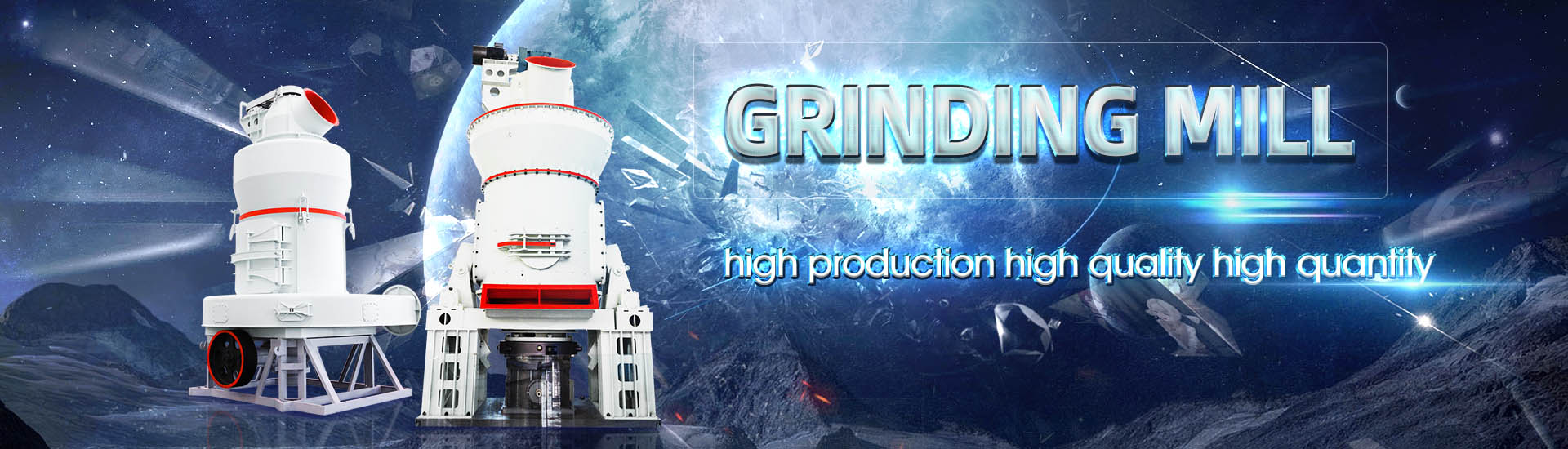
Openair quicklime coal mill system
.jpg)
Modeling and control of ball mill system considering coal moisture
2016年8月1日 Duplex inlet and outlet ball mills are widely used in 200–300 MW coalfired generating units This pulverizing system is easily adaptable to multiple coal type and is simple Coal mills or pulverizers play a very essential part in the coalfired power production system Coal mills grind the coal into fine powder, and the primary air entering the mill dries and drives the Coal Mill an overview ScienceDirect Topics2015年8月1日 Power plant performance and reliability is highly influenced by coal mills that grind, dry, and transport coal to the furnace This paper presents a review of the current state Review of control and fault diagnosis methods applied to coal Coal grinding systems have wrongs in fire and explosion protection due to purchasing process: See here why This talk pertains to indirect firing systems in form of airswept mill systems, Optimisation of coal mill systems, with fire and explosion
.jpg)
A Comparison of Three Types of Coal Pulverizers Babcock Power
Coal and preheated primary air enter one or both ends of the mill from a crusher/dryer or feeder As the mill rotates, the balls cascade and pulverize the coal by impact and attrition The Lowvibration mill running, even in partial load ranges down to 20% of the mill load, thanks to individuallyguided grinding rollers The speciallydeveloped hydraulic roller relief system enab LOESCHEMILLS2020年8月12日 This study shows the performance of a currently running vertical roller coal mill (VRM) in an existing coalfired power plant In a power plant, the coal mill is the critical An investigation of performance characteristics and energetic the combustion air passes the material bed in the preheating zone, which was preheated by the kiln offgases during the previous operating cycle The preheating of the combustion air makes New PFR lime kiln process with blast furnace gas and oxygen
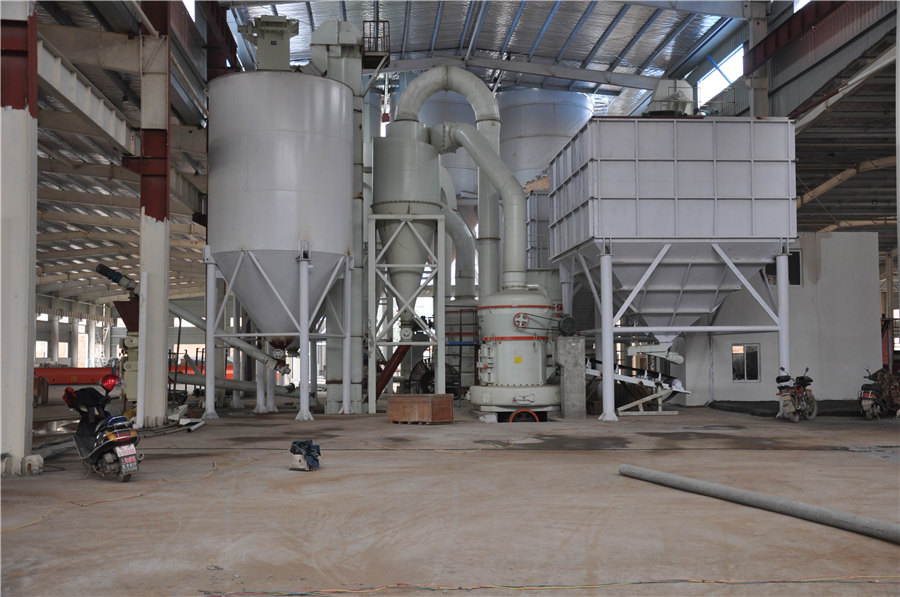
A unified thermomechanical model for coal mill operation
2015年11月1日 Coal mills are bottleneck in coal–fired power generation process due to difficulty in developing efficient controls and faults occurring inside the mills In this paper, a dynamic 2020年4月7日 The primary air system of a coal mill is mainly responsible for two tasks of coal po wder drying and transmitting the regulating valve of cold air will open quickly; in Modeling of Coal Mill System Used for Fault Considering the flammable and explosive characteristics of coal powder, Tongli’s coal vertical mill has set up multiple protection measures, including nitrogen safety protection system, multipoint gas analysis, realtime temperature monitoring, etc Tongli coal vertical roller mill is also suitable for grinding a variety of material such as clinker, coal, blast furnace slag, steel slag Coal vertical roller millVertical roller millPRODUCTTongli The coal vertical mill, also referred to as the vertical roller coal mill, is an advanced equipment developed by our company It combines modern technology with our extensive experience in powder manufacturing This coal pulverizer HighEfficiency Vertical Coal Mill Enhancing Coal

