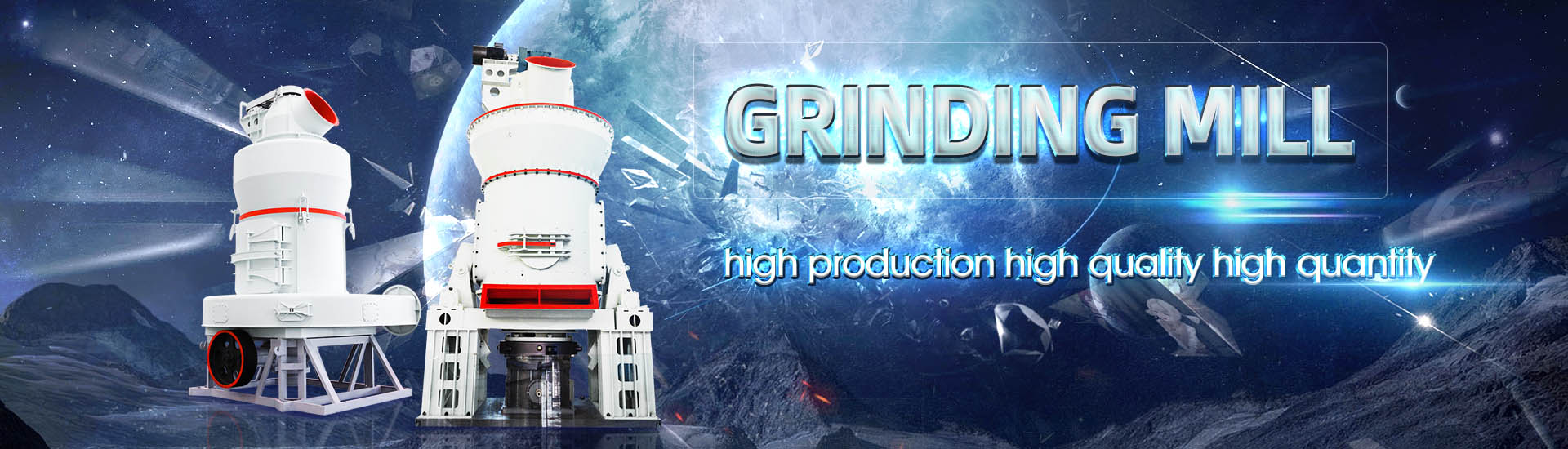
Where is the limestone sintering grinding equipment to achieve better desulfurization effect
.jpg)
ReviewRecent advances in process and materials for dry
Additionally, using smaller limestone particle sizes can significantly improve desulfurization efficiency Smaller limestone particles have a larger specific surface area, which is beneficial for enhancing contact and chemical reaction efficiency with SO 22022年1月15日 Cui et al proposed a combination of limestonegypsum wet flue gas desulfurization (WFGD) and wet condensation desulfurization technology for enhanced Summary of research progress on industrial flue gas 2015年10月30日 Limestonebased desulfurizing agent is one of the superior elements which are optimal at around 850950^ {\circ}C on high temperature desulfurization(PDF) A Review of Desulfurization Technology using Limestone in 2017年7月1日 Desulfurization tests show greater performance in terms of gypsum production SO 2 removal efficiency compared to the limestone treated with a traditional mill Multicriteria Enhancing the recovery of gypsum in limestonebased wet flue
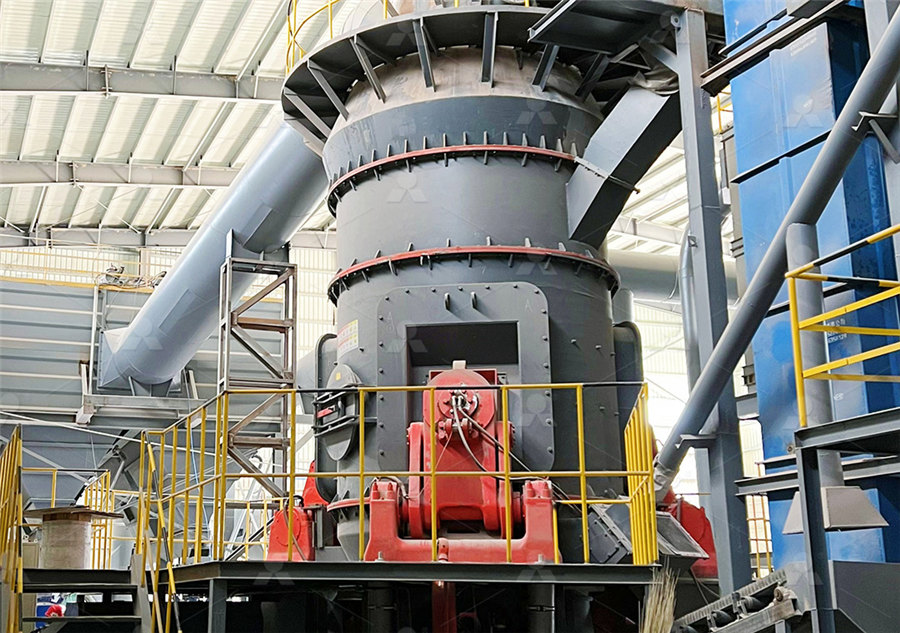
Study on the limestoneGypsum sintering flue gas
To date, limestonegypsum has been the most widely used sintering flue gas desulfurization technology in China's steel industry In order to demonstrate the application satus, this paper 2002年1月1日 This paper presents a comprehensive review of the state of the art in flue gas desulfurization (FGD) technologies for coalfired boilers Data on worldwide FGD applications Flue Gas Desulfurization: The State of the Art [J] ResearchGate2021年3月17日 Wet FGD limestone scrubbing has been predominantly used over other competing technologies However, the simplicity of the spraydrying absorption (SDA) Spray drying absorption for desulphurization: a review of recent Large investment, high energy consumption, and easy blockage of equipment restrict its development space5,6Compared with the limestone method, MgO flue gas desulfurization Investigation into the Dissolution Kinetics of Different MgO
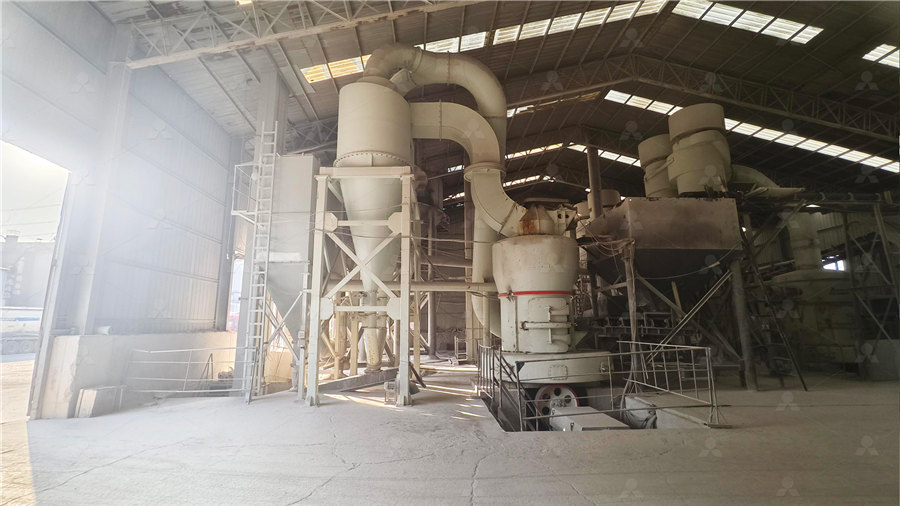
LimestoneGypsum Wet Flue Gas Desulfurization Wastewater
2021年2月1日 In this paper, chemical precipitation process is used for the treatment of the desulfurization wastewater generated by the waste gas treatment system of the limestone 2020年8月15日 Postcombustion flue gas desulfurization and denitrification technologies are essential in achieving the full compliance of fine particulate matter (PM 25, aerodynamic Comprehensive evaluation of flue gas desulfurization and 2017年2月16日 PDF Sintering is a thermal agglomeration process that is