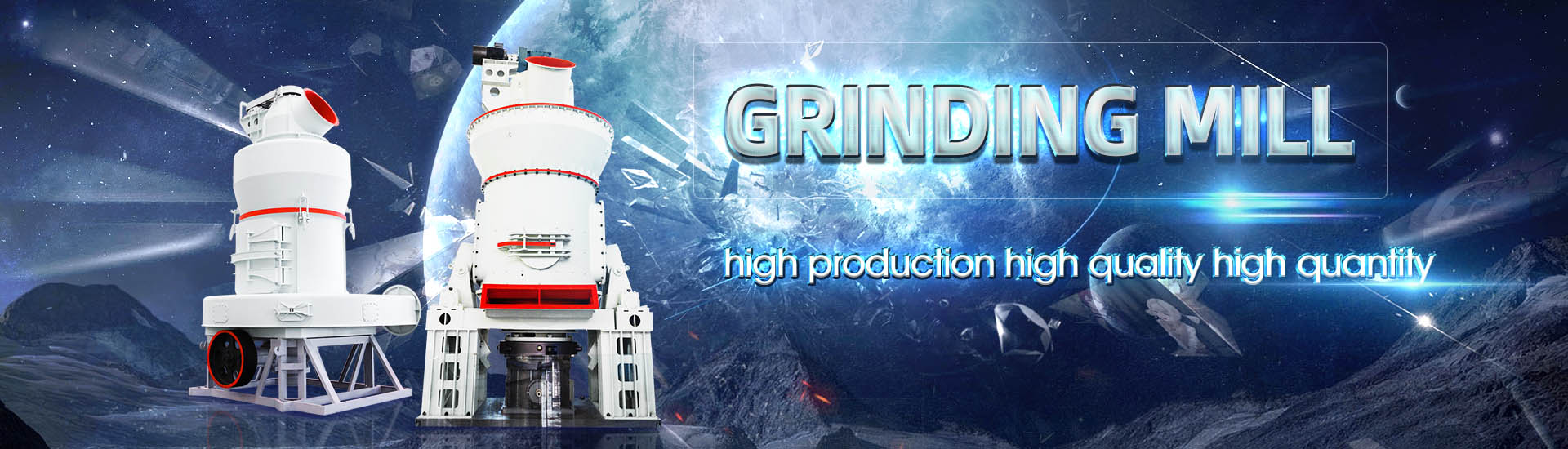
What does the grinding pressure of the vertical mill mean
.jpg)
VRM Operation and Optimization PDF Mill
Operational parameters like production rate, pressure, vibration levels, and temperatures must be monitored to optimize performance Vertical roller mills are used in cement industries for grinding clinker, coal, raw materials, and cementThe Vertical Roller Mill (VRM) reduces the power consumption for cement grinding approximately 3040% associated with other grinding mills The process variables in cement grinding process PROCESS CONTROL FOR CEMENT GRINDING IN VERTICAL 2017年4月1日 Working pressure is normalized with classifier rotor speed Vertical roller mills (VRM) have found applications mostly in cement grinding operations where they were used in Operational parameters affecting the vertical roller mill 2016年9月1日 Obtained results indicate that grinding pressure, primary air (PA) temperature and mill motor current have a tendency to rise by increasing coal feeding mass flow rates for all Operational parameters affecting the vertical roller mill
.jpg)
Vertical roller mill for raw Application p rocess materials
Grinding raw materials needs lots of energy Tube mills had been used for grinding, but the energy efficiency level was lower Therefore, the introduction of highly efficient grinding Vertical roller mill is a type of grinder used to grind materials into extremely fine powder for use in mineral dressing processes, paints, pyrotechnics, cements and ceramics It is an energy Vertical roller mill WikipediaCounteractive measures of the VRM, as eg higher grinding pressure, are used to increase the share of very fine particles (diameter below 5 μm) if necessary Advanced cement additives, SikaGrind® for vertical roller mills2024年1月17日 Any machine used for grinding or crushing consumes around 30 to 40% of the energy of a factory The loading pressure, table rotation speed, moisture content, outlet temperature and pressureParameters for the Grinding Process in Vertical Mills
%3C1PGHL[2}HK_]YT.jpg)
An investigation of performance characteristics and
