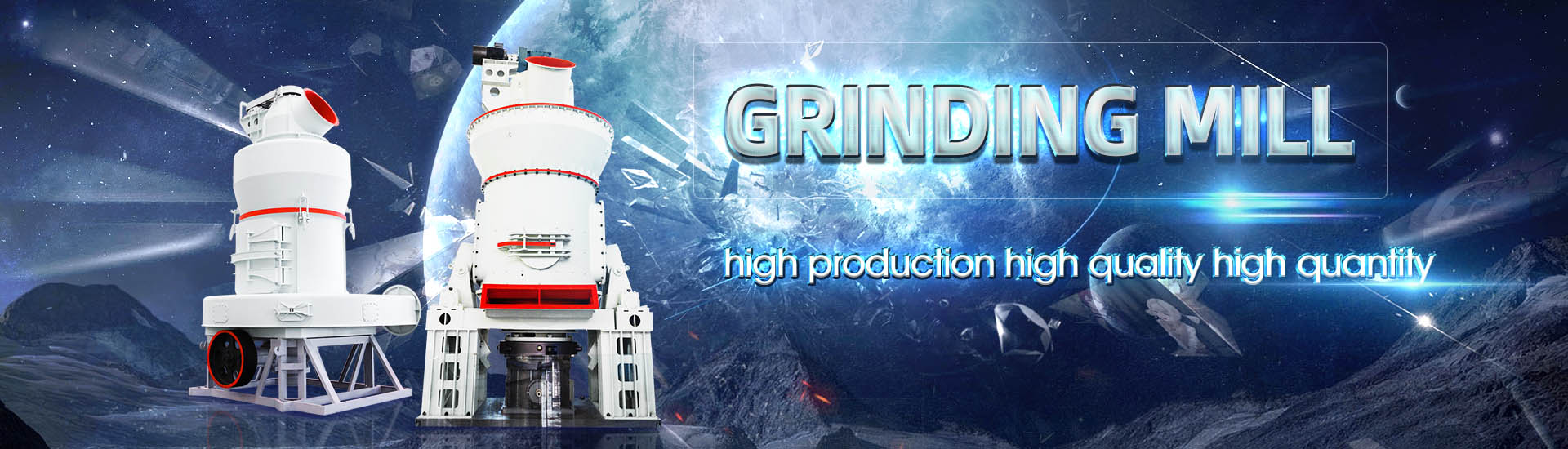
Ore mill selection misunderstanding
.jpg)
Primary Grinding Mills: Selection, Sizing And Current Practices
PRIMARY MILLS SELECTION Inherent Characteristics of Primary Grinding Primary grinding is complex because it involves several comminution mechanisms which occur simultaneously Understanding Mine to Mill is presented in five parts Part A – Setting the Scene provides some definitions of Mine to Mill (M2M) and the historical background A chronology of Mine to Mill UNDErsTaNDINg MINE TO MILL 911 MetallurgistThe purpose of this study is to understand how ore loss and dilution affect the mine call factor, with the aim of subsequently improving the quality of ore mined and fed to the mill It was necessary to know the relationship between ore Monitoring ore loss and dilution for minetomill ore sources Outcomes from reconciliation studies may be put into two categories; misclassification of significant tonnages of ore grade material (common), and discovery of Ore Grade Reconciliation Techniques – A Review Mining Geology
.jpg)
A Review of the Grinding Media in Ball Mills for Mineral Processing
2023年10月27日 Grinding media play an important role in the comminution of mineral ores in these mills This work reviews the application of balls in mineral processing as a function of the 2014年10月15日 Dualenergy Xray transmission has been used to sort ore from different mines, and an analysis identifying the economic impact of these results is presented Significant Development of ore sorting and its impact on mineral processing 2014年6月1日 Ore characterizationrelated losses continue to represent a major cost factor for mining, routing, processing and tailings handling Debottlenecking of existing or recent design Ore characterization, process mineralogy and lab automation a 2016年2月1日 The purpose of this study is to understand how ore loss and dilution affect the mine call factor, with the aim of subsequently improving the quality of ore mined and fed to the mill It wasMonitoring ore loss and dilution for minetomill
.jpg)
Mineral Processing SpringerLink
2017年8月24日 The first difference between the mills is in the ratio diameter/length of the cylinder and the features of grinding media employed: steel rods, steel ( Fig 614) or ceramic 2018年10月1日 Simulations using JKSimMet provided some insight on the impact of ore breakage variability on SAG mill performance The standard JK drop weight test breaks single Quantifying variability of ore breakage by impact ScienceDirectThe rod mill is another type of grinding mill used in the copper ore mining process This machine uses steel rods as the grinding media instead of balls, which are commonly used in ball mills The rods grind the ore by tumbling Understanding the SAG Mill in Copper Ore Mining 3 BALL MILL MODEL The population balance model may be expressed by Equation (1): > @ ¦ i1 1 i b ij m j j i j i S Ht dt d H m t (1) where: S i (t) is the size discretized selection function for Population balance model approach to ball mill optimization in iron ore
