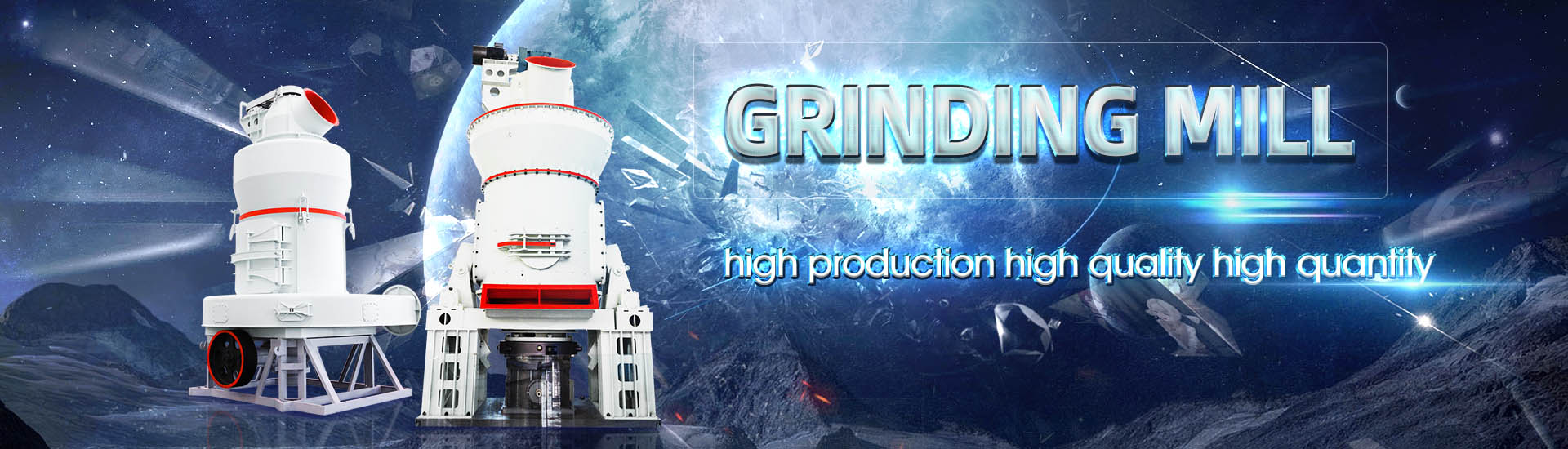
Ball mill ball ratio
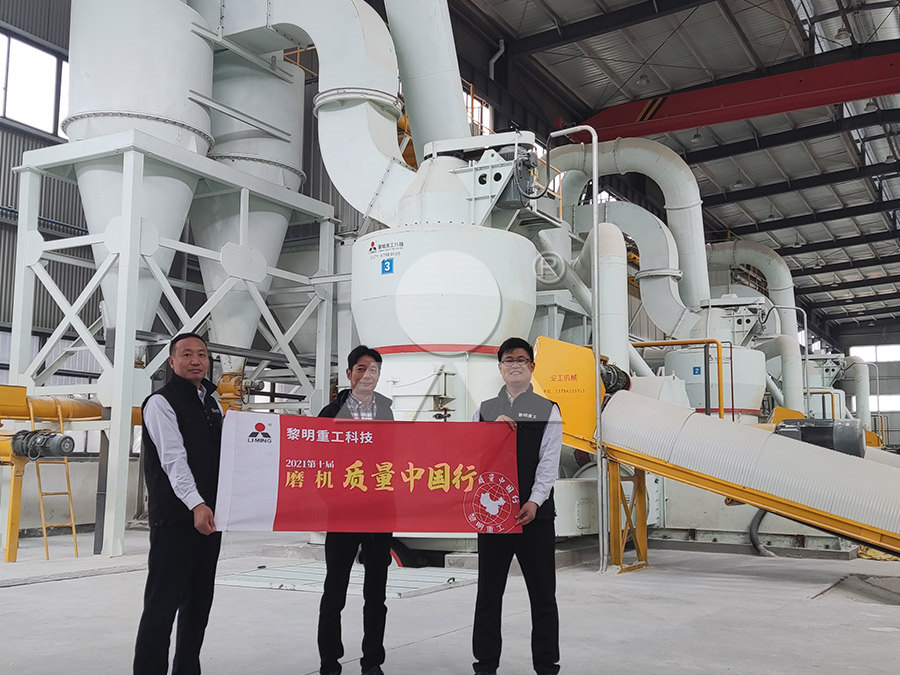
Calculate and Select Ball Mill Ball Size for Optimum
2013年8月3日 In Grinding, selecting (calculate) the correct or optimum ball size that allows for the best and optimum/ideal or target grind size to be achieved Ball mills in which the length to diameter ratio is between 3 and 5 are designated tube mills The latter are sometimes divided into several longitudinal compartments, each having a different Ball Mill an overview ScienceDirect Topics2023年4月23日 One of the most used tumbling mills is the ball mill This paper reviews different types of grinding media that have been developed and improved over the years and their properties Also(PDF) Grinding Media in Ball MillsA Review2023年10月27日 The performance of grinding media in a ball mill is measured in terms of wear rate, which is a function of the media composition, hardness, phase structure, and A Review of the Grinding Media in Ball Mills for Mineral Processing
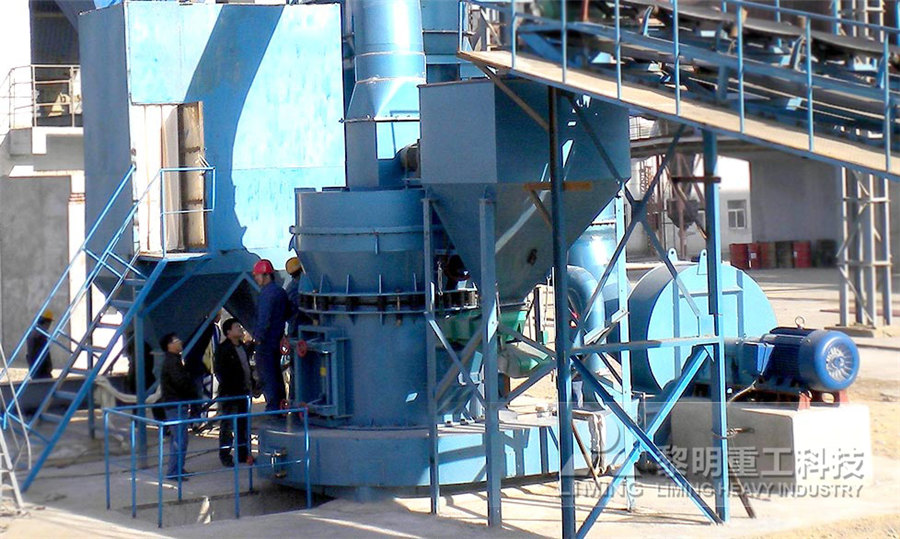
Ball mill Wikipedia
A ball mill is a type of grinder filled with grinding balls, used to grind or blend materials for use in mineral dressing processes, paints, pyrotechnics, ceramics, and selective laser sintering It works on the principle of impact and attrition: Ball mills are filled up to 40% with steel balls (with 30–80 mm diameter), which effectively grind the ore The material that is to be ground fills the voids between the balls The tumbling balls Ball Mill an overview ScienceDirect Topicsthe ball mill had an average production rate of 190tph with a specific electrical energy consumption of 355kWh/t Its operational issues included: • oversized limestone • wornout BALL MILLS Ball mill optimisation Holzinger Consulting2013年12月1日 Here we report that there exists an optimal ball size for efficient milling at a given rotation speed, based on a laboratoryscale wet ball mill Also, the effect of powder loading on Effect of ball size and powder loading on the milling efficiency of a
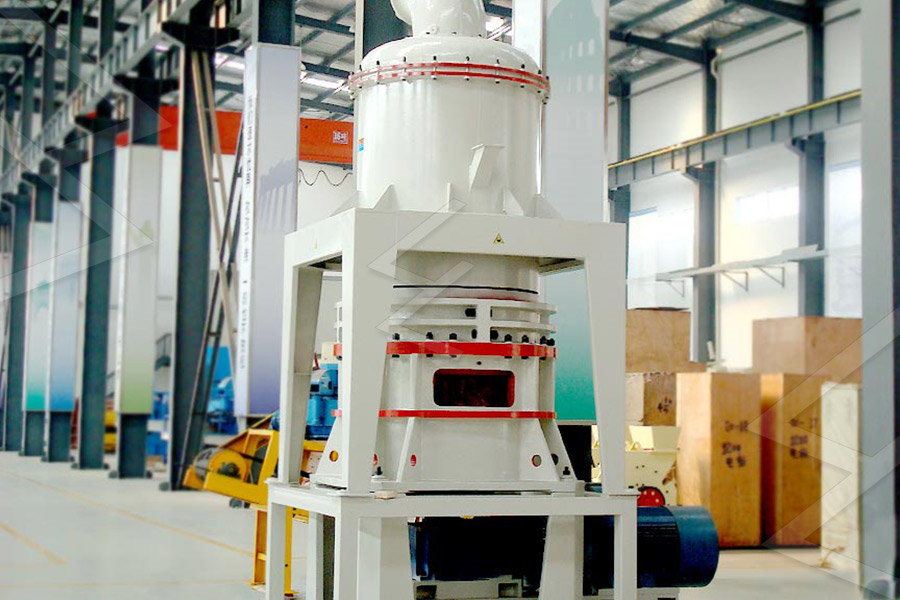
Ball Mill SpringerLink
