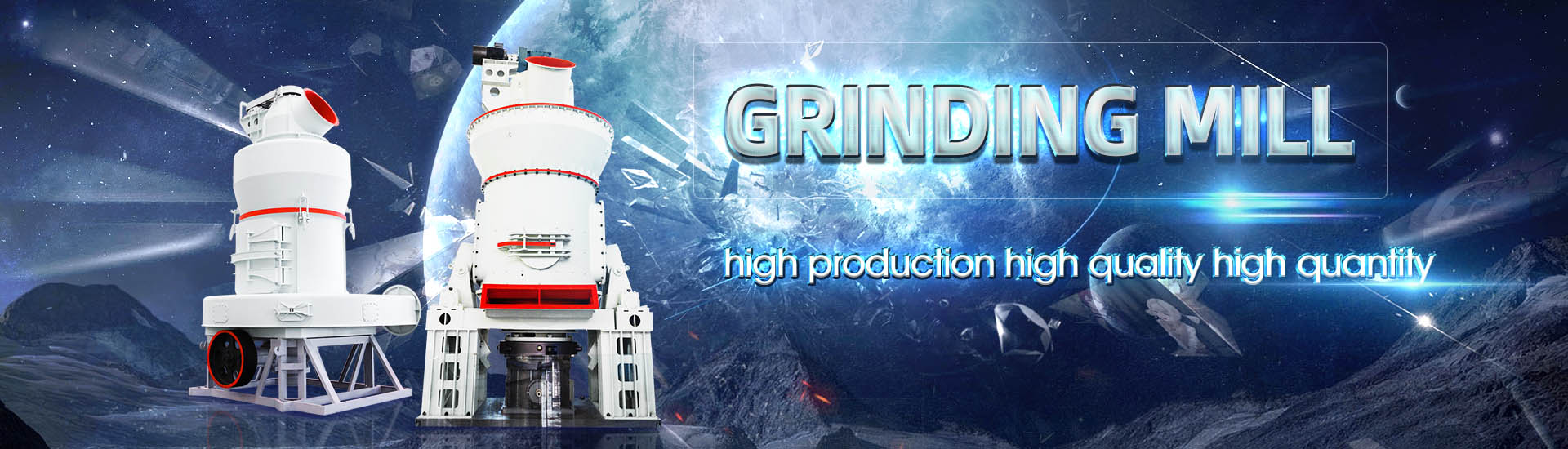
Power plant desulfurization process flow chart HD
.jpg)
Flue Gas Desulfurization: Detailed Process Overview
2024年8月13日 Figure 2 below is a simplified process flow diagram for a spray dryer absorber (SDA) process, a typical semidry FGD system The system is based on absorption of SO 2 Flow chart According to the desulfurization process period, it can be divided into the coal power plant desulfurization, desulfurization furnace and flue gas desulfurizationAccording to the Power plant desulfurizationDesulfurization of organosulfur substrates is highly important due to its relation with the industrial hydrodesulfurization (HDS) process of fossil fuels, which helps to eliminate the sulfur Process flow diagram for the HDS process2022年1月15日 Through the purification technology of flue gas desulfurization, ultralow emissions of SO 2 flue gas in industrial flue gas can be achieved This article involves dry Summary of research progress on industrial flue gas
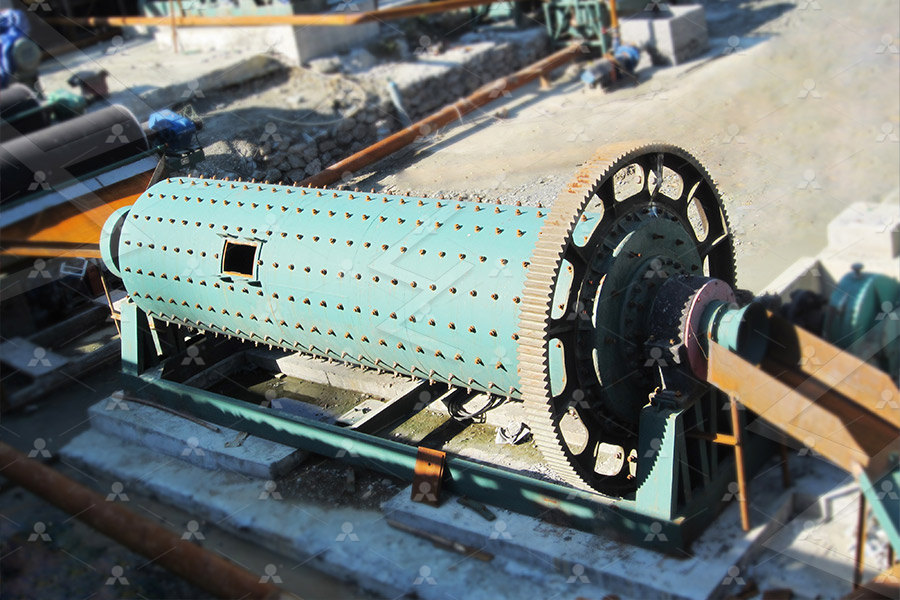
Schematic diagram of the general desulfurization
limestonegypsum wet flue gas desulfurization is the most widely used technology for SO2 removal in coalfired power plants due to its high efficiency, reliability, and costeffectivenessThe flue gas desulfurization (FGD) plant removes sulfur dioxides (SO 2) from flue gas produced by boilers, furnaces, and other sources Mitsubishi Power effectively contributes to the Mitsubishi Power Flue Gas Desulfurization (FGD) PlantsHydrodesulfurization (HDS) or Hydrotreating is a catalytic chemical process widely used to remove sulfur compounds from refined petroleum products such as gasoline or petrol, jet fuel, Hydrodesulfurization IDCOnlineDownload scientific diagram Process flow diagram of the Hydrodesulphurization unit from publication: , ”Model Catalyst Performance and Efficiency during the Hydrotreatment of Heavy Process flow diagram of the Hydrodesulphurization unit
[GYQ0R)ZQ]ESS4NJ.jpg)
Flue gas desulfurization IDCOnline
Flue gas desulfurization is commonly known as FGD and is the technology used for removing sulfur dioxide (SO2) from the exhaust combustion flue gases of power plants that burn coal The performance test results show that the flue gas evaporation and condensation system can process 1044 m³/h wastewater; the concentrated water flow is 096 m³/h on average; and the Design and operation of the lowtemperature flue gas evaporation 2022年7月11日 Desulfurization techniques process and future challenges for commercial of crude oil products: Review(PDF) Desulfurization techniques process and future Wastewater Treatment for Flue Gas Desulfurization (FGD) At Electric Power Plants 3 Introduction Flue gas desulfurization (“FGD”) treatment is incorporated in most coal burning power generation plants to remove sulfur dioxide (“SO 2”) by either wet scrubbing, dry scrubbing, or dry sorbent injection The majority ofWastewater Treatment for Flue Gas Desulfurization (FGD) at
