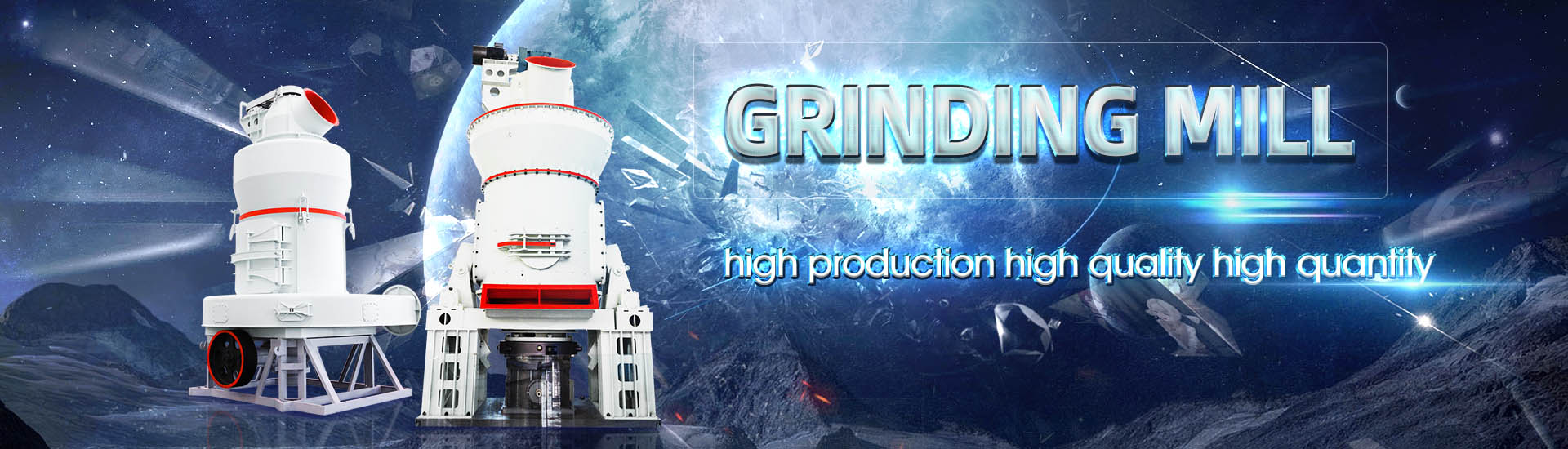
Cement wet grinding, process

Wet Process Of Cement Manufacturing With Flow Chart
The following is a wet process of cement manufacturing stepbystep guide, 1 The raw limestone from quarries is first crushed into small size fragments Then it is mixed with clay or shale in a ball or tube mill and ground to form a slurry of a fine consistency with the addition of water (The slurry is prepared with a 展开The grinding process can be done in ball or tube mill or even both Then the slurry is led into collecting basin where composition can be adjusted The slurry contains around 3840% water that is stored in storage tanks and kept ready Manufacture of Cement Materials and Manufacturing What are the steps involved in manufacturing cement? Cement production involves several key steps, including: Crushing the raw materials Homogenizing the mixture Proportioning the raw materials accurately Grinding the materials StepbyStep Guide to the Manufacturing of CementSome manufacturers grind the raw materials dry, while others use a wetgrinding process involving water Cement manufacturers quarry raw materials including limestone, clay, and sandHow Cement is Made Portland Cement Association
.jpg)
Manufacturing of Cement By Dry and Wet Process
In the dry process, the raw materials mixed, fined, and then fed into kiln whereas, in the wet process, the raw materials are crushed separately and then directly mixed in correct proportion in the presence of water to make a fine thin paste 2024年9月10日 Here is a stepbystep procedure for the wet process of Cement manufacture: Quarrying and Crushing: The raw materials, such as Limestone, clay, and iron ore, are extracted from quarries and then crushed into smaller Cement Manufacturing Process: Know Extraction, 1971年8月17日 Five different processes are used in the portland cement industry to accomplish the pyroprocessing step: the wet process, the dry process (long dry process), the semidry 116 Portland Cement Manufacturing US EPAWhat is the Wet Process of Cement Manufacturing? The wet process involves mixing raw materials like limestone, clay, and sand with water to create a slurry This slurry is then Wet Process of Cement Manufacturing: Detailed Overview
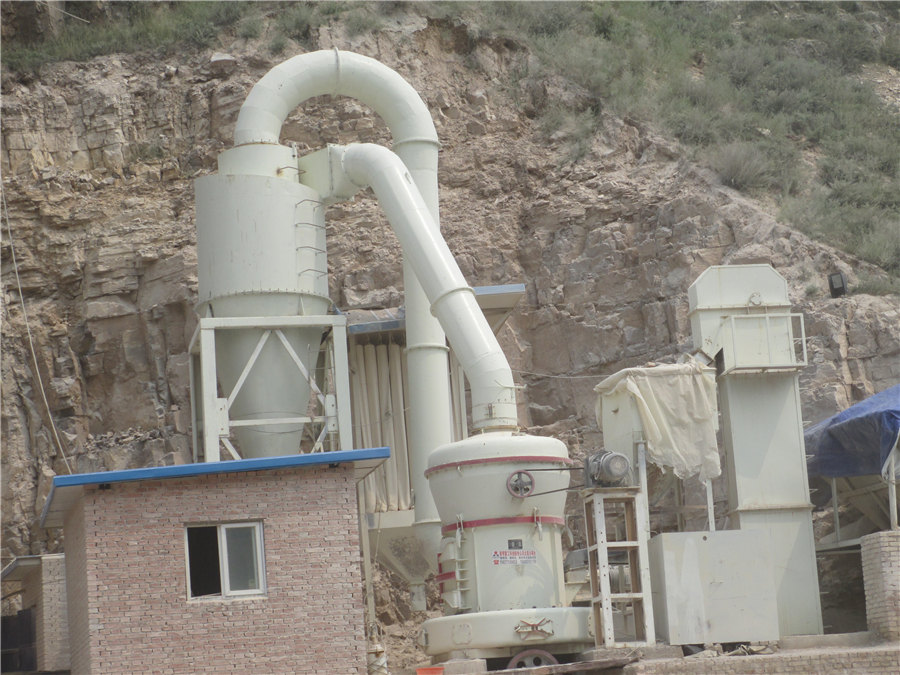
Preparation of nanokaolin by wetgrinding process and its