applied to a mixture of iron ore fines, recycled ironmaking products, fluxes, slagforming Find, read and cite all the research you (PDF) Iron Ore Sintering: Process ResearchGateIndustrial flue gas desulfurization can effectively reduce sulfur dioxide emissions to atmosphere, but emits large amounts of desulfurization byproducts Calciumbased desulfurization byproducts can be divided into two categories: desulfurization gypsum and desulfurization ash Desulfurization gypsum is mainly produced in the wetResource utilization of flue gas calciumbased desulfurization
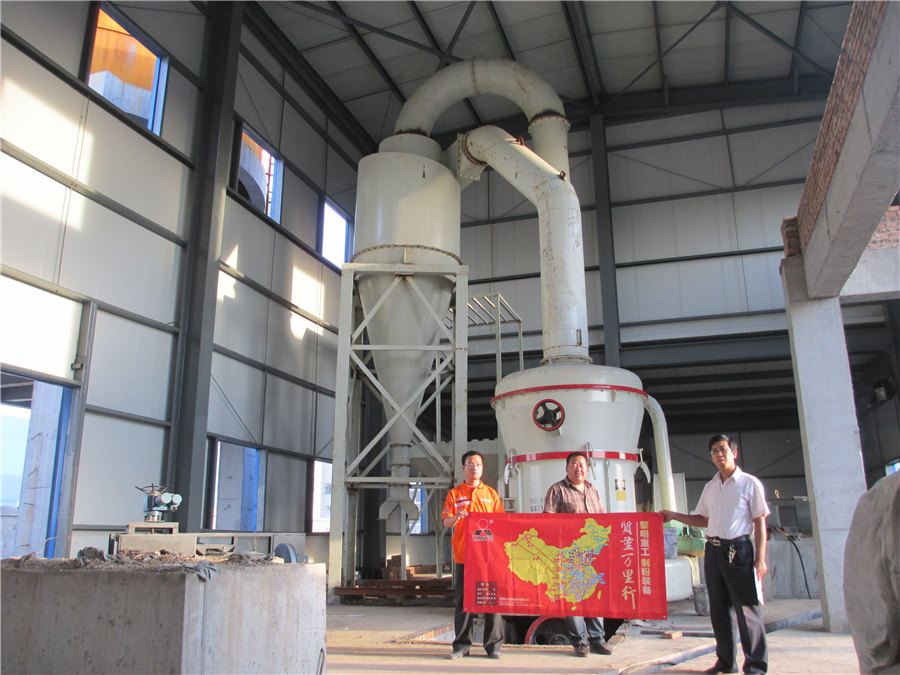
Recent advances in process and materials for dry desulfurization
Currently, desulfurization technologies can be categorized into three main types: wet flue gas desulfurization (FGD) [11], [12], [13], semidry desulfurization [14] and dry desulfurization [15]Wet flue gas desulfurization is widely employed in largescale desulfurization processes due to its high efficiency and low energy consumption [16]However, it poses a significant environmental When a piece of equipment, including a coal mill system, goes down, the typical response is to resolve the problem that caused the outage as quickly as possible and return the equipment to service A coal mill system that goes down, particularly under load, must be Everything you need to know about Kiln System Operations in 2023年10月23日 The compatibility of grinding aids (TEA/glycol) and superplasticizers (PC/SNF) in lowand highC3A cements, as well their mutual effect on the properties of pastes and fresh/hardened mortars were (PDF) A study of different grinding aids for lowenergy2015年6月5日 To better guide the industrial production, the effect of binary basicity (CaO/SiO2) on the reduction swelling behavior and mechanism of limestone fluxed iron ore pellets was investigatedEffect of Adding Limestone on the Metallurgical ResearchGate
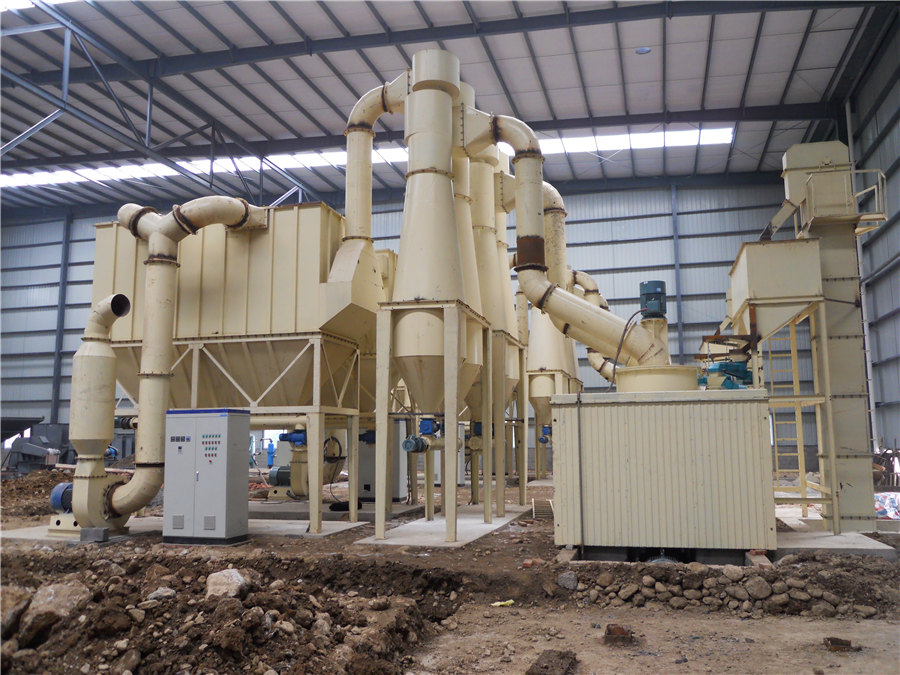
Flue Gas Desulfurization (FGD) Working Thermal Power Plant
Limestone preparation system in flue gas desulfurization (FGD) consists of following subsystems: 1 Limestone Handling System Limestone will be delivered to the limestone storage shed by truck Limestone will be delivered from the limestone unloading hopper to the limestone day silo by limestone transfer conveyor and bucket elevator 22021年3月3日 Cement is produced by a hightemperature (about 1500 °C) reaction in a rotary kiln of carefully proportioned and blended ratios of lime (CaO), silica (SiO 2), alumina (Al 2 O 3), and iron oxide (Fe 2 O 3)The production of cement is a chemical process requiring an accurate blend of the previously cited four key organic oxides and the limitation