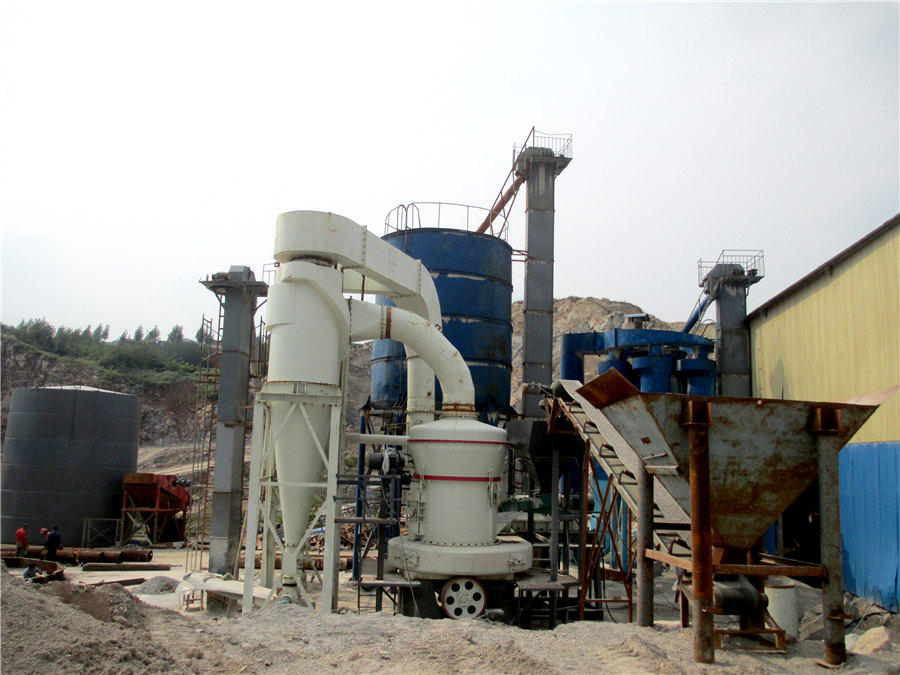
Fluegas desulfurization Wikipedia
Before flue gas desulfurization was installed, the emissions from the Four Corners Generating Station in New Mexico contained a significant amount of sulfur dioxide The G G Allen Steam Station scrubber (North Carolina) Fluegas desulfurization (FGD) is a set of technologies used to remove sulfur dioxide (SO 2) from exhaust flue gases of fossilfuel power plants, and from the 2022年1月3日 Flue gas desulfurization gypsum (FGDG) is an industrial byproduct generated during the flue gas desulfurization process in coalfired power plants Flue gas desulfurization systems have been used to limit the release of sulfur dioxide from coalfired power plants since the late 1960s, but in the past decade the production of FGDG has drastically decreasedWhat is Flue Gas Desulfurization? Wastewater DigestMax Capacity 1,050 MW Max Inlet SO 2 Concentration 80,000 mg/Nm 3 (Coal fired) Max SO 2 Removal Efficiency 99% High Reliability The flue gas desulfurization (FGD) plant removes sulfur dioxides (SO 2) from flue gas produced by boilers, furnaces, and other sourcesMitsubishi Power effectively contributes to the prevention of air pollution through its wet limestone Mitsubishi Power Flue Gas Desulfurization (FGD) Plants2024年4月19日 Limestone gypsum wet flue gas desulfurization process 2 Magnesium oxide desulfurization process The basic principle of magnesium oxide desulfurization is similar to that of limestone (lime) method, that is, the SO2 in the flue gas is absorbed by magnesium oxide slurry, which mainly generates trihydrate and polyhydrate magnesium sulfite, and then generates 4 Flue Gas Desulfurization Process You Should Never Miss
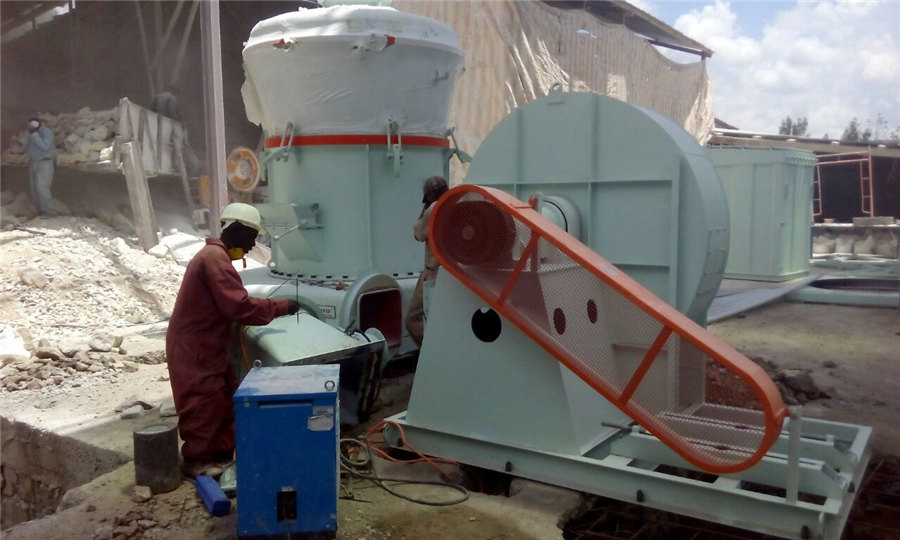
Advanced Process Control for Optimizing Flue Gas Desulfurization
2018年11月1日 Coalfired power plants can significantly improve wet limestone scrubbing with advanced process control One optimization system implemented at a Japanese facility utilized enhanced regulatory 2021年6月1日 Taking a 200 MW coalfired power plant in North China with a limestonegypsum wet desulfurization system transformation project as an example, the effect of energysaving transformation of the Technical Transformation and Energy saving