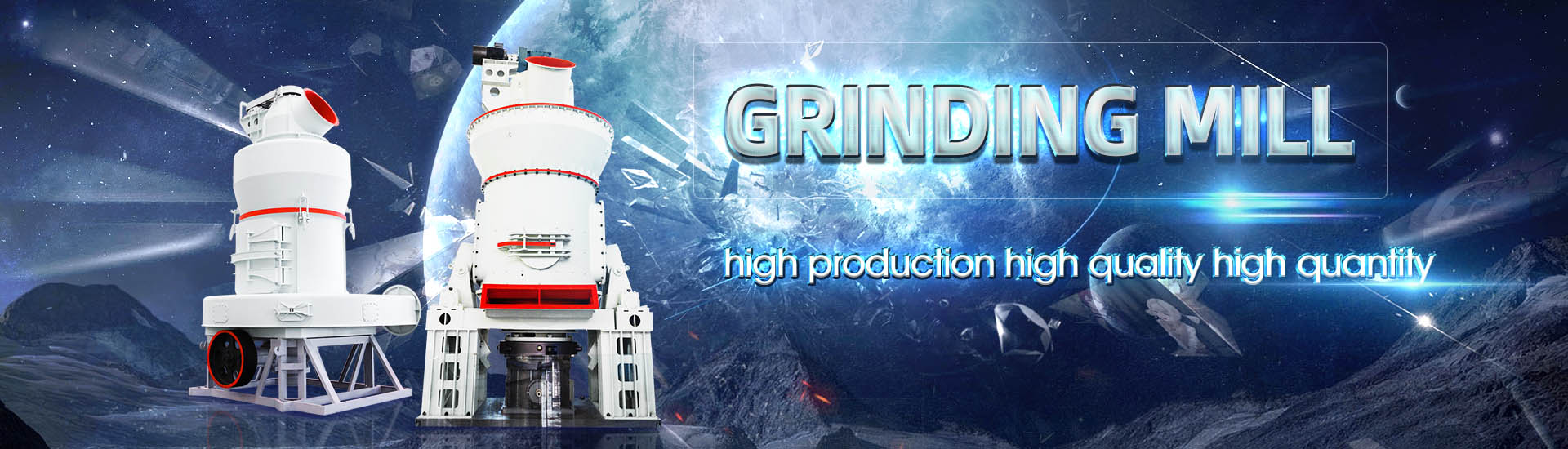
Laterite nickel powder processing equipment
.jpg)
Hydrometallurgical nickel and cobalt plants and processes
Metso Outotec can perform laterite leaching in HPAL and atmospheric conditions Depending on your mineralogical requirements, nickel laterite highpressure acid leaching (HPAL) solutions 2024年8月7日 The two main processing methods for laterite ores are smelting and HighPressure Acid Leaching (HPAL) Smelting is used primarily on saprolite ores to obtain an iron Nickel industry Part 2 Processing nickel laterites and smeltingCaron technology is a comprehensive technology for processing lateritic nickel ores, including pyro and hydrometallurgical processes Laterite ores are mainly processed using this Review on hydrometallurgical processing technology of lateritic 2024年5月3日 Ore is often processed near the mine site, but there is substantial regional and global trade in nickel laterite ores, and some trade in nickel sulfide concentrates Laterite ores occur as surface deposits and are traditionally Nickel industry Part 1 Processing nickel laterites and
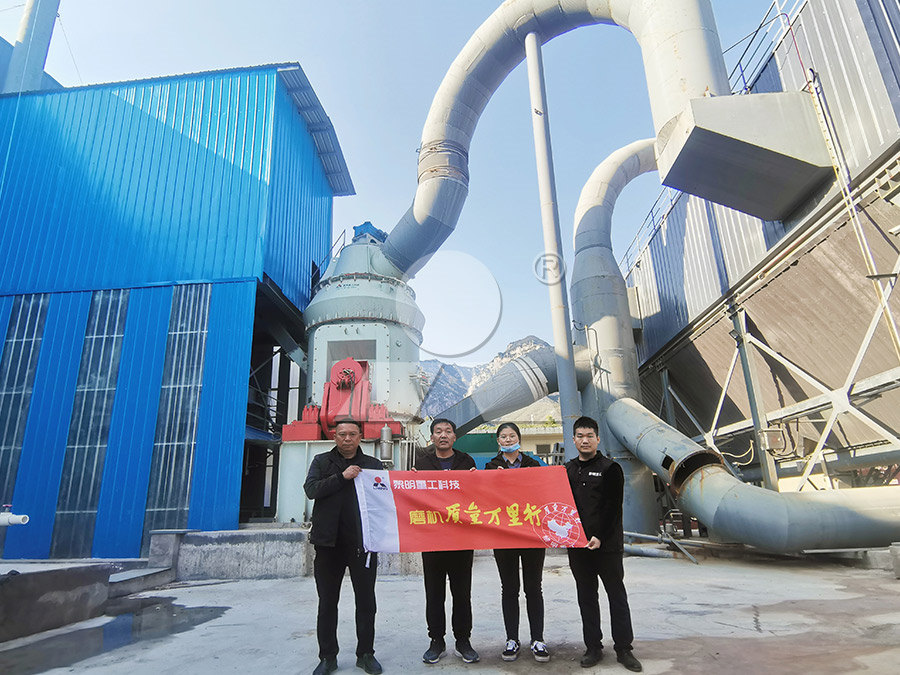
THE DNi PROCESS™ Altilium Group
The DNi Ni Process™ is a unique technology which can process the full laterite ore profile (limonite, saprolite, and transition zone) with nitric acid, and which extracts all the metals contained in the feed Boasting a 99% nitric acid 2019年3月11日 Hydrometallurgical Processing of Nickel Laterites—A Brief Overview On The Use of Solvent Extraction and Nickel/Cobalt Project For The Separation and Purification of Nickel and Cobalt(PDF) Hydrometallurgical Processing of Nickel 2024年11月1日 At present, the smelting process of nickel laterite ore in the world is roughly divided into two categories: the hydrometallurgy and the pyrometallurgy Hydrometallurgical Review on comprehensive utilization of nickel laterite ore2002年8月1日 The BIOX ® Process flowsheet involves: (i) bioleaching, (ii) pH adjustment for iron removal, (iii) solid/liquid separation, (iv) production of either a sulphide concentrate or Nickel laterite processing and electrowinning practice
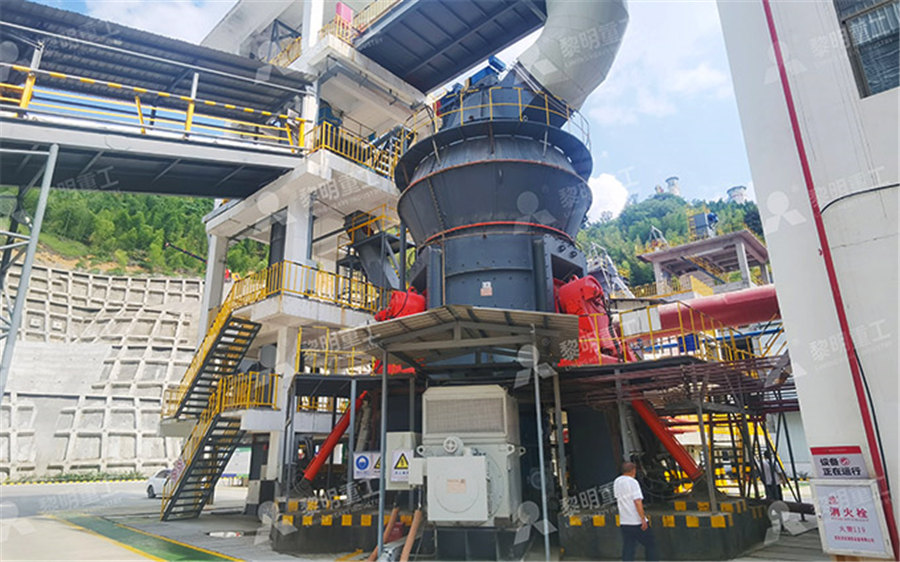
An Overview of Nickel Utilization from Laterite Ore
