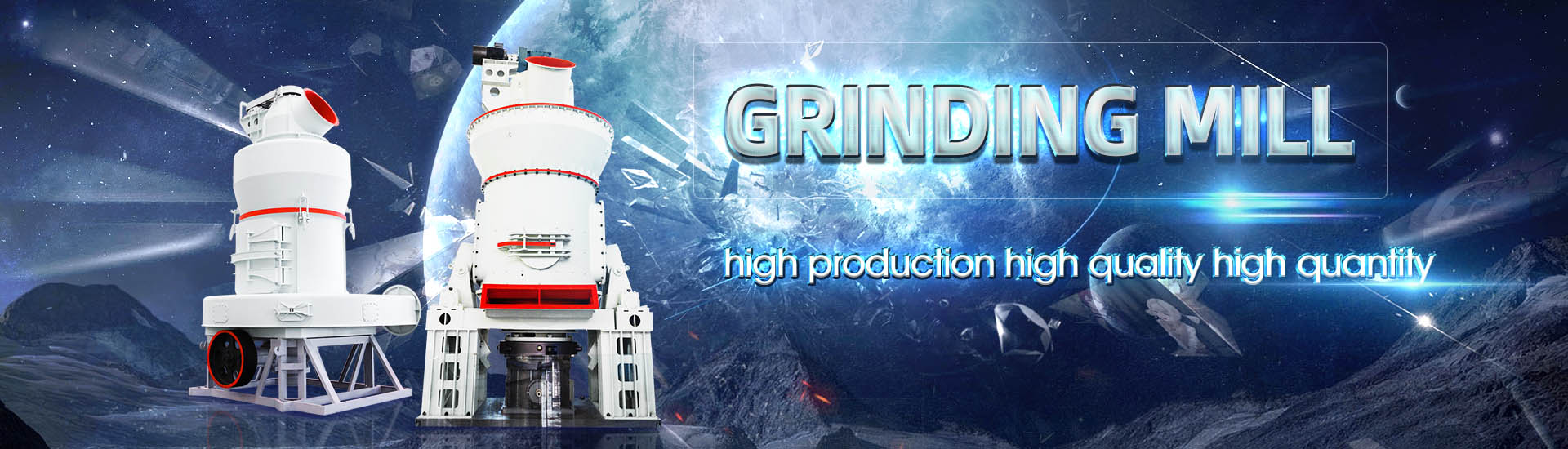
Particle crusher cleaning operation procedures
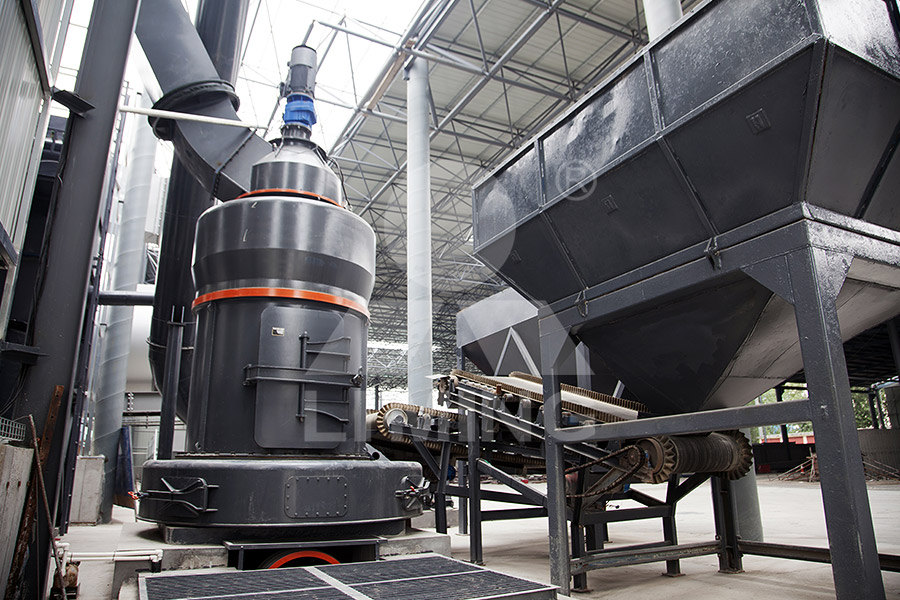
SAFE WORK PROCEDURE FOR Crushing Operations Screener
Safe work procedures (SWPs) are a written stepbystep set of instructions on how to complete a specific task safely It must clearly identify the steps required to complete the task, the hazards the worker could be exposed to, the control measures and what to do in an emergency situationPROCEDURES 1 Notify the control room that the primary crushing area preoperational inspection for a pending startup is about to begin Advise the mine of the time that the start of STANDARD OPERATING PROCEDURE PRIMARY CRUSHING AREA This unit covers the conduct of crushing and screening plant operations in the mining and extractive industries It includes: planning and preparation for operations, operating the plant, RIIPRO301C Conduct crushing and screening plant operations2024年1月26日 This article will introduce the operating precautions and particle size adjustment of the impact crusher for your referenceImpact Crusher Operation and Maintenance Guide: From
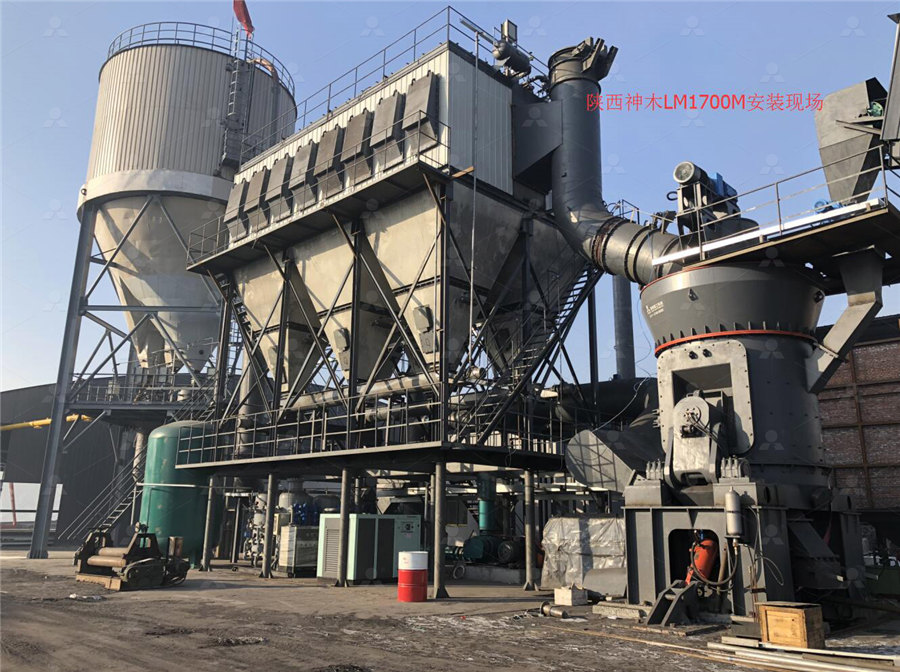
Construction, Working and Maintenance of Crushers for Crushing
There are four basic ways to reduce size of a material: by impact, by compression, by shear or by attrition Most crushers employ a combination of all these crushing methods Impact refers to In this paper, factors that affect the performance of the crushing plant operation are evaluated by focusing several critical design parameters associated with downtimes and production losses Field monitoring and performance evaluation of crushing plant 2019年9月11日 Tips for keeping a safe crusher include operating the crusher at its appropriate capacity, keeping platforms and areas around machine clean, and ensuring lubrication, flow, Site Safety and Safer Aggregate Crushing OperationsGeneral Routine Crusher Maintenance: Every crusher and its extra equipment must have regular, systematic checks This will result in fewer failures and repairs, not to mention the downtime General Routine Crusher Maintenance Midsouth Machine Service