Analysis of Desulfurization 2019年7月13日 With the increasingly prominent global energy and environmental problems, more and more enterprises have been required to desulfurize the exhausted gases Different enterprises have different demands for the desulfurization process, thus the choice of desulfurization process methods has become a focus of attention Since the evaluation of the Method of Desulfurization Process Selection Based on Improved 2015年3月15日 The term Flue Gas Desulphurisation (FGD) system has traditionally referred to wet scrubbers that remove SO 2 emissions from large electric utility boilers The FGD systems emerged in the industrial field of the coalfired power plants and on some industrial processes in the early 1970s in United States (US) and Japan, and expanded rapidly in the 1980s [1] in Status of Flue Gas Desulphurisation (FGD) systems from coalfired power
.jpg)
3 Schematic diagram of an ideal coalfired thermal
Download scientific diagram 3 Schematic diagram of an ideal coalfired thermal power plant Adapted from https:// waterusgsgov/edu/ from publication: Polycyclic Aromatic Hydrocarbons (PAHs Download scientific diagram Power plant efficiency standard—process flow chart from publication: Methodology for implementing power plant efficiency standards for power generation: potential Power plant efficiency standard—process flow chart2024年9月30日 Coalfired power plants account for a large share of the power generation market in China The mainstream method of desulfurization employed in the coalfired power generation sector now is wet flue gas desulfurization This process is known to have a high cost and be energy/materially intensive Due to the complicated desulfurization mechanism, it is Sustainable Operation Strategy for Wet Flue Gas Desulfurization 2003年4月1日 Steam Turbine Power Plants are widely known as one of the primary sources of electricity generation, utilizing coal combustion However, this process leads to the emission of air pollutants Seawater flue gas desulfurization: Its technical implications and
.jpg)
Exhaust Gas Treatment in Thermal Power Plants: A Review
2019年11月22日 An extensive review of exhaust gas treatment in thermal power plants was conducted The nature of emissions and hazards caused by pollutants at electric thermal plants were clearly indicatedDownload scientific diagram Flow diagram of the limestone scrubbing method from publication: Review of Design, Operating, and Financial Considerations in Flue Gas Desulfurization Systems In Flow diagram of the limestone scrubbing method2024年8月28日 The research, development, and application of the evaporation