2020年8月12日 To understand the performance of a vertical roller coal mill, the real operational tests have been performed considering three different coal sources Obtained results indicate that2022年5月31日 Compression crushing is also the main crushing mechanism in the VRM, but there is also shear force between grinding roller and particles Moreover, a key difference Analysis of vertical roller mill performance with changes in material 2021年1月29日 Vertical roller mills, VRMs, are widely used for grinding raw materials in factories engaged in the extraction and processing of minerals Any machine used for grinding or crushing consumes around Increase productivity of vertical roller mill using seven A mill is a device, often a structure, machine or kitchen appliance, that breaks solid materials into smaller pieces by grinding, crushing, or cutting Such comminution is an important unit operation in many processesThere are Mill (grinding) Wikipedia
.jpg)
Chapter Six: Some Operating Guidelines Vertical
2022年4月6日 Many ask me about the procedures for starting and operating the vertical roller mill, a grinding machine used in the cement industry I have to confess that answering that question is complicatedproduced by the oil pressure on the piston ring surface (grinding pressure) and reduced by the oil pressure acting on the piston bottom face (counter pressure) of the loading cylinder Tensioning rod Leackag Grinding pressure Leackage Lifting N2 Accumulator Lowering Counter pressure Hydraulic cylinder Figure 5 Hydraulic Cylinder ConfigurationCoal Pulverizer Design Upgrades to Meet the Demands of Low Vertical roller mills are used in cement industries for grinding clinker, coal, raw materials, and cement They comprise 24 conical rollers that are hydraulically pressed onto a horizontal rotating grinding table Material is fed onto the center of the table and thrown outward under the rollers where it is ground into a fine powder by both rolling and sliding motion Fine material is carried VRM Operation and Optimization PDF Mill (Grinding) Scribd2015年4月9日 Installing a grinding mill which is suitable for the purpose, Plate mills use a similar principle but are constructed of steel or ceramic plates and used more commonly in the vertical plane Output from such a mill is low and the mill in used only for small scale milling High pressure grinding rolls The high pressure grinding Grinding Mills and Their Types – IspatGuru
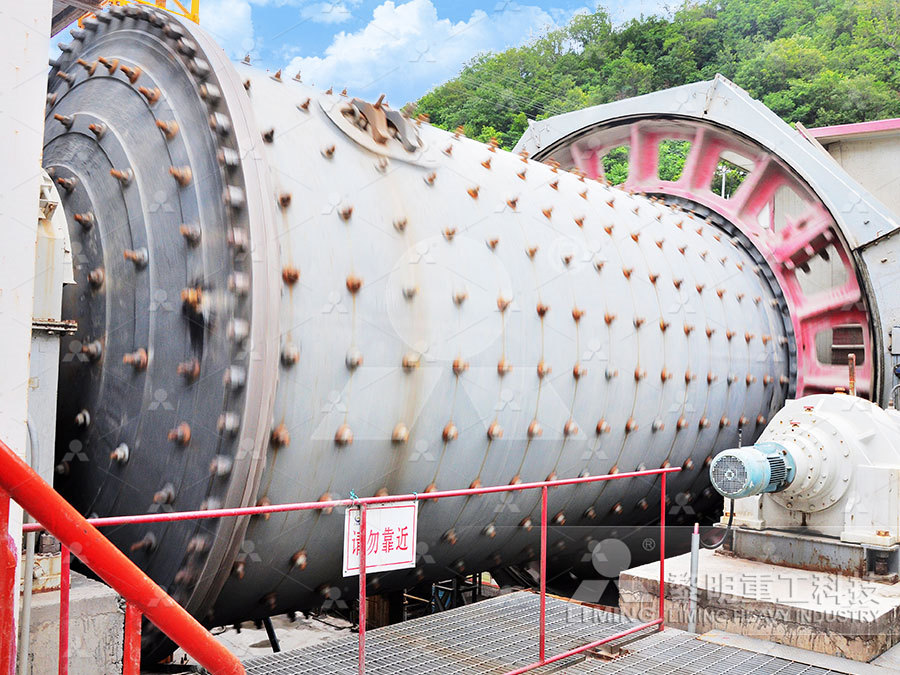
Regrind of metallic ores with vertical mills: An overview of the