of several undesirable Cement SpringerLink2021年3月5日 At present, the continuous accumulation of the flue gas desulfurization (FGD) gypsum in steel plants leads to the serious environmental issues and resource waste To achieve green and sustainable development for the steel industry, it is significant to improve the usage of byproduct gypsum Employing the sintering FGD gypsum, ferric oxide, and graphite carbon Preparation of calcium ferrite by flue gas desulfurization gypsume,The reaction between metakaolin and limestone and its effect in
.jpg)
Assessing the effect of alkanolamine grinding aids
2020年10月26日 [17] S Sohoni, R Sridhar, G Mandal, The effect of grinding aids on the fine grinding of limestone, quartz and Portland cement clinker, Powder Technol 67 (3) (1991) 277–286 2015年1月1日 Like other sintering processes, iron ore sintering converts iron ore fines of often − 8 mm sizing into larger agglomerates, namely, sinter, between 5 and 50 mm particle size, which possess the physical and metallurgical characteristics and gas permeability required for efficient blast furnace operationAs shown in Figure 141, iron ore sintering is carried out in three Iron ore sintering ScienceDirect2020年6月20日 The chemical reaction between the limestone slurry and sulfur in the flue gas produces calcium sulfate, while the limestone slurry is converted into a gypsum slurry by the desulfurization process The latter is then Emission reduction process for dechlorinating fluegas An essential advantage of grinding mills is their ability to control particle size with precision Different industries require distinct particle sizes, and grinding mills offer the flexibility to achieve the desired fineness This ensures that the produced limestone powder meets the specific requirements of diverse industrial usesThe Role of Grinding Mills in Limestone Powder Production
.jpg)
Experiment and Mechanism Analysis of Desulfurization with a
2020年11月16日 To reduce the cost of the current commercial desulfurization and eliminate effluents, the MgObased desulfurizer fixed bed desulfurization tests were carried out in a dry environment By means of Xray diffraction, scanning electron microscopy, and Xray photoelectron spectroscopy, the absorption effects of the MgObased desulfurizer on SO2 Assessing the effect of alkanolamine grinding aids in limestone calcined clay cements hydration Franco Zunino⇑, Karen Scrivener Laboratory of Construction Materials, EPFL STI IMX LMC, École Assessing the effect of alkanolamine grinding aids in limestone 2013年11月1日 Materials characterization showed that the grinding quality of the seven cements was very different This parameter was defined by the ratio of specific surface (Blaine) and residue at 40 lm(PDF) The Effects of grinding on the properties of Portlandlimestone 2021年12月31日 Grinding aid chemicals which are used in the grinding of calcium carbonate (CaCO3) to prevent agglomeration are chemisorbed on the surfaces of particles, and the compatibility of them with the (PDF) Effects of Grinding Aids Used in Grinding Calcium