11192 Crushed Stone Processing and Pulverized Mineral Processing
Processing operations may include crushing, screening, size classification, material handling and storage operations All of these processes can be significant sources of PM and PM10 2023年6月2日 Clean your equipment regularly, both externally and internally Use appropriate cleaning techniques and tools to remove dirt, grime, and contaminants Ensure that cleaning Crushing and Screening Best Practices: Maximizing Efficiency and 2022年1月1日 The name “Particle Size Magnifier” originated from the work of Okuyama et al (1984), who constructed a system for growing sub10 nm nanoparticlesThe term “PSM” is very often used synonymously to describe the whole PSMCPC combination, although it strictly refers only to the preconditioner partThe standard operating procedure for Airmodus Particle Size 2024年6月25日 Cleaning Standard Operating Procedures (SOPs) are comprehensive, written instructions designed to standardize cleaning tasks and ensure they are performed consistently and effectively These procedures Cleaning SOPs: Examples, Templates, and Best
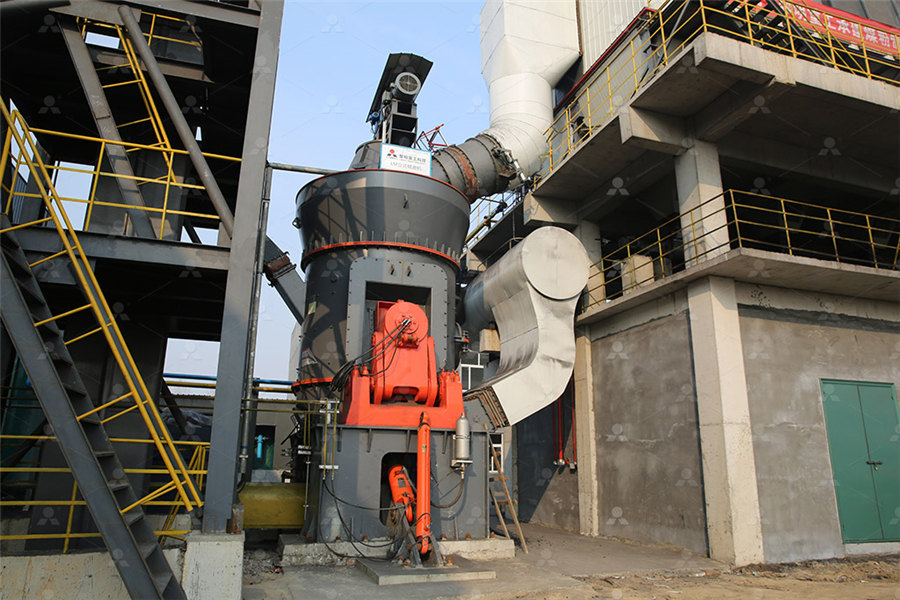
Operation cleaning of Nonviable Particle counter
2024年2月8日 Nonviable Particle counter To lay down the procedure for operation cleaning of nonviable particle counter woocommerceproductgallery{ opacity: 1 !important; } Skip to content2020年10月16日 Standard Operating Procedure (SOP) for Operation, Calibration, and Maintenance of Malvern Make Particle Size Analyzer (Mastersizer 2000 3000) SOP for Particle Size Analyzer (Malvern) 10 PURPOSE: The purpose of this Standard Operating Procedure (SOP) is to describe the Operation, Calibration, Maintenance of the Particle Size Analyzer Particle Size Analyzer (Malvern) Operation Calibration2024年4月24日 Safe Operating Procedures Operate the crusher in accordance with manufacturer's instructions and established safety protocols Keep the work area around the crusher clean, organized, and free of tripping hazards Clean up spills and