2014年10月20日 This paper presents an overview of the regrind circuits in Brazil that operate with vertical mills and the results of industrial surveys at selected vertical mill circuitsboth grinding in the mill body and a circulation factor, the res idence time for a VRM is less than one minute, while parti cles can remain within a ball mill system for 20 to 30 minCEMENTS GROUND IN THE VERTICAL ROLLER MILL FULFIL THE PROCESS TRAINING for operators of Vertical RAW Mills Heating of mill and grinding plant In fact there are three processes going on in the MPS mill namely grinding, drying and clas sifying, and only when all three processes are working well the operation is smoothPROCESS TRAINING for operators of Vertical RAW Millsthe first grinding pressures, when the mill differential pressure is relatively lower, the appropriate increase in the volume of feed, according to changes in differential pressure and the outlet Design and Realization Of Roller Mill Control System ResearchGate
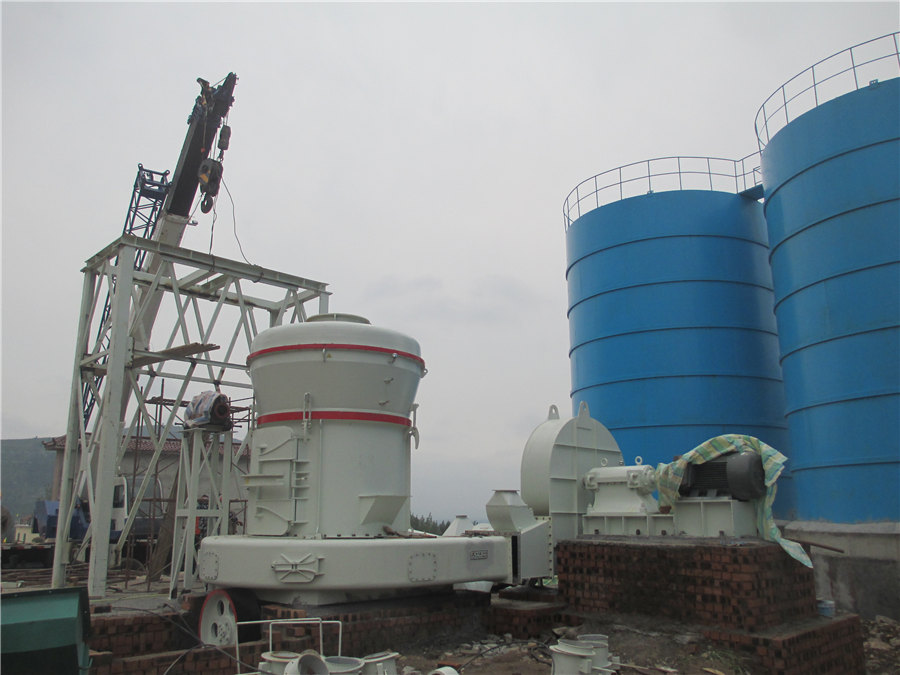
Machining 101: What is Grinding? Modern Machine
2021年7月3日 Different types of grains work better on different projects, as do different types and “grades” (ie strengths) of bond Broad areas of grinding need coarser grits and softer grades, with smaller areas requiring finer grits and 2015年3月15日 Vertical Agitated Media Mill modeling has become subject of a research project due to its potential application as a secondary grinding mill as well as regrind and pellet feed preparation projectsVertical Agitated Media Mill scaleup and simulation grinding circuits The correction for pressure drop is shown in Figure 7 and can be calculated from Equation 5 As indicated, a higher pressure drop would result in a finer separation and lower pressure drop in a coarser separation C 2 = 327 x 25% of the cyclone diameter to a maximum028 (Eq 5) Where C 2 = Correction for influence of The Sizing Selection of Hydrocyclones 911 MetallurgistVertical mill consists of main mill, classifier, fan, finished product cyclone separator, and air duct Among them, the main mill consists of frame, air inlet volute, shovel blade, grinding roller, grinding ring and housing HLM vertical roller mill Max feeding size: 50mm Capacity: 5200t/h Fineness: 200325 mesh (7544μm)News What Is Vertical Grinding Mill?
