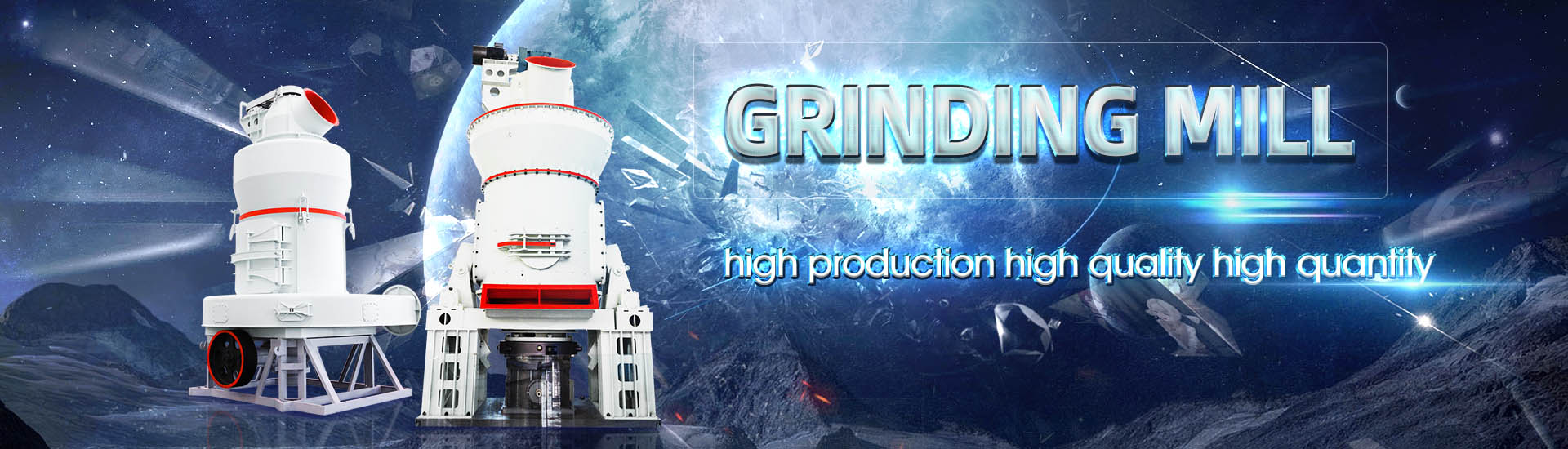
Limestone powder desulfurization process, spodumene method
.jpg)
Aspects of Spodumene Lithium Extraction Techniques MDPI
2024年9月30日 The calcination decrepitation reaction of spodumene with limestone (roasting process) involves three distinct steps : (i) decomposition of limestone at temperatures ranging from 750 to 800 °C, resulting in the formation of CaO and the release of CO 2, (ii) The calcinationdecrepitationreaction of spodumene with limestone (roasting process) involves three distinct steps: (i) decomposition (calcination) of the limestone at temperatures of 750800 Alkaline Process for Extracting Lithium from Spodumene2023年6月25日 In this study, a novel lithium extraction method was proposed for α spodumene by combining activated roasting and sulfuric acid leaching First, the thermodynamics of the An effective method for directly extracting lithium from α 2021年12月1日 Lowgrade limestone (LGL) is evaluated as an alternative absorbent in WFGD process Dissolution kinetics for LGL with different particle sizes are determined The reaction Insights into the desulfurization mechanism of lowgrade
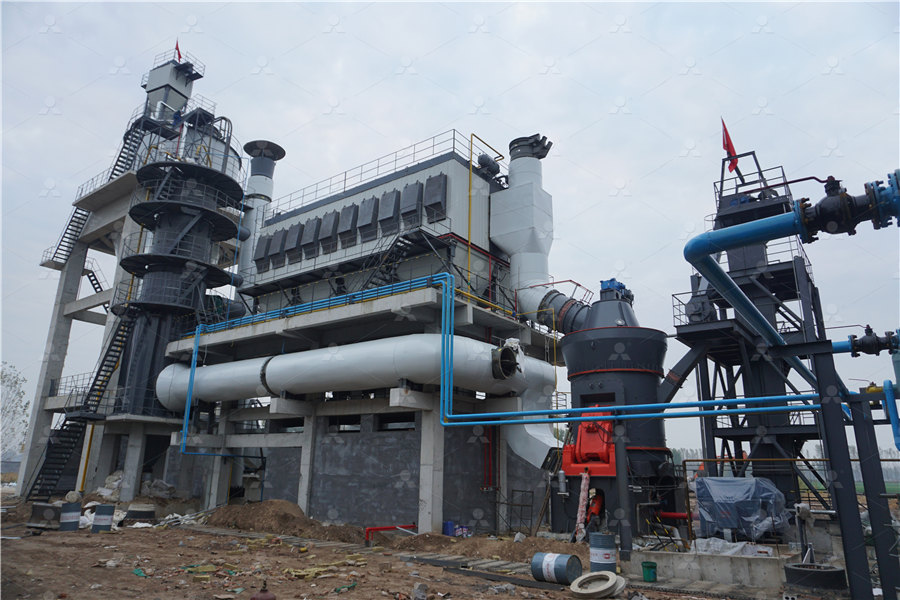
(PDF) A Review of Desulfurization Technology using Limestone in
2015年10月30日 This study investigated that status of domestic and international furnace desulfurization and desulfurization characteristics of limestone for fluidized bed use depending 2023年1月1日 TSulfuric acid process is the mainstream process for extracting lithium from spodumene, with a complex process, high energy consumption, and large discharge of waste Lithium extraction from hard rock lithium ores (spodumene, Spodumene is naturally present in the stable αmonoclinic (highly packed crystal structure) form with high grindability and hence the mineral is difficult to leach without pretreatment It is made Literature Review and Thermodynamic Modelling of Roasting 2019年10月29日 Therefore, in this paper, the application of natural ultrafine limestone, with a Sauter mean diameter of less than 20 μm, was tested by conducting benchscale, pilotscale, Applications of Ultrafine Limestone Sorbents for the
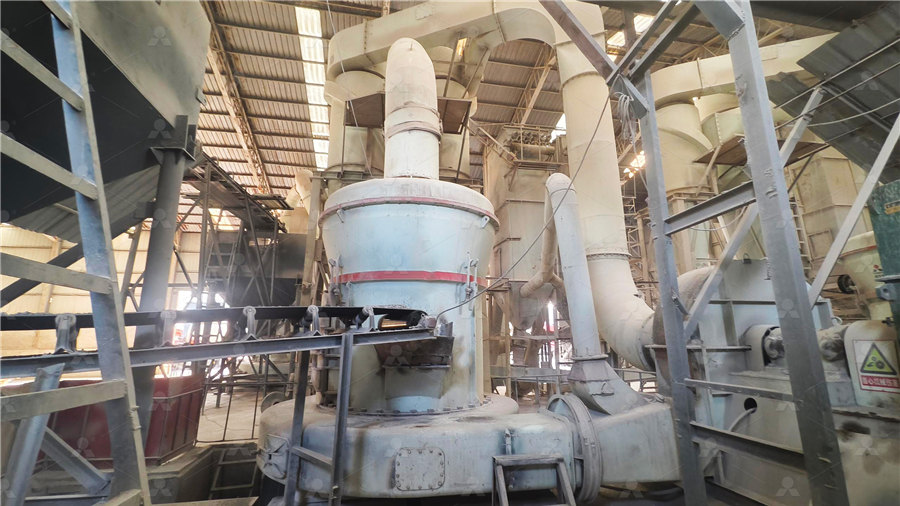
Direct Lithium Extraction from αSpodumene through SolidState
