in water, arbitrarily called “grinding”Primary Crushing SpringerLinkIn primary crushing the largest lumps of ore mined must be dealt with In secondary crushing the maximum sized piece is unlikely to exceed 6#8243; in average diameter and some of the unwanted material coming from underground has probably been removed The feed isSecondary Crushing SpringerLink
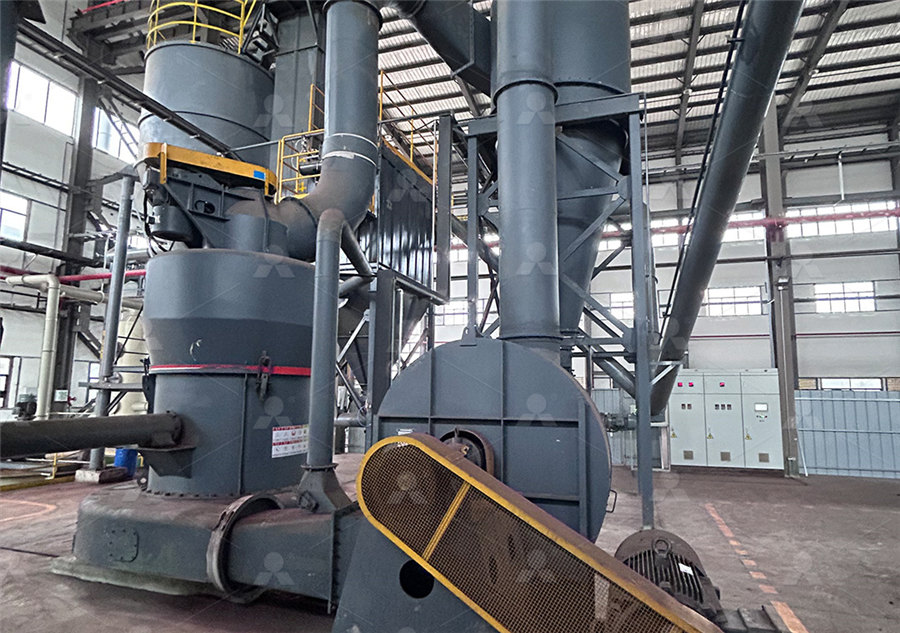
Cone Crushers (Parts of a Cone Crusher) Explained
Crushing ‘Comminution’ is the term used to define the process that reduces materials (especially mined ore)It is the action of reducing a material to minute fragments or particlesThe process is typically achieved in mining operations 2024年2月23日 This raw material can be big and oddly shaped It is then moved to the primary crusher This is usually done by large trucks or a conveyor belt After the first crush, the material might go for more crushing It could be Primary Crushing: A Comprehensive Guide JXSCA crusher is a machine designed to reduce the size of Run of Mine (ROM) large rocks to smaller rocks, gravel, sand, or rock dust; this is essential for efficient transport of the ore via conveyors etc Crushing is the first of many stages that Gyratory Crusher (Gyratory Crushers Explained)2021年1月10日 Relying on these many stages of crushing beyond only primary can add great value to a crushing operation Not only can multiple sizes of product be generated, but often in an opencircuit crushing layout, the flow and processing of material is streamlined and can increase output when compared to a closedcircuit crushing layoutWhat Is Primary, Secondary, and Tertiary Crushing?
.jpg)
SIZE REDUCTION BY CRUSHING METHODS By ResearchGate
Ore, Copper Ore, Zinc Ore and Manganese Ore 41 The art of crushing: Crushing means different things for different operations and the production goals are not always2024年3月25日 After primary crushing, secondary crushing is key It makes materials smaller for further use This step is vital in mining, construction, and making aggregates Here, materials first broken are made even finer This ensures they fit specific needs for building, making things, and other uses where size matters a lotSecondary Crushing 101: Everything You Need to Know JXSC2023年2月23日 As the main shaft rotates, it causes the mantle to move back and forth against the concave, crushing the rocks and ores between them The eccentric motion of the main shaft is a crucial component of the cone crusher working principle It creates a powerful force that allows the machine to crush rocks and ores with precision and efficiency The Cone Crusher Working Principle: Crushing Rocks and Ores with 2015年7月25日 That is because the ore must meet the circuit’s objective, in this case the correct size, before it is allowed to escape the closed loop of the crushing circuit Open Circuit Secondary and Closed Circuit Tertiary Crushing Flowsheet Our last schematic represents a CLOSED CIRCUIT This one involves both SECONDARY and TERTIARY crushingSecondary Tertiary Crushing Circuits 911Metallurgist
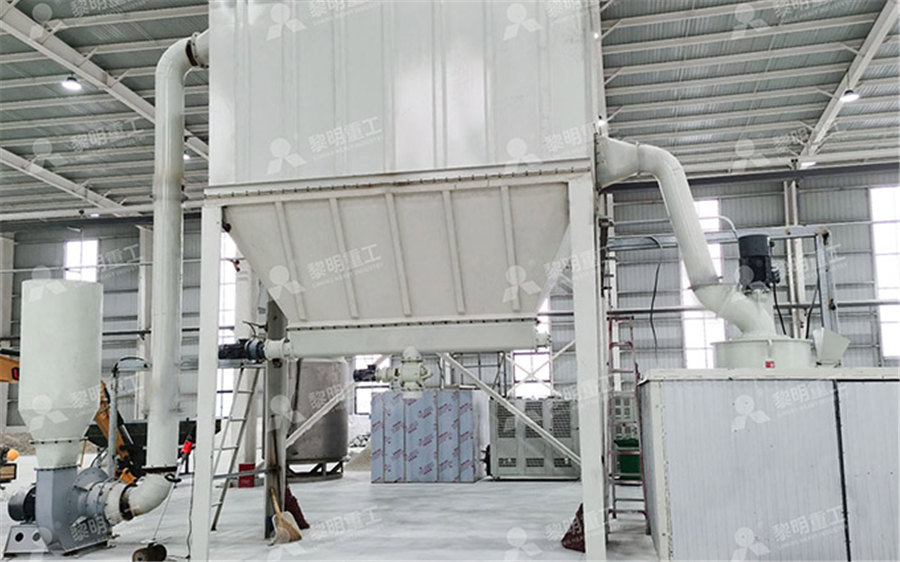
Silver (Ag) Ore Minerals, Formation, Occurrence, Deposits
2023年4月23日 Silver ore refers to natural deposits of silvercontaining minerals that are mined and processed to extract silver metal Silver is a precious metal known for its lustrous appearance, high thermal and electrical conductivity, and various industrial, technological, and ornamental uses Silver has a long history of human use, dating back to ancient civilizations, 2023年2月28日 For example, in the mining industry, impact crushers are used to break down large rocks and minerals into smaller sizes for processing In the recycling industry, they are used to break down concrete and asphalt for reuse in new construction projects Overall, impact crushers are a versatile and important tool in the secondary crushing processA Comprehensive Guide to Secondary Crusher Types