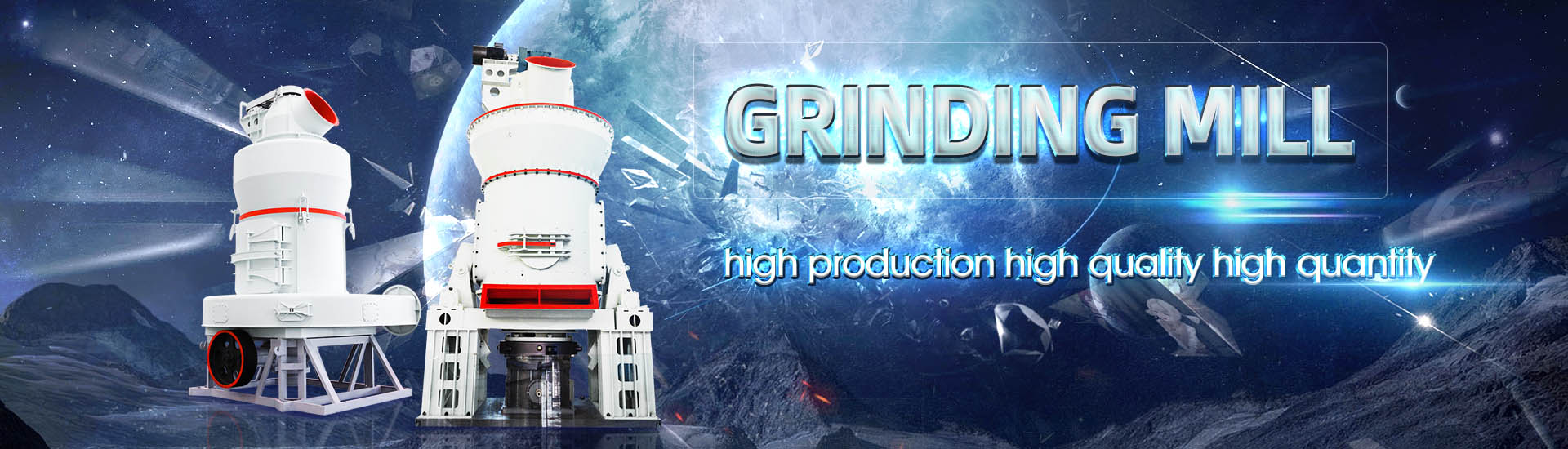
Sintered ore vertical mill
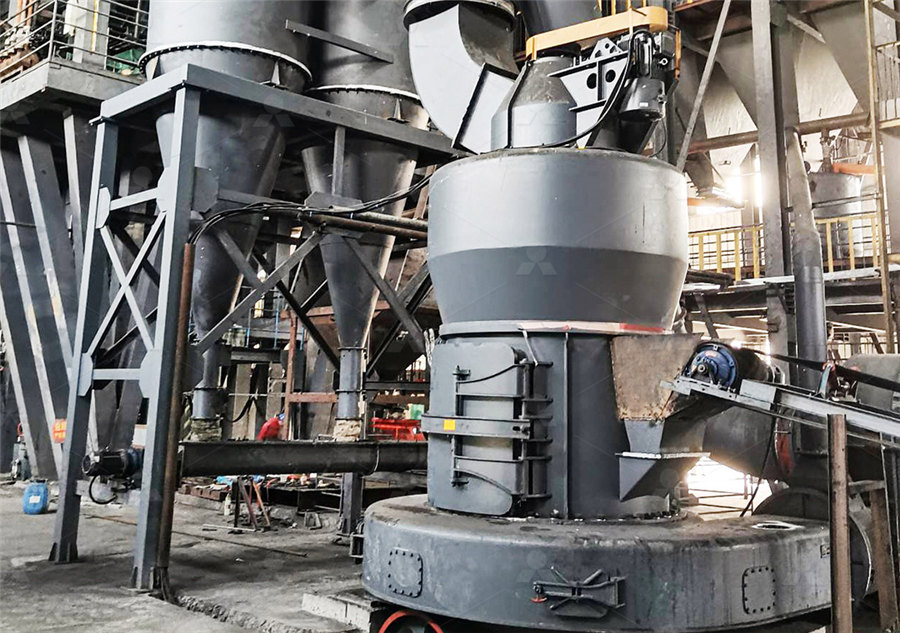
Improving Granulation of Sinter Materials by Using a Wet Vertical
A vertical wet ball mill was installed on a separate granulation line of the Wakayama No 5 Sinter Machine, and 05 mass% of Austra lian goethite ore was ground to −10 micronsOutlook of Iron Ore Supply Tetsuya SHIODA (14MB) Technical Report Improvement of Sinter Productivity by Adding Return Fine on Raw Materials after Granulation Stage (Development of No123 Special Issue on Ironmaking Nippon Steel Corporationsummarized Correspondingly, the challenges in sintering granulation field are proposed to include: (1) Development of iron ore sintering industry; (2) Ore blending optimization based on Iron ore granulation for sinter production: Developments, 2024年2月28日 Lijun, L Study and numerical simulation of gas solid heat transfer process in vertical cooling kiln of sintered ore Metall Autom 43(4), 50–53 (2019) Google ScholarNumerical study and orthogonal analysis of optimal performance
.jpg)
Effect of Addition of Mill Scale on Sintering of Iron Ores
2016年6月30日 Ironrich (65 to 70 pct total Fe) mill scale generated during processing by steel mills can be recycled by using it as a ferrous raw material in the sintering process The effect of mill scale addition on the phase formation of sintered specimens from an industrial sinter blend containing 0 to 15 wt pct mill scale was examined, and the mineral phases formed during Sintering vertical speed, sinter yield and bulk density influence the productivity (Kawaguchi and Hara, 2013) to cool the sintered bed, formed from volatile material in the coke breeze and oily mill scale, and dioxins/furans formed in the presence of carbon, chlorine and metal catalysts, such as Cu, under certain operating conditionsOre Sintering an overview ScienceDirect Topics2019年7月19日 FeO so formed combines with SiO 2 and fluxes resulting in the formation of fluxed sinter The flexibility of the sintering process permits conversion of a variety of materials, including iron ore fines, captured dusts, ore concentrates, and other ironbearing materials of small particle size (eg, mill scale) into a clinkerlike agglomerateSintering: Most Efficient Technologies for Greenhouse Emissions Sintered Ores Kenichi HIGUCHI,1)* Jun OKAZAKI2) and Seiji NOMURA1) 1) Process Research Laboratories, Nippon Steel Corporation, 201 Shintomi, Futtsu, Chiba, in a Ni crucible and heated in a vertical electric furnace The sample was heated up for 1 min from 1 100 to 1 290°C, with subsequent cooled down for 3 minInfluence of Melting Characteristics of Iron Ores on Strength of
.jpg)
Barium carbonate ore vertical mill
