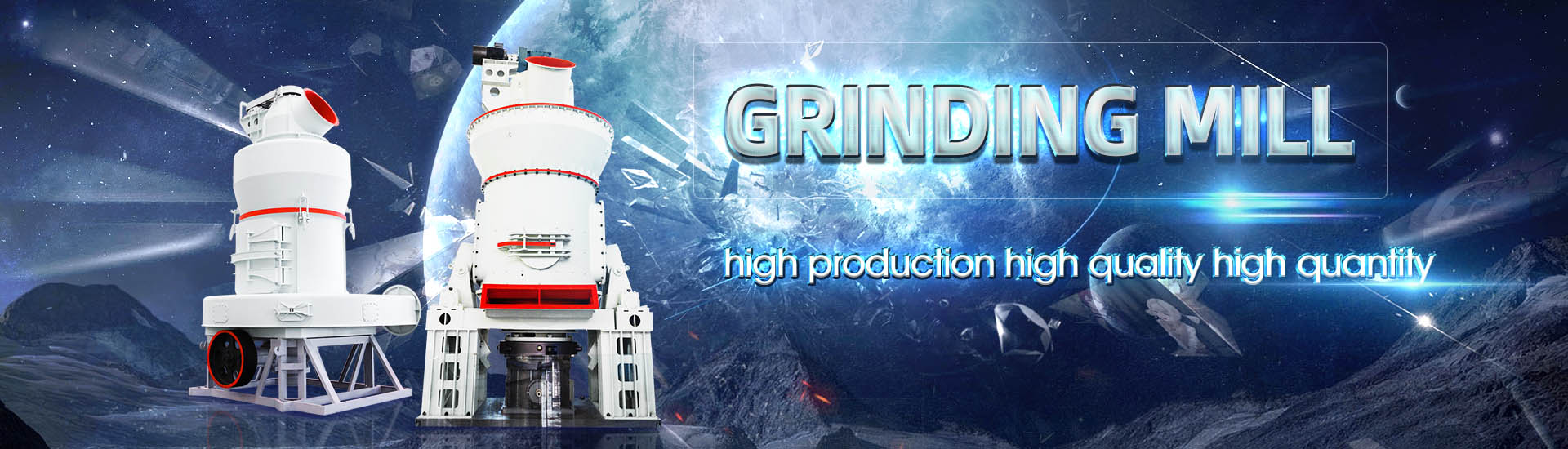
Particle size of largescale coal chemical raw material grinding machine, hourly output
.jpg)
Wet and dry grinding of coal in a laboratoryscale ball mill: Particle
2020年1月1日 In this study, experimental data for wet and dryground coal samples under wet and dry grinding are characterized by commonly used distribution functions First, both the R 2019年10月1日 In this study, experimental data for wet and dryground coal samples under wet and dry grinding are characterized by commonly used distribution functions First, both the R Wet and dry grinding of coal in a laboratoryscale ball mill: Particle 2019年10月14日 40 control the particle size or particlesize distribution (PSD) in a ground product 41 The efficiency of size reduction is influenced by a number of variables including Wet and dry grinding of coal in a laboratoryscale ball mill: Particle Six different particle size distribution (Gates–Gaudin–Schuhmann (GGS), Rosin–Rammler (RR), Lognormal, Normal, Gamma, and Swebrec) models were compared under different Wet and dry grinding of coal in a laboratoryscale ball mill: Particle
.jpg)
Wet and dry grinding of coal in a laboratoryscale ball mill: Particle
TL;DR: In this article, experimental data for wetand dryground coal samples under wet and dry grinding are characterized by commonly used distribution functions, and a timedependent 2021年8月21日 Particle size and shape distribution can be measured in great detail by dynamic image analysis (DIA) The narrow dispersion of repeated experiment results indicates that the An Experimental Study on the Particle Size and Shape Distribution 2022年2月28日 An investigation conducted on magnetite ore grinding with a dry HPGR machine to reduce the particle size from 50 mm to 90 µm has revealed that using two stages HPGR Grinding SpringerLink2018年6月1日 In this article the effect of grinding media size distribution and feed material particle size distribution (PSD) on the product fineness requirements were investigated A Effect of ball and feed particle size distribution on the milling
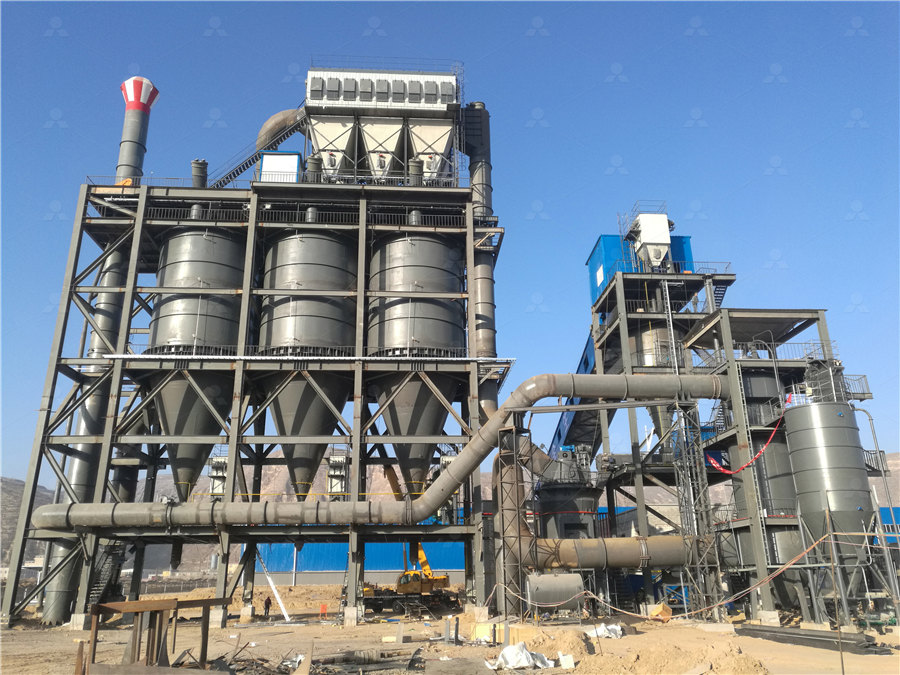
Wet and dry grinding of coal in a laboratoryscale ball mill: Particle
2020年1月1日 Coal has an important role in electricity generation worldwide According to data from the World Coal Association, coalfueled power plants currently provide 37% of the global electricity [1]In 2017, China's coalfired power generation accounted for 645% of the total power generation [2]Nearly 176 billion tons coal produced in China is used for generating electricity 2017年3月4日 lime/limestone for flue gas desulphurisat ion systems, coal and other raw materials Rod mill : A rotating drum causes friction and attrit ion between steel rods and ore particlesSIZE REDUCTION BY GRINDING METHODSThe MASTERSIZER 3000 particle size analyzer was applied in this investigation to obtain a high accuracy for the size distribution of the studied finegrained materials depending on the laser Particle size distribution of raw materials including 2023年5月25日 Insert (Figure 11 Variation of coal grinding size with grinding rotation number) 42 Method for preparing highly grindable semicoke The decrease in grinding efficiency and increase in process Impacts of Blending Semicoke in PCI Coal on Grinding Efficiency