2024年7月9日 In this work, we report an alternative method to extract Li directly from αspodumene, which is performed at lower temperatures and avoids the use of acids It is shown During the combustion process the sulfur in the coal combines with oxygen in the air to form SO2 To remove the SO2, the flue exhaust from a coalfired power plant is commonly bubbled Analysis of limestone for flue gas desulfurization in a power plant2008年2月1日 Semidry flue gas desulfurization was investigated with several kinds of SO2 sorbents, such as slaked lime, limestone, Mg(OH)2 and concrete pile sludge, in a powderparticle spouted bedRemoval of SO2 in Semi‐Dry Flue Gas Desulfurization Process 2021年12月1日 Typically, the adsorption of SO 2 in alkali slurry is a gasliquid adsorption process where gas adsorption rate can be greatly affected by the dissolution rate of solid desulfurizer However, in our previous work [24], it was elucidated that the existence of CaMg(CO 3) 2 in LGL can significantly inhibit the dissolution of CaCO 3 in acid environment, thereby Insights into the desulfurization mechanism of lowgrade limestone
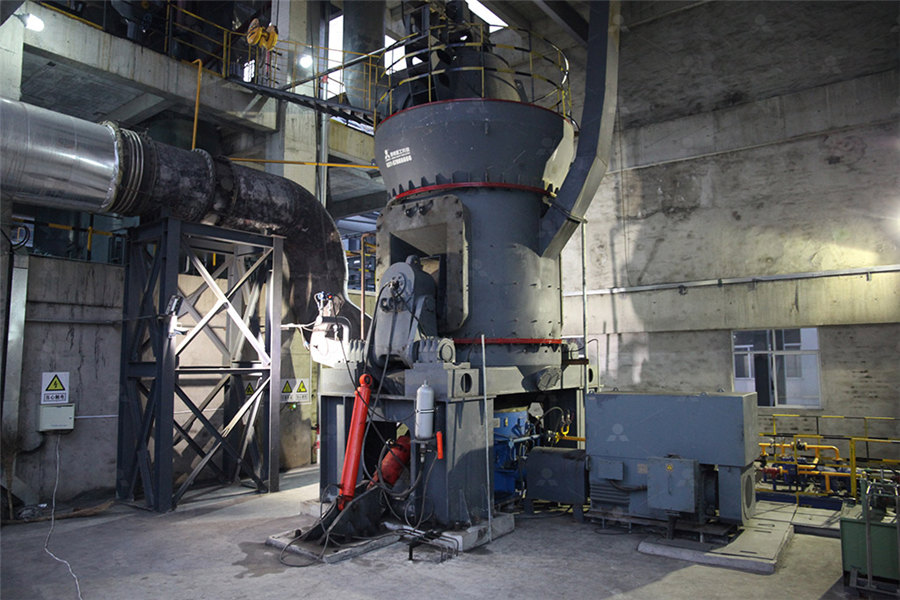
LimestoneGypsum Wet Flue Gas Desulfurization Wastewater
2021年2月1日 In this paper, chemical precipitation process is used for the treatment of the desulfurization wastewater generated by the waste gas treatment system of the limestonegypsum flue gas desulfurization process of a thermal power plant After one year of operation, the technology is reliable and stable2024年2月12日 Scientific Reports Experimental study on integrated desulfurization and denitrification of lowtemperature flue gas by oxidation method Skip to main content Thank you for visiting natureExperimental study on integrated desulfurization and Naturelimestone–gypsum desulfurization process and the majority of them are in the submicron range The fine particles formed during the limestone–gypsum flue gas desulfurization process are related to the particles in desulfurization slurry The main composition of particles formed during the desulfurization is CaSO 4 With the increase in SO 2Fine Particle Characteristics from Limestone Gypsum Desulfurization ProcessLimestone powder in flue gas desulfurization Flue gas desulfurization (FGD) These deposits are mined and quarried with special equipment and methods This ensures the limestone is taken out in a controlled and sustainable way The process of making limestone powder is closely watched from start to finish9 important Uses of limestone powder