debris immediately to prevent slips and falls Store tools, CrusherSafetyChecklist HVI APP Heavy Vehicle Inspection1998年12月16日 Standardize Instrument Operation Whenever possible you should standardize instrument operation and keep a centralized method common to most SOPs In an organization producing many hundreds of materials, including a description of the actual operation of the instrument in every single SOP would be tediousCreating Standard Operating Procedures for Particle Size Analyzers
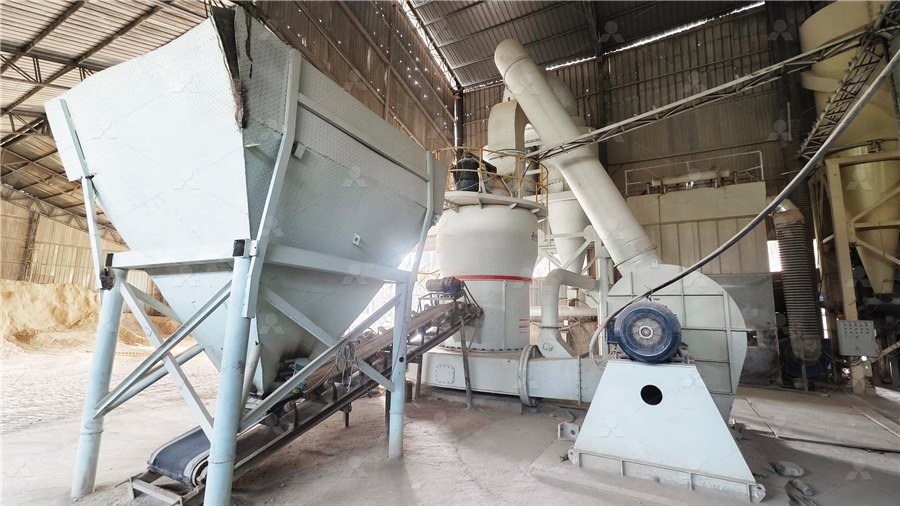
SOP for Particle Counter : Pharmaguideline
To lay down a procedure for operation of the particle counter 20 SCOPE The procedure is applicable for operation of particle counter “Met one 3400” 30 RESPONSIBILITY Officer/ Executive Quality Control 40 ACCOUNTABILITY Manager Quality Control 50 PROCEDURE2023年6月22日 Figure 3 shows a sieve analysis for a grind from a hammermill and a roll crusher Each grind produced a distribution with a mean particle diameter of approximately 710 microns, but the distribution from the roll crusher is more concentrated than the distribution from the hammermillHammermill and roll crusher maintenance and operation2016年1月27日 Normal Crushing Plant Operation After the crushing plant has been brought up to normal operating conditions the operator should attempt to even out the feed to the jaw crusher to the design tonnage of 60 mtph This is achieved by ensuring that the feed to the crusher maintains an essentially full chamber without ore spilling outCrushing Plant Startup Sequence Procedure 911Metallurgist1997年5月23日 Thoroughly clean beaker or other sample container to remove all particulates V OPERATION This operating procedure is based upon sampling a nonhazardous, low vapor pressure liquid, eg DI water Use of this equipment with other liquids may require modifications to this procedureOperation Of Liquid Particle Counter Stanford University
.jpg)
CRUSHING AND SCREENING OPERATIONS SOP v1 Squarespace