2024年1月1日 According to the ratio of cylinder length (L) to diameter (D), the ball mill can be divided into short cylinder ball mill, L/D ≤ 1; long barrel ball mill, L/D ≥ 1–15 or even 2–3; and 2023年10月27日 The ball mill is a rotating cylindrical vessel with grinding media inside, which is responsible for breaking the ore particles Grinding media play an important role in the comminution of mineral ores in these mills This work reviews the application of balls in mineral processing as a function of the materials used to manufacture them and the mass loss, as A Review of the Grinding Media in Ball Mills for Mineral 2023年4月30日 According to the ratio of cylinder length (L) to diameter (D), the ball mill can be divided into short cylinder ball mill, L/D ≤ 1; long barrel ball mill, L/D ≥ 1–15 or even 2–3; and tube mill, L/D ≥ 3–5 According to the cylinder shape of the ball mill, it can be divided into cylindrical ball mill and cone ball millBall Mill SpringerLink2022年1月1日 Effects of balltopowder diameter ratio and powder particle shape on EDEM simulation in a planetary ball mill Author links open overlay panel KyongChol Kim a b, Tao Jiang a c d, Planetary ball mill is extensively used for fine Effects of balltopowder diameter ratio and powder particle
.jpg)
Planetary Ball Mill PM 400 RETSCH powerful and quick grinding
The grinding jars are arranged eccentrically on the sun wheel of the planetary ball mill The direction of movement of the sun wheel is opposite to that of the grinding jars in the ratio 1:2 (or 1:25 or 1:3) The grinding balls in the grinding jars are subjected to superimposed rotational movements, the socalled Coriolis forces2019年8月14日 In the production of the processing plant, the more common steel ball ratio of ball mill is twostage ratio and multistage ratio Generally speaking, the multistage ratio follows the principle of less large and small steel balls and more mediumsized steel balls, namely, less steel balls at both ends, and more in the middleThe Ultimate Guide to Ball Mills Miningpedia2012年6月1日 [4, 5] and an empirical relation is suggested expressing the mill capacity as a ratio Ball mills can grind a wide range of materials, including metals, ceramics, Grinding in Ball Mills: Modeling and Process Control2023年4月23日 One of the most used tumbling mills is the ball mill media proportion and material ball ratio According to Kelsall et al [17] changes in media (quantity, density, (PDF) Grinding Media in Ball MillsA Review ResearchGate
.jpg)
Planetary Ball Mill PM 100 RETSCH highest fineness
