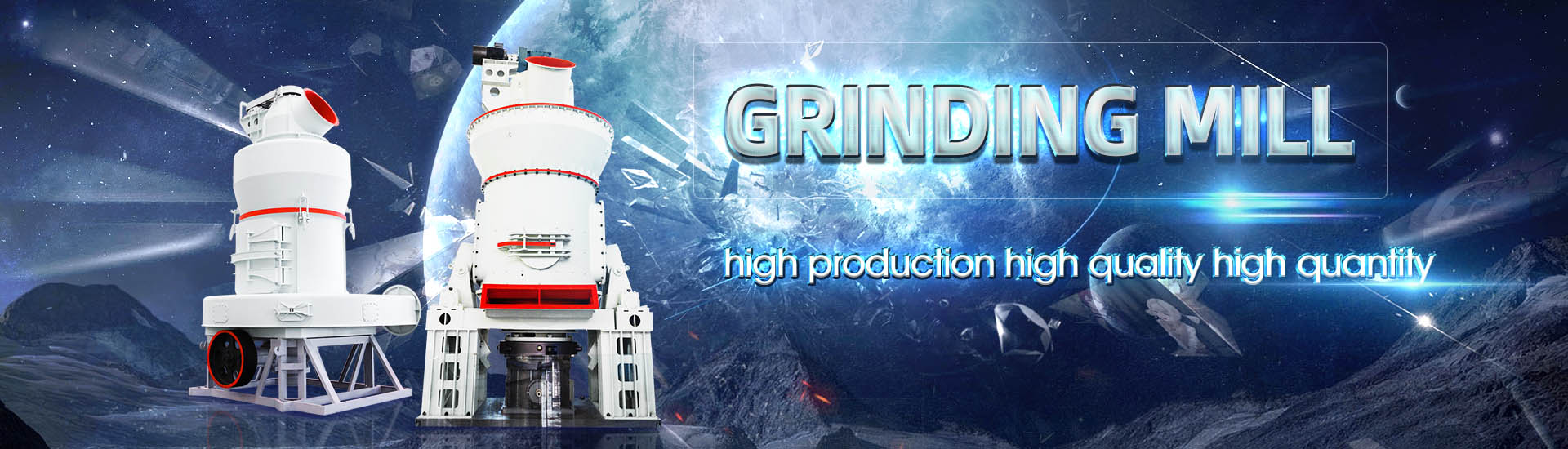
Reasons why European version of grinding mill has small feeding capacity
.jpg)
The production principles and advantages of the european version
The European Version Mill is designed for high efficiency, with a high pressure grinding technology that increases the throughput rate The optimized design of the roller and disc ensures maximum utilization of energy, resulting in reduced power consumption per unit of product2022年3月9日 The feed miller can basically produce every desired particle size From a course mash feed with minimal fines to a very fine grind, all from the same high capacity grinding line Importance and optimization of particle size in animal feed 2020年3月1日 Roller milling tends to produce a more uniform particle size distribution (PSD) and consumes less energy, whilst hammer mills have a greater grinding capacity and a higher Size reduction in feed technology and methods for determining However, in newlyfilled ponds or those with new bottoms and in tanks, pools, and raceways, a complete feed in pellet form has resulted in better feed conversion than meal feeds Once a Chapter 18 Feed Milling Processes
7TOCS.jpg)
Grinding considerations when pelleting livestock feeds
grinding will result in a betterquality pellet or extruded feed, which increases the capacity of the pellet mill or extruder and reduces wear of the pellet mill or extruder working parts such as 2018年1月22日 Grinding, or particlesize reduction, is a major function of pellet manufacturing for several reasons, all of them improving the ease of handling ingredients and their storability: The importance of grinding La Meccanica B2blogThe innovative design of the grinding components allows for finer particle size reduction and more uniform grinding results, which is critical in many industrial processes One of the significant Indepth understanding of the european version grinding mill: The Feed mills should have at least one finished feed bin for each feed type and/or medication option The lack of sufficient finished feed storage will result in an inefficient manufacturing and Feed processing to maximize feed efficiency SpringerLink
.jpg)
(PDF) Optimizing Feed Milling Processes for Enhanced Efficiency