the Mawsons Disciplinary Procedure 32 Equipment and materials required • Take 5 • PPE • Mobile crusher/screens • Excavator • Front end loader Warning: Ensure cabins are sealed – dust exposure can have severe health consequences 4 PROCEDURE Preoperational safety checks a Conduct pre start check of machines bPARTICLE COUNTER ROUTINE MONITORING BEST PRACTICES Application Note: I 2 STANDARDS CLEAN AREA CLASSIFICATIONS Cleanroom classification is provided by two primary sources, the first is ISO 146441:2015 Air cleanliness class by particle concentration shall be designated by an ISO Class number, N TheParticle Counter Routine Monitoring Best Practices ClimetTo lay down the procedure for the operation, cleaning, maintenance and qualification of the Laminar Air Flow Scope: Ensure that particle count of the work station is done using a calibrated air borne particulate matter counter 1 Laminar Air flow (LAF) – Operation, Cleaning and 2022年3月28日 (2) Every shift should be filled with lubrication holes in the plastic crusher (3) The shields of the transmission parts of the plastic crusher should be kept permanently and completely intact The plastic crusher can not drive without a complete protective cover (4) The plastic crusher should not be operated for 24 hours continuouslyAnalysis: Plastic Crusher Operation Procedure
.jpg)
STANDARD OPERATING PROCEDURE Cleaning, Calibration and Operation
STANDARD OPERATING PROCEDURE Title: Cleaning, Calibration and Operation of Liquid Particle Counter SOP No: Department: Microbiology Effective Date: Revision No: 00 Revision Date: Supersede Revision No: Nil Page No: 2 of 3 PRODUCTION DEPARTMENT 42 Cleaning Procedure Frequency: Daily or after each use2024年2月17日 10 Objective: 11 To lay down the procedure for Vibro Sifter operation and Cleaning 20 Aim: This procedure is applied to Vibro Sifter operation and Cleaning in the production department 30 Responsibility: 31 Operation: operation and cleaning as per this SOP 32 Officer and executive: for implementing this SOP 33 Manager/ Head of Department: for SOP on Vibro Sifter operation and Cleaning Pharmagudduprocedures Operation of these devices is discussed here so that many errors can be avoided Abrief