The Planetary Ball Mill PM 100 is a powerful benchtop model with a single grinding station and an easytouse counterweight which compensates masses up to 8 kg speed ratio 1:2; Grinding with up to 333 x acceleration of gravity; Batchwise processing with max 1 x 220 ml sample ;This means that during one rotation of the sun wheel, the grinding jar rotates twice in the opposite direction This speed ratio is very common for Planetary Ball Mills in general Planetary ball mills with higher energy input and a speed ratio of 1:25 or even 1:3 are mainly used for mechanochemical applicationsPlanetary Ball Mills RETSCH fine grinding of materials2021年11月1日 The filling ratio, ratio of particle to ball and mineral weight were varied to control the mill load The initial ratio of grading ball was 30 mm: 40 mm: 50 mm: 70 mm = 30: 20: 30: 20 It should be noted that the diameter of instrumented grinding media is 70 mm Rotation speed of cement ball mill was set to 80% The Assessing load in ball mill using instrumented grinding media2017年10月26日 Ball mill shape factors in the period prior to 1927 averaged 11/1 for 29 center discharge mills and 10/1 for 30 peripheral discharge mills With the resumption of new plant construction after the 1930’s depression, the Morenci concentrator continued the 1/1 ratio with its 31 x 31 m (10 x 10 ft) millsL / D Ratio in Overflow Ball Mill Design Operation
.jpg)
Mechanical Alloying with Ball Mills Retsch
This ratio is standard for most planetary ball mills For mechanical alloying applications, planetary ball mills with a higher energy input and a speed ratio of 1:25 or even 1:3 are particularly effective Unlike the Emax, these mills can accommodate larger grinding jars up to 500 ml2023年2月15日 A beneficiation plant in Singapore loads balls into a ϕ 1500mm×3000mm wet grid type ball mill, determines the filling rate ϕ = 50%, and selects cast steel grinding balls δ = 45 t/m 3 The ball mill processes the Method of Steel Grinding Ball Proportioning and Stone loading amount = 314X the square radius of the ball mill X the specific gravity of the ball X the length of the ball mill X25%*1000 Regarding the gradation of the high alumina ceramic ball of the ball mill: Due to the different grinding aids added to How to choose the size, filling amount and ratio of alumina 2024年6月27日 A new planetary ball mill device with adjustable speed ratio for enhanced mechanochemical processes† Frank Yntema ab, Cameron Webster a and Emmanouil Broumidis * ab a Pluto Mills Ltd, Michelin Scotland Innovation Parc, Baldovie Rd, Dundee, DD4 8UQ, UKA new planetary ball mill device with adjustable speed ratio for