2020年8月4日 Feed milling plays a pivotal role in the production of nutritionally balanced and costeffective animal feed, influencing the performance and wellbeing of livestock and poultry 2023年8月3日 In this study, grinding contribution and quantitative separation of impact and grinding mechanism in cylindrical mill were creatively researched, and the grinding technical Grinding Contribution and Quantitative Separation of Impact and 2021年1月29日 For the past three decades the vertical roller mill has emerged to be the preferred choice for grinding raw materials[12] It has advantages like low power consumption, process simplifications andIncrease productivity of vertical roller mill using seven Grinding Mills: Ball Mill Rod Mill Design PartsCommon types of grinding mills include Ball Mills and Rod Mills This includes all rotating mills with heavy grinding media loads This article focuses on ball and rod mills excluding SAG and AG Grinding Mills 911Metallurgist
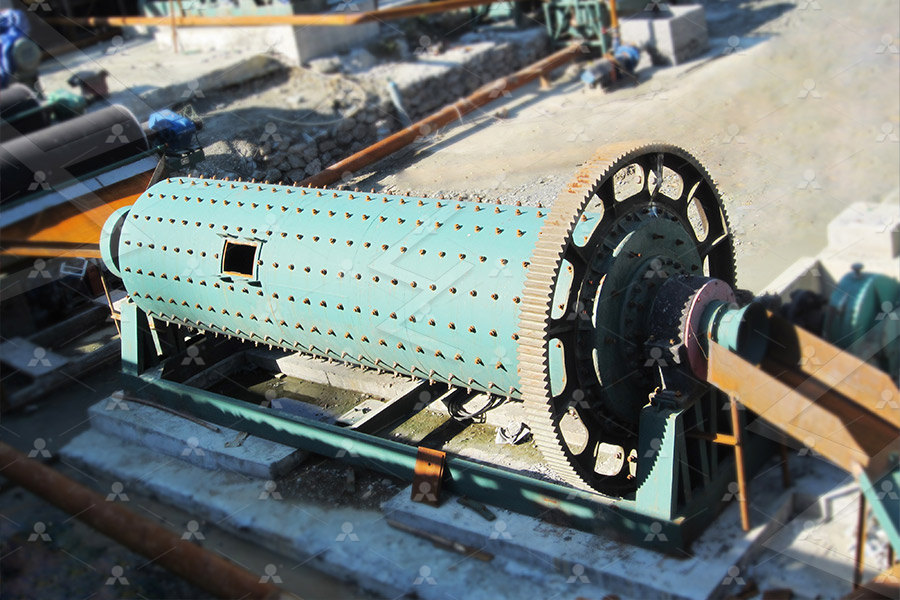
Understanding the SAG Mill in Copper Ore Mining
The Autogenous Mill, also known as AG Mill, is a type of grinding mill used in the mining industry This machine uses ore and rock itself as grinding media to perform its job Unlike other types of mills that use steel balls or rods for 2023年4月23日 study showed that grinding media shape has a small impact on power draw when the mill filling level is low Another very essential phenomenon during the grinding process that is affected by the (PDF) Grinding Media in Ball MillsA Review ResearchGate2017年9月11日 In this study, an extensive sampling study was carried out at vertical roller mill of ESCH Cement Plant in Luxemburg Samples were collected from mill inside and around the circuit to evaluate the (PDF) Performance Evaluation of Vertical Roller Mill in Cement Grinding 2016年11月7日 For the preparation of small quantities of powder many types of mill are available but, even so, the ball mill is frequently used For the grinding of the largest quantities of material however, the ball, tube or rod mill is used almost exclusively, since these are the only types of mill which possess throughput capacity of the required magnitudeGrinding Mills Common Types 911Metallurgist
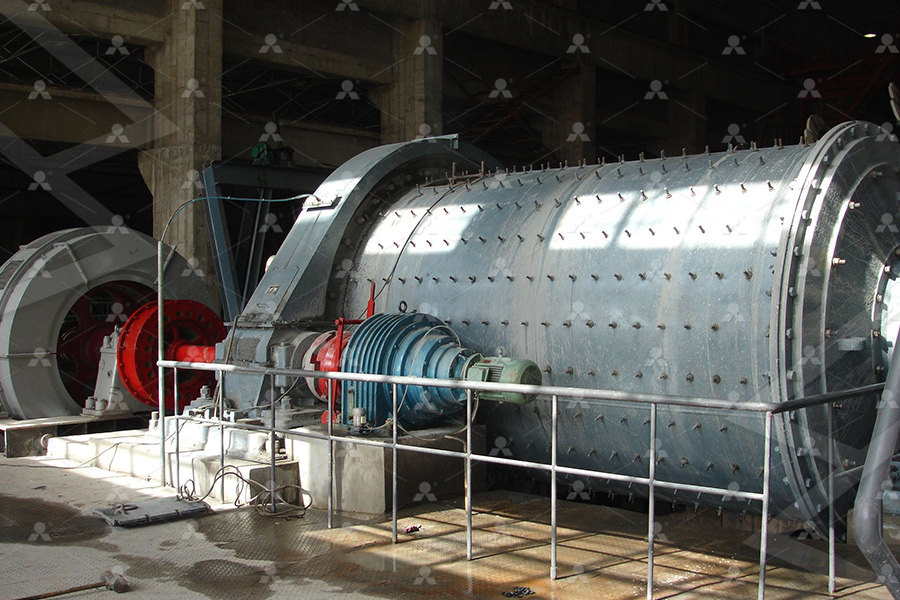
Europemill Industrial Stone Grinding Mill Engsko
Both the Standard and the Industrial grinding mills simply do the job through the optimum milling process using the proven and wellknown Engsko millstones The adjustment of stones has an adjustment gear for fine tuningEngsko Europemill is especially designed for installation in milling industries for continuous production of wholemeal flour or to use in Engsko Grinding Mill 2022年2月28日 Using an electromagnetic mill, a comparison between these two grinding environments has