2021年12月1日 Wet grinded kaolin significantly enhanced the early strength of Portland cement The results provided a novel approach to utilize kaolin in Portland cement system Achieving There are four main types of processes used in cement manufacture: Dry Process, Semidry Process, Semiwet Process, and the Wet process In all these processes, the following steps Cement Manufacturing—Technology, Practice, and DevelopmentWhat are the dry and wet process of manufacturing of cement? How dry and wet process are done in preparation of cement Pros and cons of each method Sketches Skip to In the wet process, which involves grinding raw materials 2 Types of Manufacturing of Cement Wet and Dry Stage 2: Grinding, Proportioning, and Blending The crushed raw ingredients are made ready for the cementmaking process in the kiln by combining them with additives and grinding them to ensure a fine homogenous mixture The composition of cement is proportioned here depending on the desired properties of the cement Generally, limestone is 80%, and the remaining 20% How Cement is Made Cement Manufacturing Process
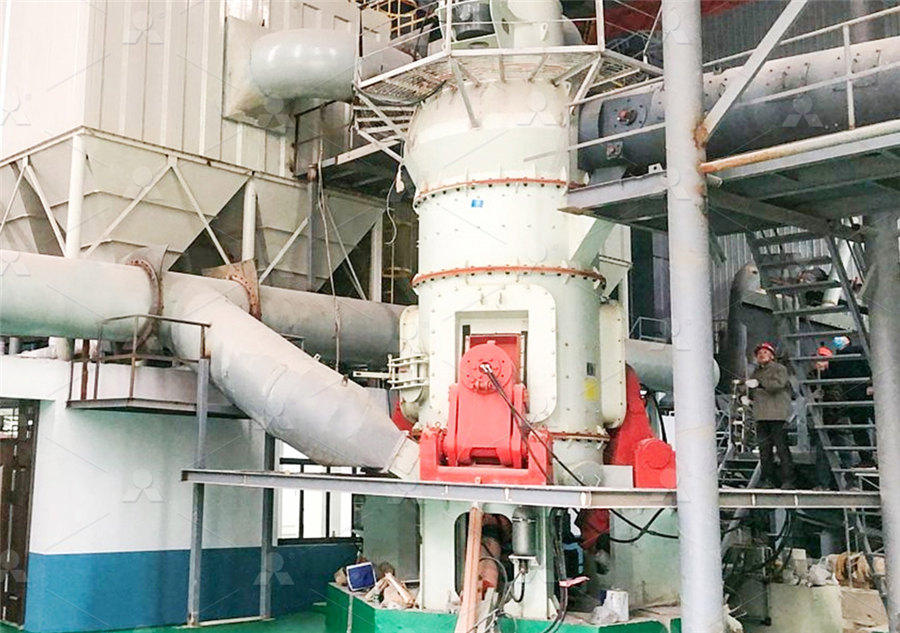
116 Portland Cement Manufacturing US Environmental
cement plants with wet process kilns is 305006, and the sixdigit SCC for plants with dry process kilns L Clinker grinding 17 M Cement silos 18 N Cement load out 19 O Raw mill feed belt 24 P Raw mill weigh hopper 25 Q Raw mill air seperator 年12月20日 With the dosage less than 10%, wetgrinded lithium slag can notably promote the early strength of the sulphoaluminate cement paste, and the main reason for the promotion is not only because of the filling effect of fine particles and nucleation seed induction of nano particles formed in wetgrinding process, but also due to the fact that the dissolved lithium can Utilization of lithium slag by wetgrinding process to improve the 2024年1月17日 Contemporary methods of manufacturing cement can be divided into two ways: dryprocess cement production and wetprocess cement production The latter measure has been widely utilized in the cement industry; it is a common manufacturing method in which fuel and power consumption have been reduced to a larger extentWhat Do You Know About Wet Process Of Cement Production2016年10月23日 Exact proportioning is dependent upon their chemical properties before and after calcining to cement clinker For good kiln practice the grind required is 8892% – 200 mesh for standard cement, 99%200 mesh for high early Uniform kiln feed size helps reduce tendency to form kiln rings WET VS DRY Grinding of Cement Wet grinding is generally Cement Grinding 911Metallurgist