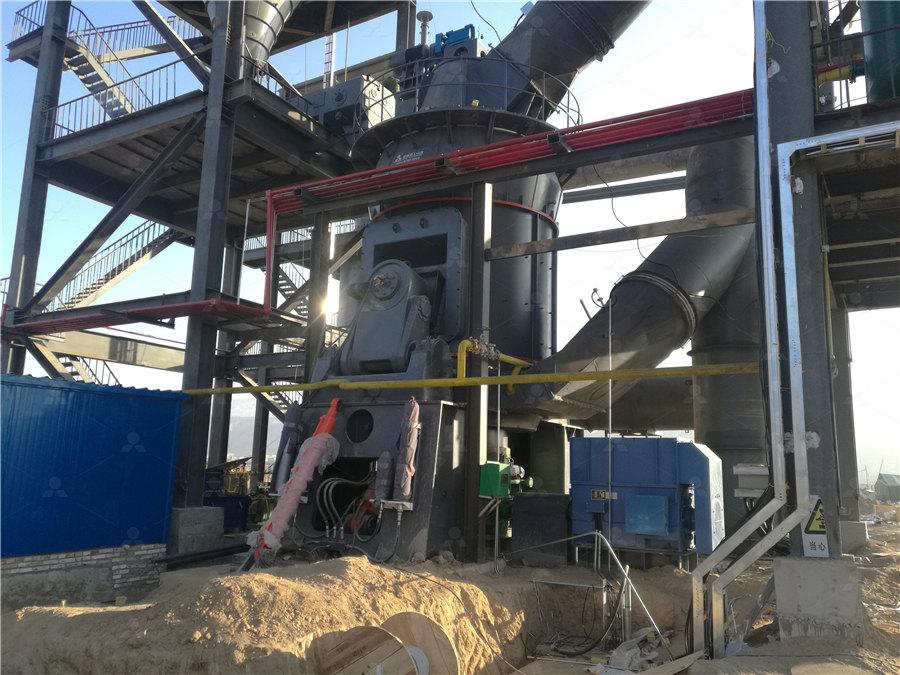
A new planetary ball mill device with adjustable speed ratio for
2024年6月27日 A new planetary ball mill device with adjustable speed ratio for enhanced mechanochemical processes† Frank Yntema ab, Cameron Webster a and Emmanouil Broumidis * ab a Pluto Mills Ltd, Michelin Scotland Innovation Parc, Baldovie Rd, Dundee, DD4 8UQ, UKThe ball mill is a tumbling mill that uses steel balls as the grinding media The length of the cylindrical shell is usually 1–15 times the shell diameter (Figure 811)The feed can be dry, with less than 3% moisture to minimize ball coating, or slurry containing 20–40% water by weightBall Mill an overview ScienceDirect Topics2015年10月15日 B) Overflow Discharge Mills operating at low ball fillings – slurry may accumulate on top of the ball charge; causing, the Total Charge Filling Level to be higher than the Ball Filling Level Grate Discharge mills will not face this issue C) This value represents the Volumetric Fractional Filling of the Voids in between the balls by the Calculate Ball Mill Grinding Capacity 911Metallurgist2021年2月19日 The ball mill process parameters discussed in this study are ball to powder weight ratio, ball mill working capacity and ball mill speed As Taguchi array, also known as orthogonal array design, adds a new dimension to conventional experimental design, therefore, Orthogonal array (L9) was carefully chosen for experimental design to understand the effects Comparative Study on Improving the Ball Mill Process Parameters
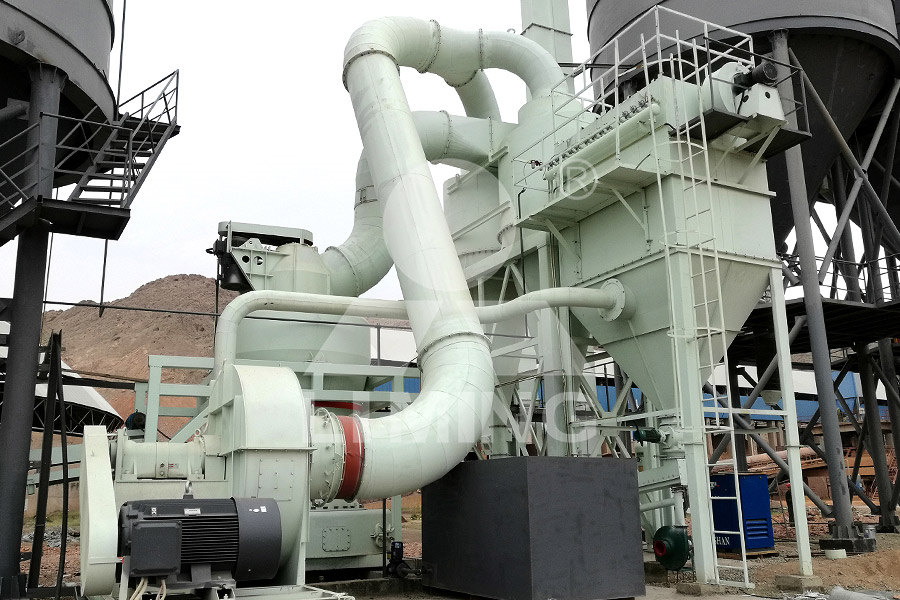
Ball Mill Circulating Load Formula 911Metallurgist
2015年10月9日 Calculating a grinding circuit’s circulating loads based on Screen Analysis of its slurries Compared to %Solids or Density based Circulating load equations, a more precise method of determining grinding circuit tonnages uses the screen size distributions of the pulps instead of the dilution ratiosPulp samples collected around the ball mill or rod mill and 2023年11月23日 Kaolin is one of the most important clay minerals that attracts attention due to its various application areas such as the ceramic industry In this study, the effects of solid/ball ratio and