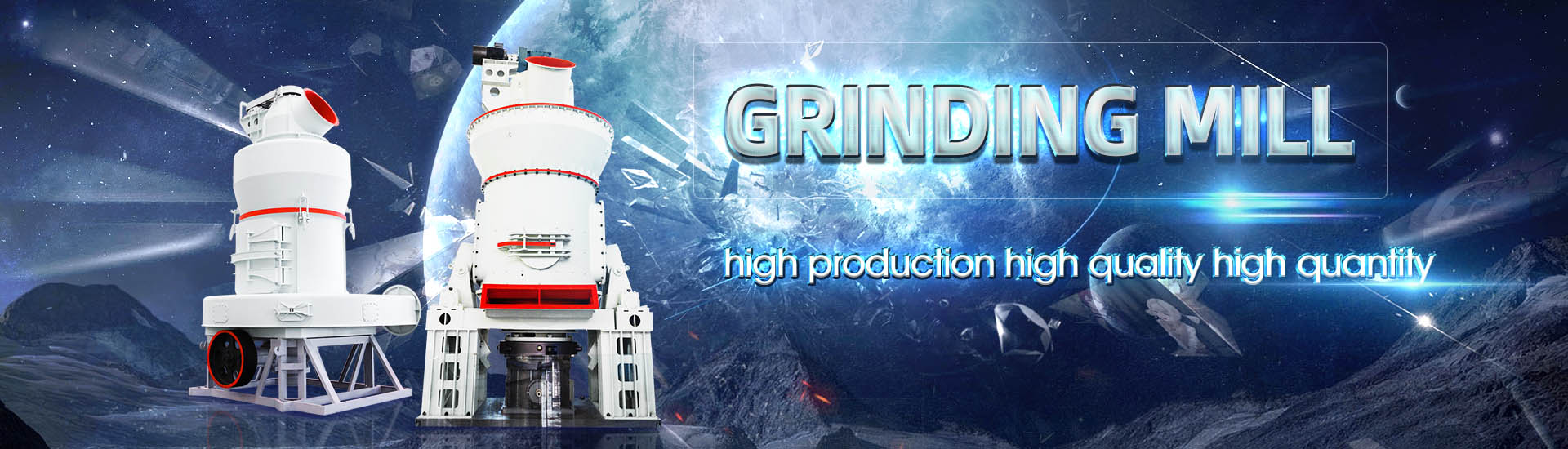
How to save fuel and electricity consumption in cement plant raw meal vertical mill
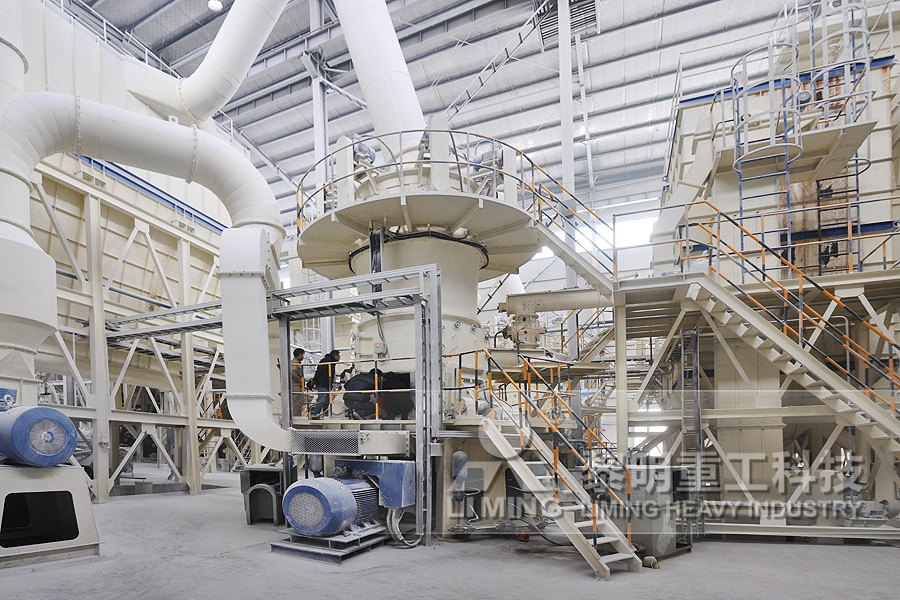
IMPROVING THERMAL AND ELECTRIC ENERGY EFFICIENCY AT
use and now account for over 90 percent of cement consumption worldwide (41 billion tons in 2016) Cement accounts for at least 5 percent of anthropogenic emissions of greenhouse 2011年5月1日 Specific energy consumption in cement production varies from technology to technology The dry process uses more electrical but much less thermal energy than the wet A critical review on energy use and savings in the cement industriesIn this paper energy use at different sections of cement industries, specific energy consumption, types of energy use, details of cement manufacturing processes, various energy savings (PDF) A critical review on energy use and savings in the cement Energy conservation has become necessary in almost all chemical industries mainly for two reasons Firstly there is a sharp rise in the cost of energy which sometimes makes the product Optimizing Electrical Energy Consumption In Cement Process
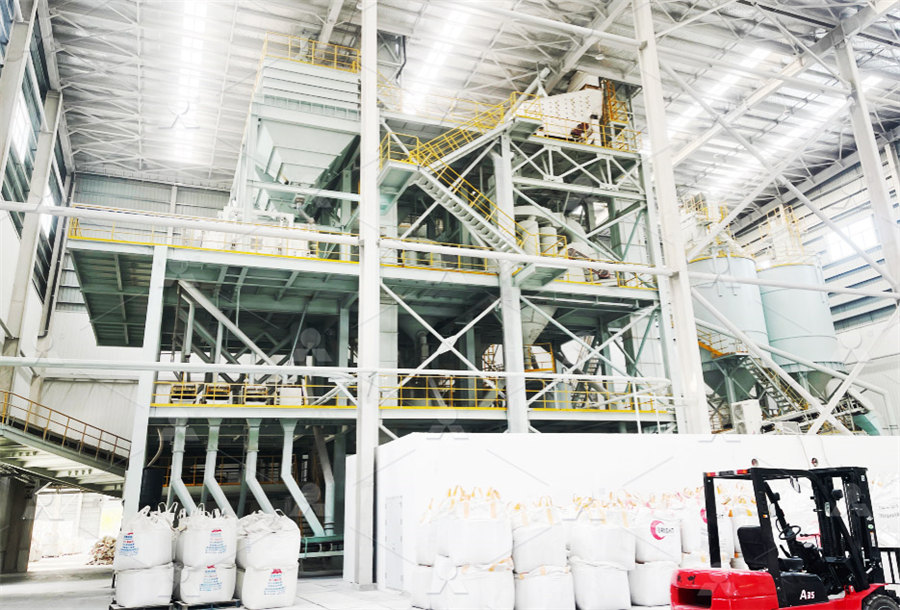
Modeling of energy consumption factors for an industrial cement
2022年5月9日 By initiating a CL for an industrial cement vertical roller mill (VRM), this study conducted a novel strategy to explore relationships between VRM monitored operational The kiln feed blend (also called raw meal or raw mix) is adjusted depending on the chemical composition of the raw materials and the type of cement desiredEnergy Efficiency Improvement and Cost Saving Opportunities for 2013年3月1日 High efficiency classifiers have been shown to bring about a reduction of 28–37 kW h/t in raw materials, save fuel and yield a narrow particle size distribution, increase the An overview of energy savings measures for cement industries2021年7月5日 In cement production, raw meal preparation and energy consumption are extremely important for cost reduction However, few studies have examined the relationship between operational process parameters and Full article: Evaluation of optimization techniques for
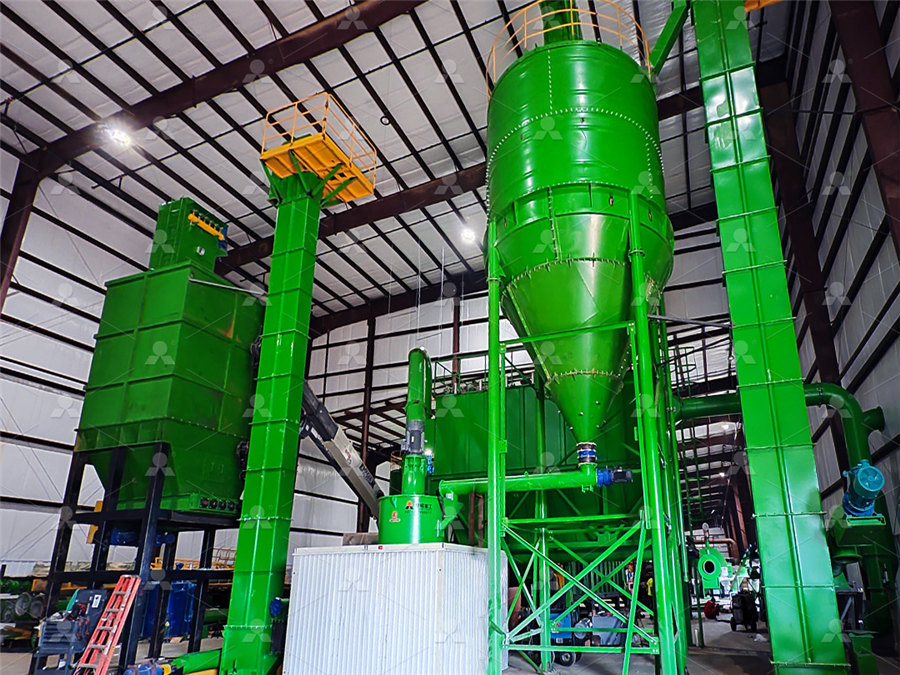
Benchmarking of Energy Consumption and CO2 Emissions in
2024年2月2日 Key energy and emissions parameters, including thermal and electrical energy intensity, recovered energy and CO 2 intensity, are computed per tonne of cement produced CEMENT SECTOR POWERING THE CEMENT INDUSTRY Cement is an energyintensive industry, but currently, electricity accounts for circa 12% within the energy mix, while the rest is various fuels Total electricity consumption in a dry process is split into equal parts between raw material