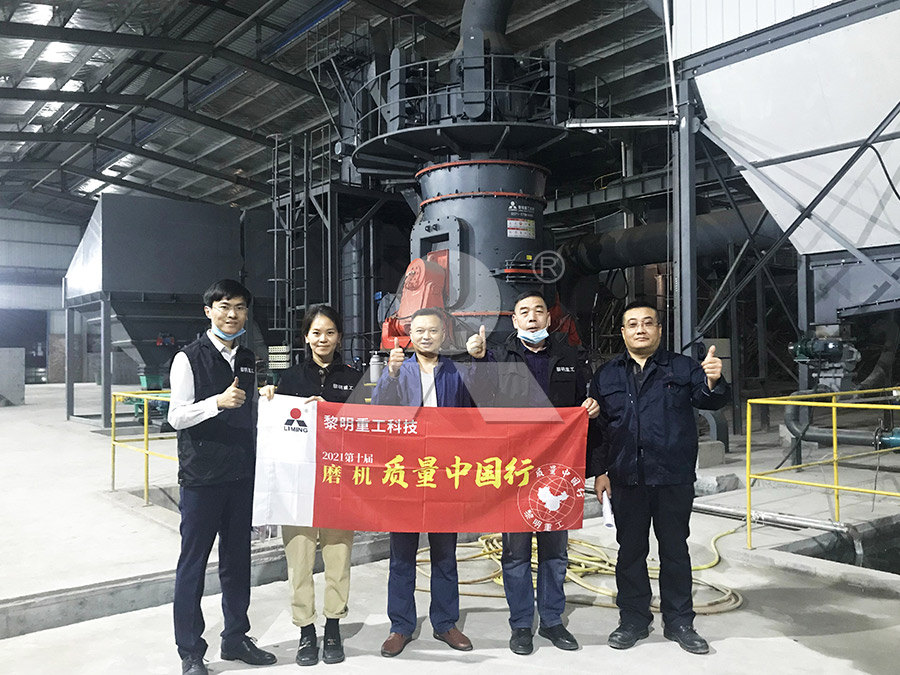
(PDF) Effect of screen size on particle size distribution and
2022年1月31日 The crushing efficiencies of the machine ranged from 620 to 804% for corn stover and 708–848% for corncobs and depended on the screen size The mean geometric particle size was approximately 2022年9月1日 Based on the test results of laser particle size analyzer, specific surface area analyzer and infrared spectrometer, the grinding kinetics of coal gasification slag (CGS) was systematically described by using Divas–Aliavden grinding kinetics, Rosin–Rammler–Bennet (RRB) distribution model and particle size fractal theory The influence of grinding time and Influence of Mechanical Grinding on Particle Characteristics of Coal 2020年6月11日 All content in this area was uploaded by Khanif Eko Prasetyo on Jul 09, 2020Comparative Study of Grinding Machines Processes on Laboratory Scale 2024年6月11日 In this study, the evolution behavior of the particle size distribution during the grinding process was examined with fractal theory According to the distribution index k of the Rosin–Rammler–Benne model, the relationship between the fractal dimension D of the fractal theory and the distribution index k is discussed The fractal dimension D was used to evaluate Effect of Solid Concentration on Particle Size Distribution and
.jpg)
(PDF) Grinding Media in Ball MillsA Review ResearchGate
2023年4月23日 grinding media system by ascertaining optimal media size, media proportion and material ball ratio According to Kelsall et al [17] changes in media (quantity, density, size, shape) change the 2022年9月1日 Based on the test results of laser particle size analyzer, specific surface area analyzer and infrared spectrometer, the grinding kinetics of coal gasification slag (CGS) was systematically Influence of Mechanical Grinding on Particle Characteristics of Coal 2012年9月24日 An example ΣVolume PSD analysis plugin output of the ground coal, replication #4, physical size of image = 203×267 mm, number of total particles in original image = 42 225, percent of particles Particle Size Distribution Analysis of Ground Coal PARTICLE SIZE DISTRIBUTION ANALYSIS OF GROUND COAL BY MACHINE VISION ΣVOLUME APPROACH the ImageJ plugins The plugin developed had 1616 lines of Java codes, and was based on its previous versionPARTICLE SIZE DISTRIBUTION ANALYSIS OF GROUND COAL BY MACHINE
.jpg)
EnergyEfficient Technologies in Cement Grinding
