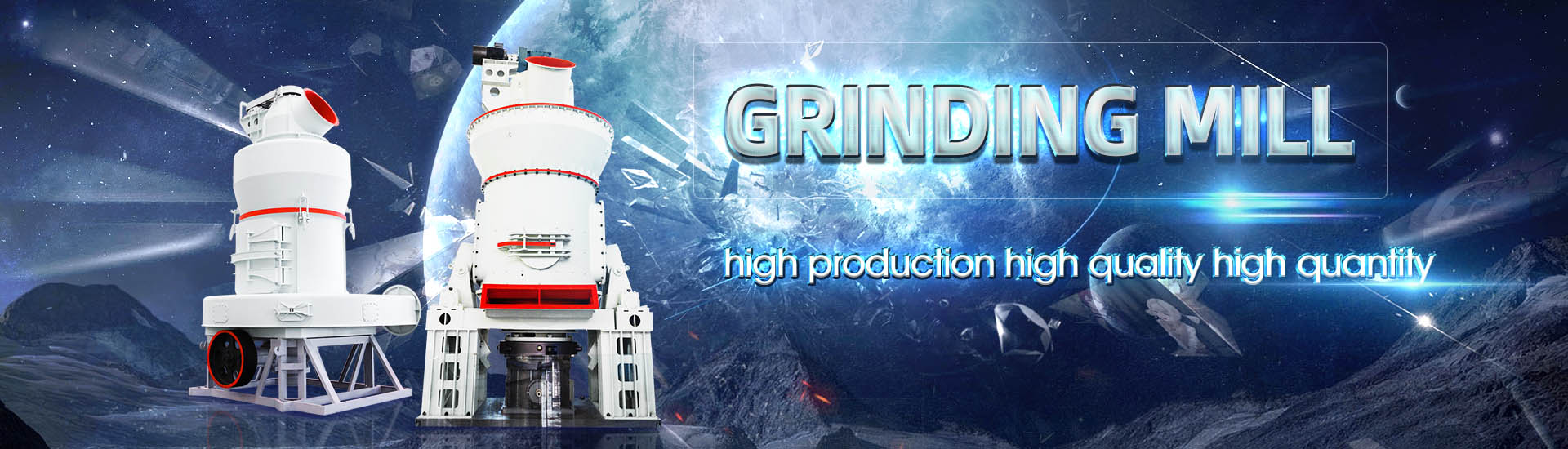
Production process of pulverized coal
.jpg)
Pulverised Coal an overview ScienceDirect Topics
Pulverized coal (PC) combustion is presently the system of choice for coalfired powergenerating plants In PC combustion, the coal is dried and is ground to a specified fineness, with a Combustion of coal in pulverised form has been developed over several decades, with continuous improvements in design and performance It is most commonly used in either large scale utility Fundamentals of pulverised coal combustion ICSCPulverized coal combustion (PCC) is the most widely used technology for coal power generation In this process, coal is milled, pulverized, and injected in the boiler with air to allow Pulverised Coal Combustion an overview ScienceDirect Topics2019年2月1日 Coal is the most abundant energy source, and around 40% of the world's electricity is produced by coal combustion The emission generated through it put a constraint (PDF) A complete review based on various aspects of pulverized
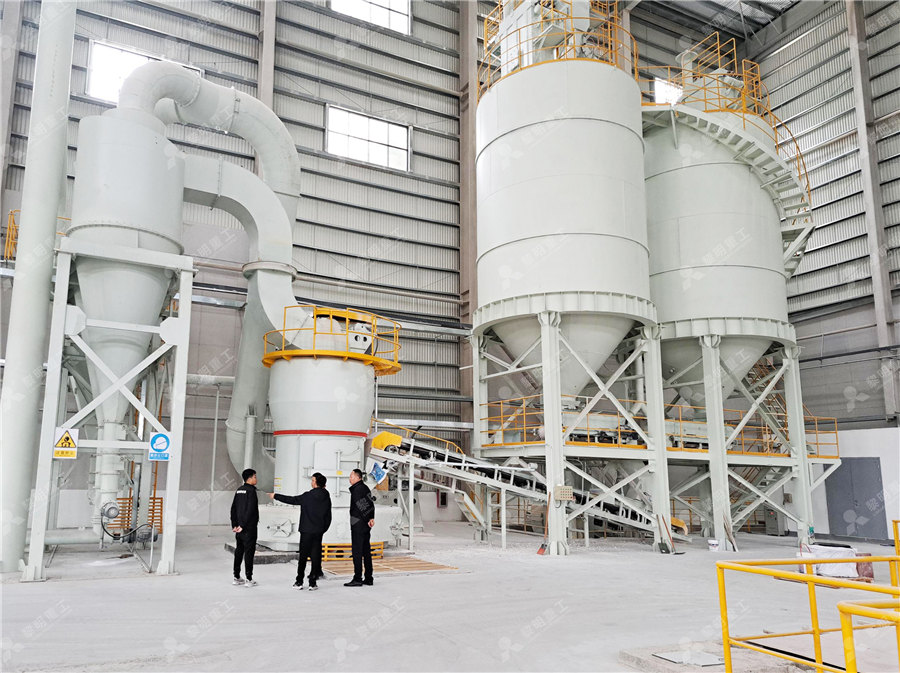
A complete review based on various aspects of
2019年2月14日 The aim of present paper is to review various aspects of pulverized coal combustion such as oxyfuel combustion, cocombustion of coal and biomass, emissions from pulverized coal furnaces, ash formation and 2023年8月1日 K2CO3catalyzed steam gasification of ashfree coal char in a pressurized and vertically blown reactor Influence of pressure on gasification rate and gas composition A Twostage gasification process simulation and optimization of According to the peak shape of the DTG and DSC curves, the combustion process of pulverized coal can be divided into two stages: (1) The volatile escaping and homogeneous combustion Combustion Characteristics of Coal for Pulverized Coal Injection 2021年11月26日 Characteristics of pulverized coals have significant influence on the spontaneous combustion and explosion processes This paper presents an experimental and Physicochemical characteristics of pulverized coals and their
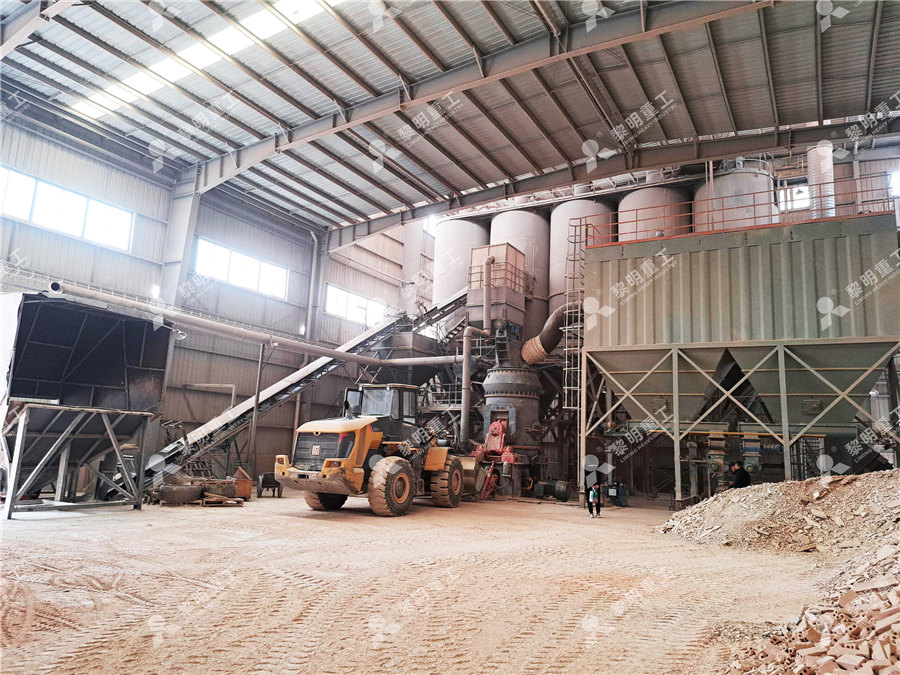
Pulverised Coal Combustion with higher efficiency