(PDF) Modeling and Control of Coal Mill Academia
Coal mill is an important component of the thermal power plant It is used to grind and dry the moisturized raw coal and transport the pulverized coal – air mixture to the boiler Poor dynamic performance of coal mill will lead to decrease in the overall efficiency of the power plant, slow load take up rate and frequent shut downThe airswept coal mill adopts advanced grinding technology and an efficient classification system, which can realize efficient pulverized coal grinding and particle size control It can effectively improve the utilization rate of pulverized coal, reduce energy consumption, and reduce the adverse effects caused by the nonuniformity of pulverized coal finenessAir Swept Coal Mill Cement Plant Equipment Coal Grinding MillSystem Description of MRHS Mill reject handling system (MRHS) consist of Following sub system or equipment: 1 Conveying Air System Conveying air compressor will located in plant compressor house to supply compressed air required for mill rejects conveying 2 Instrument Air System For actuation and process air requirement in the system MRHS Mill Reject Handling System in Thermal Power PlantFigure 7) with sufficient coal/air mill exit temperature (14009, was expected to eliminate a number of past fuel system deficiencies such as: Low mill product fineness Little mill turndown capability Utilization of maximum available primary air at all mill loads (to avoid mill roller skidding) Abnormally high coal pipe (excessive coal pipe wearWorldProven Coal Pulverizer Technology Debuts in the US
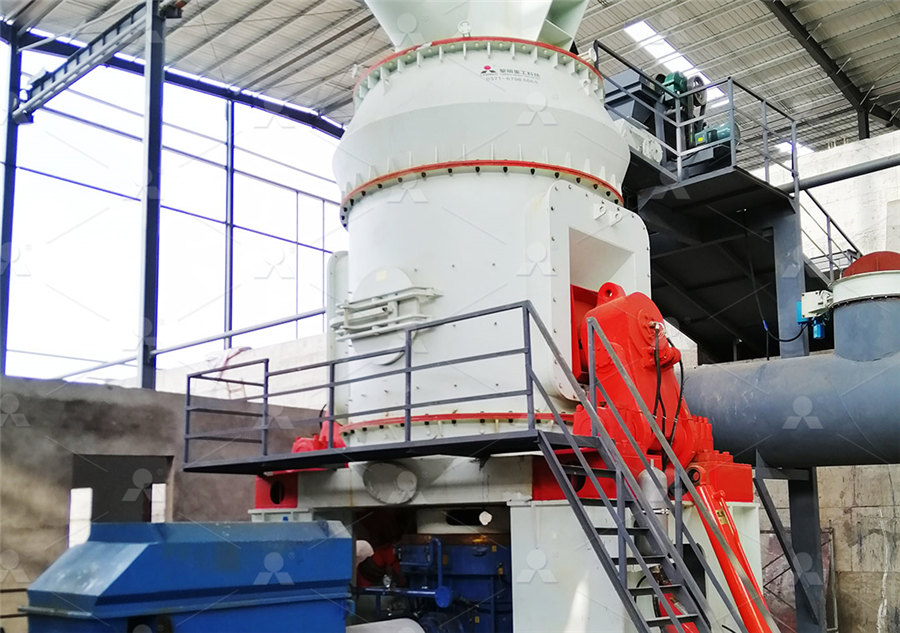
COAL GRINDING SYSTEMS SAFETY CONSIDERATIONS PEC
Coal Mill Operation Fires or explosions most likely occur during startup and shutdown of a coal mill system If a small amount of coal remains in the mill after it is shut down, it slowly increases in temperature If the pulverized coal undergoes spontaneous heating and the coal mill is2020年4月7日 Monitoring and diagnosis of coal mill systems are critical to the security operation of power plants The traditional datadriven fault diagnosis methods often result in low fault recognition rate or even misjudgment due to the imbalance between fault data samples and normal data samples In order to obtain massive fault sample data effectively, based on the Modeling of Coal Mill System Used for Fault Simulation MDPI2022年12月22日 ③ Thin oil lubrication system: The main engine drive and fan drive system are all lubricated with thin oil, and the oil is changed every four months; ④ Noresistance air inlet volute + sameresistance layout scheme, which reduces the economic loss caused by system energy consumption;Type Selection of Quicklime Deep Processing Equipment2019年11月7日 Comprehensive treatment,we should have a test on the 300 MV unit steel ball coal mill pulverizing systemAt the same time,analyze the main operating parameters before modificationTransform the Optimization and transformation of 300MV units steel ball coal mill