2023年1月19日 Based on a brief introduction of properties of metallic nickel, it summarizes the applications of nickel, demand of nickel, resources of nickel, and metallurgical processes of laterite ore, in which the rotary kilnelectric furnace 2020年4月14日 The processing of nickel laterites by high pressure acid leaching (HPAL) typically uses feeds with an average nickel content not less than 11%–12% (cutoff grade 10%) [] though recently several nickel laterite The High Temperature CoProcessing of Nickel Unlike sulphide nickel ore processing, laterite nickel ore processing requires higherprocessing energy through smeltingTherefore, briquettes, granules, rondelles and powder/flakes Class II has nickel content less than 99% The product examples of class II are Ferronickel, nickel oxide sinter, utility, andSelective Reduction of Laterite Nickel Ore JSTAGE2021年10月24日 Nickel laterite ore is used to produce nickel metal, predominantly to manufacture stainless steel as well as nickel sulfate, a key ingredient in the batteries that drive electric vehicles Nickel laterite production Nickel Laterites—Mineralogical Monitoring for Grade
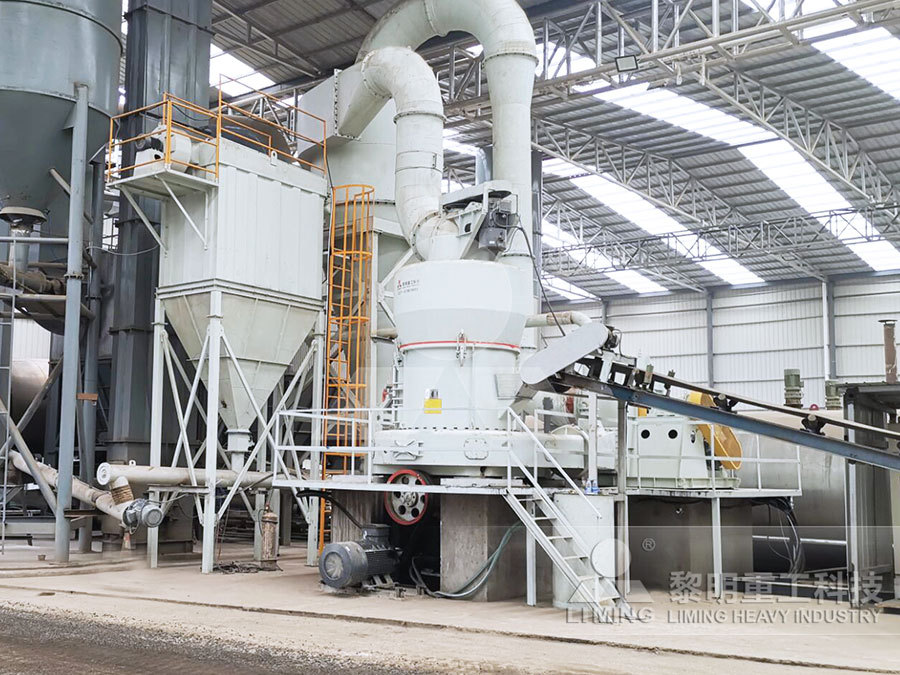
Phosphoric Acid Leaching of Ni–Co–Fe Powder Derived from
2024年2月3日 Efficient extraction of nickel and cobalt from laterite ores is essential for the rapid development of new energy vehicles (EVs) In this work, Ni–Co–Fe powder with nickel, cobalt, and iron grades of 1198%, 118%, and 7013%, respectively, was obtained from a limonitic laterite ore via rotary kiln reductive roasting followed by magnetic separationNickel laterite processing and nickel powder and flakes Norilsk is the world’s second largest nickel producer and represents a significant Minerals Engineering 12 (1), 65–73 Moskalyk, RR, Pariani, RL, 1984a Metal refining handling equipment justificationPart 1, automating starter sheet stripping Nickel laterite processing and electrowinning practicePDF On Mar 11, 2019, Sait Kursunoglu and others published Hydrometallurgical Processing of Nickel Laterites—A Brief Overview On The Use of Solvent Extraction and Nickel/Cobalt Project For The (PDF) Hydrometallurgical Processing of Nickel Laterites—A 2017年1月20日 This paper presents a life cycle assessment (LCA) study of three nickel laterite processing technologies The main goal was to quantify selected environmental impact categories and to compare and analyse each impact category for three different nickel feedstock for stainless steel production The nickel laterite processing routes were (1) high pressure acid leaching A life cycle assessment of a new laterite processing technology