Producing electricity in coal power plants can take place in a number of ways with varying degrees of efficiency In conventional coalfired plants coal is first pulverised into a fine powder 2024年1月2日 This study proposed a twostage gasification (TSG) process of pulverized coal to allow for hydrogenrich (HR) production The balance flow of this process is constructed using Aspen Plus software Gasification pressure (GP), steamcoal ratio (SCR), and oxygencoal ratio (OCR) influences on the process are studied, and the operating conditions are optimized to Twostage gasification process simulation and optimization of 2015年10月19日 The paper presents experimental and numerical investigation of pulverized coal combustion process analysis and optimization The research was conducted on the frontfired pulverized coal boiler with dedicated low A Combustion Process Optimization and Numerical A pulverized coal boiler system is an example of an entrainedbed combustion system in which pulverized coal and air are ejected from the center of the burner and Steps in the process are (1) mining of the coal from nearsurface or deep mines, (2) (1978) illustrate schematically the production of ash particles from burning coal Pulverized Coal Boiler an overview ScienceDirect Topics
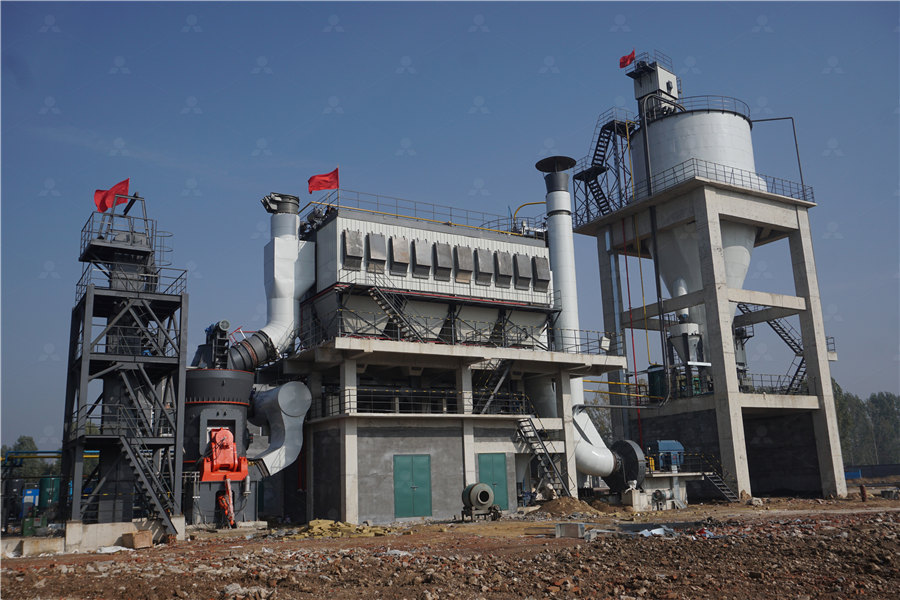
Twostage gasification process simulation and optimization of
DOI: 101016/jijhydene202308033 Corpus ID: ; Twostage gasification process simulation and optimization of pulverized coal for hydrogenrich production using Aspen plus2024年9月11日 This means that the central position of coal in primary energy production and consumption will remain the same for an extended period Oh et al [83] simulated the process of a 1000 MWe pulverized coal power plant and found that the net boiler efficiency decreased as the ammonia ratio increasedProgress in numerical simulations and fundamental characteristics 2019年2月14日 Coal is the most abundant energy source, and around 40% of the world's electricity is produced by coal combustion The emission generated through it put a constraint on power production by coal combustion There is a need to reduce the emissions generated through it to utilize the enormous energy of coal for power productionA complete review based on various aspects of pulverized coal In the steel production process, there is a special and difficulttohandle type of MDS, called waste oil sludge (WOS) According to the peak shape of the DTG and DSC curves, the combustion process of pulverized coal can be divided into two stages: (1) The volatile escaping and homogeneous combustion stage Combustion Characteristics of Coal for Pulverized Coal