grinding time on the mechanical activation of kaolin were investigated Samples with 10 µm particle size were activated in The Fritsch Pulverisette 5 Ball Mill (Two Chamber Mill) at Effect of solid/ball ratio and grinding time on the mechanical 2023年10月23日 Since planetary ball mills have diverse applications and accommodate a wide range of materials, and whether it's wet or dry grinding It's recommended to keep a record of the grinding ball size ratios that work best for a specific material during daily experiments to accumulate experience For more advices and knowledge about How to Determine the Ratio of Grinding Balls in a Ball Mill 2015年2月21日 For example your ball mill is in closed circuit with a set of cyclones The grinding mill receives crushed ore feed The pulp densities around your cyclone are sampled and known over an 8hour shift, allowing to Circulating Load Calculation Formula 911Metallurgist
.jpg)
Ball Mill SpringerLink
2024年1月1日 According to the ratio of cylinder length (L) to diameter (D), the ball mill can be divided into short cylinder ball mill, L/D ≤ 1; long barrel ball mill, L/D ≥ 1–15 or even 2–3; and tube mill, L/D ≥ 3–5 According to the cylinder shape of the ball mill, it can be divided into cylindrical ball mill and cone ball mill2013年2月7日 Planetary ball mills are well known and used for particle size reduction on laboratory and pilot scales for decades while during the last few balltopowder ratios and small ball sizes which Process Engineering with Planetary Ball Mills ResearchGate911 Metallurgist can enter the scene and see what you have become blind to We can fix issues in ways you never thought possible Our fresh eyes will open new opportunities for your plant Each mineral processing plant has varied ore types, mining equipment, (crusher, ball mill, flotation, tailings), and management (operating) philosophyThe evaluation and prioritization of variables Metallurgists Mineral Processing Engineers 911MetallurgistHow to determine whether the ratio of loaded ball is reasonable? Ball mill is one of the commonly used equipment in mineral processing equipment For ball mill, reasonable ball loading not only affects the improvement of grinding efficiency and productivity, but also relates to the service life of ball mill Therefore, it is very important to How to choose the ball loading and loading ratio of ball mill?