2023年2月28日 Performance of vertical mill: High grinding efficiency: The vertical mill adopts highspeed rotating grinding disc and grinding roller, and the material is subjected to multiple impacts and frictions between the two, which can quickly grind the material and improve the grinding efficiency Controllable crushing fineness: By adjusting parameters such as speed 2021年4月27日 Granulation of sinter feed mix is one of the most important factors in determining the permeability of sinter bed and sinter properties like sinter yield, tumbler index, etc To improve the granulation of sinter feed mix, various technologies like twostage granulation process, coating granulation process, wet vertical ball mill and use of magnetic water have been reported In Effect of Mixing Preheated Water on Granulation and Iron Ore 2024年11月1日 In this paper, the adaptability between H 2rich gas injection and sintered ore performance with different raw material ratios was systematically analyzedFirst, the sintering indexes before and after H 2rich gas injection were compared to evaluate the impact of H 2rich gas injection on the yield and quality of sintered ore with different fine ratios and basicityAdaptability analysis of H2rich gas injection and sintered ore 2014年10月20日 Rio Paracatu regrind circuit Santos Júnior et al (2011) presented some data on the Paracatu Vertical Mill circuit process, as well as its comparison to the plant's conventional ball millRegrind of metallic ores with vertical mills: An overview of the
.jpg)
Numerical study and orthogonal analysis of optimal performance
e ˜ ˚ ′ = = ′ = = ℃ 2021年10月13日 Request PDF A Technical and Economic Comparison of Ball Mill Limestone Comminution with a Vertical Roller Mill Wet flue gas desulfurization (WFGD), using limestone with forced oxidation (LSFO A Technical and Economic Comparison of Ball Mill ResearchGate2022年5月1日 The apparent densities of sintered ore particles were measured using the Archimedes drainage method [18] The density of the sintered material was obtained with AccuPyc 1340 automatic true density analyzer Before the measurement, the sintered ore particles were first crushed into powders of about 75 μm using a coal millExperimental study on storage performance of packed bed solar 2024年2月28日 The sinter cooler, essential for cooling hot sintered ore to a specific temperature, has seen recent advancements with the introduction of a vertical sinter cooling furnaceNumerical study and orthogonal analysis of optimal
.jpg)
DEVELOPMENT OF A LABORATORY TEST TO DESIGN VERTICAL
2018年9月17日 The use of vertical stirred mills in the mining industry has increased remarkably over the past few decades, as a result of growing requirement for finer ore grinding2023年7月10日 The present literature review explores the energyefficient ultrafine grinding of particles using stirred mills The review provides an overview of the different techniques for size reduction and the impact of energy requirements on the choice of stirred mills It also discusses the factors, including the design, operating parameters, and