.jpg)
Nickel Laterites—Mineralogical Monitoring for Grade Definition
2021年10月24日 Dendrogram after cluster analysis based on the correlation matrix from 40 nickel laterite samples (cluster 1 = orange, cluster 2 = yellow, cluster 3 = light green, cluster 4 = dark green), Xaxis 2019年1月10日 Flowsheet of Caron's process for processing of high iron limonitic laterite ores (Caron, 1950) The dotted box indicates the practices adopted in Yabulu, Australia (Kyle 2010) +12(PDF) Advanced Review on Extraction of Nickel from Primary 2024年11月12日 Thermal Treatment of Nickel Laterite The main nickel and ironbearing phases in nickel laterite are complex but for an approximate comparison of the reduction behavior of various species, we use the existing data for simple oxides Ni 2 SiO 4, NiO, NiFe 2 O 4, Fe 2 O 3, Fe 3 O 4, FeO, and Fe 2 SiO 4The Ellingham diagram for these oxides is in Fig 1a The A Review of Direct Reduction–Magnetic Separation Process for 2011年5月1日 Therefore, research in hydrometallurgical processing of laterite nickel ores has been vibrant, at least in the last three decades, resulting in many new technological development such as Recent Developments in the Chloride Processing of
.jpg)
Sherritt International Our Products
Sherritt International is a recognized world leader in the production of high purity nickel and cobalt metal from lateritic ore Mining and refining only in nonconflict jurisdictions, through its Moa Joint Venture, the high quality battery and alloy ready nickel and cobalt produced are used worldwide in stainless steel, specialty steel, chemical and welding applications2024年1月1日 HPAL process for short is suitable for processing nickel laterite of limonite type with less than 5% content of magnesium in general to avoid excessive acid consumption Generally, for this type of nickel laterite ore, the contents of nickel and cobalt are 08–15% and 01–02% respectivelyNickel Laterite Metallurgy SpringerLink12224 j mater res technol 2020;9(6):12223–12235 