description is also given of some methods the particle count is very low requires a clean operating environment, a welltrained operator, and access to a very large amount of liquidOptical Liquidborne Particle Counter Operation Springer2022年10月27日 Ending the operation of a crusher is an essential part of crusher safety There are a few steps to follow when shutting down a crusher that every trained worker should follow: Shut down the apron feeder Ensure equipment is free of material Shut down the primary crusher Shut down the secondary crusher Deenergize the electromagnet8 Tips for Crusher Safety StewartAmos Equipment Company
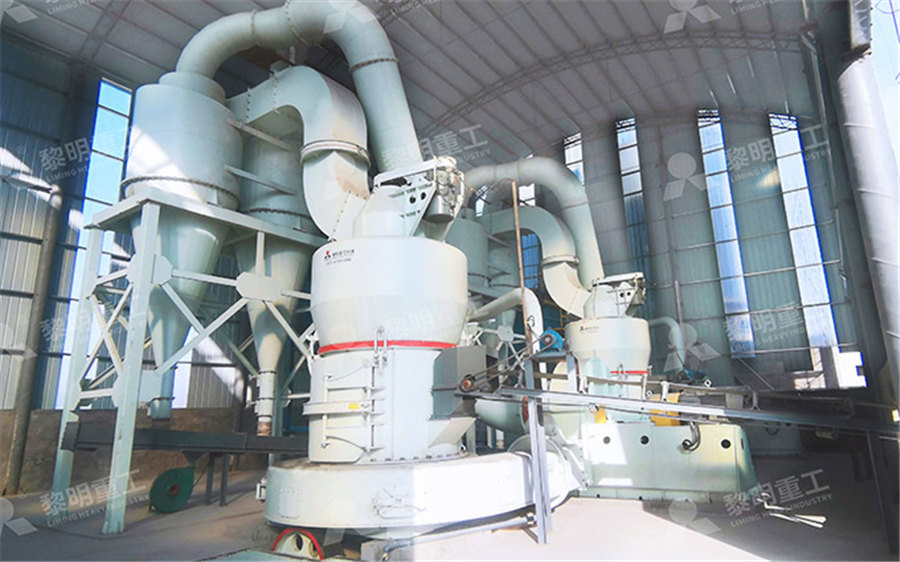
Standard Operating Procedure For Vial Filling Machine Cleaning
2023年6月15日 PURPOSE: To lay down procedure for operation cleaning of vial filling machine RESPONSIBILITY: Production Manager OPERATION: – 1 Choose syringe needle of appropriate vial 2 Adjust convey belt as per size of vial 3 Adjust volume 4 Place vials on convey belt 5 Push green button to run machine red button to stop CLEANING :Therefore, to know its operation procedure is helpful to enhance the crushing efficiency to some extent Following is the procedure introduced by Luoyang Dahua: 1 Often check the discharging situation, if found it is blocked, should clean in time 2 Adjust the opening size of jaw plate according to the required particle size 3Operation Procedure of Jaw Crusher Luoyang Dahua2024年4月17日 Standard operating procedure of cleaning and monitoring of BioSafety Cabinet by active air sampling and non viable particle count SOP for Operation, Cleaning and Monitoring of BioSafety Cabinet : PharmaguidelineSOP for Operation, Cleaning and Monitoring of BioSafety CabinetThe document provides guidelines for operating a Nonviable Particle Counter It outlines responsibilities for following procedures, reviewing activities, and calibrating the instrument Key steps include: charging the battery, purging Operating Procedure For NonViable Particle Counter
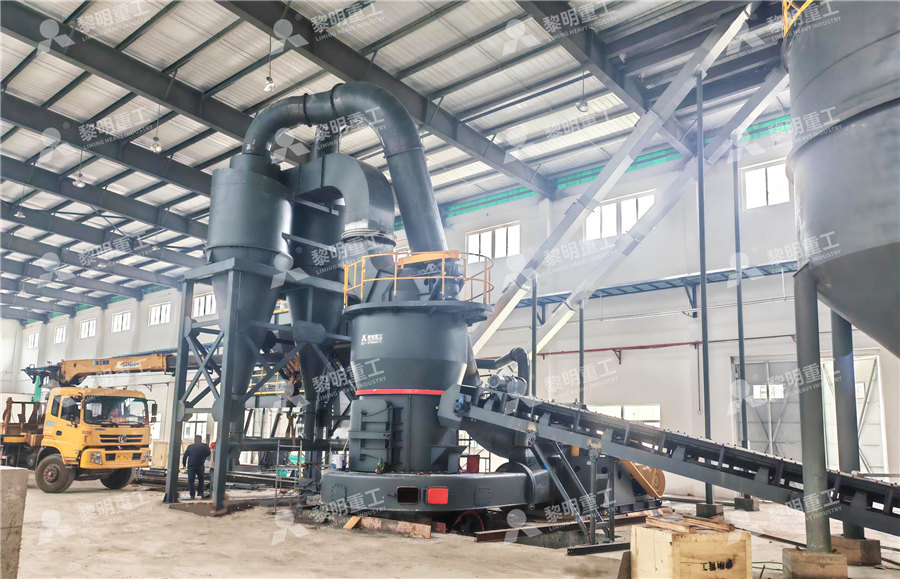
Field monitoring and performance evaluation of