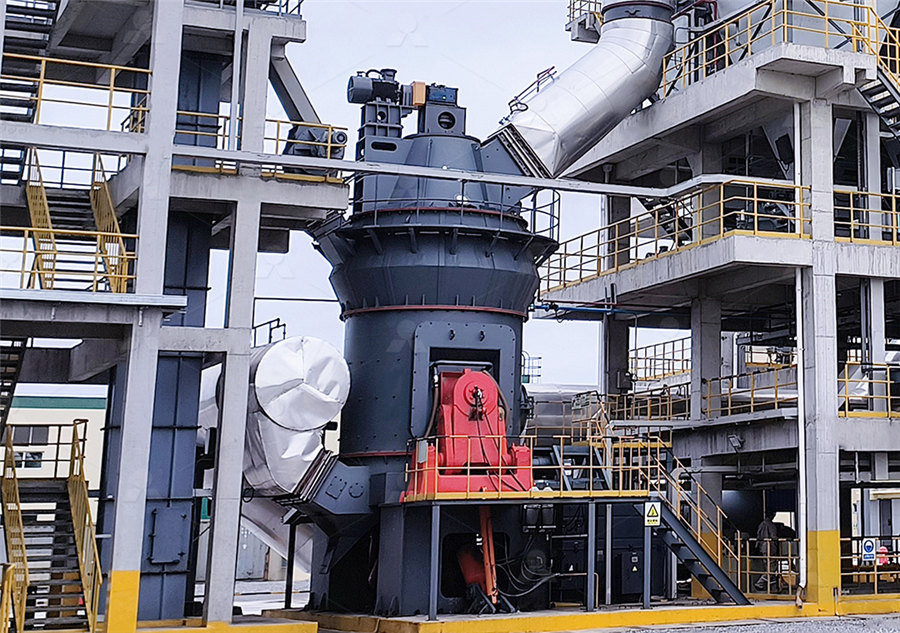
Optimum Values of Process Parameters of the “Wet Limestone
2002年4月1日 In this article the method of cost optimization of the “Wet Limestone Flue Gas Desulfurization System” is presented The optimization calculations include process and cost models2020年8月15日 Postcombustion flue gas desulfurization and denitrification technologies are essential in achieving the full compliance of fine particulate matter (PM25, aerodynamic diameter less than 25 μm) air quality standards by 2030 in China as sulfur dioxide (SO2) and nitrogen oxides (NOX) are the main precursors of PM25 Some studies have addressed the Comprehensive evaluation of flue gas desulfurization and solution or slurry in wet state, which is the most widely used desulphurization method at present Limestonegypsum method in wet process is the most mature and most widely used desulphurization method among many desulphurization methods, with a desulphurization efficiency of up to 90%Research progress of flue gas desulfurization and SJISRProcess development of e!ective semidry #ue gas desulfurization by a powderparticle spouted bed Kagaku Kogaku Ronbunshu, 22, 1400}1407 Guo, Q, Kato, K (1998) The e!ect of operating conditions on SO 2 removal in semidry Use of limestone for SO2 removal from flue gas in the
.jpg)
Flow diagram of the limestone scrubbing method
Download scientific diagram Flow diagram of the limestone scrubbing method from publication: Review of Design, Operating, and Financial Considerations in Flue Gas Desulfurization Systems In 2019年3月13日 Mathematical model Mathematical model for SO 2 removal in WFGD, considering mass transfer and chemical reactions (Hou, Bai, and Yin Citation 2013), was chosen as the main part of concentration model for its Full article: Modeling and optimization of wet flue gas 2006年8月1日 A generic wetlimestone flow diagram is outlined in Figure 1 (The diagram also applies for systems using hydrated limeCa(OH 2)as the reagent, where equipment and vessel sizes are smaller)Wet WetLimestone Scrubbing Fundamentals Power Engineering2020年5月16日 Numerous mitigation techniques have been incorporated to capture or remove SO2 with flue gas desulfurization (FGD) being the most common method Regenerative FGD method is advantageous over other methods due to high desulfurization efficiency, sorbent regenerability, and reduction in waste handling The capital costs of regenerative methods are Sulfur dioxide removal: An overview of regenerative flue gas