1 Introduction In general, increasing attention has been paid to laterite ores as an alternative to nickel sulfide ore [1–5]Separation and recovery of iron and nickel from lowgrade laterite 1 Crushing Screening The raw ore enters the jaw crusher through the feeder for primary crushing and then enters the cone crusher for medium crushing After the vibrating screen screening, the materials under the screen enter the grinding process while the screened materials enter the finecrushing process And select the cone crusher for the finecrushing operationNickel Ore Processing Plant JXSC Mineral
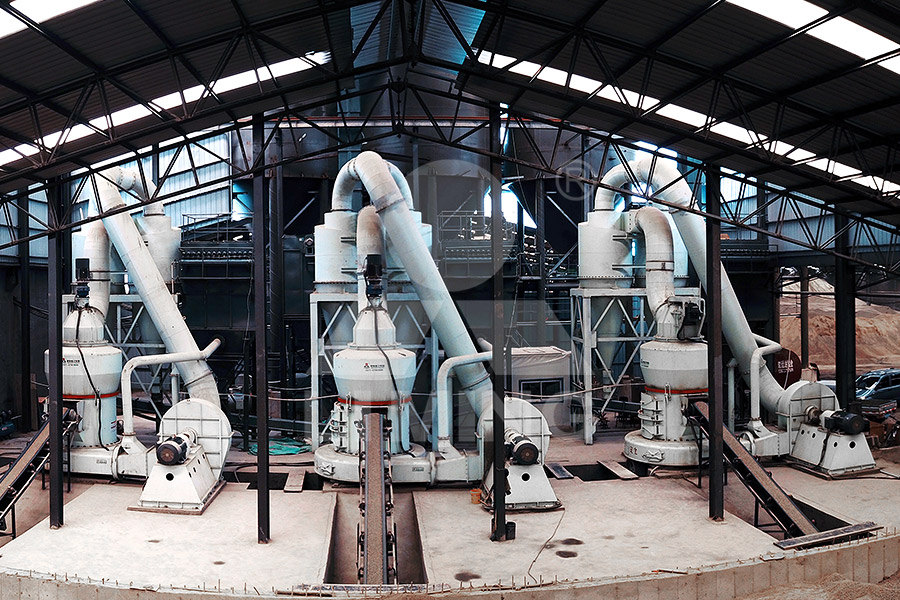
How to Extract Laterite Nickel Ore? 7 Processing Methods
2022年5月31日 The processing methods of laterite nickel ore is mainly divided into two types: pyrometallurgy process and hydrometallurgy process According to the difference of nickel, cobalt content and ore type, and different working conditions, there are 7 kinds of methods to choose from This article will introduce you to these 7 laterite nickel ore processeshydrometallurgical processing is used for ores with low nickel content with the ratio of the main components SiO 2 /MgO, Fe/Ni and Ni/Co 15 and 12 and more than 30, respectively [24] The most common concentration process used before industrial hydrometallurgical processing of nickel laterites is to remove the coarse fraction from the feedstock,Review on hydrometallurgical processing technology of lateritic nickel 2023年4月25日 In the nickel ore processing plant, different types of nickel ore need mineral processing procedures and mining equipment based on the characteristics and composition of the ore Therefore, it is necessary to conduct beneficiation tests, design a feasible nickel ore beneficiation process, and then equip corresponding mining machines2 Types of Nickel Ore: Processing Methods and EquipmentNickel is a strategic metal with a wide range of industrial and metallurgical uses (Sadat et al, 2016)The use of nickel has now spread to a wide range of sectors, including steel alloying elements, space applications, and rechargeable batteries (Buyukakinci, 2008)Nickel is highly corrosionresistant in contact with air, seawater, and organic and nonoxidizing acids; on the Bioleaching of Lateritic Nickel Ores SpringerLink