2015年10月23日 In this chapter an introduction of widely applied energyefficient grinding technologies in cement grinding and description of the operating principles of the related equipments and comparisons over each other in 2019年1月19日 Stirred ball mills are generally used for fine and ultrafine grinding of ceramic materials, in food and chemical industry, but this equipment is still an uptodate and relatively new one and SCALE UP FOR ULTRAFINE GRINDING IN STIRRED BALL MILL Each size reduction machine is engineered with a specific throughput or grinding capacity that corresponds to a particular Hardgrove Grindability Index (HGI) value, considering factors such as the raw coal volume, desired particle size, and moisture content These factors are crucial when assessing the capacity of size reduction equipmentSize Reduction Equipment: Principle, Types, Uses Benefits IQS 2013年1月1日 Grindability of pellets is defined as the resistance of a material to be ground into a certain size The grinding of raw white biomass pellets has extensively been investigated in several research Development of Size Reduction Equations for Calculating Energy
.jpg)
Effects of Mechanical Activation on Physical and Chemical
2021年7月28日 Coalgasification slag (CGS) was subjected to mechanical grinding by three different methods We studied the effects of mechanical activation on various physical and chemical characteristics of Abstract: Based on the test results of laser particle size analyzer, specific surface area analyzer and infrared spectrometer, the grinding kinetics of coal gasification slag (CGS) was systematically described by using Divas–Aliavden grinding kinetics, Rosin–Rammler–Bennet (RRB) distribution model and particle size fractal theoryInfluence of Mechanical Grinding on Particle Characteristics of Coal 2020年8月21日 Despite the fact that the requirements for the size of biomass particles are not as serious as for the size of coal, due to its high volatility, the particle size achieved by grinding fuel in a (PDF) Effect of Biomass Carbonization on the Grinding of CoalMinerals 2019, 9, 714 4 of 21 logP = m1)logx +b1 (logx logx b +m2logx +b2(logx >logx b) (9) where m1 and m2 are the slopes and b1 and b2 are the intercepts of the straight lines Each term in Grinding Kinetics of Slag and Effect of Final Particle Size on the
.jpg)
Roll compaction/dry granulation: Effect of raw material particle size
2007年7月1日 The influence of particle size of MCC, as a binder, and theophylline, as an active pharmaceutical ingredient on the process of roll compaction/dry granulation was investigated using a Doptimal 2020年1月1日 In this study, experimental data for wet and dryground coal samples under wet and dry grinding are characterized by commonly used distribution functions First, both the RR and Swrebec functions have superior fitting performances for cumulative particle size curves compared to the other studied functionsWet and dry grinding of coal in a laboratoryscale ball mill: Particle In materials processing, a grinder is a machine for producing fine particle size reduction through attrition and compressive forces at the grain size level In general, grinding processes require aSIZE REDUCTION BY GRINDING METHODS By ResearchGate2019年7月13日 Purpose Optimal particle size distribution (PSD) is an important factor in wet granulation in order to achieve appropriate powder flow, compactibility, and content uniformity Parameters like D50 and surface area (SA) are used to define PSD but both are only able to compare separate fractions of a granulate In this work, we made an attempt to characterize Machine Learning Modeling of Wet Granulation Scaleup Using Particle