.jpg)
Particle motion simulation and pulverized coal injection
2022年3月16日 The production process of direct reduced iron from titanomagnetite by coal reduction in air in rotary kiln is a key step in the extraction of titanium and iron This process is conducive to alleviating the stocking problem of a large amount of Tibearing blast furnace slag The relationships between particle movement and pulverized coal injection combustion in Nevertheless, from a holistic perspective of the entire steel production process, the substitution of biochar for pulverized coal and coke in steel production can still result in cost reduction (1) Raw material cost: The raw materials for biochar may be organic waste materials, such as wood waste or agricultural residues, with relatively low acquisition costs, ranging from $20 to $50 per tonToward Carbon Emission Reduction in Steel Production by 2024年3月22日 On average, the production cost of biochar is estimated at $200 to $400 per ton, with energy consumption ranging from 1000 to 1500 kWh per ton In contrast, the production processes of pulverized coal and coke are usually more complex, requiring significantenergy and equipment inputs The production cost of pulverized coal and coke can rangeToward Carbon Emission Reduction in Steel Production by Fig 1 Process flowchart of pulverized coal injection facility at Oita No 1 blast furnace 3 Progress and development results˜ Considering the heavy oil injection level during an increased production rate period and the experience of longterm results, the capacity of the Oita No 1 blast furnace was designed for 80 kg/t3A2 Pulverized Coal Injection for Blast Furnaces (PCI)
.jpg)
Physicochemical characteristics of pulverized coals and their
2021年11月26日 Characteristics of pulverized coals have significant influence on the spontaneous combustion and explosion processes This paper presents an experimental and theoretical framework on physicochemical characteristics of coal and their interrelations from spontaneous combustion and explosion perspectives The chemical properties, morphology, 2023年1月1日 In the process, iron nuggets are produced by reducing iron ore fines agglomerated with pulverized noncoking coal (coal consumption is about 500 kg/t) (Chatterjee, 2010) Fig 1511 shows