.jpg)
Effects of CSH Seed Prepared by Wet Grinding on the
2024年7月24日 This study aimed to utilize the hydration characteristics of cement through wet grinding techniques to efficiently and conveniently prepare a stable CSH seed suspension, providing key parameters and a scientific basis for their largescale production, which ensures the stability of the CSH suspension during production, transportation, and application This 2021年12月1日 Therefore, it was expected that wetgrinding KL (ie, WGKL) was used as a crystal nucleus, inducing cement hydration and improving the strength of cement in the early period Herein, an attempt to treat KL by wetgrinding process and use WGKL as an early strength accelerator in PC systemPreparation of nanokaolin by wetgrinding process and its Cement production in cement plants can be divided into cement wet process and cement dry process The wet process of cement manufacturing has the characteristics of simple operation, What’s more, the energy consumption of raw material grinding in the wet process is reduced by nearly 30% Disadvantages: All about the Wet Process of Cement Manufacturing2021年11月8日 In literature [32], wetgrinding technique was applied to disposal waste hardened cement and obtained particle of 249 nm Other researcher displayed that the median particle sizes of monosized quartz particles were around 05–06 μm by the wet grinding condition; the particle size of wet grinding was about 25% of that of dry grinding [33]Preparation of nano cement particles by wetgrinding and its
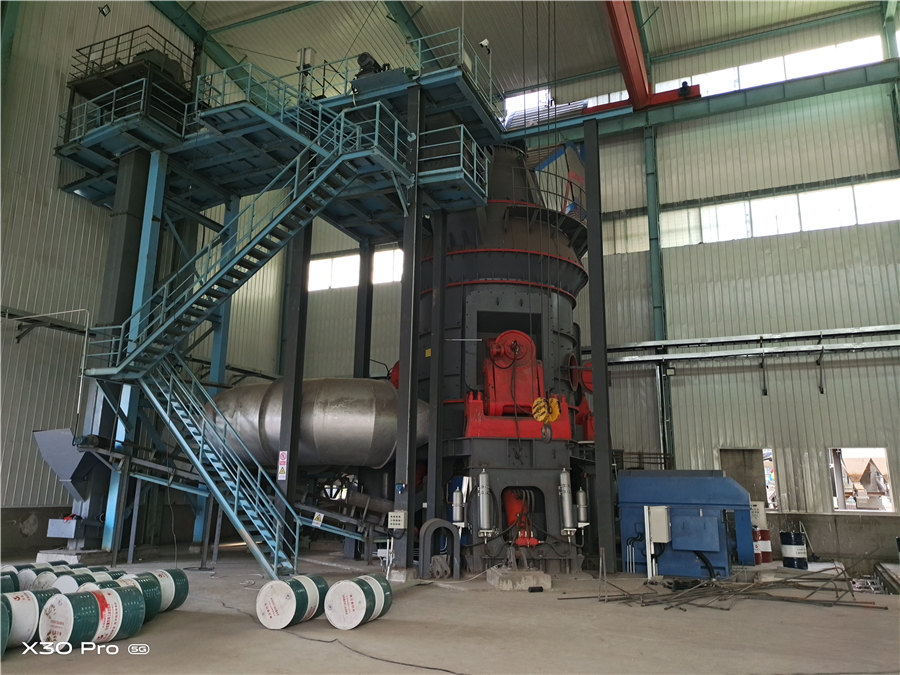
Grinding in Ball Mills: Modeling and Process Control
2012年6月1日 As the cylinder starts to rotate, the grinding balls inside the cylinder crush and grind the feed material, generating mechanical energy that aids in breaking bonds, activating the catalyst, and Wet grinding process, encompassing wet milling methods and technologies, is a cornerstone in various industries It provides efficient, precise, and environmentally friendly solutions for material processing As technology What is Wet Grinding Process Wet Ball Milling with essential process calculations Contents Section A – Process summaries 1 Introduction 10 1 The basics of cement manufacture – 2 History of cement manufacture – 3 Portland cement in today’s world 2 Raw materials management system – 22 Concrete problems 16 1 Raw materials – 2 Raw mix – 3 Reserves – 4 Crushing – 5 The