preparation and clinker production (25% each), then 43% forPOWERING THE CEMENT INDUSTRY CEMBUREAUBrick Lining of Cyclones: All preheater components need to be lined from inside with appropriate refractory to save shell/components from heat and to hold heat inside for process use Refractory castable, Bricks, Insulation Bricks are used Clinkerization Cement Plant Optimization2019年3月8日 electricity uses compared to the major electricity and fuel consumption in the five major process steps 1 Clinker can be produced in many different pyroprocessingIMPROVING THERMAL AND ELECTRIC ENERGY
.jpg)
Optimizing Electrical Energy Consumption In Cement Process
separators, grinding rolls, vertical roller mills, 5 stage suspension preheater with precalcinators etc can help in achieving substantial energy savings as outlined in the following sections Typical power consumption per tonne of cement in different unit operations is given below Cement Mill 33% Raw Mill 24% Kiln 23%2016年3月1日 Next, in November 2014, Titan Cement ordered a Gebr Pfeiffer SE type MPS 2800 BK vertical roller mill for Arabian Cement commissioned new alternative fuel processing machinery at its cement plant solar and wind The country is also pushing to restart its nuclear power programme China’s electricity consumption in Coal for cement: Present and future trendsCEMENT SECTOR POWERING THE CEMENT INDUSTRY Cement is an energyintensive industry, but currently, electricity accounts for circa 12% within the energy mix, while the rest is various fuels Total electricity consumption in a dry process is split into equal parts between raw material preparation and clinker production (25% each), then 43% forPOWERING THE CEMENT INDUSTRY CEMBUREAUIn a wet rotary kiln, the raw meal typically contains approximately 36% moisture These kilns were developed as an upgrade of the original long dry kiln to improve the chemical uniformity in the raw meal The water (due to the high moisture content of the raw meal) is first evaporated in the kiln in the low temperature zoneTIPS TO SAVE ENERGY IN CEMENT MANUFACTURING PROCESS

Optimization of Energy Consumption in ElectricPowered Modular Cement
particularly during kiln operations, leading to peak energy consumption that can strain energy resources and increase operational costs Example: A typical cement plant can consume up to 34 GJ of energy per ton of clinker produced This energy is derived primarily from fossil fuels, with electricity accounting for a smaller yet significant Vertical raw mill is one kind of raw mill, generally used to grind bulk, granular, and powder raw materials into required cement raw meal in the cement manufacturing plantVertical raw mill is an ideal