The most down times are caused by operational issues as follows: daily cleanup, chute plugs, crusher plugs and settings (close side setting which enables the production of products in desirable size) Operators have to regularly clean the All components to be made particle free are usually precleaned using standard UHV cleaning procedures for degreasing eg high pressure cleaning systems or lab washers using standard detergents The following cleaning procedure in the clean room is shown schematically in Fig 3 Standard Cleaning ProcessA Cleaning Facility to Prepare Particle Free UHVcomponentsTrinity NDT® Procedure for Magnetic Particle Examination Page 4 of 6 743 The method of magnetization shall be done using either electromagnetic yoke or permanent magnet, with pole spacing to be between a minimum of 3 inches (762 mm) and a maximum of 8 inches (2032mm) Shorter spacing may be used to compensate for the geometry of area being examined or Magnetic particle test inspection free ndt sample proceduresTo lay down a Procedure for Operation, Cleaning and intervention of Ampoule Filling Sealing Machine 20 SCOPE: This SOP is applicable for Operation and Cleaning of Automatic Twelve Head Ampoule Filling Sealing Machine (Make: Truking) in Production area at Ampoule line 30 RESPONSIBILITY:PHARMA DEVILS
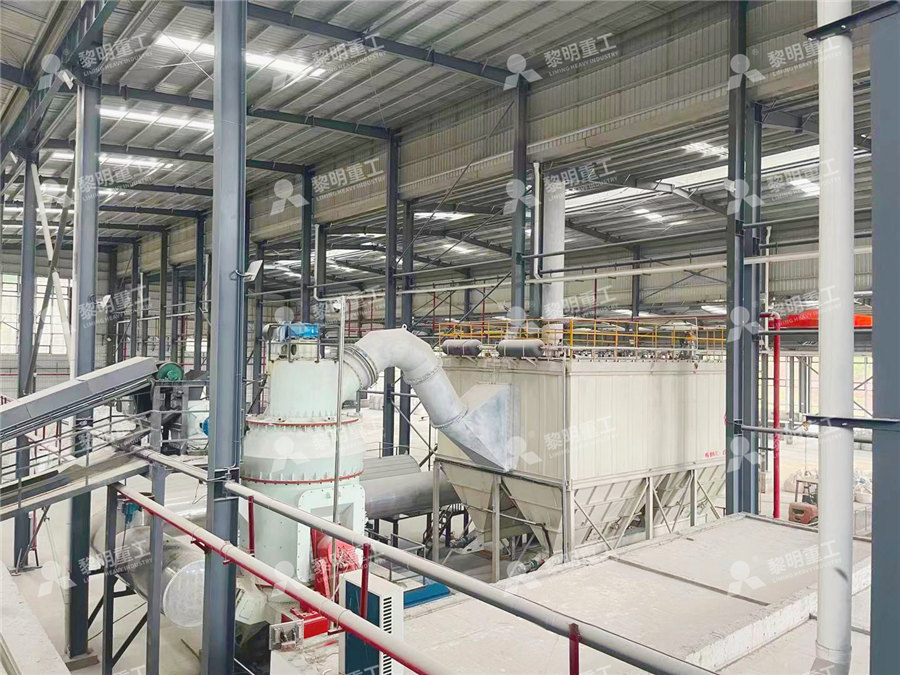
Optical Particle Counter Operating Procedures, Calibration and
Test Method for Calibration of LiquidBorne Particle Counters for Submicrometer Particle Sizing, ASTM F1226–89 Philadelphia: American Society for Testing and Materials Google Scholar Caldow, R, Blesener, J, 1989 A Procedure to Verify the Lower Counting Limit of Optical Particle CountersOP 33v7 Particle Size Analysis 4/29/2008S STANDARD OPERATING PROCEDURE NO 33 PARTICLE SIZE ANALYSIS (Including both Dry and Wet Mechanical Sieving and Hydrometer Analyses) REVISION LOG Revision Number Description Date 33 Original SOP 331 Revisions by Dr Catherine T AimoneMartin Aug 19, 2004 33v2 GMLR 927STANDARD OPERATING PROCEDURE NO 33 PARTICLE SIZE 2019年9月11日 Crusher safety starts with