Cement Plant Operations Handbook International Cement 5 天之前 There are two processes known as “wet” and “dry” processes depending upon whether the mixing and grinding of raw materials are done in wet or dry conditions With a little change in the above process, we have the semidry process also where the raw materials are ground dry and then mixed with about 1014 percent of water and further burnt to clickering temperatureManufacturing of Portland Cement – Process and Materials
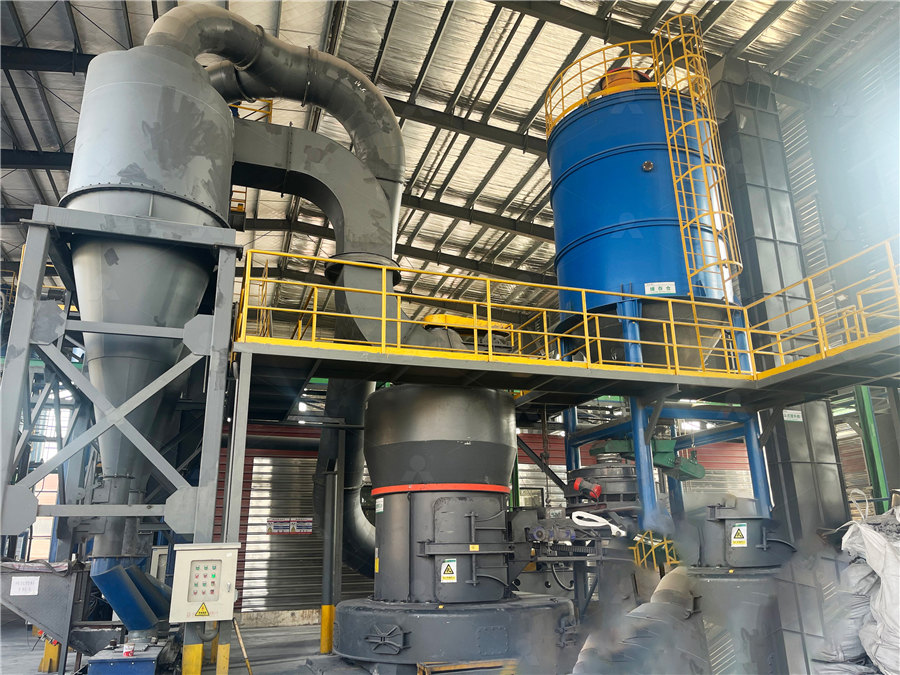
Differences Between Wet and Dry grinding: Why Choose Wet
Ball milling is a popular grinding method The wet ball milling process involves a drum filled with grinding media, The material is processed in its raw, dry state, making it a preferred method in industries like cement production Key Features of Dry Ball Milling Process Direct Approach: The process is straightforward, 2022年2月28日 Additionally, the wet grinding process produces slurry, which needs thickening and filtration steps, increasing the plant capital cost 17 Grinding Aids Many investigations have been carried out on cement grinding using stirred mills [119,120,121]Grinding SpringerLink2021年10月1日 Achieving the high early strength of cementbased materials is a necessary condition for the rapid demolding of prefabricated buildings In this study, kaolin treated by wetgrinding process was Preparation of nanokaolin by wetgrinding process and its 2021年12月1日 Achieving the high early strength of cementbased materials is a necessary condition for the rapid demolding of prefabricated buildings In this study, kaolin treated by wetgrinding process was utilized as an accelerator in Portland cementWetgrinded kaolinPortland cement system was designed, and 1–4% wetgrinded kaolin was addedPreparation of nanokaolin by wetgrinding process and its
.jpg)
116 Portland Cement Manufacturing US EPA
1971年8月17日 In the wet process and long dry process, all of the pyroprocessing activity occurs in the rotary kiln Depending on the process type, kilns have lengthtodiameter ratios in the range of 15:1 to 40:1 While some wet process kilns may be as long as 210 m (700 ft), many wet process kilns and all dry process kilns are shorter Wet process and long Nowadays, the dry process is the most popular cement making process which is widely adopted by cement plants all over the world for its great advantages in energy saving and environmental protection Cement Making Process The cement making