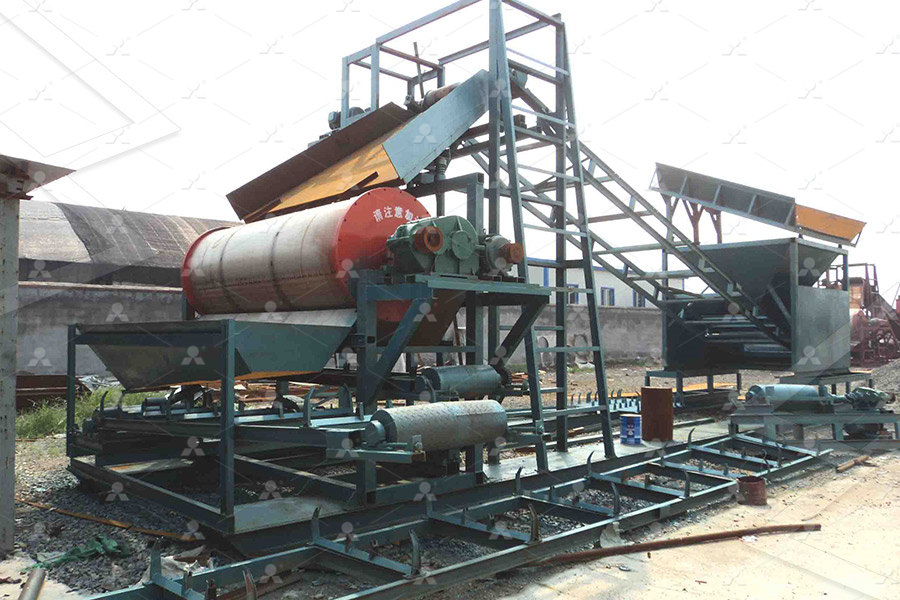
(PDF) Effects of balltopowder diameter ratio and powder
2021年12月1日 The effects of the balltopowder diameter ratio (BPDR) and the shape of the powder particles on EDEM simulation results and time in the planetary ball mill was investigated2022年1月1日 The effects of the balltopowder diameter ratio (BPDR) and the shape of the powder particles on EDEM simulation results and time in the planetary ball mill was investigated BPDR was varied from 1 to 40/3 by changing the powder particle diameter from 8 to 06 mm The size and shape of the powder particles do not give a significant change in both the ball motion Effects of balltopowder diameter ratio and powder particle Planetary Ball Mill 4*2000mL Features Wide range of machines to choose from, from benchtop mini PBM04L mill to PBM16L; There are various grinding jars and grinding media based on grinding materials: Alumina Ceramic, Agate, Zirconia, Stainless Steel, Teflon, Nylon, and Polyurethane; Automatic and programmable grinding, clockwise and counterclockwise, with HighEnergy Ball Mill Machine Landt Instruments2021年7月12日 Therefore, the ball milling treatment was used to remove sharp corners and smooth the surface of the precursor powder particles Ball milling process was conducted in a planetary ball milling machine (QM3SP04, Nanjing University Instrument Factory) equipped with four nylon ball mill tanks with an internal volume of 50 mLEffect of BalltoPowder Ratio on Morphology, Structure, and