shown; while wet grinding requires around 16 kW of energy, the dry condition needs 3 kW for the same condition It also has been shown that for an equal level of energy, the size reduction ratio in the wet method is higher than dry grinding Grinding SpringerLinkJune 2022; ARCHIVE Proceedings of the Institution of Mechanical Engineers Part C Journal of Mechanical Engineering Science 19891996 (vols 203210) 236(2):1107(PDF) A comprehensive review on the grinding process: 2023年8月3日 Optimizing and adjusting the particle size composition of grinding products is of great significance for improving economic benefits and resource recovery and utilization In this study, grinding contribution and quantitative separation of impact and grinding mechanism in cylindrical mill were creatively researched, and the grinding technical efficiency of impact and Grinding Contribution and Quantitative Separation of Impact and
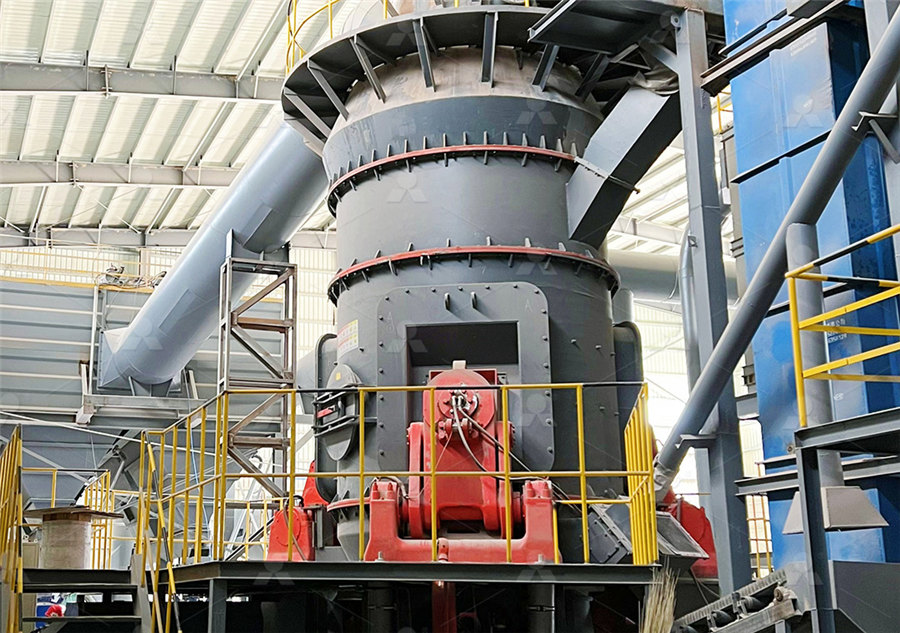
Analysis and Optimization of Grinding Performance of
2022年1月23日 Roy, GR Increasing cement grinding capacity with vertical roller mill technology In Proceedings of the IEEE Cement Industry T echnical Conference, Jacksonville, FL, USA, 5–9 May 20022013年1月1日 Coverage includes abrasives and superabrasives, wheel design, dressing technology, machine accuracy and productivity, machine design, highspeed grinding technology, cost optimization, ultra Principles of Modern Grinding TechnologyIn the case where an existing mill has a grinding unit of the number of balls close to 6, the only way to increase performance is to increase the diameter of the balls, but this requires replacement of the mill body It has to be mentioned that the number Grinding Mill an overview ScienceDirect Topics2013年1月1日 Shortly after the first applications of closed circuit ball mill grinding it was realised that classification increases mill capacity Therefore, over the years closed ball mill – cyclone THE BENEFITS OF HIGH CLASSIFICATION EFFICIENCY IN CLOSED BALL MILL
.jpg)
(PDF) Prediction of grindingmill power ResearchGate
1992年1月1日 Mill power draw can be predicted with reasonable accuracy for a known mill geometry, speed, and filling contents (Hogg Fuersteneau 1972; Morrell, 1993)Because plants constantly measure the mill 2016年6月6日 Based on experience, millliner designs have moved toward more openshell lifter spacing, increased pulp lifter volumetric capacity, and a grate design to facilitate maximizing both pebblecrushing circuit utilization and SAG mill capacity As a