.jpg)
DEVELOPMENTS IN THE HYDROMETALLURGICAL PROCESSING OF NICKEL
INTRODUCTION Nickel laterite ores comprise a significant resource in Australia and according to United States Geological Survey data nearly a quarter of world reserves are located there (USGS, 2016)2023年2月15日 laterite nickel ore mostly exists in sapropelic deposits, and the content of laterite nickel increases with depth The raw nickel ore is always companied by clay and impurities The washing ore process can remove clay The Best Mining Equipment for Philippines Nickel 2021年1月18日 However, one common processing step in laterite operations producing Class 1 nickel is high pressure acid leaching (HPAL) HPAL entails laterite ore being fed into an autoclave along with sulfuric acid at temperatures The Great Laterite Challenge: Why Scaling Class 1 2022年5月16日 The process has not been industrially applied to the processing of nickel sulfide concentrates and information on processing of nickel sulfide concentrates is limited; the original patent by Hourn, Turner, and Holzberger Full article: The Direct Leaching of Nickel Sulfide
.jpg)
Current Studies of Treating Processes for Nickel Laterite Ores
PDF On Jan 1, 2017, Xiaoping Wang and others published Current Studies of Treating Processes for Nickel Laterite Ores Find, read and cite all the research you need on ResearchGatePortable XRF is an effective method for exploring nickel laterite mineralization (Cr, Mn, Fe, Co, Ni, Mg, Al, and Si) Extraction and processing of nickel laterites usually necessitate extremely largescale acid leaching or roasting in rotating Related Equipment The Vanta Series Advanced Handheld XRF Analysis in the Field and Nickel Laterite Mineralization Explored by Portable XRF2022年8月22日 The effects of ore grade on embodied energy and GHG emissions were estimated by Norgate etal for the various nickel laterite processing routes The Leaching of a Turkish lateritic nickel ore in nitric acid solution In Mine Planning and Equipment Selection, Springer, Cham (2014) 10391045Recent Progress in Hydrometallurgical Processing of Nickel 2019年9月3日 Lowgrade ferronickel is simply an iron–nickel alloy that contains lower nickel than standard ferronickel does (ie, minimum of 15%) According to the literature, within a very short(PDF) Nickel Laterite Smelting Processes and Some