feed material properties, EnergyEfficient Advanced Ultrafine Grinding of Particles Using The Pfeiffer pilot mill used in this study is a semiindustrial vertical roller mill of type MVR with a table diameter of 400 mm The mill can be equipped with different classifiers for specific applications The process layout of the plant (Figure 2) corresponds to that of an industrial plantVertical Roller Mills used for the comminution of mineral ores2022年9月21日 Modeling of sintered iron ore deformation during ironmaking blast furnace processes is important to achieve superior process operations, particularly with the current goal of decarbonization In this study, the hightemperature softening behavior of sintered iron ore characterized by a lowmeltingpoint molten slag core and solid ironrich phase shell structure Dynamic Model of HighTemperature Sintered Iron Ore Plastic
.jpg)
Pressure drop in a packed bed with sintered ore particles as
2016年2月11日 The pressure drop over a packed bed with sintered ore particles was studied experimentally The sintered ore particles were characterized to determine their equivalent particle diameter, bed voidage, and sphericity The pressure drop experiments were performed on unsorted and sieved particles with various size distributions for a superficial velocity up to 24 2014年10月1日 Request PDF Copper Ore Grinding in a Mobile Vertical Roller Mill Pilot Plant Vertical roller mills (VRM) have been used extensively for comminuting both cement raw materials and minerals like Copper Ore Grinding in a Mobile Vertical Roller Mill Pilot Plant2015年8月1日 The physical properties of oxidative sintered pellets produced from typical South African UG2 ore are compared with the physical properties of pellets produced with conventional South African Comparison of physical properties of oxidative sintered pellets 2014年11月1日 The application of vertical mills in regrind circuits is consolidated This type of mill is now attracting interest in primary grinding applications, due to its higher efficiency when compared to Vertical mill simulation applied to iron ores
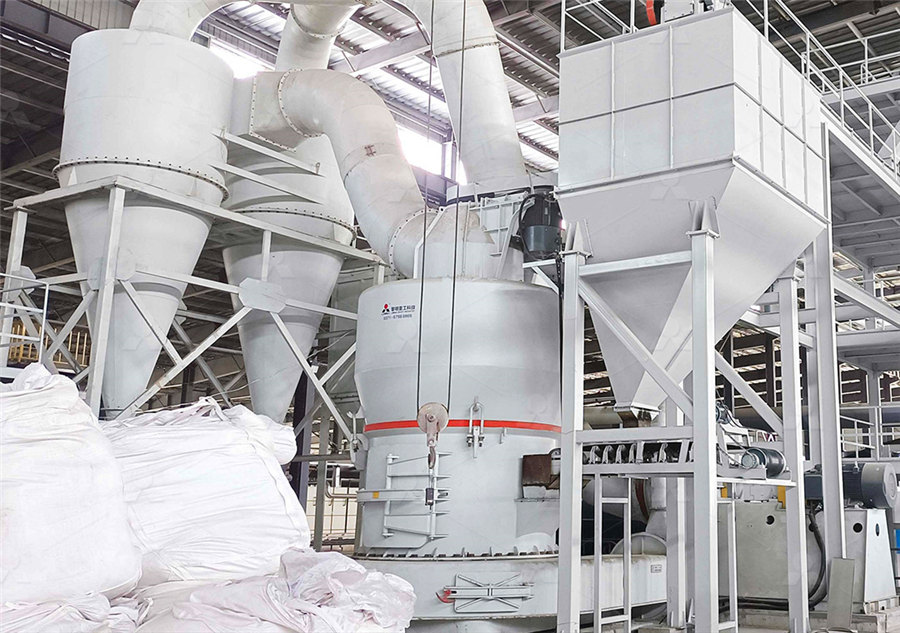
RECENT DEVELOPMENTS IN COARSE GRINDING USING VERTICAL
Figure 3: Relationship between feed size (F80) and Bond efficiency factor (Huang et al, 2019) VERTICAL POWER MILL (VPM) – PRINCIPLE OF OPERATION Declining ore grades and more complex ore bodies, as well as waste management and global net zero initiatives, lead to a clear trend for high tonnage yet energy efficient grindingSinter plants agglomerate iron ore fines (dust) with other fine materials at high temperature, to create a product that can be used in a blast furnaceThe final product, a sinter, is a small, irregular nodule of iron mixed with small amounts of other minerals The process, called sintering, causes the constituent materials to fuse to make a single porous mass with little change