.jpg)
(PDF) Progress of Desulfurization and Denitration Technology of
2019年3月30日 Gas–solid twophase flow and water vaporization processes tend to have a significant impact on the efficiency of flue gas desulfurization with a powderparticle spouted bedThe limestone grinding production line is a production process for the fine processing of limestone raw materials The limestone grinding production line grinds limestone into powders of different fineness through crushing, grinding, classification, and other processes to meet the needs of different fields This production line covers the complete process from raw material processing Limestone Grinding Mill Plant TAYMACHINERY2024年2月12日 In this paper, TiO2 catalysts doped with different Fe contents (FeTiO2 catalysts) were prepared by coprecipitation method and the Fe loading capacity was optimized, and then the integrated Experimental study on integrated desulfurization and Natureequipment for SO2, acid mist or stack fume control Air Pollution Control Equipment To control both the particulate and the SO2 emissions from the air pollution sources in nonferrous metal smelting, PPSI has developed three different equipment configurations The October 1980 Volume 30, No 10 1157Application of the Lime/Limestone Flue Gas Desulfurization Process
.jpg)
AIR POLLUTION CONTROL TECHNIQUES FOR THE CEMENT
configuration, and grinding them to achieve the proper particlesize to ensure optimal fuel efficiency in the cement kiln and strength in the final concrete product (Karstensen et al) [5]The limestone grinding production line is a production process for the fine processing of limestone raw materials The limestone grinding production line grinds limestone into powders of different fineness through crushing, grinding, classification, and other processes to meet the needs of different fields This production line covers the complete process from raw material processing Limestone Grinding Mill Plant TAYMACHINERY2021年3月17日 The performance of a wet FGD system is greatly influenced by gas–liquidphase mass transfer, ieof Ca 2+ ions in the liquid phase and of SO 2 from the gas phase to the aqueous phase (Hrdlička and Dlouhý 2019)This is further influenced by the rate of dissolution of limestone in the system, directly affecting the concentration