.jpg)
SAG Mill Design and Benchmarking Using Trends in the JKTech
Figure 3(a)—Pilot SAG mill Ecs vs Ball Load, Reproduced from Morrell (2006a); (b) SAG Mill Ecs vs Ball Load for ‘OpenCircuit’ SAG Mills in JKTech Database 0 2 4 6 8 10 12 14 16 18 20 0 2 4 6 8 10 12 14 SAG mill Ecs (kWh/t) Ball load (%) 0 5 10 15 20 SAG mill Ecs (kWh/t) Ball load (%) Coarse feed, uncrushed pebbles Very soft ores, Axb >年2月21日 For finegrinding machines, the coffeemill type still successfully holds its own against most of the newer devices, although the modern samplegrinder is much heavier, better built, and more easily cleaned than its predecessors The first mechanical samplers were imitations of Cornish quartering, the ” whistlepipe ” being the most common Ore Sampling Methods: Good Proper 911Metallurgist2023年10月17日 Ultrafine powder mill (threering / fourring mediumspeed micropowder mill) feed particle size ≤25 mm, production capacity 0545 t/h, production fineness 1503500 mesh,it is a highefficiency and lowconsumption ultrafine powder processing equipment that successfully replaces the traditional jet mill and complex process ball mill grinding and powder selection, How to choose a suitable ore powder grinding mill?2016年2月1日 The purpose of this study is to understand how ore loss and dilution affect the mine call factor, with the aim of subsequently improving the quality of ore mined and fed to the millMonitoring ore loss and dilution for minetomill integration in
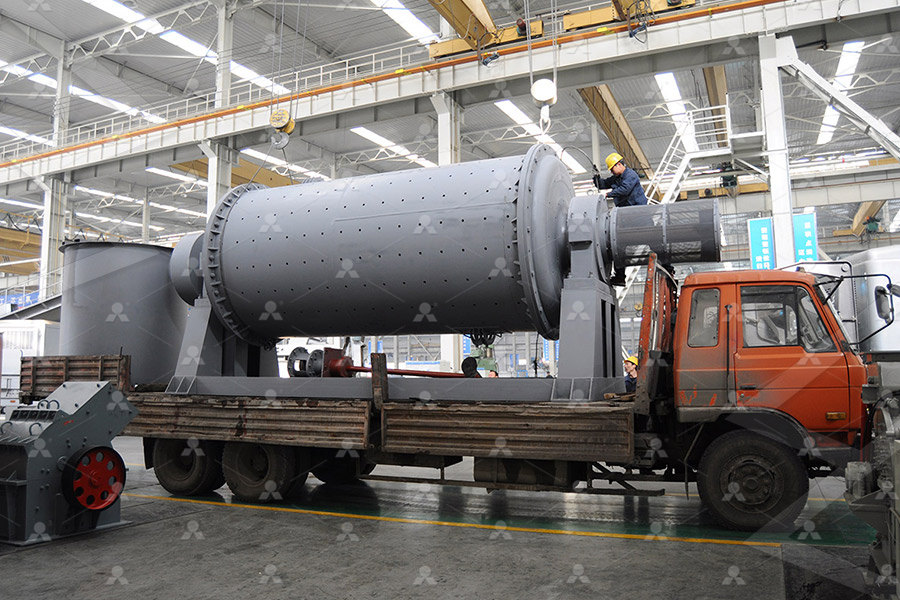
Simulation of industrial PGM and iron ore ball milling circuits from
2023年4月20日 The specific selection function is then described by Herbst and Fuerstenau (1980) primary ball mill grinding PGMs ore demonstrated that parameters calibrated based on batch2020年1月3日 Iron ores obtained from different sources differ in their chemical and physical properties These variations make the process of grinding a difficult task The work carried out in this context focuses on three different samples of iron ore, viz, high silica high alumina, low silica high alumina, and low silica low alumina The grinding process for all the three iron ores is Estimation of Grinding Time for Desired Particle Size Distribution Page 770 INTRODUCTION Pilotscale testwork based on a 6' x 2' mill is arguably still the most reliable method for predicting full scale autogenous (AG) and semiautogenous (SAG) grinding mill AG and SAG Mill Circuit Selection and Design by SimulationThe present work analyzes comminution of a Brazilian iron ore with unusual breakage behavior in batch and pilotscale tests, as well as in an industrial mill, which demonstrated the application of the scaleup approach in optimizing the fullscale mill when operating at di erent slurry concentrations 2 Mathematical BackgroundOptimization of Solids Concentration in Iron Ore Ball Milling
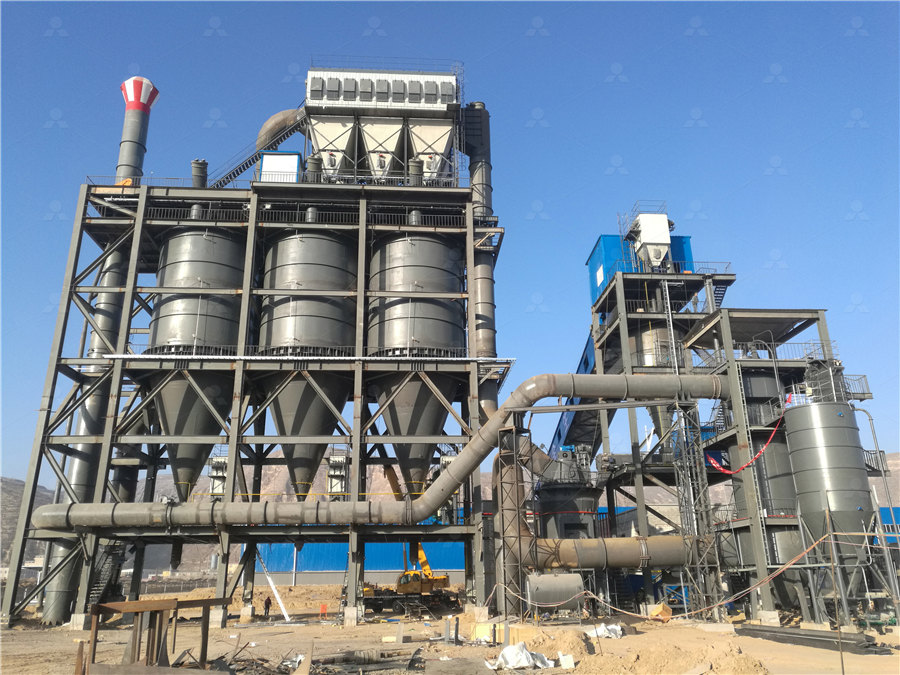
Ore Mill Bar Grille
*signature "mill burger" 1695 A 6oz angus burger, topped with cheddar cheese, bacon, pastrami, fried egg, jalapeno, lettuce and mayonnaise served on a brioche bun orbuild your own burger!2013年4月16日 ABSTRACT In this study, ultrafine grinding of a refractory silver ore tailings was studied A laboratory scale pintype vertical stirred mill and ceramic beads were employed for the grinding tests(PDF) Investigation of some parameters affecting the Ultrafine 2013年8月3日 In Grinding, selecting (calculate) the correct or optimum ball size that allows for the best and optimum/ideal or target grind size to be achieved by your ball mill is an important thing for a Mineral Processing Engineer AKA Calculate and Select Ball Mill Ball Size for Optimum 2017年11月1日 To understand the friction and wear of working mediums in iron ore ball mills, experiments were conducted using the ball cratering method under dry and wet milling conditions, which mimic the operating conditions in ball mills The liner sample is made of Mn16 steel, the ball had a diameter of 25 mm and was made of GCr15 steel, and the iron ore powder was Friction and wear of liner and grinding ball in iron ore ball mill

(PDF) Sensor‐Based Ore Sorting Technology in Mining—Past,
2019年8月29日 Sensor‐Based Ore Sorting Technology in Mining—Past, the shaft and mill but also as the selection of a size range in which natural conc entration of a wanted or unwanted 2011年2月1日 Request PDF Understanding fine ore breakage in a laboratory scale ball mill using DEM DEM models of fine grinding in ball and stirred mills have to date almost entirely focused on the motion Understanding fine ore breakage in a laboratory scale ball mill using Estimation of Grinding Time for Desired Particle Size Distribution and for Hematite Liberation Based on Ore Retention Time in the Mill Harish Hanumanthappa1 Harsha Vardhan1 Govinda Raj Mandela1 Marutiram Kaza2 Rameshwar Sah2 Bharath Kumar Shanmugam1 Received: 27 August 2019 /Accepted: 16 December 2019Estimation of Grinding Time for Desired Particle Size Distribution2009年10月1日 Request PDF Batch Grinding in Laboratory Ball Mills: Selection Function The selection functions and the breakage distribution functions are based on the experimentallydetermined particle size Batch Grinding in Laboratory Ball Mills: Selection Function