treatment technology for the wet flue gas desulfurization (FGD) wastewater in power plants will help promote the green development and technological innovation of the thermal power industry, realize the recycling of water resources, and reduce environmental pollution (Able et al 2023)Study on the automatic control method for evaporation treatment Desulfurization is a technology used to separate SO 2 from its emitting sources such as exhaust flue gases of fossilfuel power plants, oil refineries, etc The crucial requirement to decrease sulfur loading in fuels to nearly zero content is imposed by mandatory environmental and health protocols as well as the accurate tolerance needed for their use in fuel applicationsDesulfurization an overview ScienceDirect Topics
.jpg)
A visual guide to the process flow of a DM water plant
It is an essential resource in various industries, including pharmaceuticals, power plants, and electronics manufacturing The production of DM water involves several steps to ensure that the final product meets the required purity standards The process flow diagram of a typical DM water plant includes the following stages:Flow chart According to the desulfurization process period, it can be divided into the coal power plant desulfurization, desulfurization furnace and flue gas desulfurizationAccording to the temperature of desulfurization medium, there are three ways for desulfurization mainly including wet, dry and semidryAt present, flue gas Power plant desulfurizationDownload scientific diagram Simplified process flow diagram of the water steam cycle of a power plant (Wellner et al, 2016) from publication: Modeling and simulation of the startup process of Simplified process flow diagram of the water steam cycle of a power 2012年1月1日 The main objective of this study was to find a suitable flue gas desulfurization process for two oxycombustion power plants fired with either NG (467 MW) or pulverized fuel (PF) (596 MW) with Flue gas desulfurization and humidification dehumidification in power
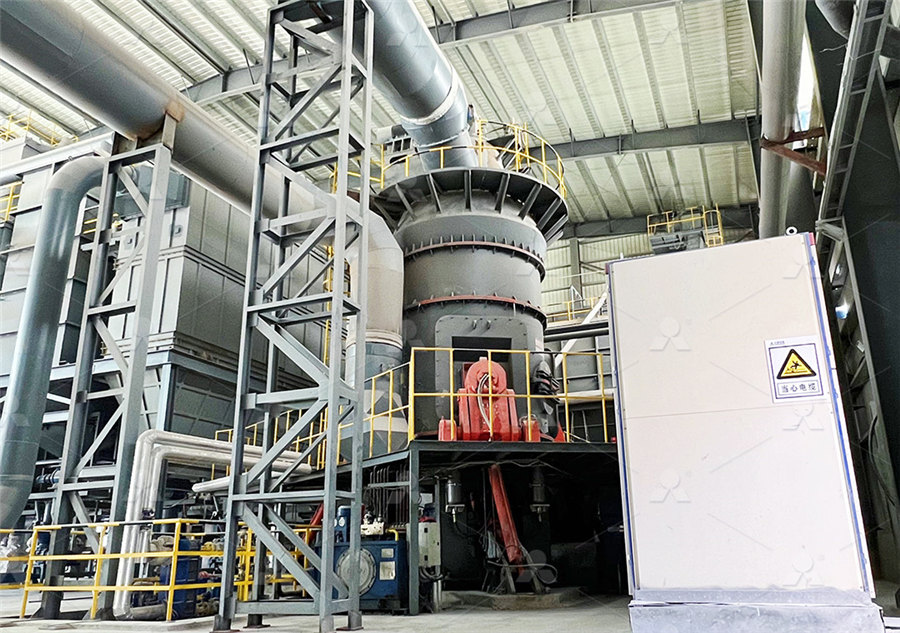
Open Access proceedings Journal of Physics: Conference series
Considering that the desulfurization process for practical applications involves complex engineering equipment and reaction processes, the twophase flow of flue gas and liquid droplets in the 2023年6月21日 It is well known that coalfired power plants play a dominant role in SO2 emissions, and consequently industrial flue gas desulfurization (IFGD) systems are widely used in coalfired power plants(PDF) Dynamic Modeling of Flue Gas Desulfurization Process via 2024年1月10日 Flue