46.jpg)
EnergyEfficient Technologies in Cement Grinding IntechOpen
2015年10月23日 In this chapter an introduction of widely applied energyefficient grinding technologies in cement grinding and description of the operating principles of the related equipments and comparisons over each other in terms of grinding efficiency, specific energy consumption, production capacity and cement quality are given A case study performed on a 2013年3月1日 This study investigated a mathematical model for an industrialscale vertical roller mill(VRM) at the Ilam Cement Plant in Iran The model was calibrated using the initial survey's data, and the Cements ground in the vertical roller mill fulfil the quality The following is expanded from material provided by John Goff The US government’s HABS efforts produced a few drawings of mills including the Leffert’s Tide Mill These machines were also in the Souther Tide Mill Grist Mill (which we know from the fact that it was a grist mill, also from Josiah Adams Fenno’s descriptions Continue reading Grist MillsGrist Mills Tide Mill Institute2024年1月23日 Grinding Pressure The amount of pressure applied during grinding impacts the material removal rate, wheel wear, and potential for thermal damage Optimizing grinding pressure is vital for efficient and accurate grinding Machine Rigidity The rigidity of the grinding machine influences its ability to resist deflection under loadWhat is Grinding: Definition, Process, Types Specifications
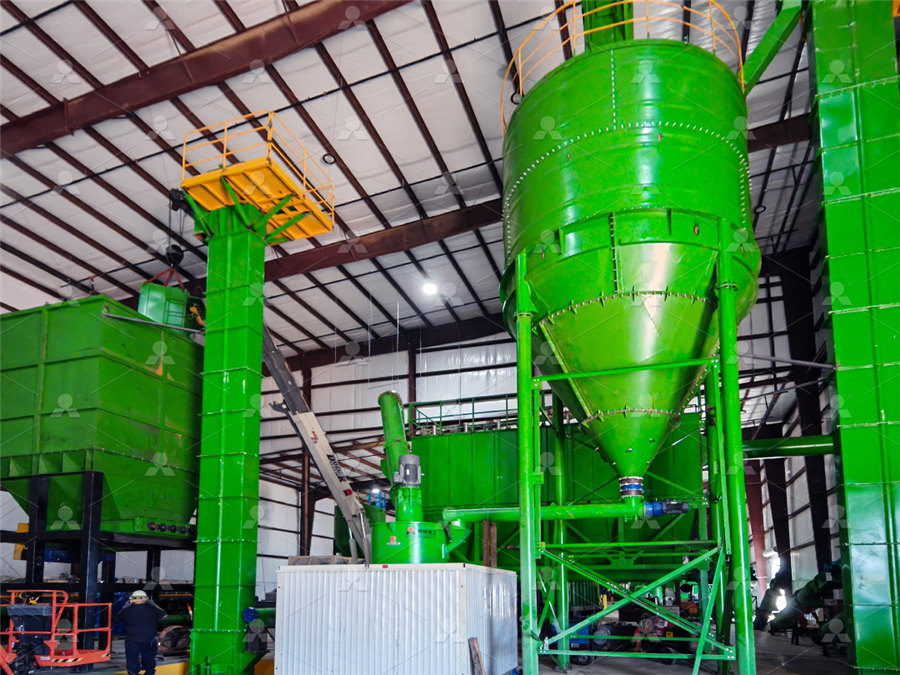
Understanding the operation of grinding mills in the mining and
Factors Affecting Grinding Mill Performance: 1 Grindability: The grindability of the ore affects the efficiency of the grinding mill Harder ores require more energy and longer grinding times, which can impact the mill's performance and operational costs 2The vertical mill has a mature grinding technology, which integrates crushing, drying, grinding, grading and conveying It can be widely used in cement, power, metallurgy, chemical industry, nonmetallic ore and other industries, and focuses on the three major fields of nonmetallic ore, coal powder and slagWhat can the vertical mill do? What are the advantages?Grinding and separation efficiency of vertical roller mill were evaluated In addition to these, performance figures of vertical roller mill and conventional closed ball mill circuit were comparedPerformance Evaluation of Vertical Roller Mill in Cement GrindingVertical Mill Calculations Free download as Powerpoint Presentation (ppt / pptx), PDF File (pdf), Text File (txt) or view presentation slides online There are two main layouts for a vertical roller mill (VRM) system, with product collection Vertical Mill Calculations PDF Mill (Grinding)