in the Sinter plant WikipediaPressure drop in a packed bed with sintered ore particles as applied to sinter coolers with a novel vertically arranged design for waste heat recovery* Fuyou TIAN 1, dry quenching operation in vertical tanks, has been proposed in an effort to improve the waste heat recovery efficiency (Zhao et al, 2009), Pressure drop in a packed bed with sintered ore particles asJet mill: 5um powder can be produced, jet pulverization, the whiteness of the finished powder is the best Highend food grade finished powder Mechanically crushed, the powder has the highest fineness It is only suitable for highend or high valueadded powders High energy consumption and low output Ultrafine vertical grinding millCLUM Ultrafine Vertical Grinding Mill
.jpg)
Iron ore granulation for sinter production: Developments,
Iron ore granulation is an indispensable process in the production of sinter that can influence and regulate the yield, efficiency and quality Although a great deal of research has been done on the granulation process over the past decades, we still need to think about the current and future development Pressure drop in a packed bed with sintered ore particles as applied to sinter coolers with a novel vertically arranged design for waste heat recovery* Fuyou TIAN 1, dry quenching operation in vertical tanks, has been proposed in an effort to improve the waste heat recovery efficiency (Zhao et al, 2009), Pressure drop in a packed bed with sintered ore particles as 2019年12月24日 Energy Resources, Its Role and Use in Metallurgical Industries RC Gupta, in Treatise on Process Metallurgy: Industrial Processes, 2014 423132 Sinter Making The iron ore fines (− 10 mm) are agglomerated using Dwight Lloyed sintering machine The iron ore fines and coke breeze fines mix with moisture is fed on the sinter bed which is ignited by a gas Sintered Ore an overview ScienceDirect TopicsA vertical roller mill, also known as a vertical grinding mill or vertical mill, is a comprehensive grinding equipment integrating crushing, drying, grinding, grading, and conveying Vertical grinding mills can be widely used in electric power, metallurgy, construction, chemical industry, and other industries to make powder, especially for materials such as cement clinker, coal Energysaving and Efficient Vertical Roller Mill Fote Machinery
.jpg)
Numerical study and orthogonal analysis of optimal performance
2024年2月28日 Conduct a reliability verification of the model The vertical cooling process of sintered ore has not yet been widely applied in existing industrial practices Therefore, the paper chose to compare the heat transfer calculation model’s accuracy with experimental data of singlegrade sintered ore from the study by Zhang 12016年10月28日 Sintering is an agglomeration process that fuses iron ore fines, fluxes, recycled products, slagforming elements and coke The purpose of