gas desulfurization (FGD) is a critical process for reducing sulfur dioxide (SO2) emissions from industrial sources, particularly power plants This research uses calcium silicate absorbent Modeling based on machine learning to investigate flue gas 2019年7月22日 The reduction of wet desulfurization wastewater is one of the important tasks of coalfired power plants, and it is important for achieving “zero emissions” Evaporation and concentration (EC) with waste heat is an effective way to reduce wastewater Here, two typical types of industrial desulfurization wastewater are used to study the change rule of pH and total Evaporation and concentration of desulfurization wastewater with
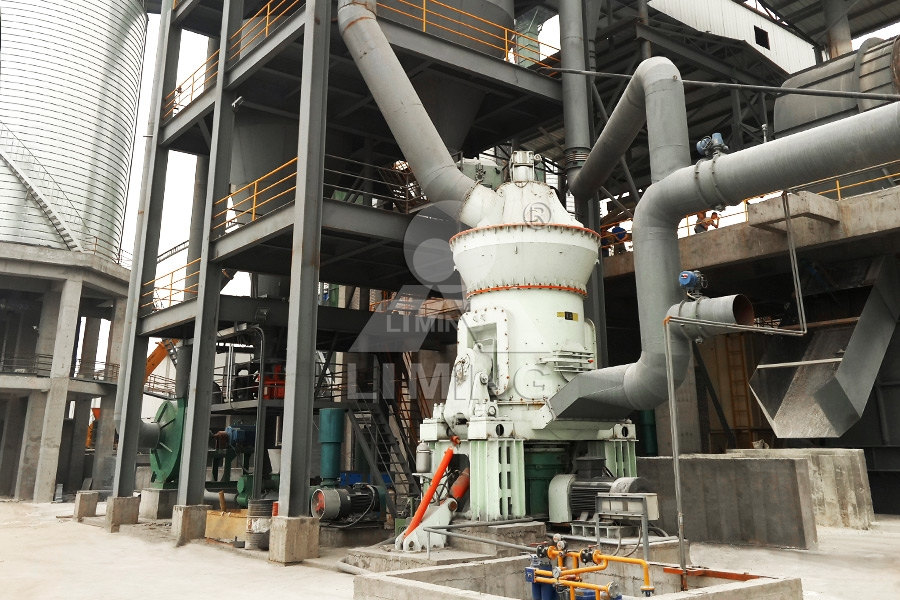
Flue Gas Desulfurization: Technology Overview
2024年8月5日 The final post explores representative FGD process flows and chemistry for each of the three FGD technology types as applied to coalfired power plant applications Wet FGD Systems Wet FGD systems utilize a scrubber, or spray tower, to contact an aqueous slurry of alkaline sorbent (typically calciumbased reagents such as limestone or lime) with the flue gas 2022年11月1日 Table 1 shows the main ion concentrations in desulfurization wastewater from a power plant in Anhui Province, China Table 1 Composition of desulfurization wastewater from a power plant in Anhui Fig 5 shows the typical process flow chart of membrane concentration evaporation crystallization process Download: Download high Zeroliquid discharge technologies for desulfurization 2012年2月24日 Thermal Power Plant Process Flow Diagram: The flow diagram of a steam thermal power plant shows how coal, air, and water are processed to generate electricity A thermal power generating plant works using the Rankine Cycle It needs three main inputs to produce electricity: coal, air, and waterFlow Diagram of a Steam Thermal Power Plant Electrical4U2022年11月1日 Table 1 shows the main ion concentrations in desulfurization wastewater from a power plant in Anhui 2019) The flow chart of the general ZLD system is shown in Fig 1 Previous studies have Treatment of industrial wastewater produced by desulfurization process in a coalfired power plant via FOMD hybrid process Review Zeroliquid discharge technologies for desulfurization
.jpg)
Investigation of courseware design of flue gas desulfurization of