the person feeding the plant This person needs to be trained on crusher best practices specific to the machine they are working with An operator may have years of experience of operating and loading a cone crusher, but that does not translate into experience of loading and operating a jaw crusherSite Safety and Safer Aggregate Crushing Operations AggNet2011年10月3日 Waste Disposal Procedures: Biomass can be placed in the nonhazardous waste garbage Decontamination Procedures: None Spill Containment and clean up procedures: Biomass can be swept up or wiped with a wet cloth and disposed of in the garbage Using substances requiring special procedures: No Written By: Catie Brewer Date: 5252011Standard Operating Procedure College of Engineering
.jpg)
Particle Trap Operation ManualParticle Trap Opera
Particle Trap Installation and Operation Manual Static Clean International :: Made in USA :: Tel: 781 2297799 :: Fax: 781 2294555:: staticclean p 7 of 10 Maintenance The Particle Trap Product Line requires very little maintenance other than routine replacement of 2024年4月17日 50 PROCEDURE 51 Ensure that the area is cleaned and air handling unit is kept ON for at least two hours before taking particle count 52 The particle count to be performed by an outside agency 53 Ensure that the particle counter used is duly calibrated and the certificate for the same must be traceable to national/ international standardsSOP for Carrying Out Air Borne Particle Count in Static Condition2023年6月2日 Choosing the right equipment is crucial for efficient crushing and screening For example, if you’re dealing with abrasive materials like granite or quartzite, selecting a jaw crusher with robust construction and installed with Crushing and Screening Best Practices: Maximizing In the paint and pigment industries particle size infl uences appearance properties including gloss and tinctorial strength Particle size of the cocoa powder used in chocolate affects color and fl avor The size and shape of the glass beads used in highway paint impacts refl ectivity Cement particle size infl uences hydration rate strengthA GUIDEBOOK TO PARTICLE SIZE ANALYSIS Horiba