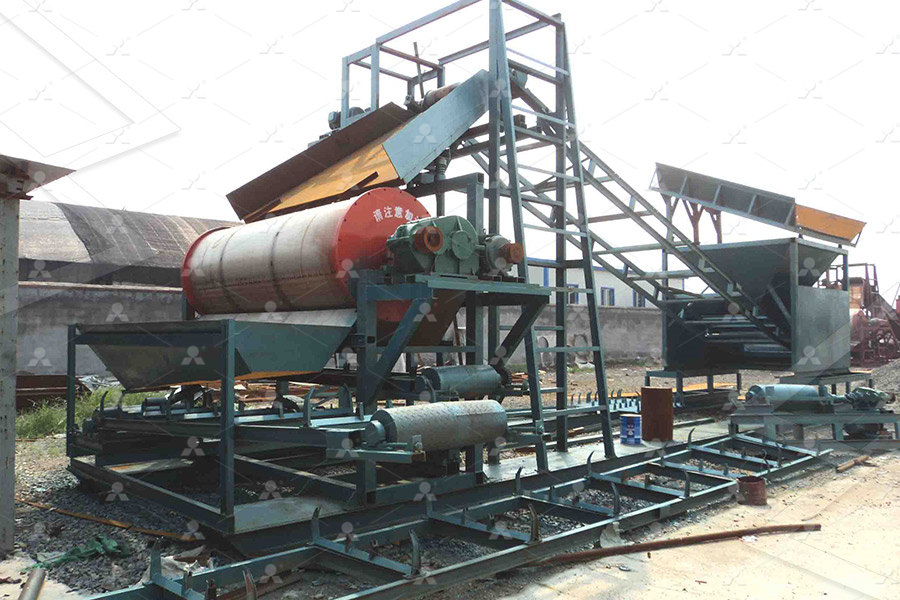
Limestonegypsum Desulfurization Process in Cement Plant
Limestone powder (kiln dust) smaller than 45μm is sent to the limestone powder silo, and the limestone powder is discharged into the limestone slurry tank by the impeller feeder, and the process water is added to prepare 30% limestone slurry, and finally the limestone slurry is pumped to absorb Tower circulation pump inletThe limestone powder of this scheme adopts 2017年7月1日 Among the reasons for the success of the wet FGD system, there is the possibility of recovering a new product to be allocated on the market namely gypsum (He and Lee, 2014)In fact, the synthetic gypsum suitable for several applications such as wallboard manufacturing is the byproduct of the SO 2 scrubbing process for scrubbers using lime or Enhancing the recovery of gypsum in limestonebased wet flue Large numbers of fine particles are formed during limestone–gypsum desulfurization process and the majority of them are in the submicron range 2 The fine particles formed during the limestone–gypsum flue gas desulfurization process are related to the particles in desulfurization slurry Their particle morphology and elements are similarFine Particle Characteristics from Limestone–Gypsum Desulfurization 2023年10月31日 A kinetic model of the RH desulfurization process was established based on the twofilm theory, considering the desulfurizer addition in the RH vacuum chamber and the slag desulfurization in the ladle The kinetic model was used to predict the variation of the sulfur content in the molten steel during the RH desulfurization process, which was in good Kinetic Model of Desulfurization During RH Refining Process
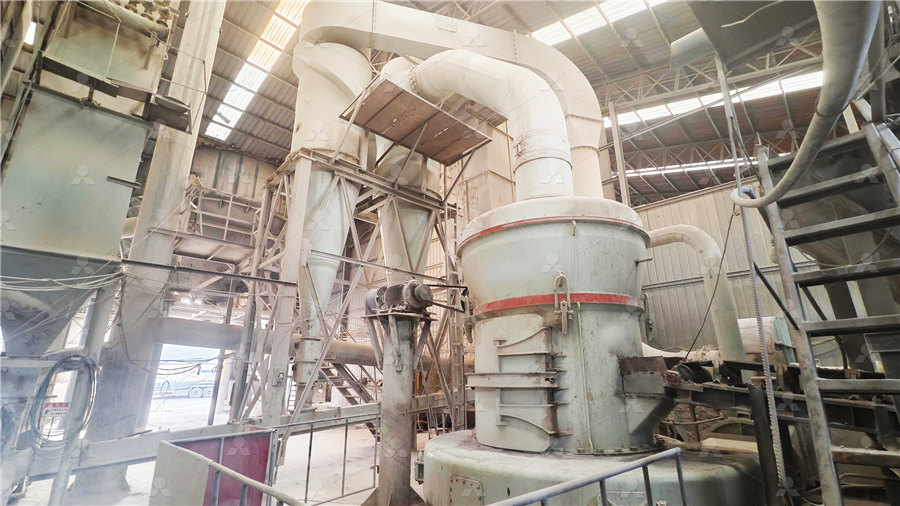
Analysis of limestone for flue gas desulfurization in a power plant