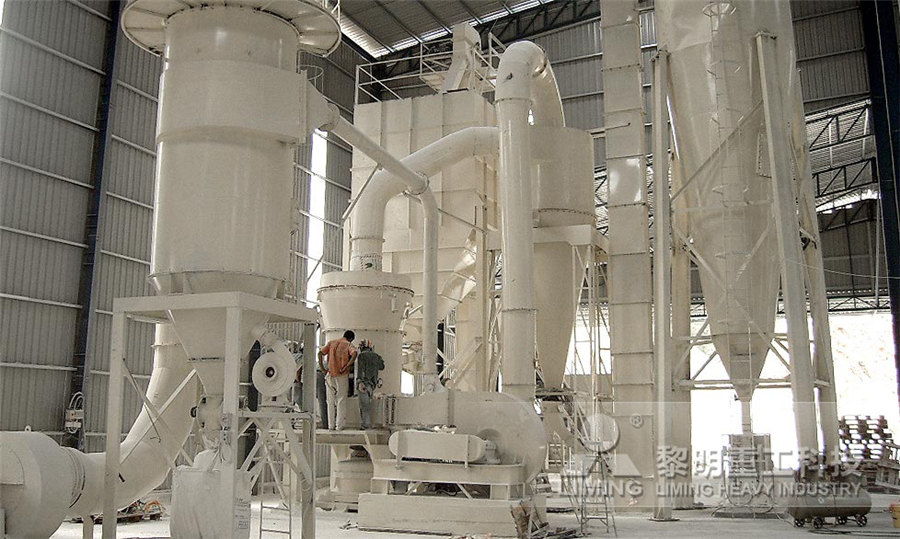
SAG Mill Grinding Circuit Design 911Metallurgist
2016年6月6日 Feed characteristics in terms of ore hardness/competency; Feed size distribution; Selection of circuit configuration in terms of liner and grate selection and closing size (screen apertures or hydrocyclone operating conditions) Ball charge (fraction of 2019年9月24日 There are numerous examples in the literature, some of which are quantifying the effect of Mine to Mill Grundstrom et al, 2001;Hart et al, 2001;Scott et al, 2002;Burger et al, 2006;Jankovic et al Simulating the Impact of Ore Competence Variability on Process AG AND SAG MILL CIRCUIT SELECTION AND DESIGN BY SIMULATION Dr S Morrell' and Dr R D Morrison2 1 Manager Comminution Research, 2 Manager, JKTech (SAG) grinding mill behaviour when treating a given ore However, the cost of a detailed pilotmill programme both in terms of providing sufficient sample material as well as theAG and SAG Mill Circuit Selection and Design by Simulation2011年2月1日 In contrast, for SAG mills which were first modelled by Rajamani and Mishra (1996) and subsequently by others (Cleary, 2001a, Cleary, 2001c, Herbst and Nordell, 2001, Morrison et al, 2001, Morrison and Cleary, 2008) at least some fraction of the rock ore has been included Cleary (2004) showed that modelling the complete mill with 95% of the rock size Understanding fine ore breakage in a laboratory scale ball mill using
.jpg)
Unlocking the Secrets of Gold Ore Mill: A Comprehensive Guide
Gold Ore Mill The mining industry configurations include singlestage AG/SAG mills followed by ball mills or twostage AG/SAG mills followed by a ball mill circuit The selection depends on factors such as hardness of the ore, desired grind size, and energy requirements 3 SAG MILL TESTING AN OVERVIEW OF THE TEST PROCEDURES AVAILABLE TO CHARACTERIZE ORE GRINDABILITY AUTHOR: FO VERRET, G CHIASSON AND A MCKEN SGS KEYWORDS Comminution, grindability, grinding, SAG mill, AG mill, milling, HPGR, work index, pilot plant INTRODUCTION The resistance of ore samples to breakage (or hardness) is SAG Mill Testing Test Procedures to Characterize Ore GrindabilityThese variables were investigated in regard to the Itakpe iron ore A representative sample of 105kg of the iron ore was collected and milled, taking appropriate quantities to study the process variables; the effect of grinding time, fraction of mill critical (PDF) Estimation of Grinding Time for Desired Particle Size 2019年4月15日 This paper presents a machine vision method for detection and classification of copper ore grains We proposed a new method that combines both seeded regions growing segmentation and edge detection, where region growing is limited only to grain boundaries First, a 2D Fast Fourier Transform (2DFFT) and GrayLevel Cooccurrence Matrix (GLCM) are Combining Segmentation and Edge Detection for Efficient Ore