.jpg)
BALL MILLS Ball mill optimisation Holzinger Consulting
efficient grinding systems available for the cement and mineral industry, including vertical roller mills (VRM), highpressure grinding units (HPGR) or simple roller presses, as well as the most traditional type of installation: ball mills, combined in circuit with an air classification system of varying generations and sophisticationsThe basic working principle of a vertical mill involves the interaction of several key components At the core of the mill is a large vertical grinding table, which rotates at a controlled speed Above the grinding table, there are several rollers that apply pressure onto the material being groundIndepth understanding of the working principle of vertical millsVertical roller mill specific grinding energies were lower than those for a ball mill at all product sizes, and when estimates of classification energy and scaleup of the VRM are included, the specific energy for the vertical roller mill is up to 35% lower than for a ball mill in closed circuitPerformance of the vertical roller mill in a mineral processing Working principle and characteristics of vertical mill Working principle The working principle of a vertical mill involves the rotation of a grinding table with rollers attached to it Raw materials are fed into the table and ground between the rollers and table The ground materials are then blown by hot air through an outlet in the mill's Working principle and characteristics of vertical mill
.jpg)
COMPARISON OF GRINDING EFFICIENCY BETWEEN BALL MILLS
COMPARISON OF GRINDING EFFICIENCY BETWEEN BALL MILLS AND VERTICAL ROLLER MILLS IN COARSE GRINDING Yakup Umucu 1, Vedat Deniz 2,Osman Mart 1 Abdi Kemal Y!ce 1, Mehmet Fahri Sara" 3 1 S leyman A gristmill is the building with the machinery to do the grinding Therefore, grist for the mill can mean the useful ingredients that the mill will use to make a profit If something is grist for the mill, it is something that can be taken to the mill and turned into a useful product As early as the 1500s people were using this phrase