grinding mill that crushing, drying, grinding, grading transfer set in one It can be widely used in cement, electric power, metallurgy, chemical industry, nonmetallic ore, and other industriesVertical raw mill Cement PlantAGICO Cement Vertical Mill AGICO Cement Ball Mill Cement Vertical Mill Grinding System Cement vertical mill, also called roller mill, is another raw mill commonly used in cement pared with the cement ball mill, it has a great difference in structure, grinding principle, process layout, automatic control, and energy consumption, which play an important role in the Raw Mill – Raw Mill In Cement Plant AGICO Cement Raw Mill25 kWh/t raw meal (Fujimoto, 1993; Holderbank, 1993; Alsop Post, 1995, Cembureau, 1997b; Gerbec, 1999) Costs for the silo retrofit are estimated to be $37/t raw material (assuming $550K per silo and an average capacity of 150,000 tonnes annual capacity) Raw Meal Process Control (Dry process Vertical Mill) The main difficulty withEnergy Efficiency Improvement Opportunities for the Cement
.jpg)
Energy balance and cogeneration for a cement plant
2002年4月1日 The cement industry is an energy intensive industry consuming about 4 GJ per tonne of cement produced A thermodynamic analysis for cogeneration using the waste heat streams is not easily available2015年8月1日 Cement production, which is highly dependent on the availability of natural resources, will face severe resource constraints in the future This is especially true for the cement industry in China(PDF) Analysis of material flow and consumption in 2020年6月24日 The consumption of the energy in the cement plant is mainly due to raw mill, cooler, preheater and rotary kiln The total energy loss of the plant is generally accounted for about 35–39% of the total energy input This energy loss is due to the loss from the exhaust gas, cooler and the radiation heat transfer from the kiln cellThermal energy consumption and its conservation for a cement 2016年4月25日 In this study, certain measures are implemented in an existing raw mill in a cement factory and the specific energy consumption of the unit is calculated to be 2552 kWh/ton farineDetermination of correlation between specific energy consumption
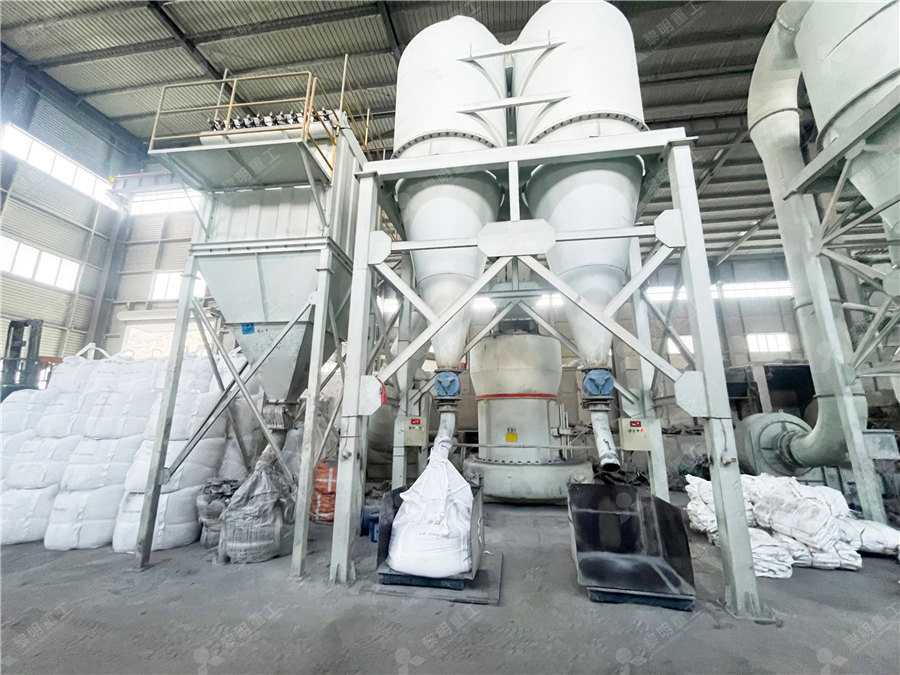
Modeling of energy consumption factors for an industrial cement