guideline, mill throughput is maximized with shell lifters between ratios of 25:1 and 50:1SAG Mill Grinding Circuit Design 911Metallurgist2017年2月20日 Grinding Mill Specifications Data According to formula 423/√d, where d is equal to internal shell diameter within new liners In this case the thickness used was 60 mm for small mill sizes up to and including 2940 and 80 mm for larger mills Volume of the cylindrical mill proper within new linersGrinding Mill Design Ball Mill Manufacturer 911Metallurgist2017年7月3日 Critical speed has been defined and dealt with by many writers It is the speed at which the centrifugal and centripetal forces, acting on an infinitely small particle traveling on and with the breast of the mill, are equal Then the particle will not leave its position It Variables Affecting Grinding Mill Power 911Metallurgist
.jpg)
Optimizing Grinding and Regrinding Capacity in Mill Design
2019年4月25日 Much work has been devoted to the technical aspects of grinding, the “how” of grinding But, in the writers’ opinion, the economically important subject of optimizing grinding capacity in mill design has not received the attention it deserves, at least not in published literature Optimizing Primary Grinding Capacity2013年3月1日 Request PDF Energy Use of Fine Grinding in Mineral Processing Fine grinding, to P80 sizes as low as 7 μm, is becoming increasingly important as mines treat ores with smaller liberation sizesEnergy Use of Fine Grinding in Mineral Processing2022年1月23日 This work concentrates on the energy consumption and grinding energy efficiency of a laboratory vertical roller mill (VRM) under various operating parameters For design of experiments (DOE), the response surface method Analysis and Optimization of Grinding Performance of 2023年5月15日 Capacity Requirements The grinding mill’s capacity should correspond to our business’s requirements for output We have to take into account the amount of limestone to be processed, the expected output and What is Limestone Grinding Mill SBM Mill Crusher
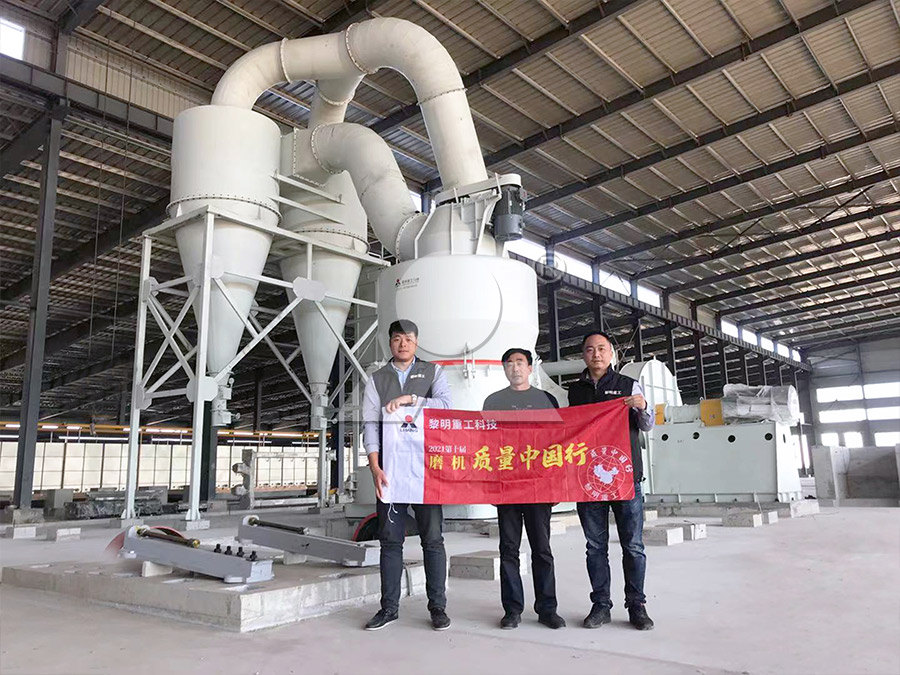
MTW European Type Trapezium MillGrinding mill machine, mineral mill
MTW European Type Trapezium Mill is the upgrade product of Traditional Raymond mill Capacity (t/h) MTW115G 30 160045, fineness can reach 1546 MTW218G 50 160045, fineness can reach to 0038 1855 Working Principle The system of MTW grinding line consists of grinding mill, separator, air blower, jaw crusher, vibrating Condition in one of the grinding chambers of the mill Results of