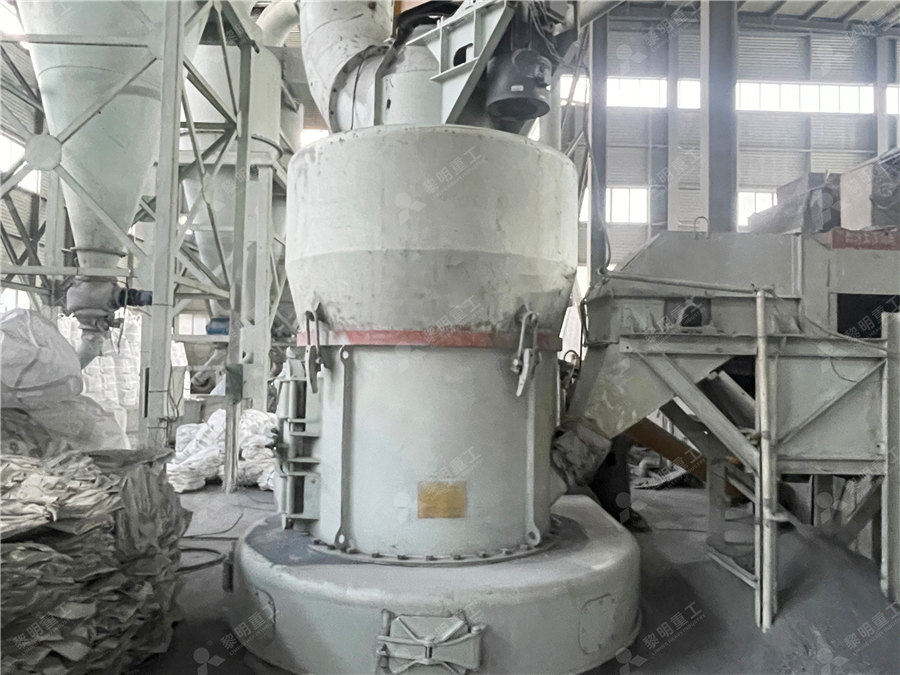
Factors Affect The Output and Quality of Ball Mills
2023年12月28日 The ball mill is widely loved by people in mineral processing, building materials, chemical, and other bonding between them improves grinding efficiency and is conducive to energy savings and high productivity of 2002年7月1日 The rotational direction of a pot in a planetary ball mill and its speed ratio against revolution of a disk were studied in terms of their effects on the specific impact energy of balls calculated Effects of rotational direction and rotationtorevolution speed ratio 2024年8月15日 Planetary ball mill specific parameters that directly influence the energetics a, Illustration of a mill and the relevant parameters that contribute to the effective impact velocity v effective in Equation 4 Angular velocity of planetary disk, ω p; angular velocity of jar, ω j; transmission ratio i=1+(r p /r j) 1/2Navigating Ball Mill Specifications for TheorytoPractice 2021年8月12日 Planetary ball mills are substantially smaller than other ball mills and are commonly used in laboratories to grind sample materials to extremely fine sizes Zhang et al used two ratios of grinding ball to biomass weight (20:1 Ball milling as an important pretreatment technique in
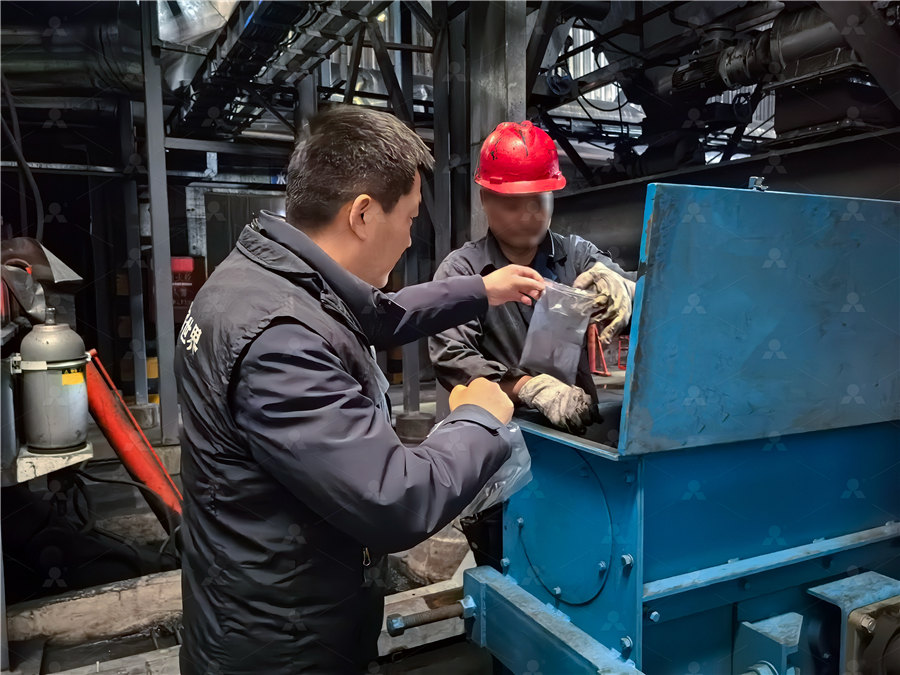
Effects of the speed ratio on the efficiency of planetary mills