dry process includes six phases: Raw material extraction/ Quarry; Proportioning, Blending, and GrindingHow Is Cement Produced in Cement Plants Cement Making Process2017年8月15日 The materials reach temperatures of 2500°F to well above 3000°F in the kiln Rotary kilns are divided into two groups, dryprocess and wetprocess, depending on how the raw materials are prepared In wetprocess kilns, raw materials are fed into the kiln as a slurry with a moisture content of 30 to 40 percentThe Cement Manufacturing Process2023年8月15日 Blending Raw Materials (Crushing and Grinding) The blending of raw materials can be accomplished through two primary methods: the dry process and the wet process Dry process The dry process involves the Cement: History, Types, Manufacturing Process
.jpg)
Cement Manufacturing Process INFINITY FOR
The commnation method belongs to the most efficient grinding processes applied in the cement manufacturing Separation: the ground and dried material is lifted up with the drying gases In the separator, the too coarse particles Wet Raw Material Proportioning and Grinding Techniques for proportioning and grinding raw materials Equipment used in this stage Word count: 1000; Section 2: Types of Cement Kilns Wet Process Kilns Description and operation Advantages and disadvantages Word count: 1000; Dry Process Kilns Description and prehensive Guide to Cement Kilns: Processes, Types, 2020年9月26日 Grinding; Storage; Mixing: The mixing of raw materials can be done either with dry process or wet process In dry process the calcareous and argillaceous materials are grinded to the required size and then they are mixed in required proportions and stored in silos, ready to be fed into rotary kilnCement Manufacturing Process Chemical Engineering World2018年8月28日 Cement Manufacturing Process Cement is the basic ingredient of construction and the most widely used construction material It is a very critical ingredient, because only cement has the ability of enhancing viscosity of concrete which in returns provides the better locking of sand and gravels together in a concrete mixCement Manufacturing Process The Engineering Community

Everything you need to know about clinker/cement Grinding