.jpg)
Bowl Mill Coal Pulverizer COAL HANDLING PLANTS
1 The hot air dries the coal 2 The hot air is used for transportation of the recirculating coal within the mill and also for transporting the coal from the pulverizer to the furnace As the coal is continuously reduced in size, the The pulverized coal is taken out of the mill by hot air Advantages Compared with the vertical roller mill, Milling System: Vertical Roller Mill: Ball Mill: Feed size(mm) ≤50: ≤25: Feed coal water content (%) ≤15: ≤10: Coal powder Coal Mill in Cement Plant Vertical Roller Mill Air 2015年8月1日 Mill problems originate mainly due to poor controls or faults occurring within the milling system As discussed by GQ Fan and NW Rees [3], the control of mills remains very simple in most of the power plants due to the fact that the mill system is highly nonlinear with strong coupling among the variables and it is very difficult to measure some important Review of control and fault diagnosis methods applied to coal TONGLI is on the vendor list of designated production enterprise of the Ministry of Coal Industry ISO9001、ISO14001、ISO45001 certified, accredited as Hightech new technology enterprise of Zhejiang Province, Tongli ZJTL series cement grinding equipment has won the Chinese National Torch AwardBall Mill Rotary Kiln Vertical Roller Mill Manufacturer Tongli
.jpg)
A Comparison of Three Types of Coal Pulverizers Babcock Power
pressurized seal air is also used to prevent leakage of coal dust from the mill and to protect bearings in the grinding rollers MILL SYSTEM COMPARISON AND PERFORMANCE Refer to Table I for a summary of the design features for each mill system Mill Comparisons—General The BTM is a lowspeed mill that primarily grinds coal by impact and attritionHard coal is a sedimentary rock which was formed by deposition and carbonization of plant remains It is hard and resistant More than 50% of its weight is made up by carbon Therefore it is classified as highrank coal Other fossil fuels like subbituminous coals with high moisture contents as well as brown coal and lignite are lower rankedCoal mills for all requirements Gebr PfeifferWhat kind of Fuel Grinding systems exist? Raw Coal from a bunker or open space is fed in a coarse form, to the raw coal silo above a Mill The coal is then fed to the mill for crushing The mill crushes the coal to a fine dust and the fines are sucked via a large duct up to the filter which separates the air from the dustExplosion Protection For the Dairy Industry White Papera standalone coal mill grinding system recirculatingprocess air coal grinding system structure stand alone PF silos bagfilter raw coal stockyard CO 2 mill mill low O 2 process air from precalciner process air throughout the system; • A simple, largely open structure with as little concrete and steel construction work as possible;Safety considerations when purchasing a standalone coal mill