2022年5月9日 The raw materials were mixed in a certain proportion and fed into a vertical roller mill (LOESCHE mill) The raw vertical roller mill has four rollers, 3000 KW main drive, 48 m table diameter, 2 2011年8月25日 A Chinabased cement plant used VFDs to significantly reduce its energy consumption in its dryprocess kilns, responsible for production of 14 million tons of cement each year Traditional damper control systems used a fixed amount of energy, so fans at the plant always ran at full capacity even when the facility wasn’t producing product—wasting energy Reduce Energy Consumption: Cement Production Control The vertical roller mill (VRM) is a type of grinding machine for raw material processing and cement grinding in the cement manufacturing processIn recent years, the VRM cement mill has been equipped in more and more cement plants around the world because of its features like high energy efficiency, low pollutant generation, small floor area, etc The VRM cement mill has a Vertical Roller Mill Operation in Cement PlantThe vertical cement mill is largescale cement grinding machine With advantages of energyefficient and stable quality, vertical roller mill is widely applied to many industries, such as cement, power, metallurgy, chemical and nonmetallic mining industry and etc As a typical type of Cement Mill, vertical cement mill set crushing, drying, grinding, grading transportation in one, it grind Vertical Cement Mill, Vertical Roller Mill Buy Cement Mill
.jpg)
Best energy consumption International Cement Review
2015年2月16日 Figure 2 shows a typical breakdown of electrical energy consumption at a cement plant The most obvious area for attention is that of grinding, Plant 3 – Vertical mill (kWh/t cement) CPJ 35 308 298 304 CPJ 45 325 2015年6月30日 The electricity consumption is calculated based on the data from previous research on limestone used in cement industry The raw material processing consumes about 28 % of the total electricity Energy consumption assessment in a cement production plant2012年6月1日 Based on the statistics of the electricity consumption of the raw material mill system of 1005 production lines in China between 2014 and 2019, it is found that the average electricity consumption Reducing energy consumption of a raw mill in cement industry2011年8月9日 2 Alternative fuel options for the cement industry Coal is the primary fuel burned in cement kilns, however, the use alternative fuels in cement kilns is now common and increasing The range of alternative fuels is Alternative Fuels in Cement Manufacturing IntechOpen
.jpg)
The essentials of electrical systems in cement plants EEP
2020年9月14日 The burning of the raw meal at approx 1,450°C is carried out in Lepol or preheater kilns Then ‘convert’ it into clinker and then into power per ton of cement Take example of Raw mill Department List all drives with Table 4 – Power consumption for whole plant Consumption: Unit/Tons Of material kWh: Material 2023年5月3日 Türkiye is the largest cement producer of Europe and the second biggest cement exporter in the world The industry is