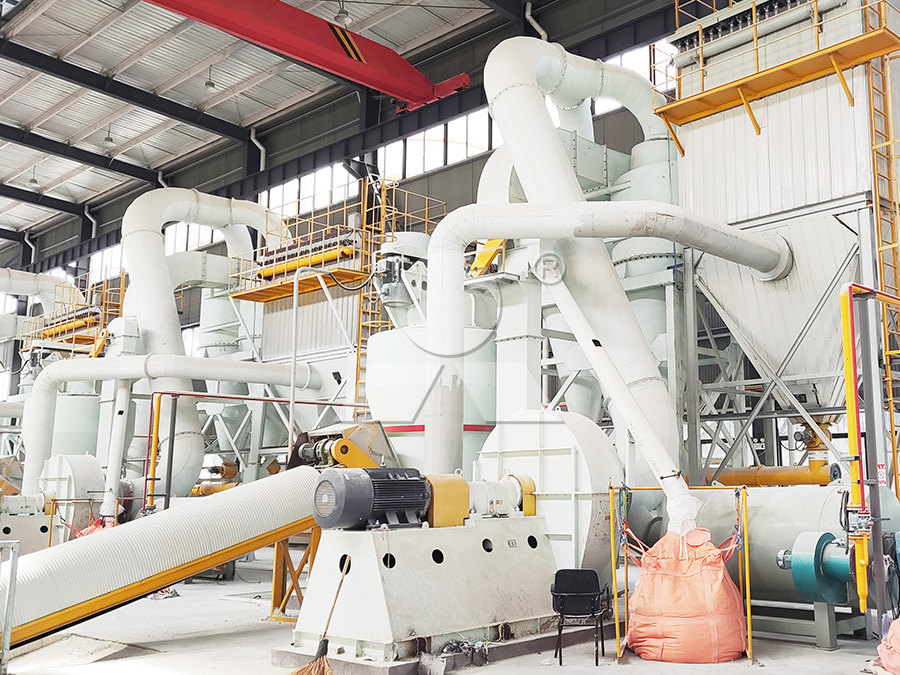
Understanding fine ore breakage in a laboratory scale ball mill
2011年2月1日 At SAG 2006, we reported the simulated and measured outcomes of treating a well characterised ore in a 12 m diameter mill This well instrumented, pilot scale mill at the University of KwaZuluNatal has been combined with some new approaches to ore testing to allow different modes of breakage to be testedFigure 5 High–low wave ball mill liner Materials The selection of the material of construction is a function of the application, abrasivity of ore, size of mill, corrosion environment, size of balls, mill speed, etc liner design and material of construction are integral and cannot be The Selection and Design of Mill Liners 911 Metallurgist2024年1月10日 If the raw materials are brittle materials such as tungsten tin ore, rare metal ores, and coal, choose a rod mill; if the materials are aluminum ash, lime, slag, molybdenum ore, etc, use a ball mill It is relatively better to deal with it According to the particle size effect of the finished product The product particle size is 1~3mmBall Mill VS Rod Mill: Difference Selection JXSC MachineLatest reviews, photos and ratings for Ore Mill Bar Grille at 17 Lake Tarleton Rd in Warren view the menu, hours, phone number, address and map Find {{ group }} making it a perfect spot for families and groups With a great selection of beer and a menu full of tasty options, Ore Mill Bar Grille is a mustvisit for anyone passing throughOre Mill Bar Grille Restaurantji
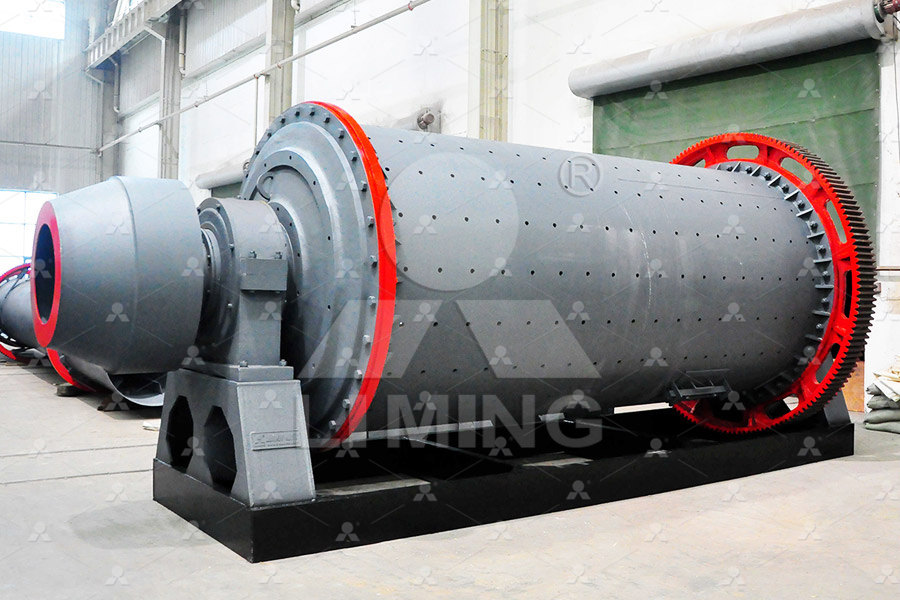
(PDF) Material handling and flowsheet selection
PDF On Nov 15, 2019, B Foggiatto and others published Material handling and flowsheet selection considerations for particlebased ore sorting Find, read and cite all the research you need on The application of ore sorting in the mining industry is one of the most promising recent technologies with the potential to cause step change in the way concentrators are designed Most typically, ore sorters are used to sort a given ore flow for grade, either to reject waste from the mill feed, or rescue ore from the waste pileSAG AND BALL MILL EFFECTS FROM ORE SORTING SYSTEM PROCESSING AND COMPLEX USAGE OF MINERAL RAW MATERIALS EURASIAN MINING 2022 No 2 pp 54–57 55 kWh/t; M ia is the Morrell index for coarse ore treatment in tumbling mills to the size P 80 > 750 μm , kWh/t; Mic is the M orrell index for ore treatment in cone and jaw crushers, kWh/t; Mih is the Morrell index for ore treatment in HPGR circuits, kWh/t; Mib is the ORE HARDNESS PROPERTIES EVALUATION BASED ON Download Table Selection and breakage functions from publication: Scale up and simulation of Vertimill™ pilot test operated with copper ore Vertimill™ has been used in regrind circuits Selection and breakage functions Download Table
.jpg)
Comparison of Ore Hardness Measurements for Grinding Mill
2021年1月14日 was surprising that the Bond Rod Mill Wi average was 113 kWh/t Since the ore is unusually soft, the Rod Mill Wi is probably irrelevant in determining required power for the SAG mill Drop Weight Tests Drop Weight tests were done at Hazen and analyzed by Contract Support Services, Inc Table 4: Summary of 6 JKTech Drop Weight Tests2020年9月22日 Grinding machine has been widely used in gold mines in South Africa since 1905 At that time, the grinding machine used river pebble as the grinding medium, which was essentially a gravel mill Later, in order to improve the production capacity of the mill, cast iron balls were used as the medium, so normal gravel mills were evolved into ball mills and rod millsGrinding Machines: Types and Selection Principles Miningpediaore sources Outcomes from reconciliation studies may be put into two categories; misclassification of significant tonnages of ore grade material (common), and discovery of problems in postmining processing and documentation (less common) A definite consequence of the former is the haulage of misclassified ore to waste dumps or waste to the Ore Grade Reconciliation Techniques – A Review Mining Selection function, breakage function, mill critical speed, Platinum ore, milling kinetics, breakage rate iii Dedication This work is dedicated to my sweet family: 62 Effect of mill speed on the breakage properties of the UG2 ore 84 621 Selection function parameters 84 622 Breakage function parameters EFFECTS OF MILL ROTATIONAL SPEED ON THE BATCH GRINDING KINETICS OF
.jpg)
Assessment of the Functionality of Selection and Breakage Rate
Selection andbreakage functions are lumped into a steadystate mill matrix This steadystatemill matrix is multiplied (on the right side) by the feed matrix which describes the particle size distribution entering the mill This multiplication yields the mill product matrix which describes the size distribution of the particles exiting the mill2006年1月1日 An overview of the selection and design of mill liners was published by Powell et al (2006), providing a reference source on mill liners, however no comprehensive technical manual or training is (PDF) Selection and design of mill liners ResearchGate