Everything you need to know about clinker/cement Grinding if You read and understand this article , you will be ready to be a cement grinding area manager FEED AND FEED SYSTEM Mill type: cement mill, dry process raw mill, wet process raw mill Diaphragm location: Raw mill: transfer diaphragm at the drying chamber outlet, intermediate, 2018年10月30日 There are two main cement production processes the wet process, where raw materials are ground into a slurry with water before burning, and the dry process, where they are ground dry In the wet process, the slurry is sprayed into a rotating kiln to lose moisture and form flakes that are converted into clinker Read lesswet process of cement PPT SlideShare2018年9月1日 Request PDF Utilization of lithium slag by wetgrinding process to improve the early strength of sulphoaluminate cement paste Lithium slag is a byproduct of lithium carbonate industry; in the Utilization of lithium slag by wetgrinding process to improve the 2024年6月19日 The concrete slurry waste (CSW) produced by concrete mixing plants is a type of hazardous waste that is difficult to handle To better recycle the CSW separated from the aggregates, this study uses a variety of wetgrinding processes to refine the solid in it, replaces some of the cement with the solid particles in wet grinding concrete slurry waste (WCSW), and Effect of Wet Grinding Concrete Slurry Waste on Hydration and
.jpg)
Dry Grinding VS Wet Grinding 911Metallurgist
2017年5月25日 The choice between wet and dry milling is, in general, unimportant in smallscale milling but is a major technical problem when largescale milling in the metallurgical industries is involved On purely mechanical Definition of the Dry Process The dry process is a method of cement production that involves grinding and mixing raw materials in their dry state This contrasts with the wet process, where materials are mixed with water In the dry process, moisture content is minimized from the outset, leading to significant savings in energy and fuel consumption during the subsequent stages of Dry Process of Cement Manufacturing: StepbyStep Guide Key 2023年4月13日 Grinding down concrete is a fairly straightforward process Most of the time, grinding down concrete slabs can be done with a handheld angle grinder and an attached diamond cup wheel Because concrete is porous, it Concrete Grinding: Everything You Need to Know2023年10月19日 Therefore, efficient grinding techniques and technologies are employed to minimize energy use and reduce production costs, contributing to the sustainability of the cement industry Types of Clinker Grinding Techniques used in cement manufacturing process Clinker grinders are an important part of the cement manufacturing processClinker Grinding Techniques in Cement Manufacturing JM