2019年2月1日 1 Introduction Planetary ball mills provide high energy density due to the superimposed effect of two centrifugal fields produced by the rotation of the supporting disc and the rotation of the vials around its own axis in the opposite direction [1]During operation, the grinding balls execute motion paths that result in frictional and impact effects2015年6月19日 The basic parameters used in ball mill design (power calculations), rod mill or any tumbling mill sizing are; material to be ground, characteristics, Bond Work Index, bulk density, specific density, desired mill tonnage capacity DTPH, operating % solids or pulp density, feed size as F80 and maximum ‘chunk size’, product size as P80 and maximum and finally the type of Ball Mill Design/Power Calculation 911Metallurgist2018年4月8日 Unlock the principles of ball mill design with 911 Metallurgist This guide offers detailed calculations and practical tips to ensure your mill is optimized for performance, efficiency, and effective mineral processingBall Mill Design Calculations How to 911Metallurgist2020年7月2日 A comprehensive investigation was conducted to delineate the effect of ball size distribution, mill speed, and their interactions on power draw, charge motion, and balls segregation in a (PDF) Effects of Ball Size Distribution and Mill Speed and Their
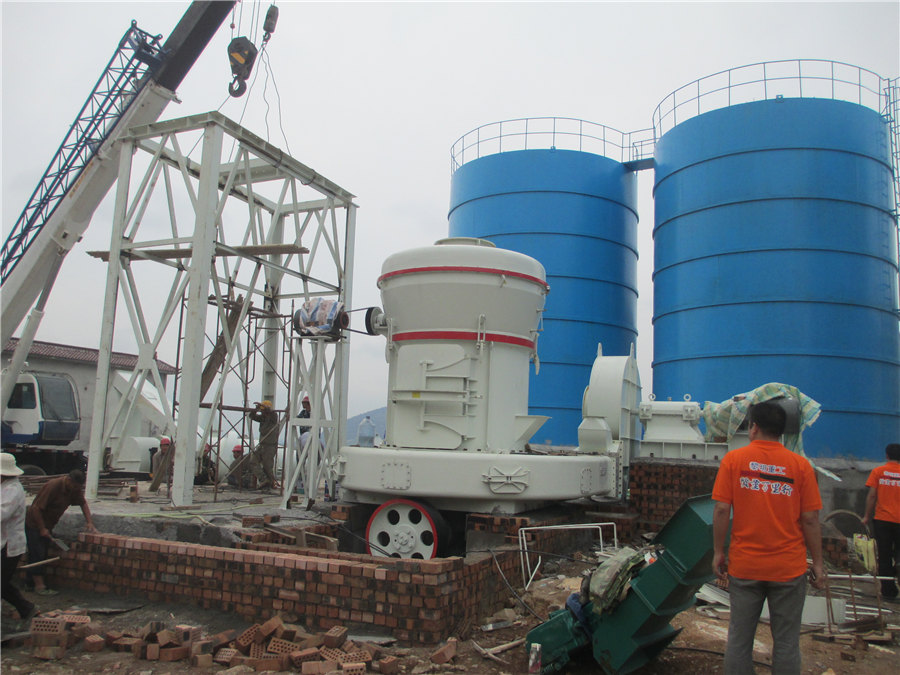
balltopowder weight ratio: Topics by Sciencegov
Here, NH4 (HCO3) was used as a space holder Mechanically alloyed CuZnAl is made using a planetary ball mill taking the ratio of Cu/Zn/Al = 70:25:5 (by weight ratio) The ball/powder ratios were varied in the four ranges 10:1, 15:1, 20:1, and 25:1