ARL OPTIM’X, lime/limestone, power plant, WDXRF, XRay fluorescence Water Vapor Gypsum out +95% SO2 captured Limestone and SO2 mix to form gypsum, CaSO4 Flue Gas Booster Fans Limestone in LIMESTONE PREPARATION Lime / Limestone ARL OPTIM’X XRF Spray Tower Flue Gas Desulfurization Unit in a Coal Fired Power Plant Element/ Oxide Concentration 2024年1月10日 Flue gas desulfurization (FGD) is a critical process for reducing sulfur dioxide (SO2) emissions from industrial sources, particularly power plants This research uses calcium silicate absorbent Modeling based on machine learning to investigate flue gas 2003年7月1日 Request PDF H 2 S Removal by Fine Limestone Particles in a Powder−Particle Fluidized Bed An efficient dry desulfurization process for hot coal gas was proposed The process uses a powder H 2 S Removal by Fine Limestone Particles in a Powder−Particle A method for removing the blinding of calcium carbonate in a fuel gas desulfurizing process is provided to make it unnecessary to stop desulfurizing facilities temporarily, thereby reducing cost and time due to temporary stopping of the desulfurizing facilities, by using organic acid such as dibasic acid When the blinding of calcium carbonate, in which a pH value of an absorption Removing method of limestone blinding at flue gas desulfurization process
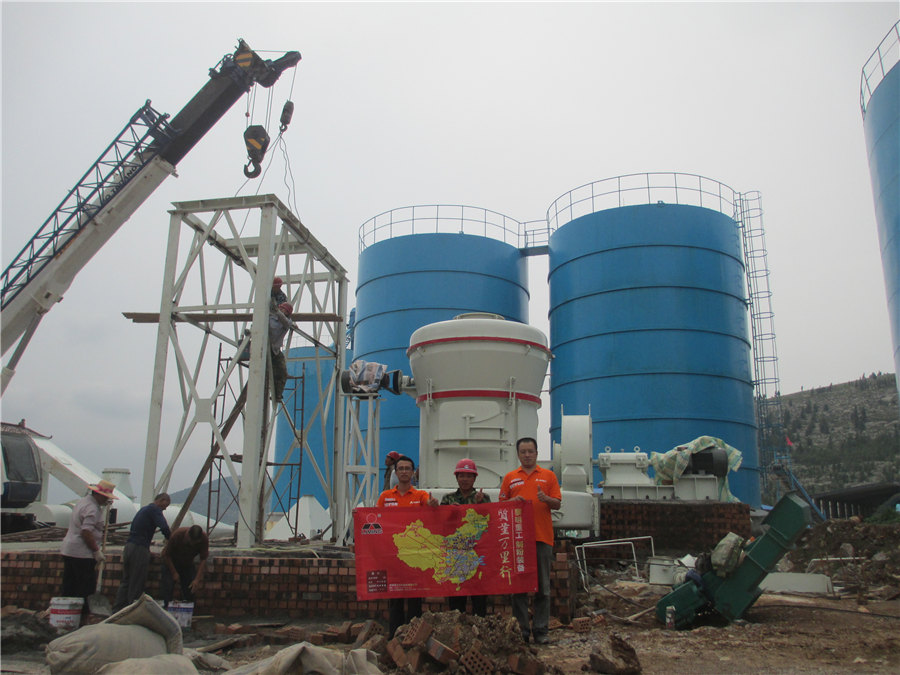
Lime / Limestone Wet Scrubbing System for Flue Gas Desulfurization
2) and limestone (CaCO 3) Rosemount Analytical pH equipment is used to control the feed rate of these chemicals PROCESS After fly ash removal, the flue gas (seen in Figure 1) is bubbled through the scrubber, and the slurry is added from aboveThe lime or limestone reacts with the SO 2 in the flue gas to create insoluble calcium sulfite (CaSO 2023年2月6日 Therefore, further analyze of the process water, limestone impurities, additives, and operation were necessary On October 9, 2020, relevant samples such as limestone powder, gypsum, fly ash, gypsum slurry, accident slurry, desulfurization process water, overflow foam, etc were collected for chemical analysis as shown in Appendix Table 7Diagnosis and Traceability Analysis of Slurry Foaming of Limestone 2015年1月1日 The desulfurization of hot metal by the monoinjection of lime powder and the coinjection of lime, calcium carbide and magnesium powders is mathematically modeled(PDF) Modeling and Simulation of Hot Metal Desulfurization by Powder 2007年2月1日 Optimization of the wet limestone (calcite) flue gas desulfurization (FGD) process is described, with the focus on the layout of subprocesses and equipmentTechnology Optimization of Wet Flue Gas Desulfurization Process