.jpg)
Utilization of lithium slag by wetgrinding process to improve the
2018年12月20日 With the dosage less than 10%, wetgrinded lithium slag can notably promote the early strength of the sulphoaluminate cement paste, and the main reason for the promotion is not only because of the filling effect of fine particles and nucleation seed induction of nano particles formed in wetgrinding process, but also due to the fact that the dissolved lithium can Clinker is the intermediate product used in the manufacturing of cement There are two primary processes used to manufacture clinker: the dry process and the wet process Our plants use the dry process, which is more energy efficient In the wet process, the raw materials are mixed with water to form slurry, which is fed into a kilnProduction Process CEMEX Philippines2017年12月5日 Wet Process of Manufacturing of Cement They are drawn from the silos in prefixed proportions into the wet grinding mills where, in the presence of a lot of water, these get ground to a fine, thin paste This is slurry which is stored in a third SILOCement Manufacturing Process: What is Cement made of2021年6月7日 Studies show that the potential hydration activity of slag is stimulated after wet grinding, and not only 80% of the proportion of cement could be substituted by slag [21], but also the selfhydration reaction occurs [22] it is also found that after the wetgrinding process, the refined CSW could accelerate the hydration of cement, the Effect of wetgrinding steel slag on the properties of Portland cement
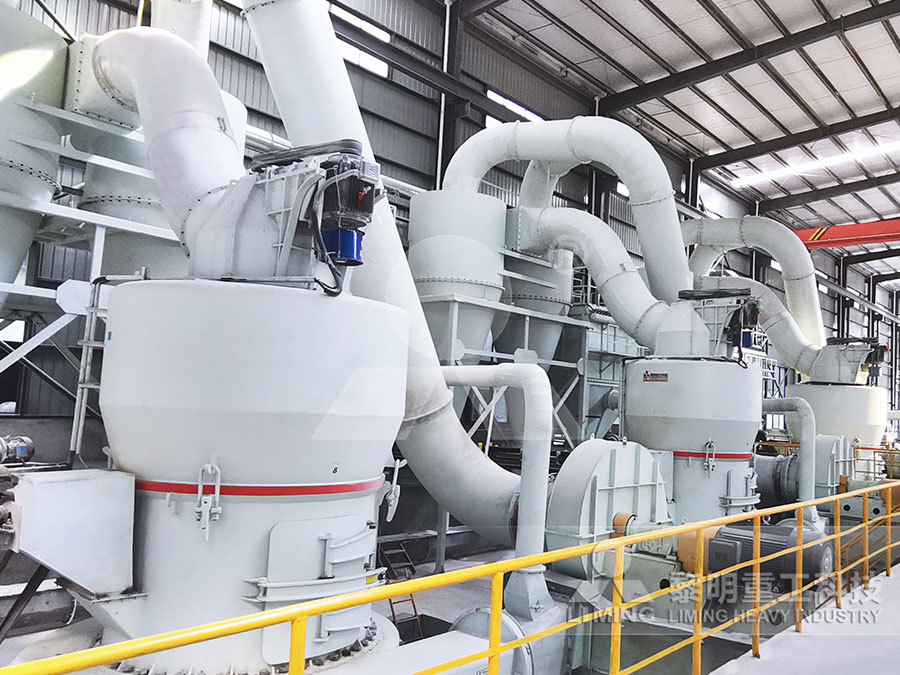
Utilization of lithium slag by wetgrinding process to improve the
In this study, one new way to utilize lithium slag in sulphoaluminate cement system was attempted Lithium slag was processed with wet grinding, in order t EN of 304 μm, which is extremely difficult to be prepared in drygrinding system, can be easily obtained with wetgrinding process; the ions dissolution of lithium, aluminum, Definition of the Dry Process The dry process is a method of cement production that involves grinding and mixing raw materials in their dry state This contrasts with the wet process, where materials are mixed with water In the dry process, moisture content is minimized from the outset, leading to significant savings in energy and fuel consumption during the subsequent stages of Dry Process of Cement Manufacturing: StepbyStep Guide