.jpg)
AusIMM – Leading the way for people in resources
%PDF16 %âãÏÓ 4215 0 obj > endobj 4235 0 obj >/Encrypt 4216 0 R/Filter/FlateDecode/ID[87C03FABF6FB2246BC4F9AB649B4B217>]/Index[4215 26]/Info 4214 0 R/Length 101 2023年6月16日 PURPOSE: To lay down a procedure for the maintenance in case of ampoule filling machine RESPONSIBILITY: 1 Section Supervisor/Shift Incharge 2 Maintenance Engineer PROCEDURE: CLEANING: After complication of ampoule filling, close the valves related to LPG, nitrogen and oxygen gasStandard Operating Procedure For Cleaning , Operation2022年3月22日 The operation procedure of cone crusher can be divided into four stages: before the start, at startup, at run time and turningoff time All conditions should be paid attention in each stage, and the potential problems can be found and Cone Crusher Tips of Operation and Regular MaintenanceWalker Roller Crusher Operation Manual,Installation and adjustment,Test run,Operating procedures,maintenance Skip to content +86 export6@jxscmining for: Home; Therefore, the injected lubricating oil must be clean and the seal must be good This machine The main oil injection point of (1) transmission bearing (2) Roller Crusher Operation Manual walker
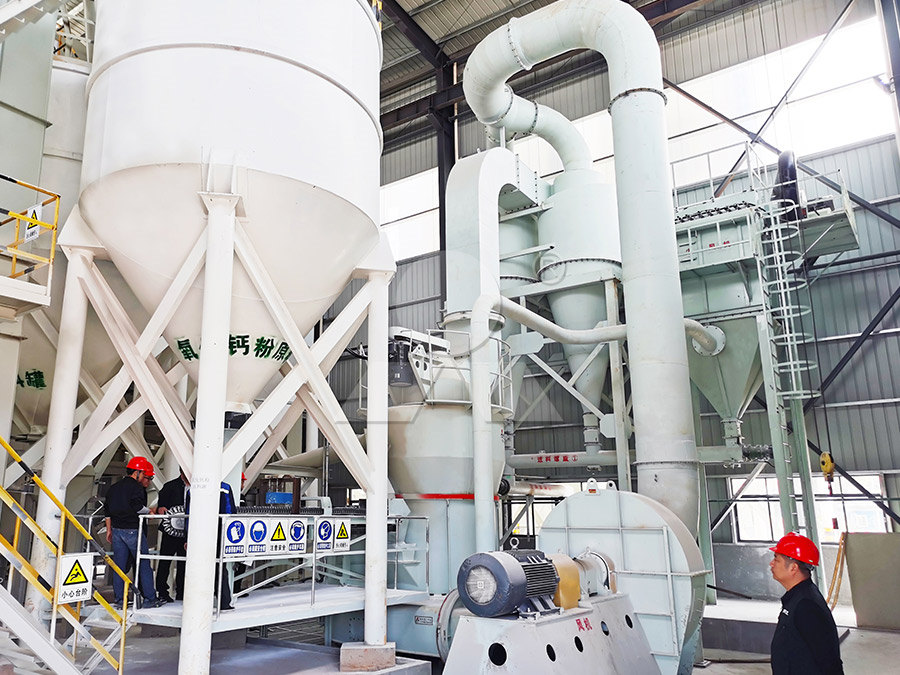
Safety First: Best Practices for Operating Plastic Crushers
2023年12月16日 Before operating a plastic crusher, operators should undergo comprehensive training and obtain the necessary certifications Training programs should cover equipment operation, safety protocols, emergency procedures, and maintenance practices Certified operators are better equipped to handle potential risks and operate the crusher efficiently 2Particle size is calculated from the diffusion coefficient using the StokesEinstein equation: D h=kT/(3πηD m) Dh:Particle hydrodynamic size k :Boltzman constant T :Thermodynamic temperature and η :Viscosity *1 Small particle light fluctuation signal Autocorrelation function Particle size distribution High Concentration Samplesoptical system Nanoparticle Analyzer Horiba