What Does Grist for the Mill Mean? Writing ExplainedA vertical roller mill, also known as a vertical grinding mill or vertical mill, is a comprehensive grinding equipment integrating crushing, drying, grinding, grading, and conveying Vertical grinding mills can be widely used in electric power, metallurgy, construction, chemical industry, and other industries to make powder, especially for materials such as cement clinker, coal Energysaving and Efficient Vertical Roller Mill Fote Machinery3 PRINCIPLES OF VERTICAL GRINDING SYSTEMS 31 – VERTICAL MILL COMPONENTS Image 1 shows a vertical mill and its components: Grinding plate Rollers pressing the material on the grinding plate Pressure system of the grinding rollers Hot gas flow for drying the raw materials and cement temperature control Dynamic third generation separatorTechnical Notebook CEMENT ADDITIVES FOR VERTICAL MILLS
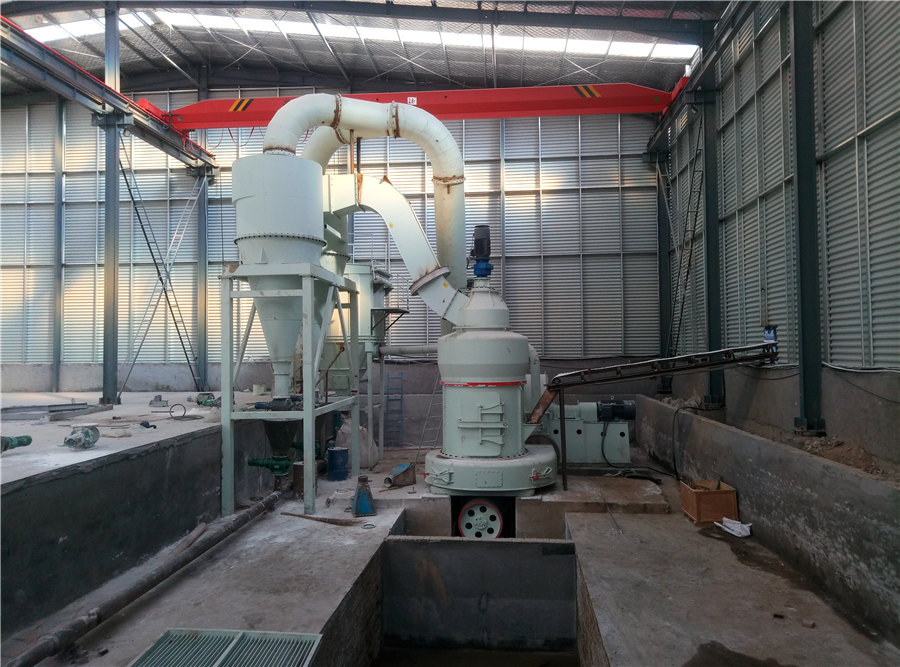
PROCESS CONTROL FOR CEMENT GRINDING IN VERTICAL ROLLER MILL
pressure difference between inlet and outlet, the grain size of the raw material [1, 2] For VRM the production capacity denotes both the capacity of grinding and drying of mill The grindability affects the capacity of grinding, type of mill and roller pressure The capacity of the mill is calculated Using G K * D 2517 // Almost any plant for the grinding of cement raw material is a combination of machines specially adapted to the particular physical properties of the material to be ground As a result, our plants work efficiently without any trouble » Highly efficient grinding, drying, and separating in one unit » Outstanding production capacities exceeding 1,400 t/h in one single millPFEIFFER MILLS FOR THE CEMENT INDUSTRY2023年12月4日 A vertical roller mill (VRM) is a grinding equipment used for the size reduction of minerals, cement, and ceramics The capacity of the VRM depends not only on the grinding material properties but also on the operational parameters of the VRM This study investigatedNumerical Investigation of Vertical Roller Mill Operation Using The “flowsheet of the future” uses highpressure grinding rolls as an alternative to a semiautogenous grinding mill, and vertical stirred mills in open circuit as an alte rnative to ball milling When co mbined with coarseparticle flotation technology, which allows improved metal recoveries at a coarser flotation feed size, the combinationFlowsheet of the Future: HighPressure Grinding Rolls, Vertical