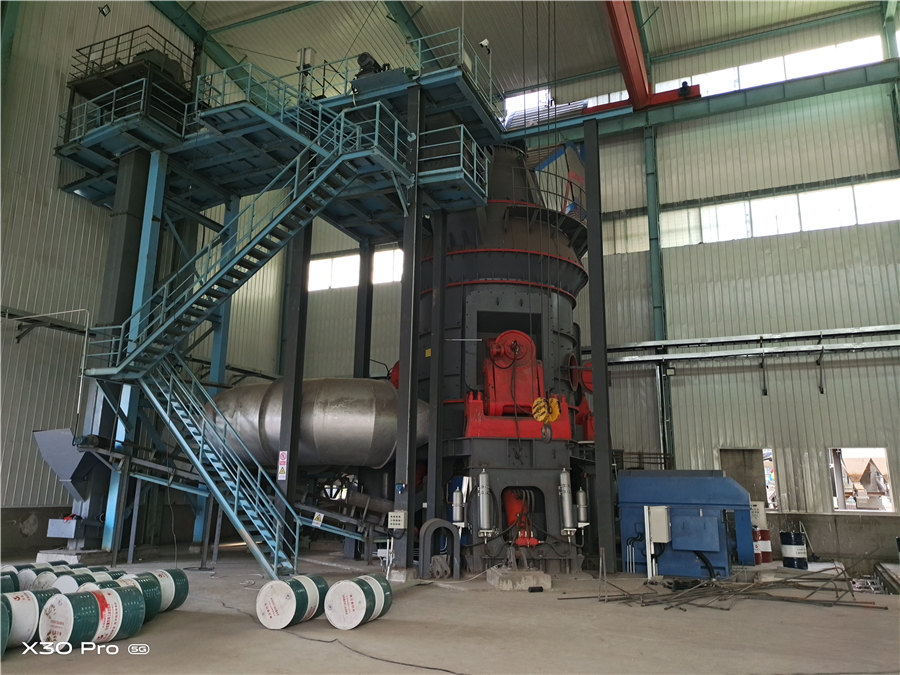
Effect of CaF2 on the aggregation and growth of ferronickel
REGULAR ARTICLE Effect of CaF 2 on the aggregation and growth of ferronickel particles in the selfreduction of nickel laterite ore Guihua Hang1,2, Zhengliang Xue2,3,4,*, Ying Jiang Wu2,5, and Bo and cobalt from all horizons of a nickel laterite profile has been introduced and discussed in some detail over the past few years [1,2,3,4,5], this approach is still being treated with caution ApartRECENT DEVELOPMENTS IN THE CHLORIDE PROCESSING OF NICKEL2020年7月22日 Laterite ores are becoming the most important global source of nickel and cobalt Pyrometallurgical processing of the laterites is still a dominant technology, but the share of nickel and cobalt Review of the past, present, and future of the hydrometallurgical 2024年1月19日 It finds extensive use in industries such as construction, automotive, aerospace, food processing, and medical equipment 3 Alloys and Superalloys (HPAL): HPAL is a widely used method for extracting nickel The Comprehensive Guide to Nickel Processing
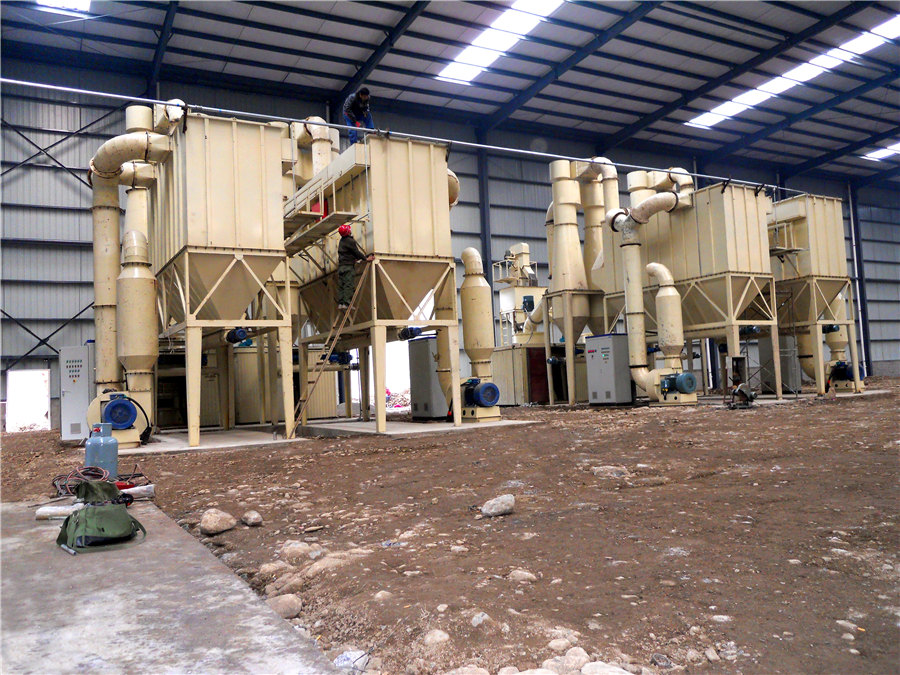
Laterite Nickel Ore Hydrometallurgical Process for Oxide Ore
2024年7月9日 1Raw ore crushing: First, crush the laterite nickel ore to a certain size for subsequent processing 2Pressure acid leaching:The crushed ore reacts with dilute sulfuric acid (such as sulfuric acid or hydrochloric acid) under pressure conditions (230260 ℃, 45MPa)2024年9月1日 Nickel resources in Australia are laterite nickel (69%) and nickel sulfide (31%), mainly in Western Australia (90%), Queensland (5%) and New South Wales (4%) [46] Scandiumrich laterite deposits have been found in New South Wales and Queensland in eastern Australia, and scandium reaches concentration values up to 800 gt −1 in the Sunrise project [ 47 , 48 ]Hydrometallurgical process and recovery of valuable elements for 2020年11月5日 Nickel slags can be produced through ferronickel preparation by the pyrometallurgical processing of laterite nickel ores; however, such techniques are underutilized at present, and serious environmental problems arise from the stockpiling of such nickel ores In this study, a modification to the process of ferronickel preparation by the