of dissolved ions in the slurry Spray drying absorption for desulphurization: a review of Electrooxidation flue gas desulfurization is a gas–liquid reaction, but the solubility of SO 2 in aqueous solution is very low with the solubility of only 94 g/100 mL at 25 °C Thus it is necessary to strengthen the contact between SO 2 and ROSs to achieve successful flue gas desulfurization Namely, the mass transfer of flue gas in electrolyte should be strengthened [314,315]Flue Gas Desulfurisation an overview ScienceDirect Topics
.jpg)
(PDF) Iron Ore Pelletizing Process: An Overview ResearchGate
PDF On Jul 11, 2018, Sandra Lúcia de Moraes and others published Iron Ore Pelletizing Process: An Overview Find, read and cite all the research you need on ResearchGate2022年1月15日 In the industrial production of China, the processing of phosphate rock, volcanic eruptions, kerosene combustion and aluminum smelting will lead to flue gas emissions containing a large amount of SO 2SO 2 is a highly irritating gas Because SO 2 is freely soluble in water and enters the respiratory tract, it can generate corrosive sulfurous acid, sulfuric acid, and sulfate Summary of research progress on industrial flue gas desulfurization 2024年1月29日 As limestone powder has numerous applications across various industries, selecting the appropriate limestone grinding machine is essential The choice depends on several factors Firstly, it's important to clarify your processing requirements, including the desired fineness of the powder, production capacity, and quality standardsHow to choose limestone grinding mill? SANDMINE2022年12月28日 The effect of carbon dioxide (CO2) on the desulfurization of sintering flue gas with hydrate (Ca(OH)2) as an absorbent was investigated, and the formation of calcium carbonate (CaCO3) and its Effect of CO2 on the Desulfurization of Sintering Flue Gas with
.jpg)
Evaluation of the Efficiency of Limestone Powder in
2018年2月21日 The major environmental impact of concrete comes from the CO2 emissions, produced during the cement manufacturing process The main goal of this research project is to evaluate the efficiency of 2023年10月1日 Carbide slag (CS) is a solid waste generated during acetylene production through the hydration of calcium carbide Its main component is Ca(OH) 2, which is strongly alkaline [1, 2]Acetylene is the main raw material for producing polyvinyl chloride (PVC), with high demand and high production in various countries worldwide [3]For every 1 ton of PVC Effect of moisture on the granulation and sintering characteristics 2023年2月28日 HGM ultrafine milling machine overcomes the difficulty of ultrafine powder classification better The fineness