Optimization The graphical analysis presented in Figure 2 represents progress of grinding along the length of the mill after optimizing the grinding process rogress of grinding is clearly visible in Desired p the graphs Figure 2: Analysis of longitudinal samplesOPTIMIZATION OF CEMENT GRINDING OPERATION IN BALL MILLS2023年9月6日 In addition, the feeding of the hammer mill also plays an important role The grinding plant can only be operated efficiently with optimum feeding and the appropriate dosing of the input material Tasks of the hammer mill’s feeding system The feeding system for a hammer mill essentially has four important tasks to fulfil: 1Feeding Systems for Hammer Mills BulkInside2014年6月1日 In this study, the effects of four grinding aids (Triisopropanolamine based (TIPA), Triethanolamine based (TEA), Hydroxylamine based (HA), and Calcium nitrate based (CN) grinding aids) in the Comprehensive understanding of grinding aids ResearchGate
.jpg)
Implementing strategies to improve mill capacity and efficiency,
closing of grinding circuits As mill sizes increased, rake and spiral classifiers became less economically viable due to their large footprint requirements and capital costs The hydrocyclone on the other hand required very little space, provided high capacity with relatively low capital costs For these reasons and the increased demand for 2017年1月17日 Grinding mills are infamous for their extremely low energy efficiency It is generally accepted that the energy required to produce new mineral surfaces is less than 1% of the electricity consumed Breaking down energy consumption in industrial grinding millsMaterial abrasivity The [%] of slag or pouzzolana content on the fresh mill feed for cement grinding The [%] of free silica at mill feed for raw material grinding Moisture content of the mill fresh feed Above or below 2 [%H2O] content The diaphragm type: the name indicated refer to Magotteaux – Slegten denominationEverything you need to know about clinker/cement Grinding2010年3月10日 This project is to design and fabricate the mini ball mill that can grind the solid state of various type of materials into nanopowder The cylindrical jar is used as a mill that would rotate the (PDF) Optimization of mill performance by using online ball and
.jpg)
Grinding Mill Circuits A Survey of Control and Economic Concerns