direct reduction of carbon Coupled Preparation of Ferronickel and Cementitious Material from Recently, the rapid development of electric vehicles has raised concerns about the availability of the metal resources required for Liion batteries, such as iron (Fe), cobalt (Co), and nickel (Ni) [1], [2]Laterite nickel ore, which accounts for 75 % of the total nickel reserves, has emerged as a primary source for nickel mining in the future [3], [4], [5]Recovery of highquality iron phosphate from acidleaching
.jpg)
What is nickel laterite? Homeland Nickel
Nickel laterite makes up 70% of the world’s nickel reserves, and at the rate that nickel sulphide deposits are being depleted, production is switching to laterites which now account for 60% of the world’s nickel Nickel laterite is normally processed by pyrometallurgy (ie heat), hydrometallurgy (ie acid), or in some cases blending with Minerals 2020, 10, 351 3 of 21 total sulfide contents provided by Poseidon Nickel Limited The primary aim was to demonstrate the technical viability for coprocessing these materials, from which Sulfide and Nickel Laterite Sources ResearchGate2022年4月29日 In order to improve the recovery ratio of valuable metals in stainless steel dust, reduce environmental pollution, and promote solid waste resource recovery and sustainable development of industry, the synergistic reduction process for preparing Fe–CrNiC alloy was studied in detail by changing the addition of laterite nickel ore and reduction process A novel process for preparing Fe–CrNiC alloy: synergetic nickel and cobalt from lowgrade nickel laterite is hydroelectrometallurgy In the previous research phase of solvent extraction, Versatic Acid 10 was chosen as an extractant to separate calcium andOptimization of The Electro Metal Electrowinning Process for Nickel
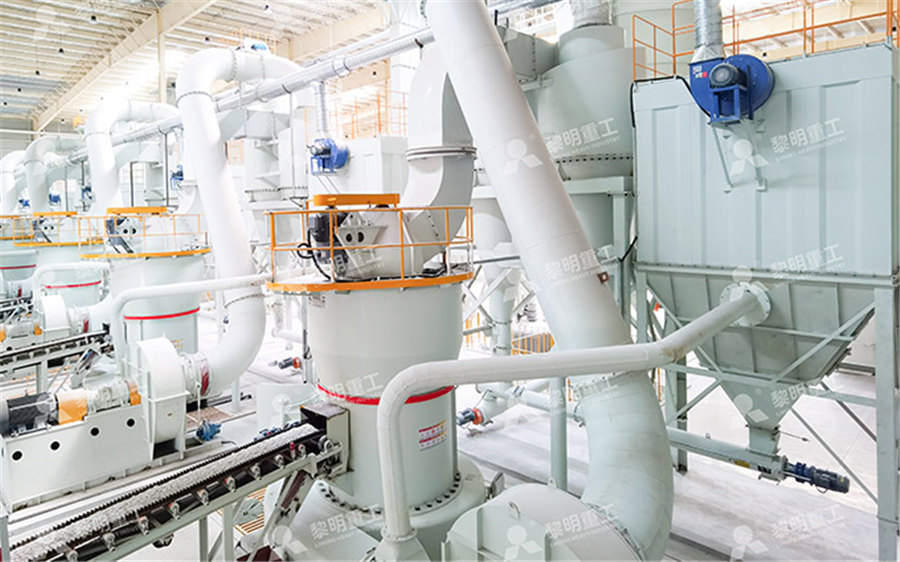
Processing of Nickel Laterite Ores: A Review of Scientific Scribd
NickelLateriteProcessingBackgroundDocumentpdf Free download as PDF File (pdf), Text File (txt) or read online for free The document discusses processing methods for nickel laterite ores It describes that laterite ores typically occur in tropical, weathered regions and have layered structures with varying nickel concentrations Two main processing methods are high