.jpg)
Coal pulverizer mill system modeling for failure simulation
2023年5月8日 The disturbance occurs because it operates using LowRank Call (LRC) coal with high moisture, causing the changing in the operating pattern of the coal pulverizer mill, such as the coal flow rate setting and primary air In this study, a coal pulverizer mill simulation was carried out with dynamic modeling to analyze mass flow rate, heat Safe operation of coal grinding systems: Raw coal silo protection against fire and explosions Safe operation of coal grinding systems: Raw coal yard management The purchasing process for coal grinding systems needs changes Talk at a virtual seminar, November 2023 Accept the probability that the fire and explosion safety of your coal grinding Coal Mill Safety: A Critical Aspect of Power Plant Operations Coal Optimisation of coal mill systems, with fire and explosion protection This talk pertains to indirect firing systems in form of airswept mill systems, both horizontal ball mill and vertical roller mill systems Click on the button below to download this publication Download (pptx) #PRESENTATIONS VideoOptimisation of coal mill systems, with fire and explosion 2022年1月26日 Pulverized Coal–Air Mixture in the MillDuct System Bartłomiej Hernik Department of Power Engineering and Turbomachinery , Silesian University of Technology , Konarskiego 18,Numerical Study of the Erosion Process and Transport
.jpg)
Coal mill model considering heat transfer effect on mass
2021年8月1日 Yukio et al [7] proposed a model consisting of blending, grinding and classifying processes for pulverizer control Agarawal et al [8] differentiated coal powder into ten size groups, divided the bowl mill into four zones, and developed a unified model Palizban et al [9] derived nonlinear differential mass equations of raw coal, recirculation coal and suspension coal in reconcile the amount of coal in the stockpiles to the book inventory Most coals are susceptible to weathering and atmospheric oxidation during storage in openair stockpiles Chapter 5 examines some of the properties and processes affected by coal oxidation/weathering including heating value losses, handleability, cleaning, combustion and cokingManagement of coal stockpiles ICSC2012年5月1日 The identification process was done for the transfer functions between coal flow, cold air mass flow and hot air mass flows to discharge temperature and total air mass flow Detailed models of the coal pulverization process in a mill