of the limestone powder is between 80800 mesh Frequency control of powder concentrator achieves better fine Necessary Matters About Limestone Powder Grinding1 Effect of milling mechanism on the CO 2 capture performance of limestone in the Calcium Looping process Monica BenitezGuerrero, a, b Jose Manuel Valverde,a * Antonio Perejon, b, c Pedro E Sanchez Jimenez b and Luis A PerezMaqueda b a Facultad de Física, Universidad de Sevilla, Avenida Reina Mercedes s/n, 41012 Sevilla, Spain b Instituto de Ciencia de Effect of milling mechanism on the CO capture performance of limestone

What is Limestone Grinding Mill SBM Mill Crusher
2023年5月15日 The Different Types of Limestone Grinding Mills Available There are several different types of limestone grinding mills available, each designed for specific purposes and applications Raymond Mill This mill, also known as the Raymond Roller Mill, is a common choice for limestone grindingJune 2022; ARCHIVE Proceedings of the Institution of Mechanical Engineers Part C Journal of Mechanical Engineering Science 19891996 (vols 203210) 236(2):1107(PDF) A comprehensive review on the grinding process: 2013年8月1日 PDF Sintering is a process by which a mixture of iron ores, fl uxes and coke is agglomerated in a sinter plant to manufacture a sinter product of a Find, read and cite all the research you (PDF) Iron ore sintering Part 1 Theory and practice of the sintering 2022年2月28日 Several investigations have been conducted to investigate the effect of grinding aids on the comminution of various minerals such as cement , feldspar , limestone , quartz , etc It is reported that grinding aids improve the grinding process by altering the adhesive forces, the state of fine particle dispersion, and powder flow characteristics [ 50 ]Grinding SpringerLink
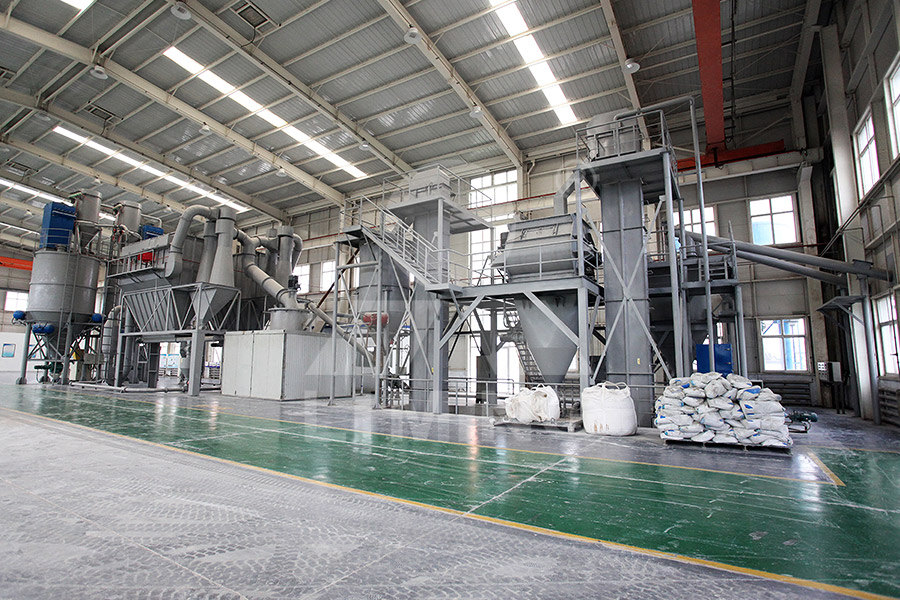
Study of standsupport sintering to achieve high oxygen
2020年4月10日 For a long time, enormous efforts have been devoted to reducing energy costs, improving sintering quality and enhancing productivity, and a series of practical technologies have been developed, such as ultrathick bed sintering (UTBS) (Zhang et al, 2017), flue gas recirculation sintering (Wang et al, 2016), gaseous fuel injection sintering (Cheng et al, 2017) 2021年11月1日 Flue gas desulfurized gypsum mainly comes from thermal power plants, smelters, and largeenterprise boilers, and contains industrial byproducts produced through a wet desulfurization combustion process, where SO 2 gas and lime slurry react under strong oxidation conditions The main component of this gypsum is calcium sulfate dihydrate, which also Production and resource utilization of flue gas desulfurized