responsible for more than 8% of global carbon dioxide (CO2) emissions and around 15% of the primary energy consumed worldwide In this paper, the specific energy consumption (SEC) and related emissions of a real scale cement factory currently A comprehensive investigation of a grinding unit to reduce energy 2021年5月3日 Commercial drivers are justified by low specific energy consumption in cement production, reductions in costs for exceeding CO2, SO2, and mercury emission quotas, and a low cost of raw materials (PDF) Energy and Economic Comparison of Different Fuels in Cement vi Normalisation Methodology for Cement Sector 104 Coal Quality in CPP 43 105 Power Mix 44 106 Product Mix 48 1061 Different cases in Cement Plants of Product Mix and use of Normalisation 52 107 Normalisation Others (REC Mechanism) 52 1071 Environmental Concern 52Cement Sector Bureau of Energy Efficiency

Reducing energy consumption of a raw mill in cement industry
2012年6月1日 Cement production in the world is currently about 16 billion ton per year About 2% of the electricity produced in the whole world is used during the grinding process of raw materials [1]While total electrical energy consumption for cement production is about 100 kWh/ton of cement, roughly two thirds are used for particle size reduction [2]Download scientific diagram Specific fuel and electricity consumption per ton of cement produced Energy is expressed as final energy (or site energy) and excludes power generation conversion Specific fuel and electricity consumption per ton of cement 2021年1月22日 In the whole process of cement production, the electricity consumption of a raw material mill accounts for about 24% of the total Based on the statistics of the electricity consumption of the raw A Survey and Analysis on Electricity Consumption of Raw Material Mill 2016年3月9日 This raw meal is blended in electrical energy consumption of a modern cement plant is Y ear 2010/1 1 Fuel Consumption in Cement Industries [25]Policy Intervention to Reduce Energy Consumption
.jpg)
Benchmarking of Energy Consumption and CO2 Emissions in Cement
2024年2月2日 Inputs encompass raw materials, electricity, and fuel, which provide the physical components, energy, and power needed to enable manufacturing activities Outputs include the desired final manufactured products, as well as waste streams and carbon dioxide emissions, which tend to be unavoidable byproducts of industrial production2016年1月20日 In the surveyed cement plant, three balances are established between input and output material in the raw mill, clinker production, and cement grinding system 248 t, 469 t, and 341 t of materials are required to produce a ton of the product in raw material