the process flow of granular ironmaking comprising the following steps ( Kikuchi et al, 2010 ) and typical composition of iron nuggets ( Michishita Tanaka, 2010 ):Coal use for iron and steel production in lowcarbon transition 2016年6月22日 The gases produced in the coke process are piped off to a byproduct plant where they can be collected for other uses In nonrecovery The 1960s saw the injection of pulverized coal when melting steel or iron in a blast furnace This provided additional energy to burn off gases and prevent iron oxide How does coke and coal play into steel making?2017年12月1日 Acetylene is one important raw material in chemical industries, which is used for the production of polyvinyl chloride (PVC), 1, 4butanediol, vinyl acetate, etc [1] The partial oxidation (POX) method and calcium carbide (CaC 2) method are currently the two main approaches to produce acetylene [2], [3]The calcium carbide process is energyintensive with Pyrolysis of pulverized coal to acetylene in magnetically rotating
R)8OC`6F[ZIB.jpg)
Clean Coal Technologies visionias/
Coal Gasification: It bypasses the conventional coal burning process altogether by converting coal into a gas With integrated gasification combined cycle (IGCC) systems, steam and hot pressurized air or oxygen combine with coal in a reaction that forces carbon molecules apart The resulting syngas, a mixture of carbon monoxide, hydrogen, CO 22024年11月10日 CoalN was mainly presented as aromatic nitrogen, and most volatileN was released from coal along with aromatic compounds during the devolatilization process at the burner plane In this process, numerous CN and N species were released as a result of the nitrogen heterocyclic ring breaking, which combined with H and O to form NH 3 , HCN, and Nitrogen migration and gasification characteristics of pulverized coal NEW TECHNOLOGIES OF PULVERIZED COAL COMBUSTION PARTIAL REPLACEMENT OF COAL1 A N Alekhnovich2 Translated from Élektricheskie Stantsii, No 10, October 2021, pp2–7DOI: 1034831 EP2021108310001 In case of pulverized coal combustion, reduction in CO 2 emissions in commonly used technologies isNEW TECHNOLOGIES OF PULVERIZED COAL COMBUSTION2023年1月1日 The power production of pulverized coalbased thermal power plants is a waterintensive process Water is a key component right from fuel extraction to power production in thermal power plants Approximately, onethird of the world’s freshwatercooled thermal power facilities are located in waterstressed regions [ 1 ]A Comparative Water Life Cycle Assessment of Pulverized Coal