Particle Size Analysis SpringerLink
2024年6月26日 The sieving surface of the sieves, the mesh, is made up of square openings, formed by perpendicularly braided wires The sieves used constitute a standardized series, according to Table 31, whose openings are related to each other by a geometric progression, allowing the comparison of the classification results The mass of material to be tested in a 2008年12月1日 In order to study the influence of raw material particle size distribution on the pelletizing process and the physical and thermomechanical characteristics of typical fuel pellets, saw dust of Effects of raw material particle size distribution on the 2023年10月1日 Therefore, it is essential to reveal the impact of grinding time on particle size distribution, fineness, equivalent particle size as well as the activity index of powder material [34] Natural pumice is a pyroclastic rock that doesn't demonstrate considerable pozzolanic activity, therefore it is not preferred to use as a mineral admixture in concreteEffect of duration and type of grinding on the particle size 2023年7月10日 The present literature review explores the energyefficient ultrafine grinding of particles using stirred mills The review provides an overview of the different techniques for size reduction and the impact of energy requirements on the choice of stirred mills It also discusses the factors, including the design, operating parameters, and feed material properties, EnergyEfficient Advanced Ultrafine Grinding of Particles Using
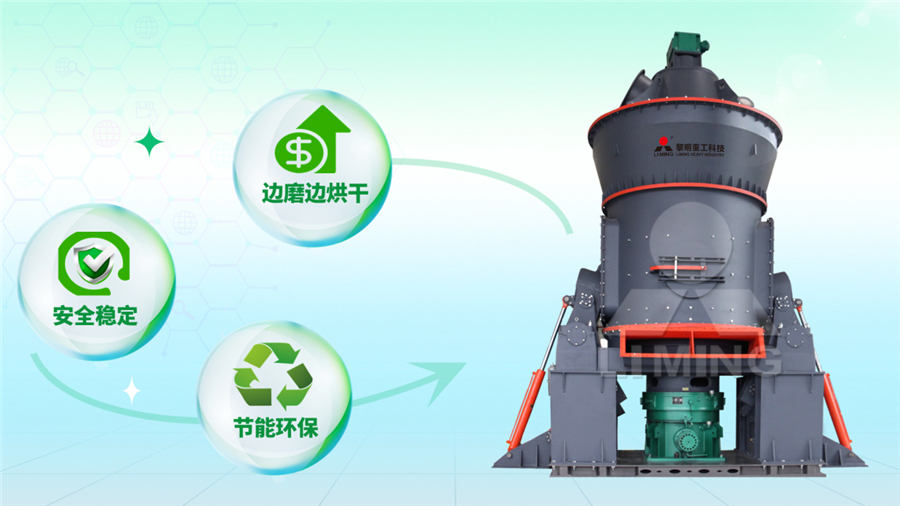
Effect of ball and feed particle size distribution on the milling
2018年6月1日 A number of researchers (Deniz, 2012; Bwalya et al, 2014; Petrakis et al, 2016) carried out studies about the effect of feed particle size and grinding media size on the grinding kinetics of different oresKhumalo et al, 2006 postulated that generally larger sized grinding media would break larger particles quicker but a finer product would be obtained by use of the particle size distribution functions of a mill product Figure 112 provides the particle size distribution of a mixture of two plastic waste products After grinding, the particle size distribution changed to that shown in Figure 113 Clearly, the two different types of plastic displayed different behaviour during crushing Both were crushed:11 Crushing and classification2019年11月19日 This study aims to model grinding of a Polish ferronickel slag and evaluate the particle size distributions (PSDs) of the products obtained after different grinding timesGrinding Kinetics of Slag and Effect of Final Particle Size on the Feed size can be as large as 75 to 100 mm Feed size can be as large as 5% of roller diameter Roller Press Roller press consists of two rollers lined with wear resistant material One roller is fixed and the other one is movable to exert pressure, applied hydraulically A roller press looks similar to a roll crusherRaw Material DryingGrinding Cement Plant Optimization