Ultrasonic Power to Enhance Limestone Dissolution in the Wet
Ultrasonic Power to Enhance Limestone Dissolution in the Wet Flue Gas Desulfurization Process Modeling and Results from Stepwise Titration Experiments Cataldo De Blasio 1,*, Claudio Carletti 1, Jarno Salonen 2 and Margareta BjörklundSänkiaho 1 1 Department of Chemical Engineering, Faculty of Science and Engineering, Åbo Akademi University,ue gas mainly include dry method, semidry method, and wet method The dry process is relatively simple, has little corrosion to the equipment, does not produce waste water and waste acid, but has a low desulfurization eciency The rate is slow and dicult to apply on a large scale However, the semidry method has a short process ow, easy productDesulphurization mechanism and engineering practice of carbide 2024年8月13日 This blog post is the third in a threepart series that discusses flue gas desulfurization (FGD) The first post provides overviews of sulfur dioxide (SO 2) and emissions regulations, the FGD industry, and global FGD market trendsThe second post provides highlevel overviews of wet, semidry, and dry FGD technologies with respect to SO 2 capture Flue Gas Desulfurization: Detailed Process OverviewWet Flue Gas Desulfurization (FGD) In most developed countries, wet scrubber (fluegas desulfurization; FGD) technology is a wellestablished process for removing SO 2 Also, costs have been reduced significantly from 150200 $/KW in the 1980s to 70150 $/kW in the late 1990s Wet FGD TechnologyWet Flue Gas Desulfurization (FGD) ARCOR Epoxy
.jpg)
Removal of SO2 in SemiDry Flue Gas Desulfurization
Removal of SO2 in SemiDry Flue Gas Desulfurization Process with a PowderParticle Spouted Bed Tsutomu Nakazato1, Yunyi Liu2 and Kunio Kato1* 1 2 Department of Biological and Chemical Engineering, Gunma University, Kiryu, 2006年1月24日 In the present work attention was focused on a wet flue gas desulfurization process using limestone suspensions, which is the most common method used to reduce SO2 emissions from power plant New Wet Flue Gas Desulfurization Process Using Granular Limestone 2016年3月1日 Based on the fundamentals of heterogeneous nucleation, a method to eliminate sulfuric acid aerosol associated with water recycling in the process of limestonegypsum