2009年2月1日 A worldwide survey on grinding mill circuits in the mineral processing industry was conducted The aims of this survey are to determine how milling circuits are currently controlled, and to find 2017年10月26日 The following are factors that have been investigated and applied in conventional ball milling in order to maximize grinding efficiency: a) Mill Geometry and Speed – Bond (1954) observed grinding efficiency to be a Factors Affecting Ball Mill Grinding Efficiency2020年6月3日 The design of such grinding mills is extremely critical, requiring sophisticated software tools, proprietary calculation worksheets, and experienced technical engineers and drafters This blog will review how the mill design How grinding mill design changed over the last 30 yearsIntroduction of MTW European Grinding Mill European version mill, also known as European version Raymond mill, is a grinding equipment with international leading technical level and a number of independent patent technical property rights developed by the company by absorbing European grinding technology and ideasMTW European Grinding Mill Fodamon Machinery
.jpg)
Xometry Resources
The latest Xometry product updates, news, and trends in manufacturing2017年9月1日 Request PDF Fine grinding: How mill type affects particle shape characteristics and mineral liberation In minerals beneficiation applications, the main function of comminution circuits is to Fine grinding: How mill type affects particle shape ResearchGate2012年6月1日 As the cylinder starts to rotate, the grinding balls inside the cylinder crush and grind the feed material, generating mechanical energy that aids in breaking bonds, activating the catalyst, and Grinding in Ball Mills: Modeling and Process ControlEuropean Type Coarse Powder Mill is necessary equipment of medium and fine crushing work, mainly suitable for crushing various soft and hard ores of compressive strength not higher than 320MPa (MPA) High capacity, high crushing ratio, high rate of finished products It has performance advantages of grinding mill and crusherCM European Type Coarse Powder MillGrinding mill machine, mineral mill
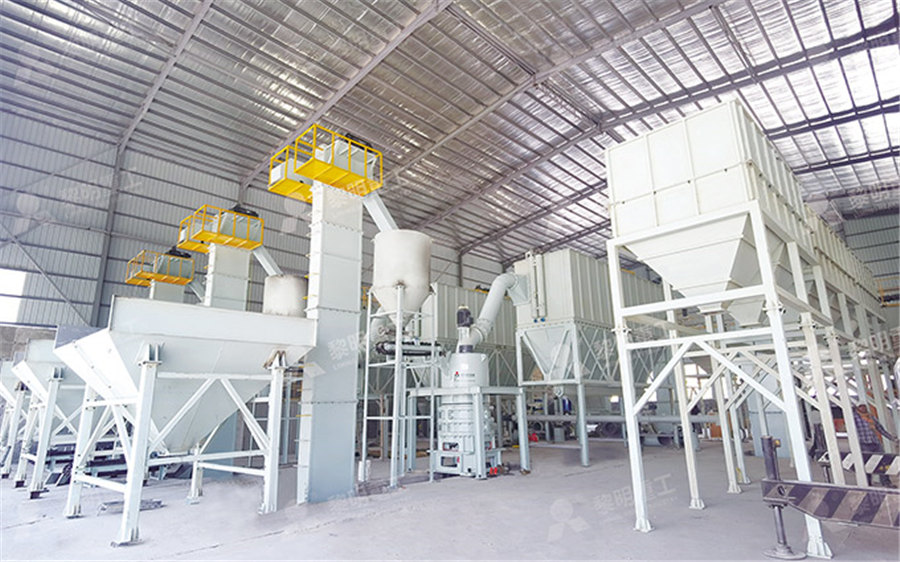
A comparison of wear rates of ball mill grinding media
2016年1月1日 In wet grinding practice, highstress abrasion occurs over a small region when ore particles are trapped between the grinding balls and the mill liner, and the load is sufficient to fracture 2023年7月10日 The present literature review explores the energyefficient ultrafine grinding of particles using stirred mills The review provides an overview of the different techniques for size reduction and (PDF) EnergyEfficient Advanced Ultrafine Grinding of Particles