have been presented by Austin, Shah, Wang, Gallagher, and Luckie (1981) , Austin et al, 1982a , Austin et al, 1982b , Robinson Derivation and validation of a coal mill model for control2019年11月2日 The compressed air generated from a high temperature of 150° C introduces the pulverization energy of the jet stream to have the ceramic powder grind under 7–8 μm, which maximize efficiency The grinding pressure of the conventional cooling air jet mill system is the same as the developed uncooled air jet mill systemImprovement of pulverization efficiency for microsized particles
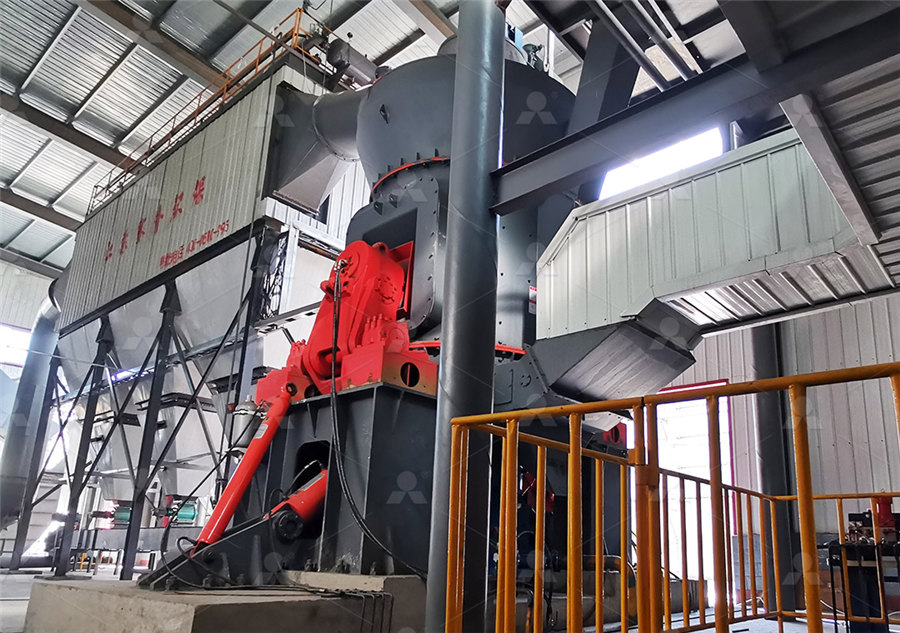
Modelling and control of pulverizing system considering coal moisture
2015年2月1日 In the mill system, when MC is greater than the design value, the energy provided by primary air (PA) cannot dry the coal particles to the design level if PA temperature is remained unchanged This results in an accumulation of pulverized coal in the mill system and consequently blocks the coal pulverizing system [14]They are used to pulverize raw coal into fine powder of desired temperature and fineness There are plenty of coal mines in China, but the quality of raw coals varies greatly Therefore, ball mill coalpulverizing systems are widely used to grind various raw coal The flowchart of ball mill coalpulverizing system is shown in Fig 2, which Optimal Decoupling Control Method and Its Application to a Ball Mill PAPER OPEN ACCESS During the operation process of direct fired pulverizing systems with medium speed mill, air coal ratio can get from the DCS dial and the output of the pulverizing system should be checked Suppose output is 35t/h, calculate air coal ratio and compare with actual air coal ratio If the result is greater than or equal PAPER OPEN ACCESS Program Design and Calculation Example of 2020年8月12日 To understand the performance of a vertical roller coal mill, the real operational tests have been performed considering three different coal sources Obtained results indicate that grinding pressure, primary air (PA) temperature and mill motor current have a tendency to rise by increasing coal feeding mass flow rates for all used coalAn investigation of performance characteristics and energetic
.jpg)
Quick Lime Dryers Vulcan® Drying Systems
Wet quicklime (calcium oxide, calcium hydroxide) is loaded into the shredder 1The feed conveyor 2 transports the quicklime to the slinger conveyor 3A burner 4 fires into the combustion chamber 5, delivering hot gas into the direct fire 2024年5月1日 Nowadays coal supplies over a third of global electricity generation In China, Coal accounts for around 70% of primary energy consumption Statistics show that China's coalfired power generation in 2022 were 573 trillion kWh, accounting for 584% [1]With continued consumption of coal resources, the available highgrade coal is decreasing and the proportion A green and efficient lignitefired power