sintering is to obtain a product with suitable Iron Ore Sintering: Raw Materials and Granulation2015年1月1日 Like other sintering processes, iron ore sintering converts iron ore fines of often − 8 mm sizing into larger agglomerates, namely, sinter, between 5 and 50 mm particle size, which possess the physical and metallurgical characteristics and gas permeability required for efficient blast furnace operationAs shown in Figure 141, iron ore sintering is carried out in three Iron ore sintering ScienceDirect2015年3月10日 DOI: 101016/JMINPRO201410002 Corpus ID: ; Copper ore grinding in a mobile vertical roller mill pilot plant @article{Altun2015CopperOG, title={Copper ore grinding in a mobile vertical roller mill pilot plant}, author={Deniz Altun and Carsten Gerold and Hakan Benzer and Okay Altun and Namık A Aydogan}, journal={International Journal of Copper ore grinding in a mobile vertical roller mill pilot plant
.jpg)
Sintering: A Step Between Mining Iron Ore and Steelmaking
2019年6月11日 World resources are estimated to be greater than 800 billion tons of crude ore containing more than 230 billion tons of iron The only source of primary iron is iron ore, but before all that iron ore can be turned into steel, it must go through the sintering process Sinter is the primary feed material for making iron and steel in a blast furnace2016年6月30日 Secondly, any Fe 2 O 3 which forms through oxidation of the FeO and Fe 3 O 4 in the mill scale only begins to convert to Fe 3 O 4 above ∼1150°C (see Figures 1 and 2) and so no appreciable Effect of Addition of Mill Scale on Sintering of Iron OresChina Vertical Shaft Impact Crusher (PCL1100) and China Make Mineral Ore Making Machine,Make Mineral Ore to Sand of metallurgy slag, especially carborundum, sintered » Free Online Chat Ma’aden Magnesite Project – Scribd Vertical Shaft Kiln A Vertical Shaft Kiln is utilized for the production of sintered or deadvertical shaft for sintered ore – Grinding Mill China2022年1月1日 The mineral processing of iron ore generates a large quantity of fines, considering particles under 5 mm in size [1,2] Blast furnace (BF) ironmaking involves a vertical countercurrent process Iron ore sintering ResearchGate
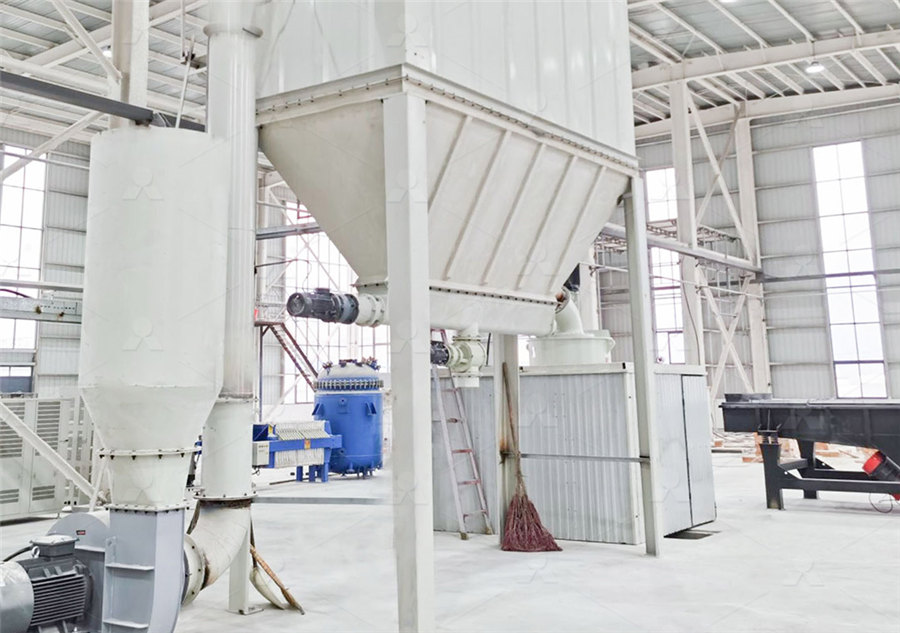
vertical roller mill Archives International Mining
A new LOESCHE vertical roller mill is in the process of being assembled at Aluminium Corp of China’s (Chinalco) copper smelting plant in the southern Chinese province of Fujian The threeroller mill will be operated by Chinalco’s Southeast Copper Ltd subsidiary and is able to grind 100 t/h of copper matte to a fineness of 20% with a sieving residue of 0074 mm, according to Request PDF On Mar 15, 2015, Mathis Reichert and others published Research of iron ore grinding in a verticalrollermill Find, read and cite all the research you need on ResearchGateResearch of iron ore grinding in a verticalrollermill