desulfurization Figure 9a Flue gas flow chart Figure 9b Calcium current flow chart For the production of dynamic demonstration of the running system, show of flue gas flow and calcium current as samples are used to reveal all kind of mass transfer processes in this paper Colored coatings shown in Fig 9a indicate a flow direction of the flueThe environmental behavior of FA when the wet desulfurization of flue gases is used does not differ from that of the “pure” FA from the power plants not using FGD process The FGD products in the form of suspension contain 5–15% of solids Desulphurisation an overview ScienceDirect Topics2020年11月16日 Novel Regenerative Desulfurization of power plant flue gas streams November 2020 Conference: The 29th Thai Institute of Chemical Engineering and Applied Chemistry Conference (TIChE 2020)Novel Regenerative Desulfurization of power plant flue gas A power plant in northern China has two 330MW coal fired generating units Circulating fluidized bed semidry desulfurization process flow chart After selective non catalytic reduction of boiler denitration, the flue gas passes through the boiler tailLQLUFXODWLQJ)OXLGL]HG%HG%RLOHUV IOPscience
.jpg)
(PDF) Advanced and Intensified Seawater Flue Gas Desulfurization
2020年11月13日 Seawater flue gas desulfurization (SWFGD) is considered to be a viable solution for coastal and naval applications; however, this process has several drawbacks, including its corrosive absorbent Download scientific diagram Process flow diagram of the power plant from publication: Energy and Exergy Investigation of a Thermal Power Plant Boiler This investigative research work utilizes Process flow diagram of the power plant ResearchGate2022年2月24日 Lee S, Kim Y, Hong S (2018) Treatment of industrial wastewater produced by desulfurization process in a coalfired power plant via FOMD hybrid process Chemosphere 210:44–51 Li XD, Zhou CY, Li JW, Lu SY, Yan JH (2019) Distribution and emission characteristics of filterable and condensable particulate matter before and after a lowlow temperature Experimental study on the treatment of desulfurization desulfurization (FGD) system of coalfired power plants, which accounts for nearly 602% of the total installed capacity [1], has become an indispensable choice Limestonegypsum wet scrubber technology is commonly applied in domestic coalfired power plants During the operation of desulfurization process, it isTHERMODYNAMIC AND ECONOMIC ANALYSES OF DESULFURIZATION
.jpg)
A model for performance optimization of wet flue gas desulfurization
2008年11月1日 It is well known that sulfur dioxide is not only harmful to health, but also contributes to acidification of soil and water The emission of SO 2 from coalfired boilers is regulated strictly in many countries There are many methods available for controlling the emission of SO 2 of coalfired boilers Because of its high efficiency and reliability,