.jpg)
Combustion Enhancement of Pulverized Coal with
2021年2月28日 In this study, a targeted oxygenenrichment technology was proposed to enhance coal combustion in an ironmaking blast furnace The coal flow and combustion characteristics under targeted oxygenenrichment were Today, the “heavymedia” process using magnetite is standard for coarse coal cleaning Attempts to recover middlings and fine coal have continued through the is chosen to achieve a given degree of separation depending on the Coal Mining and Processing Methods The National 2016年6月23日 During the roasting process of fluxed pellets in a coalfired rotary kiln, the incomplete combustion of pulverized coal injection accelerates deposit formation, which further limits the production Combustion Reaction of Pulverized Coal on the Depositthe process of pulverized coal combustion has been investigated in this paper KEYWORDS biomass, continue being dominant energy production source as coal reserves are abundant worldwideA complete review based on various aspects of pulverized coal combustion
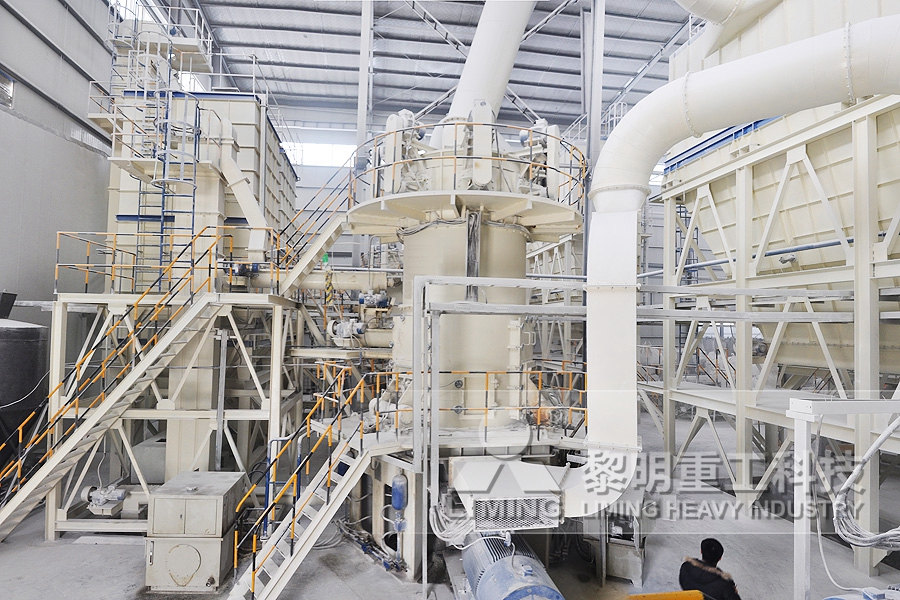
How is pulverized coal processed? SBM Ultrafine Powder
2022年2月24日 Production of clean pulverized coal for boiler combustion heating and power supply Fineness: 200 mesh, D8090, according to the needs of backend combustion Suitable coal types: bituminous coal, anthracite, blue carbon, etc The production of clean pulverized coal is used for boiler combustion heating and power supply to improve the operating efficiency of 2018年10月21日 Fig 1 Pulverized coal combustion and gas composition in raceway The extent of combustion (combustion efficiency), and hence the amount of unburnt material transported out of the raceway, depends on several parameters which include (i) properties of the coal, such as the VM content, particle size and density, and (ii) operating conditions, for example, blast gas Understanding Pulverized Coal Injection in Blast Furnace2023年3月27日 In this paper, the combustion process of a 350 MW opposite pulverized coal combustion boiler is studied using a combined field test and numerical simulation Considering the turbulence–radiation interaction (TRI) effect caused by turbulent particle pulsation during the combustion process, the TRI model is modified by introducing optical factors The interaction Simulation of Pulverized Coal Combustion Process Considering 2024年6月3日 Hydrogen can replace partially pulverized coal in the blast furnace injection as the clean and highcalorific energy, which can reduce energy consumption and carbon emission in molten iron production In this study, a discrete phase model is used to describe the complex flow and thermochemical behavior associated with the coinjection of hydrogen and pulverized coal Numerical Simulation Study of Coinjection of Pulverized Coal
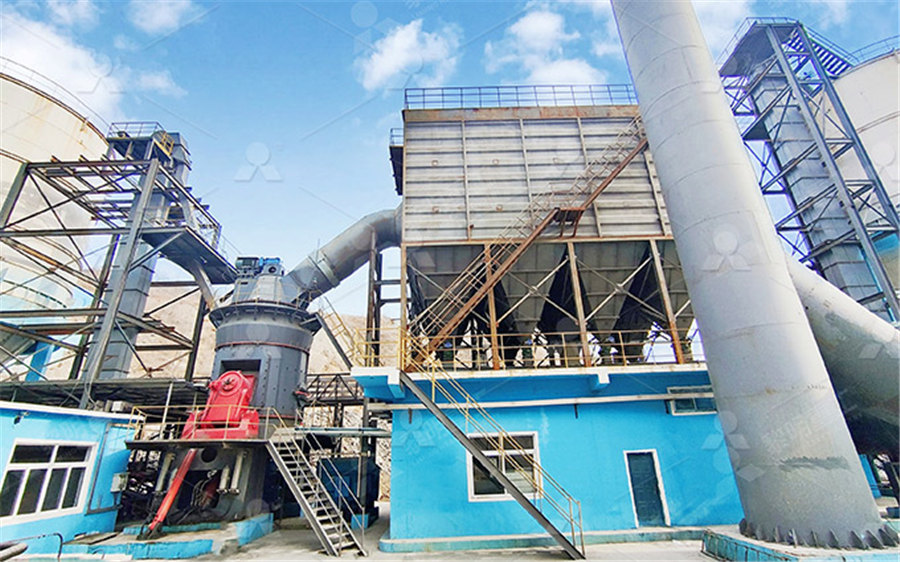
Optimization of pulverized coal injection (PCI) rate in an
2022年5月1日 It uses coke and auxiliary injectants like pulverized coal (PC) to generate the reductants and energy needed However, coke production causes considerable energy consumption and greenhouse emissions and accounts for a big portion of pig iron production costs [1] Also, coking coal resource is gradually depleted on the earthproduction process, metallurgical dust and sludge (MDS) are primarily produced in dry or wet dust collection and metallurgical wastewater treatment systems1 In 2020, the In the pulverized coal injection (PCI) process of a blast furnace (BF), intensifying the combustion of pulverized coal inCombustion Characteristics of Coal for Pulverized Coal Injection 2015年2月1日 Currently, the most energy efficient technology for cement production is a dry rotary kiln process with a multistage preheater and a cement calciner (Benhelal et al, 2013)The latter, cement calciner, is a pyroprocessing unit found in front of the rotary kiln, and inside of which the raw material, mainly composed of limestone, undergoes the calcination processImproving the sustainability of cement production by using 2016年1月22日 A new process is proposed to prepare highquality syngas (H2+CO) for the production of dimethyl ether, methanol and other chemical products at atmospheric pressure, during which the pulverized New Process of HighQuality Syngas Production through
.jpg)
A complete review based on various aspects of