generation process based 2016年8月7日 4 • interlocks stand by lop starts • if fan is running and lub oil header presure 1 sec and other lop in standby id fan inlet and outlet gate will open on auto, if • id fan is running (60sec delay) [if other fan is not running gate will open immediately] or • id fan a b are not runningPulverized coal fired boiler startup procedure2015年9月4日 A lime slaking and addition system can consists of two systems to control the pH in the rougher and cleaner flotation circuitsA pebble lime silo will dose dry lime to the SAG mill feed belt; a hydrated lime make down system will provide slurry lime to multiple addition points in the flotation circuit Other lime delivery options are detention slakers and Vertimill slakersLime Slaking Equipment 911Metallurgist
.jpg)
Coal Mill Safety In Cement Production Industries
Safe operation of coal grinding systems: Raw coal silo protection against fire and explosions Safe operation of coal grinding systems: Raw coal yard management The purchasing process for coal grinding systems needs changes Talk at a virtual seminar, November 2023 Accept the probability that the fire and explosion safety of your coal grinding system is nothing more than a mirageThe quality of quicklime is affected by several factors related to the limestone feed and the calcination process These include the chemical composition and crystalline structure of the limestone, as well as operating conditions in the kiln such as temperature, particle size of the limestone, rate of temperature rise, retention time, and CO2 concentration Controlling these Factors Affecting The Quality of QuicklimeIn discussion: Coal Mill Safety At best, coal mill safety is not well understood and, at worst, it is ignored When it comes to coal mill systems, most cement plant operators just presume that the supplier of the equipment knows all of the standards and rules and is 100% capable of making a system that conforms to these and is therefore safeIn discussion: Coal Mill Safety Coal Mill Safety, Explosion and Advantages of air swept coal mill The feeding device of the airswept coal mill adopts a louvertype structure with oblique air intake, which enhances the heat exchange capacity of the mill and can effectively prevent material blocking at the entrance of the coal mill; optimize the support system, improve the lubrication structure, and reduce system resistanceAir Swept Coal Mill Cement Plant Machinery
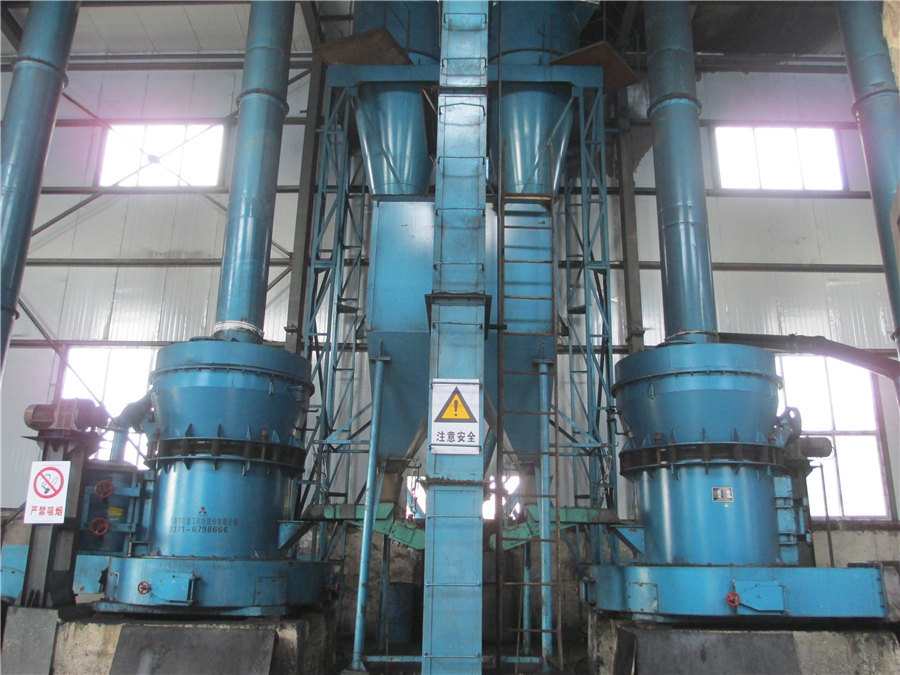
Coal Mill – Coal Mill In Cement Plant AGICO Cement Equipment
The coal mill grinding system is an important part of the dry process cement manufacturing In cement plants, we usually adopt the air swept coal mill system or vertical mill system as the pulverized coal preparation system, which is arranged at the cement kiln head or kiln tail to provide fuel for clinker calcination However, due to the flammable and explosive