preparation, clinker production, and cement grinding stages; waste gases account for Analysis of material flow and consumption in cement2022年12月1日 In the cement industry, the total energy consumption accounts for 50–60% of the overall manufacturing cost, while thermal energy accounts for 20–25% (Wang et al, 2009; Singhi and Bhargava, 2010)The modern cement industry requires 110–120 kWh of electrical power to produce one ton of cement (Mejeoumov, 2007)Thermal energy is used mainly during Review on energy conservation and emission reduction 2017年9月11日 In this study, an extensive sampling study was carried out at vertical roller mill of ESCH Cement Plant in Luxemburg Samples were collected from mill inside and around the circuit to evaluate the Performance Evaluation of Vertical Roller Mill in Cement
.jpg)
Cement Plant an overview ScienceDirect Topics
Blended raw meal, cements, Fourth, CO 2 is produced from two distinct sources in a cement plant, fuel oxidation and limestone decomposition The dual origin of cement CO 2 has some important ramifications for potential CO 2 capture technologies The electricity consumption increased by 120 2016年7月28日 Burning of raw meal to form cement clinker in the kiln: The components of the raw meal react at high temperatures (9001500 °C) in the rotary kiln, to give cement clinkerInstallation of waste heat recovery system in a cement plant: a The consumption of the energy in the cement plant is mainly due to raw mill, cooler, preheater and rotary kiln [14] The total energy loss of the plant is generally accounted for about 3539% of the total energy input [15] This energy loss is due to the loss from the exhaust gas, cooler and the radiation heat transfer from the kiln cellThermal energy consumption and its conservation for a cement 2021年3月30日 The cement industry is highly energyintensive, consuming approximately 7% of global industrial energy consumption each year Improving production technology is a good strategy to reduce the energy needs of a cement plant The market offers a wide variety of alternative solutions; besides, the literature already provides reviews of opportunities to Technological Energy Efficiency Improvements in Cement Industries
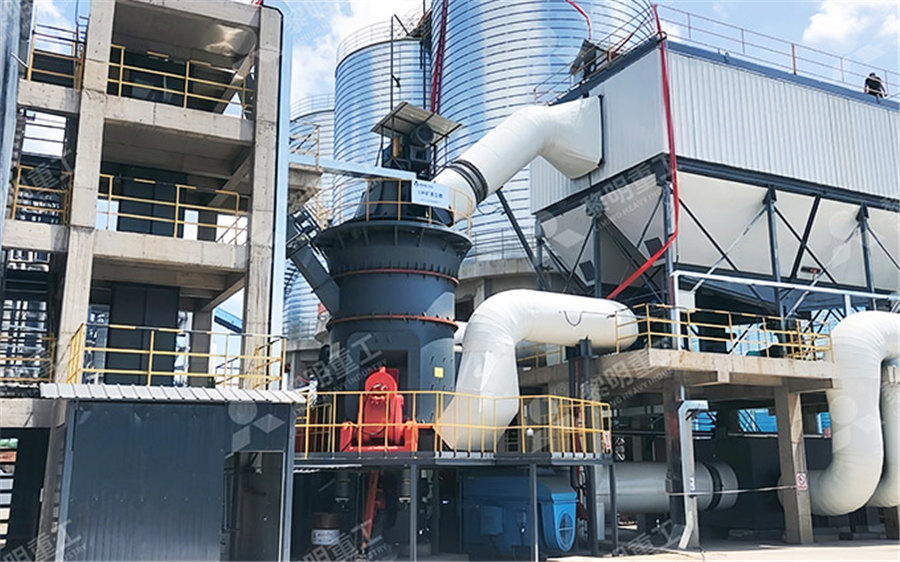
An overview of energy savings measures for cement industries
2013年3月1日 The specific energy consumption varies from about 340 GJ/t for the dry process to about 529 GJ/t for the wet processIn India, the best reported specific energy consumption is 306 GJ/t; while in some countries of the world it is lower than 295 GJ/t [20], [21], [22]The higher value in India is partly due to the harder raw material and the poor quality of the fuel [23]