desulfurization was investigatedImproving the removal efficiency of sulfuric acid droplets from flue The major environmental impact of concrete comes from the CO2 emissions, produced during the cement manufacturing process The main goal of this research project is to evaluate the efficiency of limestone powder as a partial cement replacement, in order to reduce energy consumption and CO2 emissions This study utilizes limestone powders, with different particle sizes, to replace Evaluation of the Efficiency of Limestone Powder in Concrete and
.jpg)
Use of limestone for SO2 removal from flue gas in the semidry
2000年10月15日 Hydrated lime is normally used as SO 2 sorbent in spray dry scrubbers, whereas limestone is considered unreactive under conditions prevailing in such a system However, limestone is more easily available and several times cheaper than hydrated lime We tried to use limestone to remove SO 2 from flue gas in the semidry FGD process with a 2023年8月1日 Throughout the years, many sulfur dioxide removal technologies have been invented and implemented on a wide scale Despite the high sulfur dioxide removal efficiency of conventional treatment methods, such as limestonegypsum desulfurization and spray dry absorption, they generate a large number of secondary sulfurcontaining byproductsSulfur dioxide catalytic reduction for environmental sustainability limestone, sed oiler lu g desulfurization sing ry, semi dry and methods ere used or research ound meston used for esearch as en rom ea objects, e from meston powder torag tanks, sed h flu gas esulfurization stallationExamination of the influence of macro and microscopic 2012年7月21日 Limestone method is widely used in FGD process because of high desulfurization efficiency and low cost However, it is easy to precipitate and block the equipment because of large particle sizeCharacterization of calcium carbonates used in wet flue gas
.jpg)
Enhancement of citric acid on lowgrade limestone wet desulfurization
2022年6月15日 However, the desulfurization efficiency would be definitely less optimistic for WFGD process when using lowgrade limestone as absorbent in view of its relatively large contents of impurities including CaMg(CO 3) 2, SiO 2, Al 2 O 3 and Fe 2 O 3 [13]As such, possibly effective attempts to upgrade the lowgrade limestone have been actively studied in