2019年2月14日 Coal is the most abundant energy source, and around 40% of the world's electricity is produced by coal combustion The emission generated through it put a constraint on power production by coal combustion There is a Coalbased power plants with conventional stoke firing suffer from some shortcomings such as the inability to handle load fluctuations due to limited combustion capacity, difficulties in removing large quantities of ash, and interference of the formed ash in the combustion process Pulverized coal combustion systems offer a viable solution to Pulverised Coal an overview ScienceDirect Topicspressurized oxyfuel combustion of pulverized coal Xiaorui Liang, Qinhui Wang, * Zhongyang Luo, Heng Zhang, Kaikun Li, Yi Feng, Abdul Rahim Shaikh and Jianmeng Cen Chemical kinetic modeling was applied to simulate N transformation in the pressurized oxyfuel combustion process of pulverized coal Modeling accuracy was validated by experimental Simulation of nitrogen transformation in pressurized oxyfuel 2023年8月1日 As the major primary energy source in China, coal has been proved to be capable to improve its physical and chemical characteristics by the pretreatment of the selfpreheating burner In this study, the effects of altering operating conditions including preheating temperature (Tp) and primary air equivalence ratio (λp) on preheating characteristics of three typical Experimental Study on Product Characteristics of Typical Pulverized
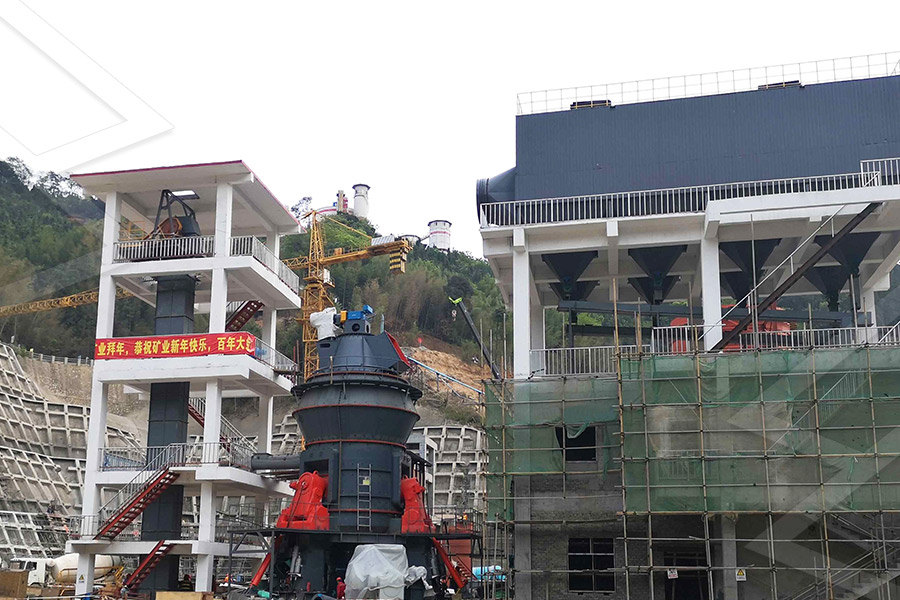
Influences of ammonia cofiring on the NO generation
2023年12月15日 Zhang et al [21] studied the ammoniacoal cofiring process in a pulverized coal combustion device of a single swirl burner by using simulation calculations Experimental study on the impact of adding NH 3 on NO production in coal combustion and the effects of char, coal ash, and additives on NH3 reducing NO under high temperature2019年1月1日 Review of the investigations of pulverized coal combustion processes in large power plants in laboratory for thermal engineering and energy: Part B January 2019 Thermal Science 23(Suppl 5):16111626(PDF) Review of the investigations of pulverized coal combustion 2023年5月1日 Steel production process can usually be categorized to four primary different methods like blast furnace/ basic oxygen furnace (BFBOF), According to the modeling and experimental studies, pulverized coal injection (PCI) can be fully replaced with biochar in both types of mini and large blast furnaces [31], To what extent could biochar replace coal and coke in