.jpg)
Operational parameters affecting the vertical roller mill
2017年4月1日 In the airswept mode, the verticalrollermill and a high efficiency dynamic classifier are suited above each other as a single unit (Fig 1) Material is fed to the grinding chamber and transported by table rotation to the grinding gap between the fixed grinding rollers and the mill table Crushing and grinding take place by compressive grinding1 What is a Vertical Grinding Mill? The Vertical Grinding Mill (VGM) is an upright steel vessel with an inlet, an outlet and a central portion of the inlet It is used for fine size reduction when output to input reduction required is large These mill crushers consist of a reducing rotating mill for size reduction The whole closed circuit is Vertical Grinding Mill: How it Works, Application And AdvantagesVertical cement mill pressurize with a hydraulic system, the pressure acts on the material between the grinding roller and the grinding disc, so as to achieve the purpose of grinding Vertical cement mill is applied for the processing of nonflammable and nonexplosive mineral materials with mohs hardness below grade 8 and humidity less than 10%Vertical Cement MillBall race mill (Petersmill of the Claudius Peters Joint Stock Company, Hamburg, Germany) The cement industry employs the Petersmill (pre viously called FullerPetersmill) mostly for coal grinding It is a few years now that the shockproof construction (shock resistance – 35 bar) of the Petersmill was designed for coal grindingRoller mills INFINITY FOR CEMENT EQUIPMENT
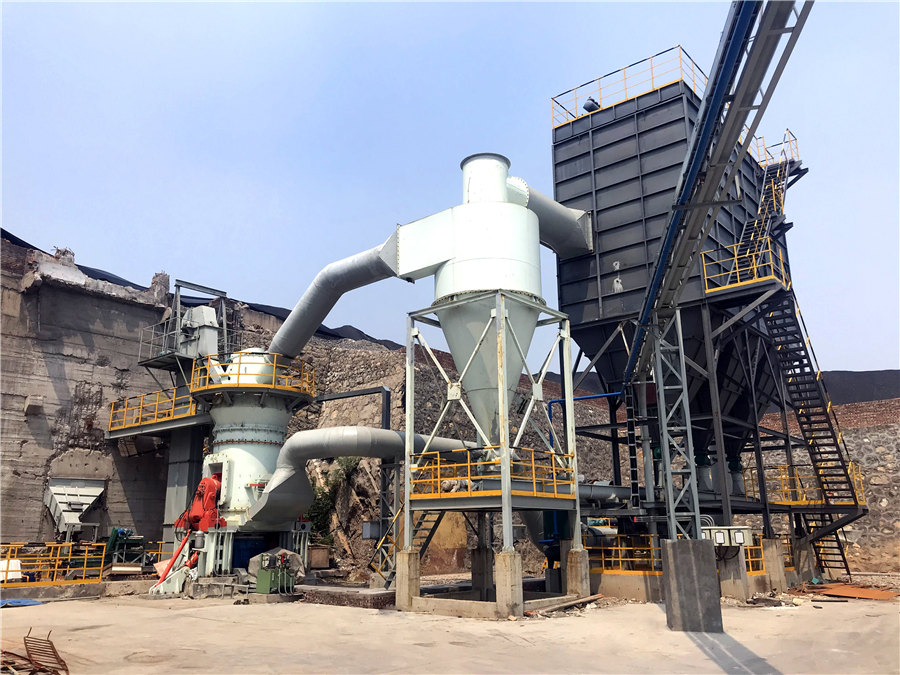
How it Works: Crushers, Grinding Mills and Pulverizers
2017年6月2日 Autogenous grinding (AG) and semiautogenous grinding (SAG) mills use the material to be ground as the grinding media Autogenous grinding mills use larger rocks to impact and break smaller rocks as the mill rotates Semiautogenous mills are basically the same autogenous mills, but with the addition of balls, similar to those in ball mills2020年6月15日 Inside the grinding housing, the raw material is reduced not only by the repeated blows of the hammer but by the walls of the grinding chamber and the impact of particle on particle Specially designed metal screens or steel grates classify the material and discharges it once it’s been reduced to its desired sizeUnderstanding the Working Principle of Hammer Mills Prater