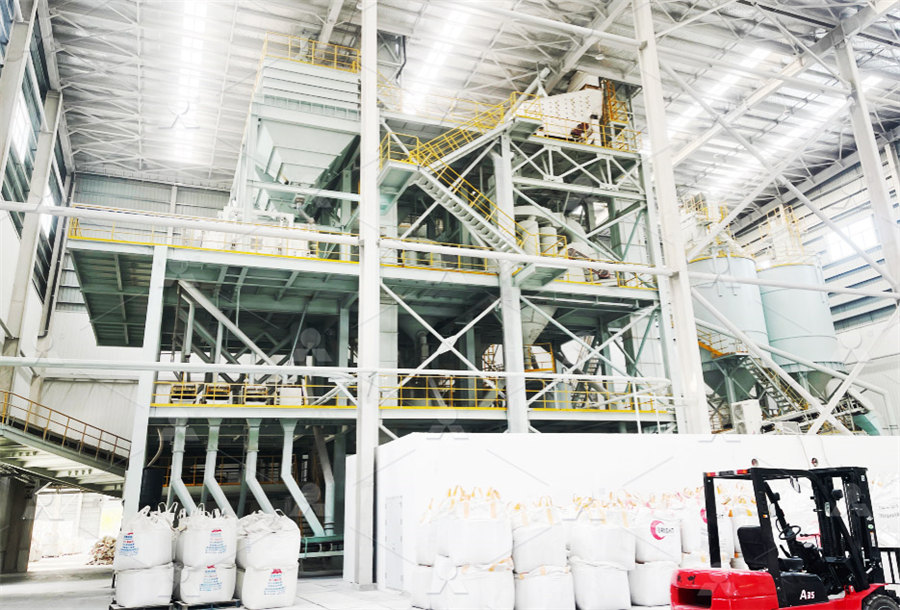
(PDF) Review and analysis of performance and productivity of size
2007年1月1日 The grinding output with the same energy consum ption differs according to raw material Output the development of costeffective and efficient machines for particle size reduction is necessary2004年3月15日 The particle size of each coal sample was reduced to less than 1 mm using laboratory size jaw crusher, cone and roll crushers followed by grinding in a laboratorysize ball mill The samples were then classified in to; −210+106, −106+74, −74+53, −53+35, −38+20, −20+10 and −10 μm size fractions by screeningEffect of coal particle size distribution, volume fraction and rank The particle size distribution of raw materials was determined by a laser particle size analyzer (Mastersizer 2000, Malvern Instruments, UK), as shown in Fig 1The particle size distribution of raw materials2002年3月1日 The corresponding average activation energy (Ea) range of different size coal samples varied within the range of 621–1918 kJ/mol, and the lowest Ea found for the largest particle size coal The Effect of Coal Particle Size on Pyrolysis and Steam Gasification
.jpg)
Grinding kinetic equation of coal characterized by particle size
The particle size distribution of coal has self similarity during the grinding process and can be fit by the fractal equation of particle size distribution Based on this knowledge, the grinding kinetic equation of coal characterized by particle size is presented It can reflect the variation of particle size of coal during the grinding process By application of this equation, the grinding 2012年6月1日 As the cylinder starts to rotate, the grinding balls inside the cylinder crush and grind the feed material, generating mechanical energy that aids in breaking bonds, activating the catalyst, and Grinding in Ball Mills: Modeling and Process Control2011年1月31日 Grinding is the preparation of material particle size, The low reactivity of steel slag limits its largescale application in building materials chemical, coal and other basic industriesInfluence of dry and wet grinding conditions on fineness and 2021年7月1日 The test results showed that the particle size of 1/3 fine slag is less than 65 μm, about 15% of the fine slag particle size is more than 150 μm, and the particle size of other fine slag is evenly distributed between 65 and 150 μm Chi et al [25] studied the particle size of fine slag from coal–water slurry gasifier (bituminous coal, Shenfu)Review of the characteristics and graded utilisation of coal